Assignments
-
Individual assignment:
- Propose a final project masterpiece that integrates the range of units covered, answering:
- What will it do?
- Who's done what beforehand?
- What will you design?
- What materials and components will be used?
- Where will come from?
- How much will they cost?
- What parts and systems will be made?
- What processes will be used?
- What questions need to be answered?
- How will it be evaluated?
- Your project should incorporate 2D and 3D design, additive and subtractive fabrication processes, electronics design and production, embedded microcontroller interfacing and programming, system integration and packaging
- Where possible, you should make rather than buy the parts of your project
- Projects can be separate or joint, but need to show individual mastery of the skills, and be independently operable
My final project
My final project idea was to make a fruit and seed dryer for the jungle of Peru one of the problems I saw on my trip to Madre de Dios where I had a workshop on agriculture and technology I could hear some problems of people living in these native communities, they have difficulties with respect to the cultivation and drying of their production in cocoa or copazu, which is dried outdoors and in days is ready, thinking of a solution I saw in being able to make automated drying modules where you can control the temperature and humidity depending on the type of seed or fruit that is in the comfort can be modified and adapted to any fruit or seed.
Hero shots
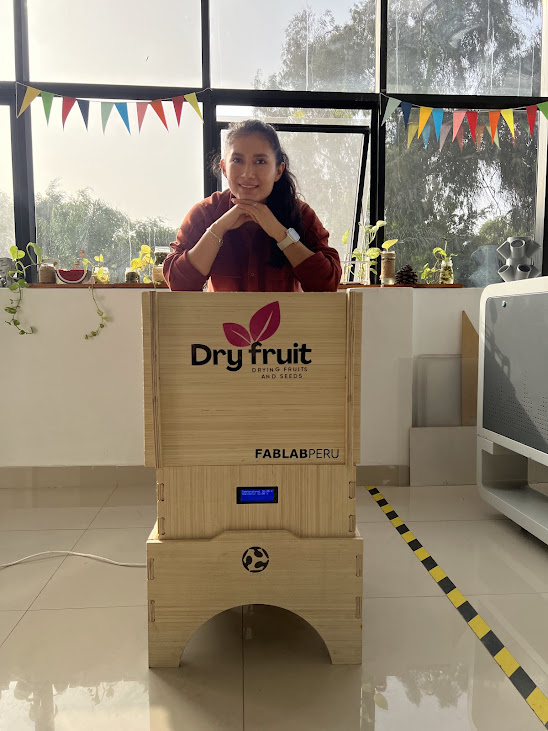
What will it do?
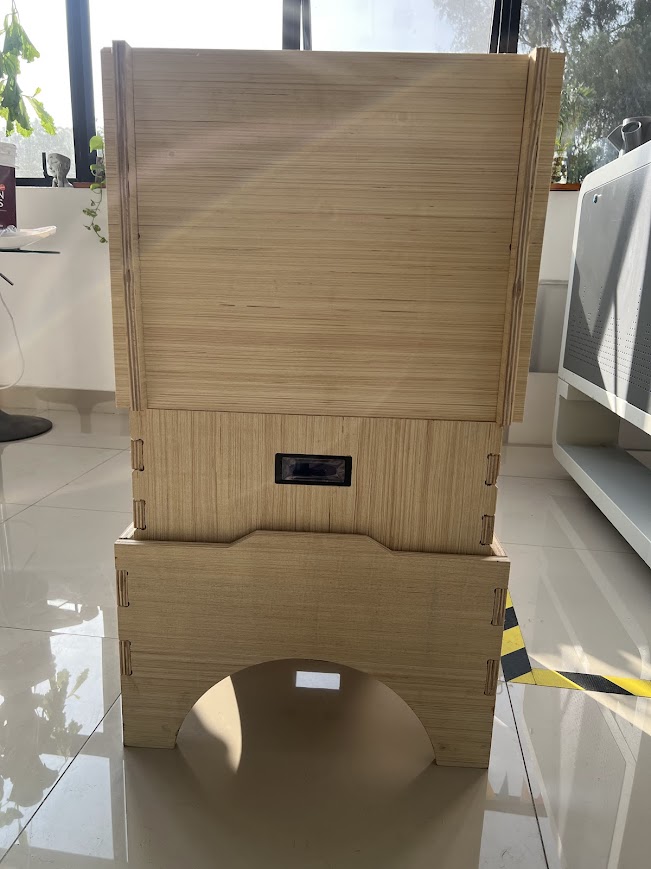
The automated modular dryer for fruits and seeds will provide a controlled environment where program temperature and humidity can be adjusted to optimize the drying process. This will allow the native communities of Madre de Dios, Peru, to dry products such as cocoa and copoazú more efficiently and with higher quality, reducing damage to the seeds from fungi or exposure to the elements and being affected by climatic conditions. The functions of the dryer will be to maintain a temperature of 45°C to 60°C depending on the type of product, also to maintain the relative humidity at optimum levels to prevent mold and ensure proper drying, with the fan the constant and uniform air circulation inside the module for a homogeneous drying. An interesting detail is that I traveled 1578.9km from Lima to Puerto Maldonado for that agriculture workshop, and I cannot return as soon as I would have liked, but I am still in contact with many people dedicated to agriculture and who are interested in doing more technological projects to improve their processes.
