Molding and casting
This week's assignment was molding and casting.
The process to make it involved a number of steps and doing most of them for the first time, we couldn't help to think that it was going to fail in one of them and render the whole asignment wrong.
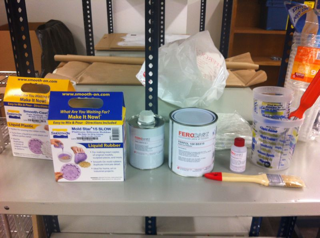
First one was buying materials and some equipment.
The stock that we wanted to mill was wax, but unfortunately there was no machanizable wax available, so the only thing left was making it. The material used for molding was silicone, of the smooth-on brand, Mold-star 15 (slow) that, at least in paper, seemed right as it didn't need degaussing and special equipment for it. Curing time was acceptable. Casting was done with the Smooth-cast 300 which was recommended and is very used in makers community. We also got the equipment for making the wax.
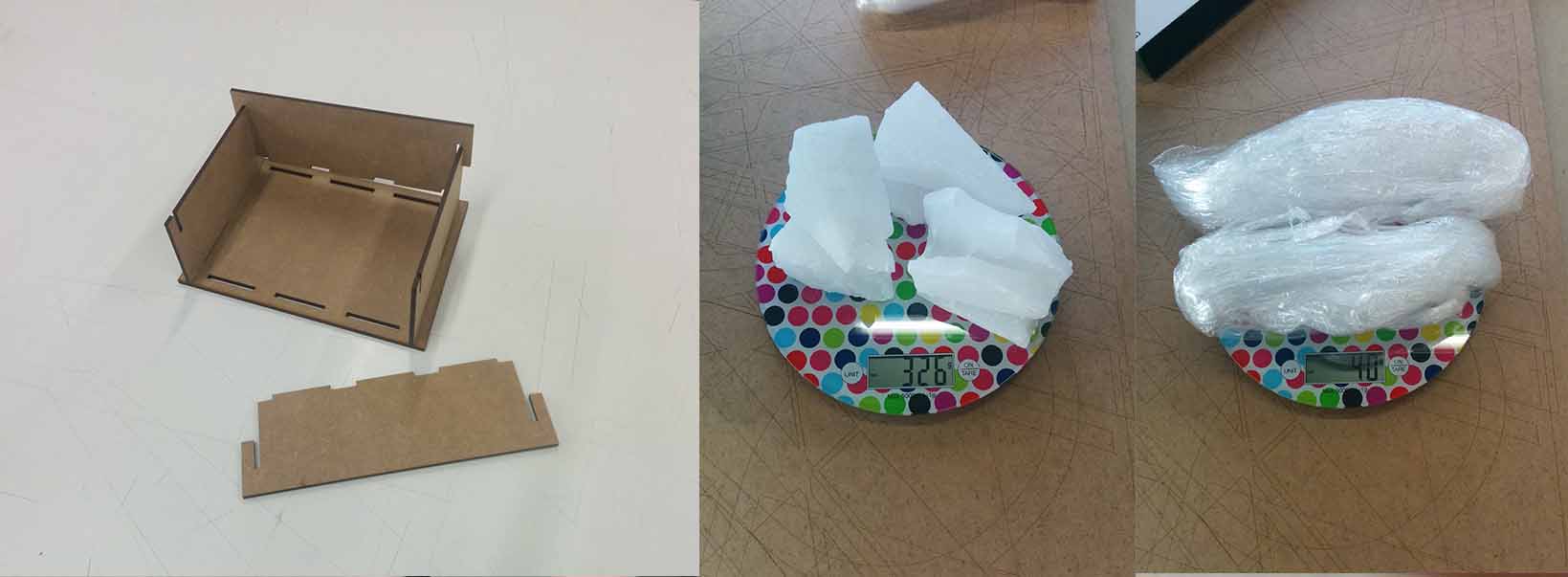
The process of making the wax was surprisingly simple and quite straight forward. Yoy need some parafine, some low density polyetilene and something used to give the mix some color to be able to distingsh fine features. The mix of the parafine and polyetilene is 20% max of polyetilene of the amount you put of parafine. We made 2 diferent mixtures to check the properties, one 20% and the other 15% and found that the 15% mixture was more homogenic.
