Task to be Perform for this week
Individual Assignment:
Propose a final project masterpiece that integrates the range of units covered. Answering the following questions.
Your project must be incorporate the following:-
2D and 3D design.
Additive and subtractive fabrication processes.
Electronics design and production.
Minterfacing and programming.
System integration and packaging.
Learning outcomes
1) Define the scope of a project.
2) Develop a project plan.
Introduction:-
In this week Prof. Neil reviewed of different kind of project done by fabacademy and its various applcations and benefits for the society.As our final project is the part of fabacedemy course, so In this week we need to give the answer of some basic quetions related to our final project asked by fabacademy.So, we have discussed with our Fablab instruction and tried to give the detail ideas about our final project like objectives, methodology ,processed used in the project.how we planed for the project and the various outcomes. So for this week of Individual assignment I have to answer various questions about my Final Project. These answers will direct me to prepare a plan for development of my Final project and clarify the doubts.
About my final Project:- Idea of my final project is wanted to make Edible Oil Temprature controller during frying Process.LINK Deep frying is the universal, prevalent and one of the most important processes involve in the food processing industry even in the home kitchen. Psychologically thinking of the reason behind is only the economic reason as the oils are expensive and after the first use, there is a lot of oil remaining on the pot, that makes people use it again and again without any concern of the health effect of this oil. Although for a country like India where 60% of the edible oil imported from the other source of the country which bears a lot of economic expenses. Every year elevation in the price of edible oil which causes people to use the same oil in repeated frying for food. In this review, the paper focuses on the jeopardize effect on health and the statistical and economic analysis on the edible oil in India.Referance Link By reffering this as this idea comes in mind while dicussing with instructor at vigyan Ashram If we are able to maitain the temperature of edible oil in between perticular range the effect of rehaeting and the quality of oil can me maintain.
The figure shows the Effect of reheting of edible oil
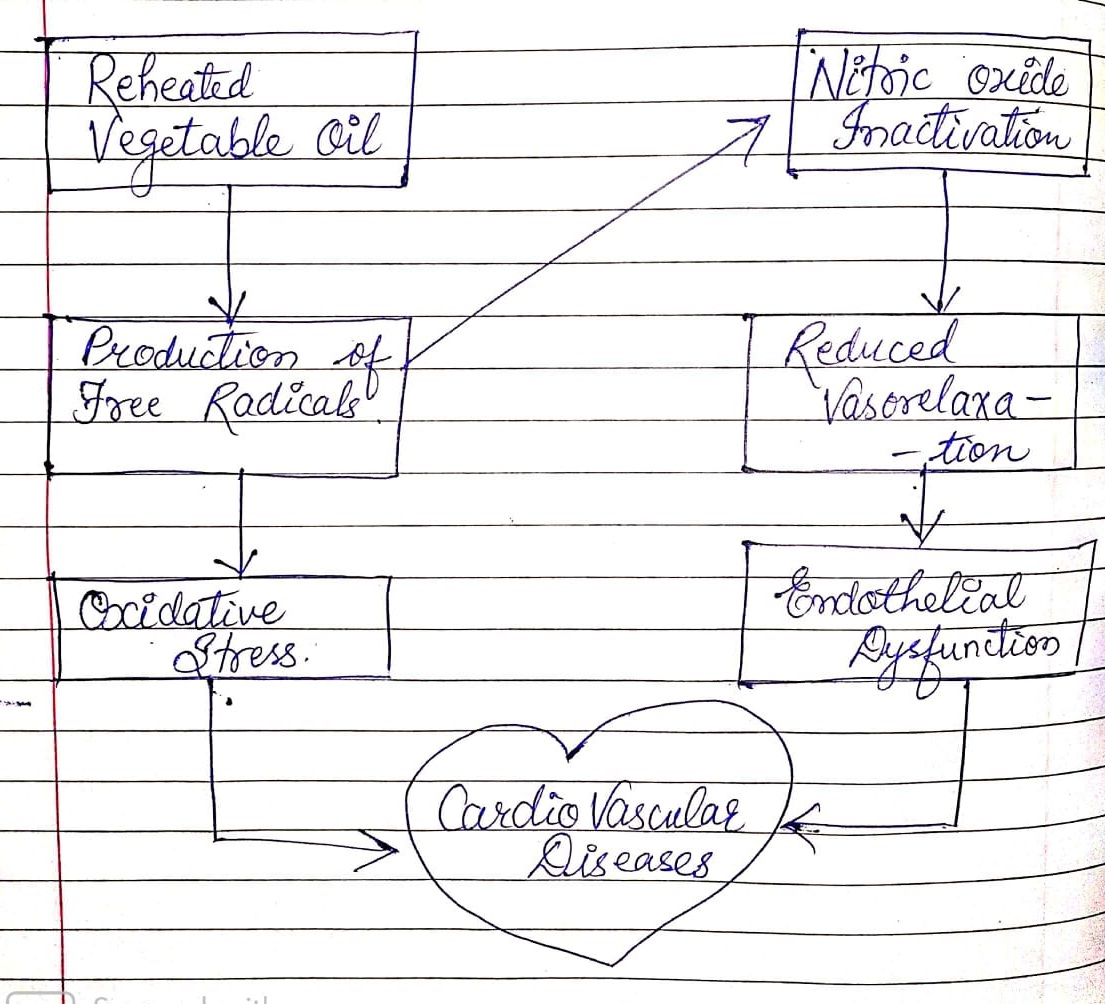
This is an Initial sketch.
