Assignment
Design a Mold around the stock and tooling that you'll be using, mill it (rough cut + (at least) three-axis finish cut), and use it to cast parts
Group Assignment:
Review the safety data sheets for each of your molding and casting materials,then make and compare test casts with each of them
In this week we have study about the Safety tools for the moldeing and Casting, in our Lab there are deffernt type of material but we have choose two materails for the Molding we select The MOLDMAX-60, and for the Casting SMOOTH CAST-305
Molding Material MOLD MAX-60 :
Mold Max™ 60 is a Shore 60A tin catalyzed silicone mold rubber formulated for applications requiring high heat resistance (up to 560°F/294°C). It features a low mixed viscosity and cured rubber exhibits very low linear shrinkage. Parts A & B are mixed 100A & 3B by weight. Pot life is 40 minutes and cure time is 24 hours. Applications include making foundry patterns, flat pattern reproductions and casting low-melt metal alloys such as tin and pewter.for more details HERE.
Features:Hazard(s) Identification :
Classification of the substance or mixture:Not a hazardous substance or mixture according to United States Occupational Safety and Administration (OSHA) Hazard Communication Standard (29 CFR 1910.1200), the Canadian Workplace Hazardous Materials Information System (WHMIS) and Regulation (EC) No 1272/2008 and subsequent amendments.
GHS Label elements, including precautionary statements:Description of first aid measures :
Inhalation:Remove source(s) of contamination and move victim to fresh air. If breathing has stopped, give artificial respiration, then oxygen if needed. Contact physician immediately.
Eye Contact: Flush eyes with plenty of water. If irritation persists, seek medical attention.
Skin Contact: In case of skin contact, wash thoroughly with soap and water.
Ingestion : Do not induce vomiting unless instructed by a physician. Never give anything by mouth to an unconscious person.
Most important symptoms and effects, both acute and delayed None known. After first aid, get appropriate in-plant, paramedic, or community medical support.Toxicological Information:
Instructions :
Important: you must weigh Part A & B components using a gram scale to be successful with Mold Max™ 60, for more details HERE.Because no two applications are quite the same, a small test application to determine suitability for your project is recommended if performance of this material is in question.
Preparation :Materials should be stored and used in at room temperature (73°F/23°C). These products have a limited shelf life and should be used as soon as possible. Wear safety glasses, long sleeves and rubber gloves to minimize contamination risk. Rubber may be inhibited by sulfur base clays resulting in tackiness at the pattern interface or a total lack of cure throughout the mold. If compatibility between the rubber and the surface is a concern, a small-scale test is recommended. Apply a small amount of rubber onto a non-critical area of the pattern. Inhibition has occurred if the rubber is gummy or uncured after the recommended cure time has passed.
Applying A Sealer / Release Agent :To prevent inhibition, a “barrier coat” of clear acrylic lacquer sprayed directly onto the pattern is usually effective. Allow to thoroughly dry. Although not usually necessary, a release agent will make demolding easier when casting into or over most surfaces. Ease Release™ 200 is a proven release agent for making molds with silicone rubber and for releasing new silicone from cured silicone. Mann Ease Release™ products are available from Smooth-On or your Smooth-On distributor. IMPORTANT: To ensure thorough coverage, lightly brush the release agent with a soft brush over all surfaces of the model. Follow with light mist coating and let dry for 30 minutes.
Measuring & Mixing:Before you begin, pre-mix Part A (base) thoroughly to re-disperse fillers that may have settled. Using a gram scale, dispense required amounts of parts A and B into a mixing container and mix for 3 minutes. Scrape the sides and bottom of the container several times. After mixing parts A and B, vacuum degassing is recommended to eliminate any entrapped air. Vacuum material for 2-3 minutes (29 inches of mercury), making sure that you leave enough room in container for product expansion.
Pouring / Curing / Post Curing :For best results, pour your mixture in a single spot at the lowest point of the containment field. Let the rubber seek its level up and over the model. A uniform flow will help minimize entrapped air. The liquid rubber should level off at least 1/2” (1.3 cm) over the highest point of the model surface. Allow the mold to cure overnight (at least 24 hours) at room temperature (73°F/23°C) before demolding. Post curing the mold an additional 4 - 5 hours at 125°F (51°C) will eliminate any residual moisture and alcohol that is a by-product of the condensation reaction. This water and alcohol can inhibit the cure of some casting resins. Allow mold to cool to room temperature before using. Do not cure rubber where temperature is less than 65°F /18°C.
