STEP 1: Separate the broken part of the umbrella and scan it in 3D
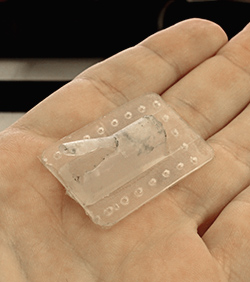 |
|
First to do is get the broken piece, separating it of the umbrella to scan it. For th 3D scanning I use the Roland Modela MDX-20 wich serves both, as 3D scan and milling.
This type of scanner has the limit of scanning by points, and only those accessible in the Z axis, so the holes of the workpiece will not appear in the digital model. After getting the scanned points, the software make a reconstruction, generating a mesho formed by the scanned points.
To make the scan I used Dr. Picza software, provided by Roland.
|
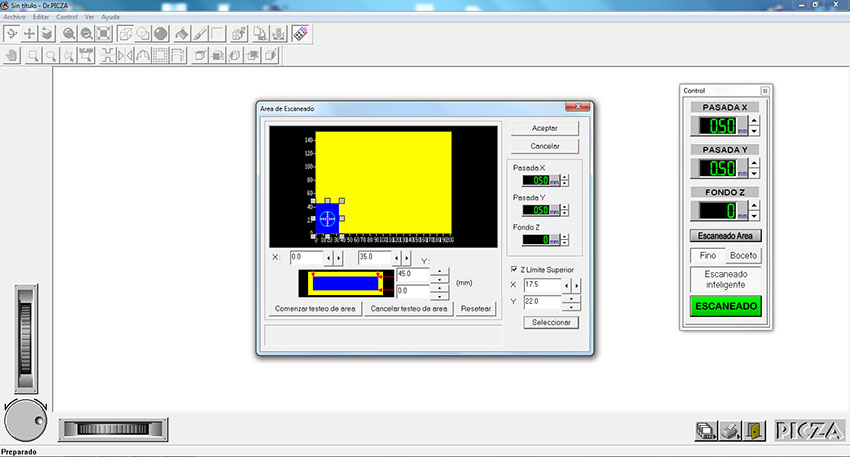
In the software we chose the scan area to reduce the scan time by limiting the area where the piece is placed. As my piece is small, the limits are 45 mm in Y axis and 35mm in X axis.
Now regulate the separation of the steps in X and Y to detect the scanned points. The problem with this type of scanner is the time it takes to perform a scan. A closer spacing means more accurately but more time scanning. For such a small piece (45x35x15 mm), making separation of 0.3 mm step, the scan took more than 4 hours!!! So I finally chose a 0.5 mm step and the scan spent 1 hour.
To reduce the scan time I manually indicate in the software where the highest point in Z axis is to avoid wasting time scanning air. In my case this point is in 17.5X 22Y coordinates.
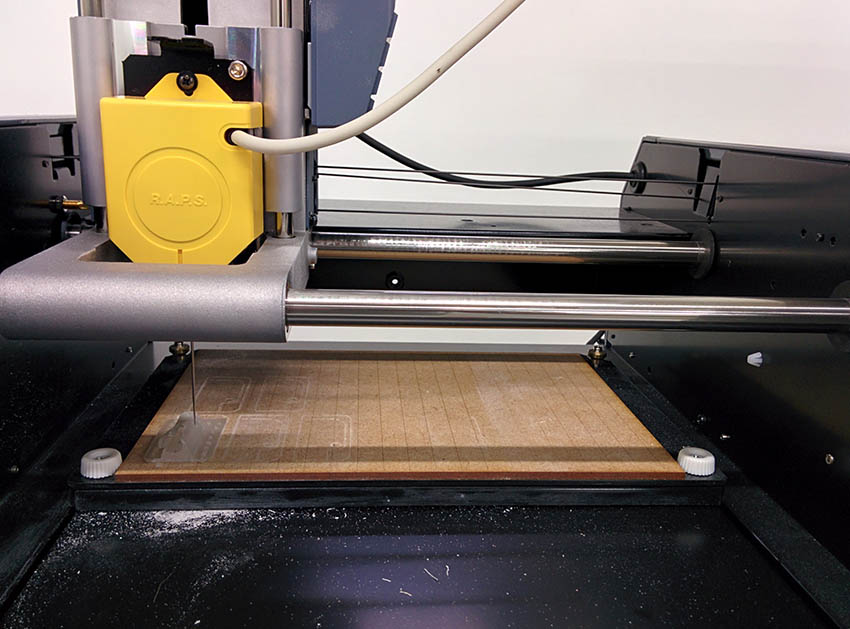
Problem: In the first scan, I had problems putting the piece directly on the base surface of the machine because the scan sharp end did not come down to the base and I lost the lower part of the piece in Z. To fix it I had to use a base of 3 mm thick and so I got to scan of the entire piece correctly.
