Computer Controlled Machining
Overview of week 7
Group Assignment
- Complete our lab's safety training
- Test runout, alignment, fixturing, speeds, feeds, materials and toolpaths for our machine
Individual Assignment
• Make (design+mill+assemble) something big
extra credit: don't use fasteners or glue
extra credit: include curved surfaces
Individual Assignment :
CNC Wood Router
A CNC wood router is a computer-controlled cutting machine used for carving, engraving, and shaping wood with high precision. It automates the routing process, reducing manual labor and increasing accuracy. CNC routers are versatile, capable of working with hardwood, plywood, and MDF. They are ideal for furniture making, sign making, decorative woodwork, and prototyping. Key features include high precision, repeatability, and speed in production. When choosing a CNC wood router, consider factors like work area size, spindle power, software compatibility, and build quality. These machines are essential for mass production with consistent quality.
In our lab we have a CNC Wood Router STM1325
Specification
- Model - STM1325
- Working Size - 1300mm*2500mm*200mm
- Body structure - Steel tubes X, Y Structure rack and pinion drive Z Structure Ball Screw/option gear wheel
- X, Y Resolution - <0.01mm 5. Max Moving Speed - 32000mm/min6. Max Engraving Speed - 20000mm/min
- XYZ travelling positioning accuracy - 0.03/300mm
- XYZ repositioning accuracy - 0.03mm
- Spindle power - 3kw/4.5kw/5.5KW
- Spindle Speed - 24,000 rpm
- Table style - T-slot table
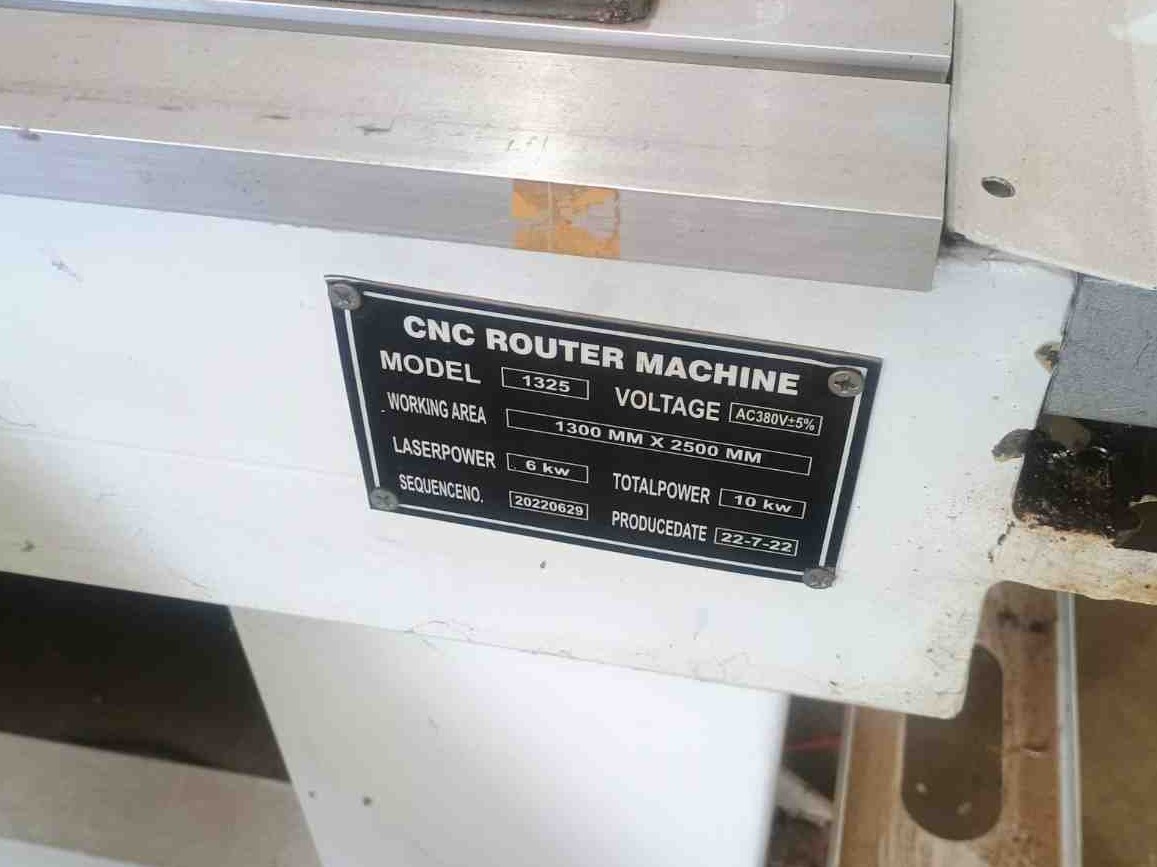
Fusion360
Fusion 360 is a cloud-based 3D CAD, CAM, and CAE software developed by Autodesk. It integrates design, simulation, rendering, and manufacturing tools in a single platform. Fusion 360 is widely used for product design, mechanical engineering, and CNC machining. It supports parametric, direct, freeform, and surface modeling. The software also includes simulation and generative design features for optimizing parts. Its built-in CAM tools enable CNC programming for milling, turning, and laser cutting. Fusion 360 is popular for prototyping, reverse engineering, and collaborative design.
I have planned to design and cut a bookshelf for this week’s assignment. I am starting with Fusion 360 to design the bookshelf.
I conducted a Google search for bookshelf references and found this simple yet elegant design.
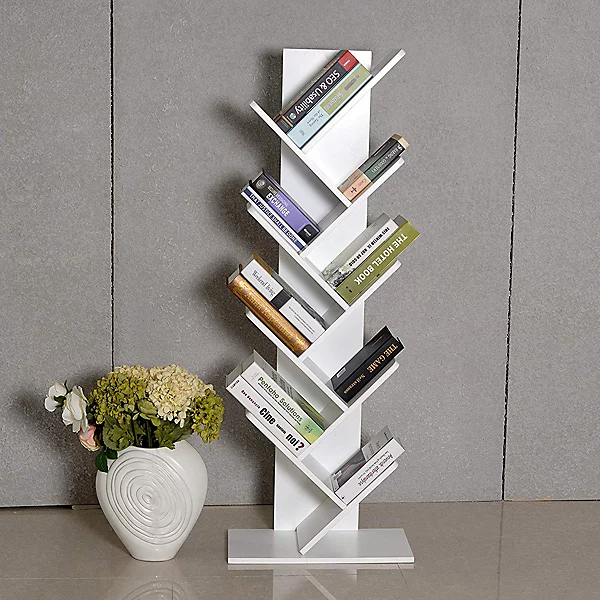
First, I sketched the rough dimensions on paper. Then, I proceeded to draw the base and set it according to the defined parameters for parametric modeling. After setting the base, I positioned the book holder at a 45-degree incline.
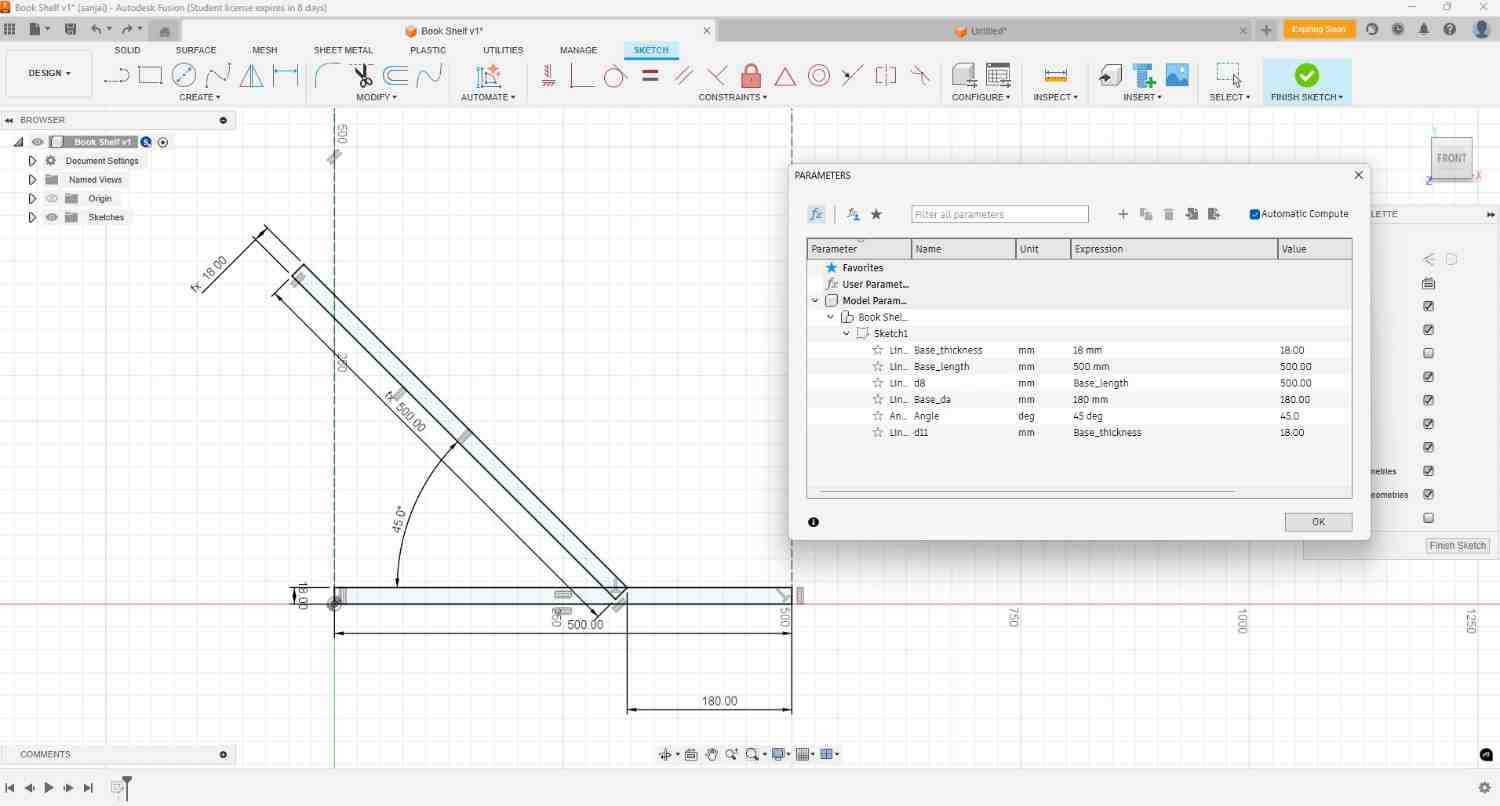
Then, I adjusted the two sides wooden flat relative to the center position by modifying the driven dimensions.
