Molding and Casting and something else......
Group Assignment 2022 (Raffaele Alone)
On this page I will be putting everything related to the review of the safety data sheets of each of their molding and casting materials, then I will compare the test models with each of them.
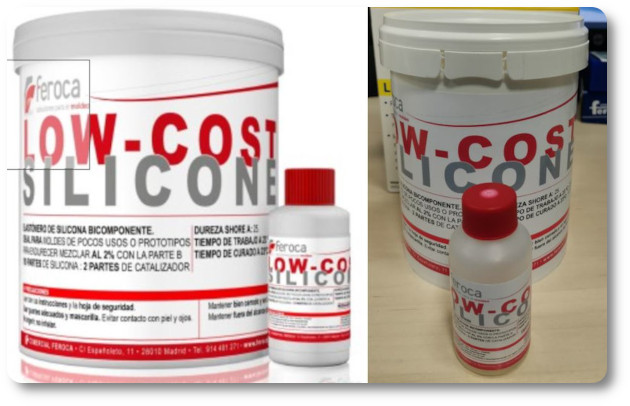
COMPOSITION | HAZARDS ID. 1 | HAZARDS ID. 2 | HAZARDS ID. 3 | HAZARDS ID. 4 | HAZARDS ID. 5 | HAZARDS ID. 6 | Advice 1 | Advice 2 | Advice 3 | Advice 4 | Advice 5 | Advice 6 |
---|---|---|---|---|---|---|---|---|---|---|---|---|
Siloxanos y Silicatos, Silicato de tetraetilo, Bis, Titanium tetrabutanolate | Flammable liquids | Acute toxicity | Irritación ocular | Eye irritation | Specific target organ toxicity | Specific target organ toxicity | Request special instructions before use | Keep away from heat | Do not breathe dust | Wear protective gloves/ clothing/ goggles/ mask. | SKIN CONTACT. Immediately remove all contaminated clothing. | In case of fire use water spray |
Cost Silicone is a two-component silicone elastomer (parts A and B) that cures at room temperature, the base (part A) has the appearance of a viscous liquid that, after the addition of the catalyst (part B), becomes elastic. material. It features outstanding fluidity and good operability. It is recommended for the application of molds for casting Plaster, Polyester Resin, Polyurethane Resin, Epoxy Resin, Fiberglass, Wax, Soap, Bronze, etc. viscosity using Silicone Fluid. It is suitable for molds with complicated gaps that are difficult to remove from the mold.
Instructions for use
- Prepare the box for the mold and the original.
- Set aside 100 parts of the base (Part A) and add 2 parts of catalyst (Part B), mix both parts VERY well until a homogeneous mixture is achieved.
- Pour the silicone wash into the box or apply with a brush if it has been previously thixotroped.
- NOTE: Normally, low hardness silicone is used for casting molds, as it allows a better demoulding and thus does not damage the original.
- Wait 15 hours for the silicone to solidify and remove the mold.
Here are some interesting links
- To purchase the product visit the page by clicking here.
- To purchase the Low Cost Silicone Datasheet clicking here.
- To purchase the Safety data Sheet Part A: clicking here.
- To purchase the Safety data Sheet Part B: clicking here.
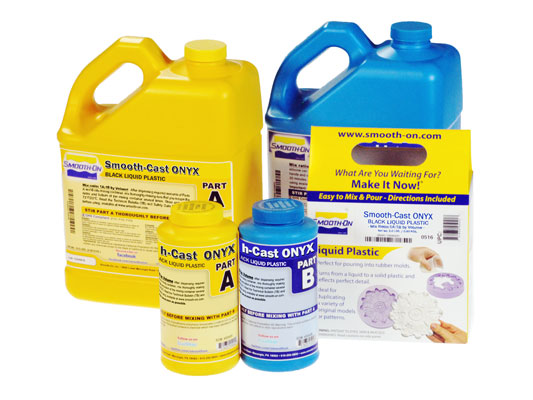
COMPOSITION | HAZARDS 1 | HAZARDS 2 | HAZARDS 3 | HAZARDS 4 | HAZARDS 5 | HAZARDS 6 | IF ON SKIN: | IF INHALED: | IF IN EYES: | IF SKIN |
---|---|---|---|---|---|---|---|---|---|---|
Polyurethane Elastomer | Skin corrosion/irritation | Skin sensitization | Eye Damage/irritation | Acute toxicity, inhalation | Respiratory Sensitization | Specific target organ toxicity | Wash with plenty of soap and water. | Remove person to fresh air and keep comfortable for breathing. | Rinse cautiously with water for several minutes. | Get medical advice/attention. |
Smooth-Cast™ ONYX™ is a mercury-free urethane resin that cures at room temperature to a deep black, solid plastic. ONYX™ resins offer the convenience of a 1A:1B by volume mix ratio and have very low viscosities, so they are easy to mix and pour. ONYX™ resins have an ultimate Shore hardness of 80D and offer higher physical properties and higher heat resistance vs. other general purpose resins.ONYX™ FAST resin has a pot life of 2.5 minutes and a cure time of 10-15 minutes. ONYX™ FAST is a good choice for creating fast cold cast bronze, brass, copper, nickel/silver, etc. effects.
