3D scanning and printing
Design and 3D print an object (small, few cm3, limited by printer time) that could not
be easily made subtractively
3D scan an object, try to prepare it for printing (and optionally print it)
Group
assignment:
Group Assignment
Here you can find the
group assignment.
3D scanning
Setup
- Prepare the EinScanPro+: Mount it to the tripod (if you are doing a fixed scan and not a handheld one) and connect it to the PC. Other details are found in the manual
- We also set up the camera to the scanner, to capture the texture of the scanned object
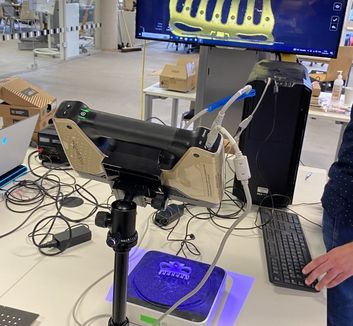
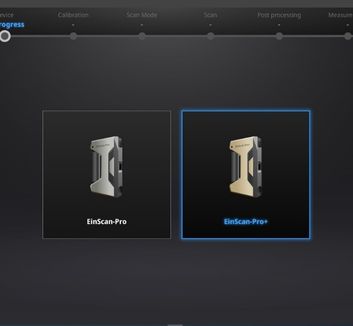
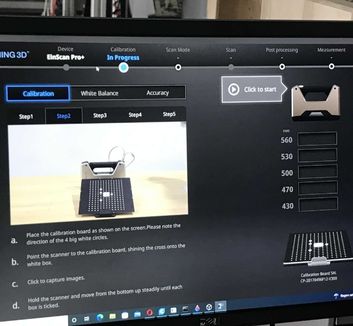
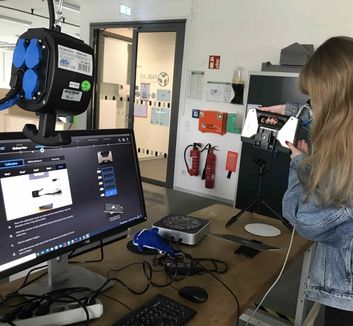
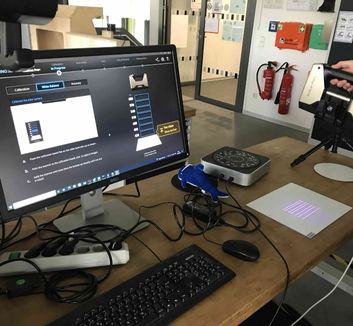
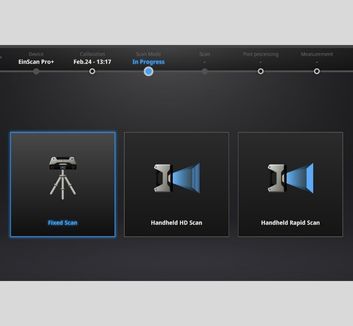
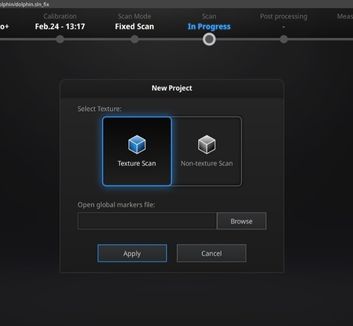
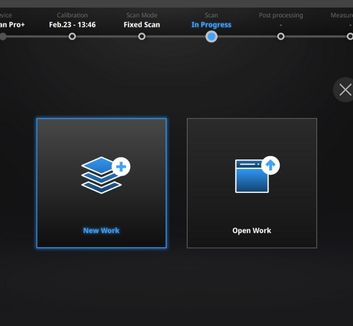
Settings
After putting the scanner back on the tripod, you now can start scanning your desired object. In my first attempt, I want to scan my hairclip, so I can alter the basic model to design my own version of it. Now it's important to get the settings right, there are a few options:- The very first thing to adjust is the brightness . It can be changed via the slider and changes what will be recognized by the scanner. Everything that is shown in red on the camera above will be scanned.
- HDR: The High Dynamic Range setting is used for objects with a high contrast in color (e.g. black and white). If HDR is checked, you will not be able to adjust the brightness by yourself, the program will do it for you so that all the bright and dark spots are scanned in the first go.
- "With Turntable" activates the turntable when checked, so that a fixed scan is possible and the model gets rotated on the turntable.
- The turntable steps determine in how many steps the turntable will rotate. During the process of scanning your object, you should at least once select an even and an odd number, to scan the object from every angle.
- The Align Modes: There are 3 different Align Modes to work with: Turntable Coded Targets, Features and Markers.
- Turntable Coded Targets uses the coded white targets on the turntable as markers for the orientation off the object. While using this mode, you cannot change the position of the object you want to scan.
- But after a few scans you can change to Features: Features does not use any premade markers, it detects features of the to-be-scanned object by itself.
- Markers recognizes little Marker stickers you can put on your object. (But I discourage from using it. At the place of the markers, holes will be left behind in the model , Marker Stickers also fall off easily.)
Scanning
In my first attempt I tried to scan the hairclip with Turntable Coded Targets and self adjusted the brightness.
