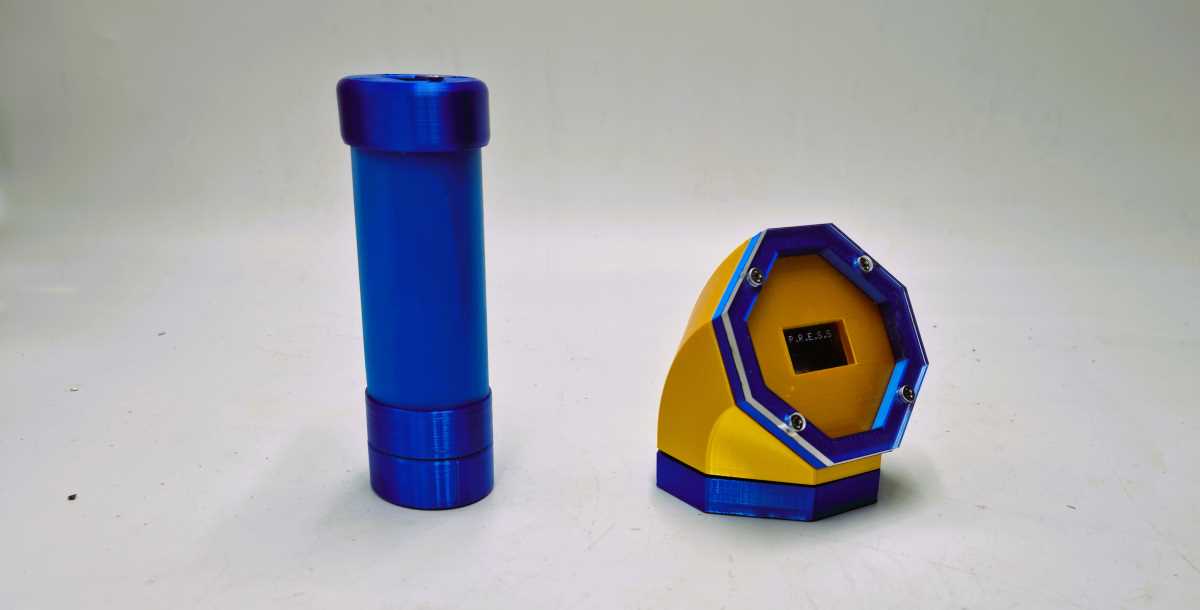
My Final Proyect:
Here you can check what´s my final project about. Follow how it progresses from an initial idea/concept, to a fabulous working and useful machine..(hopefully!) with all the possible ups and downs.
As you can observe, the Final Project is divided in three sections, navigate through all of them to get all the information:
- Project proposal: You will find the initial idea, the spiral development and first skecthes of my final project.
- Project development: Will give you a detailed explanation of all the fabrication process, linking to all the weekly assignments used and answering to what worked and didn´t?, lessons learned?, what has been completed and what tasks remain?
- Final project: Were you will find the final slide and video, questions and answers and all the final files.
SLIDE
Objetive measurement of musculoskeletal biomarker/s in non-clinical environments
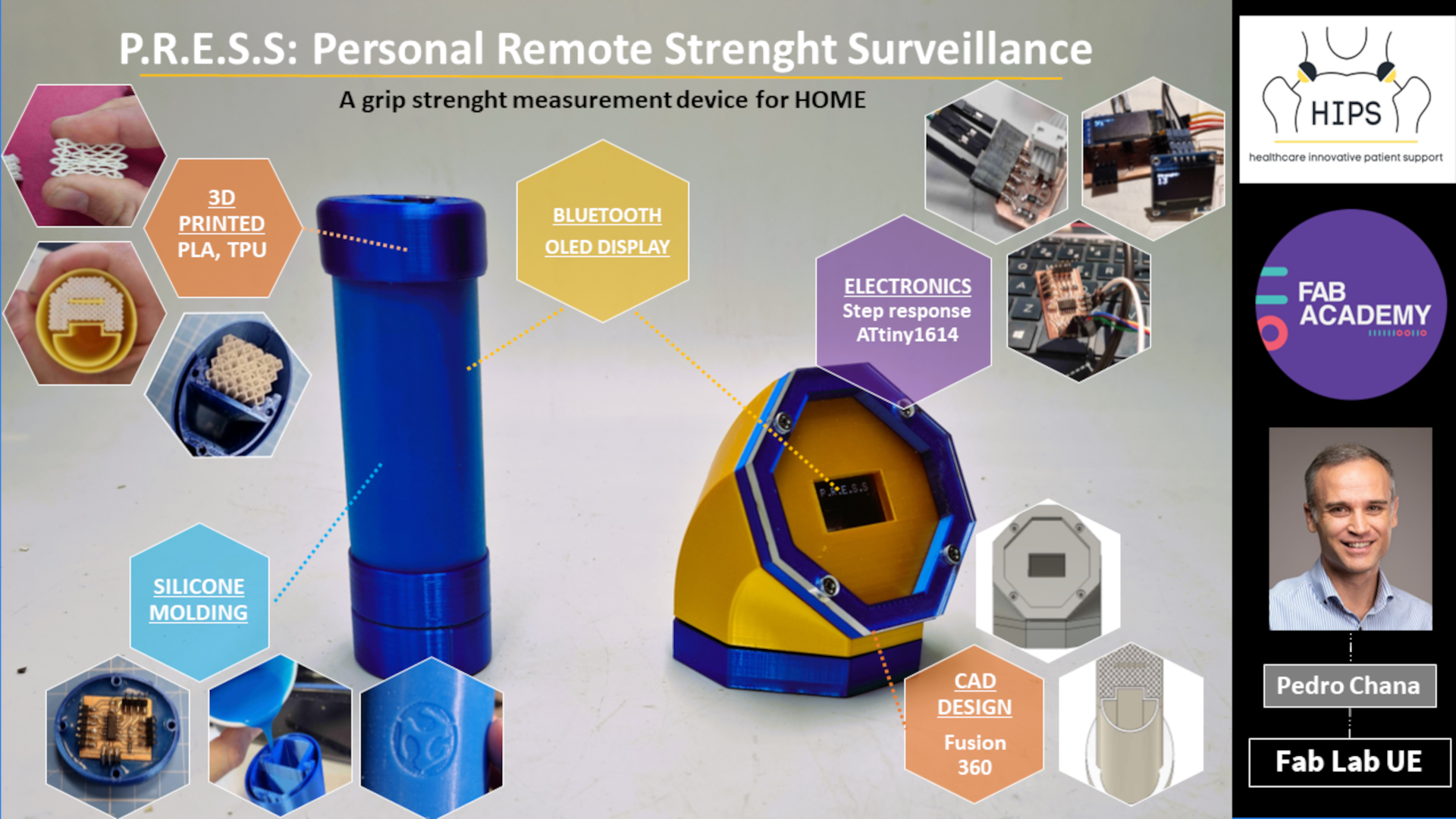
VIDEO
QUESTIONS AND ANSWERS
1. What will it do?
As a Healthcare professional and researcher, my aim is to incorporate digital fabrication, trough frugal innovation, into the healthcare environment, to fill the gap that new technologies and real world data are creating. One of these needs is to start measuring objective and clinically significant variables in non-clinical settings, that can help healthcare professionals decision making. And one the most relevant variables, considered a biomarker (a variable that by itself can have a significant impact on health issues) is grip strenght.