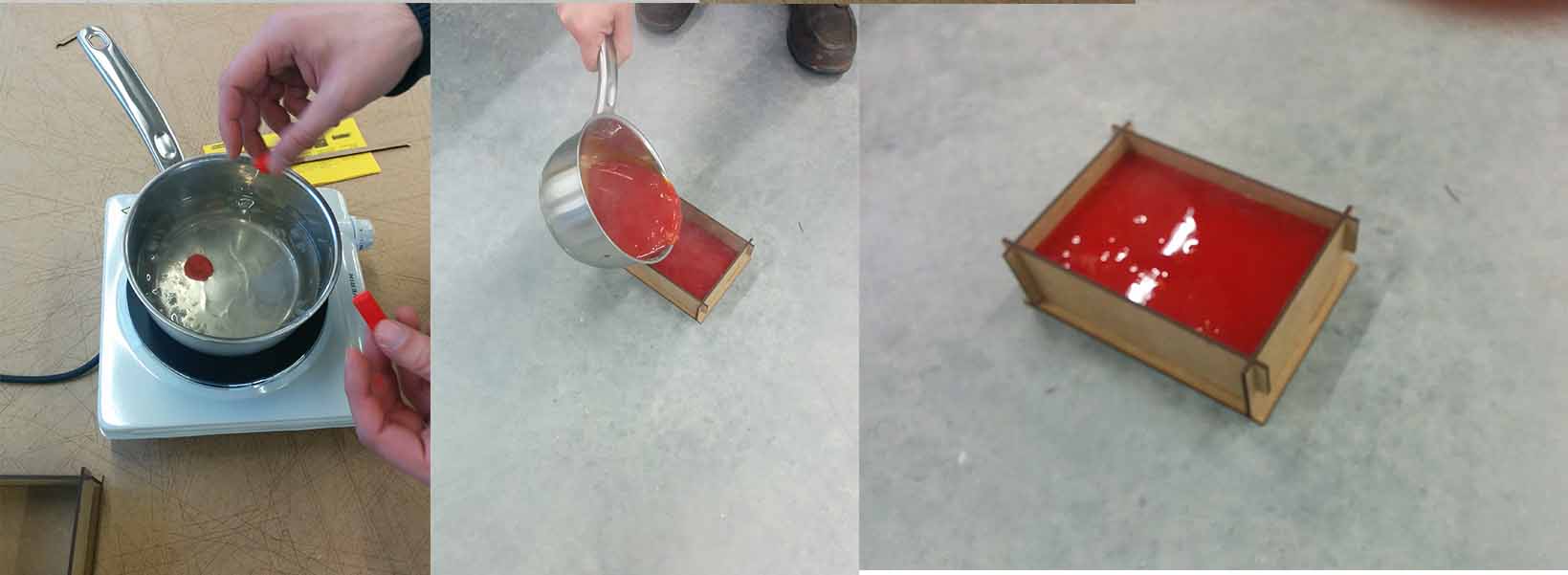
After disolving both ingredients, you have to add the colorant. We used Manley crayons, and the results were satisfactory. Final measures used for the mix were:
- 200 gr. of parafine
- 30 gr. of LD-PE
- 1 Manley crayon (5 gr.)