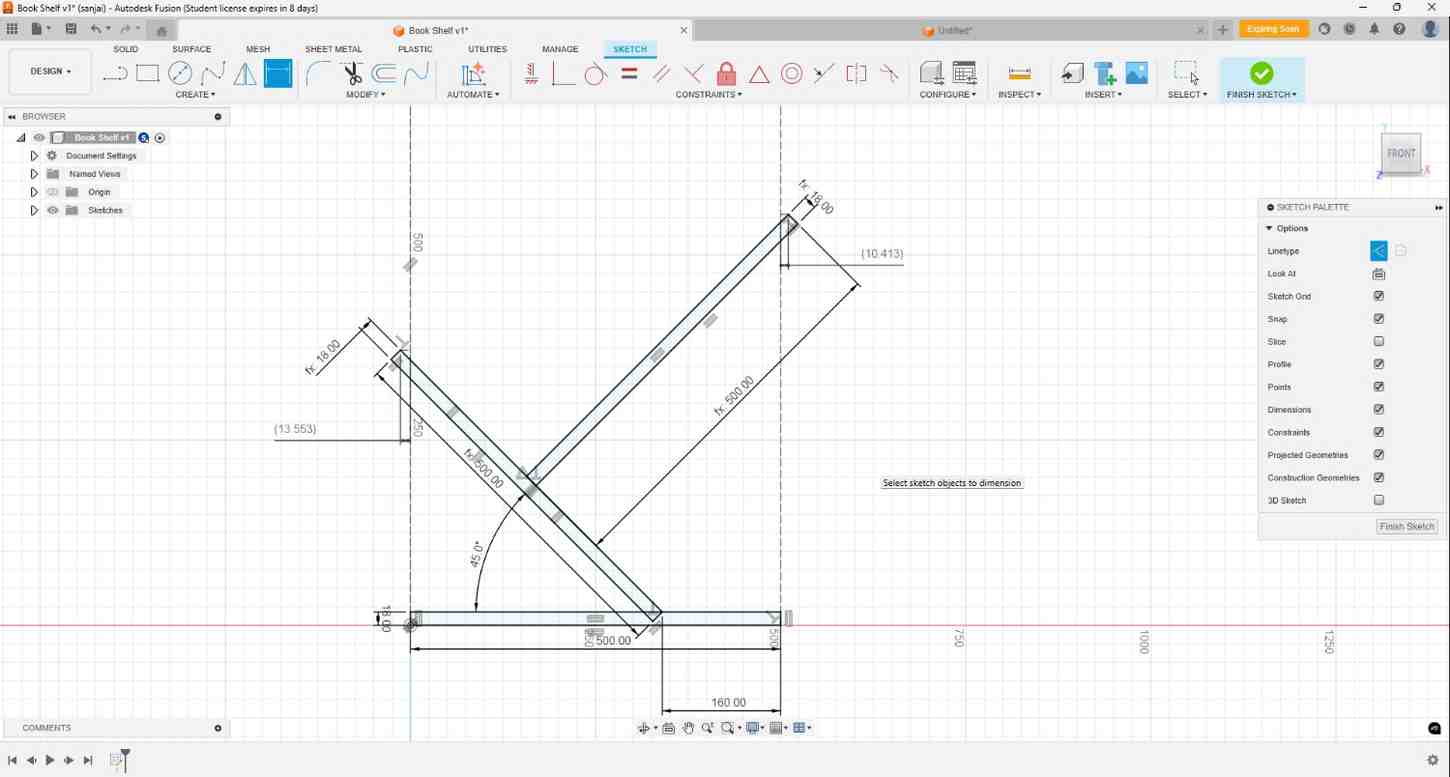
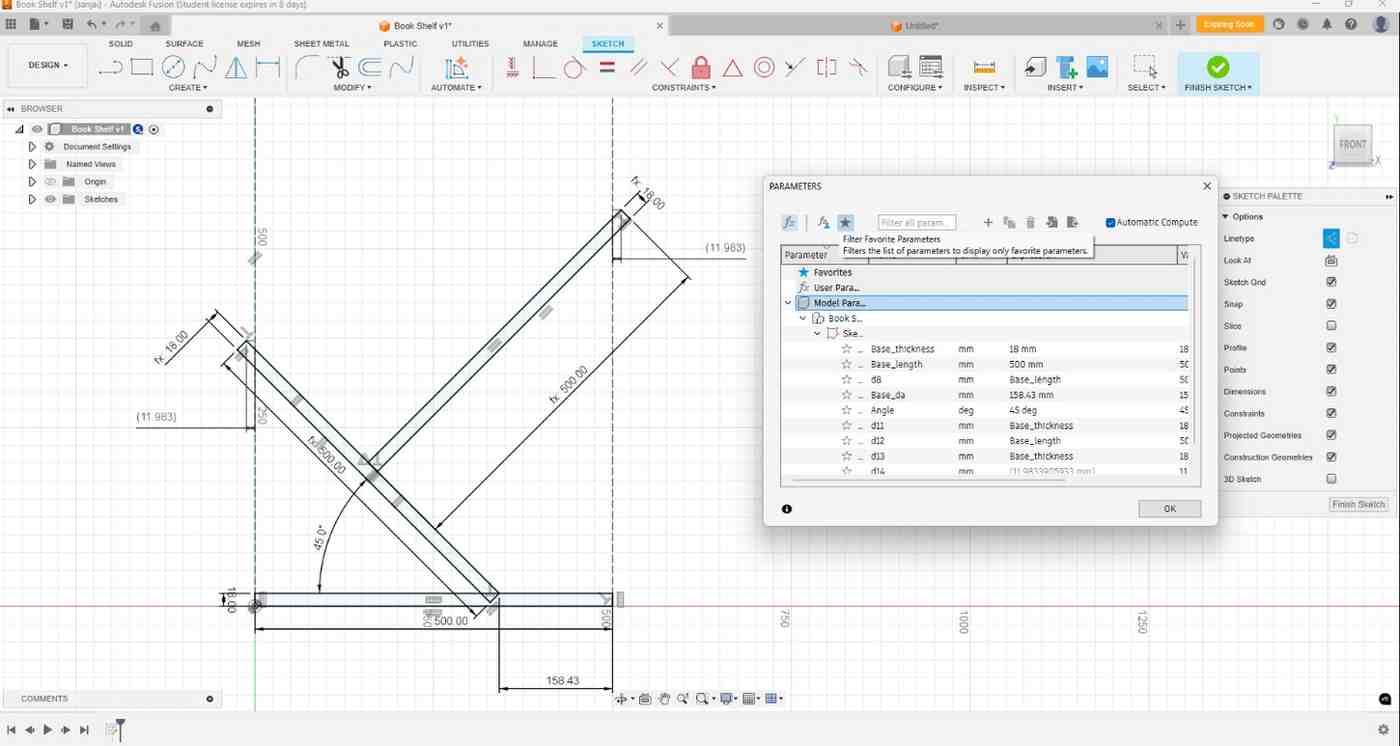
After finalizing all the adjustments, I obtained this drawing based on my design.
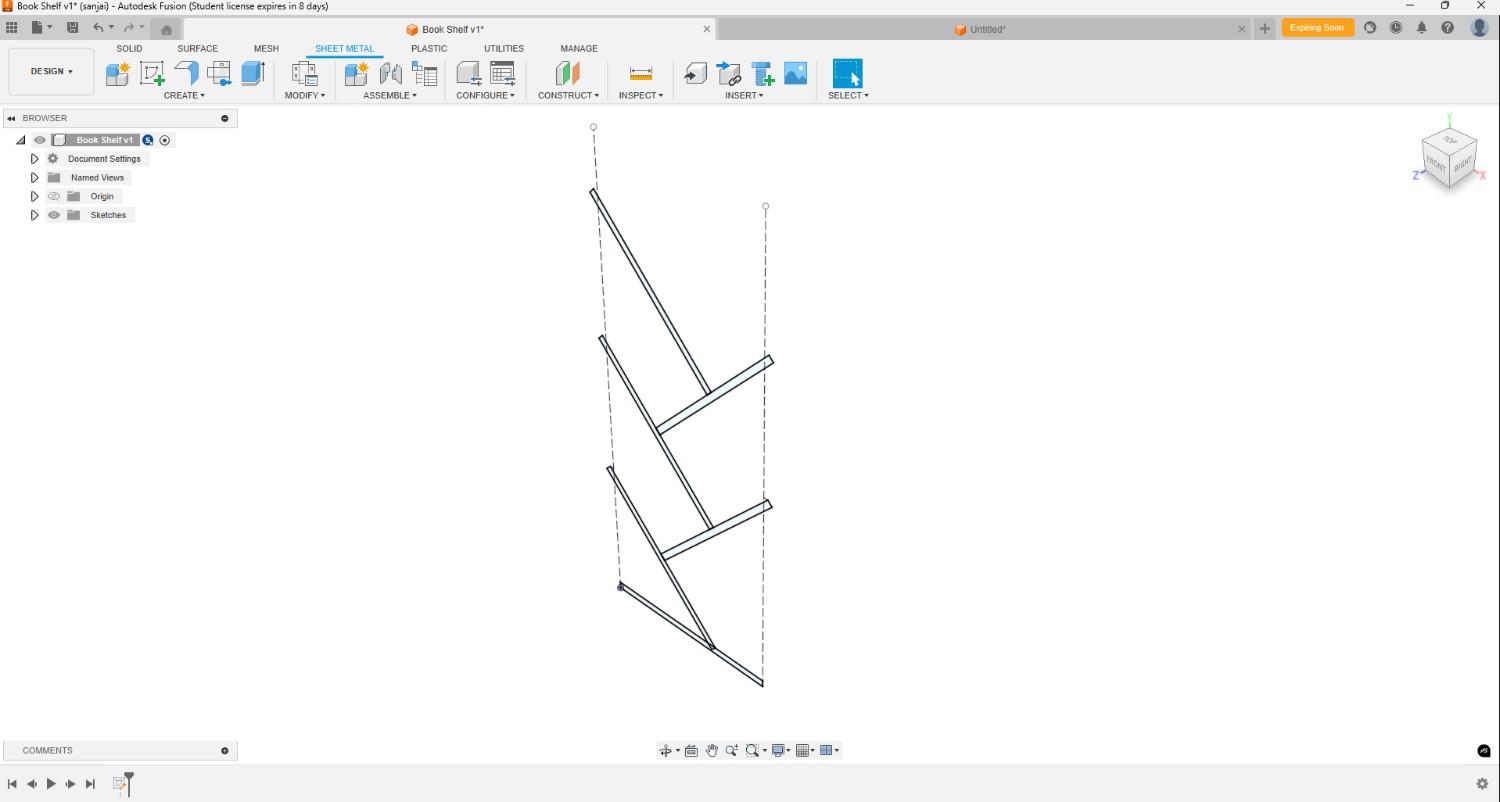
Then, I converted it into a 3D design using the extrude command.
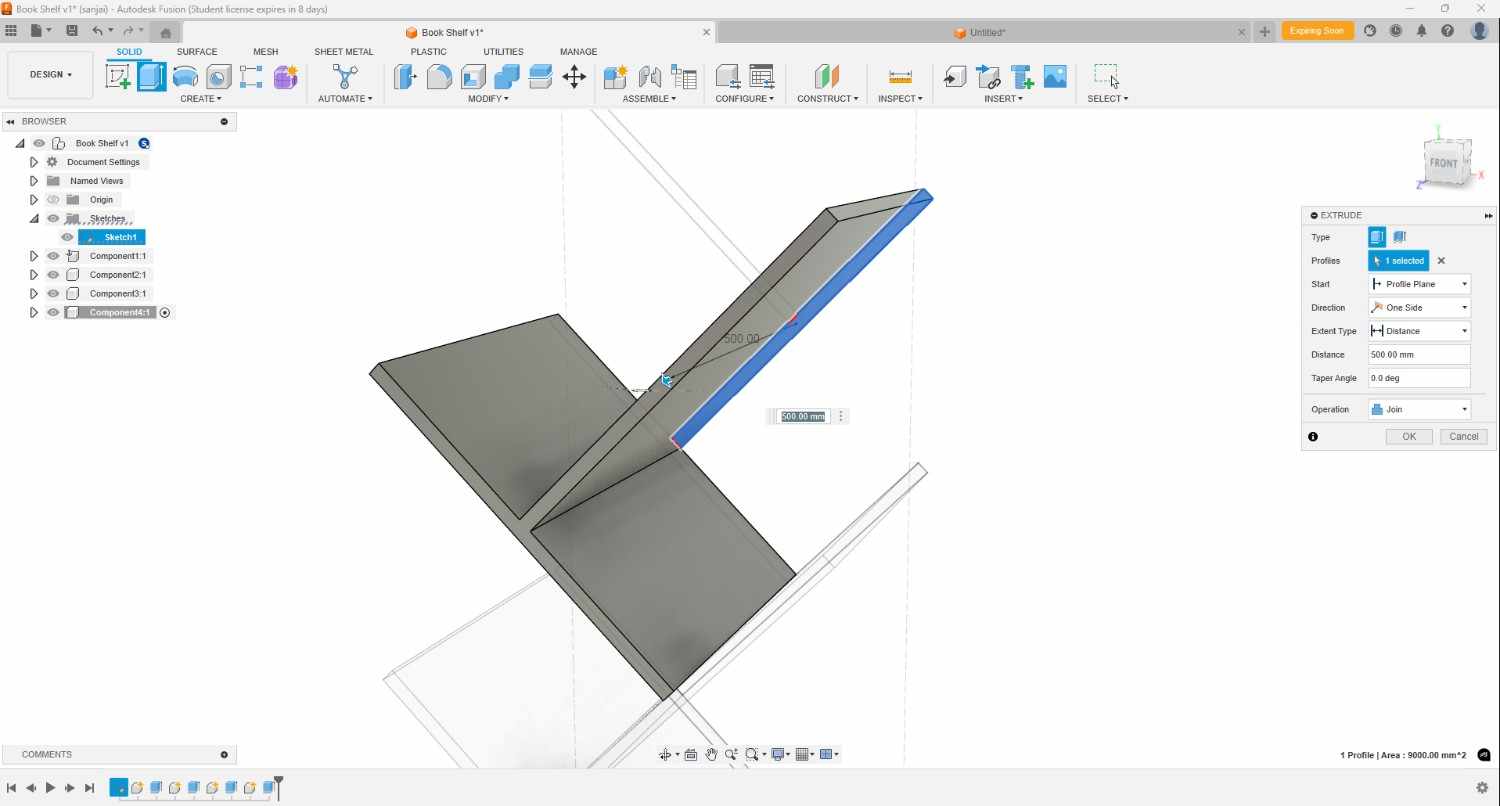
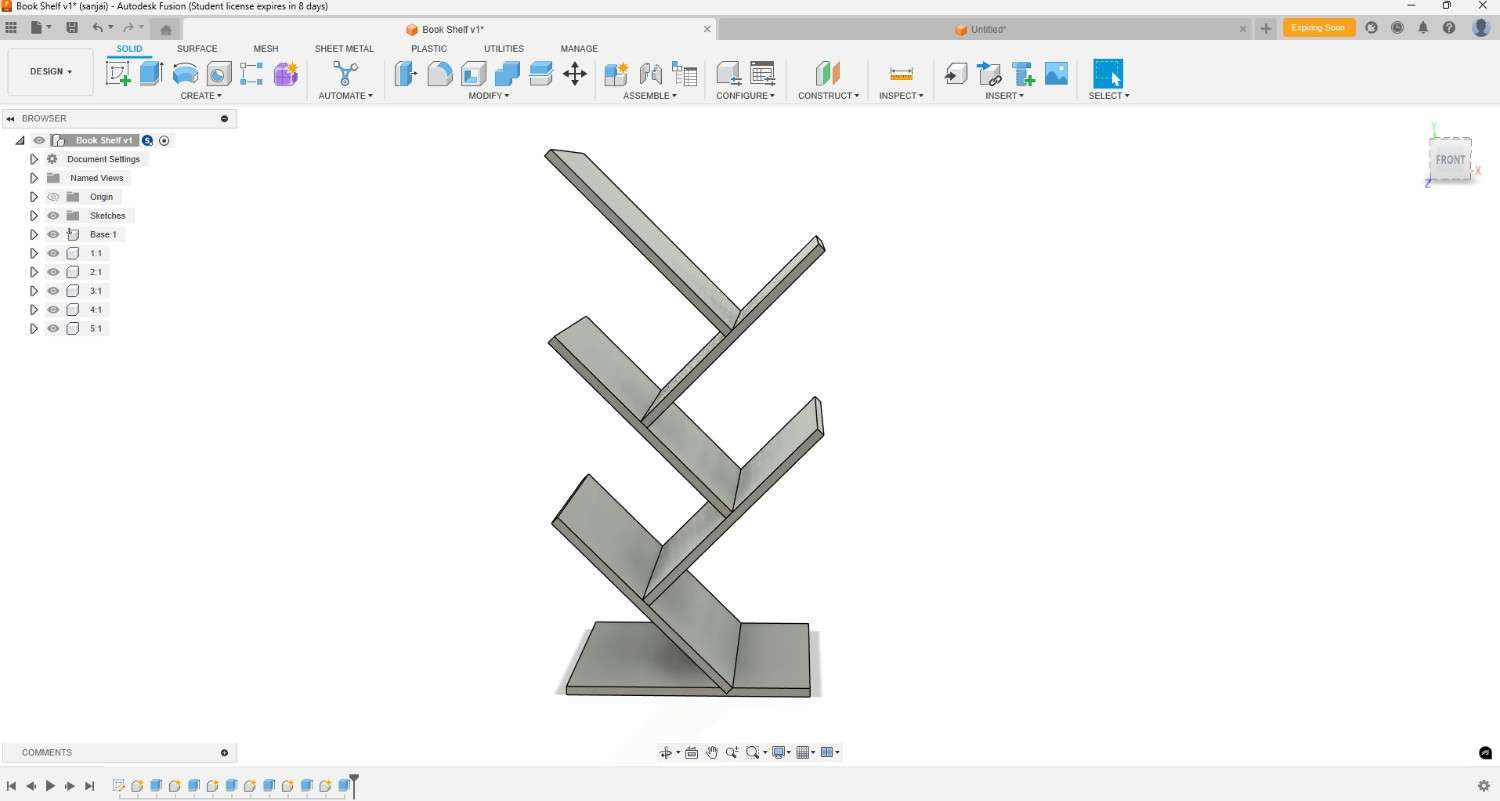
I drew a rectangle that will be a part as the support material for the bookshelf.
