Assignment 17 - Applications and Implications
Assignment
- Propose a final project masterpiece that integrates the range of units covered, answering the Questions below!
Intro
For my final project, I am going to design and build a vertical farming machine. It will should able to attend to plants on multiple levels, automatically tedning to plants that need attention by gathering sensor readings.
What will it do?
The whole contraption will look like a giant cylinder. Movement wise, the inner circle on which the toolhead and the z-axis are resting, should be able to freely turn around 360 degrees or at least 180 degrees in both directions. Coupled with the movement of the z-axis, moving the toolhead up and down the cylinder, a third axis will be present on the toolhead, which will move the tool from the inside of the central circle to the outside of the circle, to reach the plants opn the outside. The machine will gather data from the plants via a combination of soil moisture sensors and temeperature and humidity sensors. These sensors will be connected in Groups to small PCBs, whichs job it will be to accumulate the data presented by the sensors. These gathering modules will then each send their findings to a central "Mainboard", which will then grab all of the data. Here, an algorithm will be sorting through the data, determining if a plant needs water and if multiple plants need water, which plant will be watered first. Since this task is not really real time dependant, the sensor reading do not have to be shipped to the mainboard constantly, but rather in boigger time intervals. Once the plants, that need attention are identified, GCode has to be created, which will move the Toolhead to the desired position for each plant. To move the stepper motors, I will use my already created and tested stepper driver Board, using GRBL and an ATmega328p. Since this project will later on be developed further by myself as part of my masters thesis, more applications will be added later on. For now, these include a new design for the tool head, which should then be able to slot into the planting pots and lift them up, as to reorganize them within the cylinder, as well as the connection of this project with other projects already developed by ITQ, by connecting the machine to the existing Cloud network.
Who's done what beforehand?
There are many things that were done beforehand. I will mainly focus on stuff that was being done beforehand in Fabacadamy, but i will also shortly describe what was done at ITQ beforehand. At ITQ, as I stated above, demonstrators already exist, which are able to attend to a planting bed, not only watering the plants, but also planting new plants as well as distinguishing between plants and weeds, and removing weeds automatically. This demonstrator is build like a portal robot, moving on a X/Y-axis. As to the projects that were done beforehand in Fabacademy, the topic of agriculture is gigantic. Thankfully the Argilab has put together a list of (almost) all agriculture related fabacademy projects on own website. Here I could take a look into many projects. The projects that helped me the most were:
- The portal farming bot from ITQ (I have to reassure that I can share this, will update here later if im able to share)
- For the later applications of this project, my main influence came from robots that sort stuff
- Mainly this park robot that sorts cars in a vertical garage: Link
- Automated sorting systems used in logistics like this one: Link
- And of course the many agriculture based projects from previous Fabacadany years, first and foremost this one:
- Grow It Yourself
This was the first project I saw when I first visited the Fablab in Kamp-Lintfort and I was fascinated. I guess this fascination juts stuck around.
What will you design?