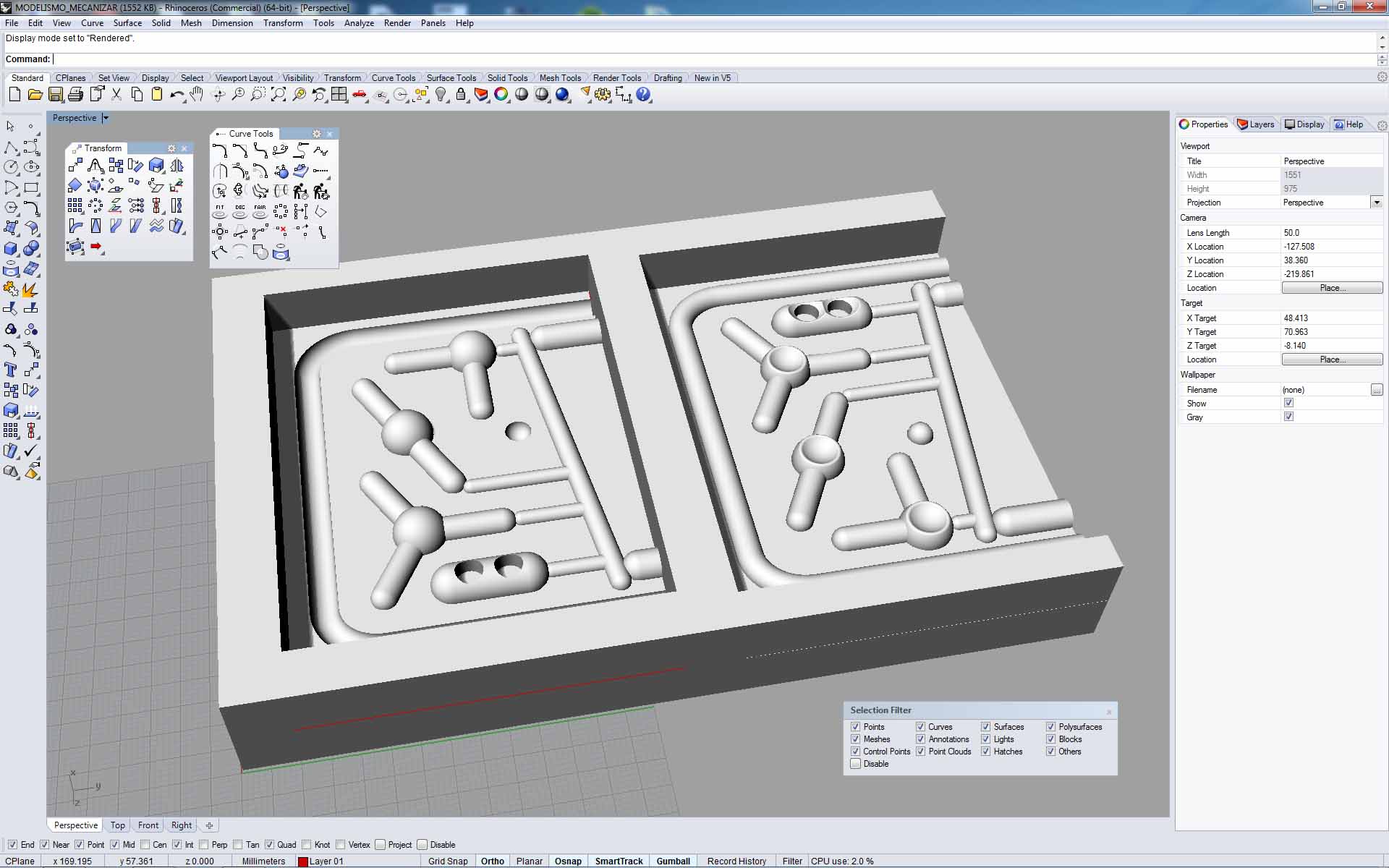
The parts I'm designing are some connections to make a construction set with straws. Design is quite simple and mostly done for casting purpouses and similar to injection molded parts similar to, for example, Airfix kits.