Decreasing demold time with Accel-T™ Silicone Cure Accelerator:Important: Thoroughly Pre-mix Accel T™ with Part B before adding Part A.Be aware that the working time is drastically reduced with the addition of Accel T™. Also, library life of cured rubber is reduced in proportion to the amount of Accel-T™ added.
Using The Mold :New silicone rubber molds exhibit natural release characteristics. Depending on what is being cast into the mold, mold lubricity may be depleted over time and parts will begin to stick. No release agent is necessary when casting wax or gypsum. Applying a release agent such as Ease Release™ 200 (available from Smooth-On) prior to casting polyurethane, polyester and epoxy resins is recommended to maximize mold life. Visit Smooth-On’s FAQ section at www.smooth-on.com for information on a powder coating technique that will yield a dry matte finish to cured castings.
Mold Performance & Storage :The physical life of the mold depends on how you use it (materials cast, frequency, etc.). Casting abrasive materials such as concrete can quickly erode mold detail, while casting non-abrasive materials (wax) will not affect mold detail. Before storing, the mold should be cleaned with a soap solution and wiped fully dry. Two part (or more) molds should be assembled. Molds should be stored on a level surface in a cool, dry environment.
Casting Material SMOOTH CAST-305 :
Introduction
The Smooth-Cast® 300 Series of liquid plastics are ultra-low viscosity casting resins that yield castings that are bright white and virtually bubble free. Vacuum degassing is not necessary. They offer the convenience of a 1A:1B by volume or 100A:90B by weight mix ratio. The differences between them are pot life and demold time.
These resins readily accept fillers (such as URE-FIL® 3 from Smooth-On) and can be colored with SO-Strong® or Ignite® color tints (Smooth-Cast® 325 series accepts pigments better than the Smooth Cast® 300 series). Fully cured castings are tough, durable, machinable and paintable. They resist moisture and mild solvents. Applications for Smooth-Cast® 300 Series Liquid Plastics include reproducing small to medium size sculptures, making prototype models, special effect props and decorative jewelry, for more deatils HERE.
Instructions :
Safety : Materials should be stored and used in a warm environment (73° F / 23° C). These products have a limited shelf life and should be used as soon as possible. All liquid urethanes are moisture sensitive and will absorb atmospheric moisture. Mixing tools and containers should be clean and made of metal, glass or plastic. Mixing should be done in a well-ventilated area. Wear safety glasses, long sleeves and rubber gloves to minimize contamination risk.
Applying A Release Agent : A release agent is necessary to facilitate demolding when casting into or over most surfaces. Use a release agent made specifically for mold making (Universal® Mold Release or Mann’s Ease Release® 200 available from Smooth-On or your Smooth-On distributor). A liberal coat of release agent should be applied onto all surfaces that will contact the plastic.
IMPORTANT: To ensure thorough coverage, apply release and brush with a soft brush over all surfaces. Follow with a light mist coating and let the release agent dry for 30 minutes. Smooth-On silicone rubber molds usually do not require a release agent unless casting silicone into the mold. Applying a release agent will prolong the life of the mold.
IMPORTANT: Shelf life of product is reduced after opening. Remaining product should be used as soon as possible. Immediately replacing the lids on both containers after dispensing product will help prolong the shelf life of the unused product. XTEND-IT® Dry Gas Blanket (available from Smooth-On) will significantly prolong the shelf life of unused liquid urethane products.
Measuring and Mixing : Liquid urethanes are moisture sensitive and will absorb atmospheric moisture. Mixing tools and containers should be clean and made of metal, glass or plastic. Materials should be stored and used in a warm environment (73°F/23°C).
Stir or shake both Part A & Part B thoroughly before dispensing: After dispensing equal amounts of Parts A and B into mixing container (100A:90B by weight) and mix thoroughly. Stir deliberately making sure that you scrape the sides and bottom of the mixing container several times. Be careful not to splash low viscosity material out of the container.
Pouring : Pour your mixture in a single spot at the lowest point of the containment field and let the mixture seek its level. This will help minimize air entrapment.