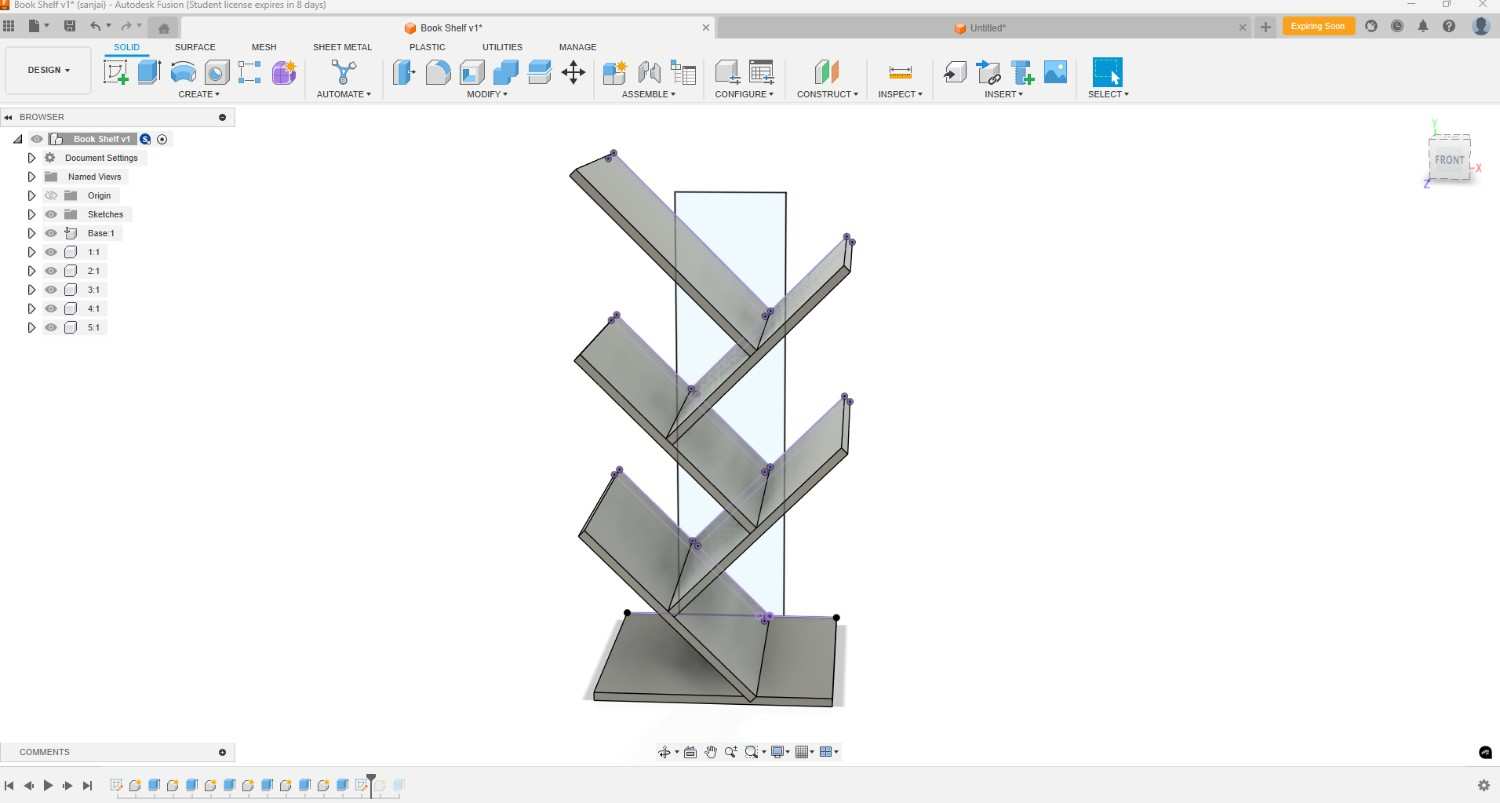
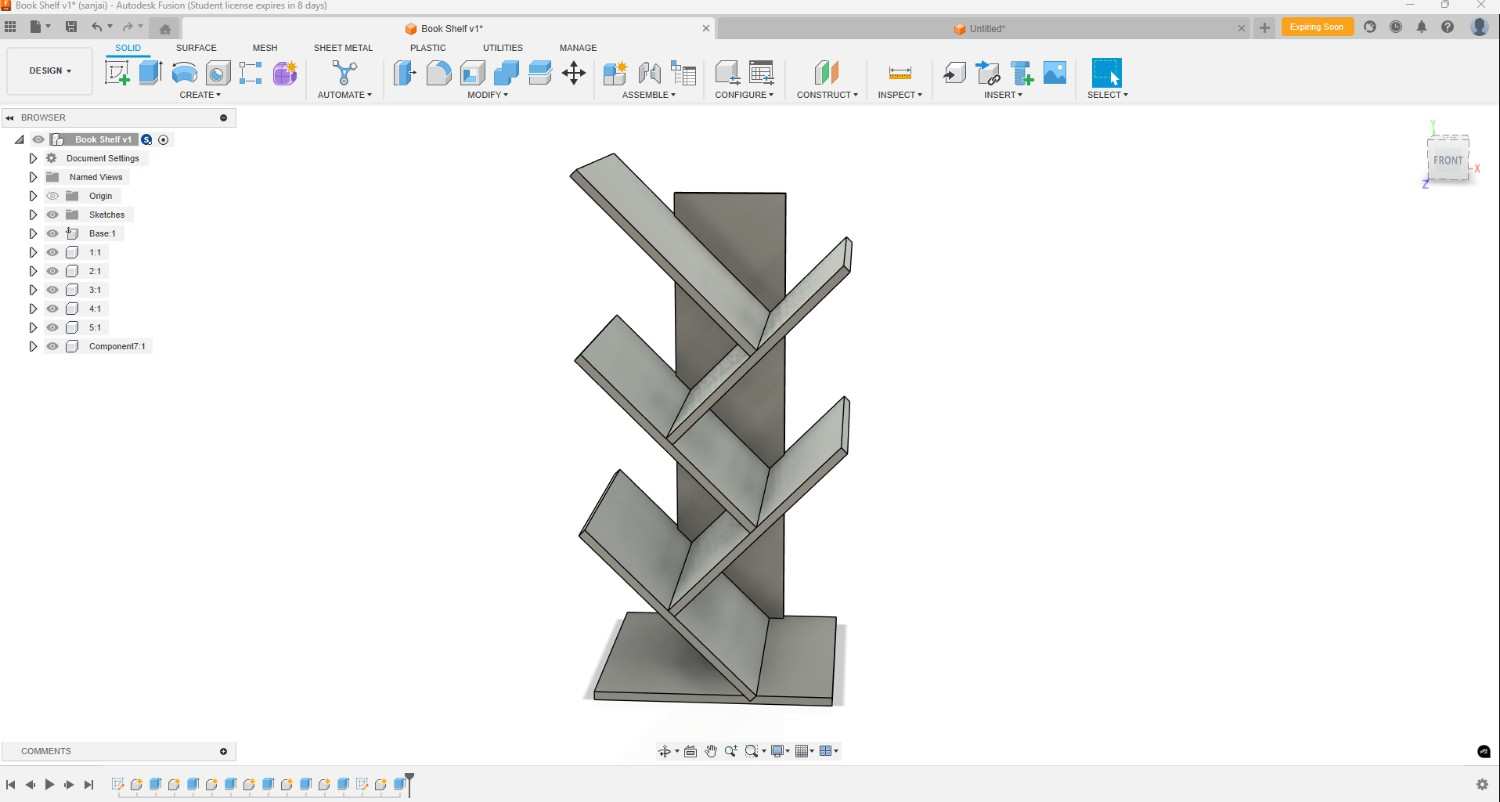
After creating the 3D model, I designed a trapezoidal shape on the wooden surface to facilitate dovetail-like joints for secure attachment.
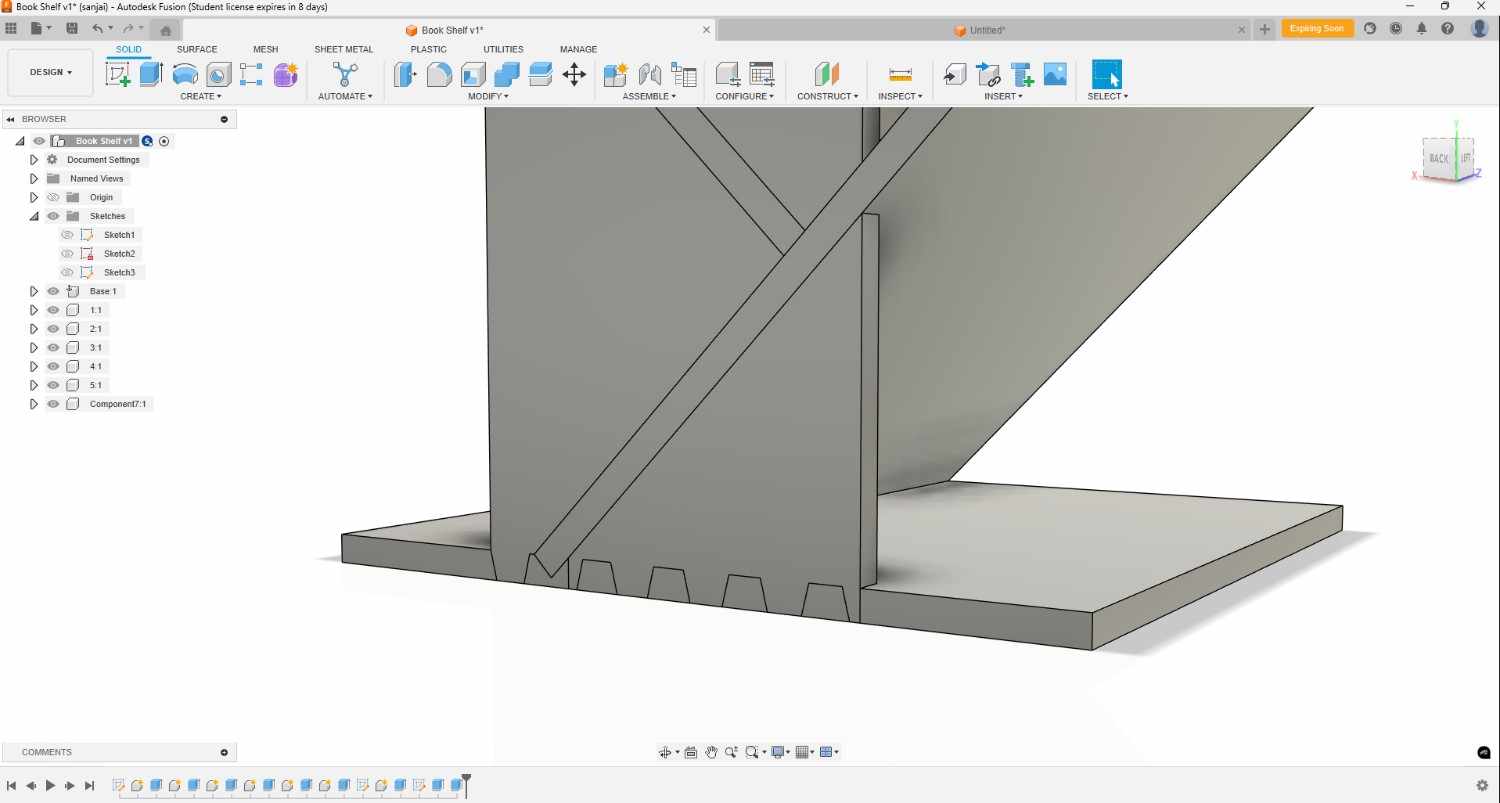
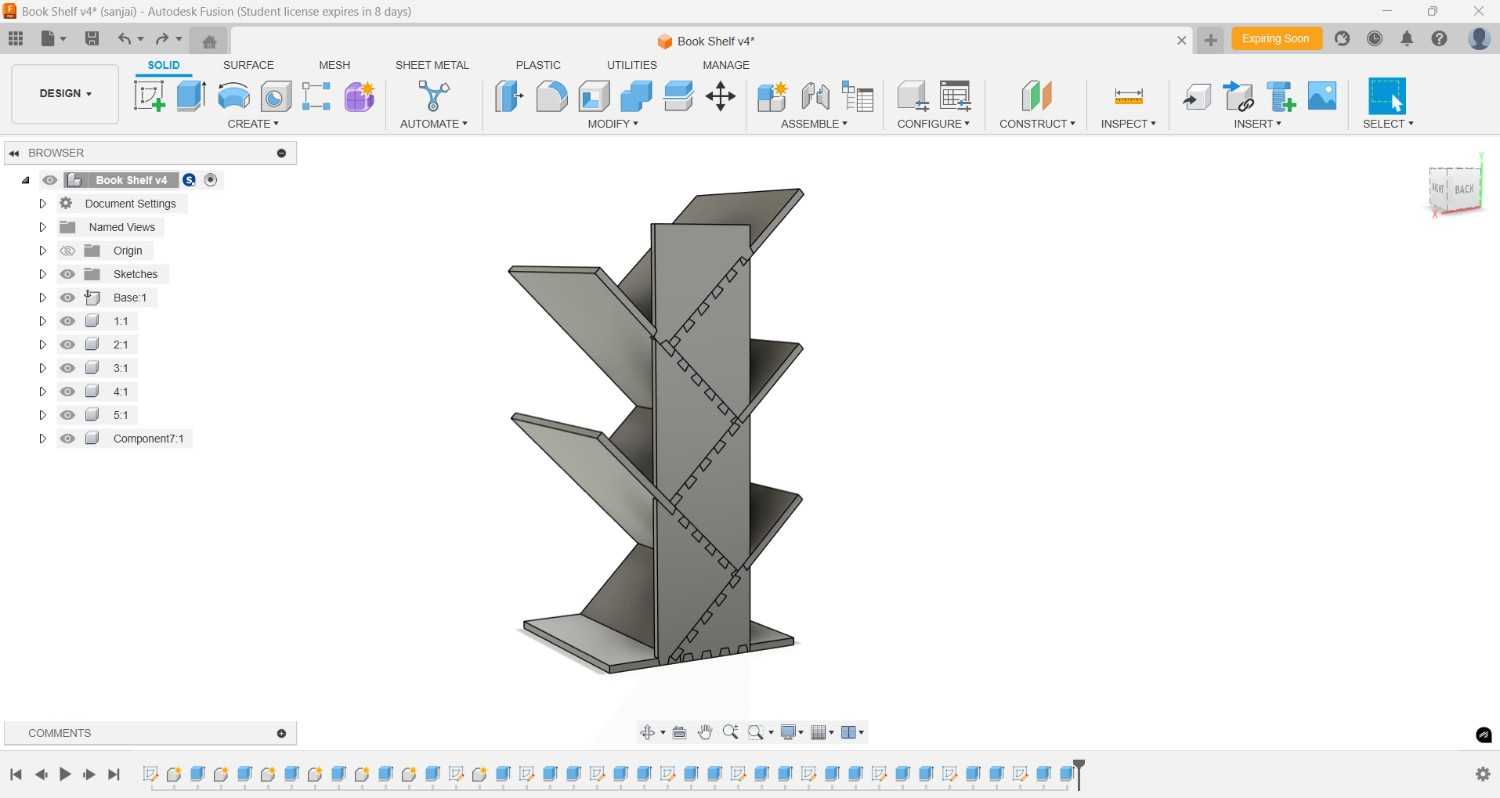
Then, I proceeded with rendering the design to enhance its visual representation.
