Computer-Aided Cutting
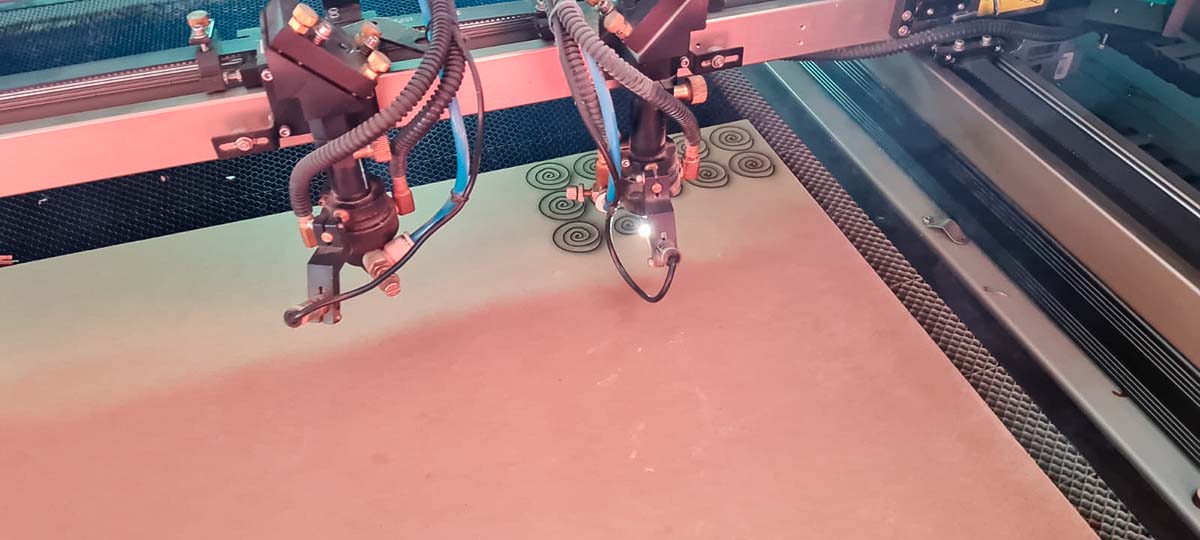
This week's assingment is Computer Aided Cutting, in which we use Laser-Cutting and Vinyl-Cutting machines for assembly and "sticker" creation.
Firstly we had to design and cut different kind of assemblies, most of which were perpendicular, for different applications. But in order to correctly design this pieces,
it is necessary to characterize each of the machines we work with. We have a CamFive CFL-CMA1390T which has a 100 Watt CO2 Laser Tube, and can move up to 250mm/s.
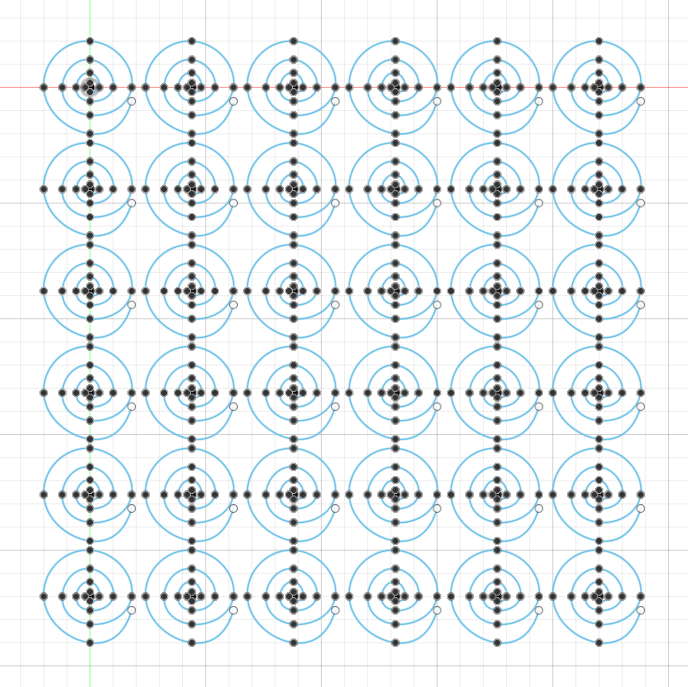
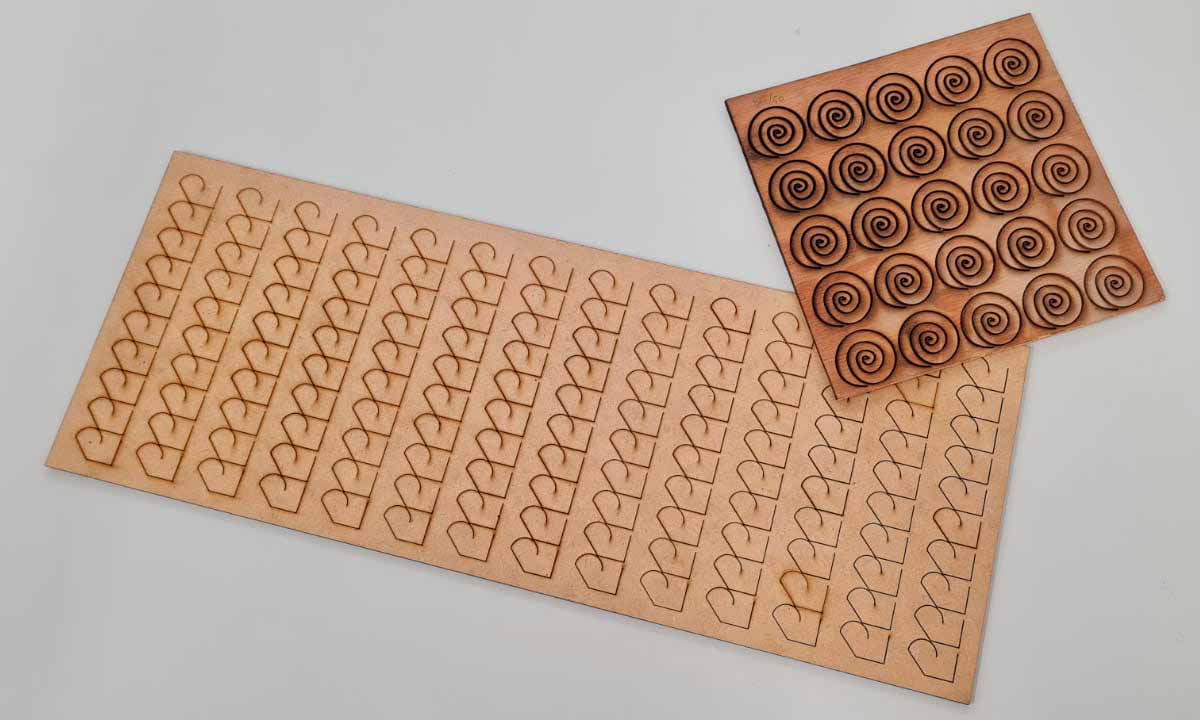
For the configuration of the machine, we use a software called SmartCarve(I couldn't find an official website for the download so be careful when downloading it, also you may need a USB drive key that works as a licence carrier) which has a simple interface where one can adjust the different parameters for cutting/engraving. The main parameters to be adjusted are: Speed of the laserhead, measured in mm/s, and power of the laser, measured in %. I used 80% power on the first one, with 50mm/s speed. On the same row I used 50mm/s increments, and for the next rows I decreased 10% of the power, with the same speeds.
