About me!
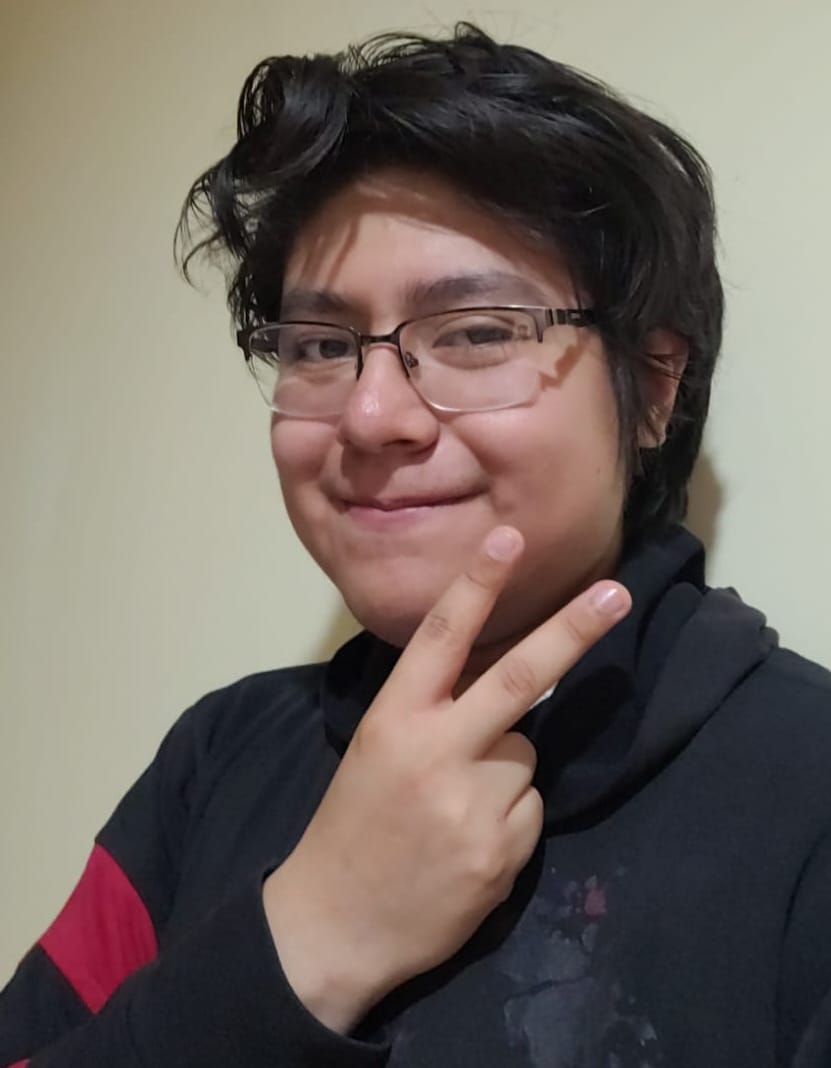
Hello! My name is Erwin Efrén Vivar Tobón. I'm from Puebla, Mexico, and I was born on April 20, 2004 (fun fact, it’s a date that some people find quite memorable...). That makes me 20 years old. I'm currently in my 6th semester of Mechatronic Engineering at Universidad Iberoamericana de Puebla.
I’m not much of a talker, so if I don’t say much, don’t take it the wrong way. I promise it’s nothing personal! I’m actually pretty friendly, and if you ever need a hand with something, I’ll do my best to help :)
I enjoy anything related to video games, electronic music, anime, and those tricky math puzzles that keep me up for three nights straight.
I’d say my strengths lie in calculations and programming, but right now, I’m working on improving my skills in manufacturing and building things from scratch.
Here you can see my Student agreement
Projects I have been involved in!
Throughout my career I have been involved in various projects. Some of them are...
- A CNC "laser cutter":
- A car that follows various predefined commands through logic gates:
- A submarine:
- An animatronic, head octopus an tentacle control:
Honestly, this was my first major project when I started university, and I lacked experience in many areas. As a result, the CNC had several flaws, one of them is that the laser failed at the last minute, the proyect ended up as a drawing CNC machine holding a pen instead of a laser. Despite its imperfections, this project taught me valuable lessons and became a key source of motivation during my early years in college.
This project has an interesting background. Initially, my team and I planned to build a basic drone with simple movements (turn left, right, move forward, etc.), but due to its complexity and the final requirement of implementing a state machine, we had to change direction. Instead, we adapted the idea to a terrestrial vehicle, using our drone progress to design a car that followed different patterns in a loop. In my view, we created a state machine of multiple state machines, allowing infinite pattern additions without major changes to the logic circuit. Beyond the technical skills gained, this project helped me overcome my fear of electronics and sparked an ambition that I now have to balance—sometimes, I find myself wanting to bring fictional ideas to life, even if they seem impossible or poorly planned.
This project had its ups and downs. On one hand, it helped me realize my potential in programming, but it also exposed my lack of skills in design and mechanics. While the electronics and code for controlling the submarine worked flawlessly, the structural aspects faced challenges. Although my main focus was on electronics, I often felt overwhelmed when trying to contribute to the mechanical and design aspects.
In the end, a sealing failure caused water to leak into the structure just four days before delivery, damaging multiple components and forcing us to rethink and reinforce the sealing in every possible way. Fortunately, we managed to get the project afloat, though not exactly as we had originally envisioned.
This project is recent—my partner and I presented it less than three months ago. I have to admit that I made several mistakes, but I see them as lessons I won’t repeat. Our idea was to create an animatronic inspired by an octopus, but ambition got the best of us, and we aimed for a nearly human-scale model. We divided the tasks: I was in charge of the head, while my partner worked on the tentacles.
His tentacles turned out great, but my head was far from complete. I wanted to replicate expansion, retraction, and smooth neck rotation, designing a complex system with multiple connecting rods, cranks, 12 servomotors, and a 6-DOF mechanism inspired by FDM delta printers. My biggest mistake was overestimating the servos' strength and not considering weight and torque properly.
As a result, I shifted my focus to controlling the tentacle system, integrating AI (Mediapipe) for gesture recognition so the tentacles could follow a person. Due to time constraints, lack of sensors, and mechanical limitations, the movement wasn’t perfect, but we made it work as best as possible.
With this project, I completely overcame my fear of designing complex parts and became more confident in using 3D printers and the university’s laser cutter more frequently. More importantly, it taught me the value of taking a more realistic approach to my projects.
Unfortunately, I had to reset my computer to factory settings due to an irreversible error, resulting in the loss of all files. As a result, I don’t have any photos or documents to showcase these projects. I might still have something saved on my phone, and when I have time, I'll check my gallery and upload some photos...