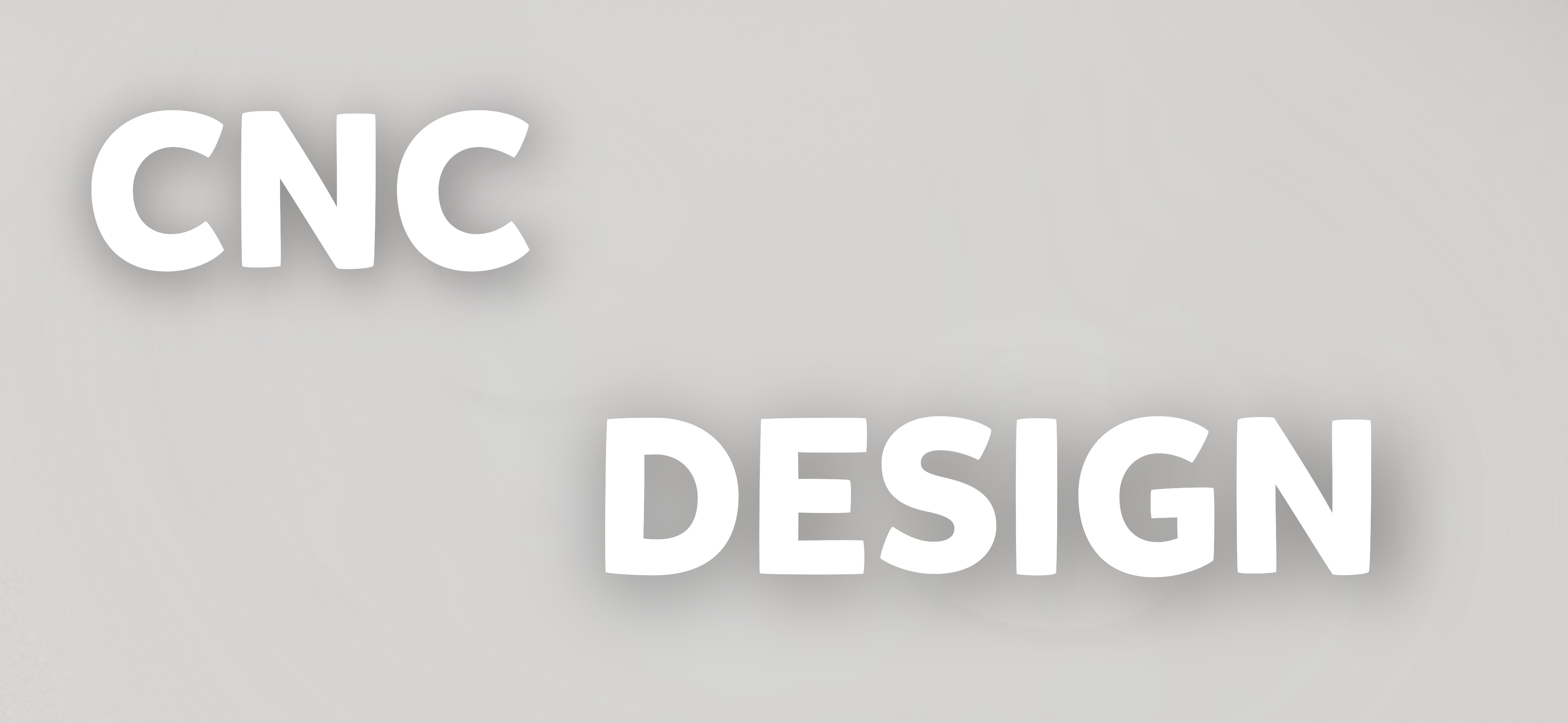
Gotcha Extravaganza
As a team, we decided to take on a unique challenge: designing a CNC machine for vertical paintball art—and, fortunately, it worked! Although I was involved in much of the creation process, we each focused on different areas based on our expertise. I was part of the design team. In this week's documentation, I'll detail my individual contributions.
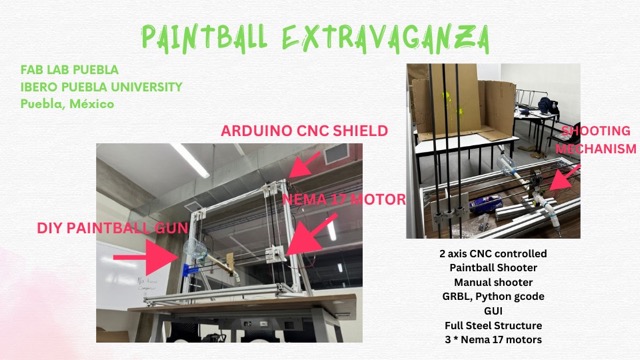
Design proccess
Sketching and brainstorming
First off, I collaborated with Bernardo Lamuño on the design of the CNC. We began by consulting with other team members to clarify certain programming aspects we didn't fully grasp, aiming to understand each part of the machine thoroughly. After that, we moved on to sketching to develop a functional design. Below are some of the initial sketches from this process. Once we had a solid plan, Bernardo took over and completed the modeling in Fusion 360.
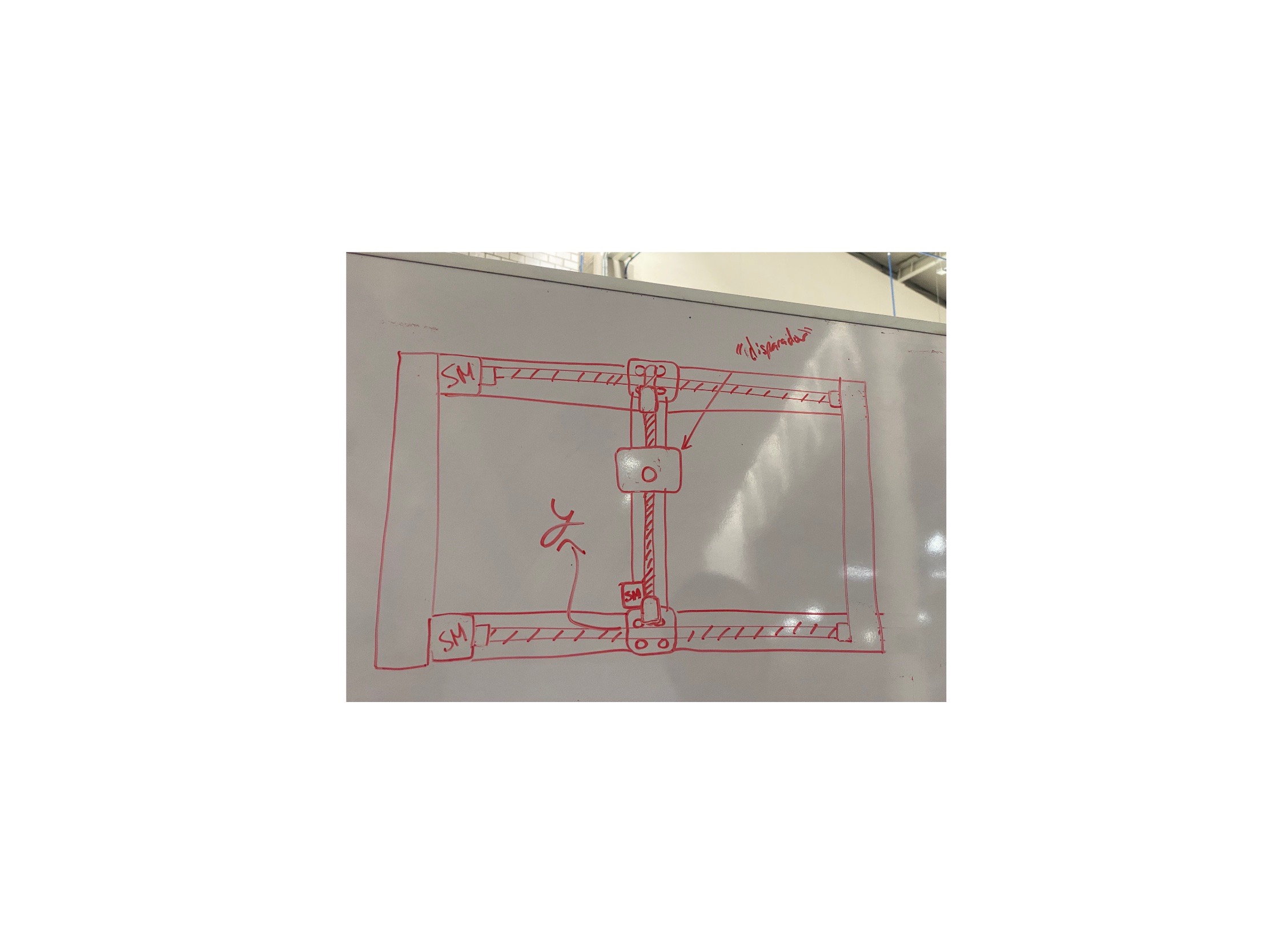
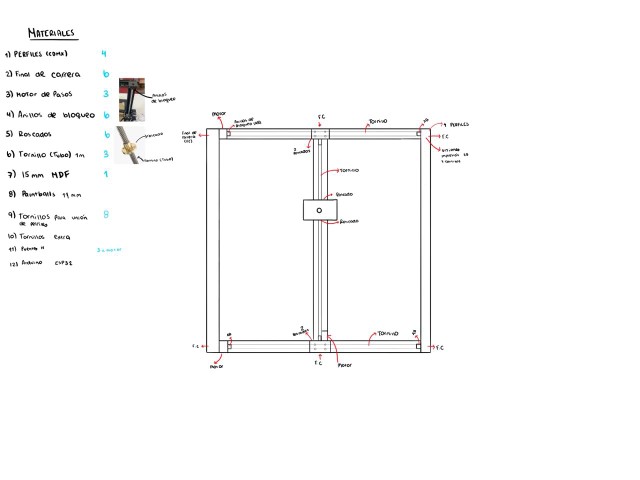
3D modeling
Once Berna and I had figured out the design. Berna continued to model it in Fusion 360 since it was easier to do it in one computer only.