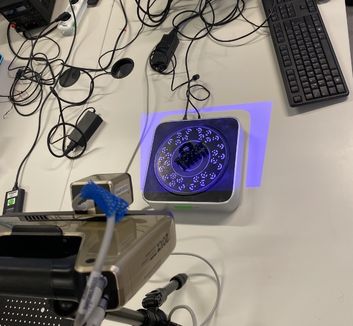
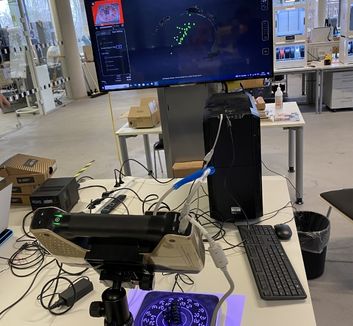
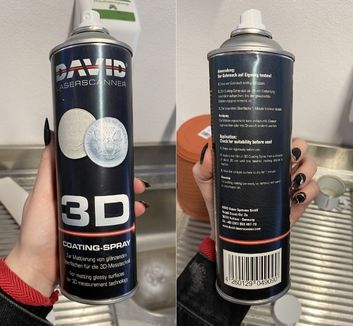
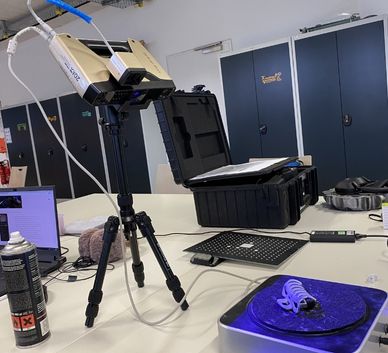
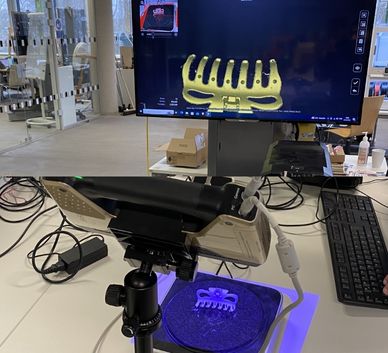
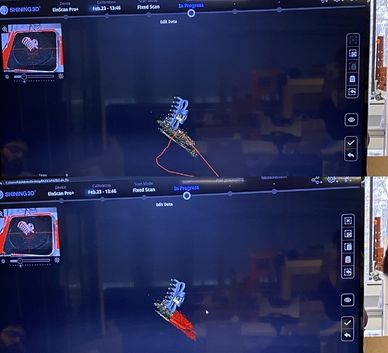
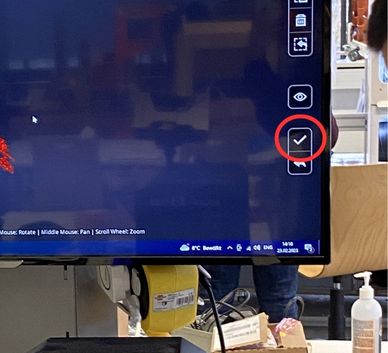
We did a lot of scans. Features was the most used method. We variied between even and odd turntable steps and changed the position/rotation of the hairclip to scan every angle of it.
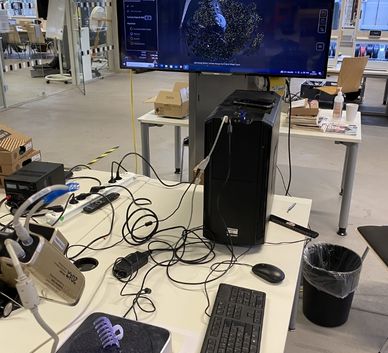
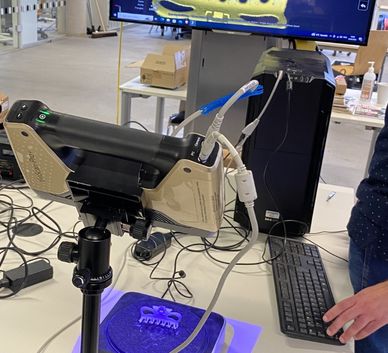
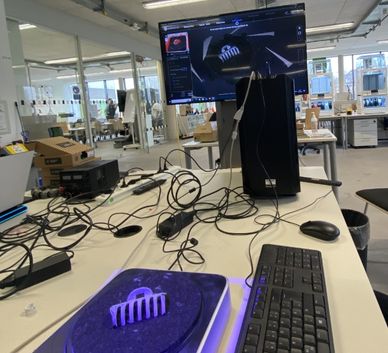
Once you are happy with the point cloud and every area seems to have been scanned, you can mesh your model:
- When meshing, choose Watertight model (this will make sure,that you don't have holes in the surface of your model.)
- I also chose High detail (Produces the highest resolution, but also the biggest file, choose what's best for you. You can always remesh it later e.g. in Blender.)
- If needed, you can make any last adjustments fter meshing. I didn't have to. So I saved.
- The program also shows you the dimensions of your model. It is very accurate to the dimension of my real hairclip.
I scanned all parts of my hairclip individually to get one model for every part.
Therefore I repeated the steps described above for the other side of the clip and for the
spring.
While the other side of the clip worked wonderfully just like the one before, the spring made
problems. It is very featureless and has no indicator which could show the program: "This is up,
and this is down" since it's very symmetrical.
Even though it is the much less complex object, it made the most problems. I had to scan it
from various angles to get the missing parts:
I helped myself with some coins to vary the angle just slightly.
In the end, I managed to scan all parts successfully.