STEP 2: Edit the digitalized piece by CAD
Scanning the piece we get a 3d mesh that can be opened directly in a 3D CAD program. I used Rhinoceros 3D, opening the exported file from the scanner software in dxf file.
In the two images below you can see the mesh of the piece just as scanned, the scan imperfections and broken parts of the original part appear in the digital piece.
I modify the scanned piece for three reasons:
- the scanned the piece has all the problems the original piece had, that is, we can see that it is cracked on top.
- The scanner used, only scan in the z axis, so there are parts that are not accessible to the scanner, so I'll have to draw them manually.
- The scanner works by points, making a reconstruction of the surface from these points placed in space. The problem with this is that sometimes this reconstruction will not correspond with reality, as happens for example in the holes, where to be an interpolation of the points will not be understood as holes but a convex surface so we drilled them manually using CAD
To operate well in Rhino, we transform the mesh to Nurb curve with the command MeshtoNurb Nurb by allowing a more agile and quick editing. Now modify the necessary points and using Boolean operations we can remove parts of the scanned object, to obtain the improved piece we want to print.
Having the corrected and modified piece with the improvements we want, we can go to print in 3D and export in STL format. |
|
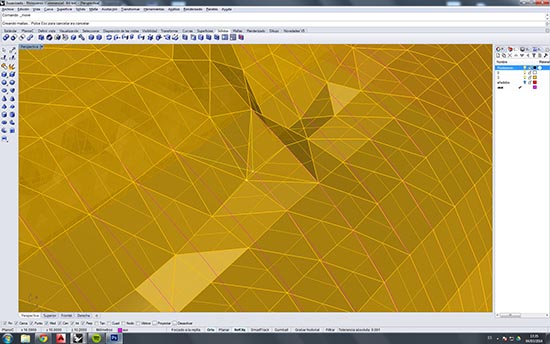 |
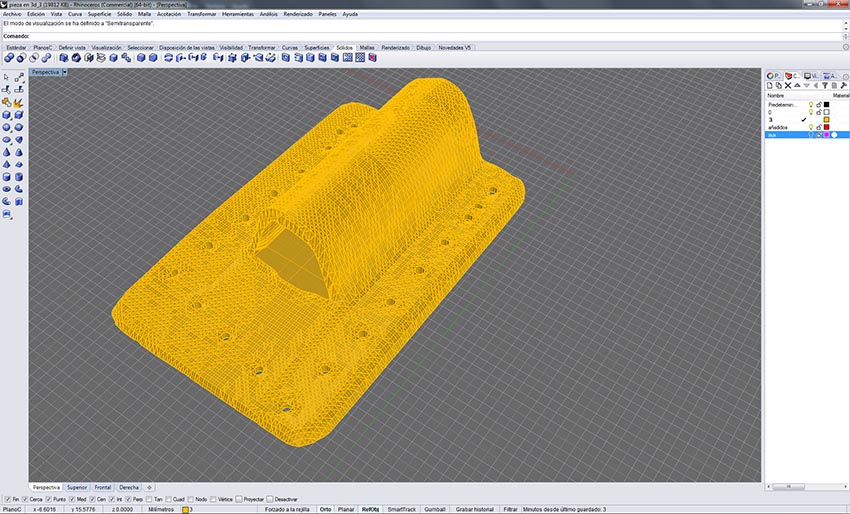
STEP 3: Print the corrected object
For the 3D printing I use Makerbot Replicator machine with Rlicator-G software. In print options, I choose printing base in contact with the hot base of the machine (no raft) for better adherence of the piece, but with raft in holes to allow the machine to print it.