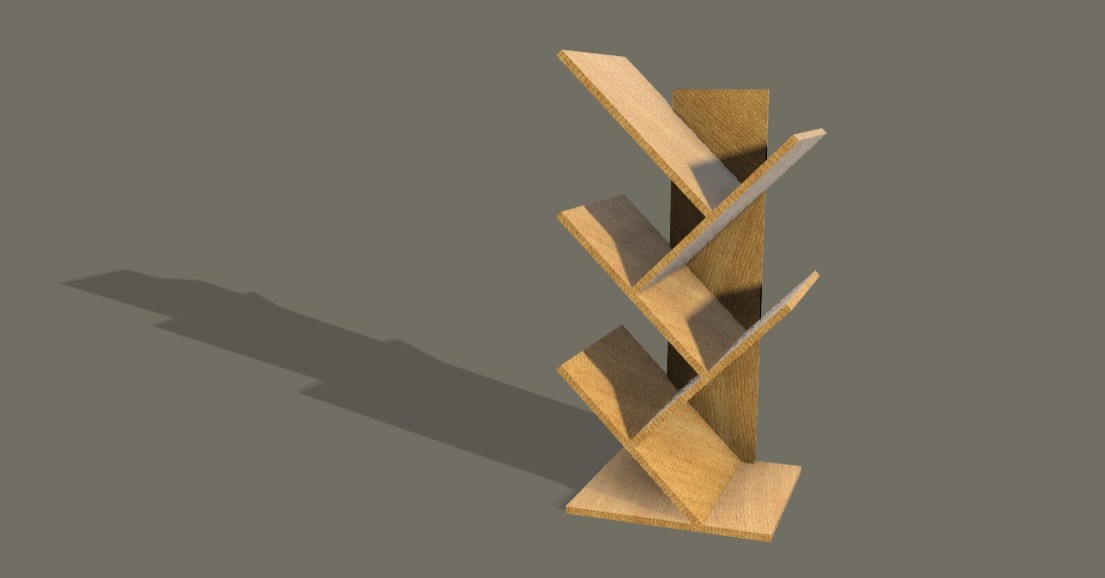
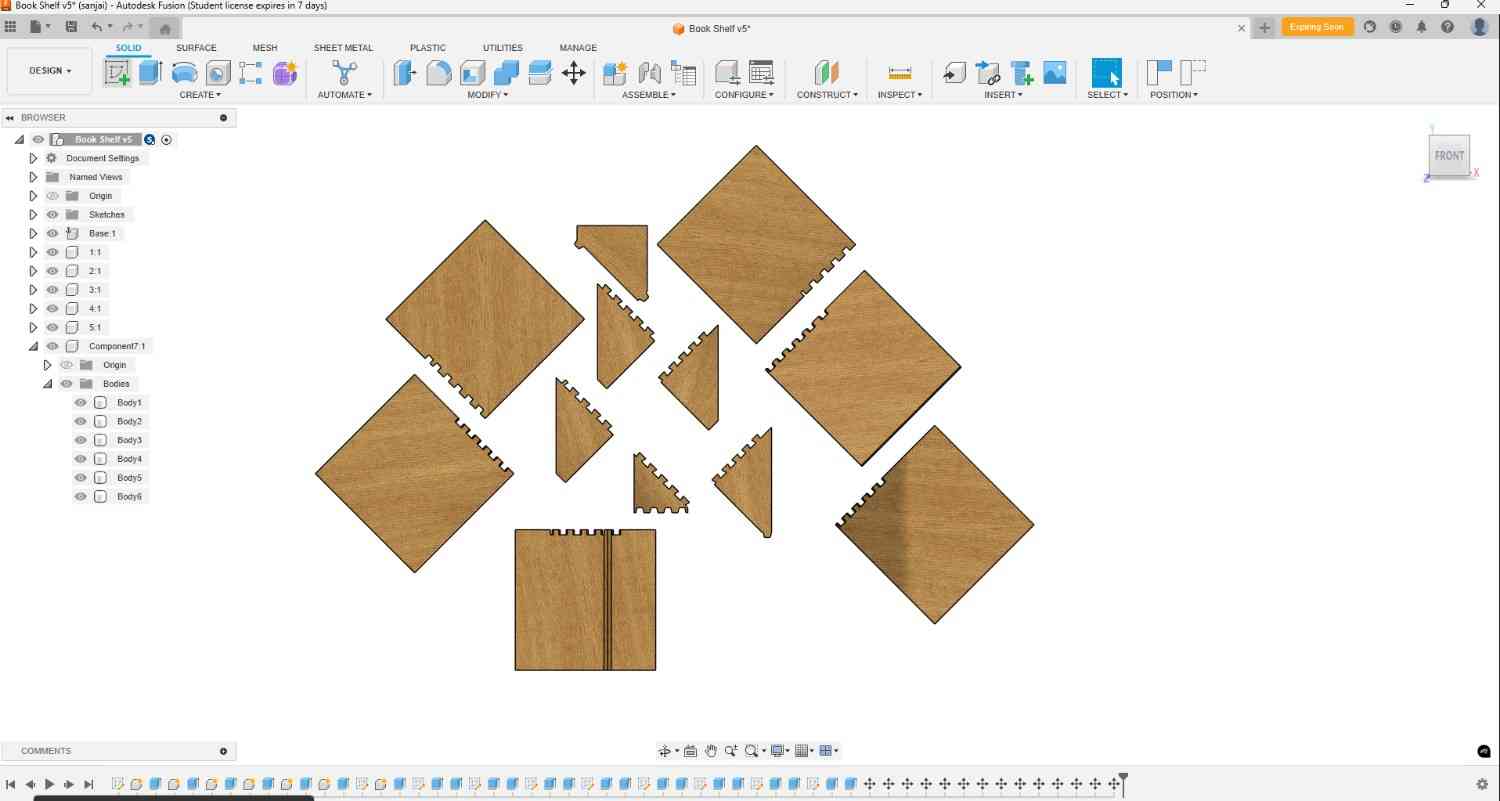
Then I rearrang it properly for the milling operation by using the move command.
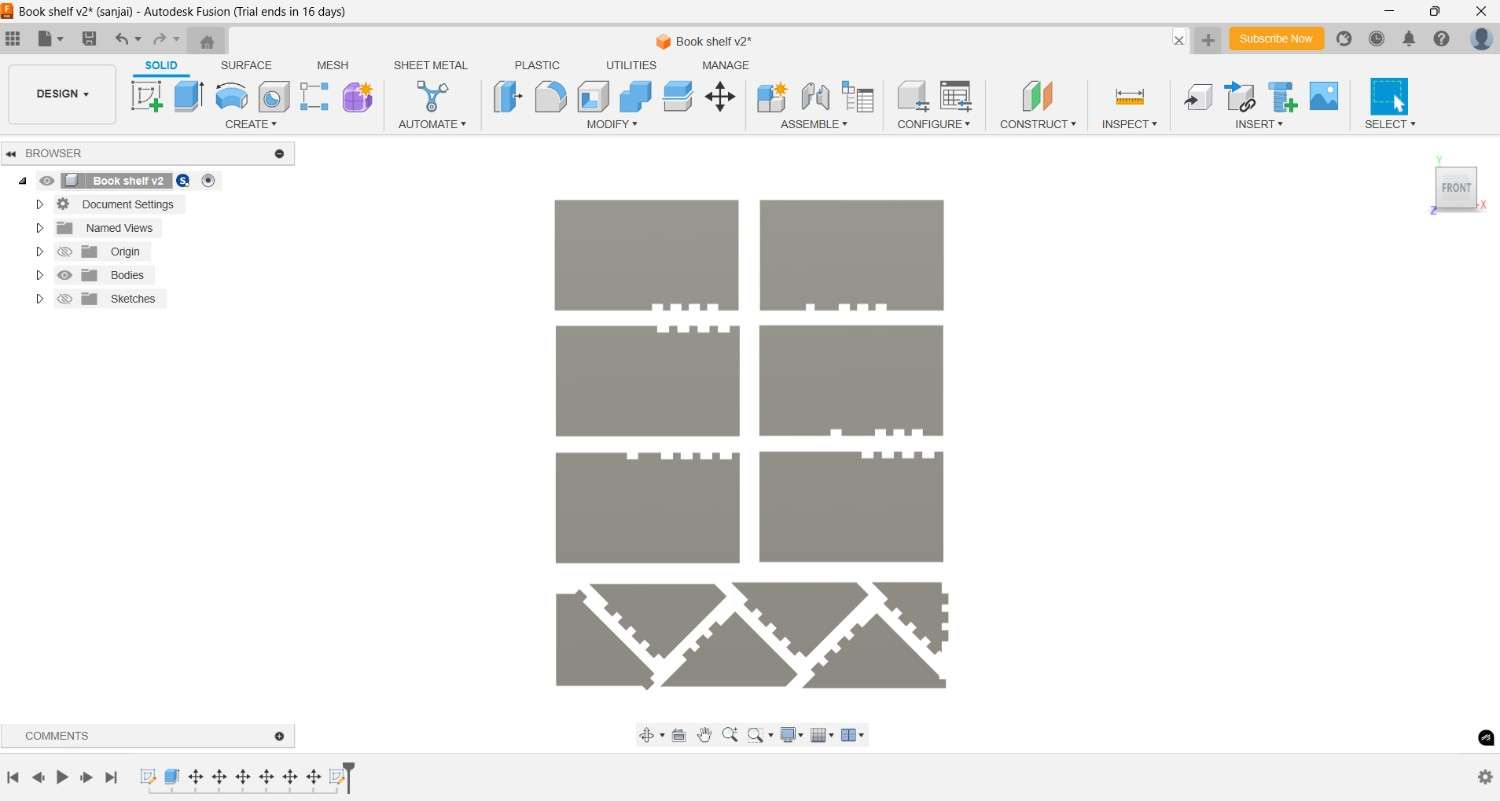
ArtCAM
ArtCAM was a CAD/CAM software developed by Delcam (later acquired by Autodesk) for designing and manufacturing artistic reliefs. It specialized in 2D and 3D modeling, mainly used for woodworking, sign making, and jewelry design. ArtCAM combined vector design tools with powerful sculpting and machining capabilities. It allowed users to create intricate designs and generate toolpaths for CNC machines.