For Best Results : Best results are obtained using a pressure casting technique. After pouring the mixed compound, the entire casting assembly (mold, dam structure, etc.) is placed in a pressure chamber and subjected to 60 PSI (4.2 kg/cm2) air pressure for the full cure time of the material.
Curing Important: Use this product with at least room size ventilation or in proximity to a forced outlet air vent and do not inhale/breath fumes. Fumes, which may be visible with a significant mass concentration, will quickly dissipate with adequate ventilation. Castings with significant mass may be hot to the touch and irritate skin immediately following cure. Let casting cool to room temperature before handling.
Demold time of the finished casting depends on mass and mold configuration. Low mass or thin-walled castings will take longer to cure than castings with higher mass concentration. Smooth-Cast® 305 will cure in 30 - 40 minutes (Smooth-Cast® 300 in 7 -10 minutes and Smooth-Cast® 310 in 2 - 4 hours) depending on mass and mold configuration.
Post Cure : Castings will reach “full cure” faster and achieve maximum physical properties if post cured. Allow material to cure for recommended Cure Time at room temperature followed by 4 - 6 hours at 150°F/65°C. Allow casting to come to room temperature before handling.
Performance : Cured castings are rigid and durable. They resist moisture, moderate heat, solvents, dilute acids and can be machined, primed/ painted or bonded to other surfaces (any release agent must be removed). If machining cured material, wear dust mask or other apparatus to prevent inhalation of residual particles. Castings can be displayed outdoors after priming and painting. Unpainted castings will yellow over time - more quickly when exposed to ultra-violet light,for more details HERE.
Assignments :
Mold Design :
In this assignment I have Decide that First I have to design the Mold of lotus flower ,I have Downlaod the this Image from This Site HERE. and Open in solid work Software.image import in solid work to generate the vector line.
First Import the Image of Lotus Flower
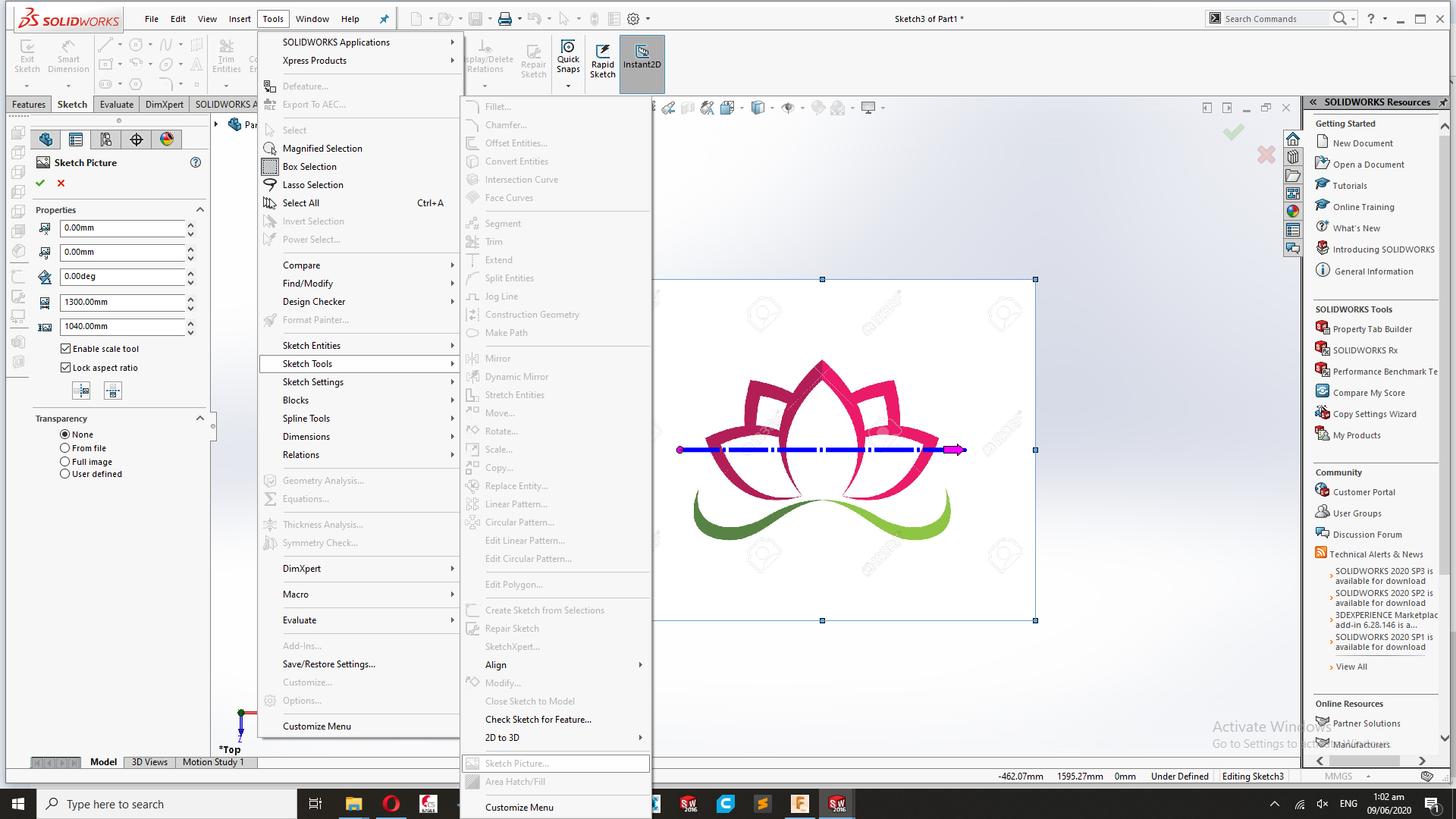
This the Image which is Import in Solid Work.
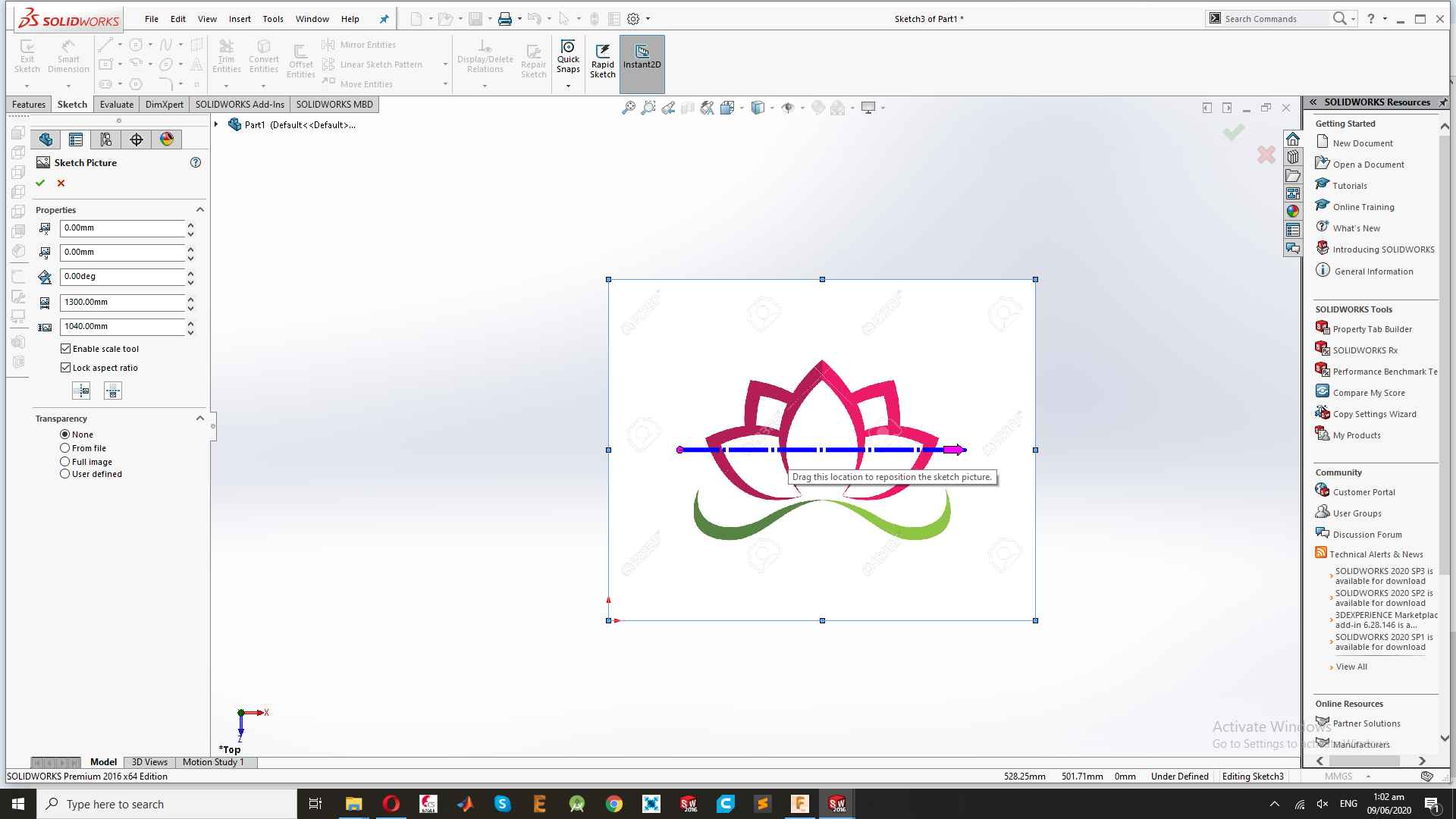
Now use the Spline and put the Boundary arcoss the image.