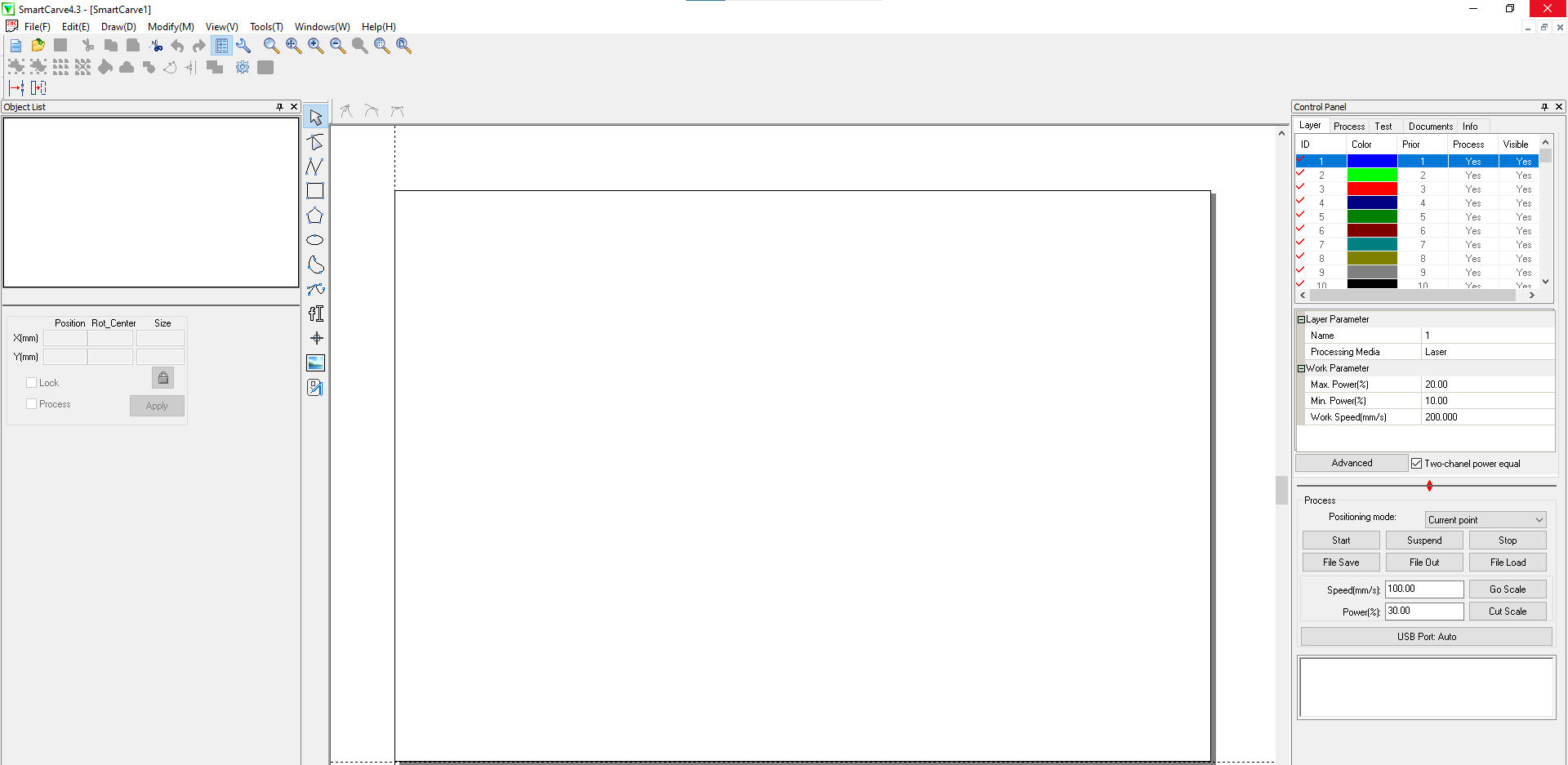
The next step for the propper characterization of the machine was to measure the Kerf. Kerf is the part of the material removed by the laser, with a clean cut it should be almost non-existing, however measurable. I started with a very simple design, a rectangle with 10 separations which will be cut through the laser. I knew which power and speed I needed to use thanks to the previous test (75%power and 20mm/s). Then it is possible to measure the gap that is created after the cut. In this case it was 2.24mm, and to calculate the exact Kerf one must divide it by the number of cuts, in this case it was 11, so the Kerf=.02mm.