I used this software for tool path generation, here I attached the download link - Artcam
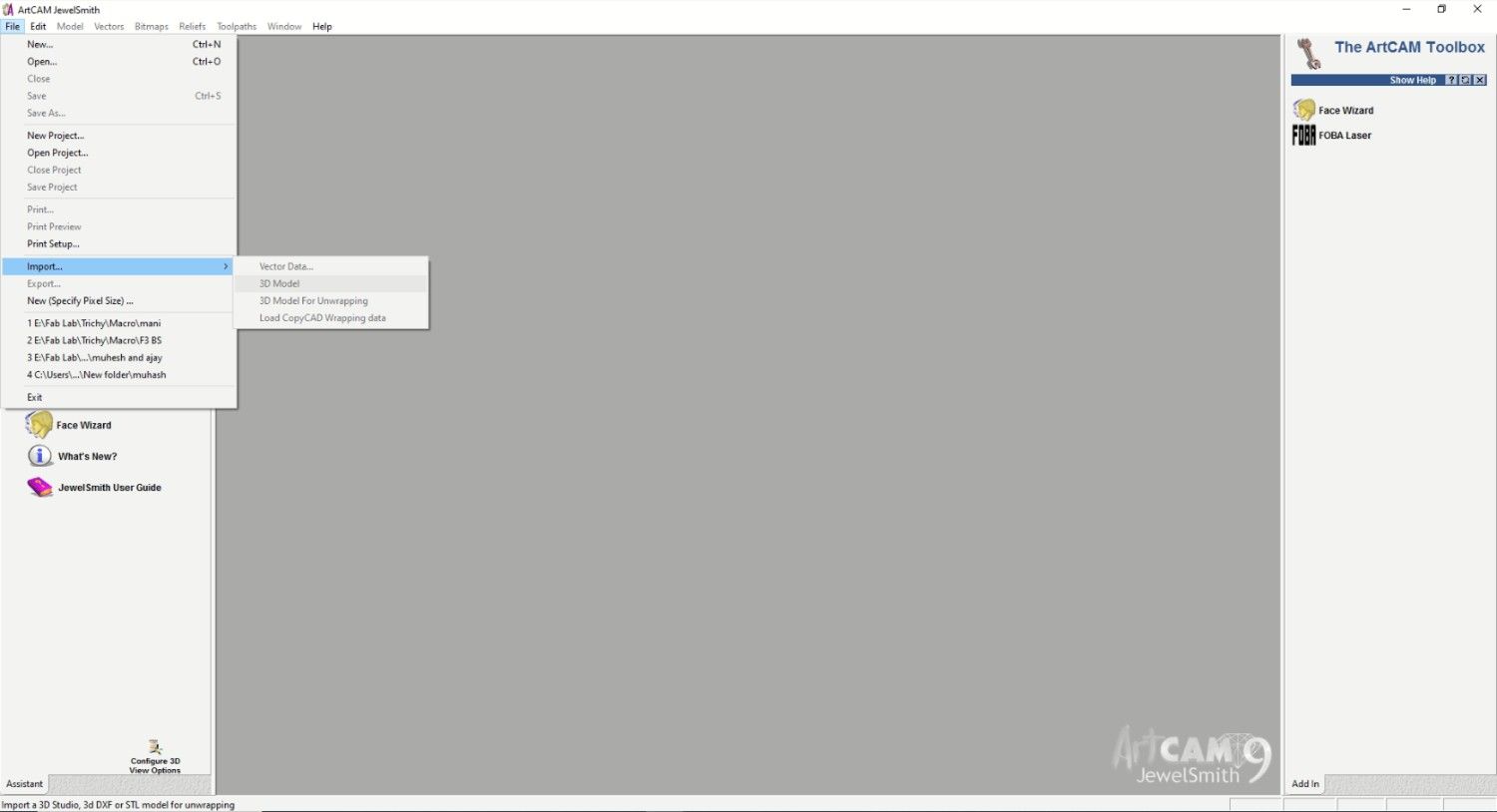
Import the step file into it, and set up the orgin for the required space where your desing will be in frame, after setup everything click apply and paste.
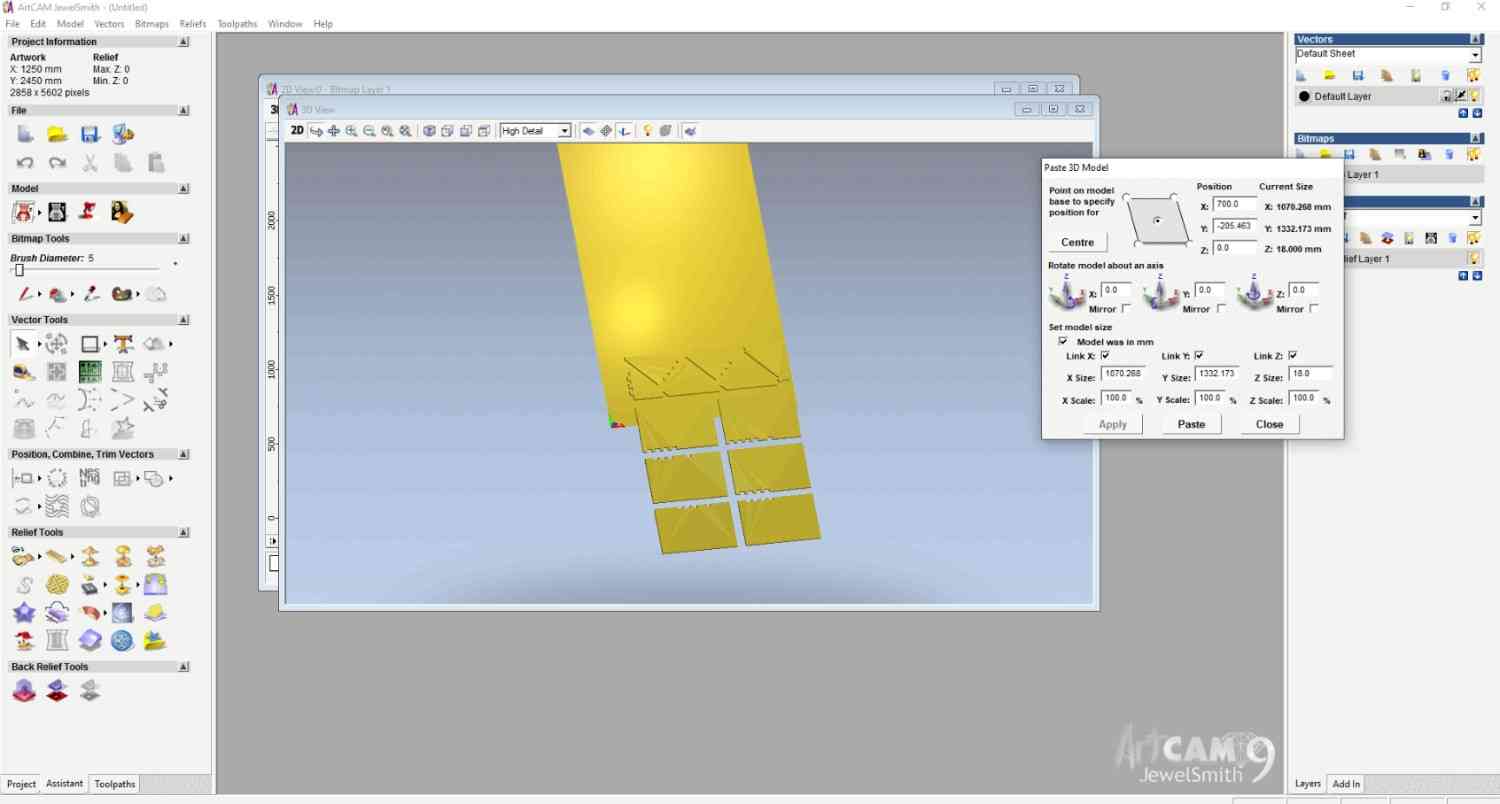
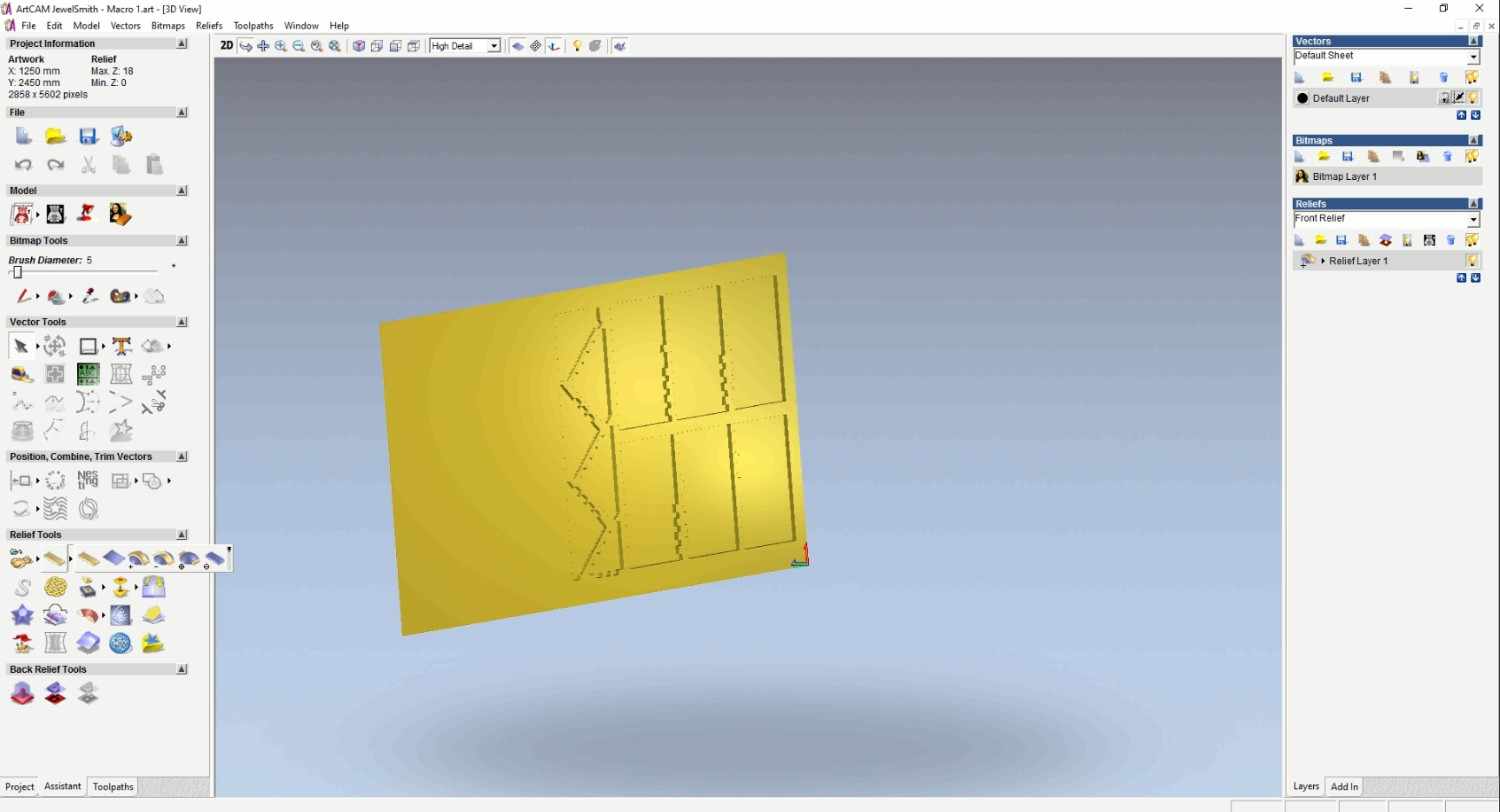
You can also check with the 2D viwer
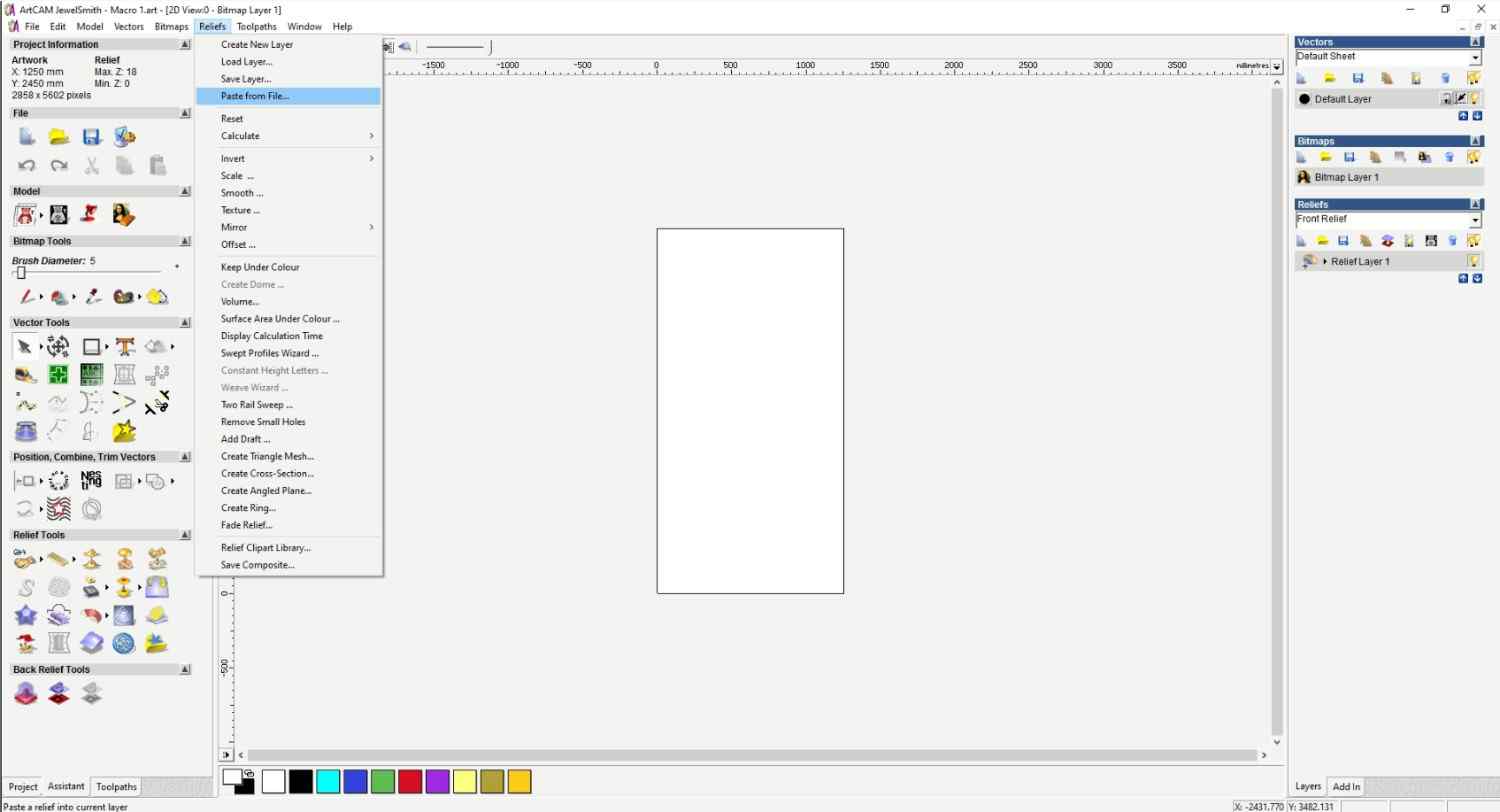
After setting it select the tool parameter according to our design, in my case i selected the End mill 6 mm tool for the milling
