Laser cutting is a thermal cutting process that employs a concentrated laser beam within the cutting area to melt the material. Subsequently, a gas or air is utilized to expel the molten material, resulting in the desired cut.
Laser Cutting Machines
In our FAB LAB, we have two different types of Laser cutting machines. One is the Trotec Speedy100, which is primarily used for the FAB academy and is capable of cutting materials like acrylic, wood, and cardboard. The other machine is the Trotec Speedy400, which is part of the Super Fab Lab. This machine is specifically designed for engraving circuits to create PCBs. Both machines are manufactured by Trotec, with the Speedy400 being slightly more powerful than the Speedy100.
We encountered an issue with the first machine, the Trotec Speedy100, which is currently out of operation. Consequently, we've been utilizing the second machine, the Trotec Speedy400, for engraving purposes. The cutting part was out of operation. More details are available here
.png)
Focusing methods
Automatic Focus: Sonar Technology TM (automatic focusing with ultrasonic sensor), ensure the ultrasonic sensor is clean. Choose the appropriate lens in the software settings. Position the laser pointer onto the workpiece surface for focusing. Press both keys of the Z-axis control button to move the table to the focus position, aligning the laser beam. With focus achieved, commence laser processing.
Focus tool: position the processing head using the X/Y Laser head control buttons. Hang the focus tool on the laser head. Adjust the working table upwards with the Z-axis button, avoiding collisions. Elevate slowly, tapping the Z-axis button to ensure the focus tool's alignment before it reaches the material surface.
Additionally, we've been utilizing the SIL Laser Cutter and Engraver for both engraving tasks and group assignment. However, this is an open machine and the pungent smell, makes it very difficult to use the machine.
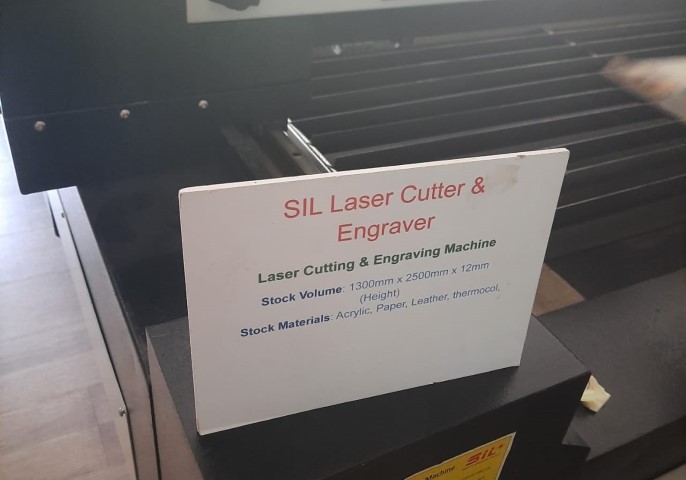
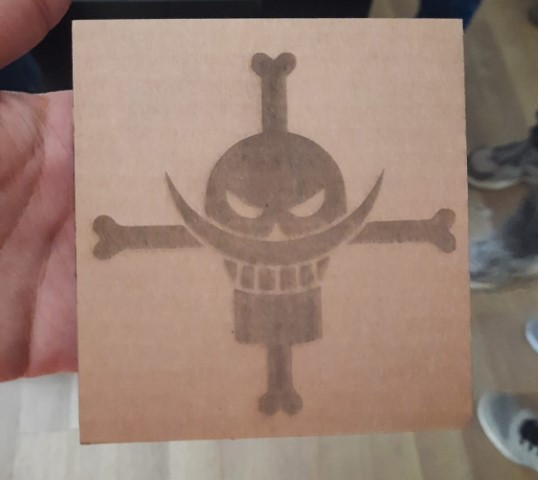
ZUND G3 L-2500 Digital Cutter
A Zund cutting machine represents a digital cutting system utilized for cutting a diverse range of materials including paper, cardboard, textiles, and plastics. This machine employs a computer-controlled cutting head capable of movement along multiple axes, enabling it to execute precise and intricate cuts. Zund cutting machines are available in several models, each offering distinct cutting capabilities such as cutting, creasing, and routing.
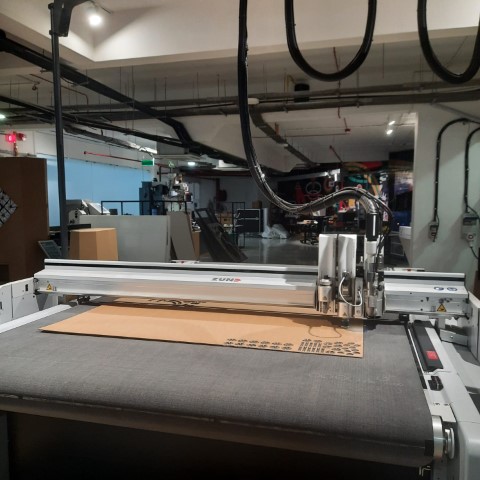
- To initiate cutting using a DXF file format, begin by accessing the cut editor. Navigate to the file menu and select "Add job" to incorporate the desired file for cutting.
- Next, proceed to optimize the spacing between individual sketches. To achieve this, press the space key and manipulate the geometry as necessary. Additionally, select all figures and navigate to "Objects" followed by "Numerical Geometry." Here, offset the X and Y axes from the origin to establish an initial clearance before the cutting process commences.
- To optimize the design, either press "O" or navigate to "Tools" and select "Optimize." Confirm the optimization by clicking "OK." Starting from the rightmost corner, define the type of operation required. Choose from a variety of operations such as creasing or cutting. After selection, specify the material to be used for cutting from the options available in the right-hand corner. The machine features a scanner that automatically scans the bed and locates the corners of the inserted sheet. Alternatively, manual adjustment is possible. While creating a Job register is not mandatory, it can significantly reduce manual effort. To create one, add another step and select "Register." Choose the desired starting cutting position. Ensure the register process occurs first by moving up the job using the arrow mark. Activate the job and close the application. Then, navigate to the Soft Cut Queue where the activated job will be visible. Double-click the job to open job settings.
- In the job settings, select the appropriate tool and adjust the base depth to ensure the sheet is cut through without affecting the bed.
- Set the starting point for the Zund to cut. Once all settings are confirmed, start the job.
- Cutting process
.png)
.png)
.png)
.png)
.png)