Week 16. Wildcard Week
This week is a free week, where we can do something different from what we have seen so far in class. In my case I am going to test the composites technique because it is the one that I want to use to create the landscape of my model for the final project.
- Demonstrate workflows used in the chosen process. ✔
- Select and apply suitable materials and processes to do your assignment.. ✔
- Documented how you made your creation. ✔
- Described problems and how you fixed them. ✔
- Included your design files and ‘hero shot’ of the result. ✔
Like every week, my weekly schedule. 😊
As I have mentioned, I am going to try to use the composite technique for my final project as a base for the landscape. It will be light and resistant. If I have time, I also wanted to try creating a soft robotics. 🤖 😊
Group Assignment.
The Group Assignment page is at the following link.
If you click on this link, you go to the Group Assignment section that I have done for this week.
Safety Data Sheet (SDS) and Technical Data Sheet (TDS) for the resins
For this assignment I am going to use an Entropy Resins (Super Sap) brand epoxy laminating resin. Clear, general use, laminating epoxy for composites, coating, and adhesive applications. CLR is a SUPER SAP® Formulation.
The one in the Fab Lab León is the CLF (Fast) model. It has the following Technical Data Sheet (TDS).
- Mix Ratio (by volume): 2: 1 (Part A / Part B)
- Mix Ratio (by weight): 100: 45 (Part A / Part B)
- Pot Life (25ºC): 21 min.
- Tack Free Time (35ºC): 4 hrs.
- Recommended Full Cure: 7 days 25ºC
On the Safety Data Sheet (SDS). Good ventilation is recommended, wearing safety glasses, rubber gloves and long sleeves. As we are in COVID-19 period, I use the mask. 😷 This type of resin is corrosive and irritating on the skin and on the eyes, so you have to protect yourself.
Important: If we have leftover resin, we should not throw it away without curing or throw it down the sink. We will let it dry in the container and remove the film. We will have to throw away the brushes and rollers, because we will not cover them.
Design a 3D mold
During Week 02, Computer-Aided Design used Blender to design the modules for my model. Because I had already modeled each module the way I wanted, I export each one in the .STL format.
With Rhinoceros, I perform boolean cutting operations using a plane, to obtain two parts of the landscape of each module. Top and bottom; because in between the railway goes.
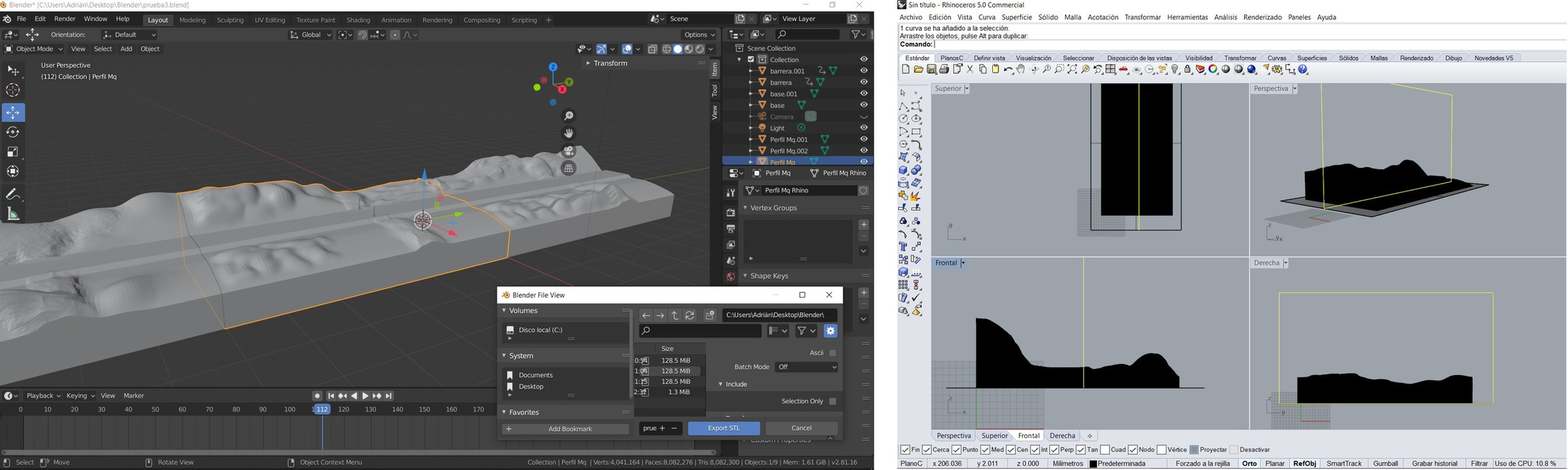
This is the result of module 1. Important: as Nuria's recommendation and because of the distance between the CNC base and the spindle (as I explain in week 07, I can only use ~ 40 mm depending on the mill). And the polystyrene plates are 40 mm, so I make horizontal cuts to each part, I slice it.
I take advantage and make all the cuts for the three modules of the project. In this assignment I am going to mill only a part of module 2. I upload the file to SketchFab because it is too big for the repository.
The next step is to mill the part.
3D Milling
To mill in 3D on the CNC milling machine in the Fab Lab León that I taught in week 07, I will use Vectric's Aspire software. Before going to the Fab Lab, I test the toolchain at home, and do the simulation to see how long it takes. I use the trial version of the Aspire 10. I try to perform a rough milling and then finish two of them turned 90º.
Using a 6mm mill polystyrene gives me a total time of 3 hours. I'll have to see how it looks in the Fab Lab León Aspire simulation.
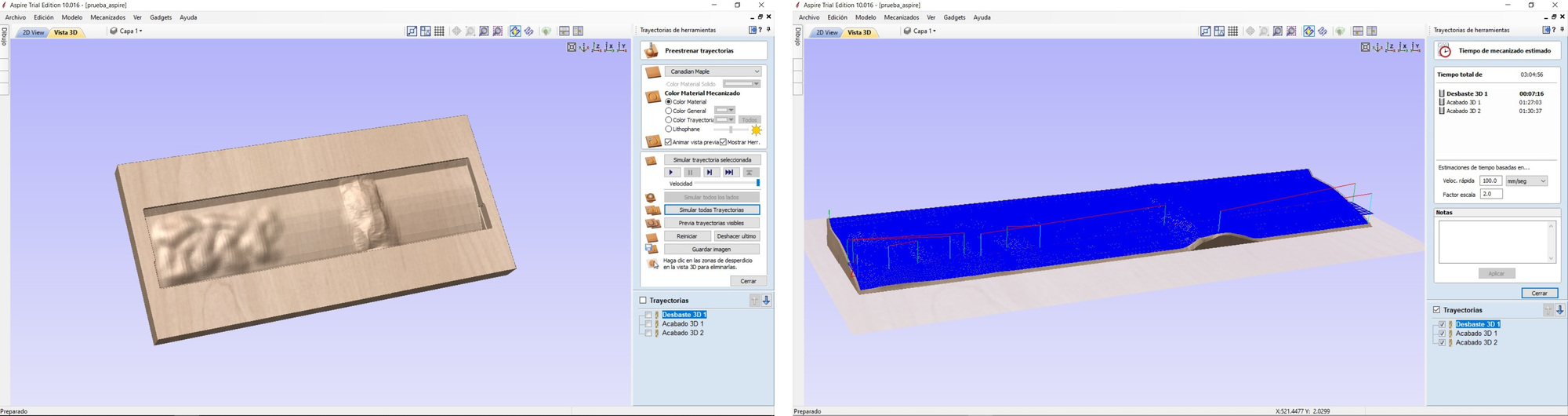
The Aspire of the Fab Lab León is an old version and some things compared to the modern one. The first thing I choose is the size of the material (the material plate is 1250 x 600 x 40 mm). I import the STL and orient it, I tell it that the position plane 0 is down completely.
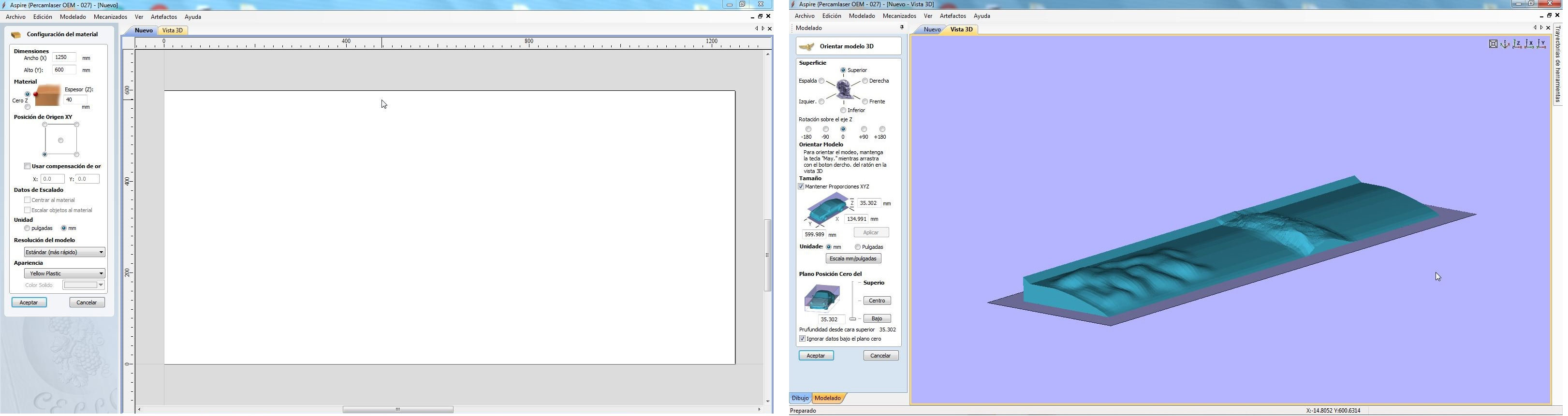
I choose the 6mm cutter for polystyrene to make the rough. I see in the simulation that it mills all the material (in the modern version of the Aspire, it only mills the part). So Nuria recommends that I adjust the material to the piece.