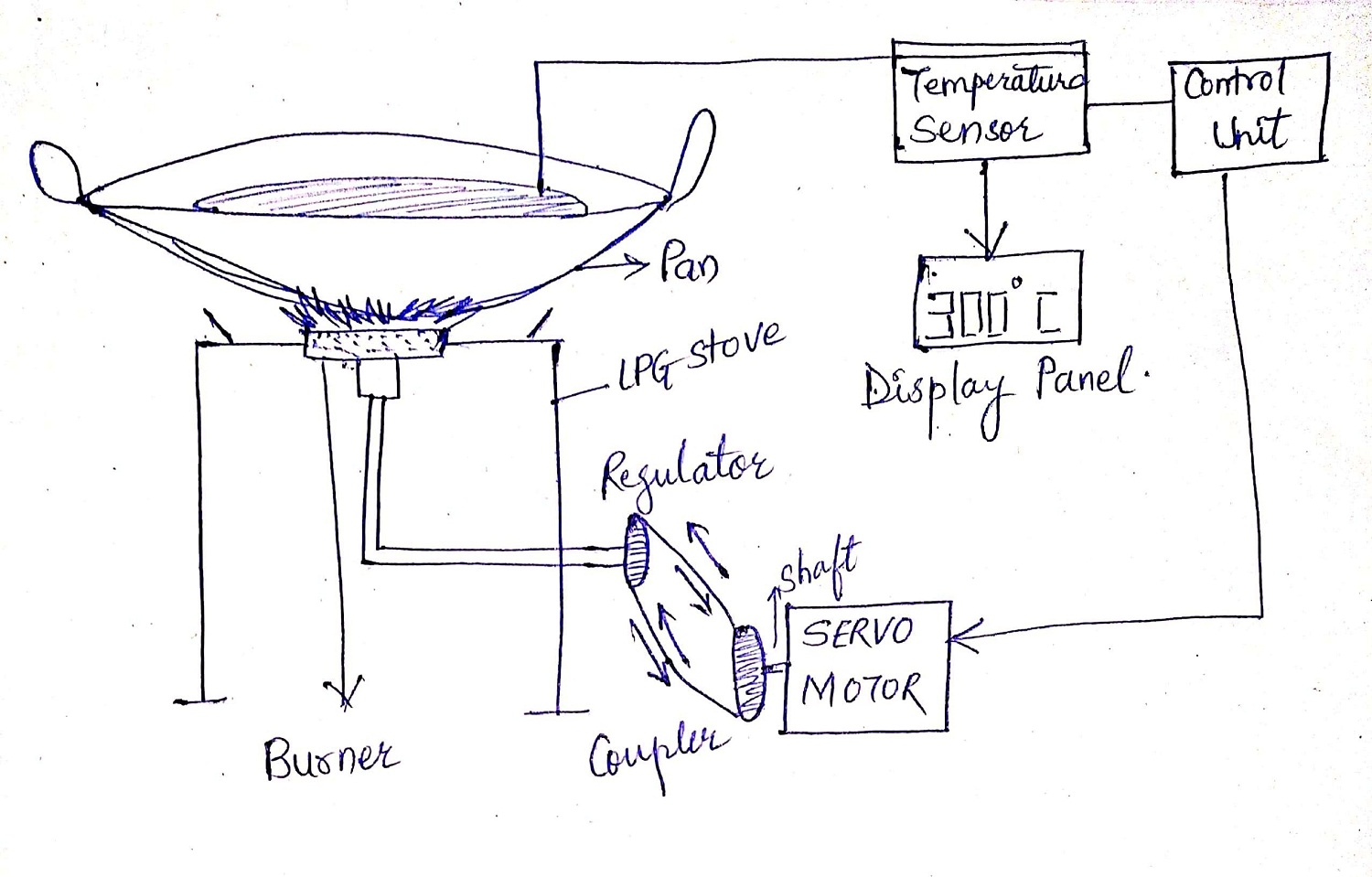
1.What it will do?