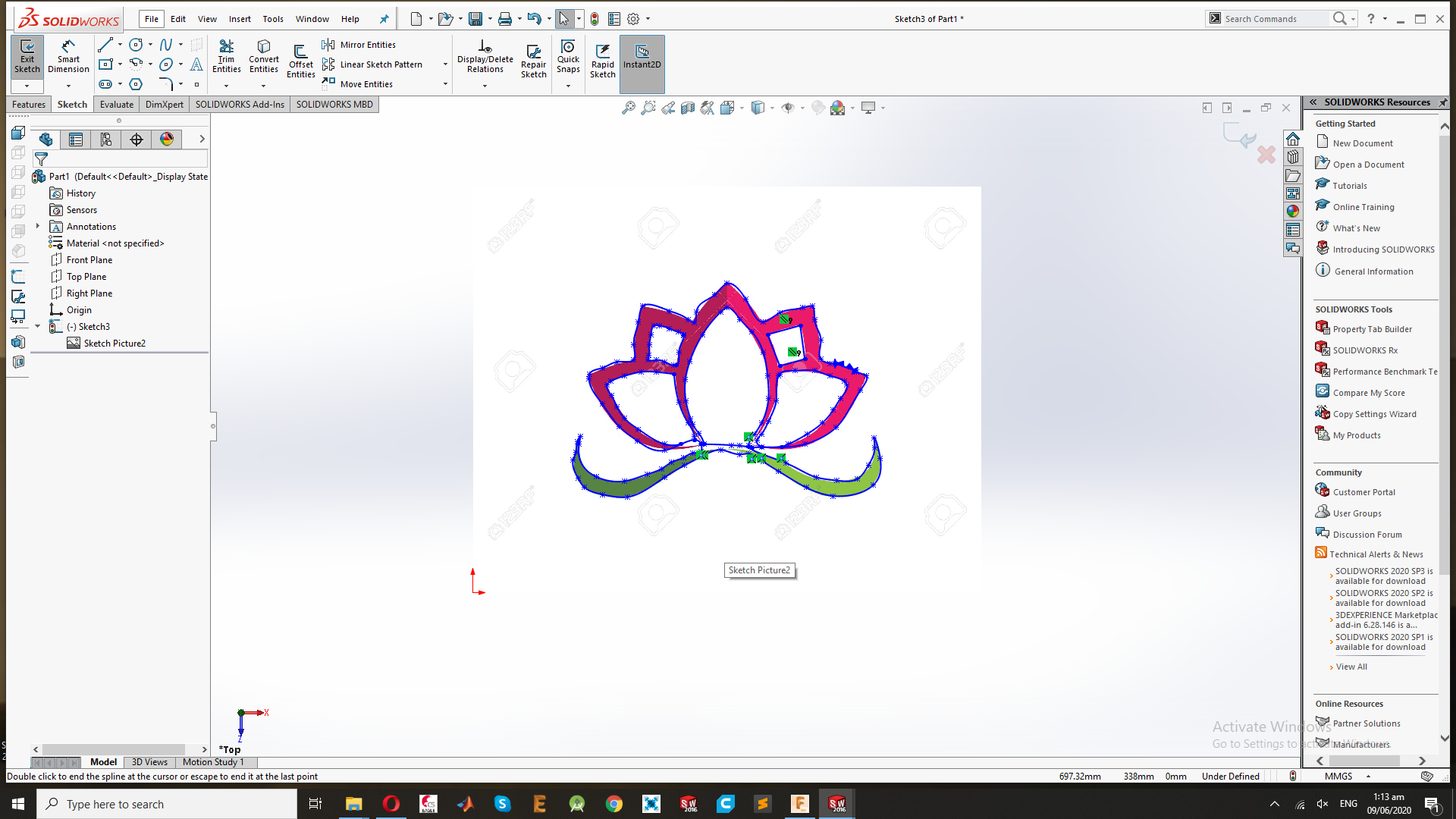
Now remove the background image the Lotus flower for the sketch.