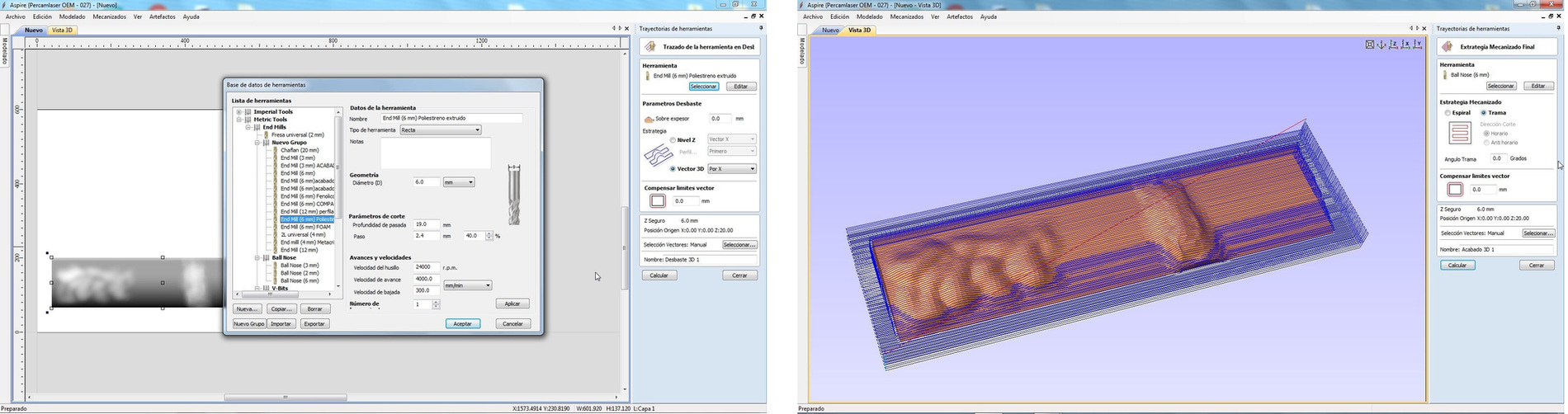
I choose the 6 mm cutter for polystyrene to make the rough. I see in the simulation that it mills all the material (in the modern version of the Aspire, it only mills the part). So Nuria recommends that I adjust the material to the piece.
Also in my case I don't need it to be a perfect surface, because it will be part of the landscape and I will camouflage it with vegetation and herbs. So I'm going to try doing just the rought machining, without using the ball mill to make the finish finish. It only takes 25 minutes.
Once the simulation has been carried out and the strategy that I am going to use has been decided, I move on to the CNC milling machine. These are the two mills, 6 mm for polystyrene and the ball (the latter I will not use). I must tighten the mill well to the spindle.
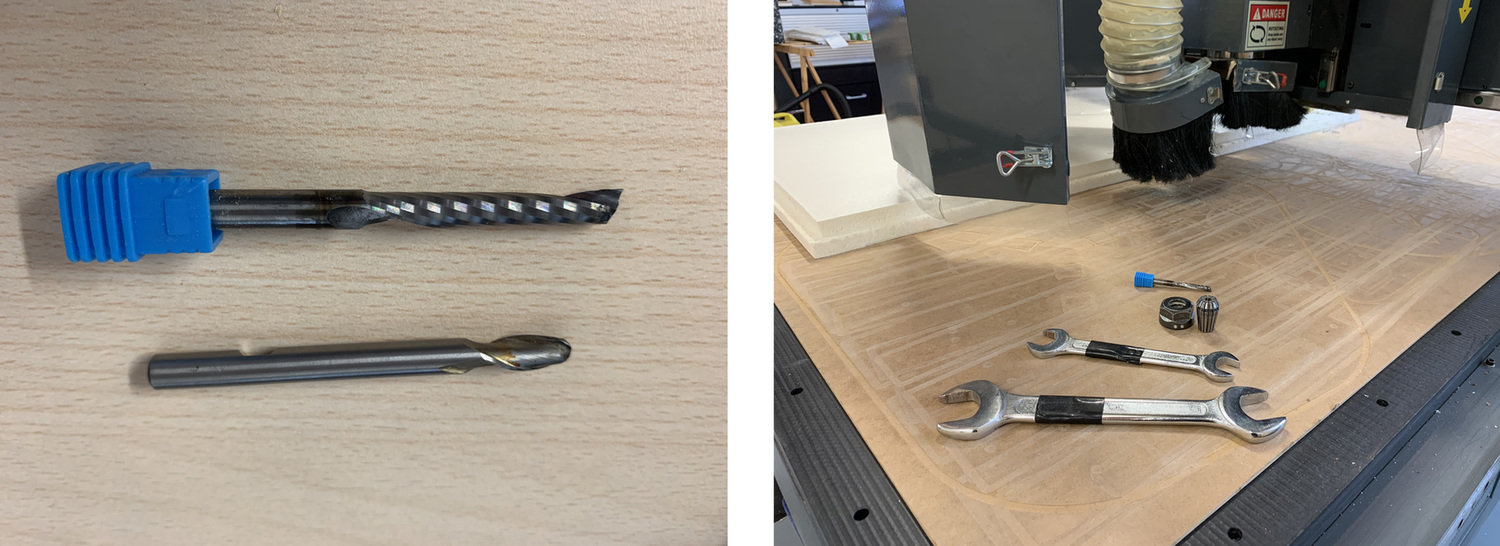
I make the Z zero of the machine and it gives me a material thickness of 39 mm. I recalculate the trajectories and start the machine. It starts working and goes down to almost the base of the CNC. 😰 I stop immediately.
I drilled the base of the CNC again, I was quick and stopped it. I made a mistake, a serious mistake. I measured the zero Z first at the material surface and then at the base of the CNC. I keep the base of the CNC as Z. 😖 Remember Adrian: First the Z is measured at the base of the CNC and then at the surface of the material.
After the scare was over, I re-measured the Z well.
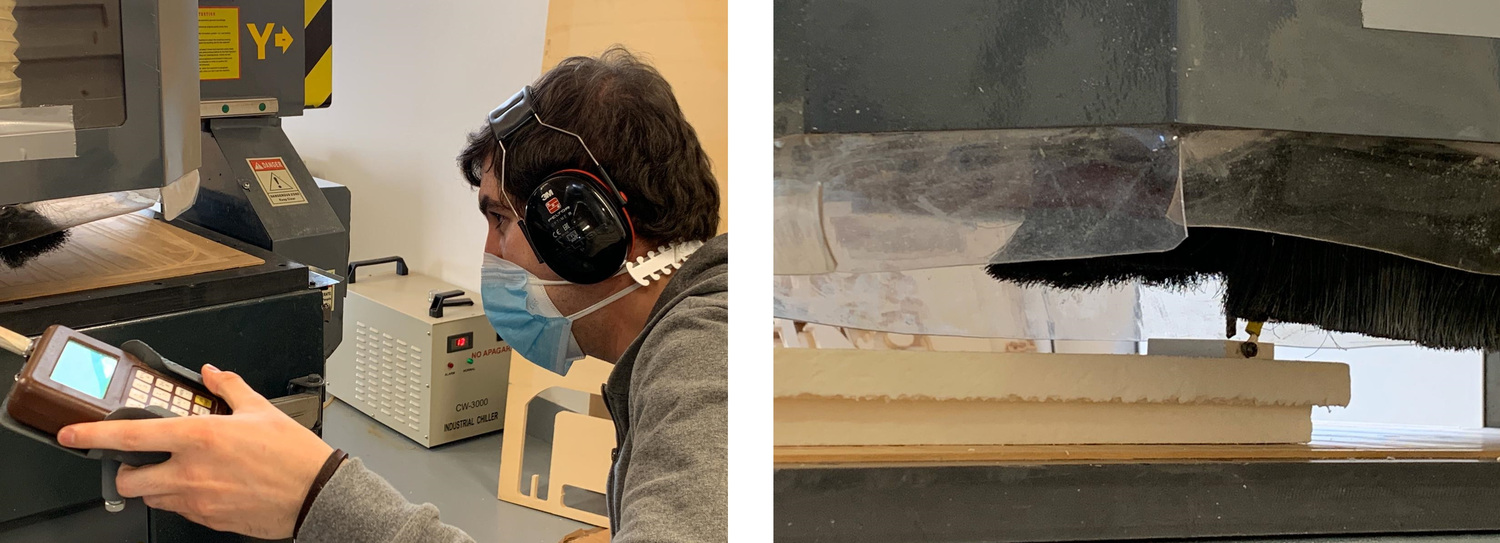
Once I have milled with the rough technique, I decide to stay with it because the lines are not going to be noticed much and the landscape is not uniform.