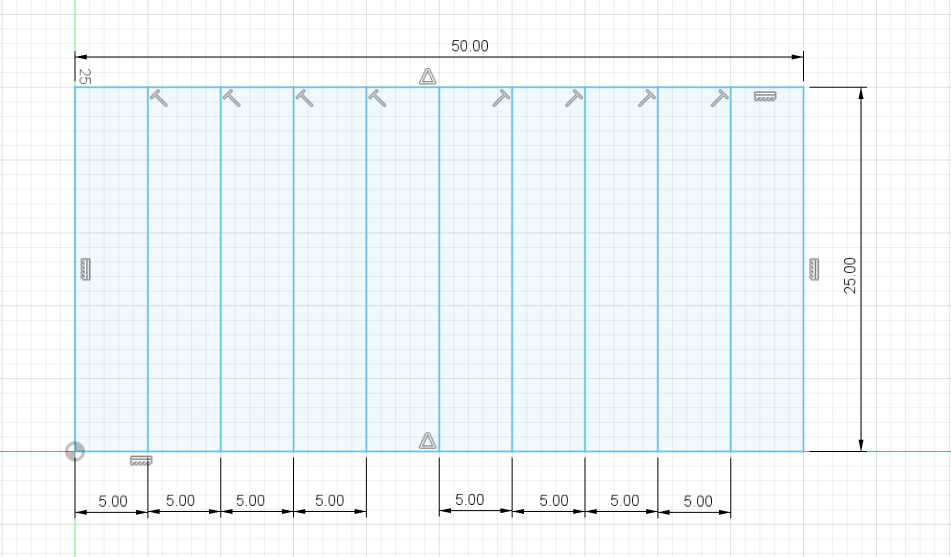
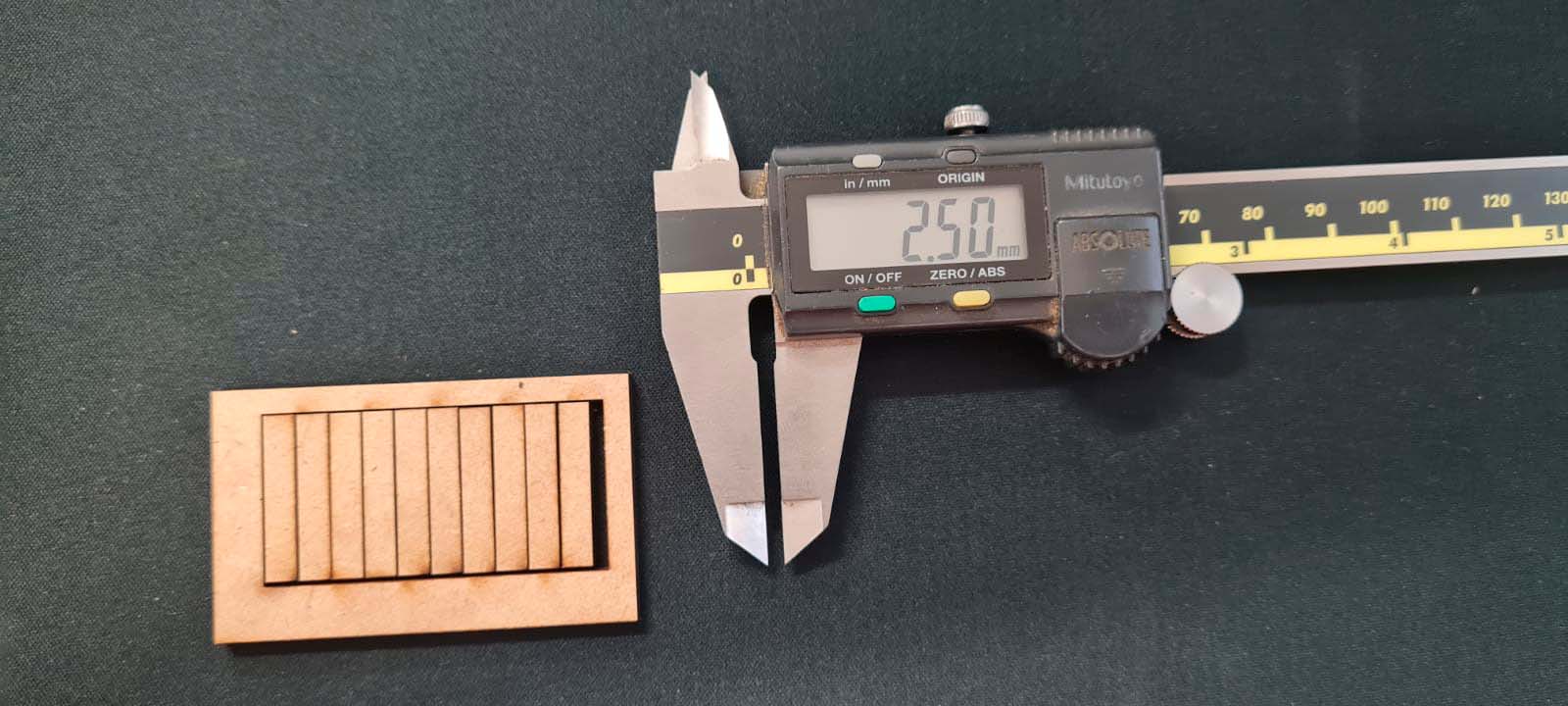
So now having the propper parameters for the cuts, the next task is to cut and assembly this pieces. It is necessary to consider the Kerf for every cut, so I came up with the formula:
For outside cuts:
Nominal lenght + Kerf
For inside cuts:
Nominal lenght - Kerf/2
There are different kinds of joints so let's start with the beginning. The joints I designed and tested were the Pinned Joint and the Flexture Joint.
