Week 16: Applications and implications
Checklist for this week:
- ☑ What will it do?
- ☑ Who has done what beforehand?
- ☑ What will you design?
- ☑ What materials and components will be used?
- ☑ Where will they come from?
- ☑ How much will they cost?
- ☑ What parts and systems will be made?
- ☑ What processes will be used?
- ☑ What questions need to be answered?
- ☑ How will it be evaluated?
Task for this week
Propose a final project masterpiece that integrates the range of units covered.
Your project should incorporate:
- 2D and 3D design
- Additive and subtractive fabrication processes
- Electronics design and production
- Embedded microcontroller interfacing and programming
- System integration and packaging
Where possible, you should make rather than buy the parts of your project. Projects can be separate or joint, but need to show individual mastery of the skills, and be indepently operable.
See Final Project Requirements for a complete list of requirements you must fulfil.
The answers to the questions below will allow you to create your BOM (Bill of Materials).
Develop a project plan
The client is suggesting a collaboration with Singapore Polytechnic Fablab and engaging students in the creation of 3D sculptures representing endangered animals. This project is intended to coincide with the June School holidays 2023, specifically focusing on World Environment Day on 5 June 2023. The sculptures will be constructed using sustainable cardboard material, aligning with the theme of sustainability, and will be showcased at Marina Square Central Atrium. The exhibition will run from 26 May to 11 June 2023.
- To increase the awareness of environmental issues such as marine pollution and global warming through captivating 3D display
- To promote eco-conscious practices
- To drive actions and commitment for a greener and sustainable future
Objectives of Campaign:
In order to enhance the fun and interactivity of the sustainability program at the atrium, the client has suggested several engaging activities to complement the 3D installations within the spacious 420 sqm Central Atrium.
- Upcycling workshops for visitors
- Crafts workshops for kids in line with the cardboard/ endangered animal theme
- Augmented Reality Broadcast (AR with wildlife content- currently in talks with vendor)
- Invite WWF to be part of the program
The list of endangered ocean animals for the 3D sculptures:
- Whale
- Shark
- Dolphin
- Turtle
- Seal
- African Penguins (cluster)
- Polar Bear
The PR campaign, managed by the appointed PR Agency, will include a media preview day scheduled for 25 May 2023 (Thursday). It is imperative that all sculptures are set up prior to this date. The budget for the campaign will be finalized by the end of February, allowing us to prepare the contract by mid-April 2023. Following the contract agreement, production will commence promptly.
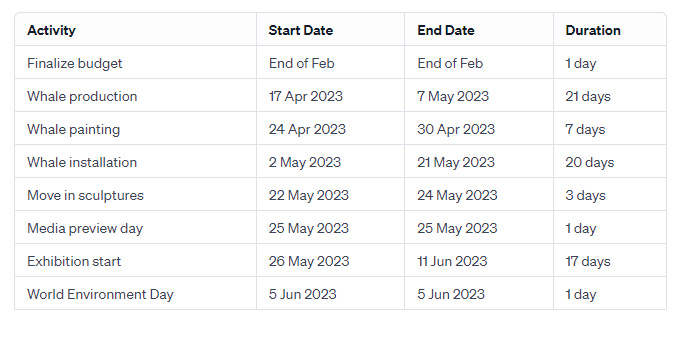
1.1 What will it do?
I often find myself pondering the underappreciated potential of cardboard as a versatile material. In this final project, I have constructed a remarkable life-size whale entirely from sustainable resources, specifically cardboard. The end result (that I aim for) is an awe-inspiring creation that truly comes to life.
In pursuit of continuous improvement and innovation, I have opted for a spiral development approach. As part of this methodology, (during phase one) I am incorporating a PIR (Passive Infrared) sensor to initiate a specific action performed by a servo mechanism. This integration of sensor and servo technology adds an interactive element to the project, enhancing its overall functionality and impact. For phase one, I have incorporated all the knowledge I learnt through out the weeks, from Electronic Design and Production, 3D printing, Flatbed cutting to Embedded programming, spiral development, project management, and counting.
1.2 Who has done what beforehand?
I am finding it challenging to articulate, but I am currently investing significant effort in seeking resources and building a network of participants for my final project at FAB23 in Bhutan.
Envision an annual occurrence where attendees of FAB, united in their collaboration, engage in the creation and unveiling of a sculpture that embodies the central theme of FAB.
Essentially, my focus is on ensuring the realization of my project physically at FAB23. I've been allocating excessive time and energy to searching for assistance and support. With this mission in mind, no one has done that before (to my knowledge).