I make a profile path around the piece, for the milling machine to cut and obtain the final piece.
Once the part is removed and aspirated, this is the result. A piece of my future model for the final project.
Composite process
As Neil explained in class, it's about applying a resin to a fabric or fiber. Fiber alone is good for tension, but bad for compression. The resin is good for compression and bad for tension. So if we combine the two materials we obtain a compound resistant to tension, but also to compression.
The composites process is as shown in the following drawing. We have a 3D mold, which we protect with a protective film (the kitchen one is worth it). Then we will place the fiber or the fabric impregnated in the epoxy resin. Next we put a release film (it will help us to get the excess resin out of the mold). Then a blanket that covers the entire mold and absorbs excess resin. Finally all this is put inside a vacuum storage bag.
Once I am clear on the process, I protect the floor and the work table and prepare all the necessary materials.
The first step is to protect the polystyrene mold that we have milled with the film. So we can use it more times.
Using the textile vinyl sheet, I iron the fabrics that I am going to use in this case burlap. Then I cut it to the size of the mold, and cut the corners a little diagonally. In my case for the final project I will not need the edges, I will have to cut them, because they will rest on the model frame. For this test I will use only one layer of burlap.
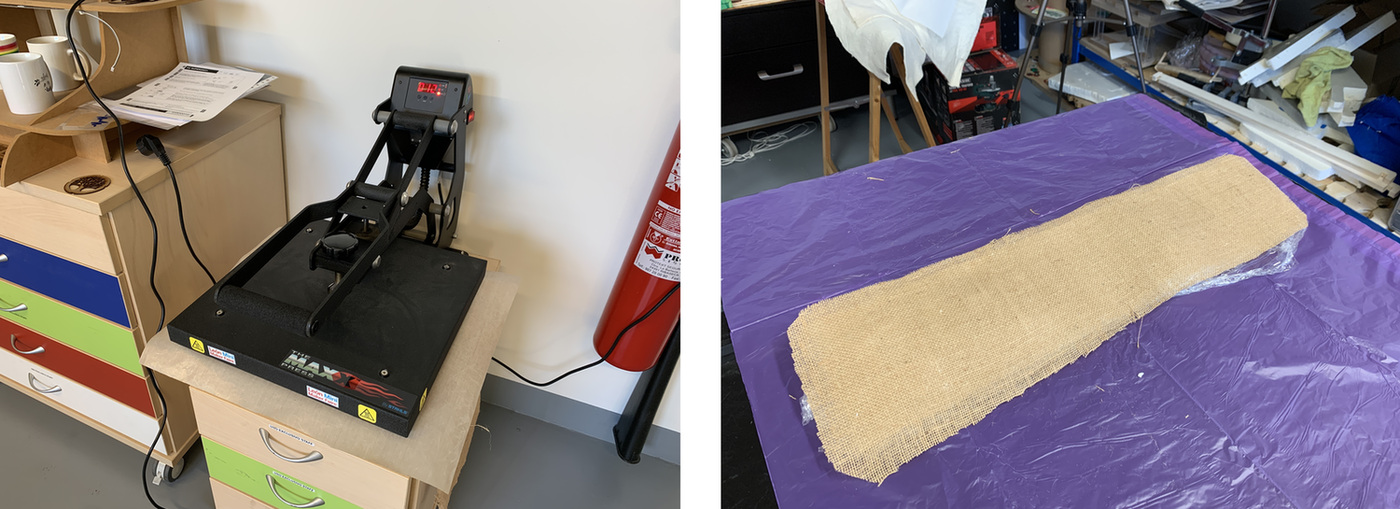
Now I proceed to mix the epoxy resin. It is recommended to use two pairs of gloves, because the resin is quite sticky. It consists of two parts, Part A and Part B. I am going to add 100 gr of Part A and 45 gr of Part B. The plastic cup is 5 grams. I have 21 minutes to work with the resin.
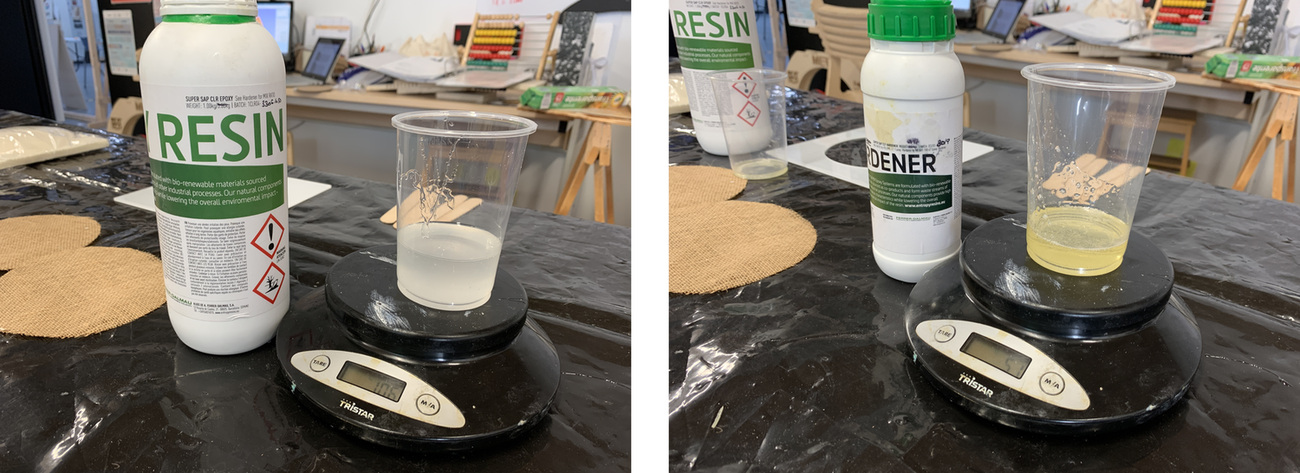
With the help of a roller and a brush I spread the epoxy resin on the burlap. It is recommended to protect the table with another plastic since we are going to soak the fabric. Then we will place it on top of the mold.
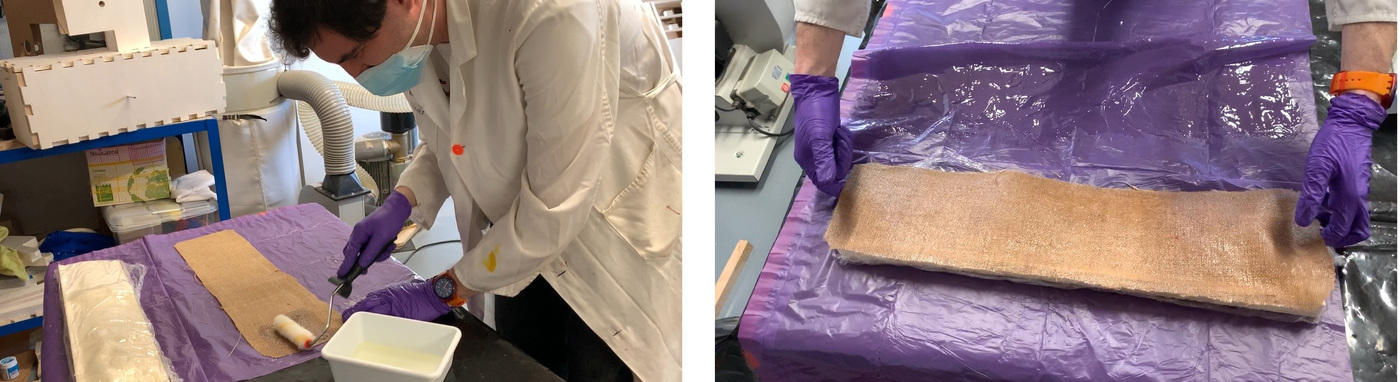
The next thing is to cut a piece of release film (it is a perforated film to help evacuate excess epoxy resin). In the photo you can see the detail of the little holes.