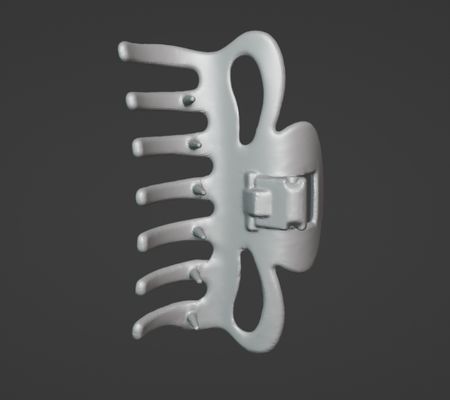
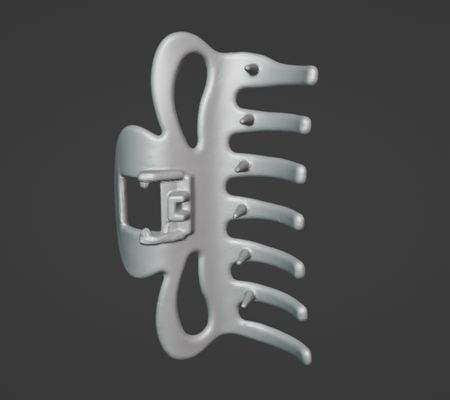
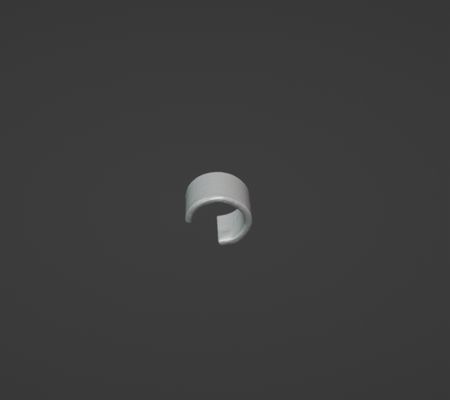
All parts together in Blender:
Editing in Blender
I want to create a butterfly hairclip. Now with the base model scanned, I will add the butterfly
part with Blender.
Tutorials I watched during the process:
Artistic trees in Blender |
Quad Remesh
Preparing the basic model
Steps: (Read from left to right)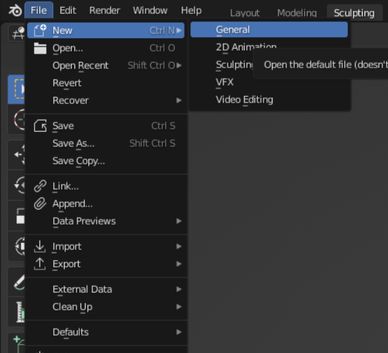
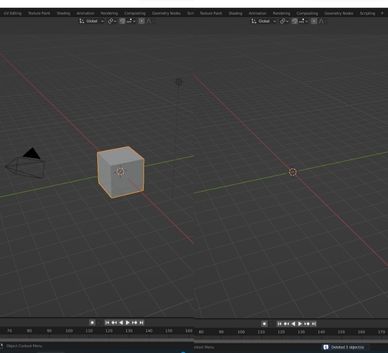

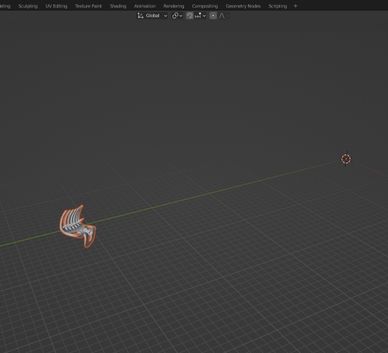
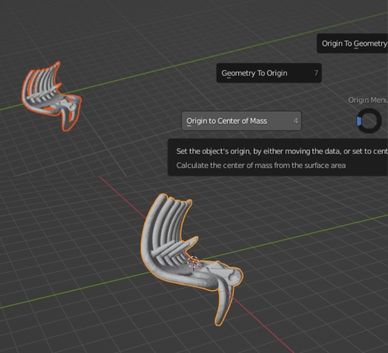
This centers it.
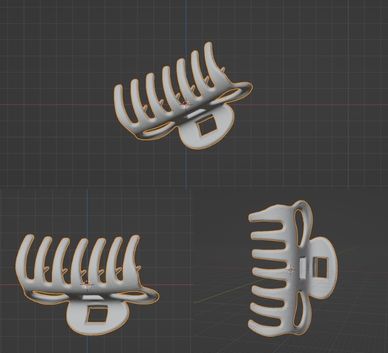
Other movement controls: G -> Grab & Move | Ctrl+M followed by X,Y or Z to mirror | S -> Scale