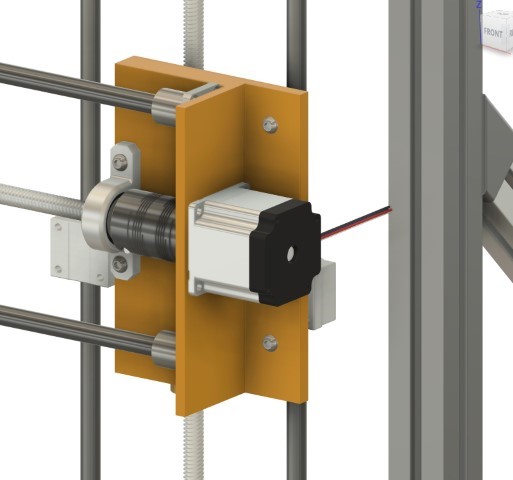
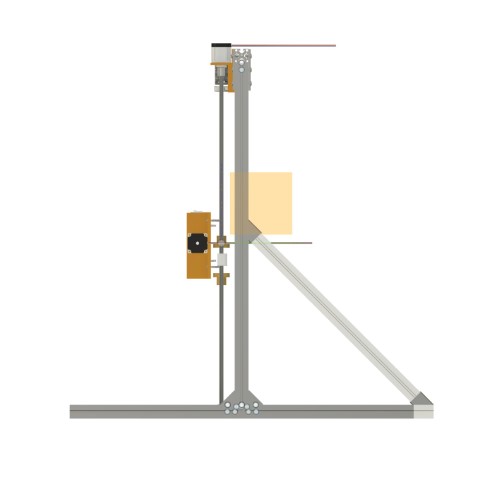
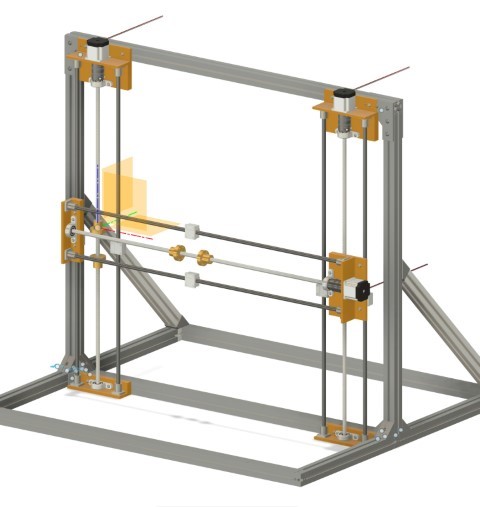
Chossing parts for the CNC
Berna and I went to look for the materials. It was a bit challenging since we had no previous experience with most materials but with a little help we were able to select them.
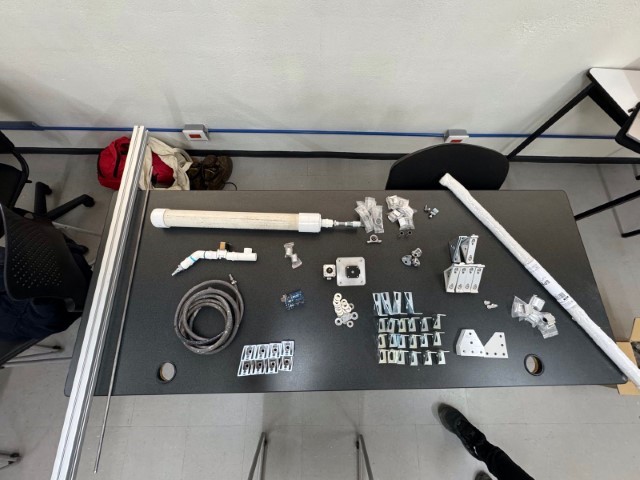
Finding paintballs
I was also responsible for purchasing paintballs, which proved challenging because in Puebla, all the paintball facilities only offered one color, and we needed at least three. After visiting each location and being turned away, I finally discovered a place where I could buy yellow paintballs in batches of fifty.
Designing the paintball dispenser´s base
Designing the base for the paintball dispenser was quite challenging, as I wasn't sure what the ideal design should look like. Initially, I sketched out a few ideas. Eventually, I decided to use a laser cutter and 3 mm MDF. I took measurements from the existing paintball dispenser and then designed the base in Fusion 360. This approach allowed me to create a parametric design, making it easy to adjust the size if necessary.