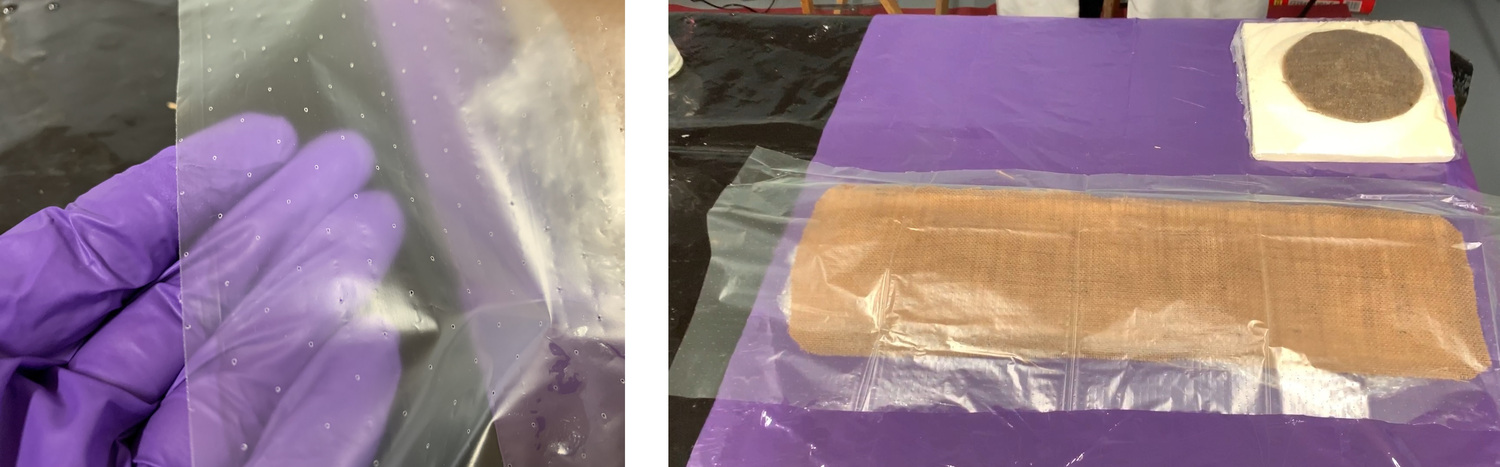
Later we will place a blanket, to absorb the rest of the epoxy resin and that does not stick to the vacuum storage bag.
The final moment comes, insert the mold with all the previous layers into the vacuum storage bag. So that the suction valve is not blocked, we will place a piece of blanket under it (blue blanket). This way we will continue to vacuum the vacuum cleaner. Thanks to the help of my instructors, Nuria and Pablo I can carry out this assignment. 😍
We close the bag tightly and vacuum with the vacuum cleaner until there is no air left. The bag begins to wrinkle and you see how the excess resin begins to transfer the release film and soaks the blanket. Is incredible. The manufacturer says that after 7 hours the composite can be manipulated, in my case I will leave it for 24 hours. Then until 7 days have passed it will not be completely healed.
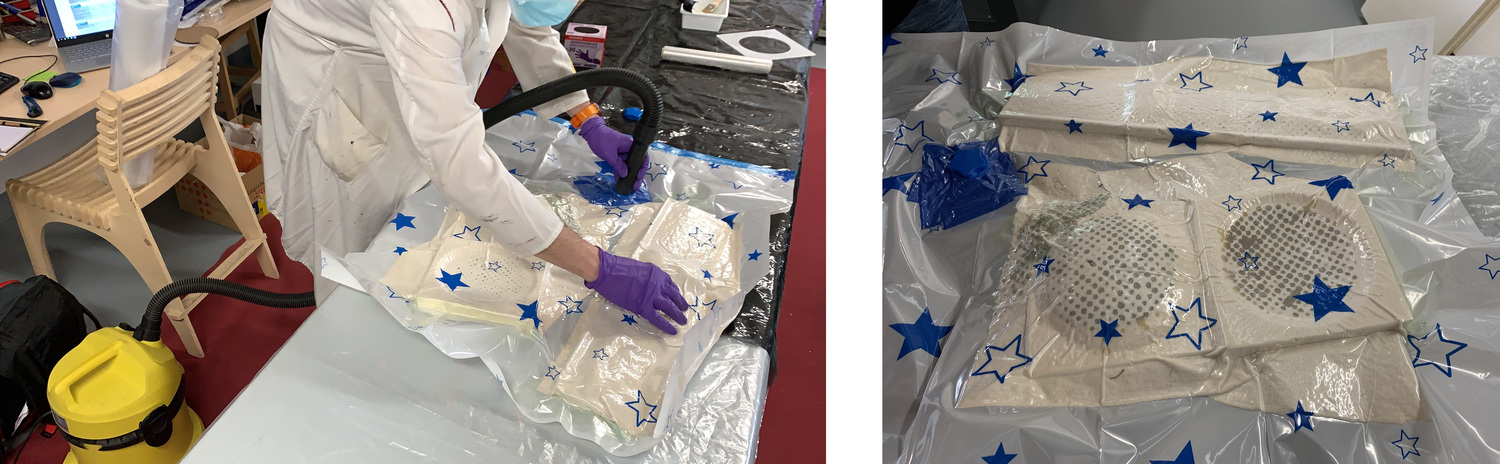
After 24 hours I return to the Fab Lab, and check that the bag remains the same, it has not lost its vacuum. That is a good sign. So I take out the mold, peel off the blanket and notice that there are little dots of resin left over. Then I remove the realease film, and I get the burlap perfectly sealed, all its holes bonded with the resin.
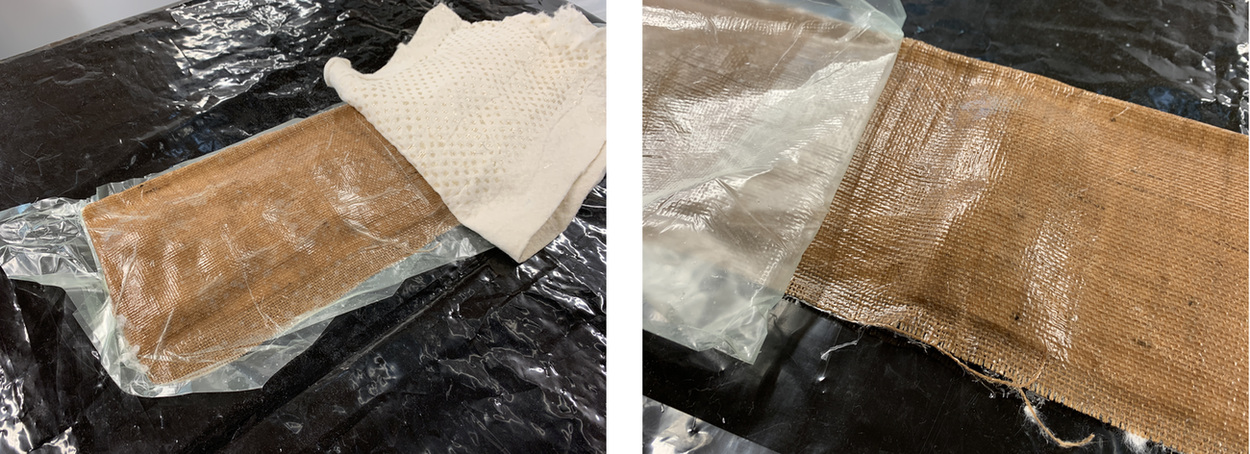
And this is the result, my first piece of landscape from my model. I will have to let it cure for 7 days and cut it to fit the model frame. One of the advantages of using this technique is that I can recover the mold, reuse the realease film, the blanket and the vacuum bag. I just have to make more resin and more burlap. Incredible. 🤗
Produce test coupons for your composite fabrication process(es).
To test the coupons, I'm going to use a cut-out-of-a-sphere design, up and down inside a prism. The size is 200 x 200mm. To design it, I use Rhinoceros. Once I have both designs, I go to the Aspire, where as in the individual assignment I simulate the result of the 3D mold. I do two trajectories, rough and finish. As I liked the rough finish, I will do it alone, it takes 20 minutes for the two pieces. At the bottom of the page are the STL files to download.
Once the two molds have been milled with the 6 mm cutter for polystyrene, this is the result.
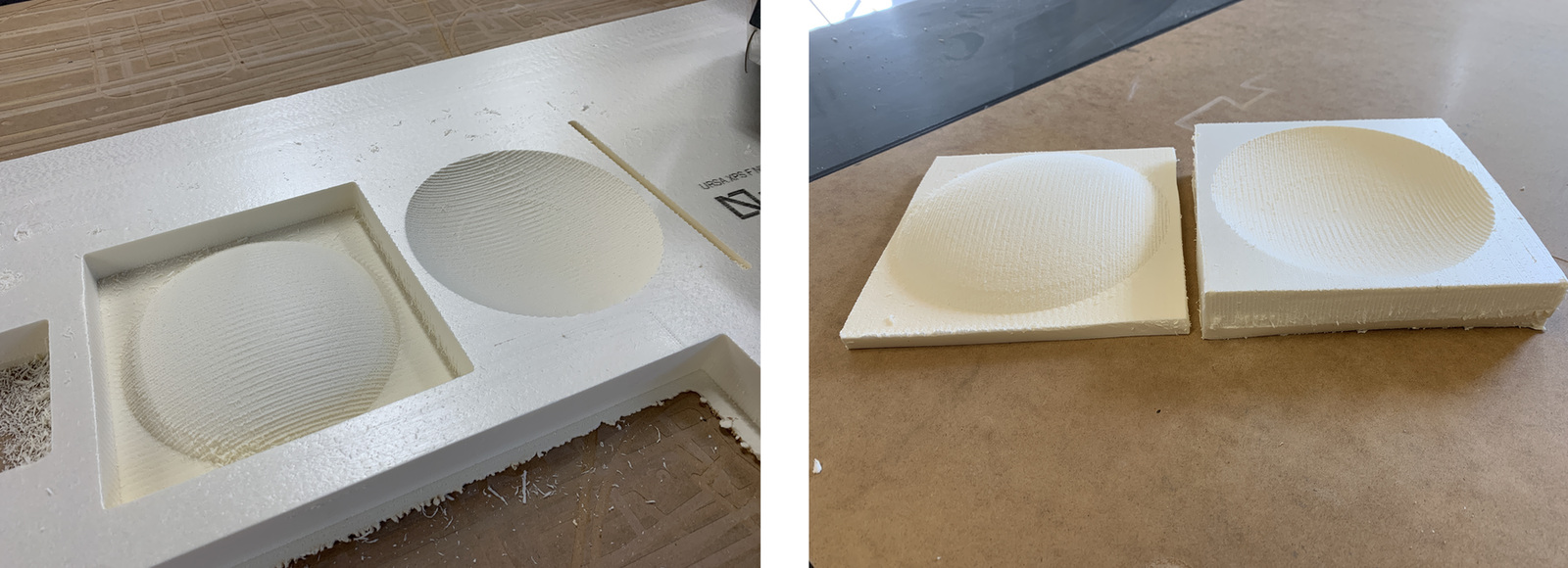
The next step is to cut the burlap and linen, for this I will use the laser cutter. Before I iron the fabrics on the textile vinyl sheet. Use the following parameters Vector: Power: 37% / Speed: 100% / Frequency: 1574 Hz ppi 400, but it fell short cutting. So increase the power and frequency, these are the correct parameters Vector: Power: 80% / Speed: 100% / Frequency: 3548 Hz ppi 400.