Who's done what beforehand?
In the Academy we did not see a project related to the drying of seeds and fruits I have seen projects oriented to agriculture for cultivation to improve the growth of plants or to be able to make a bio orchard to control the temperature of this space but not exactly for the final product to do the drying to pass it to make the product with a chocolate or a sweet like dried fruit. The idea of being able to make this seed and fruit dryer came when I went to a talk on agroforestry and technology in which we gathered farmers and people who work with technology to provide solutions to brainstorm among us in teams which I realized several problems that farmers in Madre de Dios go through which allowed me to propose some solutions within these was to make an easy-to-use module so that farmers can dry in a better way their seeds and fruits grown in their chakras.
What will you design?
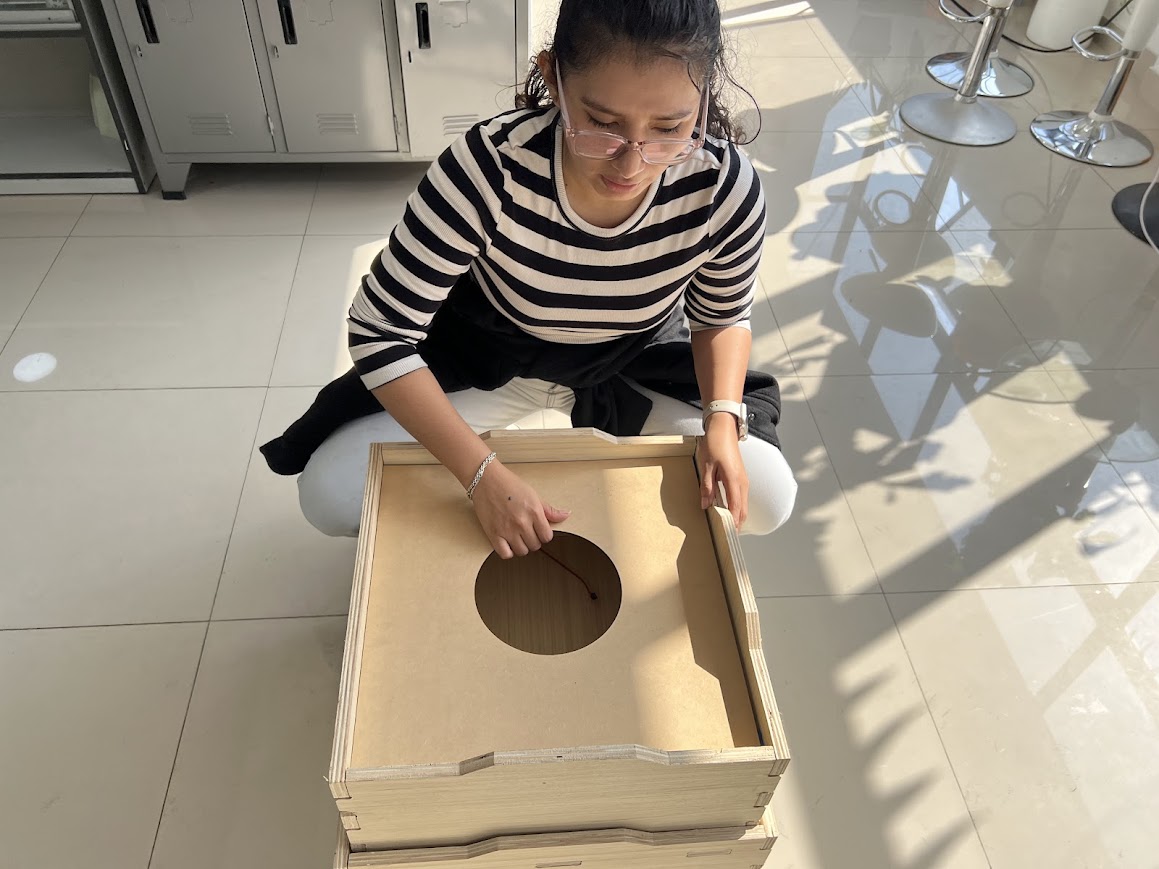
What I designed is the modular nestable piece where the fruits and seeds will be dried with interlocking parts that are easy to assemble and disassemble. I am also going to model the Case for the circuit in 3D, design and create a board which I program to control the temperature and humidity. and to turn on the fan and the heat generator and all this information is displayed on the LCD.
What materials and components will be used?