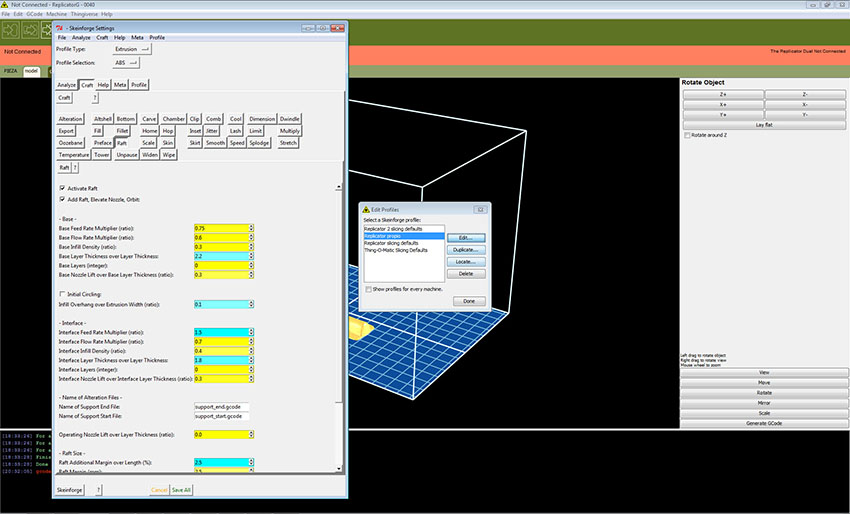
The piece is solid and Layer Heigh is 0.2 mm. I Generat the G code to print the piece.
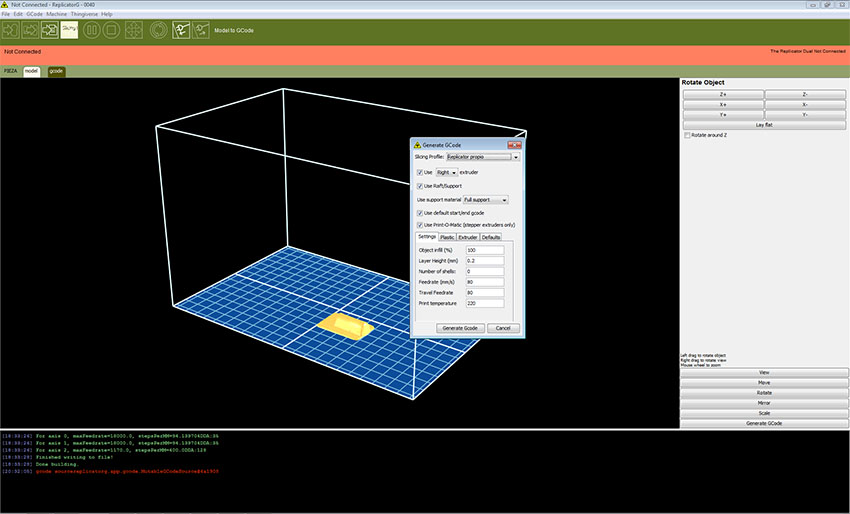
Before printing, to check the Layers to print, I use the software Repetier where I can see exactly how each layer will be printed. In my experience, when Repetier show a problem with the layers, the machine reproduce the same problem.
Now that I know how the piece will be printed I can export the G-code to insert the SD card in the machine.