My overall plan is, that apart from standard parts I will be using, I am going to design everything else by myself. This includes the mechanical parts and the electrical parts. For example, I already designed the mechanical "shell" of the machine:
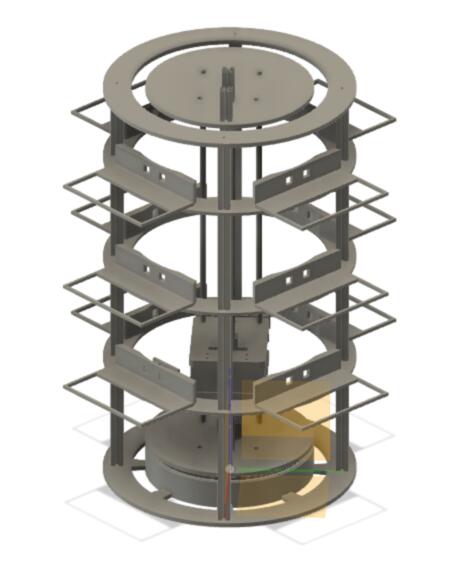
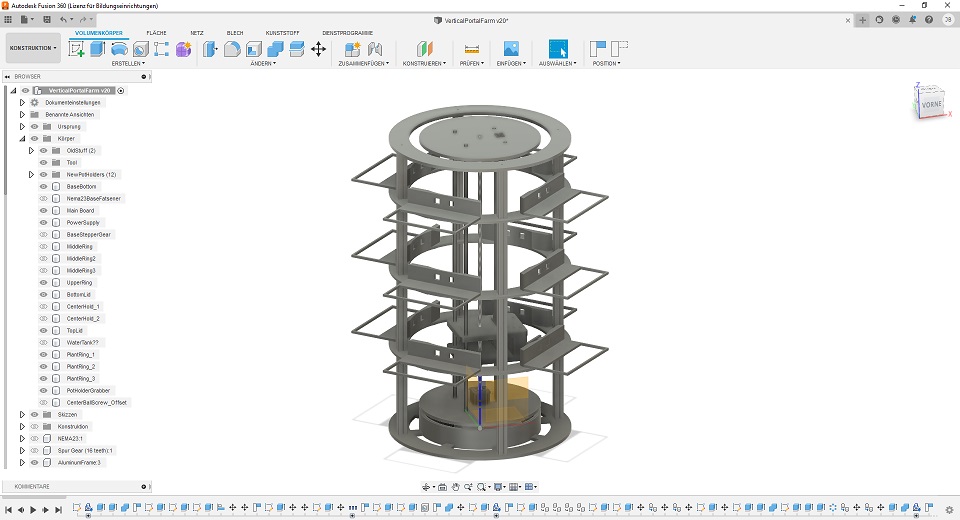
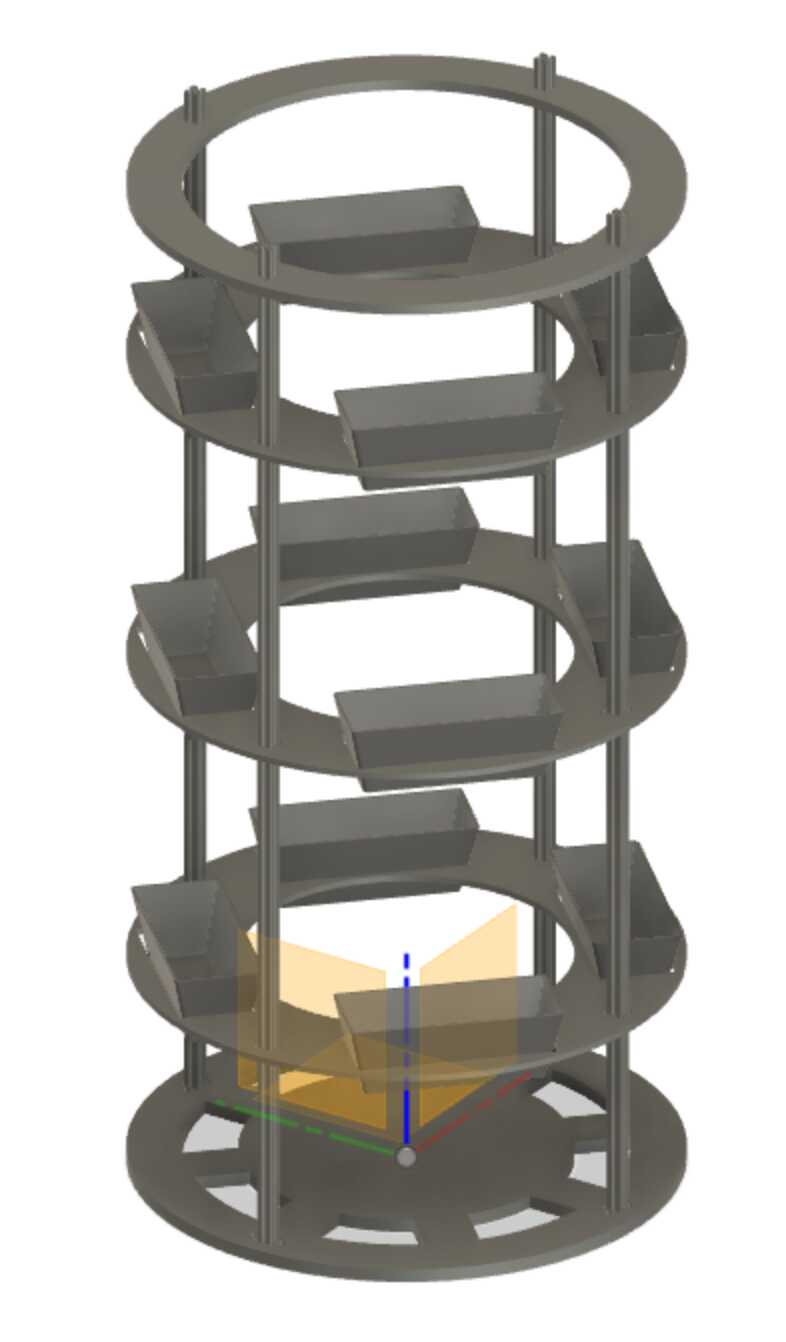
There are different versions, as the further development of the machine requires other mechanical properties. For the final project of the FabAcadamy, the machine should be able to warter the plants. This will be done with the third CAD model from above.
I also already designed the stepper motor driver Board in multiple iterations with multiple failures. For everything