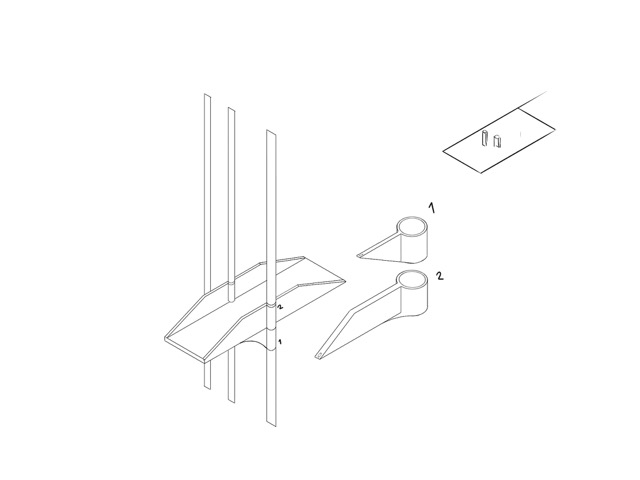
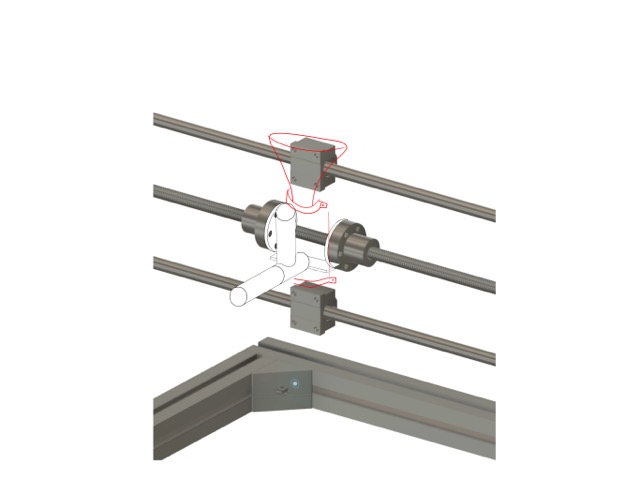
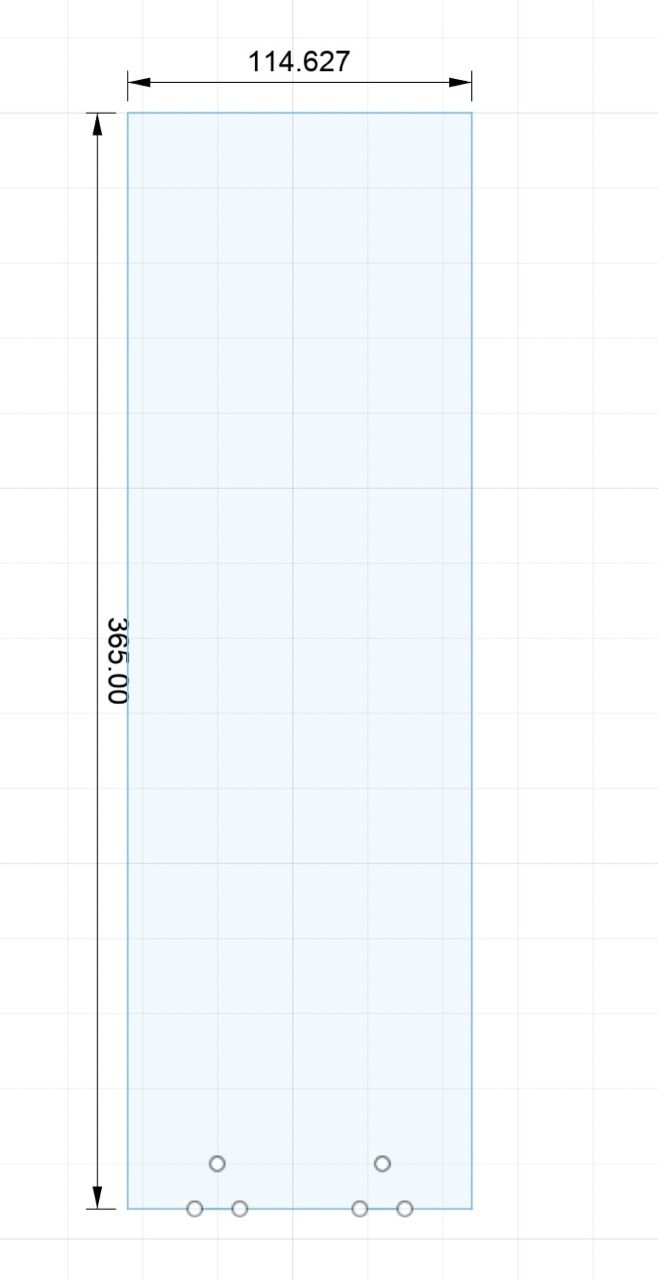
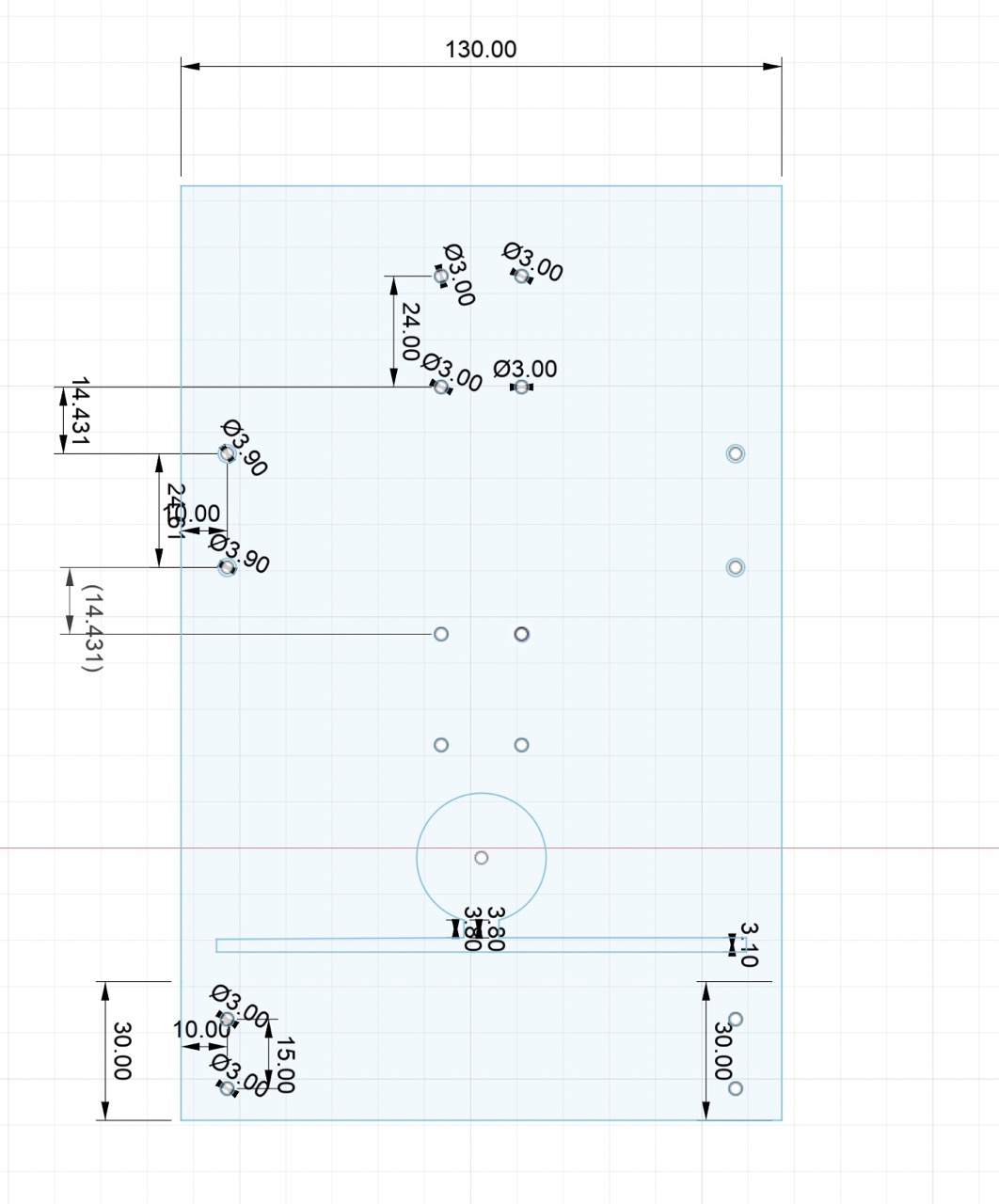
Result
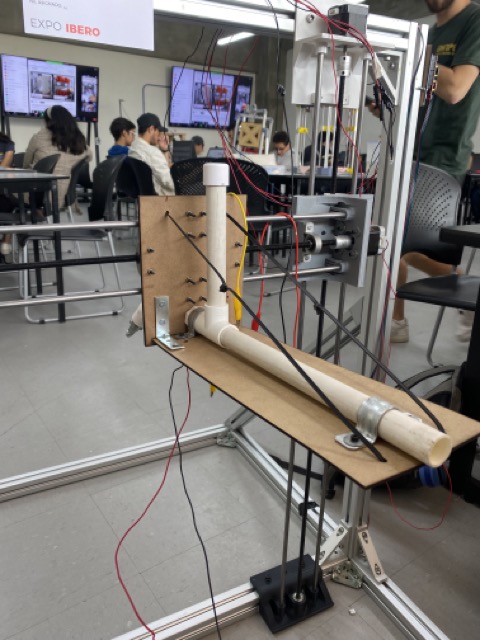
Designing joints
I also designed a joint to connect the different motor bases. This joint needed to be compact and capable of linking the