Pinned joint
The Pinned joint works with a pin, as its name dictates, there is a cross whose center "square" lines up with another square, in which a pin is introduced for maximizing rigidity and stability.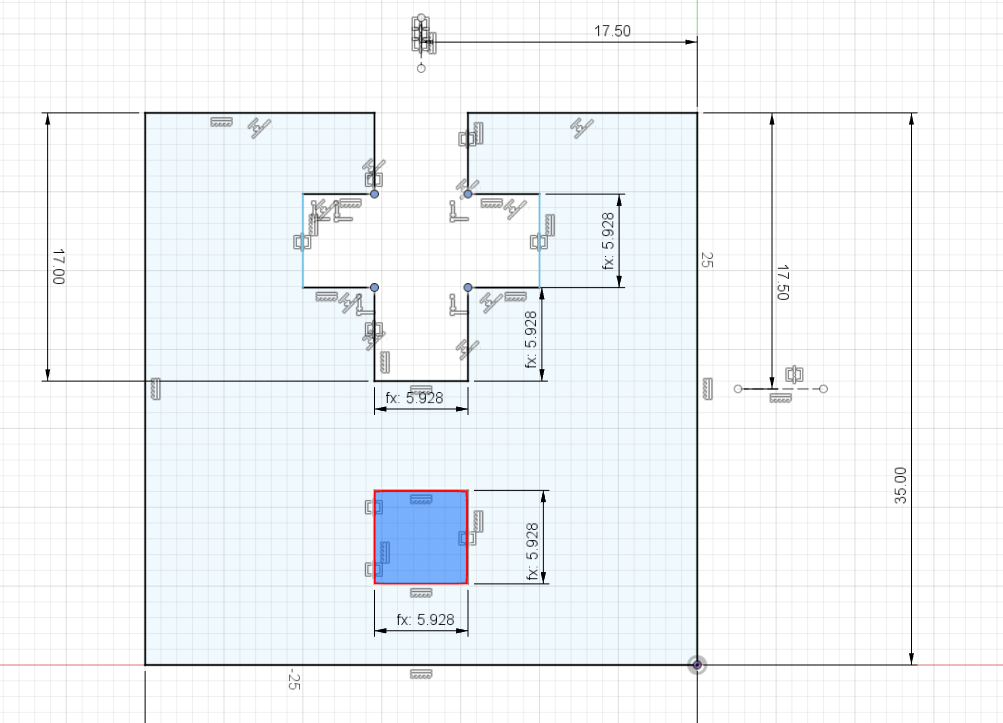


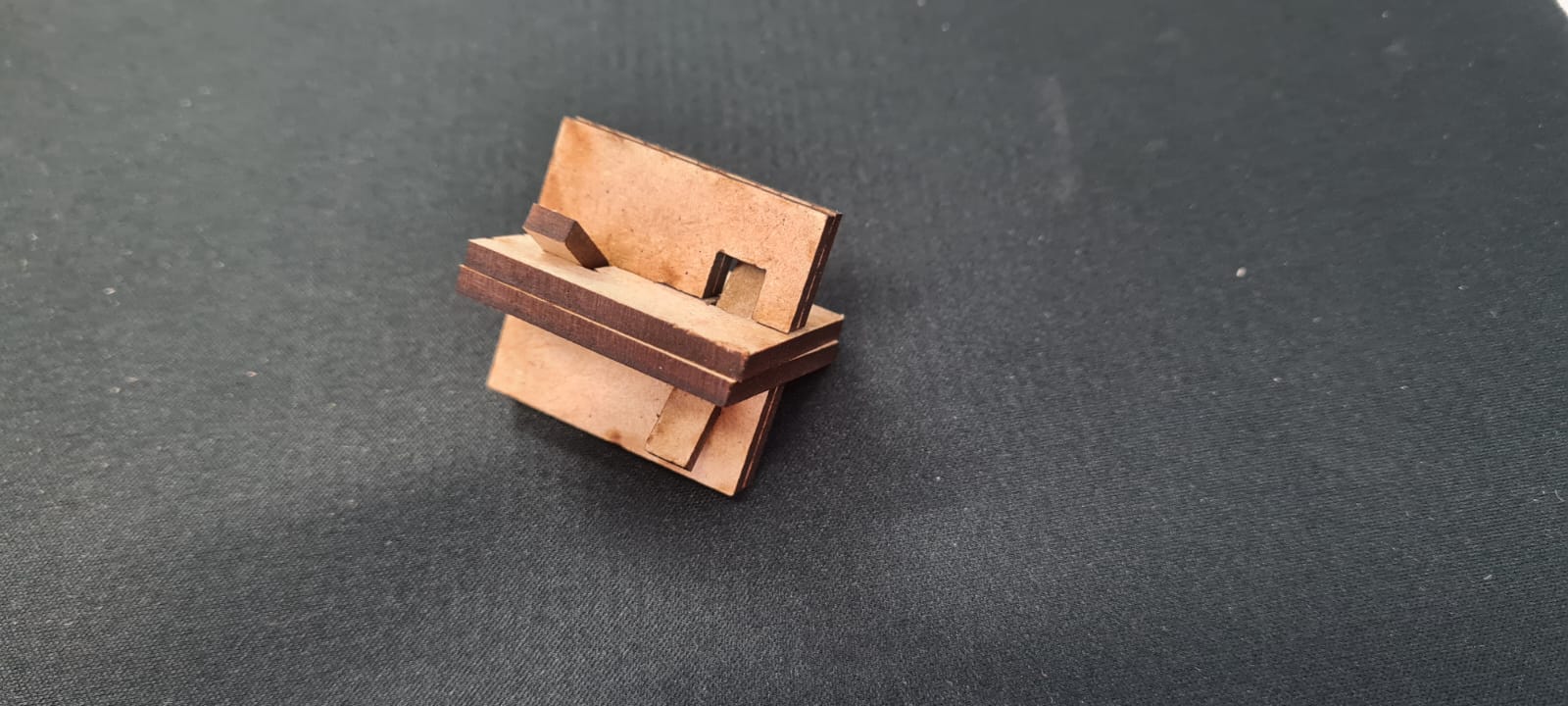
Flexture Joint
This joint consist on spring-like cuts which press the walls of the other part and ensures stability and strenght, as the flexible