regarding the stepper driver Board, you can read up about it on my Machine Building Week page. What I still need to design, are the Boards, that receive the data from the sensors via I2C and the Main Board that gathers all the data and generated the GCode accordingly and then sends it off to the stepper driver Board.
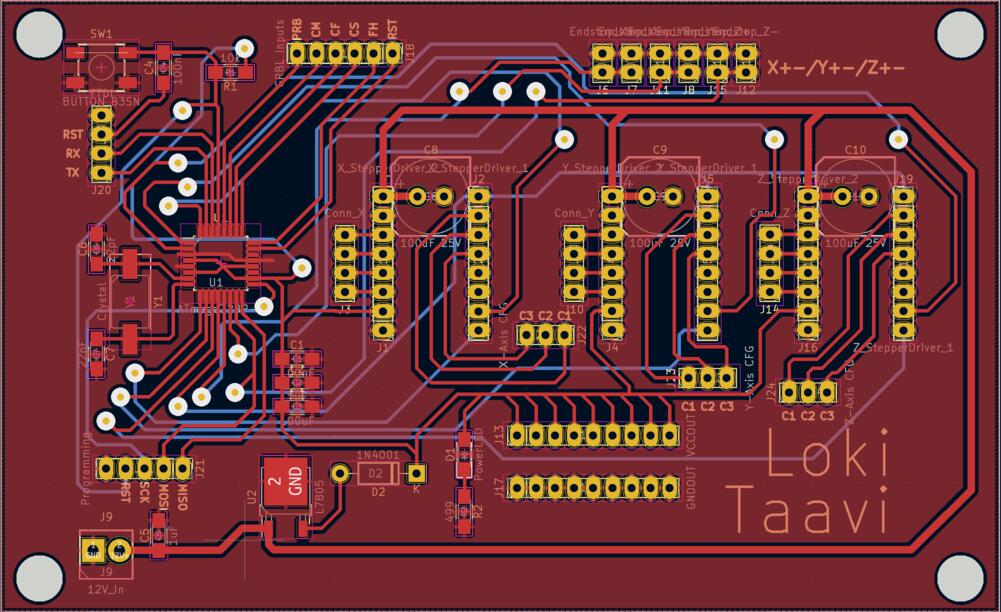
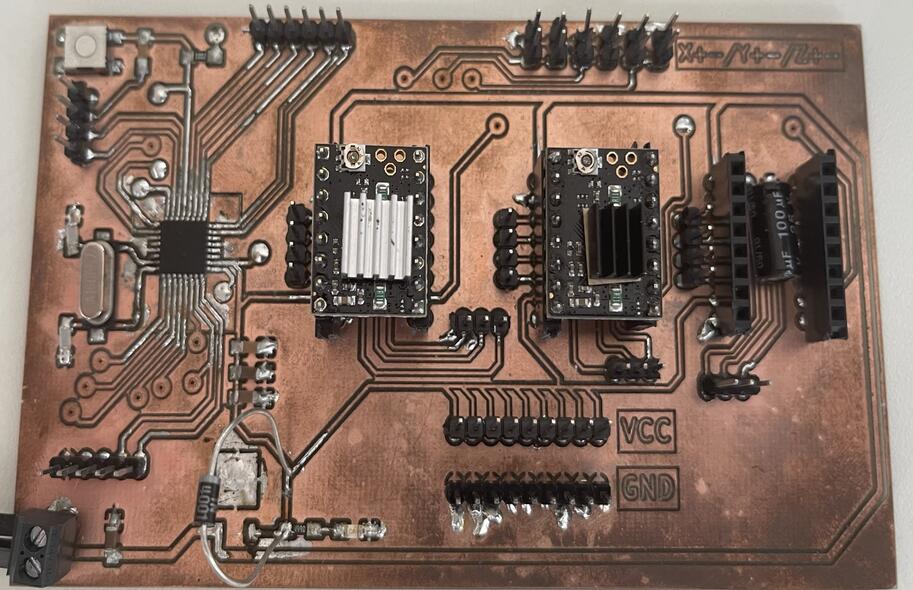
What materials and composites will be used?
Since this project will be further developed as a demonstrator unit, I will be using metallic materials instead of wood. For the most parts I will be using aluminum. Some part will be made from steel. I will also use premade planting pots out of plastic. I will buy them rather than building my own, as