I cut three circles of linen (left) and three circles of burlap (right).
I make the coupons at the same time as the piece for my assignment, so I take advantage of the mixture of the epoxy resin and the vacuum bag. First, place the protective film to recover the molds and reuse them more times.
For the concave mold I use burlap and for the convex mold I use linen. 3 layers in each mold. To place each layer, I use a acrylic cut to size, with it I guide myself. To put the epoxy resin I use the brush.
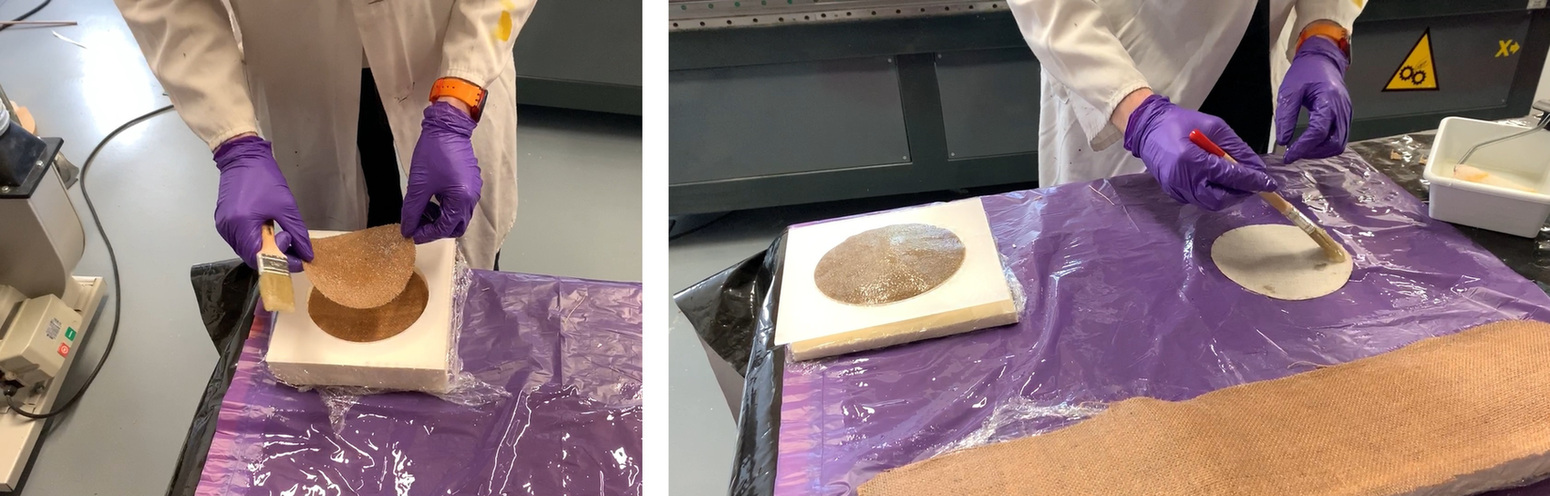
Next I put the release film and the absorption blanket. I put it in the vacuum bag and when I start to vacuum, the excess resin begins to filter through the real film. Is incredible.
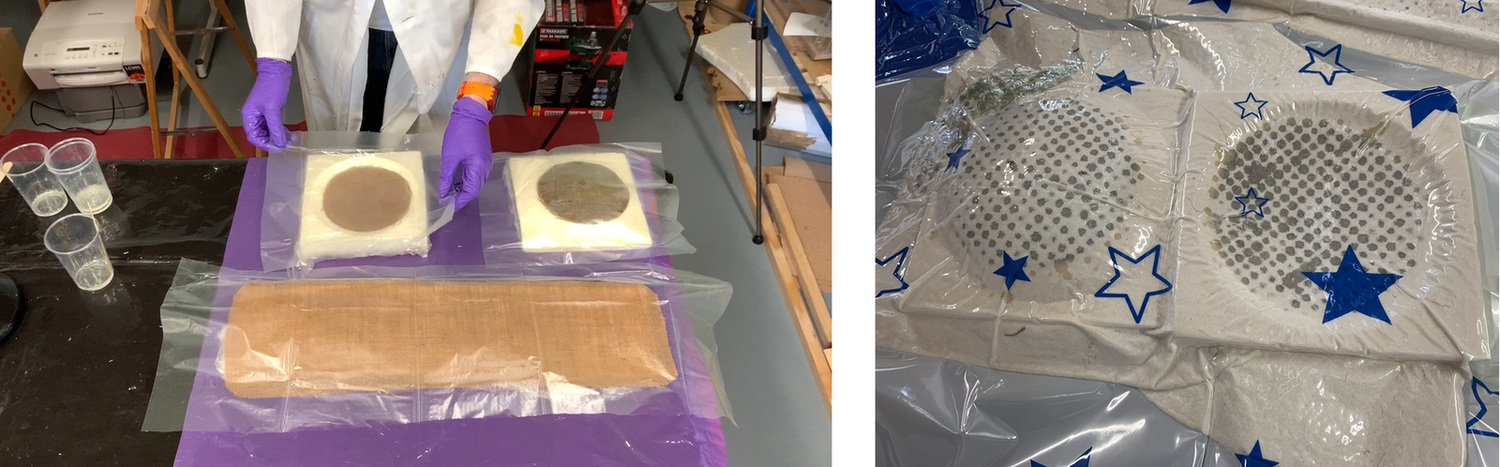
After 24 hours, I take the molds out of the vacuum bag. The first thing I notice is linen. There were three layers and it has become one and solid. I notice that in the concave area that is the one that went against the mold it is completely smooth, the outer area has some wrinkles.
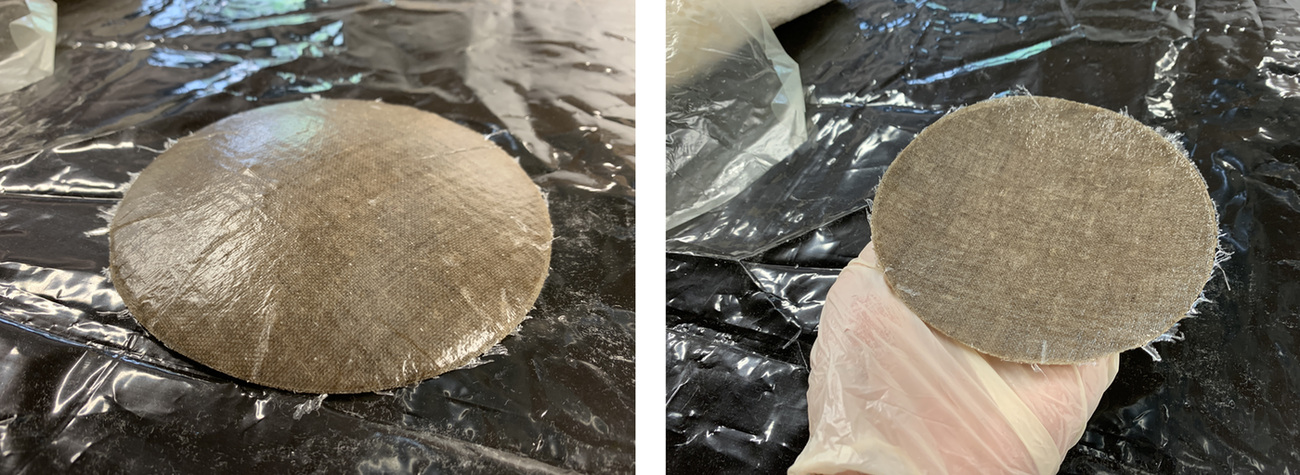
Video of the resistance test of the composite with linen. 💪
On the burlap, it also had three layers. And the same thing happens, in the mold area, the convex side is smooth and the outer area has some wrinkles.