Components
Name | Description | Units | Price |
---|---|---|---|
Temperature sensor | The DHT11 is a low-cost, easy-to-use digital temperature and relative humidity sensor. | 1 | 5 $ |
LCD | I2C Liquid Crystal Displays. | 1 | 8 $ |
Fun | Cooler Fan | 1 | 5 $ |
Resistor | Nichrome Wire Electrical Resistors | 1 | 20 $ |
Xiao | Seeed Studio XIAO ESP32C3 | 1 | 15 $ |
Relay module | A relay is an electrically operated switch | 1 | 3 $ |
53 $ |
Materials
Name | Description | unit | Price |
---|---|---|---|
Plywood | Triplay Capinuri D/D Trimasa 1.22 X 2.44 12 Mm | 1 | 30 $ |
PETG 1Kg | PETG filament roll for 3D printing with a diameter of 1.75mm. | 1 | 10 $ |
Glass | Glass thickness 10 mm | 1 | 5 $ |
Baking sheet | Full aluminum baking tray 66cm x 46cm | 1 | 5 $ |
Keke mold | English Cake Mold 31X11.5X7Cm | 2 | 10 $ |
60 $ |
Total
Name | Price |
---|---|
Components | 63 $ |
Materials | 95 $ |
158 $ |
Where will come from?
For the construction of this module I used pressed plywood which I used in my week 7 and I had leftover scraps of some parts of my dryer I made it with scraps that I had left over from the previous activity. Apart from the electronics I used show SP 2032 which cost me 40 soles and that is what I used to make my various