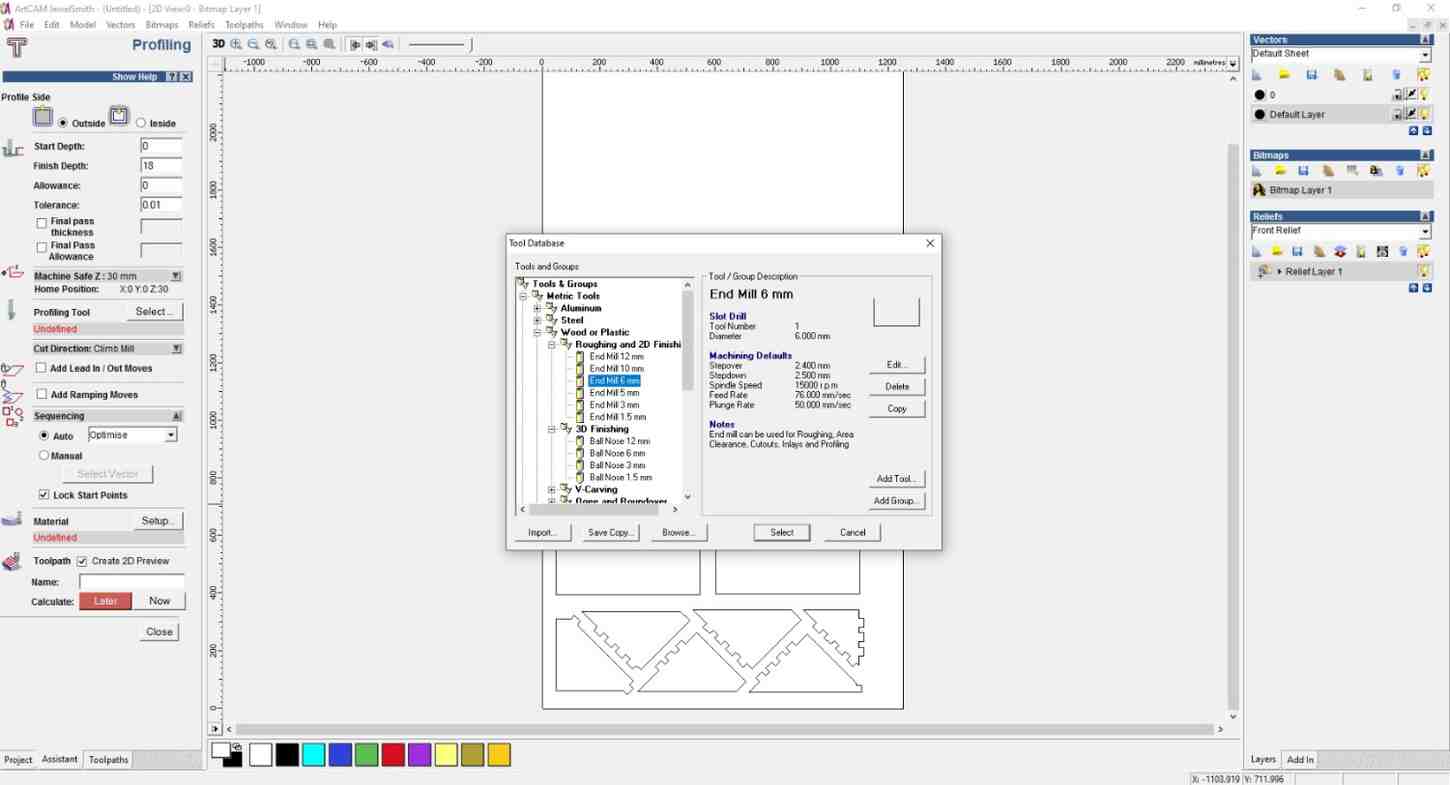
After setting the tool, I give the tool path
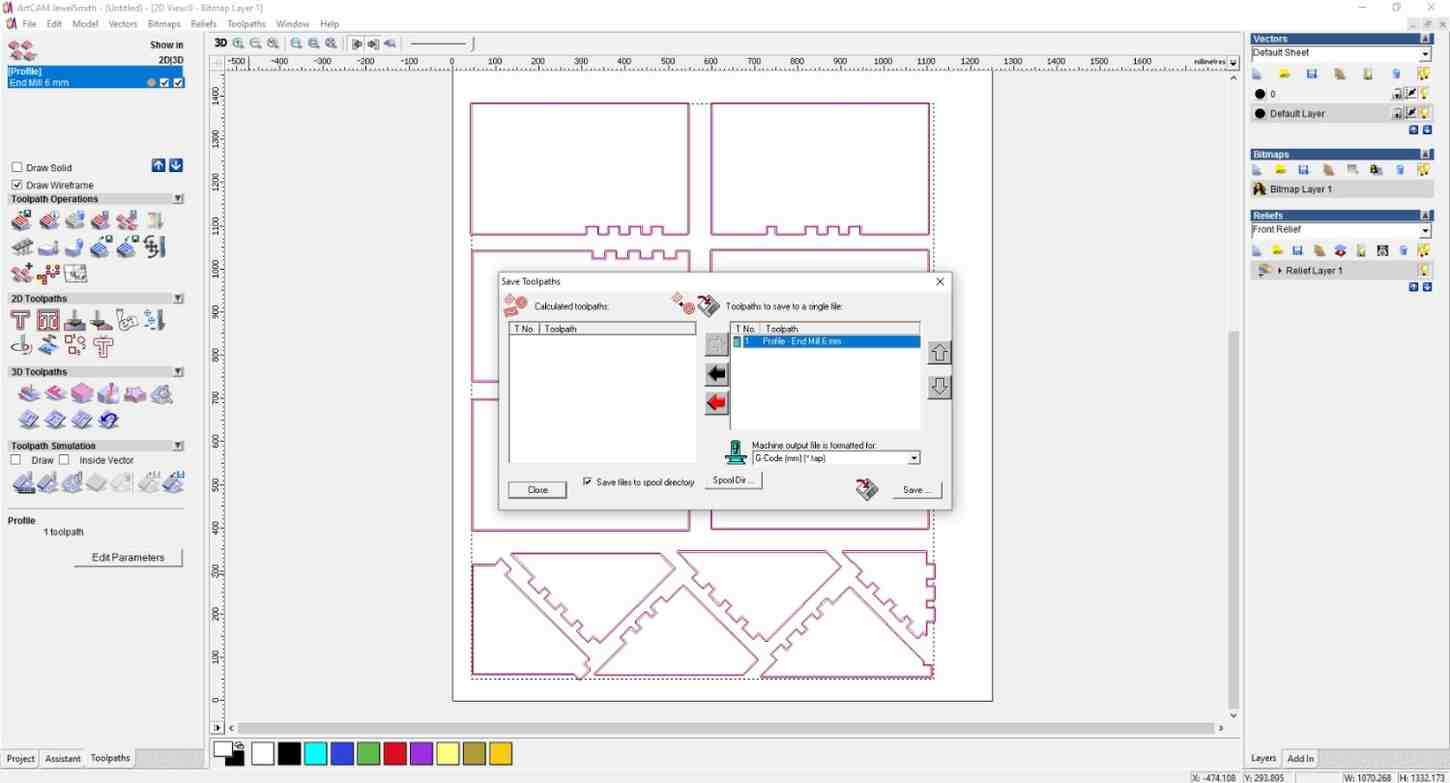
Then converted it into the G-code fot the machining operation.
CNC Milling
After the software part I straightly jump into the CNC router, it has very essential part to us to operate the machine carefully.
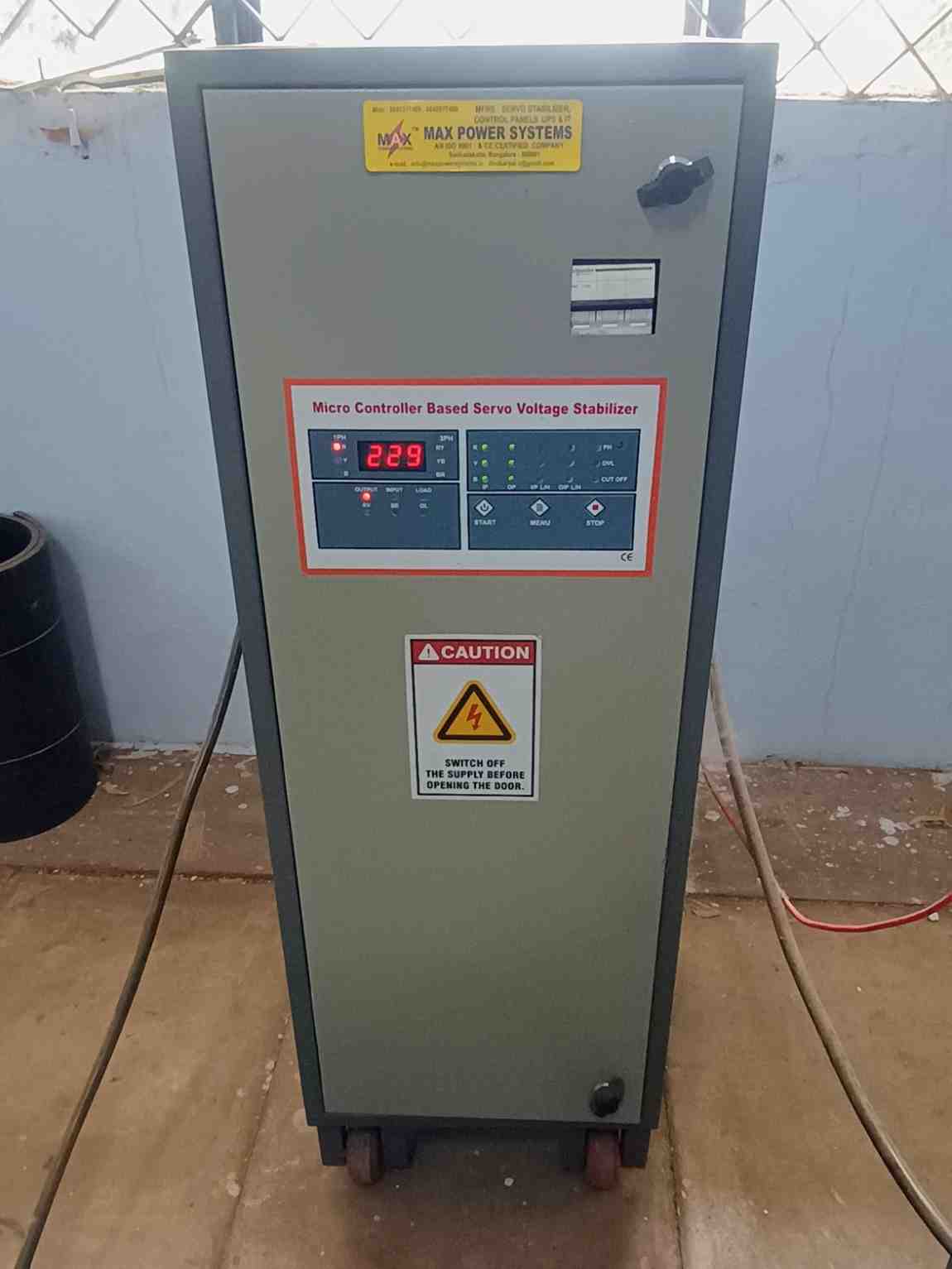
In our CNC router the machine has attached with the dust collector to prevent us from heavy dust while the machine is working.