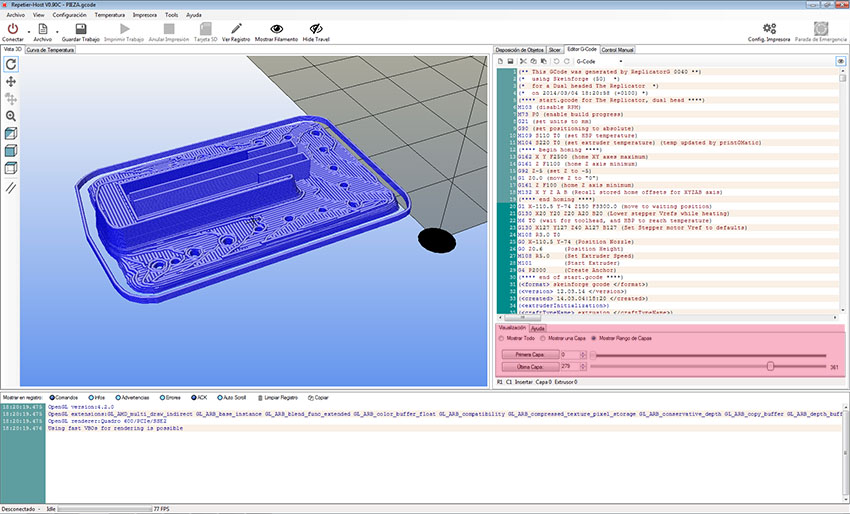
To improve the adhesion with the hot base of the Replicator and avoid the detach of the piece while is printed, smoothly I sand the teflon base and add a bit of ABS plastic diluted in acetone. Thus the new piece adheres better and does not detach during printing. |
|
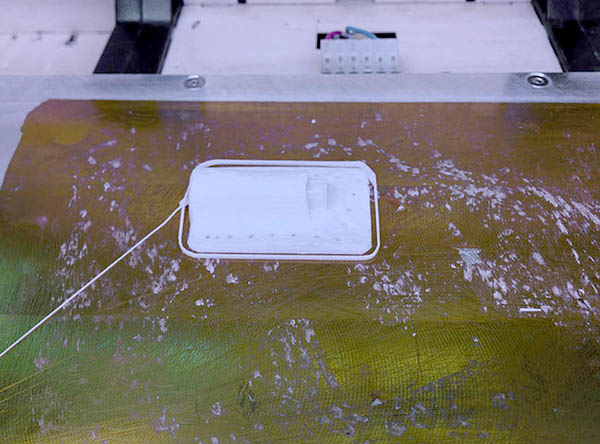 |
Now I have the new fixed piece to put it on my umbrella.
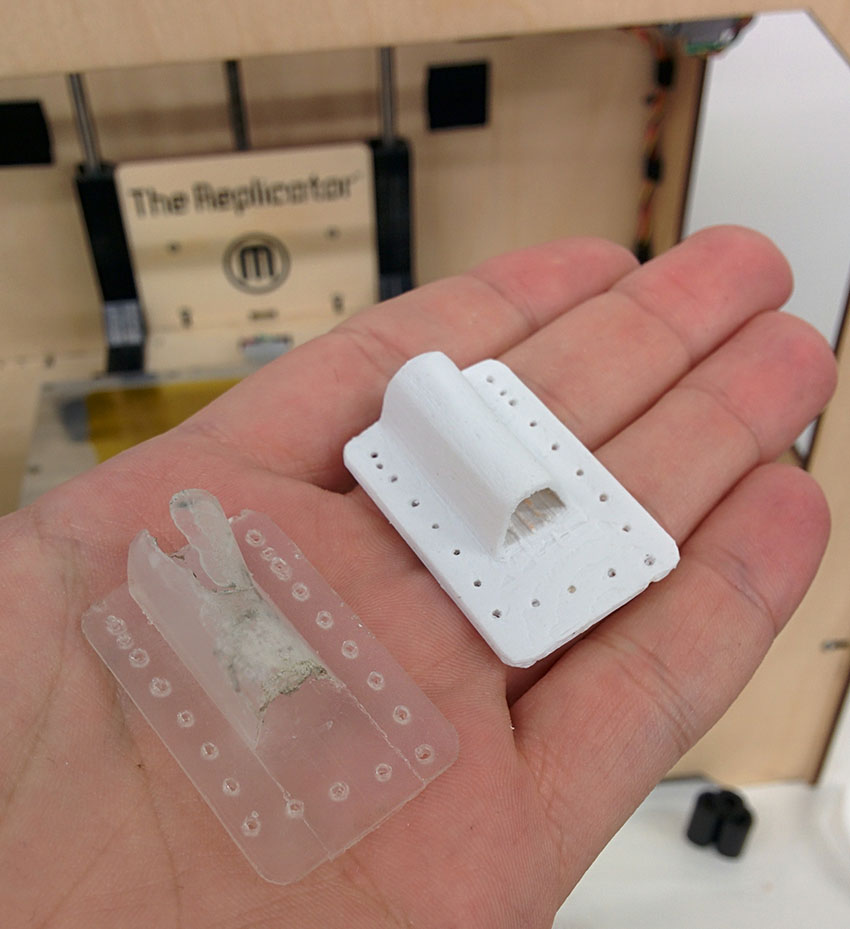
|