So, what my device will do, is to be able to measure in non-clinical environments (at home) grip strenght, with a digital fabrication device, in order to be able to help healthcare professional decision making. But for that being possible, fabrication has to be sustainable. My goal is that this device can be created on demand in any hospital, that means that they should have a small fablab prepared to desing and produce personalized objects for therapeutic purposes, contributing to improve the quality of life of patients.
2. Whose done what beforehand?
In relation to who has done something similar before, after exploring in the fabacademy repositories, I haven´t found any past student that has done this before. Actually, there are few studies that explore alternative ways of measuring grip strenght usign frugal innovation, such as:
3. What will you design?
For this project, my idea is to design and create everything I can form scratch, divided in the following sections:
The only components that I won´t create or design are the Oled module display (128x64) and the bluetooth HC-05.
4. What materials and components will be used?
MATERIALS AND COMPONENTS TO USE:
PARTS OF THE PROJECT | COMPONENTS USED |
---|---|
Grip design | 3D printing filaments (PLA and TPU) and silicone 20 shore for insert molding. |
Data display | 3D printing filament PLA and metachrylate. |
Step response: | Electronics: pcb board (FR1), 2 resistors, 1 capacitator, ATtiny1614, one 3x6, two 3x4 and one 3x3 pin connectors, and dupont cables. |
For the Oled module and HC-05 board: | pcb board (FR1), ATtiny1614, 2 resistors, 1 capacitator, one 3x6, two 3x4 and one 3x3 pin connectors, and dupont cables. |
General material: | Sand paper, glue. |
5.Where will they come from?
The 3D printed material will come from recreus and geetech supliers, and the silicone will come from Reschimica and all delivered by amazon. Regarding the electronics, all the materials needed will come from Digikey and Amazon.
6.How much will they cost?