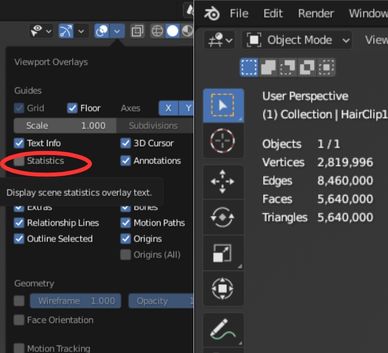
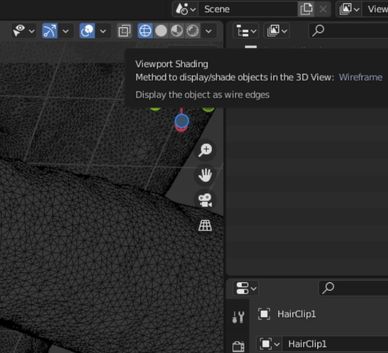
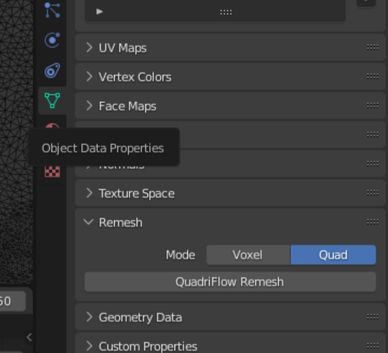
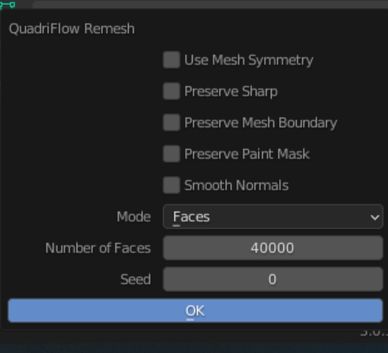
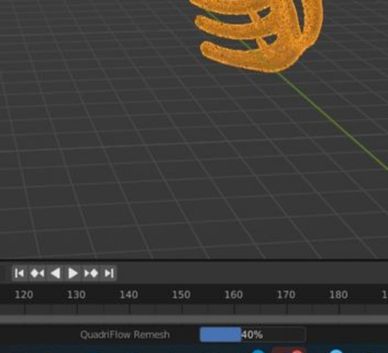
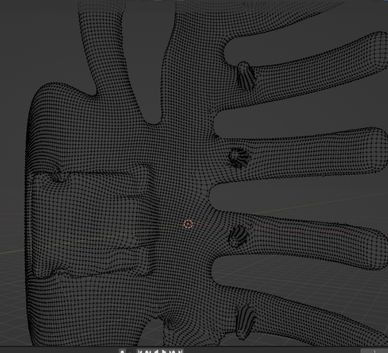
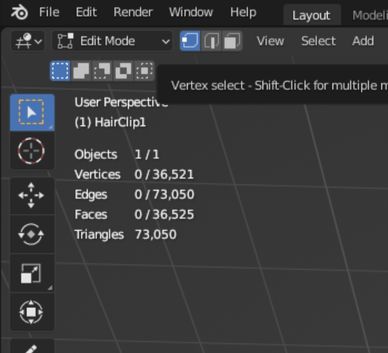
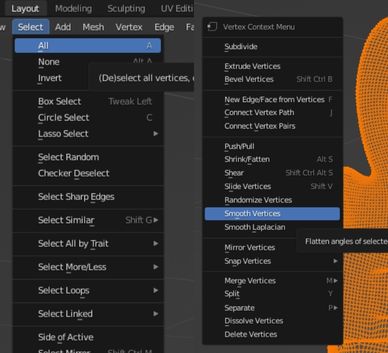
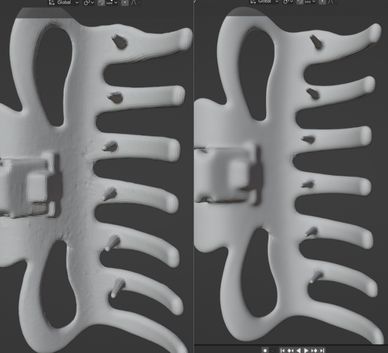
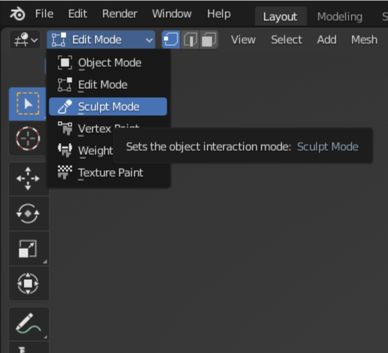
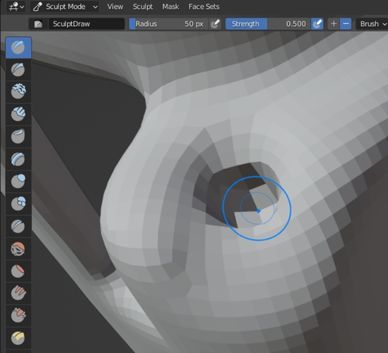
Creating the butterfly
Inspo: (Picture from SHEIN website)
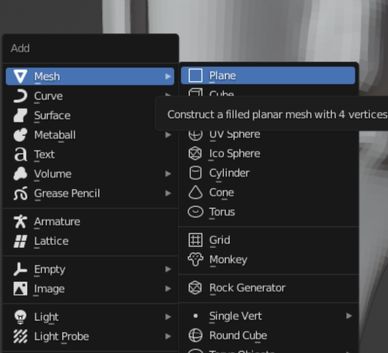
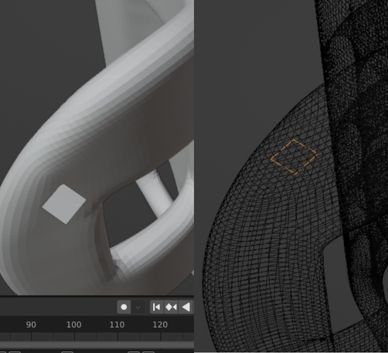
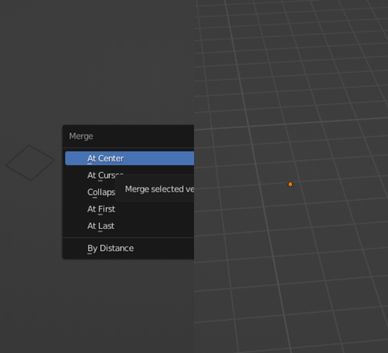
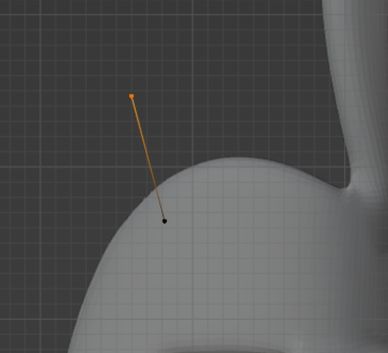