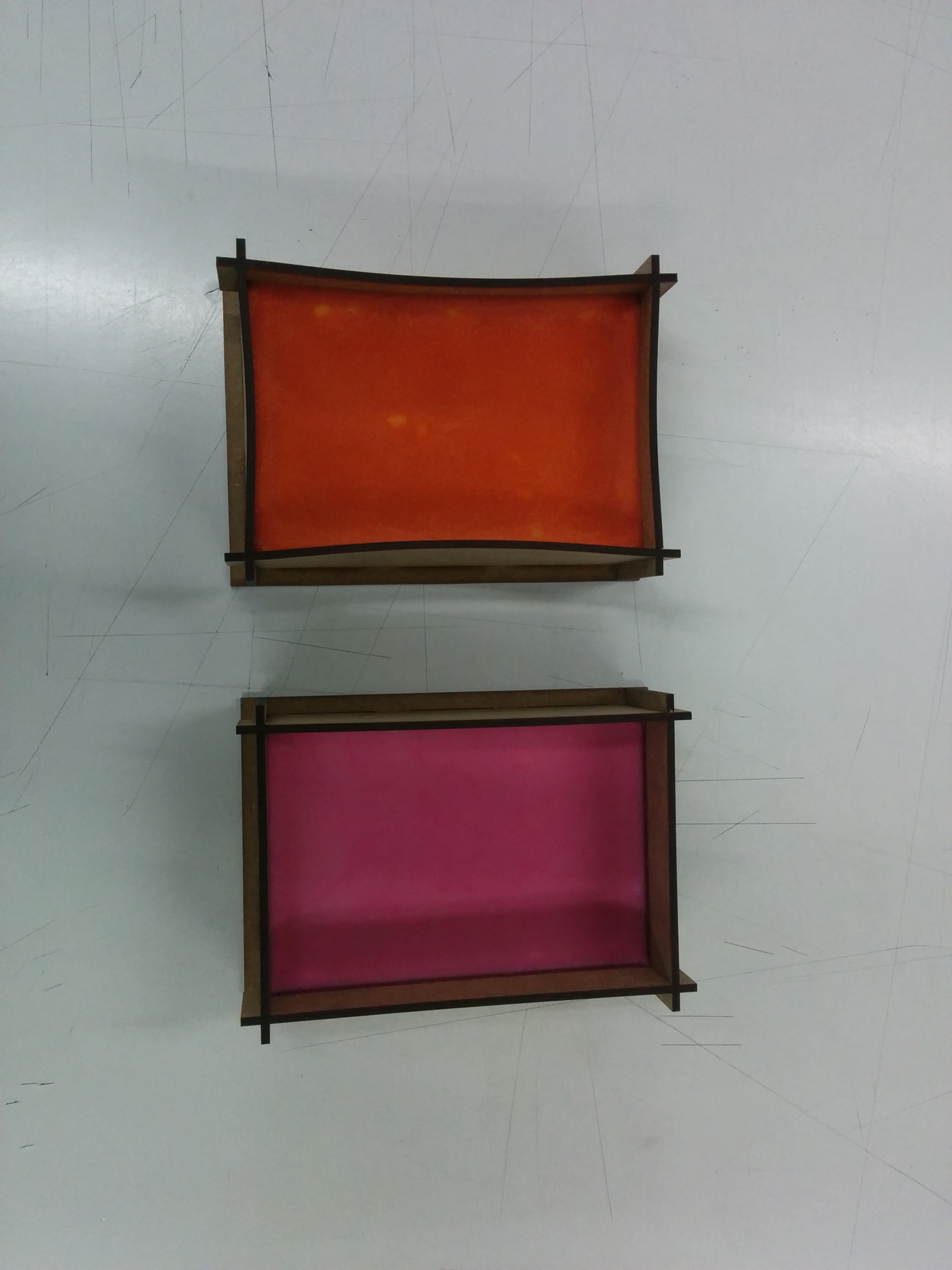
Pouring of the mix was done in a container made of 3mm. MDF walls, we observed severe retraction and consider that it would be recommended to use, at least 1cm. walls, specially if you want to make bigger volumes.