threaded rod to the bases. I opted for a semicircular shape and incorporated a nut within the joint to ensure a secure fit. For this I also used Fusion 360
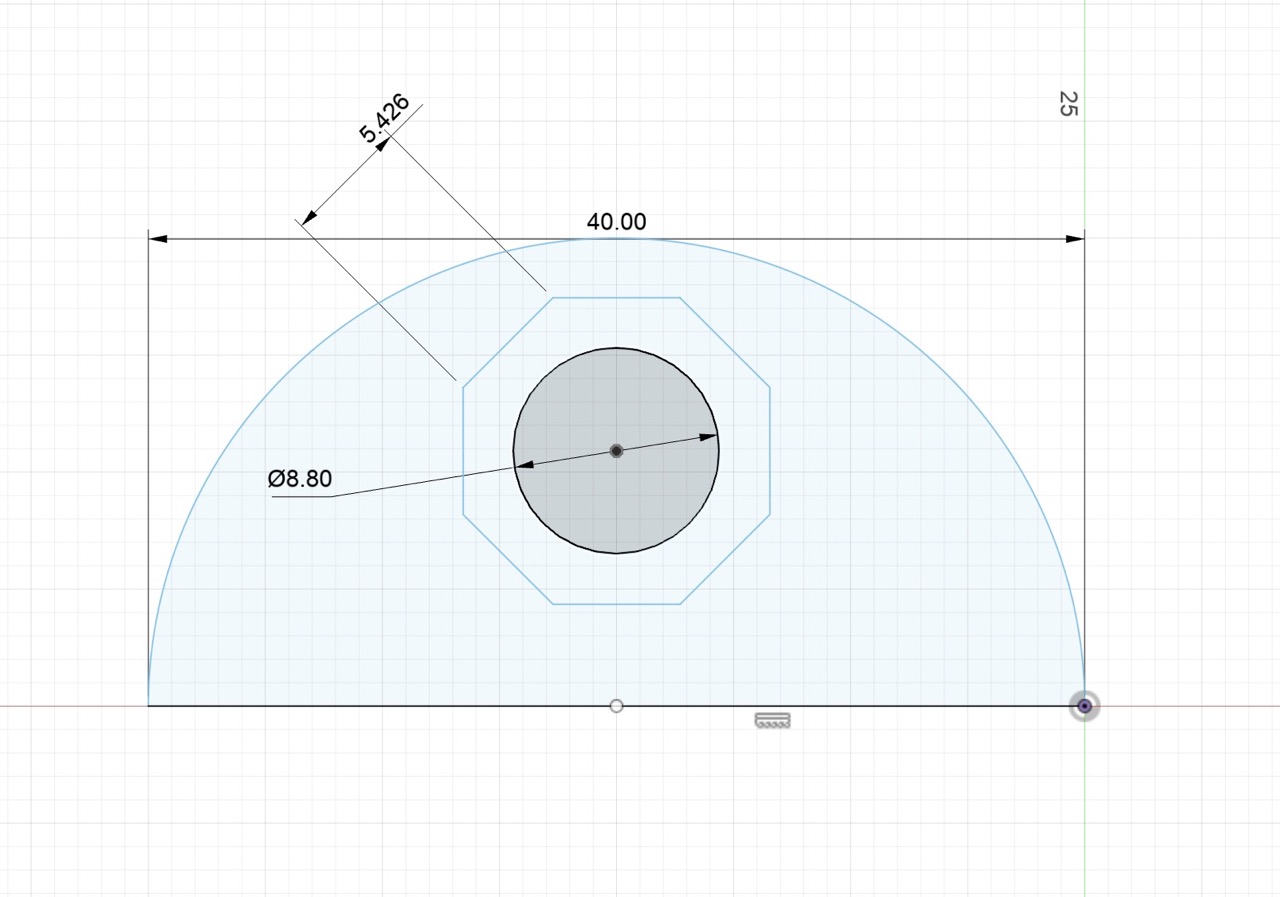
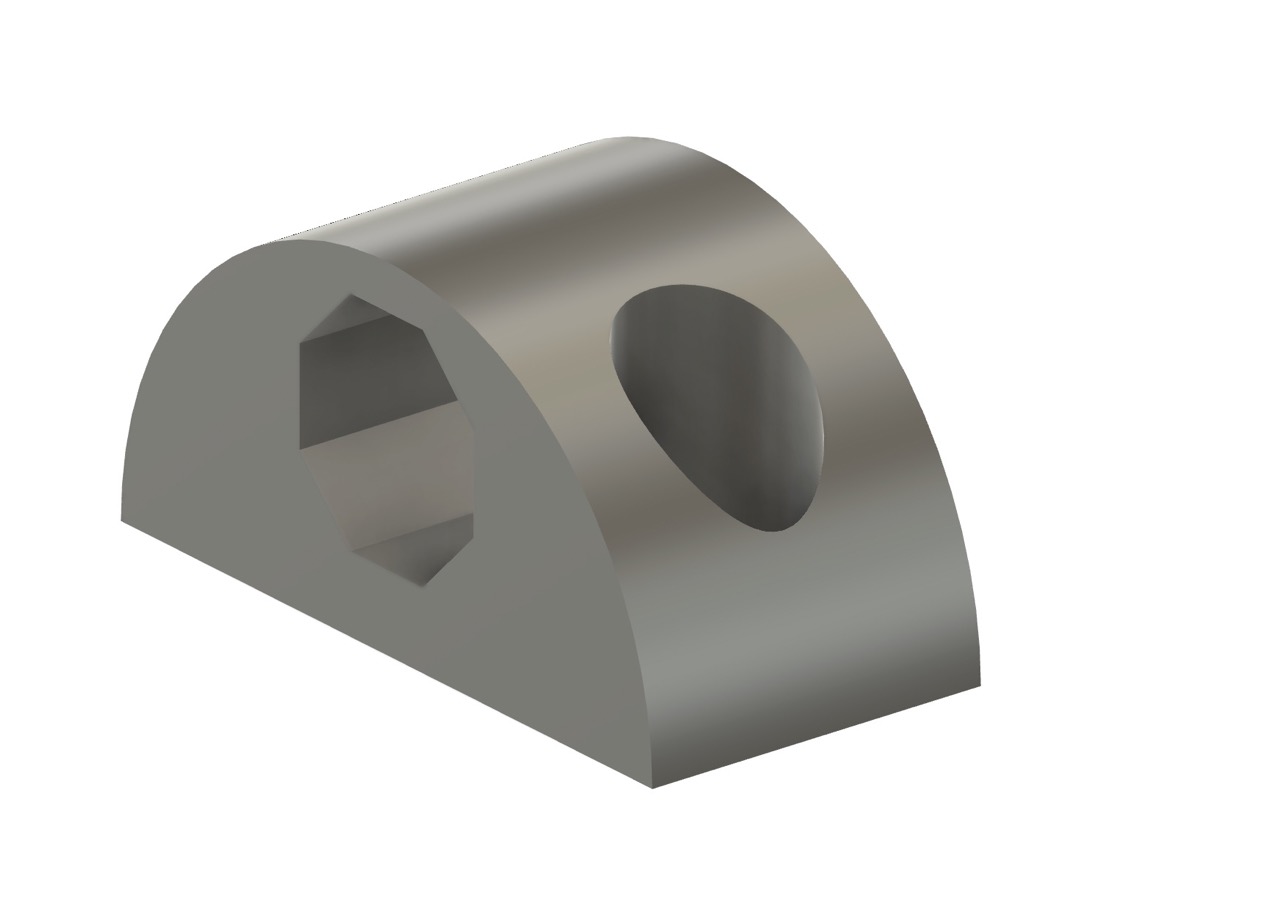
Result
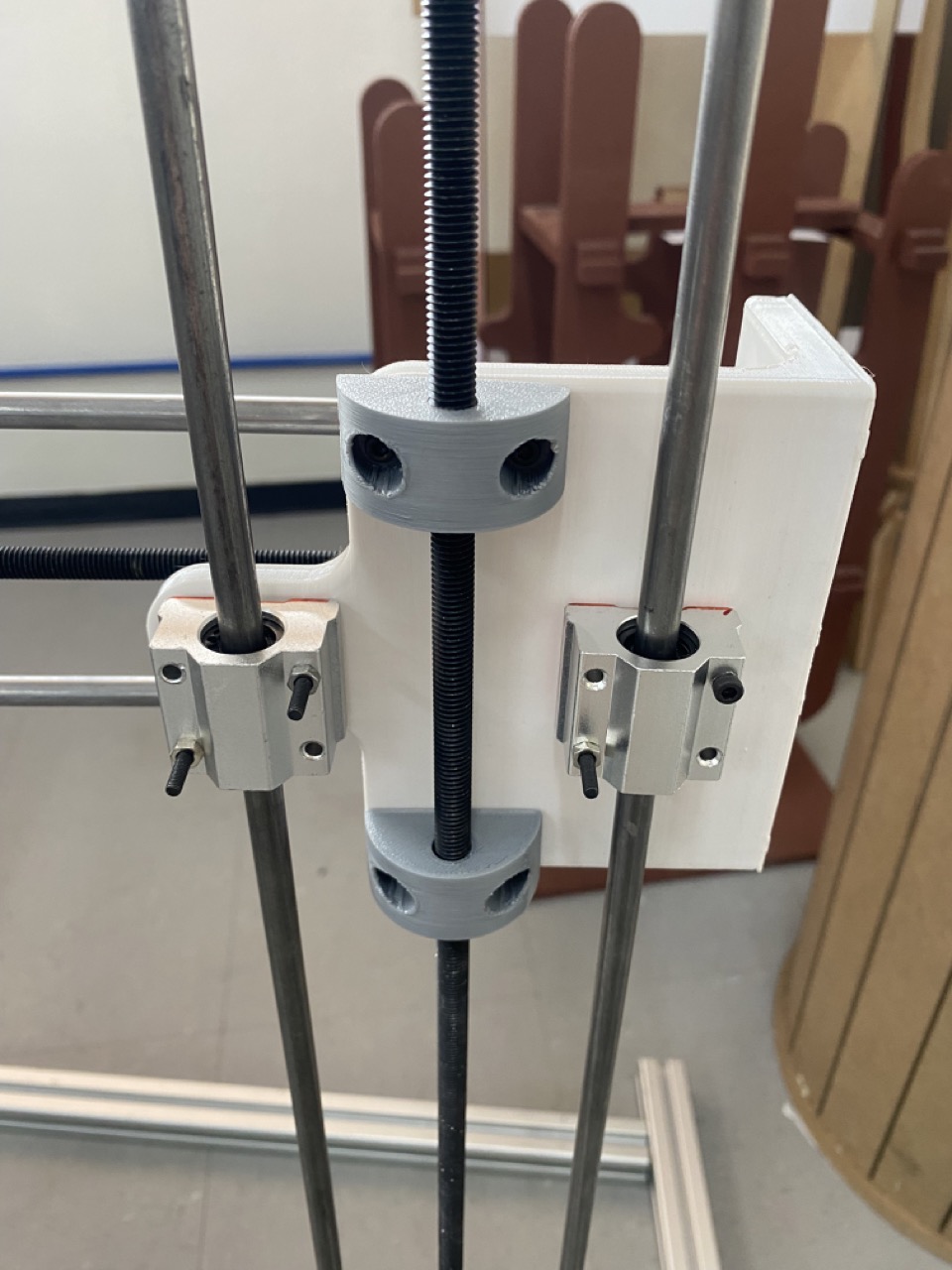
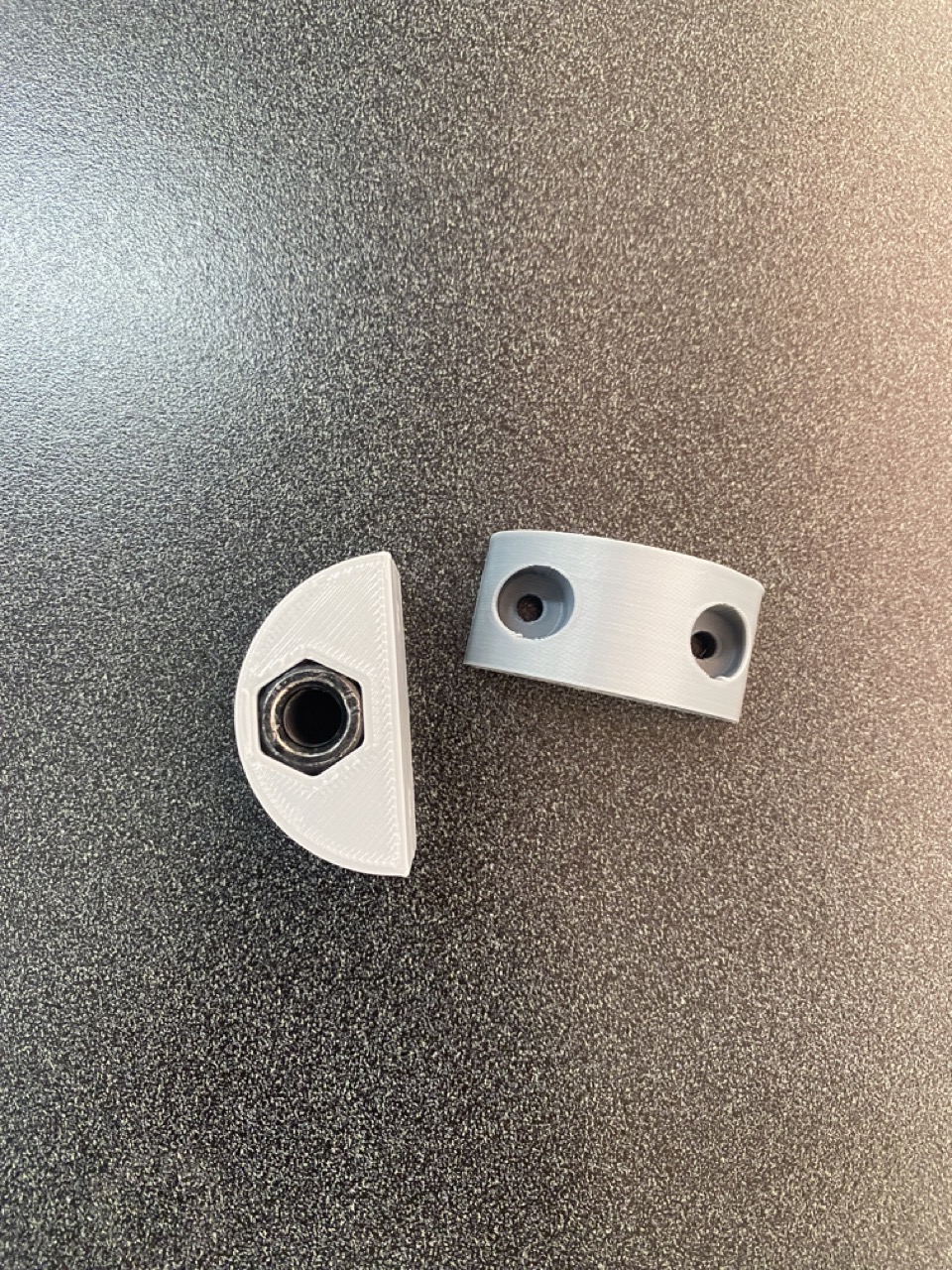
Designing a base for the Arduino
I thought it would be beneficial to create a dedicated base for the Arduino board to ensure it was securely attached to the CNC machine frame. To achieve this, I found a detailed datasheet online with the measurements of the Arduino board. Using this information, I designed a 3mm MDF base in Fusion 360, tailored for cutting with a laser cutter.