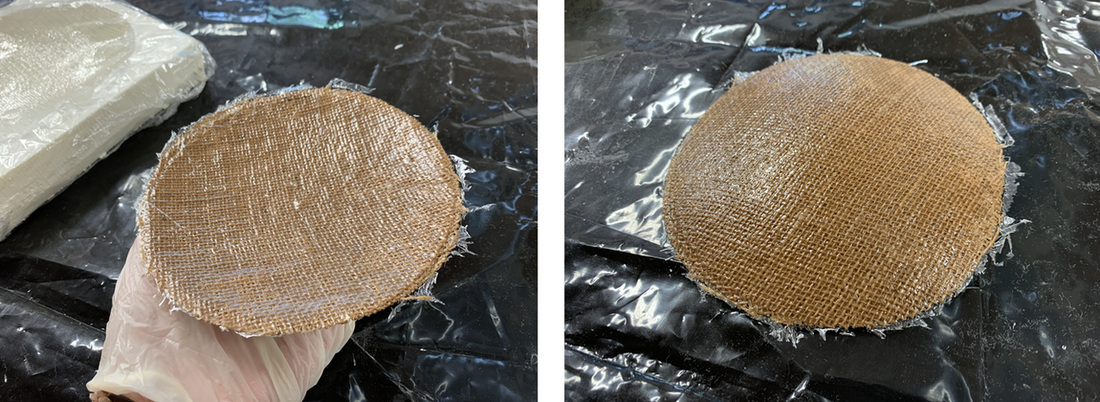
Video of the resistance test of the composite with burlap. 💪
Conclusions
The resistance and flexibility of the composites are incredible. In my case, for the application of the model creation, before we used the hand-carved polystyrene and glued paper to it. That made the models weigh a little more.
Now I also have the opportunity to preserve the 3D mold to repeat more landscapes and make the model much lighter and more resistant.
Final Project
Within Project Development I have a section where I make all the necessary composites for the model, if you click on the following link you can see the result.
Extra credit. Soft Robotics
During the year 2017, my instructor Nuria Robles carried out the Fabricademy. One of the things that surprised me the most were inflatables and soft robotics. During week 03 I made an inflatable and this week I wanted to try creating a flexible silicone gripper.
So following the soft robotics video class (minute 1:00:00) at Fabricademy taught by Dr. Lily Chambersand seeing the documentation of Montserrat Ciges (Fabricademy 2019) I start to investigate.I have also followed the advice of Adriana Cabrera. 😍
In Instructables I find a tutorial to create a Soft Robotic Gripper.
So the first thing I do is print the 3D mold, I use PETG because it holds more temperature than PLA in the oven. I take advantage of the fact that I have the Prusa I3 MK3S from the Fab Lab at home to print the piece and do the whole experience at home. The design I have taken from Instructables, and you can download it at the end of the assignment.
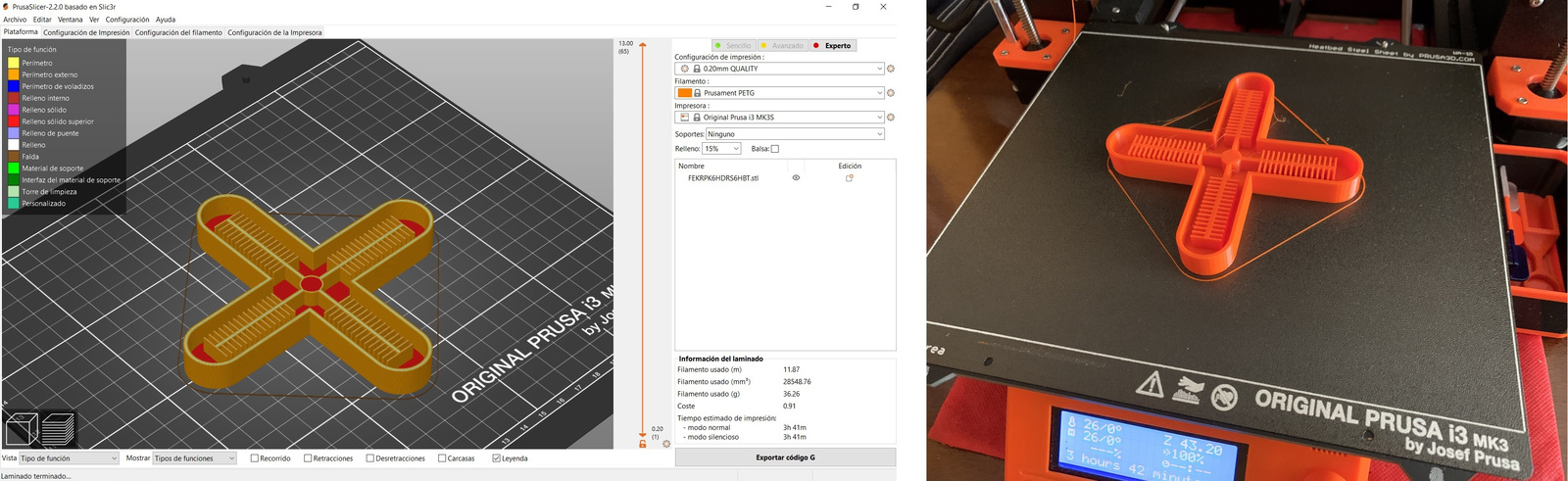
The next step is to prepare the silicone.
Ecoflex™ 00-30
- Super-soft, Addition Cure Silicone Rubbers.
- It has a pot life of 45 minutes and a cure of 4 hours.
- Within the security aspect, good ventilation is recommended, wearing safety glasses, vynil gloves and long sleeves. Wear vinyl gloves only. Latex gloves will inhibit the cure of the rubber. As we are in COVID-19 period, I use the mask. 😷
- Mix ratio is: 1 Part A : 1 Part B by weight or volume.
- Curing Allow rubber to cure a minimum of 4 hours at room temperature 23°C before demolding.
- Post Curing Optional... Post curing the mold will aid in quickly attaining maximum physical and performance properties. After curing at room temperature, expose the rubber to 176°F/80°C for 2 hours and 212°F/100°C for one hour. Allow mold to cool to room temperature before using.
- More information, here.
This is the result of mixing the two parts, it gives us a soft, transparent silicone. Next I make a summary with the safety pictograms. (Gloves, glasses, and an apron or long sleeve are mandatory.)
So once I have seen the characteristics of silicone, I prepare the work area (in this case the kitchen of my house, it will soon become a Lab 😂) with everything necessary.
Next I calculate the volume of the 3D mold, to prepare the proportion of silicone. I use water, the mold without it weighs 35 grams and with water weighs 74 grams.
Apart from the 3D mold, we must create a thin film so that when we remove the silicone, we will close the silicone with that thin film (I will create it on acrylic). For this I am going to have 50 grams of Part A and 50 grams of Part B.
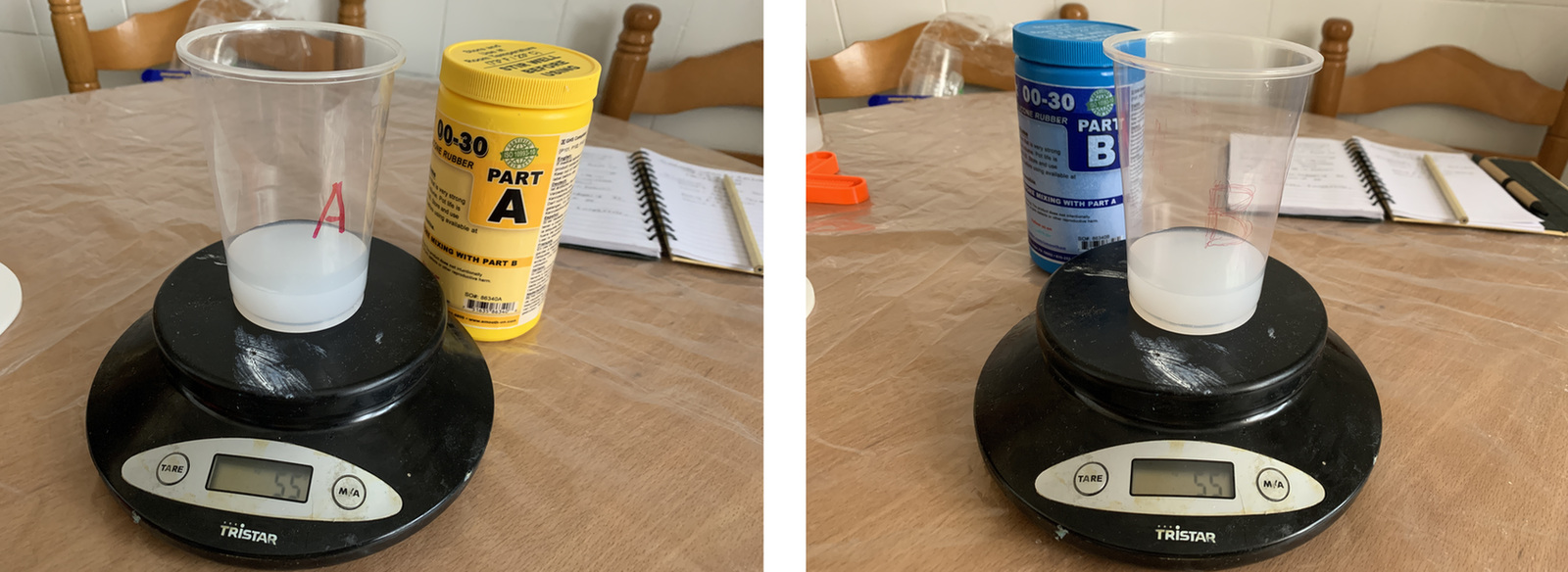
We will slowly deposit the silicone and hit the mold so that the bubbles come out. We will create a very thin film of silicone on a flat surface, in my case I use a acrylic.