part of the joint secures it.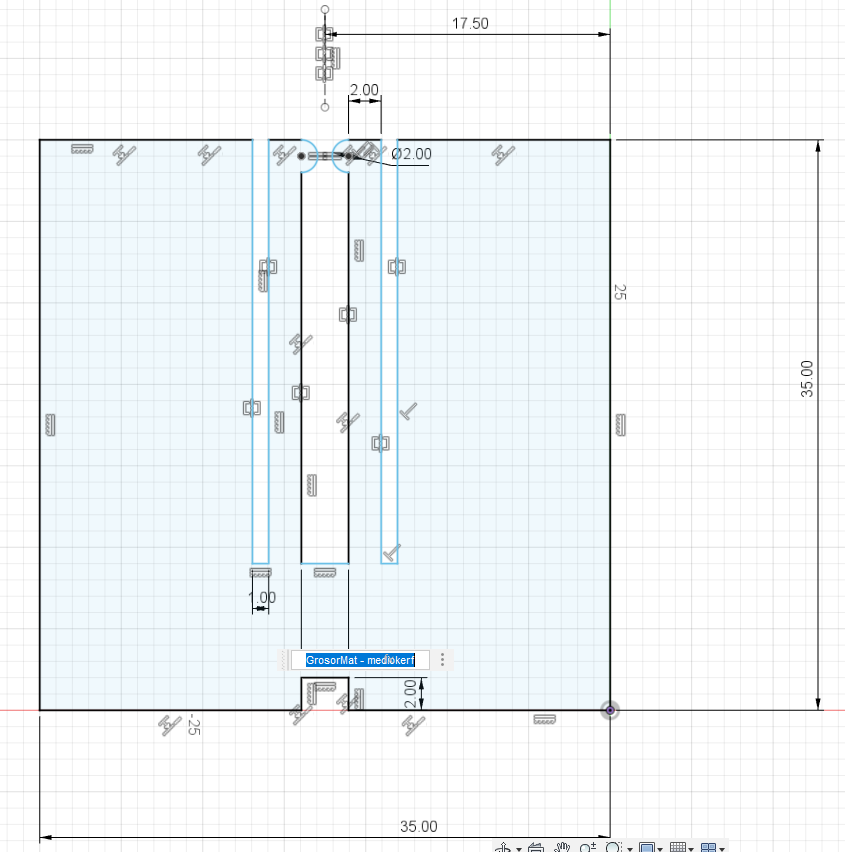

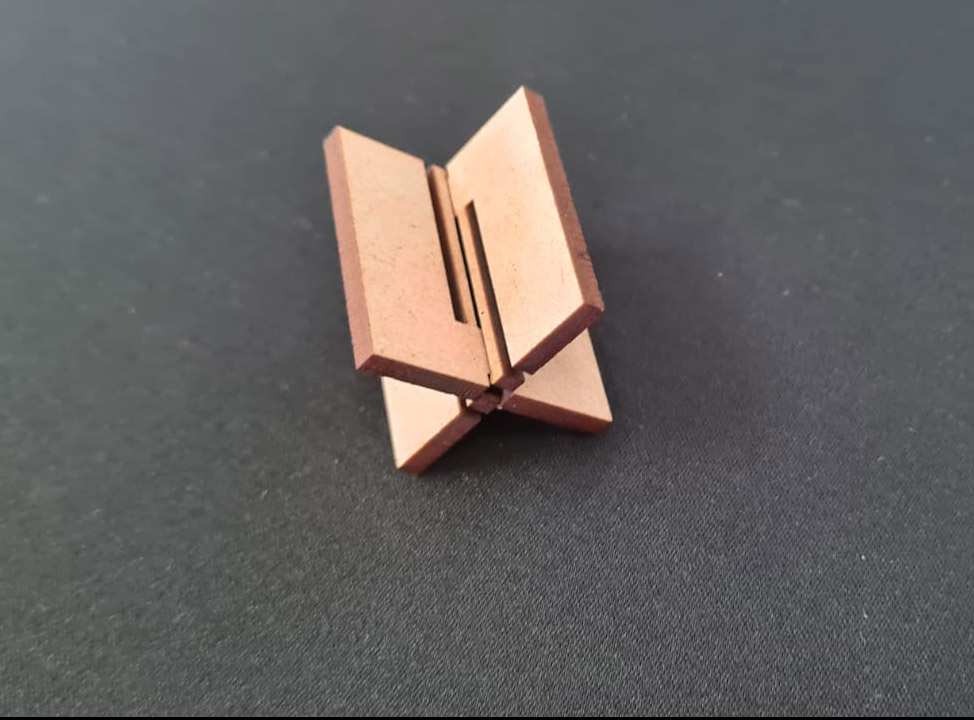
Group assignment
As a team we designed and tried different kind of joints which are presented bellow:Finger and Chamfer joints