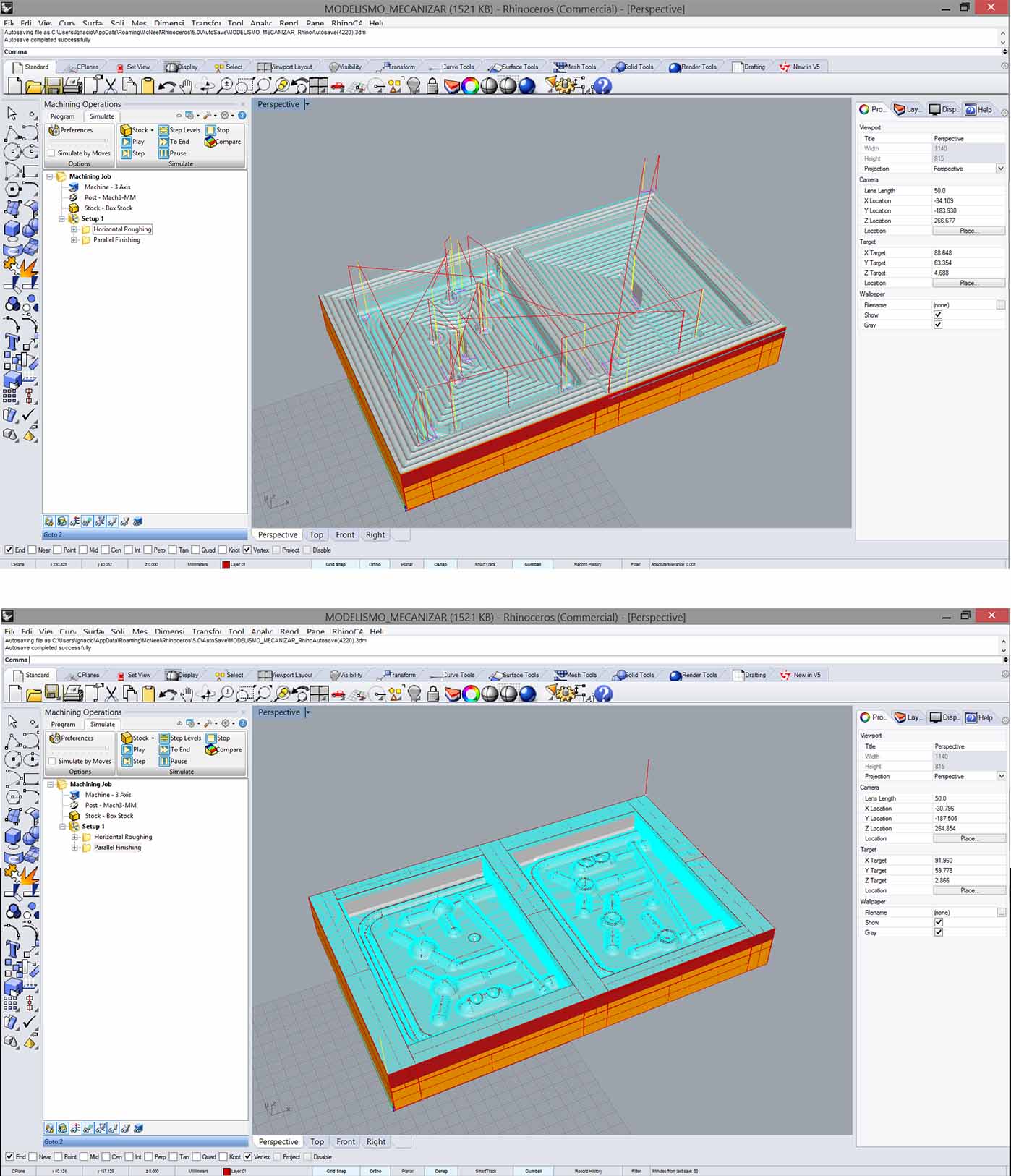
Then we milled the wax with the FH 250, it is the big CNC Mill in the Lab. We wanted to use this one to see how acurate was and also to test 3D milling from RhinoCam for 3D milling.
Options for milling in RhinoCam are good enough for 3 axis CNC routers. We made to toolpaths, one for roughing and the other one for finishing. The roughing one was with 5 mm. z-step layers and 80% overlap of the bit. Speeds were 1500 mm/s. Milling time was 10 minutes. Finishing toolpath had 10% bit overlap and speeds were also 1500 mm/s. Also assemble the top board and we have the finished piece.