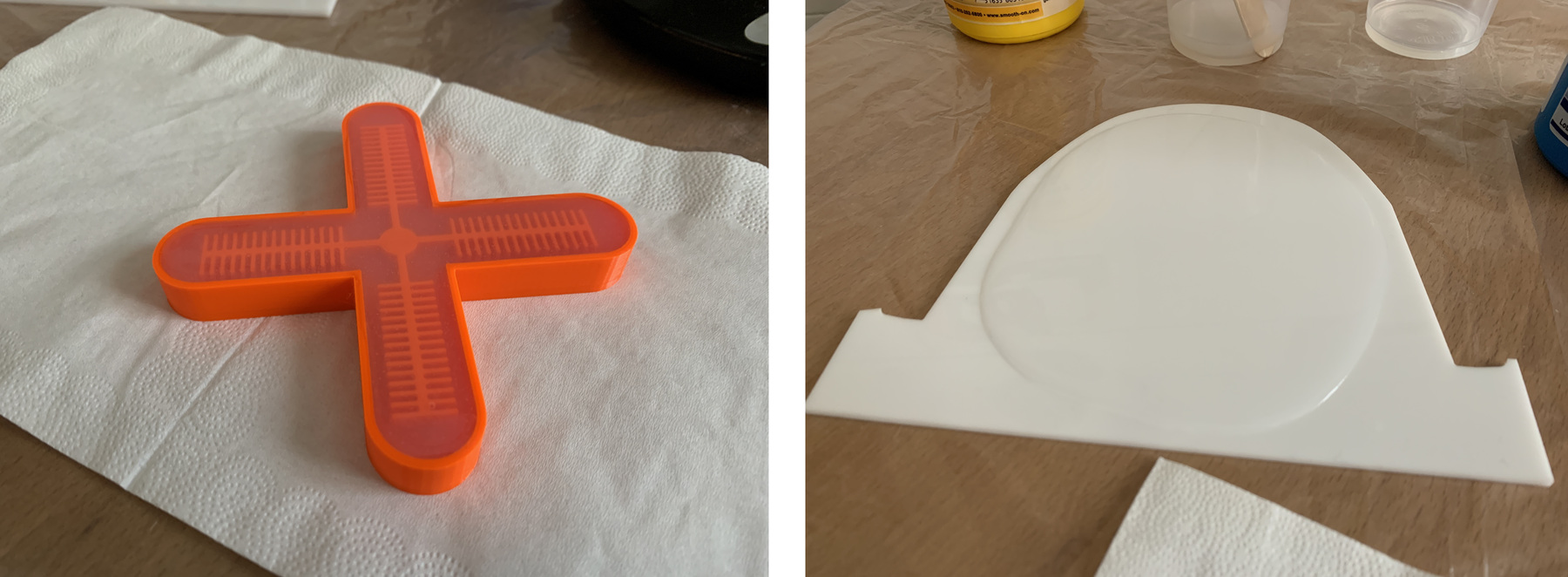
Following the assigment of Montserrat Ciges, I observe that he puts the two pieces to cure in the oven at 65 degrees and for 15 minutes. The oven of the Fab Lab León, the minimum temperature is 100 degrees, so I will try to put it alone for less than 10 minutes. 🔥🔥 But ... unfortunately I received more heat from the account, and I am not able to remove the silicone from the mold and even the PETG is soft. 😢 It is time to repeat the mold.

Once the process of creating the silicone has been repeated, this time I wait for it to cure naturally for 4 hours. And this is the result, incredible and has been perfect.
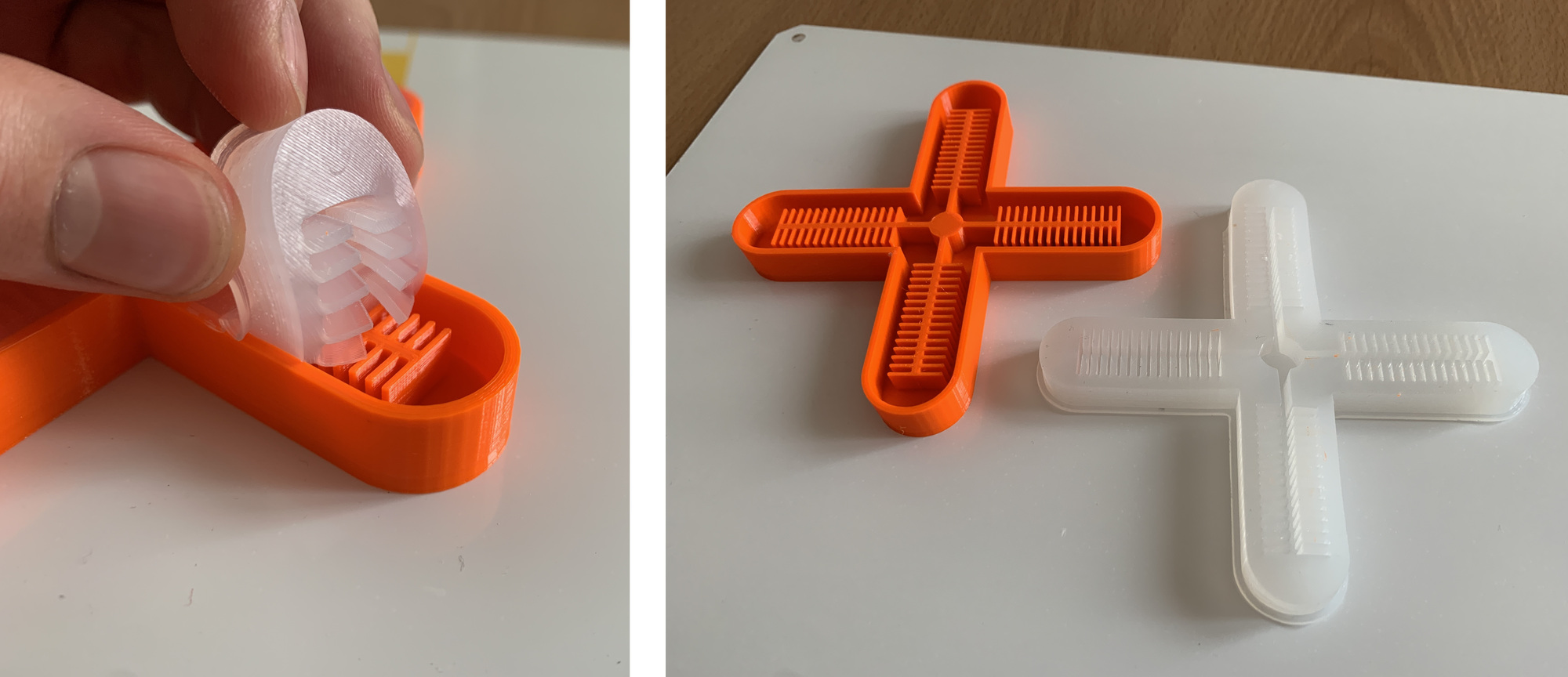
It is time to join the two parts, the flat part and the gripper. We make a small mixture of the silicone and put a thin layer on the base (1 mm or so). We place the gripper and try not to get too much silicone into the channels, but they will clog it. Then, with a brush we seal the two parts well, the flat part and the gripper. We will leave the pieces to cure for 4 hours.
Once the 4 hours have passed, we remove the silicone from the acrylic and verify that the two pieces have been completely sealed. I trim the excess silicone.
