Week 9: Molding and Casting
Goal: Design a 3D mold, machine it, and cast parts from it.
Step 1: getting the machinable wax
Let's get machinable wax from the following components: Paraffin, Polyethylene and crayons.
Quantities :
Pure paraffin. 320 gr.
LDPE (polyethylene) 64 gr.
1 One coloured wax crayon ( Manley)
First, heat the wax until fully melted, then I gradually add the LDPE. I used the plastic used in the kitchen for wrapping food. Polyethylene needs more time to dissolve.
PROBLEM: The amount of LDPEthat I have used is excessive, and the last parts of polyethylene have not dissolved properly. I read this problem appears spending 20% polyethylene or more in the mix, when the 15% is more than enough for a good result (in the FabLab we did the two mixes, mine just over 20% and my partner's with something more than 15% and his result was better). However wax didn't have problems for drilling.
Once melted the LDPE I added a piece of wax crayon for getting the color we want. This last step is pretty fast, if you spend too much time the smoke starts to smell burnt.
Then pour the wax into the form (I built one in DMF wood cut with laser with the dimensions needed) and let it cool.
IMPORTANT: hot wax produces too much smoke and odors, work in a well ventilated area.
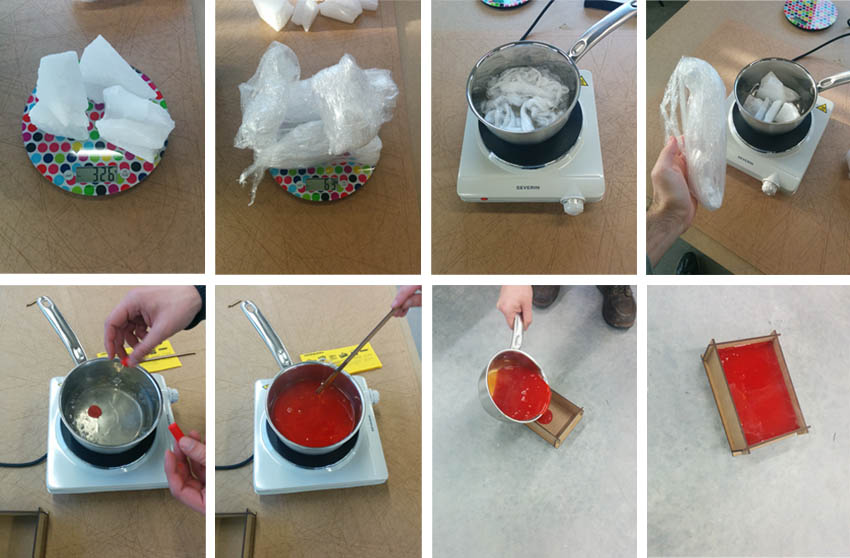
Step 2: designing the model in CAD
The piece I am making is a a spinning top. I downloaded the 3D model from the 3D Warehouse og Google Sketchup and then I worked in Rhinoceros to build the entire piece.
IMPORTANT: you have to design the part in positive, including attachments and a cannula to enter the rubber in the final process. |
|
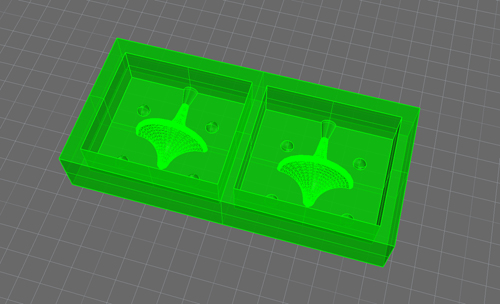 |
Step 3: Drilling the wax
To mill the piece instead of the Modela I used large format drill machine because I wanted to try using RhinoCAM to set machining parameters.
IMPORTANT: My piece of wax has shrunk too much in cooling process, so I have to pay attention to calibrate the Z axis because it is not the same in the center of the piece as in the ends.
I have used a 3mm Ball Nose drill with speed of 1500 mm / min because all my surfaces are curved. The only flat surface is the juncture of the two countermoulds, so it is not important how the finish look in this part.
