Composites
This week we are building composites by adding tension and compression strength materials together. Compression materials consisted of alternating core materials (foam, MDF and OSB boards) as well as Epoxy 105. The compression materials were cut in sets of two; one for composite and the other to serve as a constant. For the tension material, we used linen cloth. Instead of being too creative with this project I decided to start with a simple task in order to familiarize myself with the composite process. I decided to simply composite a wood core with linen and mixed Epoxy 105. Nothing special, but the end result would be me having experience for the next composite project.
To begin, I designed a simple 6" by 12" board in PartWorks Software that would serve as the dimensions for each of my composite cores. I first cut the foam boards after.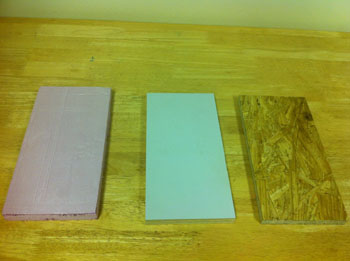 I then designed my linen fiber outline in Coral Draw. 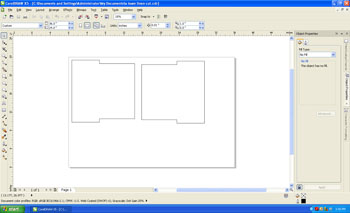 With the laser cutter, I then cut out the linen design after first testing it's dimensions on paper. After the linen design was tested to fit, I then cut out an appropriate piece of release fabric and breather material. After my composite package was complete, I designed my vacuum bag which consisted of vacuum durable plastic, mastic tape for an airtight seal, and one sized slit on the topside of the bag.
I then repeated the same preparation steps for the OSB and MDF boards. After my linen was cut for each of the core pieces, I gathered my materials needed for the composite process.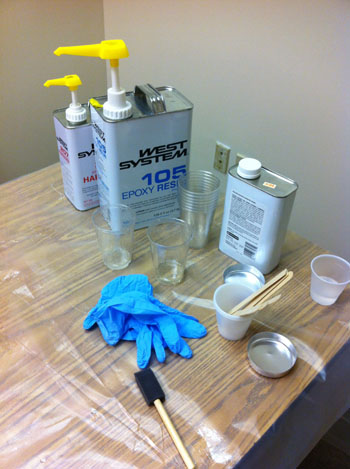 My materials consisted of Epoxy 105, Clear Hardener 207, Acetone, rubber gloves, face mask, eye wear, plastic cups for mixing, 3 mini pumps for equal distribution, foam brushes, vacuum air compressor, my composite packages (core material, vacuum bag, release fabric, etc.). The process was a messy one but my resulting samples improved from one to the next.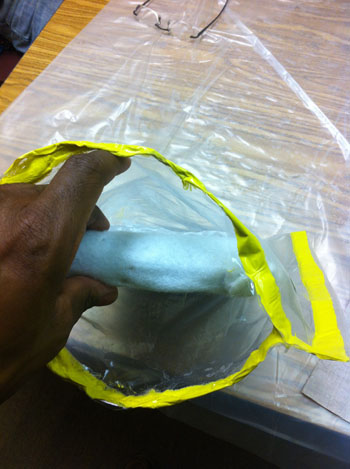 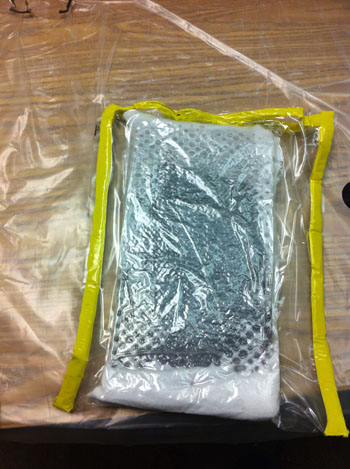 I also had a few small air ways around the suction cup that I recognized during my first attempt and so I used mastic to help seal them up. 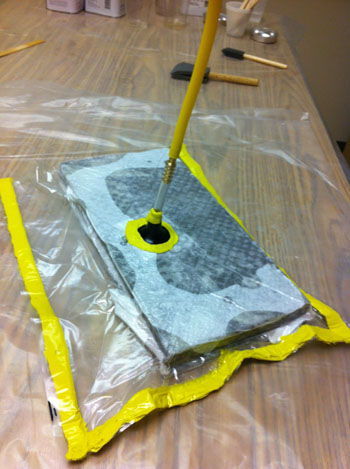 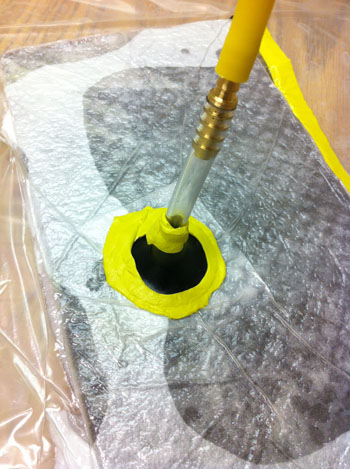 The mastic helped the vacuum by blocking off added air that would seep in like it did on my first attempt. The result was a more compact and defined finish. 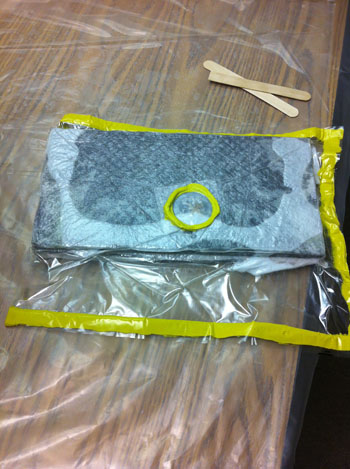 The composite process for the foam was the most difficult, maybe because it was the first attempt or maybe because the epoxy and hardener wouldn't stick as easily as I would have liked. After the first attempt the process became a bit easier and the resulting composites matched their original shape better than the first. Either way
the resulting pieces were apparently stronger than their original piece. 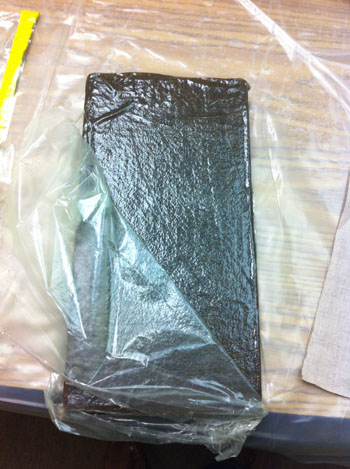 This experience of the composite process helped my understanding of what compositing pieces can accomplish. I feel confident enough to make a design and create it using composite materials knowing what to expect as a result. The laminate feature is not only durable but is also water resistant and can be refurbished if needed. 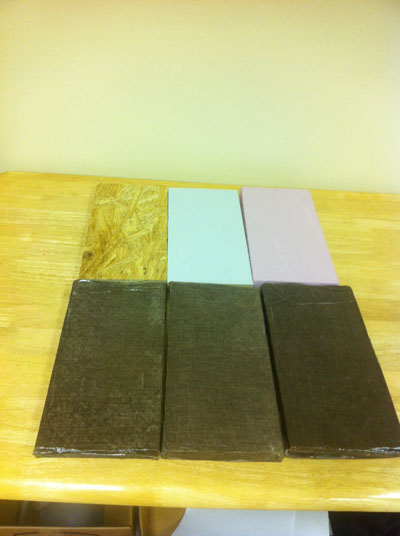 I really look forward to my next composite project.
|