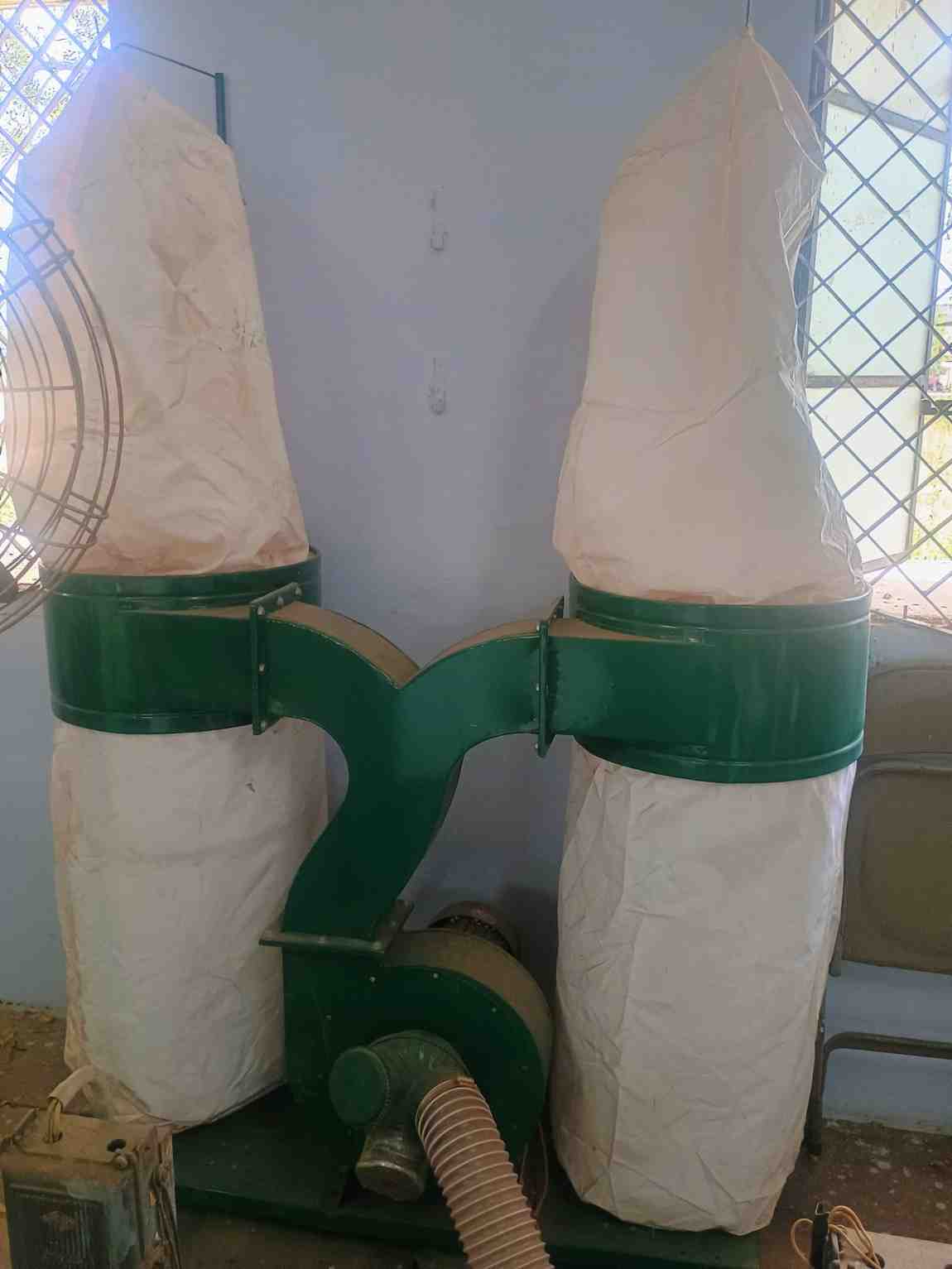
For setting up the tool in spindle we remove it first from the machine
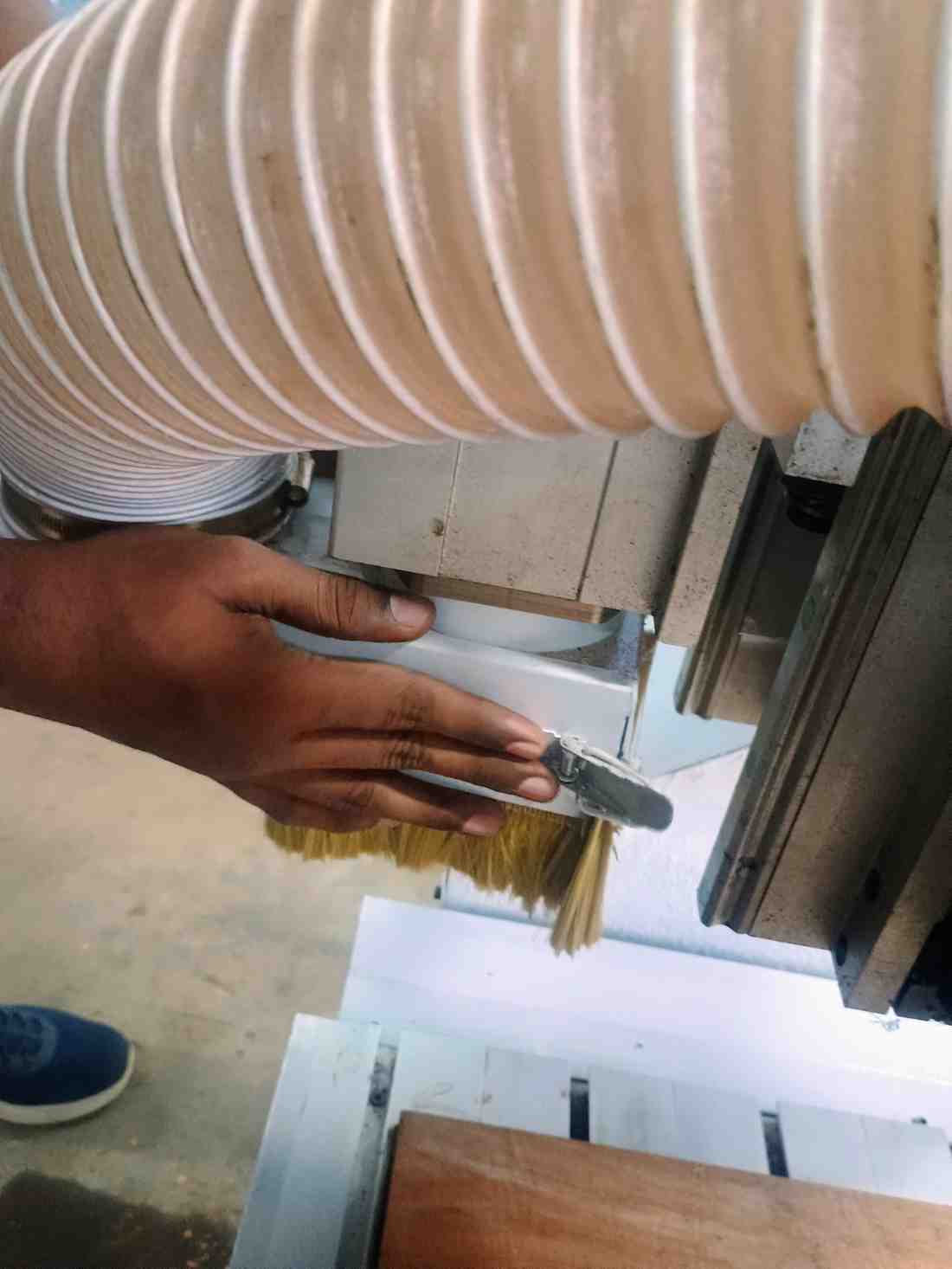
In inner we can see the tool holder like this
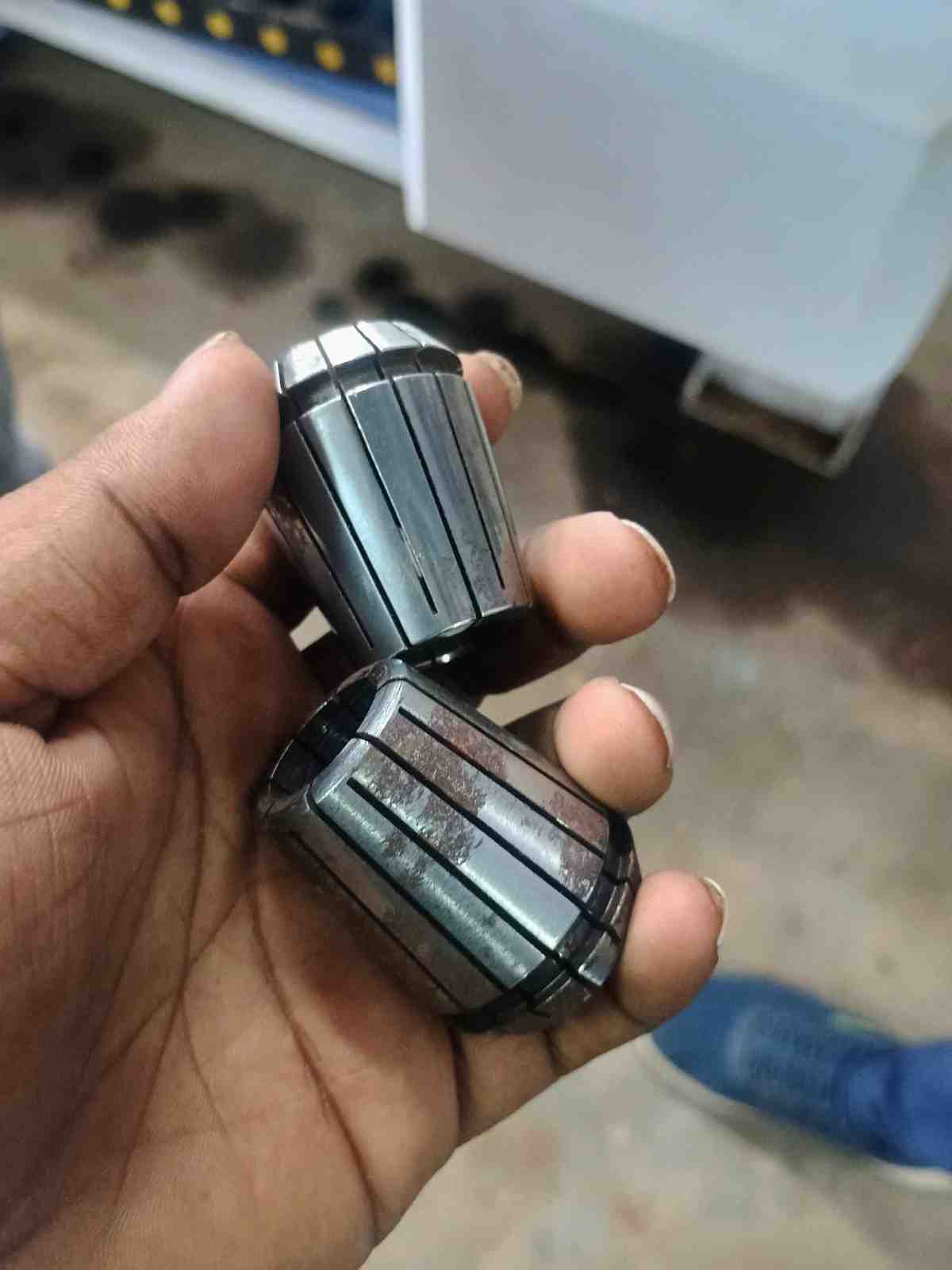
In the spindle some brush are also placed for cleaning the dust while the machine is running. We can controlled the spindle movement by using this controller pad
I used the End mill 6mm tool bit for my milling operation according to my design.
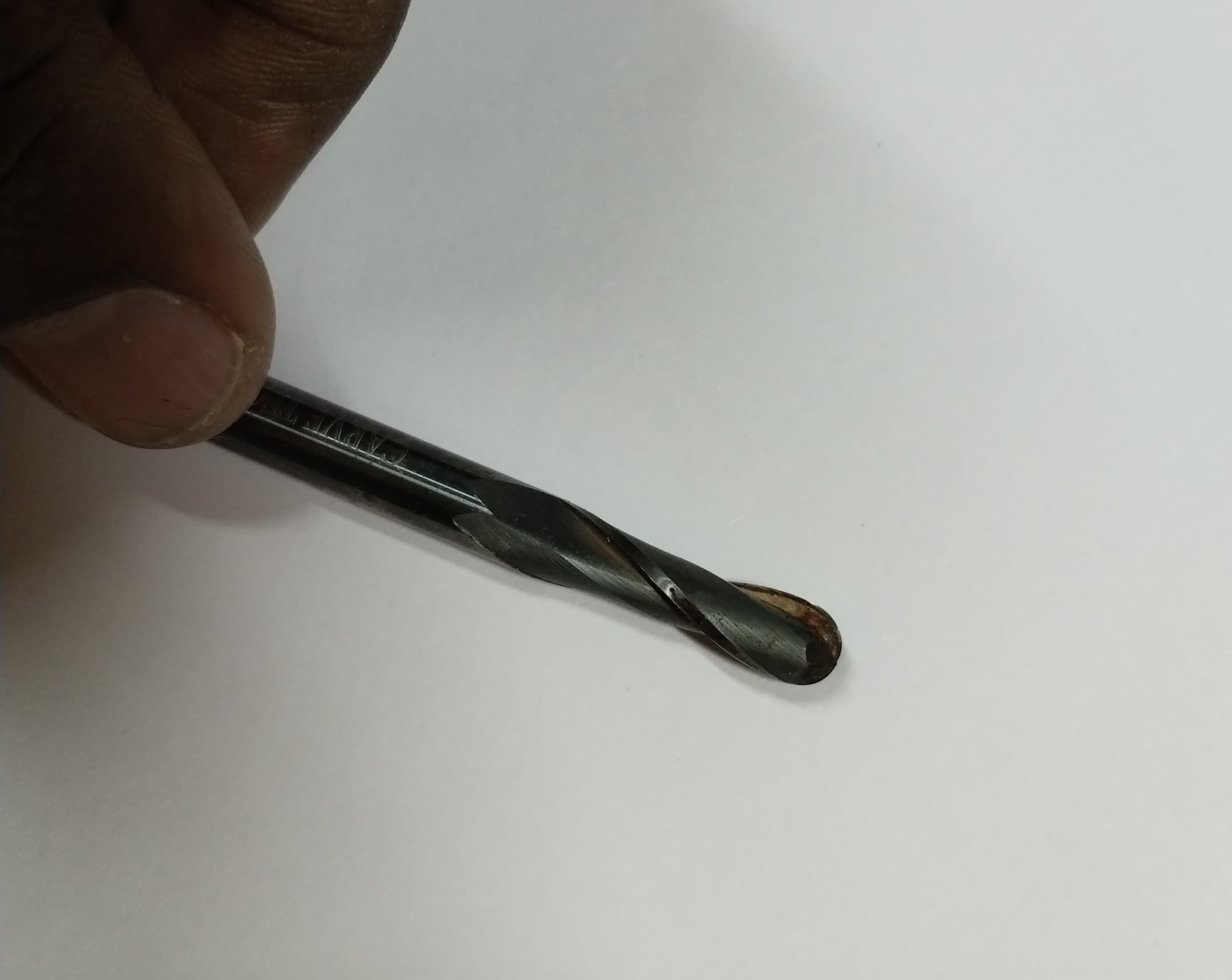
I tightening the tool holder as much as possible without getting slip.