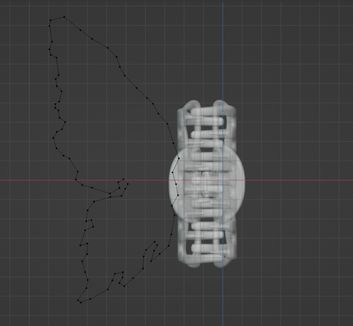
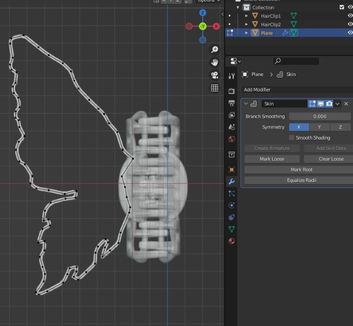
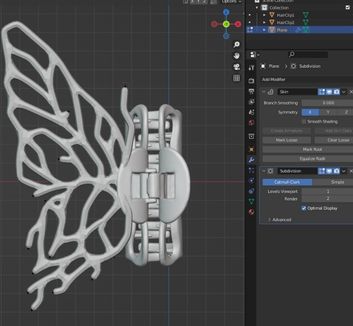
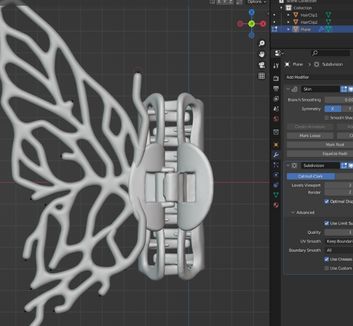
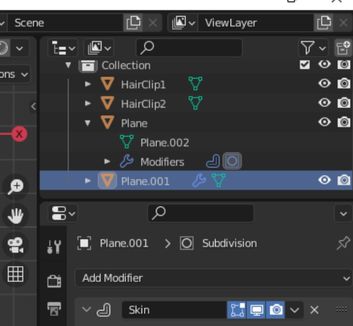
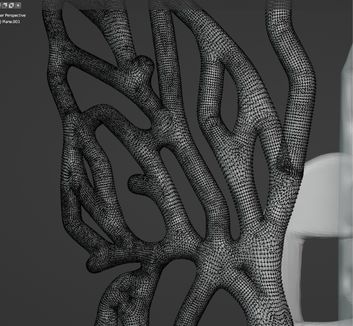
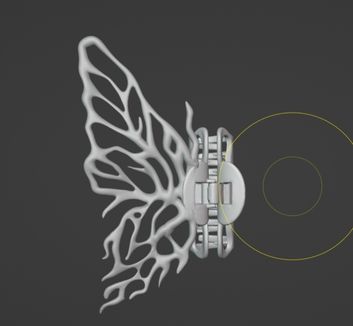
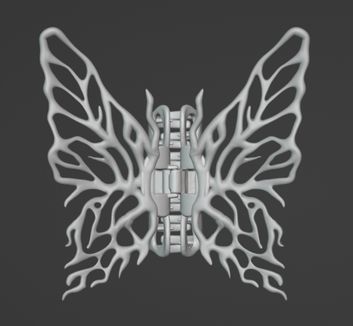
3D printing
Formlabs resin printer
I want to print my butterfly hairclip with a resin printer, since the finish is a lot smoother and shinier and it's a bit faster. For this, open PreForm and prepare your resin printer.
Preparing the file
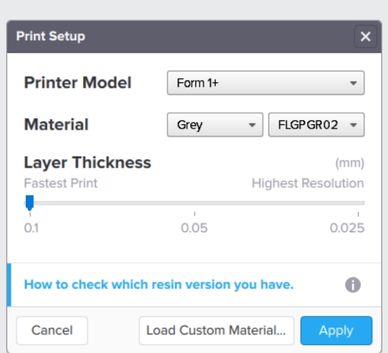
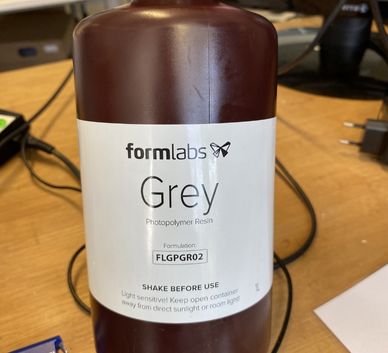
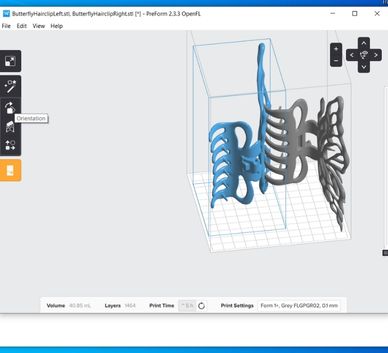
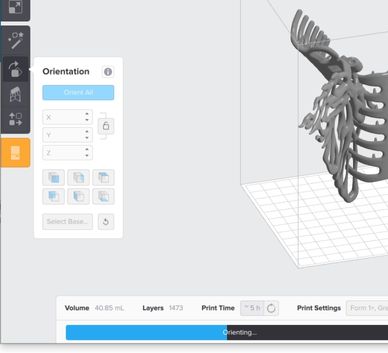