COMPONENTS USED | UNITS | UNIT PRICE | UNIT TOTAL PRICE |
---|---|---|---|
PLA and TPU filament | 150grms | 2.5 euros | 2.5 euros. |
Silicone | 80grms | 6 euros | 6 euros. |
Oled module display | 1 | 6 euros | 6 euros. |
HC-05 bluetooth module | 1 | 6 euros | 6 euros. |
ATtiny 1614 | 2 | 0,97 euros | 1,94 euros. |
Power supply: 3.7 battery or powerbank | 2 | 7,5 euros | 14,99 euros. |
Other consumables (resistors, capatitators, connectors, cables, 50x50mm of 3mm-acrylic,..) | 1 | 5 euros | 5 euros. |
Total (aprox) | 29 euros |
7.What parts and systems will be made?
As I mentioned before, my itention is to make everything from 0, except the Oled module display and the HC-05 bluetooth.
8.What processes will be used?
The processes used for this project will be:
- For the Grip and Display designs: I´ll use Fusion 360.
- For the grip silicone coating, i´ll use it as insert molding using a 3D printed mold of the grip.
- For the electronics schematics and pcb design: I´ll use eagle from Fusion 360. And they will be produced in the Roland Modela MDX-40A to be soldered after.
- To program my boards i´ll use Arduino IDE and will connect both boards wirelesly via Tx-Rx (master-slave). And i´ll use as the interface processing to view in the computer the values .
- I´ll laser cut the acrylic designed in autocad for the display module.
9.What questions need to be answered?
At this point of the fabacademy, no critical questions need to be answered. I had to wait until input and output assignments in order to understand and have the knowledge about how I could measure grip strenght the most effective way, with digital fabrication, avoiding hysteresis and mapping the initial values.
Now, the question I need to answer (by doing several iterations and tests) is how I have to design the inner structure of my grip device in order to have the optimal measurement regarding materials and the step reponse. To do it, i´ve researched thoroughly everything related to metamaterial designs and 3D printing. So, i´ve learned a lot and managed to design something clinically useful.
Other question that needs to be answered is, how many data do I need to register per second so its future analysis can be clinically useful. To do it, I also had to research the evidence and obtained a minimum of 5 measurements per second, so, we´ve programmed to register 10 measurements per second to be sure we fulfill the standards.
To achieve my aim. I reviewed the literature in order to obtain how many measures per second are needed for an optimal value, and during how much time:
ARTICLE/SENSOR | SETTINGS USED |
---|---|
Grip sensor 4256-E: | 10 measurements per second, in a minimum of 10 seconds. |
Intrinsic hand strenght measurement, 2017: | No description, uses arduino board. |
Distal phalanges strenght measurement, 2017: | 5 measurements per second, uses arduino board. |
Weight load measurement on crutch: | 10 measurements per second. |
Bachelors degree final thesis: | From 5 to 10 measurements per second. |
Robotics, 2017. | Measuring between 3 and 10 seconds duration. |
The Gold Standard hand grip measurement protocol, indicates that to measure maximum grip strenght we need between 3 to 5 seconds of time measurement. From that time onwards, the maximum peak force decreases.
10.How will it be evaluated?
To evaluate it with a fist spiral, we need it to give stable data, not overpassing the mapping values with a biofeedback use. For a second spiral, we will test repetitive measures to see if the values are optimal, and will compare them with the gold standard dynamometer used to measure grip strenght in clinical environments. And for a third spiral, we will test it with volunteers of different genders and antropometric characteristics to test it´s utility and making changes regarding their experience and opinions.
FABRICATION PROCESSES
All the information regarding the final project 2D and 3D designs, fabrication processes and programming of my own fabbed microcontroller PCB, in a cronological/task order, including the input and output devices, and links of the weekly used assignments, are in the PROJECT DEVELOPMENT section.
FILES
2D DESIGNS:
Download Grip design top, body and bottom part .f3d files.
Download Display acrylic screen design .dxf file.
Download Display design top, body and bottom part .f3d files.
Download TPU grid design flexible material .f3d file.
Download fablab logo .svg file.
3D DESIGNS:
Download Grip design top, body and bottom .stl files.
Download TPU grid design flexible material .stl file.
Download Display design top, body and bottom part .stl files.
ELECTRONIC DESIGNS:
ATtiny1614
Download ATtiny 1614 board schematic and board files.
Download ATtiny 1614 board traces and interior .png files.
Step response
Download ATtiny 1614 board schematic and board files.
Download ATtiny 1614 board interior and traces .png files.
INTERFACING AND PROGRAMMING:
Grip ATtiny 1614
Download spiral 1, spiral 2, Grip ATtiny 1614 arduino IDE .ino file.
Computer display via processing interface
Download spiral 1 Processing interface Processing .pde file.
Display module
Download spiral 2 Display ATtiny 1614 arduino IDE .ino file.
Back to top.