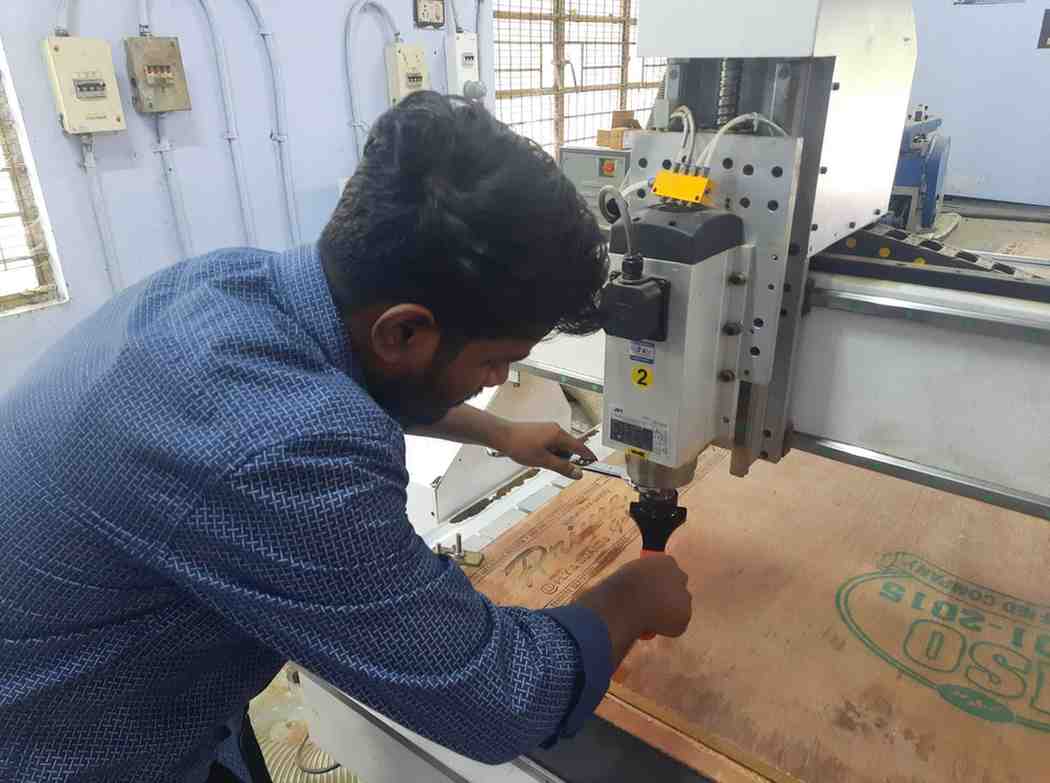
I also set up the workpiece on the bed of the Milling machine by tightening the L clamp.
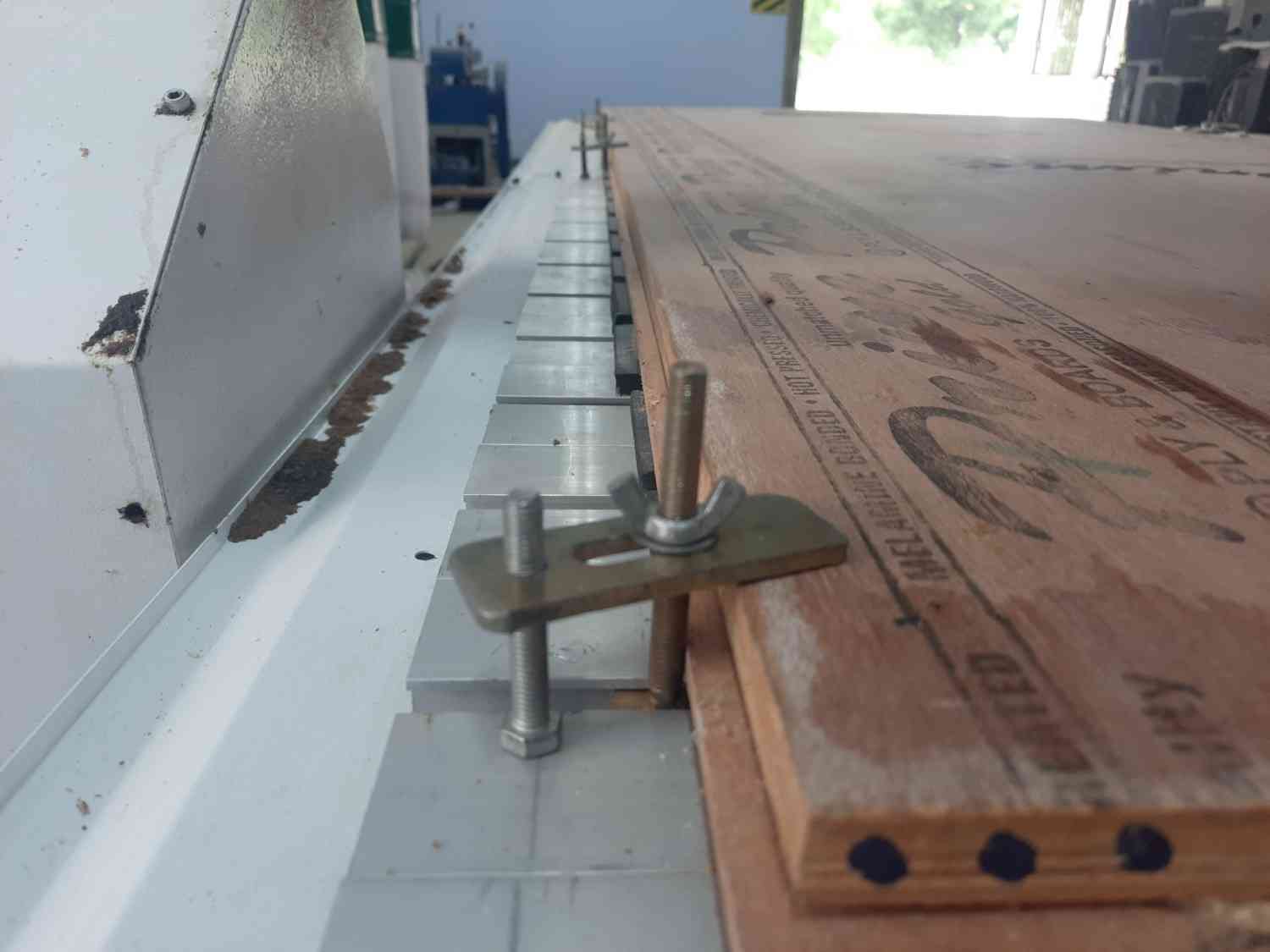
After tighterning it hardly I moved the spindle towarsa where I want to milling.
By adjusting the Spindle in Z axis I ensure the tool only touch little bit the surface of the workpiece.
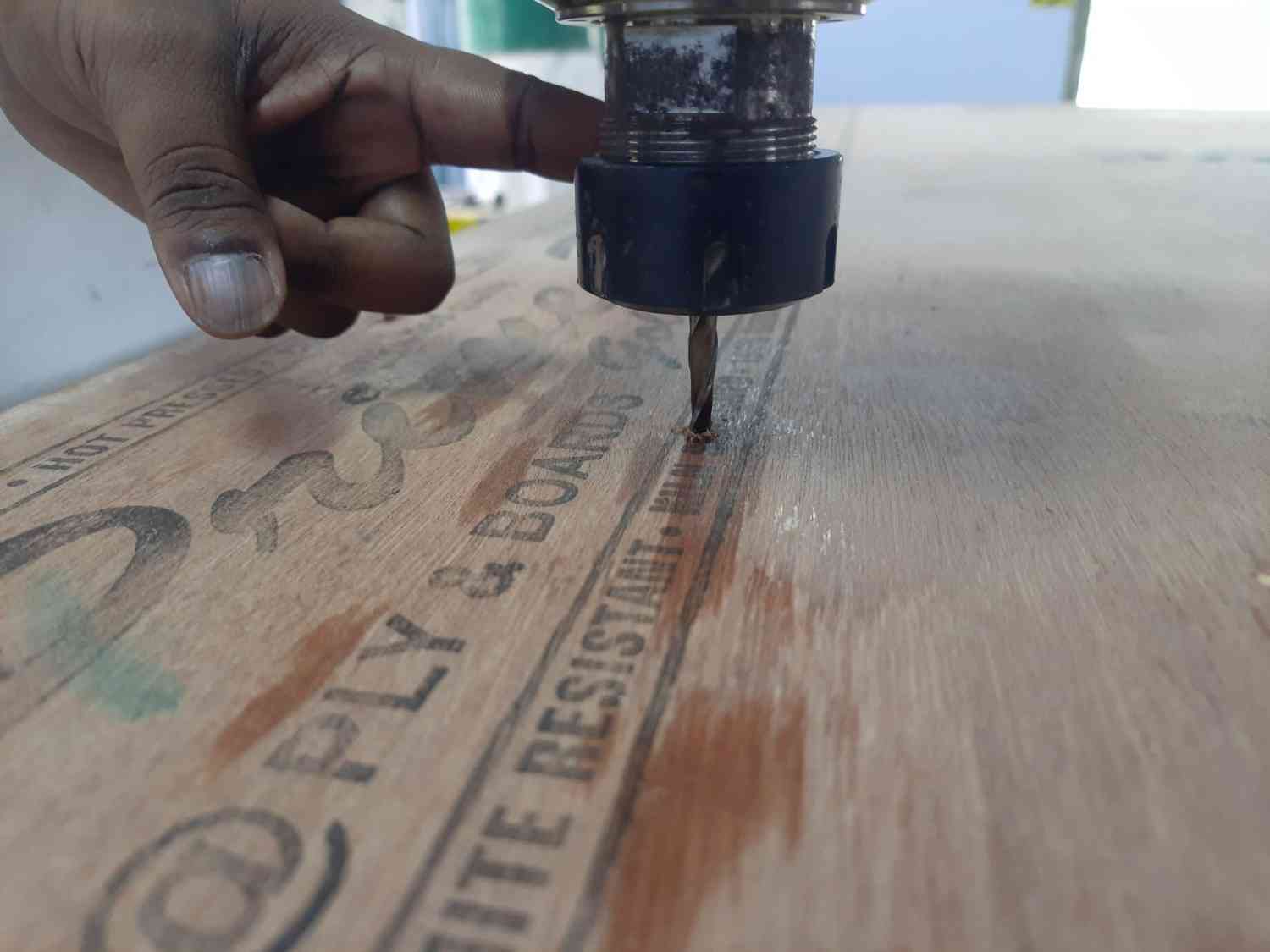
I import the tool path G-code into the machine, start to operate the machine after adjusting the tool into the spindle, make sure the tool is tighted fully otherwise it leads to cause any damage.
Then place the wood on above the machine bed tightly, and start running.
I cross checked the cutted parts whether it is cutting properly or not
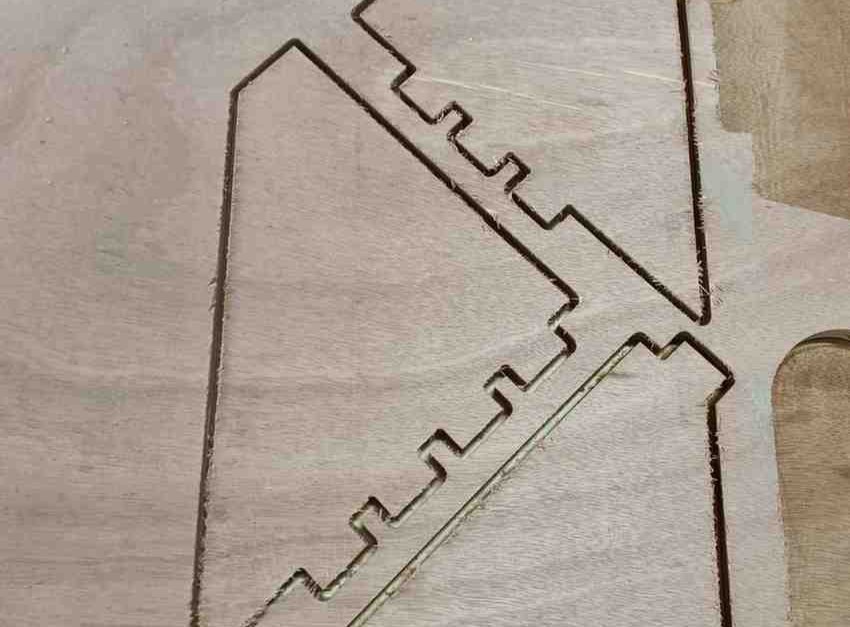
After cutting down properly I took out my cutted parts from the machine bed.
Then I assemble the parts after did some patch work