we do not have the capabilities of vaccum forming in such a scale. If I were to lower the scale, this would be no problem to vacuum form, as can be seen in my page for Wildcard Week. I shortly contemplated if I wanted to 3D pront the planting pots. 3D printing them works more than fine, as can again be seen in my Wildcard week, but the time needed to print them is just not feasible when comparing it to premade planting pots. The scaled down version of the planting pot, I did in Wildcard Week to almost nine hours, and this was scaled down to 50% its original size! So, all in all, the project will (at some point) be using aluminum, steel, wood (maybe), and plastic.
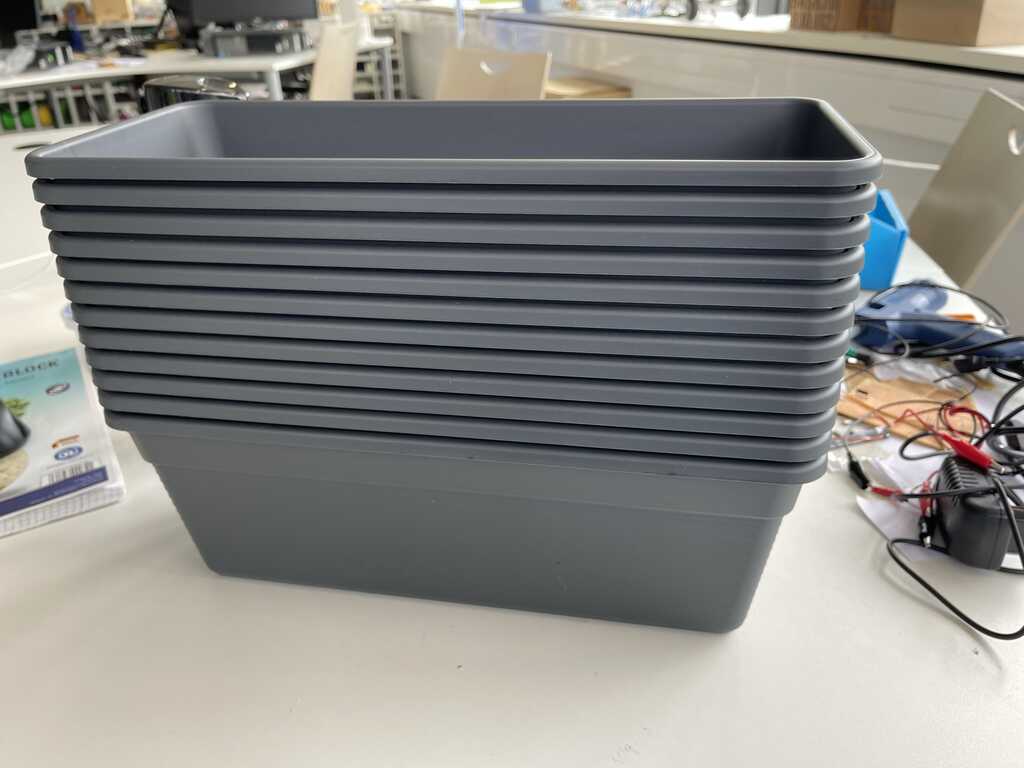
Where will they come from?