versions of plate and in the case of nicron wire that generates heat was recycled and recovered to connect it to the system to be controlled with the relay and the microcontroller with this also recycled a 12 volt fan to maintain the temperature inside the box the part of the top glass cost me 14 soles and I used scraps of filament to print the supports where the divisions would go. I will make a table of approximate prices of what it would cost if you buy it.

I will tell you that here in Peru there is a place called Paruro, here I leave the address, it is important that you go during the day because it is a somewhat dangerous place at night, it is important that you have all the components you need written down and if necessary in photo, you should ask people you know which stores you can go to in Paruro, there are places that are not safe, there in Paruro I bought my SMD components, then look for the resistance to generate heat, there were several alternatives, but one that was recommended to me in the Open global was the heater, I had thought about it but with your advice I was more confident in using it, I controlled it with the relay and the microcontroller and my LCD with the DTH11 sensor, which could be another one of better quality since this one has a probability of failing . So we are going to improve the following versions.
How much will they cost?
For the construction of this module I used pressed plywood which I used in my week 7 and I had leftover scraps of some parts of my dryer I made it with scraps that I had left over from the previous activity. Apart from the electronics I used show SP 2032 which cost me 40 soles and that is what I used to make my various versions of plate and in the case of nicron wire that generates heat was recycled and recovered to connect it to the system to be controlled with the relay and the microcontroller with this also recycled a 12 volt fan to maintain the temperature inside the box the part of the top glass cost me 14 soles and I used scraps of filament to print the supports where the divisions would go. I will make a table of approximate prices of what it would cost if you buy it.
What parts and systems will be made?
- I will use electronics
- CNC machine
- Milling machine for the creation of the plate
- Milling machine for the creation of the plate
- Laser cutting for the divisions
- 3D printing to place the brackets for the partitions
- Vinyl cutting to place the fablab logo and names on my drying box