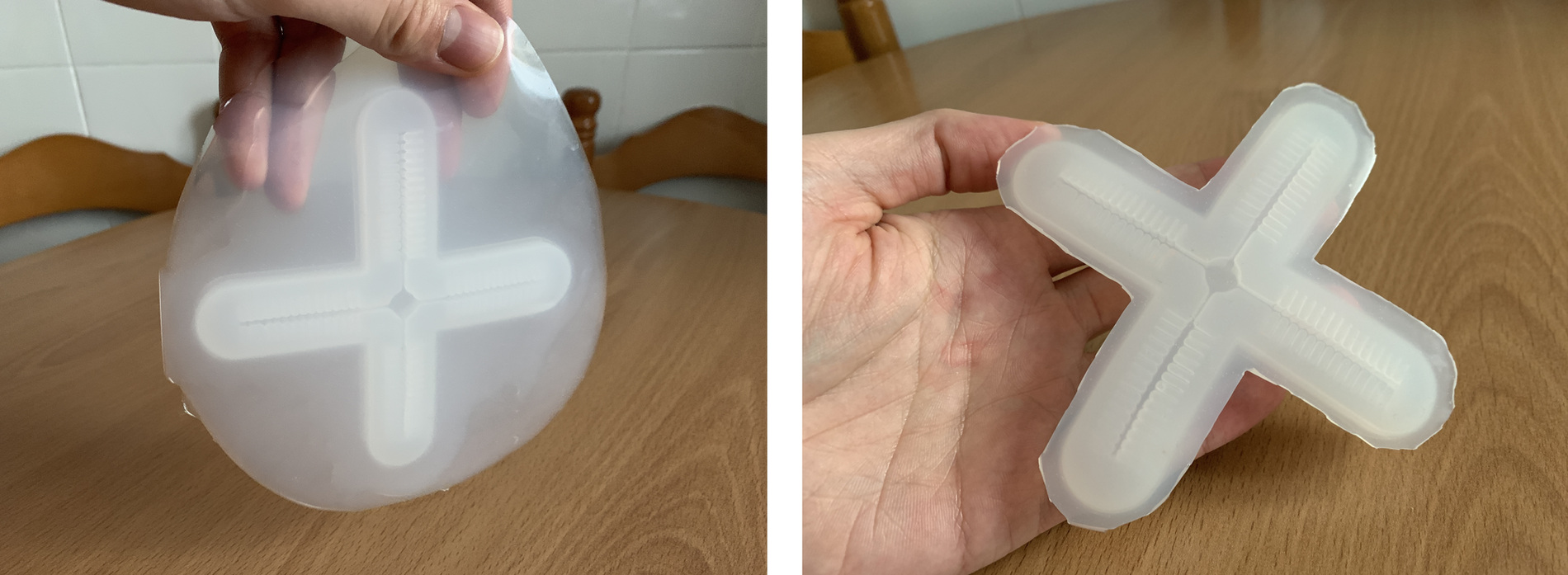
We make a small cut between the two legs of the gripper, to insert a tube (it is recommended to cut the tip in the shape of an arrow at 45 degrees). I place a non-return valve so that when I inflate with the pump the air is maintained.
This is the video, it's amazing how the legs unfold and inflate. It looks like an octopus or a jellyfish. Awesome. 🤩
26/08/2021
During Fab 16, Adriana Cabrera did a Soft Robotics workshop, I left the video link on Youtube. And seeing it made me want to create new molds again and I kept experimenting, especially with an electric pump and the Adrianino.
The first thing I do is with the acrylic and laser cutter I prepare a design similar to that of Montserrat Ciges. I'm also looking for other 3D printed designs, like Wendy Neale's. You can find the designs at the end of the page.
Once the acrylic molds are cut and assembled, I fill everything with silicone.
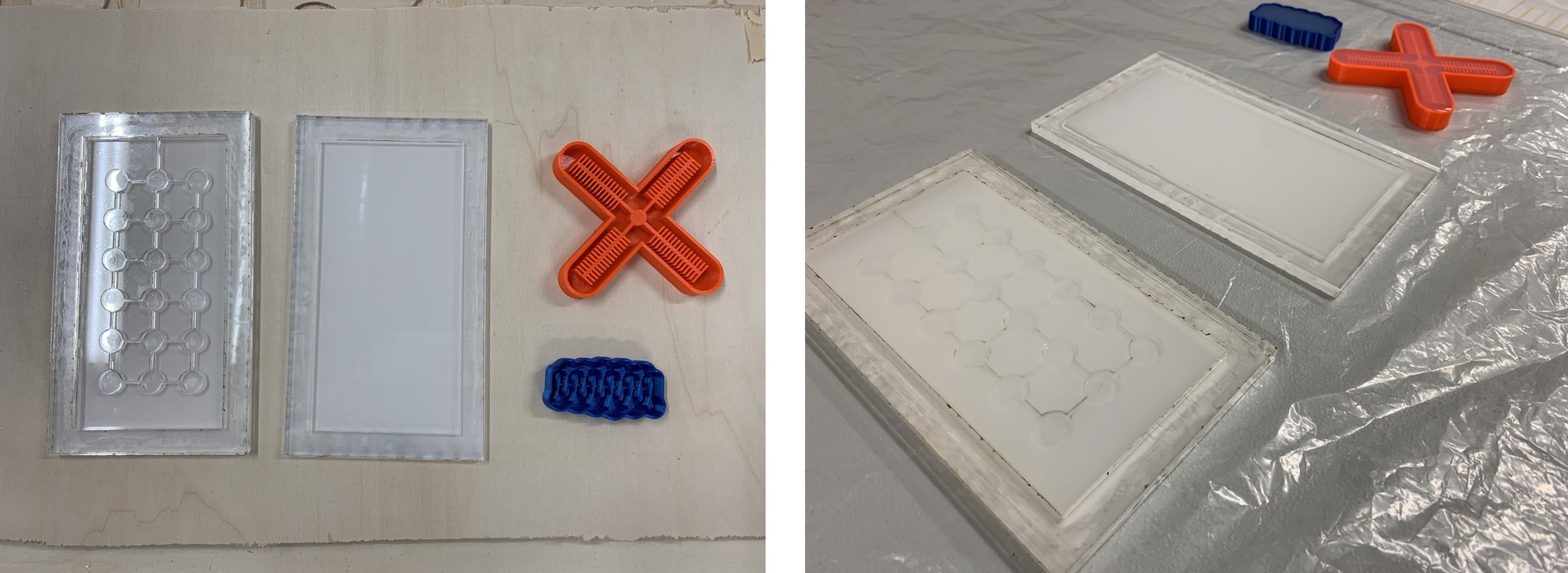
When the silicone dries, we remove it from the molds. With the acrylic molds I have created two parts of the mold, which will unite them. On the other hand, I have to place a thin silicone sheet on the 3D printed molds to complete the soft robotic.
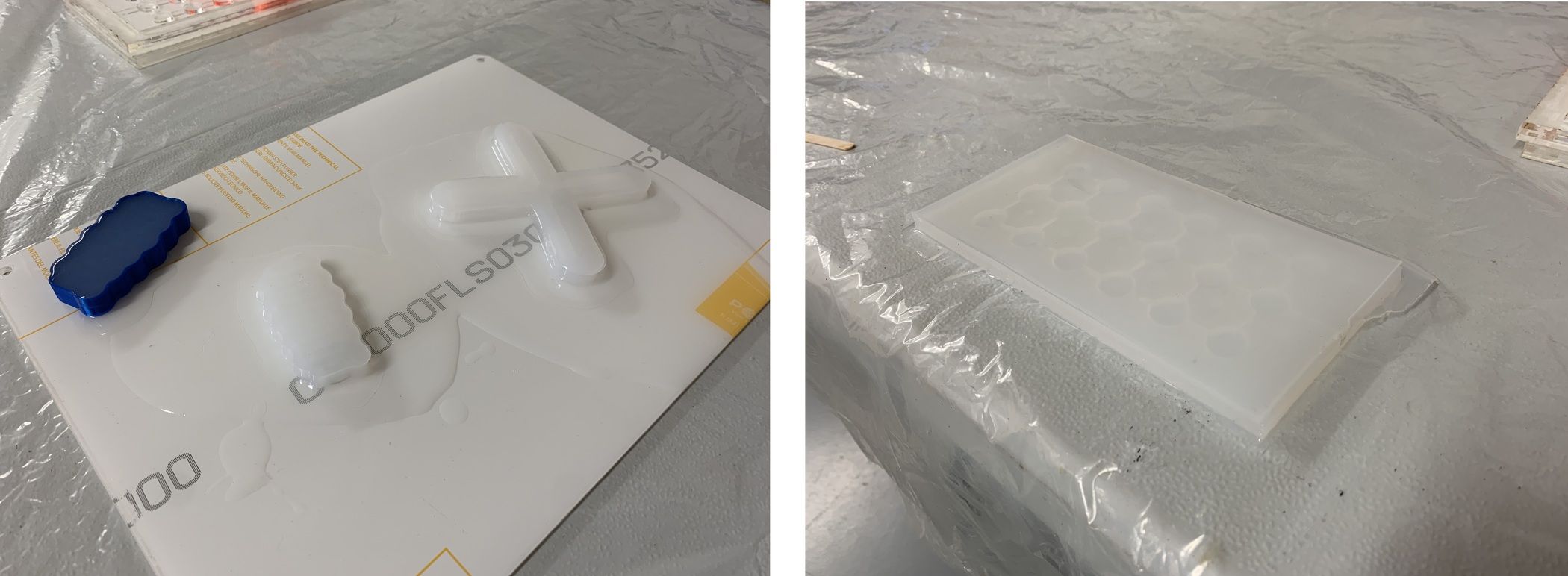
This is the end result of the new soft robotics. 🤗
Now it's time to test it with the pump and the Adrianino. Unfortunately, the large soft robotic has been perforated on one side and there are some channels that have been closed with the silicone from both sides. 😭😭
With the 3D printed mold, designed by Wendy, it works. 😍😍
Review of the class
During the review of this class I volunteered with the composites and soft robotics in the minute 1:19:00. 😊
20200527 wildcard review from Academany on Vimeo.
Files
Find below the files that I made for this assignment.