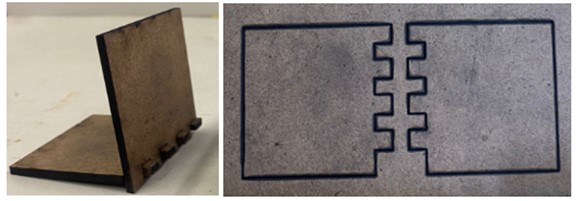
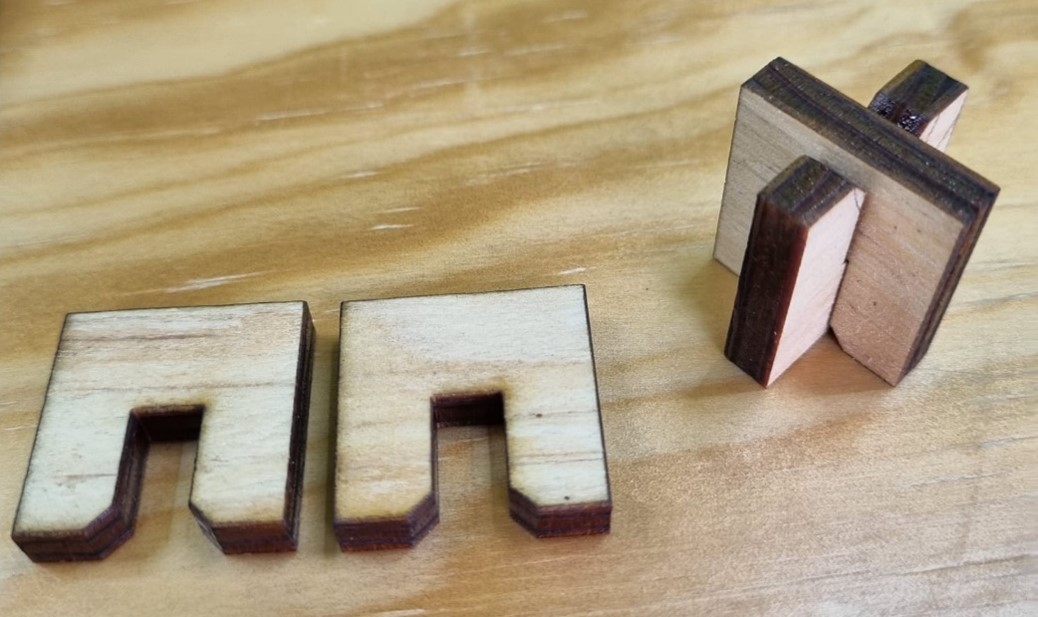
Wedge and Snap-fit joints
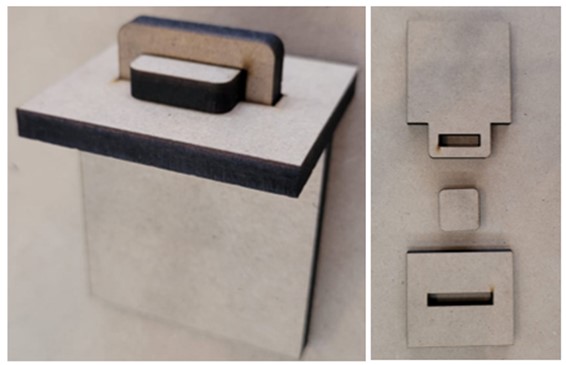
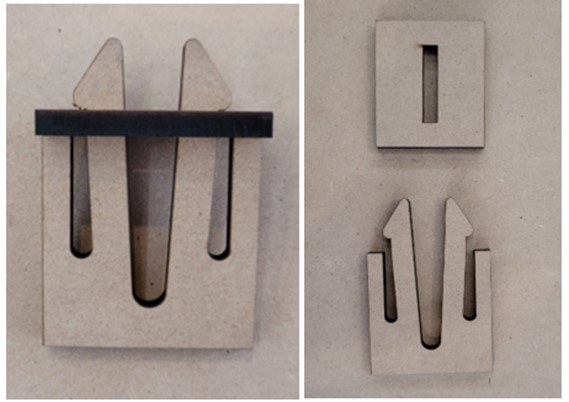