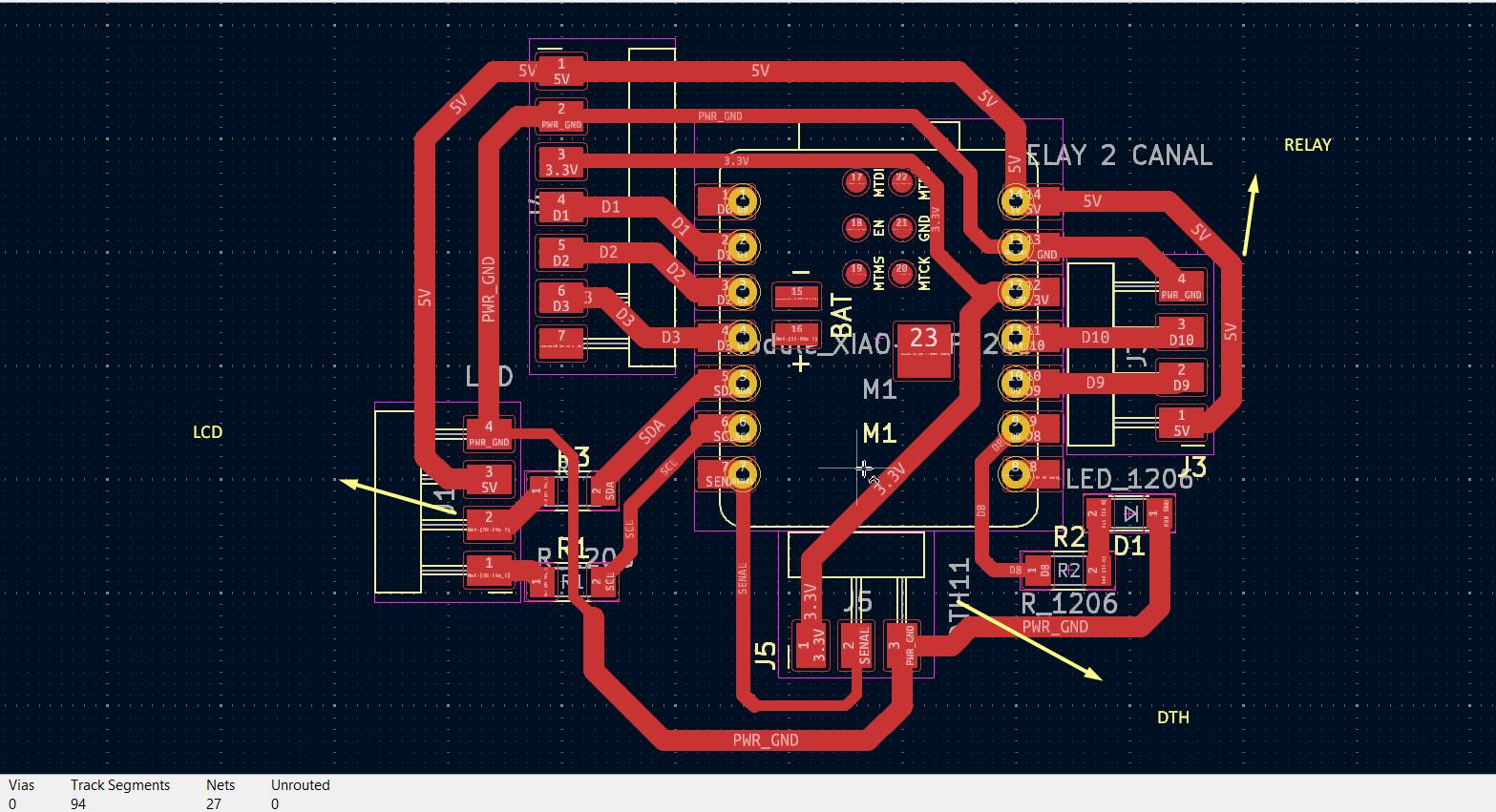
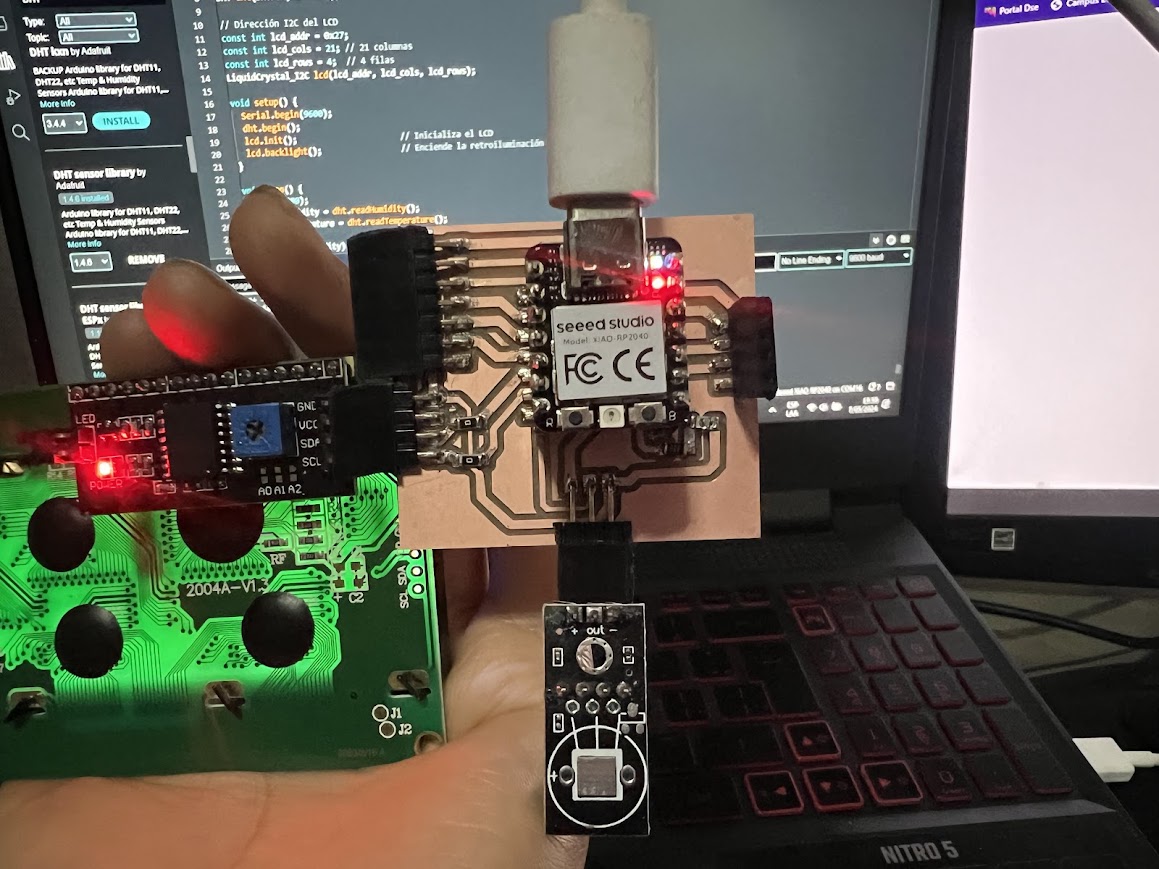
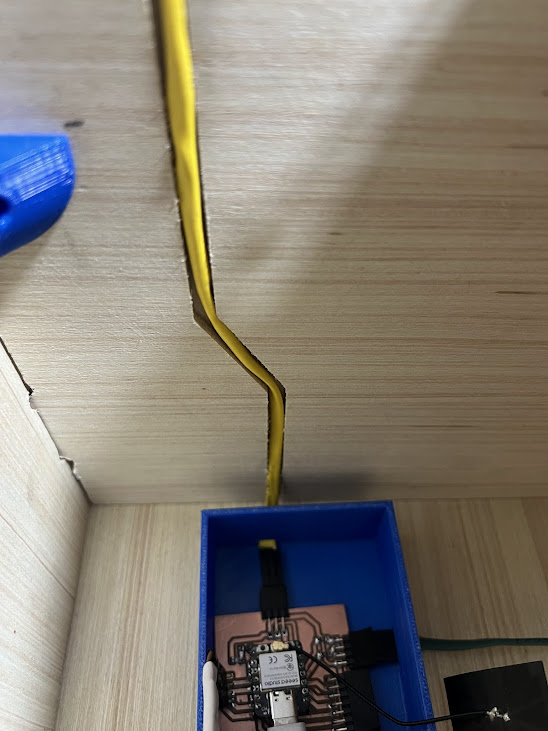
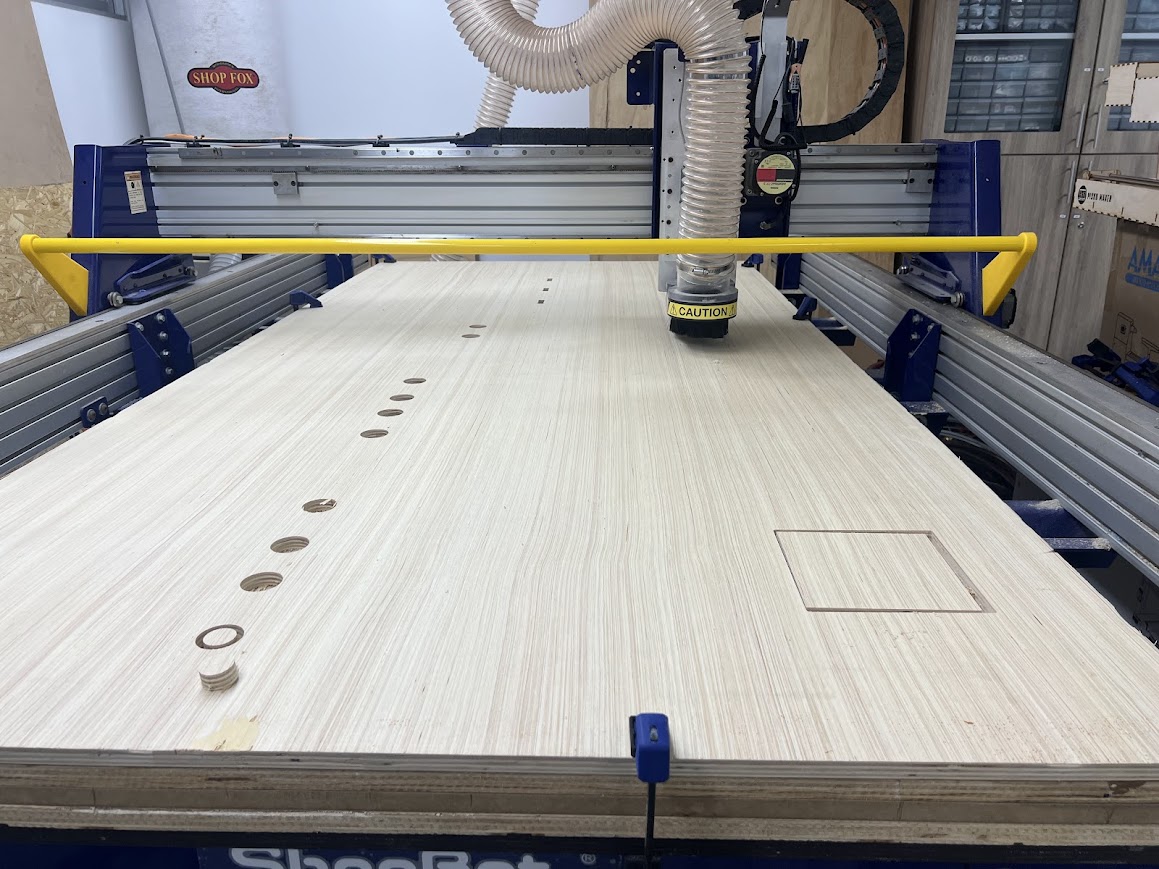
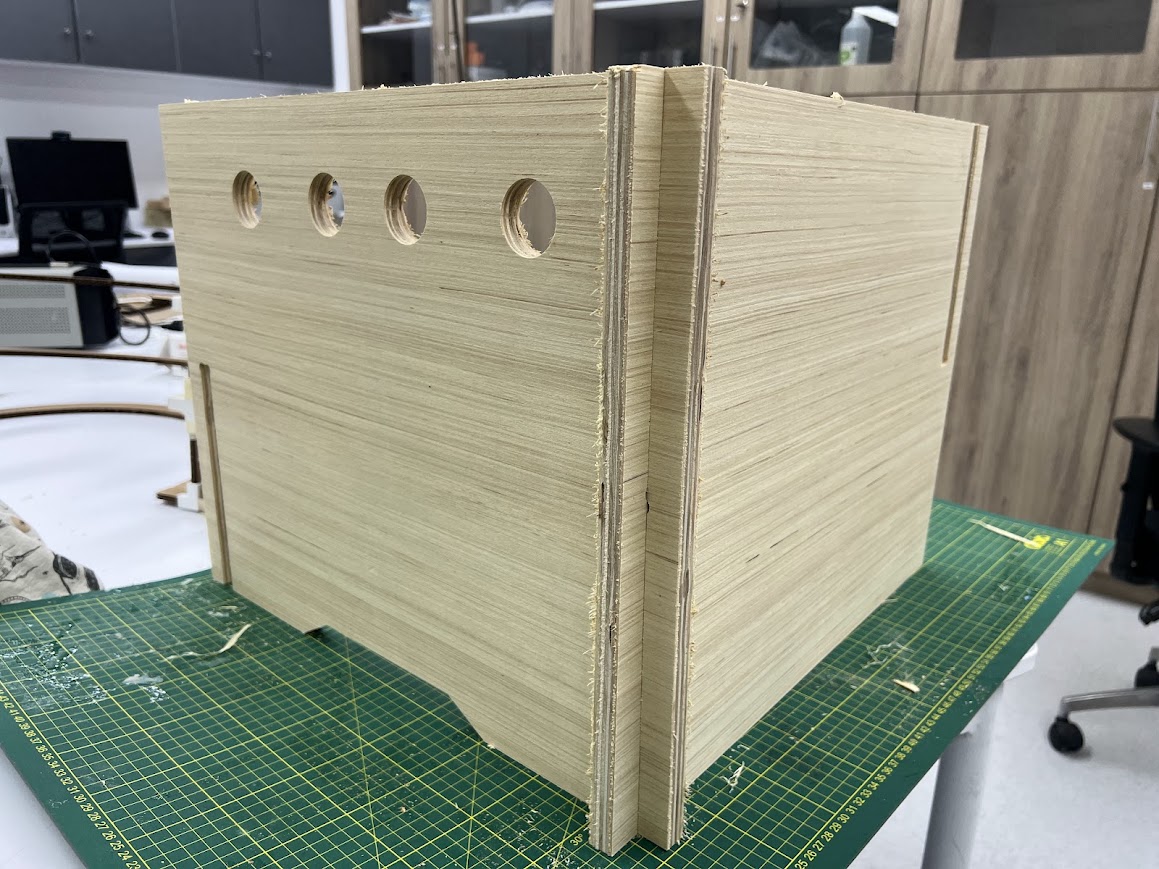
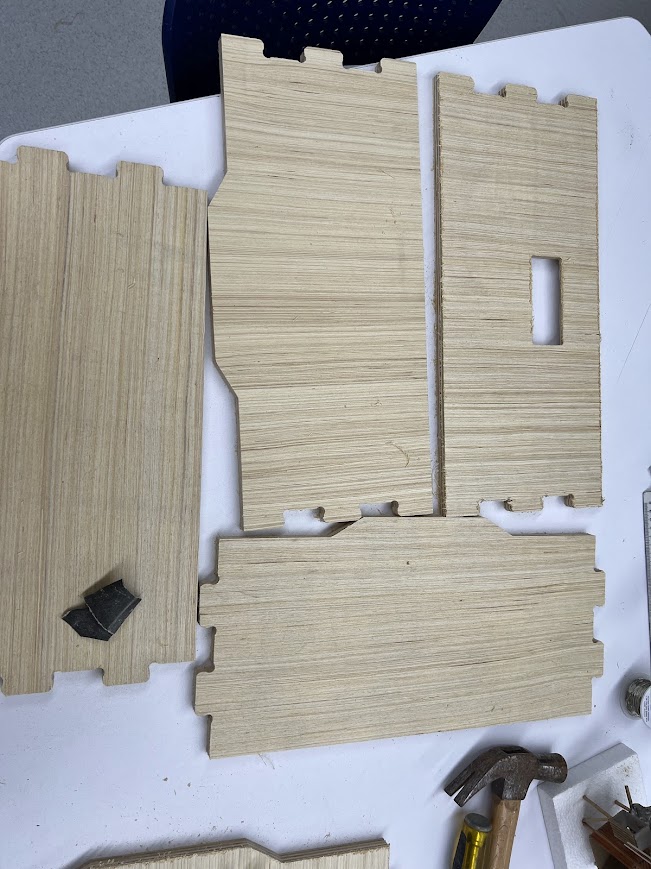
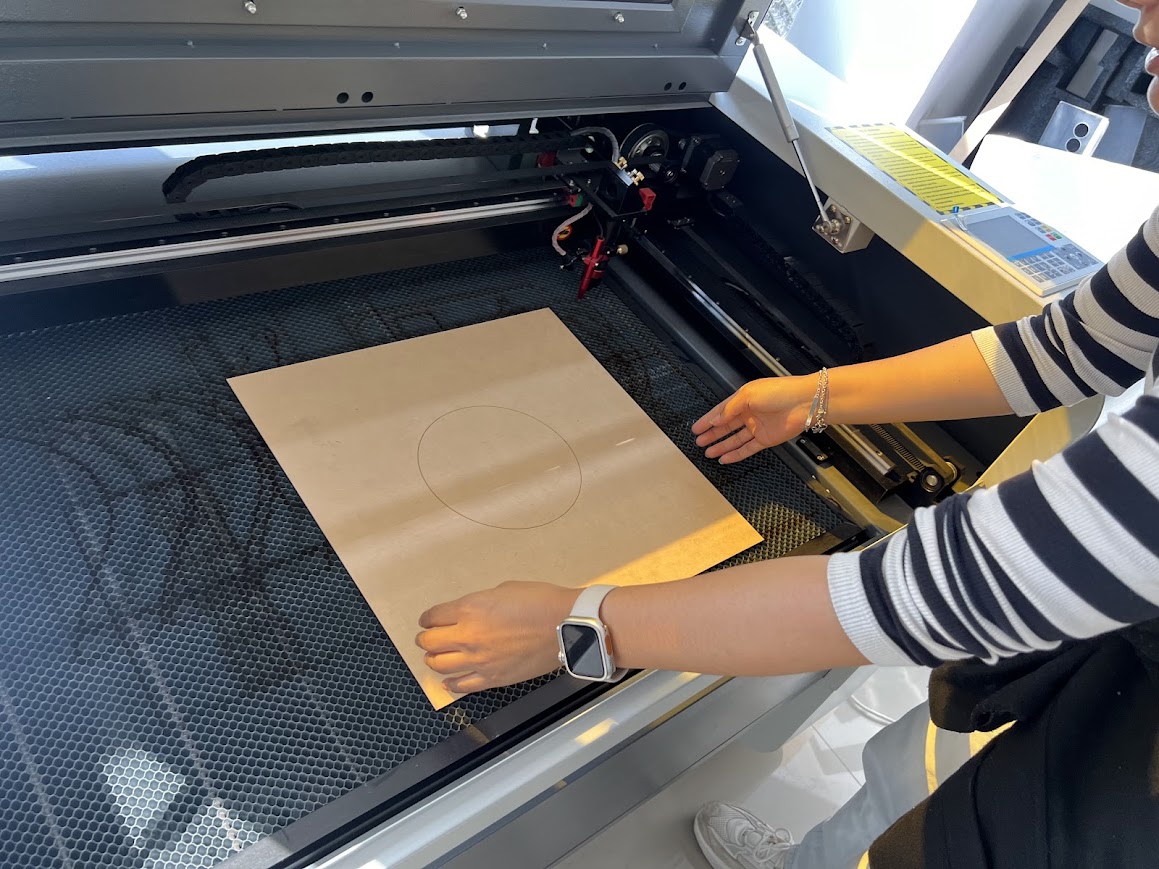
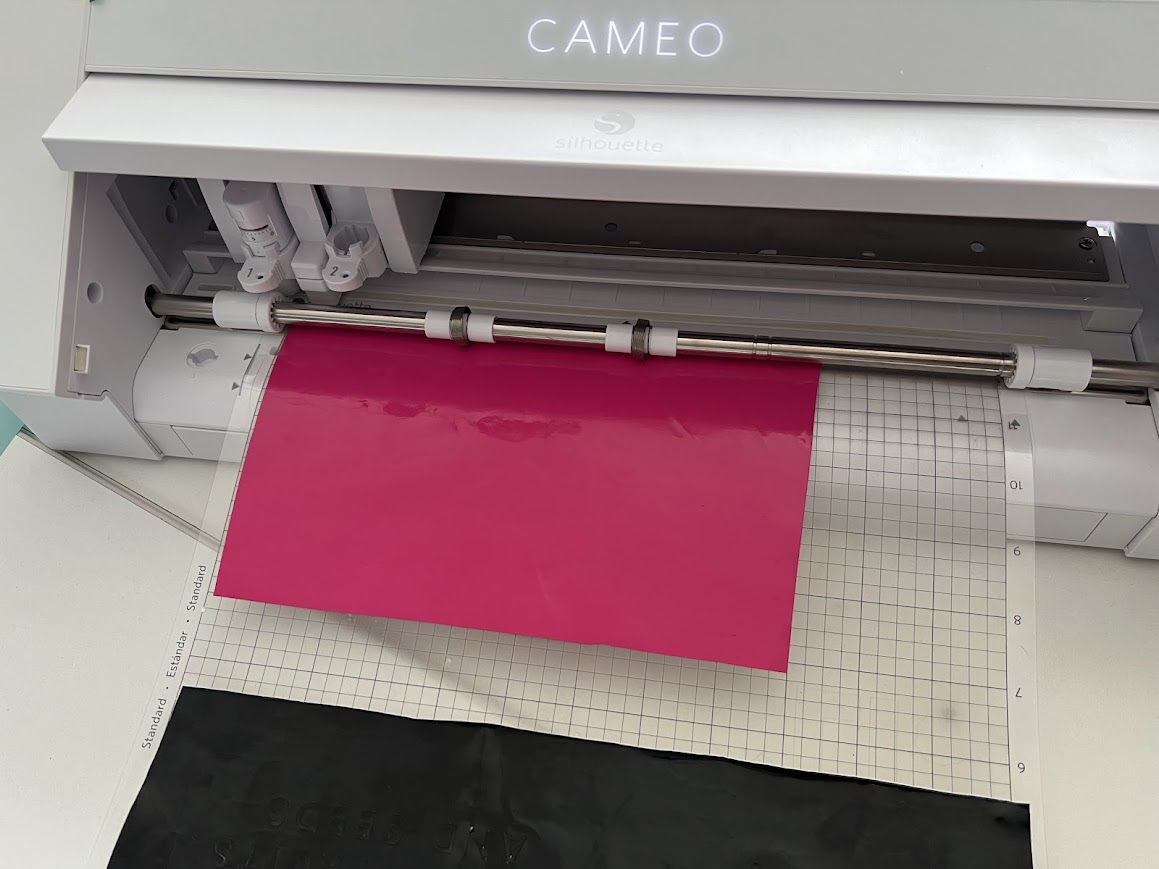
What processes will be used?
Parts that will be manufactured will be the structure with CNC machines designed in fusion 360 take the plans in Autocad to make the cut in the shock box then we have the design of the electronic board using then pass it to the milling process and to weld, also programming will be used in arduino ide to control the sensors with the microcontroller I will use vinyl to make the logo and put the letters on my fruit and seed dryer, I will also use the 3D printing process in which I had the idea of being able to look for references of supports to make my divisions and be able to print them and place them with bolts to my box and generate the divisions then I also used laser cutting to create the bottom of one of the divisions of the electronics Al Calor allowing this to generate a hole so you can place the nicron wire that would generate heat and at the same time to separate the electronics with the space where it will be at high temperature.