The edible oil temperature controller it is simply by controlling the flame of LPG with the help of stepper motor.The edible oil temperature controller project simply funstions on the idea of controlling the flame of LPG gas burner.
It mainly operates with sensor and stepper motor for the flame regulation as per our need.
Deep frying (also referred to as deep fat frying) is a cooking method in which food is submerged in hot fat, most commonly oil, as opposed to the shallow oil used in conventional frying done in a frying pan. Normally, a deep fryer or chip pan is used for this; industrially, a pressure fryer or vacuum fryer may be used. Deep frying may also be performed using oil that is heated in a pot. Deep frying is classified as hot-fat cooking method. Typically, deep frying foods cook quickly: all sides of a food are cooked simultaneously as oil has a high rate of heat conduction. as per survey the good or correct frying temperature depends on the thickness and type of food, but in most cases it lies between 350–375 °F (177–191 °C). An informal test for a temperature close to this range involves adding a tiny amount of flour into the oil and watching to see if it sizzles without immediately burning.
In India the fried food is highly consumed taking from breakfast dishesh to some of dinner dishesh too. When the cooking of such food happens the oil may get rapidly heated and due to that oil quality gets decrease beacause of some chain reactions.
Also cost of oil is quite high so the reusing of reduced quality oil is reused in hotels.
So, repetative heating of oil also changes its natural quality to some harmful contents which can be very hazerdous for human health.
So one of the precise solution for this issue is by maintaining the temperature range of edible oil in between safe boundaries so as to prevent it from overheating and rapid heating.
So for avoiding this overheating we are implementing the technique of temperature control with the help of stepper motor
And temperature sensors for controlling the the flame of LPG to the specific requirement.
2. Who's done what beforehand?
Some litarature have been found realted to this topic as below.
Why do we need temperature controllers?
Temperature controllers are needed in any situation requiring a given temperature be kept stable. This can be in a situation where an object is required to be heated, cooled or both and to remain at the target temperature (setpoint), regardless of the changing environment around it. There are two fundamental types of temperature control; open loop and closed loop control. Open loop is the most basic form and applies continuous heating/cooling with no regard for the actual temperature output. It is analogous to the internal heating system in a car. On a cold day, you may need to turn the heat on to full to warm the car to 75°. However, during warmer weather, the same setting would leave the inside of the car much warmer than the desired 75°.
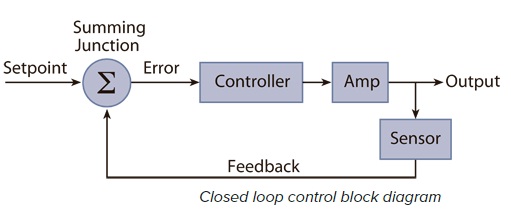
A temperature controller is a device used to hold a desired temperature at a specified value.
The simplest example of a temperature controller is a common thermostat found in homes. For instance, a hot water heater uses a thermostat to control the temperature of the water and maintain it at a certain commanded temperature. Temperature controllers are also used in ovens. When a temperature is set for an oven, a controller monitors the actual temperature inside of the oven. If it falls below the set temperature, it sends a signal to activate the heater to raise the temperature back to the setpoint. Thermostats are also used in refrigerators. So if the temperature gets too high, a controller initiates an action to bring the temperature down
Common Controller Applications:-
Temperature controllers in industry work much the same way they do in common household applications. A basic temperature controller provides control of industrial or laboratory heating and cooling processes. In a typical application, sensors measure the actual temperature. This sensed temperature is constantly compared to a user setpoint. When the actual temperature deviates from the setpoint, the controller generates an output signal to activate other temperature regulating devices such as heating elements or refrigeration components to bring the temperature back to the setpoint.
Common Uses in Industry
Temperature controllers are used in a wide variety of industries to manage manufacturing processes or operations. Some common uses for temperature controllers in industry include plastic extrusion and injection molding machines, thermo-forming machines, packaging machines, food processing, food storage, and blood banks. The following is a brief overview of some common temperature control applications in industry:
Here is the reference LINK
PID temperature controller DIY Arduino
PID temperature controllers work using a formula to calculate the difference between the desired temperature setpoint and current process temperature, then predicts how much power to use in subsequent process cycles to ensure the process temperature remains as close to the setpoint as possible by eliminating the impact .