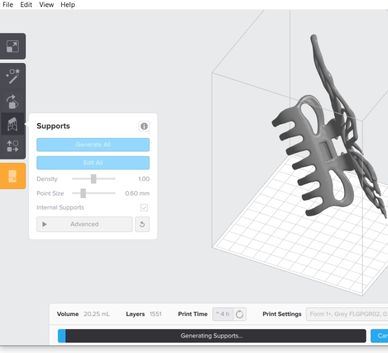
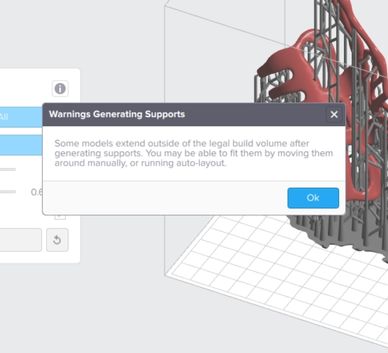

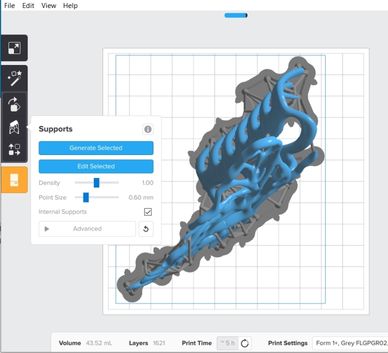
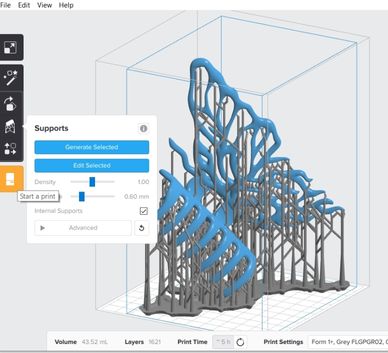
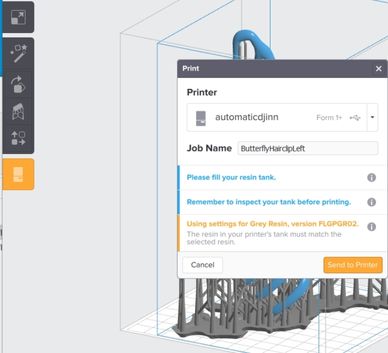
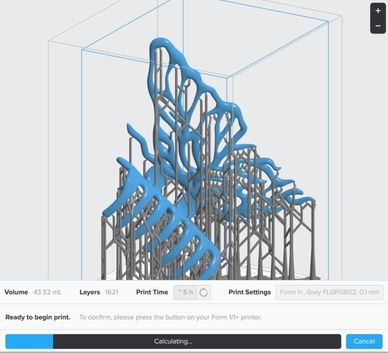
Preparing the printer
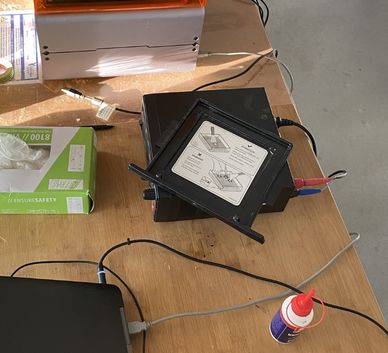
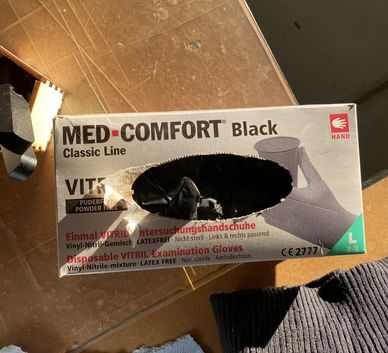
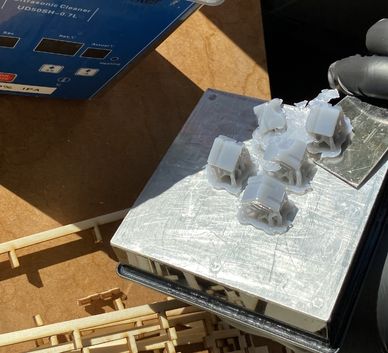
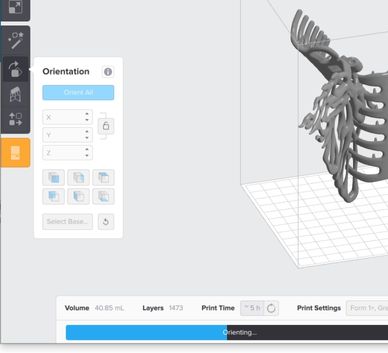
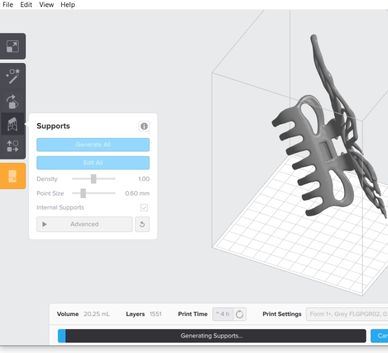
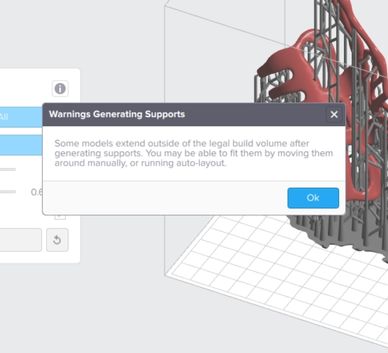

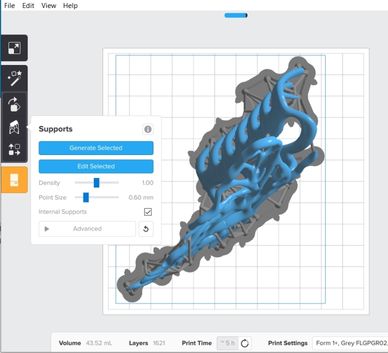
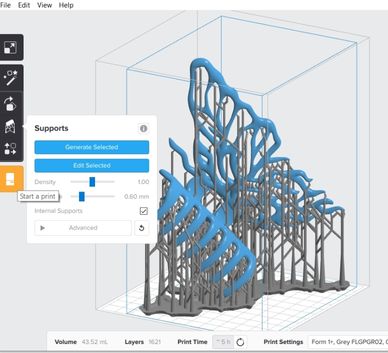
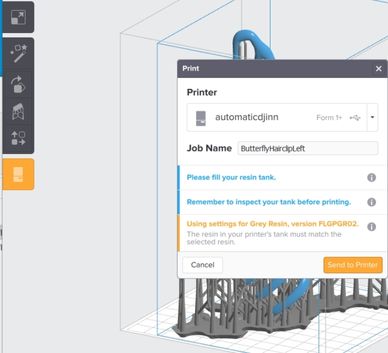
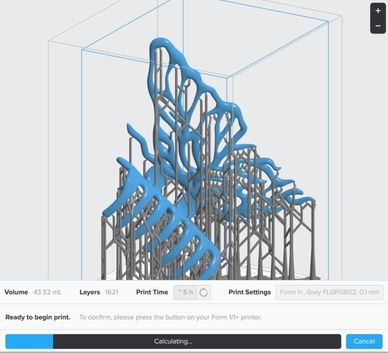
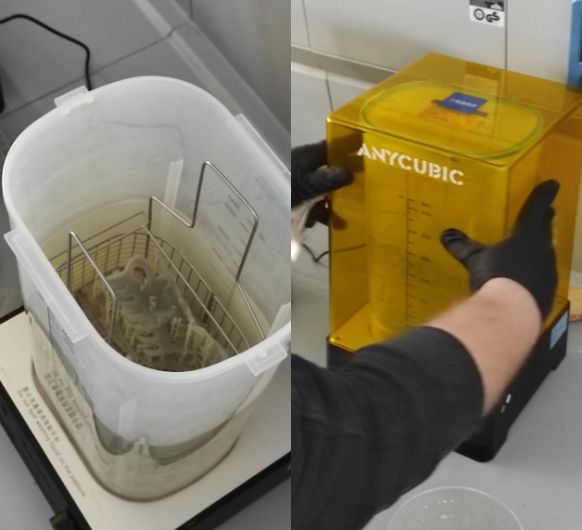
