Week 15. Applications and Implications. My final project is a prototype of a CNC controlled Electrical Discharge Machining (EDM) wire cutter. In this prototype, it can be modelled with a hot wire foam cutter. Two stepper motors move the object and the string stays in place at the bottom. EDM machines can cut very hard materials without stress to the moving parts, therefore stepper motors moving the object will not have to be especially strong. The object moves in the directions of X-axis and Y-axis. Rotational A-axis could be added if there is time. It will be designed as much as possible to be scalable to the bigger machine just growing the size of parts.
What will it do?
The prototype can be used as a foam cutter for example for modelling and casting objects. It should be able to cut fairly precise 2D-shapes, including sharp corners and holes with bores or models for cogs.Who's done that beforehand?
In the end, I’m hoping to sort of combine these three MIT-projects: Machines that make: cardboard stages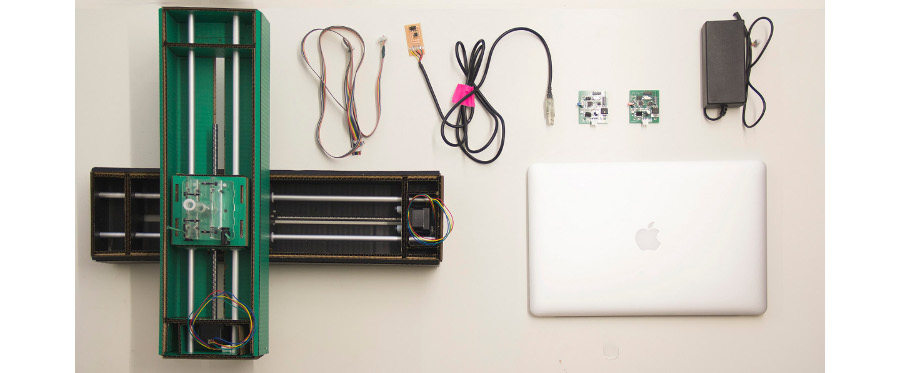
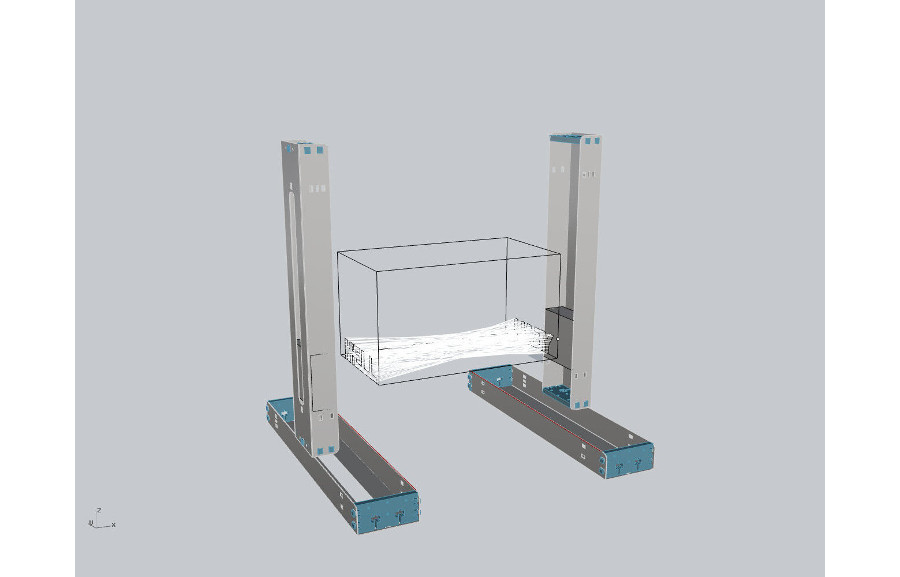
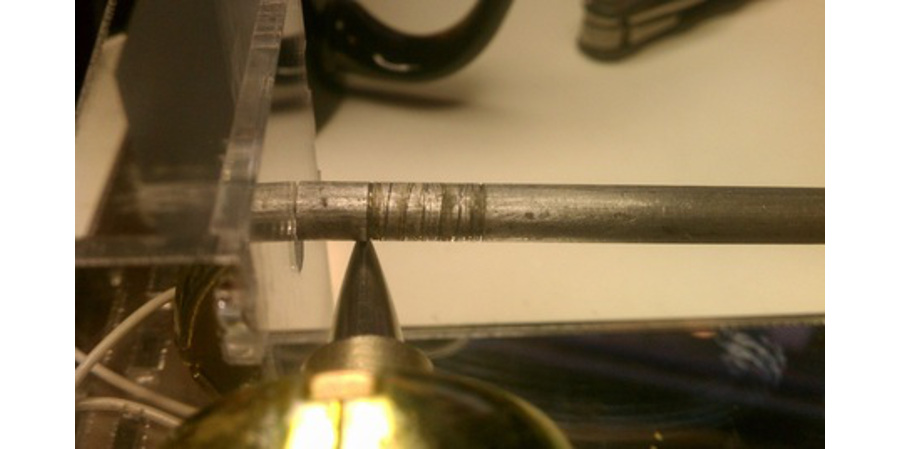
What materials and components will be required?
In terms of material, the project requires in minimum, mechanical and electrical parts for two axis CNC-machine and appropriate power supply for the hot wire.Where will they come from?
We are trying to recycle all the materials and electronics as much as possible. I’m hoping to use the modules of the machine building week and power supplies found in the lab.How much will it cost?
If developed further, the parts for the DIY EDM machine are estimated to 500 euro, parts to move the wire while cutting would be around 100 euro and the alloy wire would be around 250 euro. Sharing the costs would have to be discussed.What parts and systems will be made?
The machine requires mechanical parts: two linear axis and holders for them as well as holders for the wire and electrical parts and/or connections.What process will be used?
Mechanical parts would require either laser cutter or wood router, and/or 3D-printer. Electronic parts probably need some custom made PCB’s and the system needs to be programmed.What tasks need to be completed?
Supplies must be acquired. Mechanical and electronic parts must be designed and assembled, MCU’s must be programmed and the machine must be built and tested.What questions need to be answered?
First questions are mechanical. Since the machine building week is not done yet, I’m out of scope for this part. Also firmwares, tooling paths for such machine etc. needs to be figured out. If prototyping is continued to EDM, the electrical issues rise too. In this case the current used to plasma cutting is quite a lot. Also reversing the machine back needs to be taken care of in the final product. Either the current must be cut or wire reversed a little for this action not to have extra sparcs and/or break the wire. Wire movements and tighteners should be designed or bought.What is the schedule?
- 1. week: learn to built machines
- 2. week: design the dissemination of the product (if time left, design the first prototype)
- 3. week: built the machine
- 4. week: final presentation (if time left, develop the product further)