Computer Controlled Cutting
This week, we explored computer-controlled cutting, a subtractive fabrication method. We're getting hands-on with tools like laser cutters and vinyl cutters to dive into different manufacturing techniques. The to do list for this week is:
- Create a paramteric design using CAD to be laser cut and assembled in multiple ways (for extra credit include elements that aren't flat)
- Create a design (eg. logo sticker) to be vinyl cut
- Group assignment: do your lab's safety training characterize your lasercutter's focus, power, speed, rate, kerf, joint clearance and types
Joint types,images from Neil's lecture
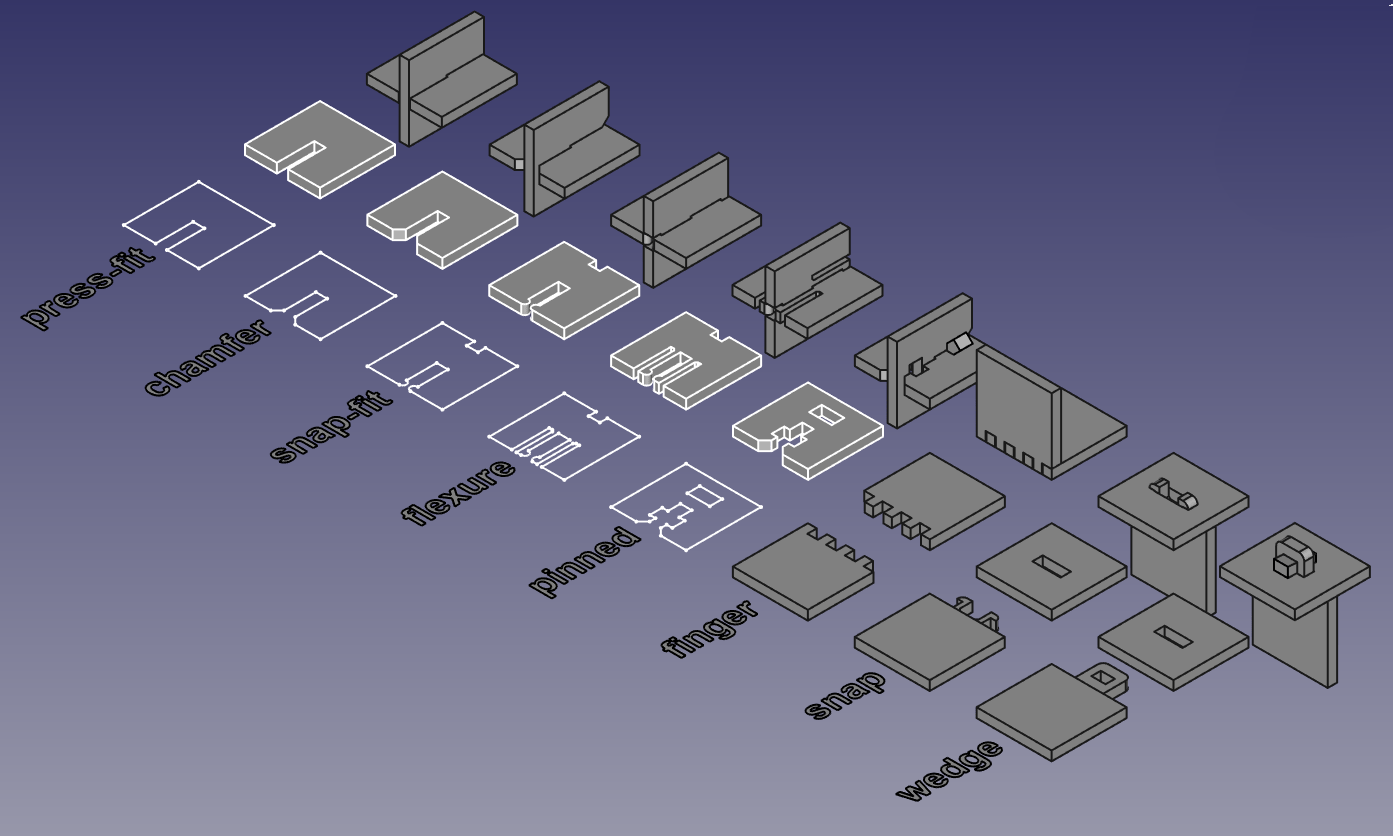
Notes from lecture:
- Try Rhino/grasshopper geometry nodes
- Play with contraints in Free Cad/splines
- Look up fusion 360 slicer
- JOINTS: A press fit joint won't fit if slightly misaligned wihtouht a chamfer..
A chamfer joint will work even if slgihtly misaligned, the chamfer helps align it.
Snap fit joint has a bump on insertion peice.
A flexure joint is like a backback buckle. It's mechincally bi-stable to it clicks into place.
The stongest joint is a Pinned joint. (much more complex)
A Finegr joint is good if you want to make a right angle. But it doesn't hold very well.
A Snap Joint is better, stronger even is a Wedge joint that has a paper wedge tapped into place (like in woodworking) - A laser cutter burns and melts. It produces combustion products. Done correctly these should be pushed down by the air assist and they sucked out by the exhaust. If you smell something you should yell.
- The path the laser cuts needs to be offset by half of the width of the beam, this process is called offsetting. You need it to make good joints.
- Good cardboard bows when bent. Cardboard is the best material for this week.
- Fabric & Pasta can be laser cut
- Fibre lasers are shorter wave length and they can do metal cutting
1. Design too complex for fusion
I stared with my logo with the idea of having them connected to a parametric stand like a spikey tree. I imported the SVG from illustator but the spline wsn't importing with green handles and would not allow me to modify. I travelled to the lab (2 hour drive) on this day so was lucky to have Clairs help. we tried workshopping though I eventually just re drew the logo in fusion and then we started trying to make it parametric. Due to the various curves and holes it porved extremely difficult, we eventually deemed it impossibe.
2. Trying a golden ratio spiral instead since it's based on math (it didn't work)
Claire suggested I try a golden ratio instead (as it's imilar to my logo, and based on math) and I eventually listened to her. I found a tutorial on YT on how to create a golden ratio in Fusion and followed it. Then I set up the parameters as Claire showed me how to do, though did not have much luck sclaing. Clairethen tried setting up a few different paraeters and we got close but still couldn't get the spiral to scale without warping.
3. Trying the most simple shape I could think of (it still didn't work)
As a final attempt before the drive home, I made a very simple shape and set up parameters on it. This was 99% working, though the long leg kept offstting itself on the Y axis. We gave up and cut some stickes with the vinyl cutter! I will return to the CNC design attempt later this week.
4. Fail proof - following a parametric fusion tutorial
I followed THIS tutorial