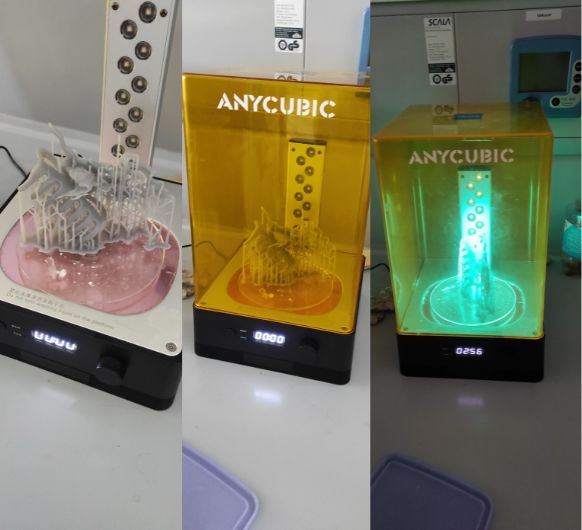
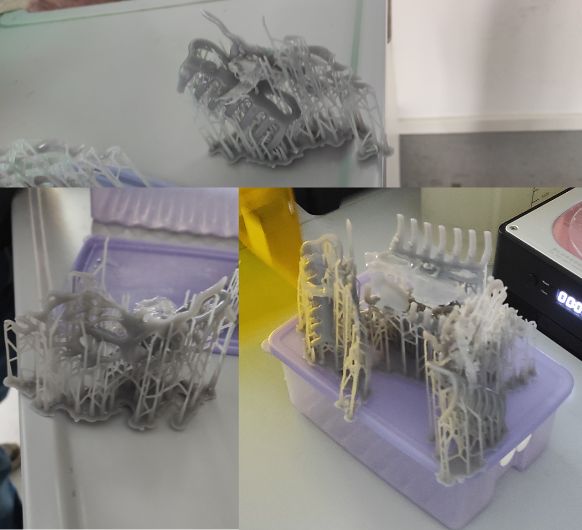
Ultimaker S5
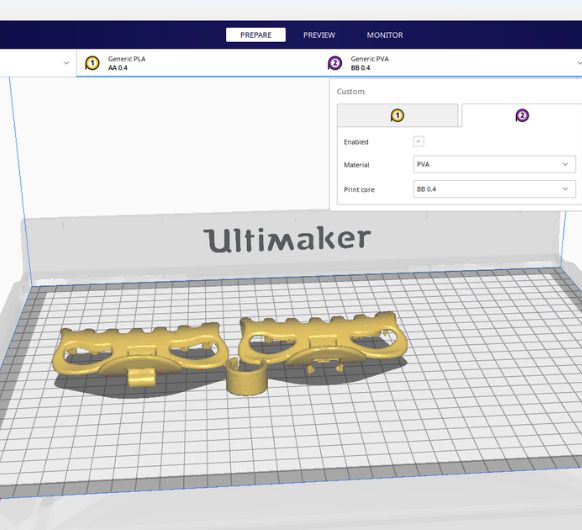
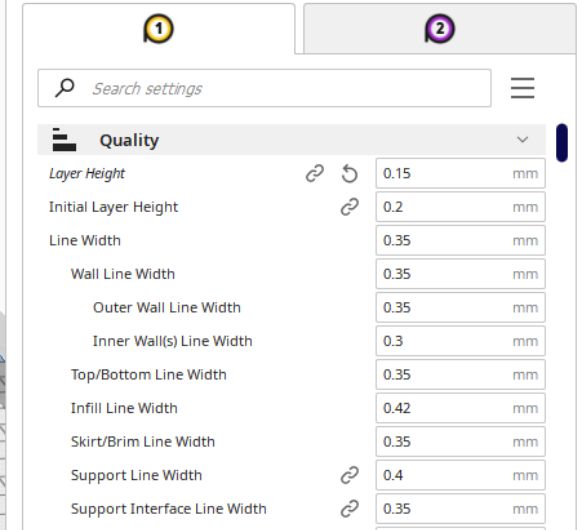
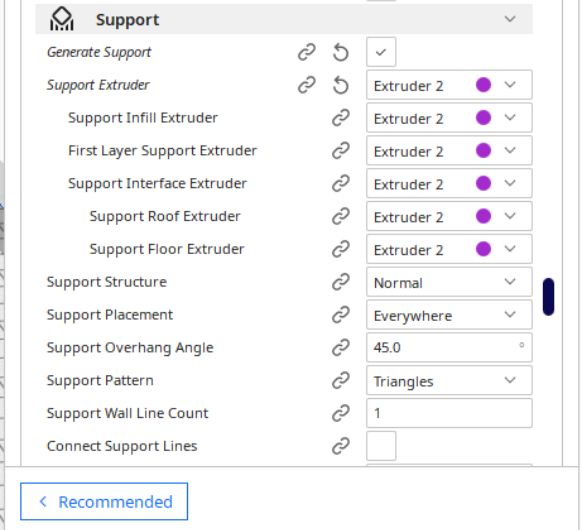
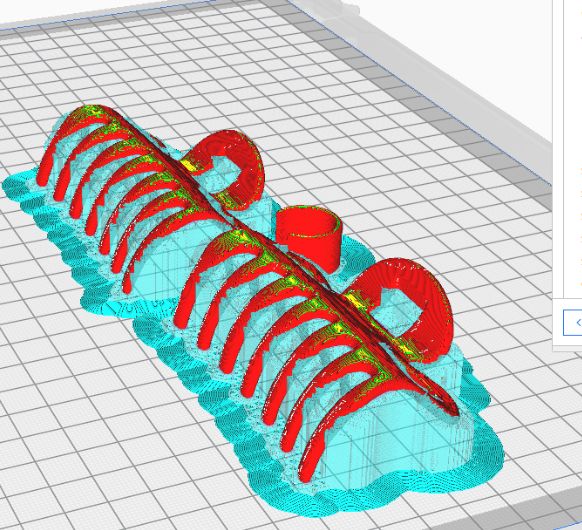
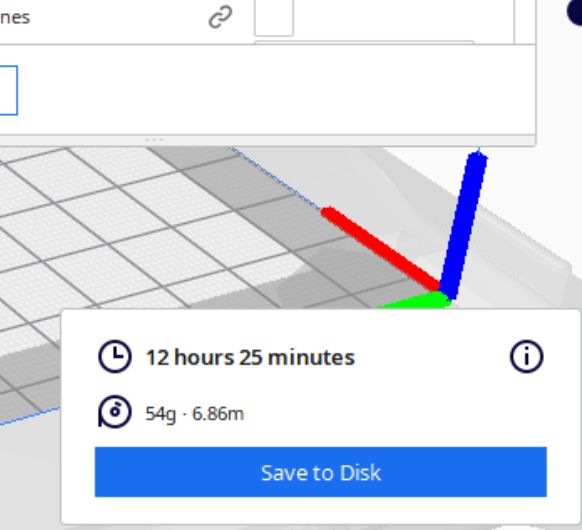
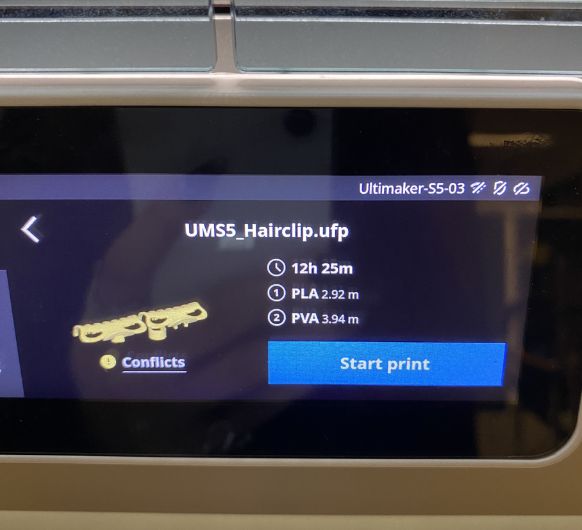
(2022) Preparation in Blender
Last year I scanned this donkey using the same method as with the hairclip.
Since I wanted to use the 3D scanned donkey as my 3D print object, I first had to import the
.obj file into Blender, to adjust the size of vertices/polys (reduces size of the enormous
file):
(A fellow Fab Academy student showed me how to do this, but this tutorial is also very helpful)
- Import the .obj
- Add Modifier > Decimate
- I reduced the ratio from 1.0 to 0.001. This gave the donkey a nice low-poly look and got rid details that would be too much for the 3D printer (reduced the face count from 2299602 to 2298).
- Now the unnecessary platform underneath had to be removed to create a flat ground. This can be done with Boolean operations, that can also be added via the Modifier tab. See tutorial.
- Simply add a box (Shift+A) of the needed size and place it where the donkey model should be cut.
- Now add the "Boolean" Modifier (it needs to be applied to the object that is being cut):
- Choose the cube as the cut "tool"
- Et voilĂ :D
Preparation in Ultimaker Cura
-min.png)
-min.png)