Most of the parts will be sourced from local retailers. Stuff like the motors, the aluminum sheets and so on are easily sourcable from local vendors or online shops here in germany. Apart from this, I really really wanted to try out ordering from a Board House. Since my Stepper driver Board has made it through alot of problems and redesigns to be the Board it is now, I wanted to leave this prototype be and ordered the Board from JLCPCB. So at least the stepper driver Board will be sourced form China and not from Germany. The prototype however was fully done here in the Fablab in Germany :).
How much will they cost?
Most of the small parts I will use are rather cheap, like all the electronics components, etc.. What drives the price up by a multitude for my project, is the fact that I am going to use aluminum and steel for my construction. The aluminum sheets alone are quite expensive as one 700mm by 1000mm sheet will cost around $350. AT this point in time, ordering Aluminum in the sizes I would need, is not feasible at all, due to prices and due to delivery times. Because of this circumstance, I will be trying to make everything out of Wood for now and later on, during the later development cycles, I will be redoing parts out of aluminum. However, the other parts that I use for the project are still somewhat pricey. Each soil sensor is costing about 8.50$ and the linear railings and carts for the toolhead cost around 200$ all together. The Ballscrew for the toolhead and the smaller parts for connecting everything, are also round about 200$. All in all you can see that this project will be very pricey, which is understandable, as it is also planned as some sort of demonstartor.
Small Update:
Since last time I checked, the delivery estimate for the aluminum sheets skyrocketed to a poitn where I wont be able to get the aluminum for my final project. As some kind of back up plan, I will now go with wooden exterior for now. The main reason I wanted to use aluminum in the first place, was, for one the look of the demonstartor in the end, and on the other hand, the sturdiness. I am just a little afraid, that the wood will not be able to handle the pressure introduced by the planting pots.
The whole BOM will be available to downlaod on this page once I am done with it. I will note all the prices on there too.
What parts and systems will be made?
Parts:
- The Base
- The planting rings
- The top ring
- The Gear for the Base
- The Gear for the Motor
- The spinning plate (top and bottom)
- The toolhead
- The Stepper driver Board (prototype, end product ordered from JLCPCB)
- The Main control Board
- The data collection Boards
- The Valve for water flow
Systems:
- Data gathering System on data collection Boards (Maybe later on with predictions based on trends)
- Data interpretation system on the main control board
- Algorithm to determine which plants are watered first if more than one needs watering
- GCode creation (Needed because of different movement system than just X/Y/Z)
What processes will be used?
The processes that will be used to achieve this project are:
- Wood/Aluminum milling on the big CNC
- PCB milling on the small CNC
- Laser cutting and engraving
- Soldering
- 3D printing for mounts, etc.
What questions need to be answered?
- Smooth way of delivering power to the rotating platform
- Cable Management for the moisture sensors and the collection PCBs
- Head of the Tool (solenoid valve)
How will it be evaluated?
For me, this project can be called a success, if the machine is able to sense the moisture in the planting pots, receive this data, calculate if and what plant needs watering, and furthermore moving the toolhead to these positions and watering the plant. If all of this works at least rudimentary, I can call this project a success!