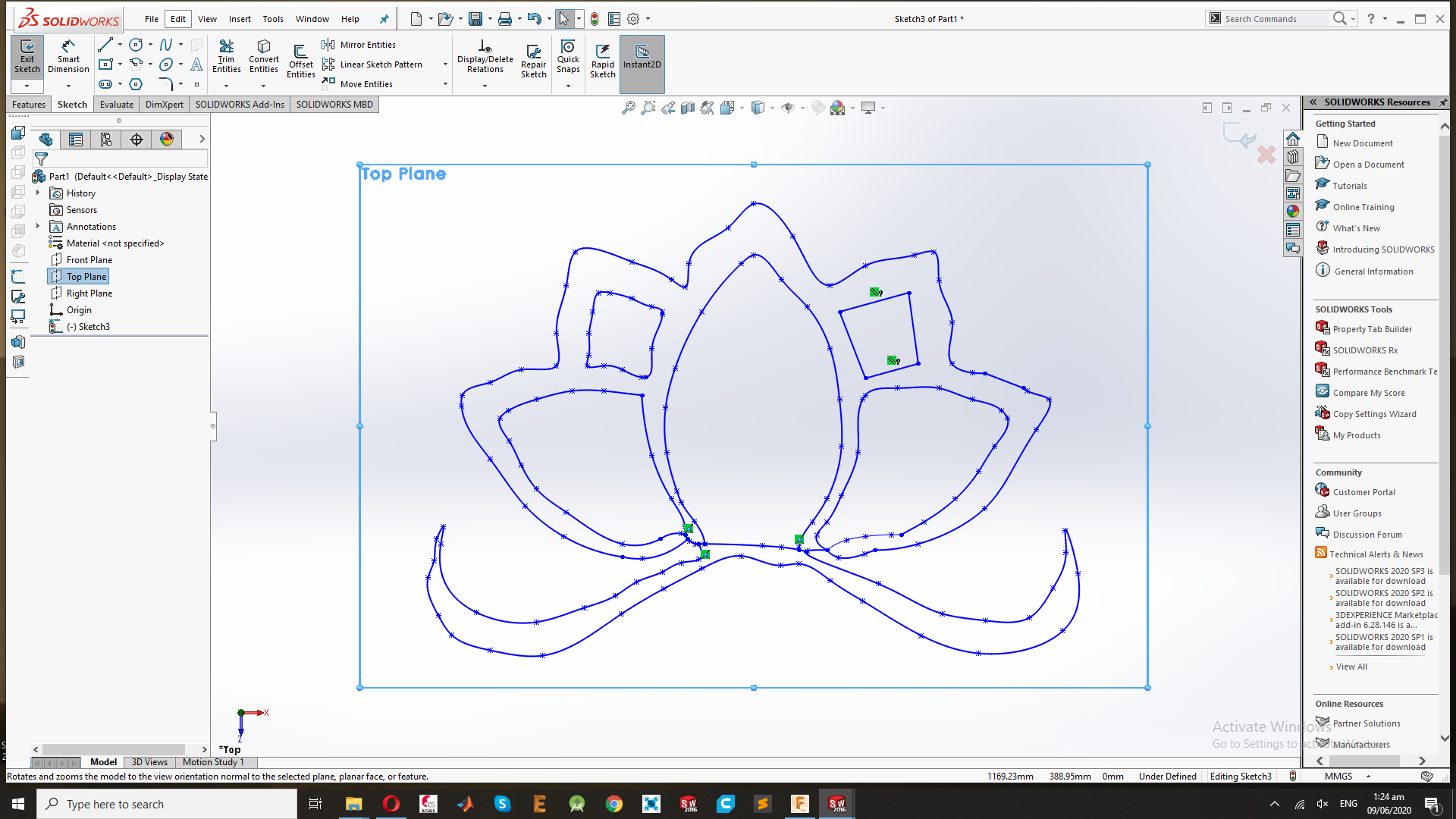
Now Extrude the sketch at 10mm.