Instructions
Preparation - All liquid urethanes are moisture sensitive and will absorb atmospheric moisture. Water based clays are not recommended. Mixing tools and containers should be clean and made of metal or plastic. Materials should be stored and used in a warm environment (73°F/23°C). This material has a limited shelf life and should be used as soon as possible. Mixing should be done in a well-ventilated area. Wear safety glasses, long sleeves and rubber gloves to minimize contamination risk. Because no two applications are quite the same, a small test application to determine suitability for your project is recommended if performance of this material is in question.
Applying A Release Agent - A release agent is necessary to facilitate demolding when applying into or over most surfaces. Use Mann’s Ease
Release 200 which will release both urethanes and silicones. A liberal coat of release agent should be applied onto all surfaces that will contact the plastic. IMPORTANT: To ensure thorough coverage, apply release and brush with a soft brush over all surfaces. Follow with a light mist coating and let the release agent dry for 30 minutes.
Here are some interesting links
- To purchase the product visit the page by clicking here.
- Safety data Sheet clicking here.
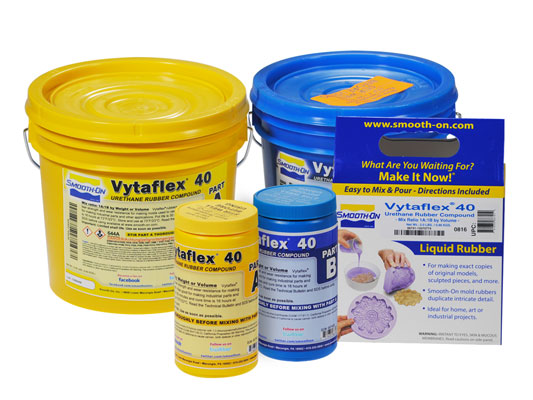
COMPOSITION | HAZARDS 1 | HAZARDS 2 | HAZARDS 3 | HAZARDS 4 | HAZARDS 5 | HAZARDS 6 | IF ON SKIN: | IF INHALED: | IF IN EYES: | IF SKIN |
---|---|---|---|---|---|---|---|---|---|---|
Polyurethane Elastomer | Acute toxicity, oral | Acute toxicity, dermal | Acute toxicity, inhalation | Skin irritation | Eye irritation | Specific target organ toxicity | Wash with plenty of soap and water. | Remove person to fresh air and keep comfortable for breathing. | Rinse cautiously with water for several minutes. | Get medical advice/attention. |
Using Smooth-On’s exclusive “V-Polymer™” technology, VytaFlex™ urethane rubbers offer superior physical and performance properties for casting concrete. VytaFlex™ urethanes are available in 10A, 20A, 30A, 40A, 45A, 50A and 60A Shore hardness’s and feature convenient one-to-one by volume mix ratios. Vacuum degassing is not necessary and VytaFlex™ rubbers cure with negligible shrinkage to a durable rubber that will last in production. VytaFlex™ mold rubbers work especially well for casting pigmented / colored concrete. Molds made with VytaFlex™ Series urethanes will render accurate and uniform colored castings.
Instructions
Preparation - Store and use at room temperature (73°F/23°C). These products have a limited shelf life and should be used as soon as possible. Use in a low humidity environment (below 50% RH). Mixing containers should have straight sides and a flat bottom. Mixing sticks should be flat and stiff with defined edges for scraping the sides and bottom of your mixing container. Good ventilation (room size) is essential. Wear safety glasses, long sleeves and rubber gloves to minimize contamination risk.
Applying A Release Agent - A release agent is necessary to facilitate demolding when casting into or over most surfaces. Use a release agent made specifically for mold making (Universal™ Mold Release available from Smooth-On). A liberal coat of release agent should be applied onto all surfaces that will contact the rubber.
IMPORTANT: Stir Part B thoroughly before dispensing. After dispensing equal amounts of Parts A and B into mixing container, mix thoroughly for at least 3 minutes making sure that you scrape the sides and bottom of the mixing container several times.
Here are some interesting links
- To purchase the product visit the page by clicking here.
- Safety data Sheet clicking here.