After cleaning the wax, we can see how the finishing is very good, in fact the only problem was using a 3mm. ball bit. Next time we will faithfully trust recommendations, because feature detail in when parts meet the wall is missing because of the bit nature.
Then, we mix the silicone mold components. Equal parts as detailed in the instructions.
And pour it into the wax. We also tested it with a 2 euros coin, mostly to check curing times with it, instead in the assigment parts. Also to test it with alloys and much fimner engraved detail. Nothing to do with counterfeiting... We wait the whole night to check results.
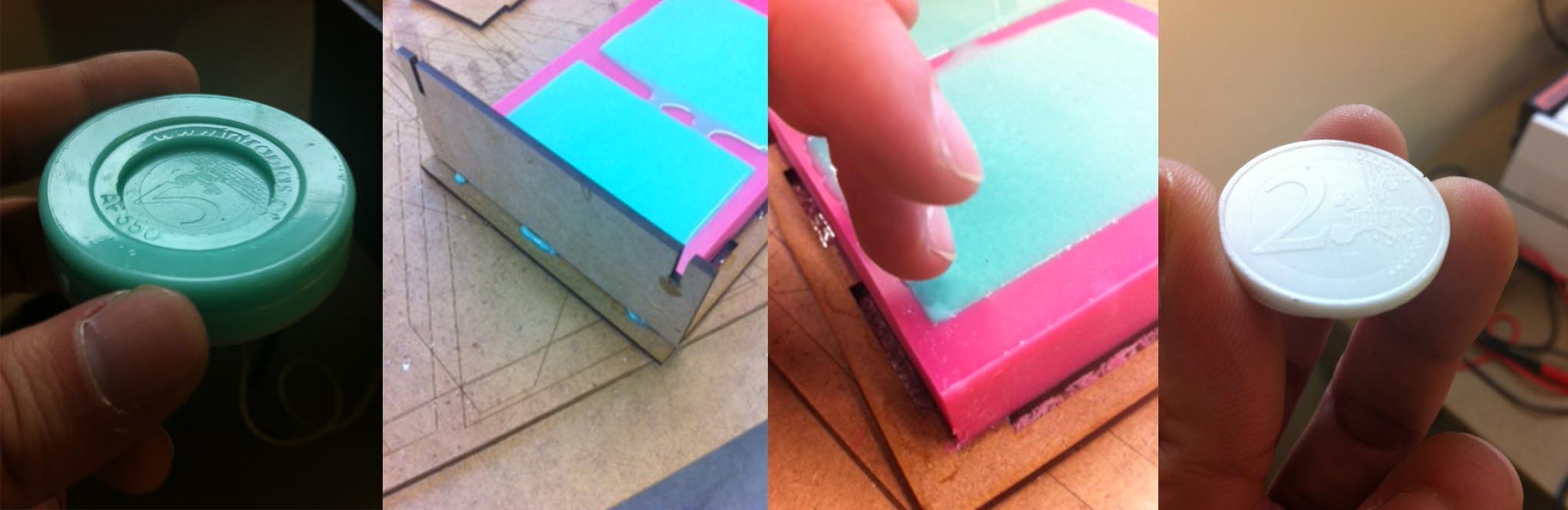
First we checked the curing of the coin. Perfect, feature detail was amazing. No problems. Green lights everywhere.
Then we tried to demold the assigment parts and right after taking out the MDF I could see TROUBLE. Mold has not cured correctly. Even the most superficial layers are uncured.
The only explanation we could see was bad stirring and differential mixing done in the pouring process. Let's review it... SAME MIX. Daniel's parts were poured first, his parts could be demolded, but there were lots of bubbles and the inside layer was not cured. My parts, demolding process couldn't even be done. Test coin, perfectly demolded, no bubbles and perfect features. So the only explanation we could give is that when we poured the coin, little mix was left, so pouring was done at a smaller flow rate and differential mixing was less prominent. That's our explanation but we are open to sugestions.
As the only correct mold we have is the Coin test one, we tried casting on it to check problems we could have further ahead when we revisit our parts. Everything seems fine.