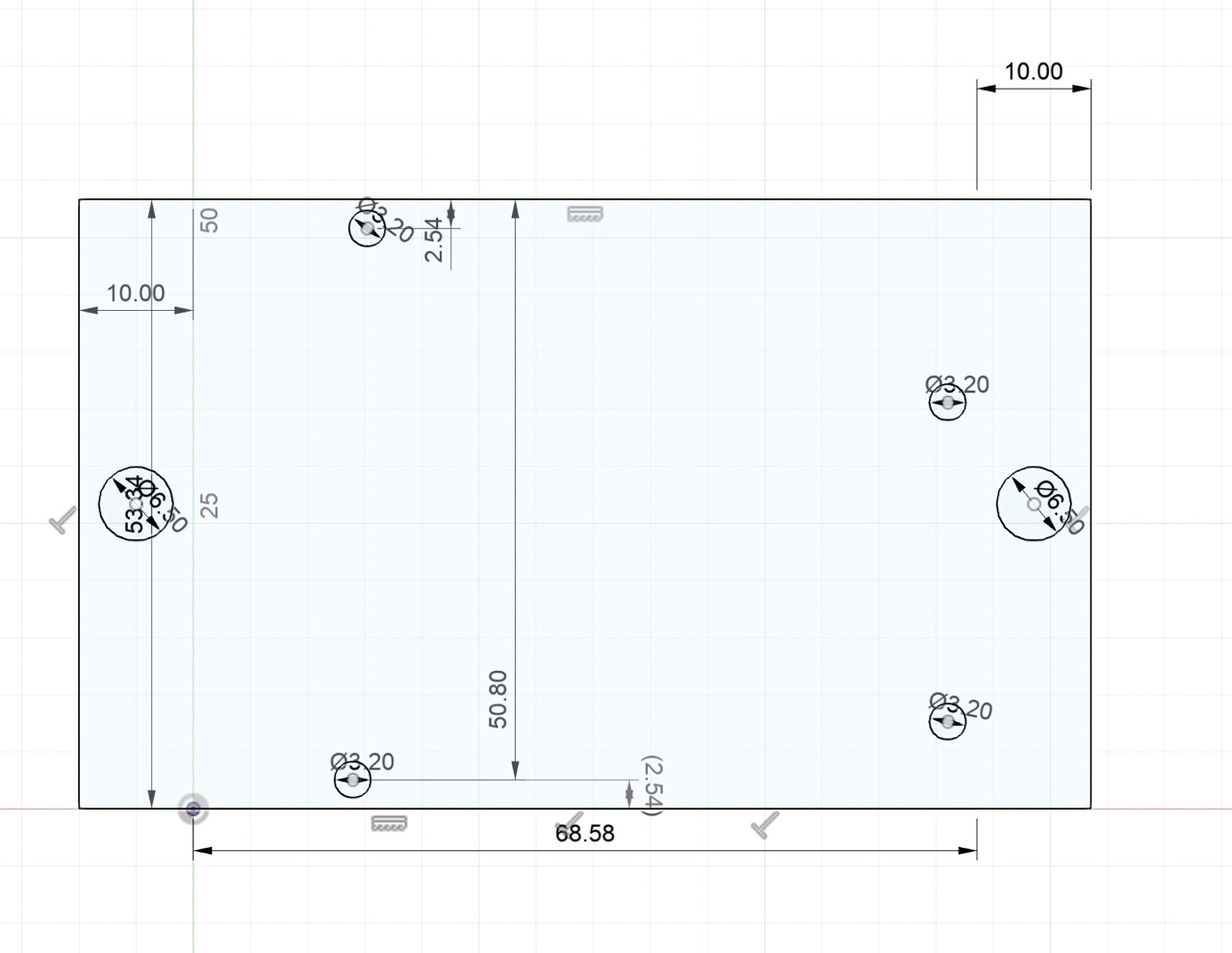
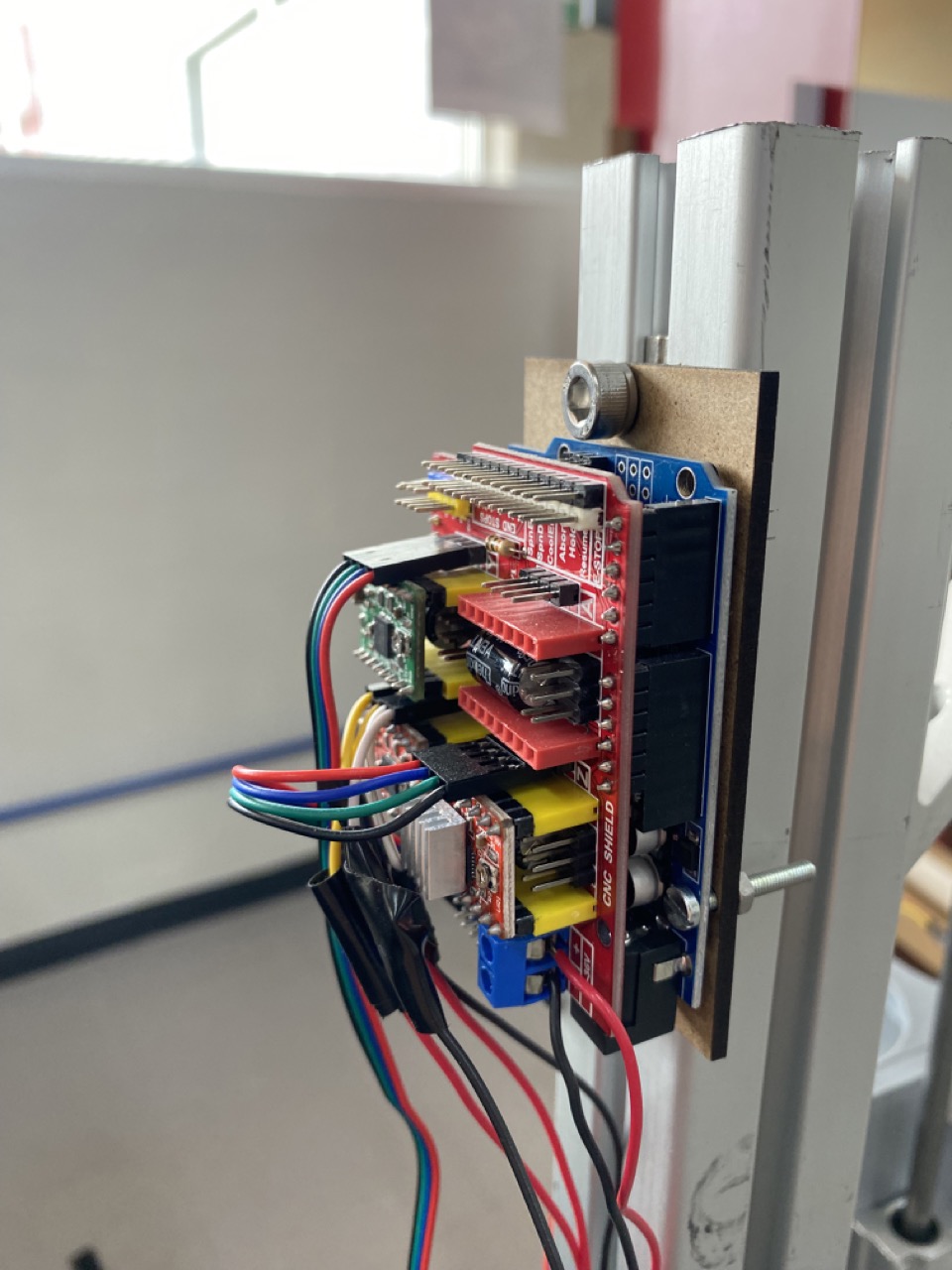
Designing bases for the threaded rod
I designed a base for the threaded rod, but unfortunately, some parts broke. As a result, we never got to print this initial design. Instead, we revised it to create a stronger version.
