15 - Wildcard Week
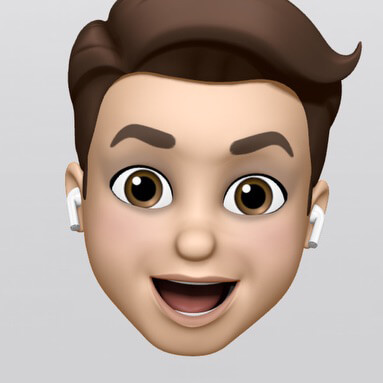
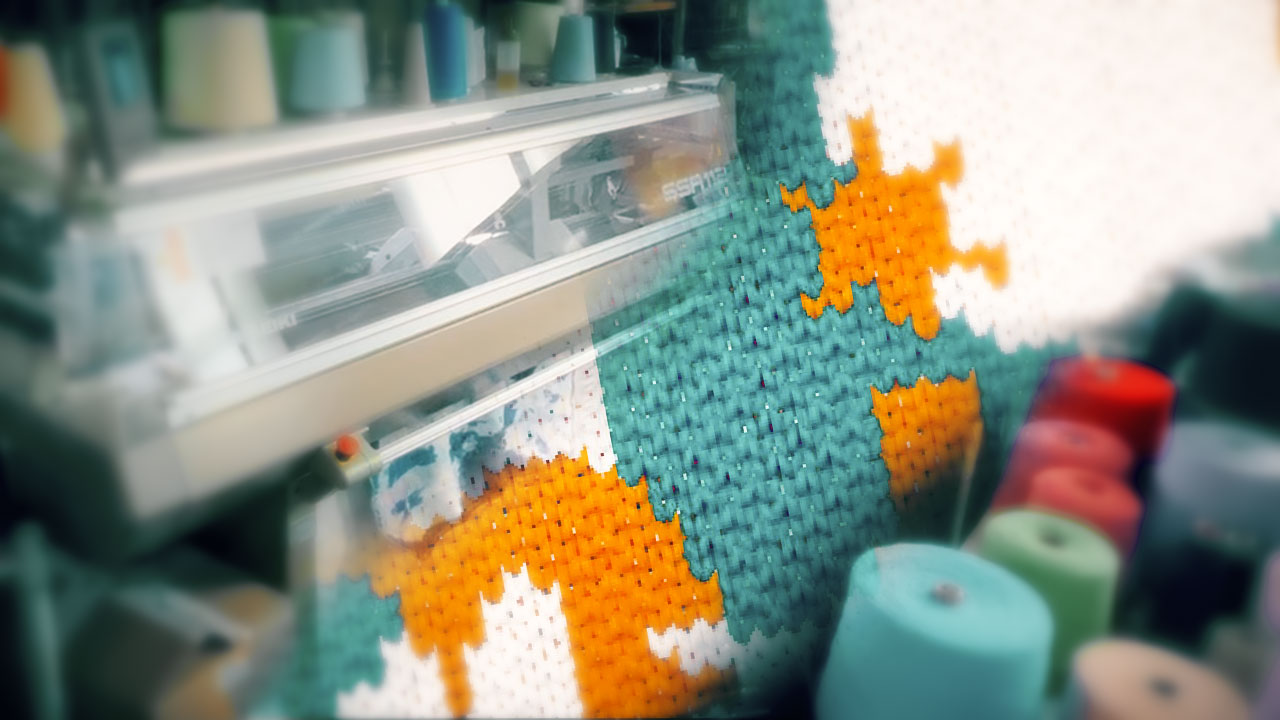
This week I went to ESNE (Madrid) to learn about a digital textile manufacturing process and much more.
This week I went to ESNE (Madrid) to learn about a digital textile manufacturing process and much more.
Assigments
Design and produce something with a digital fabrication process (incorporating computer-aided design and manufacturing) not covered in another assignment, documenting the requirements that your assignment meets, and including everything necessary to reproduce it.
Individual Assigment
On Wednesday I traveled to Madrid, thanks to the invitation of my colleague Pablo Pastor to learn how the Shima Seiki knitting machine works and to document a small part of what this machine is capable of at the ESNE (University School of Design, Innovation and Technology) fab lab. A day of hard work and learning awaited us.