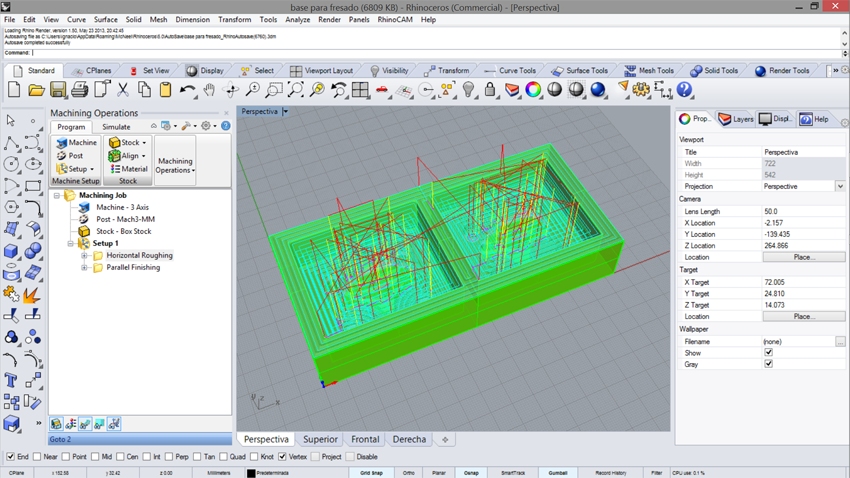
Step 4: Countermould in Silicone
To make the countermould in silicone I used the Smooth-om material in 2 components. Mix and stir the mix. Then, fill the positive mold of wax with the liquid and leave it curing for 4 hours. |
|
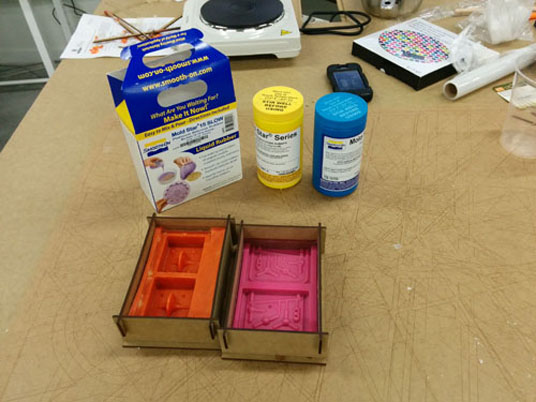 |
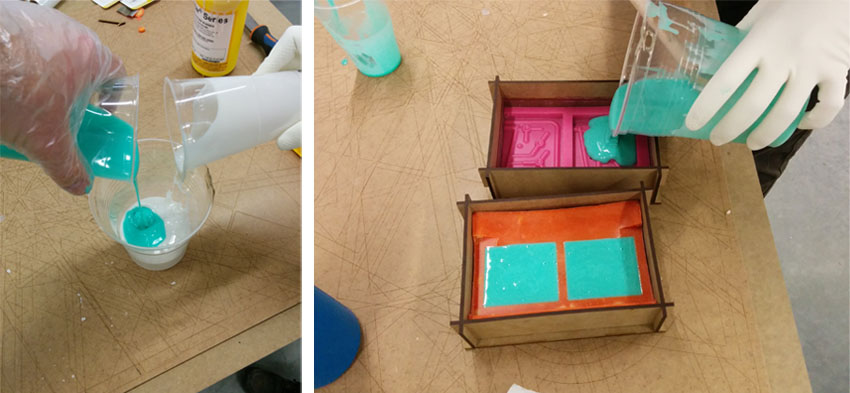
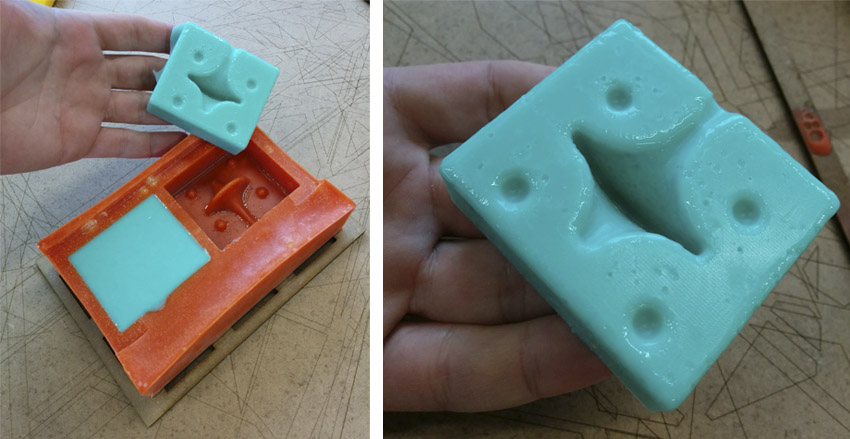
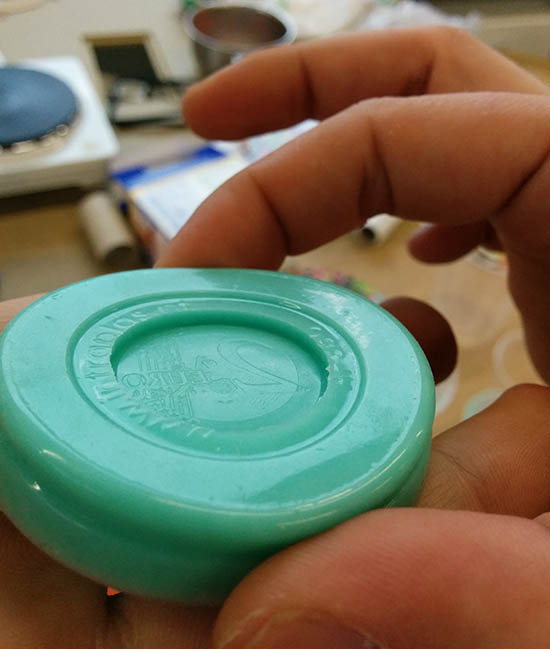 |
|
PROBLEM: after waitting more than 12 hours, the molds didn't curate well. We don't understand exactly where is the problems because in our FabLab we did 3 molds with the same mix of liquid and we get 3 different results. In my assignment, the mold outside looks good, but the layer in contact with the wax is not cured and with a lot of bubbles. The secon mold belong to my partner Ignacio Prieto, and his mold was very liquid, despite been more narrow than mine, when you touch the mold you can feel it more liquid. Finally, we approach the rest of mix making molding a coin, and the result this morning was perfect.
So we can't find a logic in this process because is not consecutive; the first try is bad, the second is the worst an the third is good.
We will try to repeat the experiment and find a solution. |
|