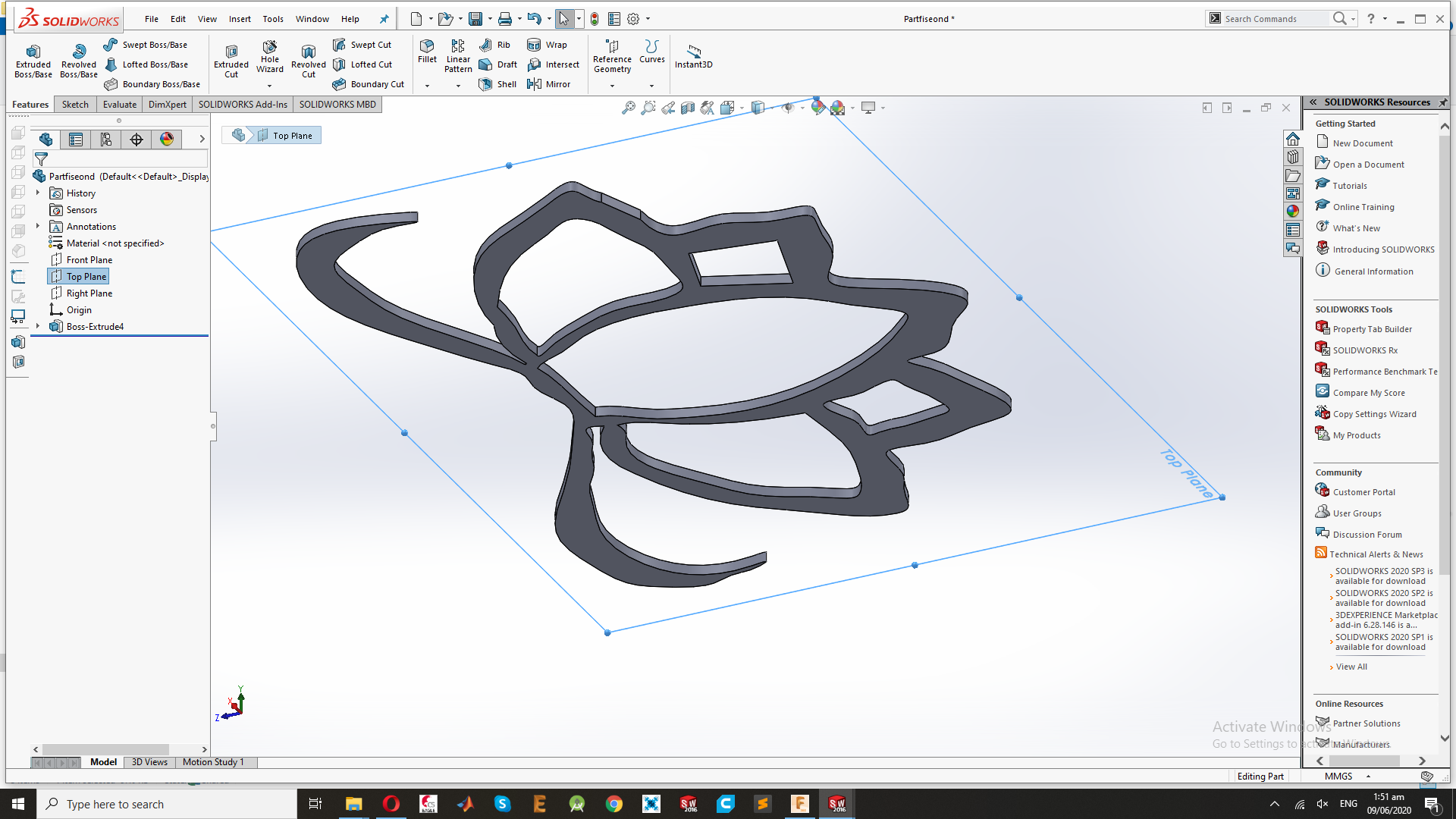
Now set the outer boundery of the mold.