The trip was long but comfortable on the new AVE line that connects Galicia with Madrid, in just over 4 hours and a half I was already in Madrid. Considering how big Madrid is, the train station is close to ESNE, so at 11 in the morning we were already at the university.
ESNE is a point of reference in higher education in the areas of Design, Innovation and Technology.
ESNE-University School of Design, Innovation, and Technology is located at 97, Avenida de Alfonso XIII, in Distrito de Chamartín, in the center of Madrid, near M30 and the metro station “Colombia”.
ESNE offers the latest technology in Digital Fabrication at the FAB LAB. This space is fully equipped with 3D printers, laser cutters and CNC, among others, and is included in the international network of the Fab Foundation originally launched by the MIT. Fashion design students can also use Shima Seiki’s computerized machines, the latest Japanese technology for knitwear.
Knitting machine
To practice with this machine I wanted to weave the Amigus Labs logo, for this Alberto and Diana, the professors of the Fashion Design career, gave Pablo and me a masterclass throughout the morning, in which they taught us technical aspects of the materials that we were going to use and how this influences the programming of the machine.
The Shima have their own equipment to work with, both the cpu, trackball and its software. Even for the most accurate colors, it is made up of a properly calibrated EIZO monitor.
Diana started by showing us how to do the first steps in the Shima Seiki software to prepare our .jpg image for knitting. The software offers many possibilities, but since we had so little time, Alberto told us that the most accessible thing would be to make a jacquard from the jpg image that we wanted.
In jacquard fabric, the pattern is not printed or embroidered, but is directly woven into the fabric due to the jacquard loom system. Therefore, through jacquard, very complex patterns and drawings can be achieved.
We start by preparing our images and importing them into the program, in my case the Amigus Labs logo.
With the loaded image we scaled it to obtain a cloth 50 centimeters wide and 50 centimeters high, we made our designs of this size because it was the one recommended by Alberto.
When we scale the image we go on to do the color treatment, this step consists of indicating in the program how many pure colors our design has, it is a very important step since later the machine will use a spool of thread for each of these colors
After color treatment, the image appears composed of pixels, each pixel is the closest color to those indicated above, this makes some color pixel that was closer to purple than blue appear orange or blue and vice versa. In this case you have to clean the pixels of the design with an unwanted color or a needle of that color will pass through this point. To select the color we have to press the READ | CAL key on the trackball. |
Then you must indicate the gauge of the machine (ESNE’s Shima Seiki is gauge 7, this value cannot be changed), the number of colors and the needles per cm.
After this case we get a render of our cloth
Once the previous steps have been completed, the file must be prepared to be programmed in the programming part of the software machine.
In the programming software of the machine, the way in which the back of the fabric will be formed is selected (It also affects the front part).
When this step is completed, the software generates the file that we will introduce to the machine, this indicates which color we must load in each thread rail so that the cloth is made correctly.
In this file if we zoom, the program tells us at each point what operation the machine will do, if we want to modify any operation we can do it in this step, we can modify each of the points.
After this step, all the files that the machine needs are generated, with them we can do a fabric simulation to see if the program gives us any errors.
Thermoform
In the afternoon, taking advantage of the fact that I needed to make a small dome dome for the buoy of the solar project, I brought a piece ready to do the thermoforming.
The first thing we did was make the model with foam in the CNC, a hemisphere of 5 cm in diameter.
We prepare the piece in Vcarve for milling.
Formech Compact Mini
The Formech Compac Mini is a plug ‘n’ play machine and the perfect entry-level vacuum former solution for creative hobbyists, artisans and students. Can thermoform plastics such as HIPS, ABS or PETG up to 4mm thick.
Once the piece is milled, we go to the thermoformer. We tested with three materials, a transparent plastic, a red one and a green one.
The machine manufacturer provided ESNE with a schedule, so we relied on the proposed time of 50 seconds to heat the plastic.
The operation of the machine is very simple, place the model, then the material to be thermoformed, program the heating time. Once programmed, tighten the blade locks, drag the heating plate, wait 50 seconds, and lower the lever once the time has elapsed, and activate the suction.
Remove the heat plate and wait a few seconds, and when we believe that enough time has elapsed. Vacuum and unmold, once the formed part has cooled, air is blown between the mold and the sheet to help them separate.
I have really enjoyed this day in Madrid, it brought back many memories of my time as a student. Thank you very much Pablo! ;)