In current times the industries are using PID ( Prapotional Integral Derivative.) based controller for maintaining the temperature of edible oil
In their equipments of food making.
This is what I have gone through the literature about this concept.
In market some devices like electric oven, frying pots in which the LPG flame or heating process gets controlled with the predefined system protocols. It gets automatically switch on or off accordingly.
In an oil fryer control system it simultaneously controls oil temperature and cooking time.
In the proportional, integral and derivative temperature control system it function in the range of sets points of temperature to avoid over heating of oil.
For making this final project I have gone through the literature of Some Industry base PID controller used to maitain the temperature of hot furnace.
link1
link2
As I wanted to make a simple stepper motor base conditional controller which can monitor the temperature of edible oil and the value of temperature is increases beyond the set limit the stepper motor will reduce the flow of LPG.
3. What will you design?
As we explore the various Cad designing software in the 2ND week.
1. First of all I will design the 3D assembly of my final project in Solidworks Software.
2. Then I have made the Mount for Nema -17 stepper motor using FreeCAD. software.
3. Final Project Microcontroller Board Designed:- Then I will design the schematic and Board designed of Atmega328p Microcontroller Board in Autodesk Eagle Software.
4. Then In output devices week I have desined the PCB Board for mounting the A4988 Stepper motor driver.
5. Designed the Casing for stepper motor in lessercutter machine using Acrylic material.
6. Designed the motor connector as coupler for LPG stove and stpper motor in freecad Software.
4. What materials and components will be used?
For Final project I need some hardware part listed as shown in below table.
Ans: The list of components with specification:
Sr. No. | Name of Components | Specification | Qty. |
---|---|---|---|
1. | NEMA 17 Stepper Motor | 1.8 Degree Step angle,(200 step per revolution,Each phase draws 1.2 A at 4 V,3.2 kg-cm Torque) | 1 Nos. |
2. | Couplling for stepper motor. | As per requirement | 1 Nos. |
3. | A4988 Stepper Motor Driver | 35V-12V/2A Per Phase. | 1 Nos. |
4. | PT1000-S Waterproof 1m 30mm Stainless Steel Pole Probe Temperature Sensor,Length of the probe: 30mm. | Accuracy ±(0.3°C+0.5%|t|),Max range 550°C. | 1 Nos. |
5. | Atmega328P Microcontroller Board | - | 1 Nos. |
6. | 4.7 kohm series Resistance | Variable Potentio meter. | 1 Nos. |
7. | LCD Display with I2C module | 1 Nos. | |
8. | Stuffing Electronics Component Like resistor, Capacitor, Power LED, 20Mhz Crystal Oscillator. | -- | As per requirement |
9. | Cummertial LPG Stove with circular Knob. | -- | -- |
10. | DC Power Adaptor. | 12 Volts | |
11. | Iron material for assembly to stepper motor | As per Size and Dimenssion of LPG stove. | -- |
12. | Miscellaneous Accessories | - | As per requirements |
5. Where will they come from? and How much will they cost?
Sr. No. | Name of Components | Supplier | Cost (Approx.) |
---|---|---|---|
1. | Nema 17 Stepper Motor | FABLAB Inventory | 800/- |
2. | A4988 Stepper Motor Driver | FABLAB Inventory | 110/- |
3. | 12 Volts DC power Adaptor | Amazon/flipkart | 120/- |
4. | LCD with I2C Module | FABLAB Inventory | 300/- |
5. | PT1000 Temperature Sensor; | Amazon/Flipkart | 200/- |
6. | Copling for Stepper Motor | FABLAB Inventory | 150/- |
7. | Iron Material for Stucture | Vigyan Ashram Inventory | 1000 |
8. | ATMEGA328P IC | Vigyan Ashram Inventory | 300 |
10. | Wire and other Miscellaneous | Fab Lab Inventory | 500 |
The total aproximaterly cost is Rs. 3280/-
6. What parts and systems will be made?
1. I have made the body of iron material to stucture to place the stepper motor in front of LPG strove.
2. Then Casing using plasama cutting machine for fixed the motor.
3. Then I have made the ATMEGA328p Microcontroller Board in Eagle Software and mill it using SRM-20 PCB milling machine.
4. I have desinged and Develope the stepper motor Mount using FreeCad Software and print it on 3D Printing Machine.
5. For microcontroller board Acrylic casing box.
6. Driver Footprint for A4988 module using SRM machine.
7. What processes will be used?
I have used the following Processes.