Never-the-less, there are NO shortage of cardboard creation anywhere and everywhere, but no one has done it at the global FAB at this scale. Below are the artists whom have been my sources of inspiration over the years (not in particular order):
Joseph DeLappe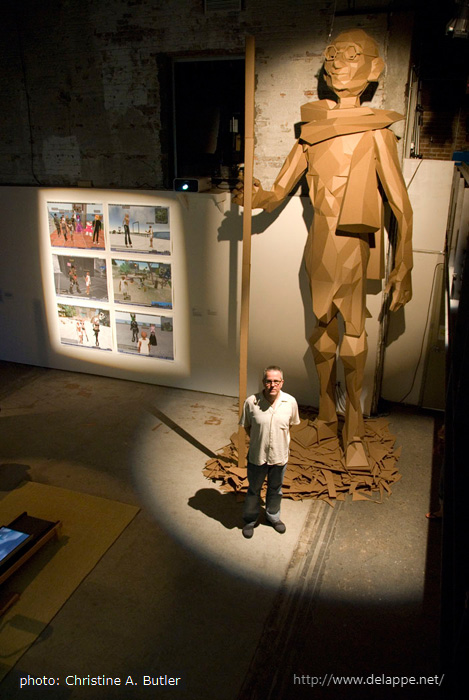
Kiel Johnson
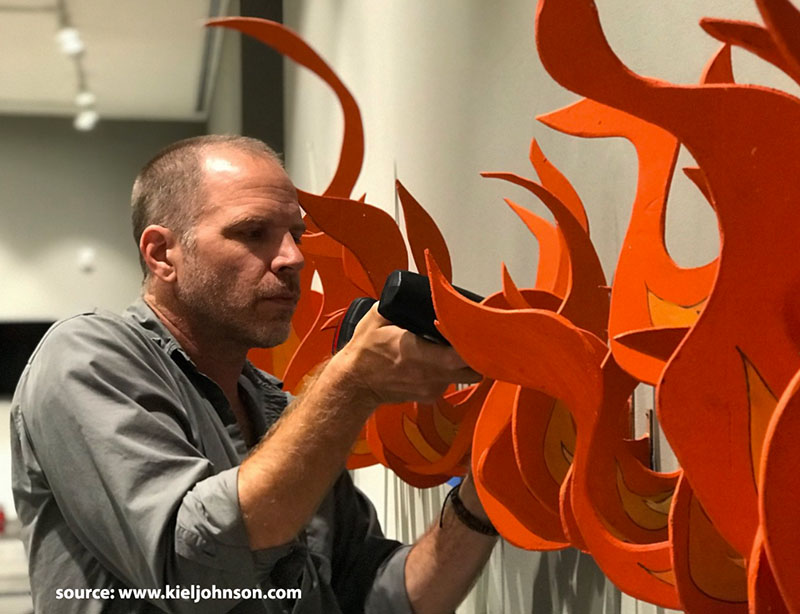
Horst Kiechle
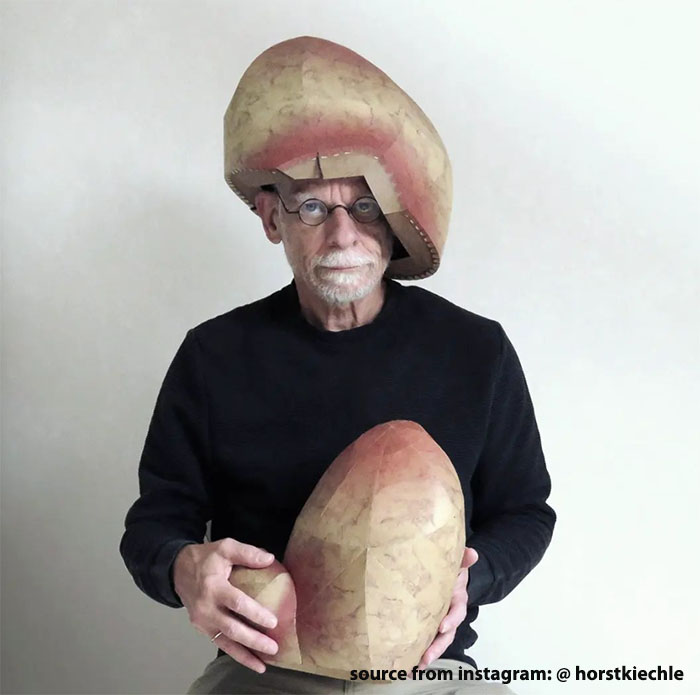
1.3 What will you designed?
With the sustainability theme in mind, I designed an endangered marine animal- a gentle beast in the sea. The effort included the creation of 3D model in Blender, unfolding the model and layout all the hundreds pieces of templates in Adobe illustrator to fit into the cardboard material size (1.4m x 1.1m).
I also make a small cardboard whales that is easily replicated and produced (die-cut) them in thousands (as a token of appreciation for participants in this project).
1.4 Materials and components
Refer to bottom of Final Project page.
1.5 What parts and systems will be made?
- An 8m long whale made out of cardboard that could last for minimum 5 years under indoor condition - 3D design
- Vinyl sticker for the Bar code (link to online instruction video) - 2D design
- Seeed Studio RP2040 on customized PCB - Embedded microcontroller
- Integration case
1.6 What processes will be used?
- Flatbed cutting for all the cardboard, for A-flute (5.5mm) and E-flute (1.8mm) - subtractive fabrication process
- 3D printing for the PCB case - Additive fabrication process
- Electronic Board CNC milling
- Embedding programming for the PIR sensor and actuators (Servo)
- Sticker printing and cutting for Bar code (Link to online instruction video for Mini Cardboard Whales)
1.7 What questions needed to be answered?
- How many manhour required to finish the sculptures?
- Is it necessary to build life-size?
- Who is paying?
1.8 How will it be evaluated?
- Implementation of Spiral Development: The initial "prototype" has been successfully created in Singapore. Contrary to common occurrences in life where actions do not align with words, this incident stands as a rare exception for me.
- To successfully arrange all the logistics to Bhutan.
- To get participants excited about building it together on the spot. A group photo of all FAB23 participants with the project would be bonus.
- Most challenging task, open collaboration (invitation) to all fellow students to do something on the whale (E.g. design a mechanism to shoot something from the head, projection mapping, doodling on the skin, etc)