What questions need to be answered?
What kind of food can I put in the dryer? How long does it take me to dry an apple? What do I have to do if I have another type of fruit and I want to dry it in this module? Is the power consumption of this device It could work with solar panels How many kilos of seeds could I dry per day Could any farmer in madre de Dios be able to have it Any person could manipulate handle or use this Drying Module.
How will it be evaluated?
How it will be evaluated in one of the Open global that was ricko and Adrian and Pabloalways recommended me to work in spiral and is one of the things that stayed with me and helped me a lot to organize myself nil in the Wednesday classes also reminded us that the project consists of the spiral development the first part of what I wanted to do was that the sensor can detect the temperature and can be displayed on the LCD the second spiral I did was to activate with the relay my fan and the third spiral was to integrate the heat generator with the relay and the temperature sensor and humidity which allowed me to have a progressive advance of my project reaching a fourth spiral in which I made improvements in the operation of the system making the heat is activated until it reaches 45 degrees Celsius and the first spiral was to activate the heat generator with the relay and the temperature sensor and humidity which allowed me to have a progressive advance of my project reaching 45 degrees Celsius. humidity which allowed me to have a progressive advance of my project reaching a fourth spiral in which I made improvements in the operation of the system by activating the heat to reach 45 degrees Celsius being the ideal passing this temperature turns off the heater and turns on the fan to maintain the proper temperature down to 45 degrees Celsius is turned on again the heater is paid the fan and all this is seen from the LCD screen with input and 12 as the temperature sensor is measuring these changes within the dryer seeds and fruits.
Consideration
- If you want to replicate this project, take safety into account with the nichrome wire, it must be insulated and the system must have adequate ventilation.
- The initial tests I did were with a heater that had a nichrome wire and a fan, allowing me to make the test safer. If you don't have that heater and you try to replicate this project, be careful with the heat generated by the wire.