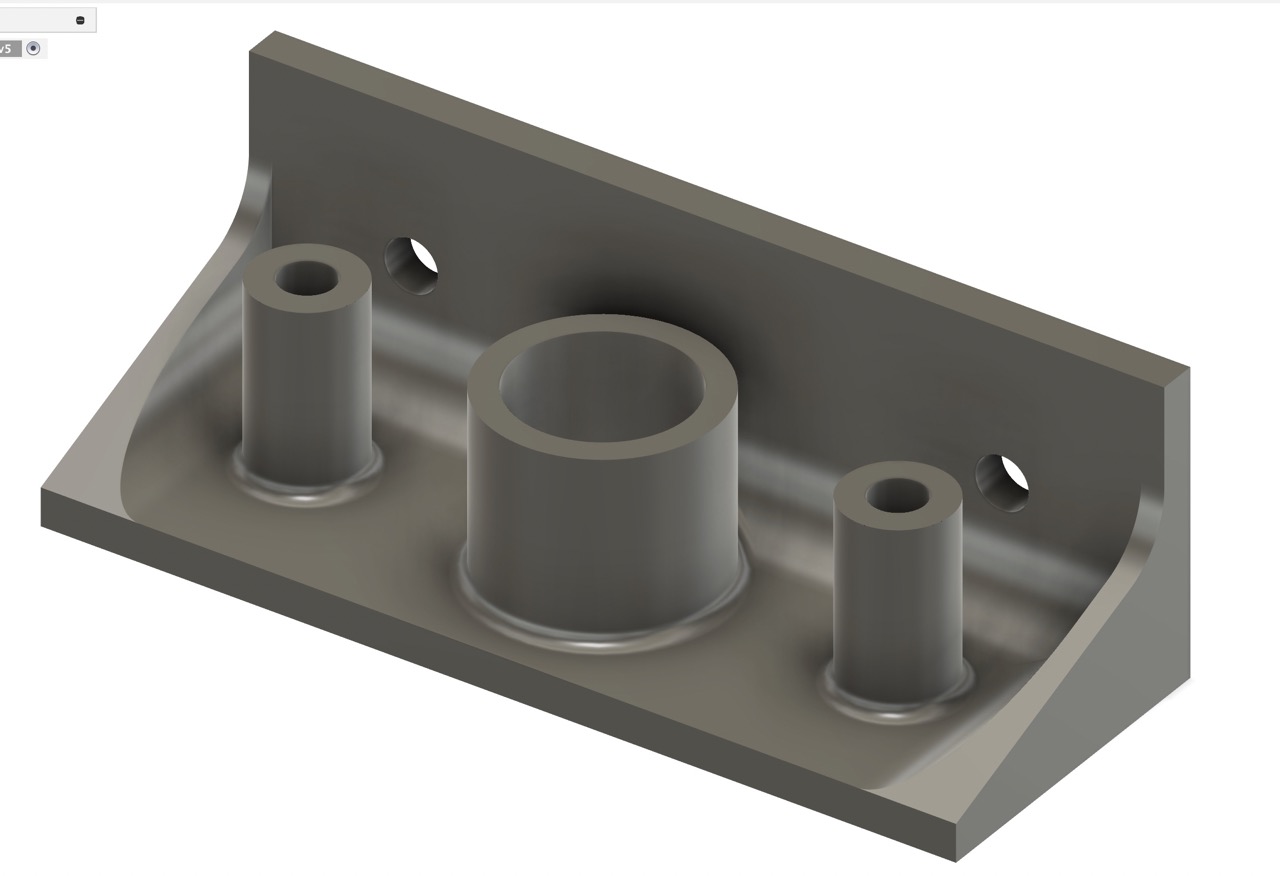
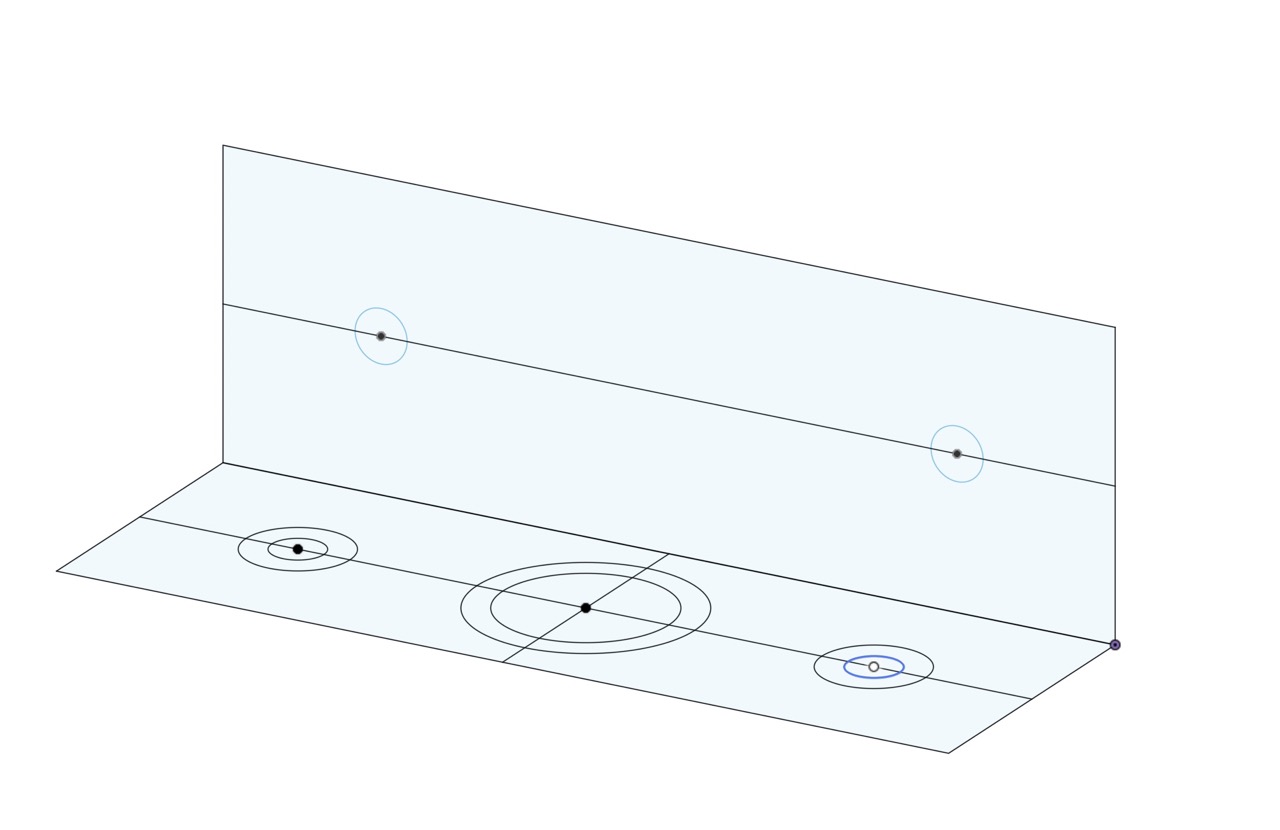
Assembling process
I was actively involved in the assembly process and also participated in purchasing components. Additionally, we tested the paintball compressor and verified that the motors were functioning properly.