1. Firsly I have define the objective of my final project.for that by reffereing some litrature on this topic proceed my work.
2. Initial Step of my final project is to calibrations of PT1000 temperature sensor.
3. Then, I Initially tried to draw the skecth of final object.
I have used the various CAD Desinging softwares for drawing the assembly and some required part of project in CAD Designing process.
4. I have learned the Arduino IDE And its programming language for preparing the final code.
5. Desinged and Develope the Microcontroller controller board using Eagle software.
Milling of Microcontroller Board using Mods and SRM Milling Machine ans stuffing the component on it using soldering process.
6. Develope the LPG stove Valve by moulding and casting process.
7.Develope the Stepper motor mount using 3D printer.
8. Develope the body to placed and fixed the stpper motor in front of LPG knob by welding an the stepper motor.
9. welding, grinding and painting the iron stucture used for final project.
10. Calibrations of PT1000 temperature sensor using Microsoft Excel tool, plot the graph of temperature Vs Voltage and done the calculation for Calibrating the factor so that temprtaure sensor will display the proper value.
1. Firsly I have define the objective of my final project.for that by reffereing some litrature on this topic proceed my work.
2. Initial Step of my final project is to calibrations of PT1000 temperature sensor.
3. Then, I Initially tried to draw the skecth of final object.
I have used the various CAD Desinging softwares for drawing the assembly and some required part of project in CAD Designing process.
4. I have learned the Arduino IDE And its programming language for preparing the final code.
5. Desinged and Develope the Microcontroller controller board using Eagle software.
Milling of Microcontroller Board using Mods and SRM Milling Machine ans stuffing the component on it using soldering process.
6. Develope the LPG stove Valve by moulding and casting process.
7.Develope the Stepper motor mount using 3D printer.
8. Develope the body to placed and fixed the stpper motor in front of LPG knob by welding an the stepper motor.
9. welding, grinding and painting the iron stucture used for final project.
10. Calibrations of PT1000 temperature sensor using Microsoft Excel tool, plot the graph of temperature Vs Voltage and done the calculation for Calibrating the factor so that temprtaure sensor will display the proper value.
8. what questions need to be answered?
1. Whether the stepper motor able to controlled the knob of LPG Precisely.
2. Should I use any other motor(link Servo, DC motors..) to controlled the valve of lpg instead of stepper motor
3. Where this model is feasible for mainting the temperature and controlling the LPG flame.
4.What is the required torque to controlled the knob of LPG stove.
5.Can Nema 17 3.2 kg Stepper motor is provide the sufficient torque.
6. Is Pt1000 temprature sensor is measure the accurate value of oil temperature.
7. Is my final project is fullfill the objective as I decided.
9. How will it be evaluated?
My final Project can be evaluted on the basis of following point
1). The evalution of my final project is on the basis of the temperature sensor i.e. PT1000 whether sensor is able to continiously monitor the temperature of edible (frying) oil or not, and as per temperature reading/value of temperature which I have set in the coding (As per required range ) the stpper motor is able to controlled the flame of LPG Stove.
2). The temperature will be continiouly monitor the LCD display.
3). If the temperature of oil is increases beyond the set limit the stepper motor is reduce the flame of LPG .
4). If the temperature of edible oil is reduce with the help of stepper motor flame of LPG should increase.
Plan for my final project is shown in below Table.
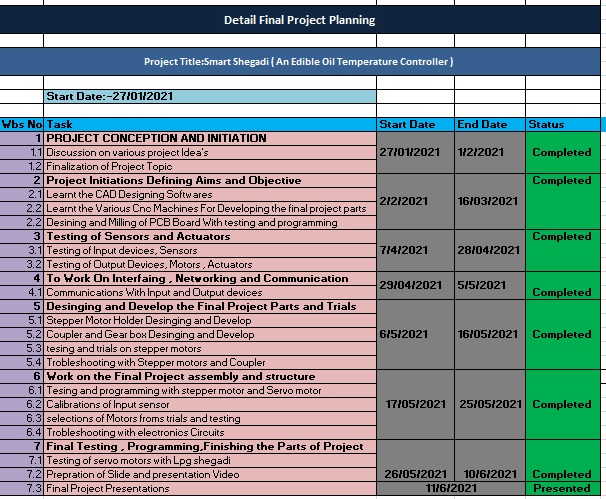