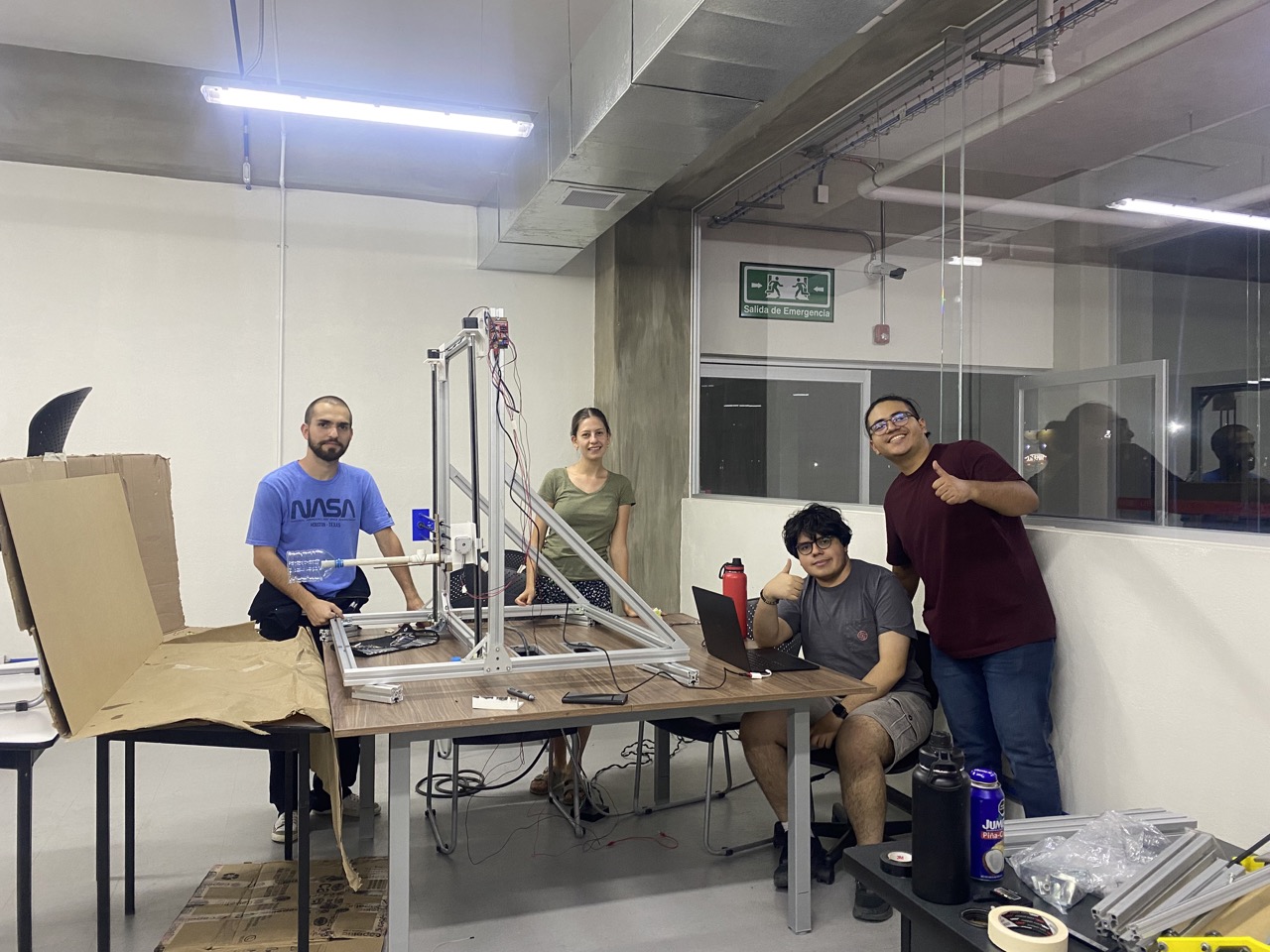
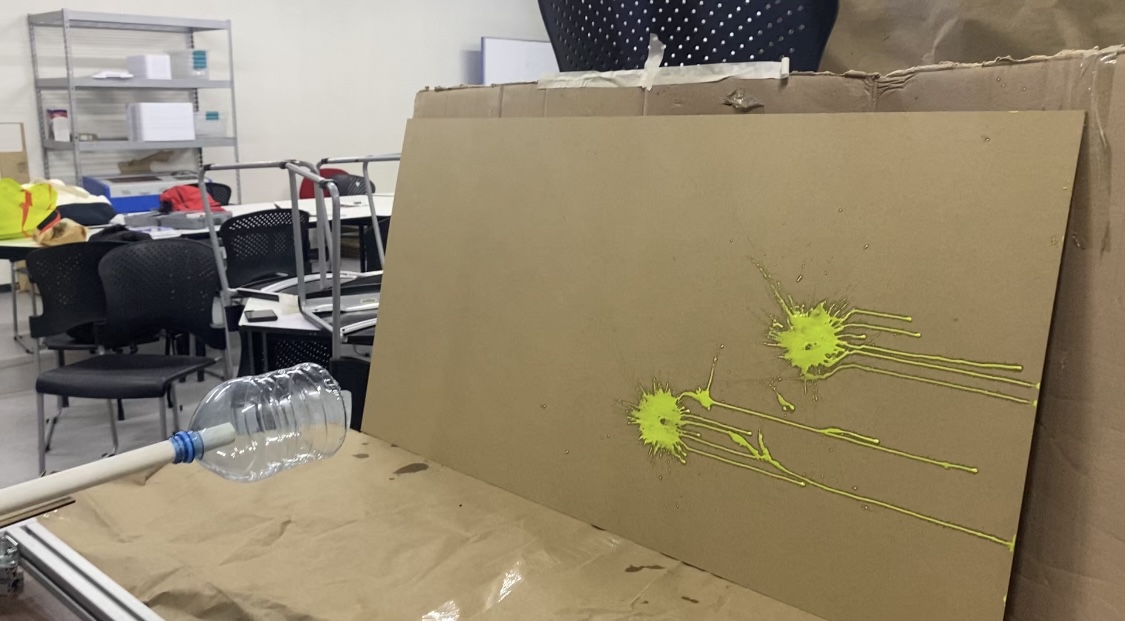
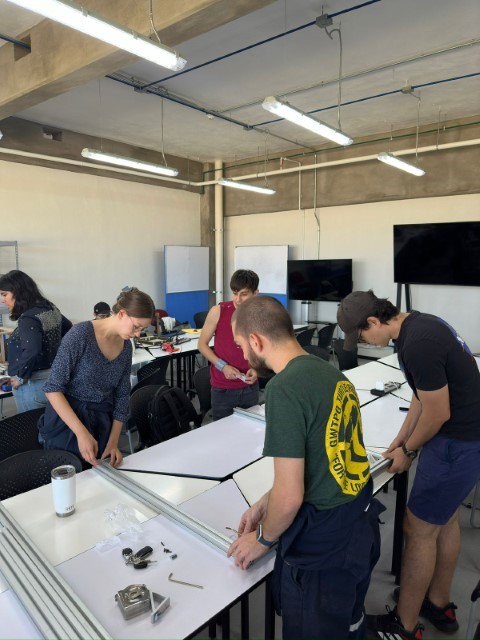
Challenges faced
As an industrial designer, I encountered several challenges. Initially, I felt overwhelmed by the array of materials needed and the operation of the CNC machine. However, after engaging with the team and asking numerous questions, I gradually gained a clearer understanding of our tasks. Another hurdle was figuring out my role within the team. Initially, I assumed the engineers had a better grasp of the project, but I soon realized the value of my design skills—such as sketching, modeling, and 3D printing—which proved essential to our success. I took a proactive approach, taking responsibility for sourcing many of the materials and components, including the challenging task of finding paintballs, which we fortunately accomplished. As a team, we also faced issues with time management and getting the motors to function correctly.
TEAM WORK
Teamwork was crucial to the success of this project. After many hours spent working together, I realized that our collaborative approach was highly effective. It had been a long time since I'd found working in a team to be more advantageous than working alone. This project provided each member with the opportunity to showcase and apply their knowledge, skills, and especially their patience. Although we initially divided the tasks, we ended up assisting each other and collaboratively tackled nearly all aspects of the work. It was a wonderful experience that also served as a great way to bond and connect with more people in the Fab Academy course, whom I might not have met otherwise. I am grateful for both the relationships formed and the successful outcome of our CNC project.