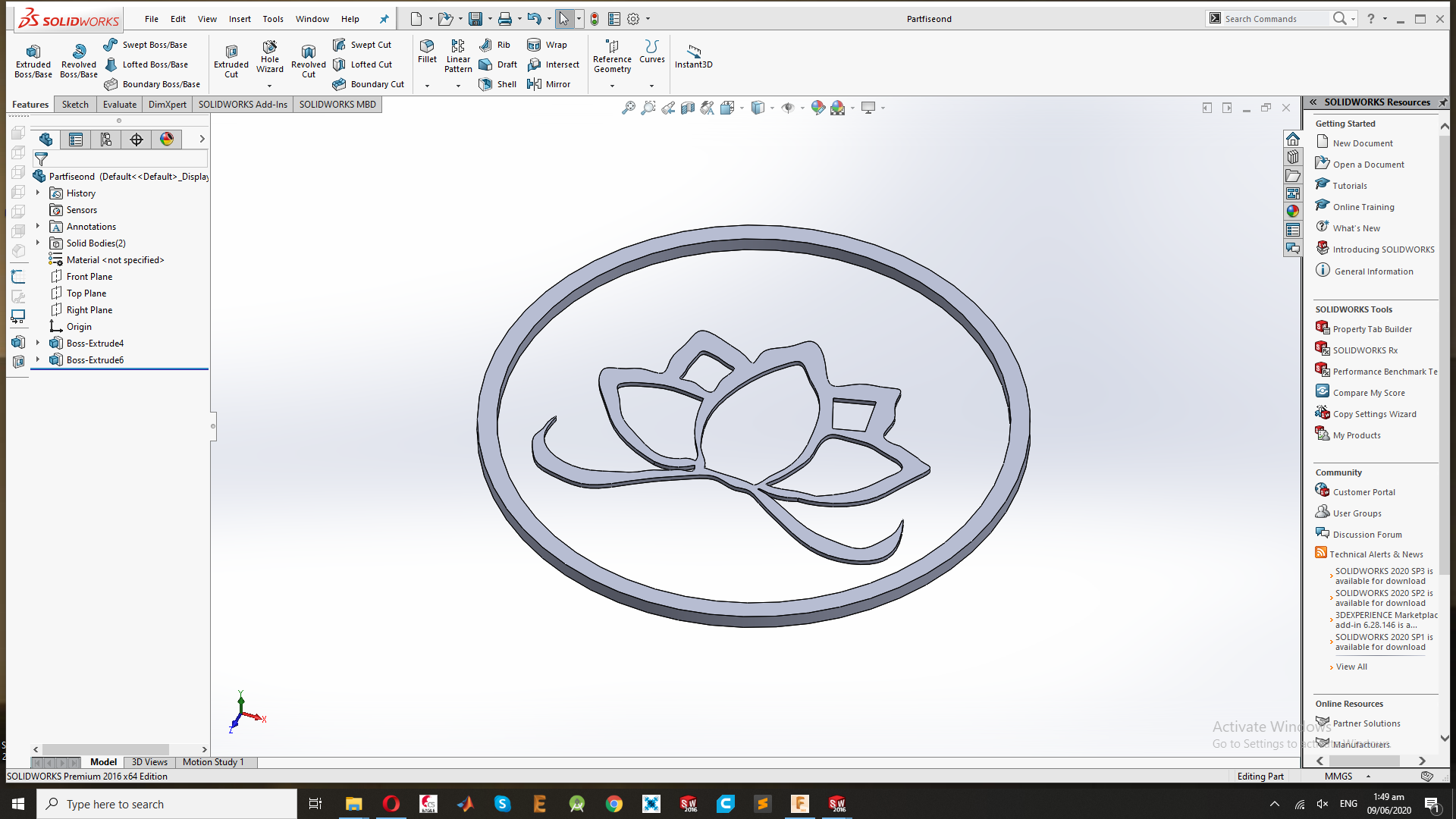
Now phase to generate the .stl for the Modela player 4 to generate the Mold, before going to generate the Roughing and finishing file for the SRM-20.I have open the .stl file in Cura software, I found that this design has some issue of dismission and not valid for the mold, in cura I have set the all dimension and other requirments and save them.
After the all setting of the File and now phase to open the generate the RMl file using the Modela player 4.
Open the Modela Player 4.
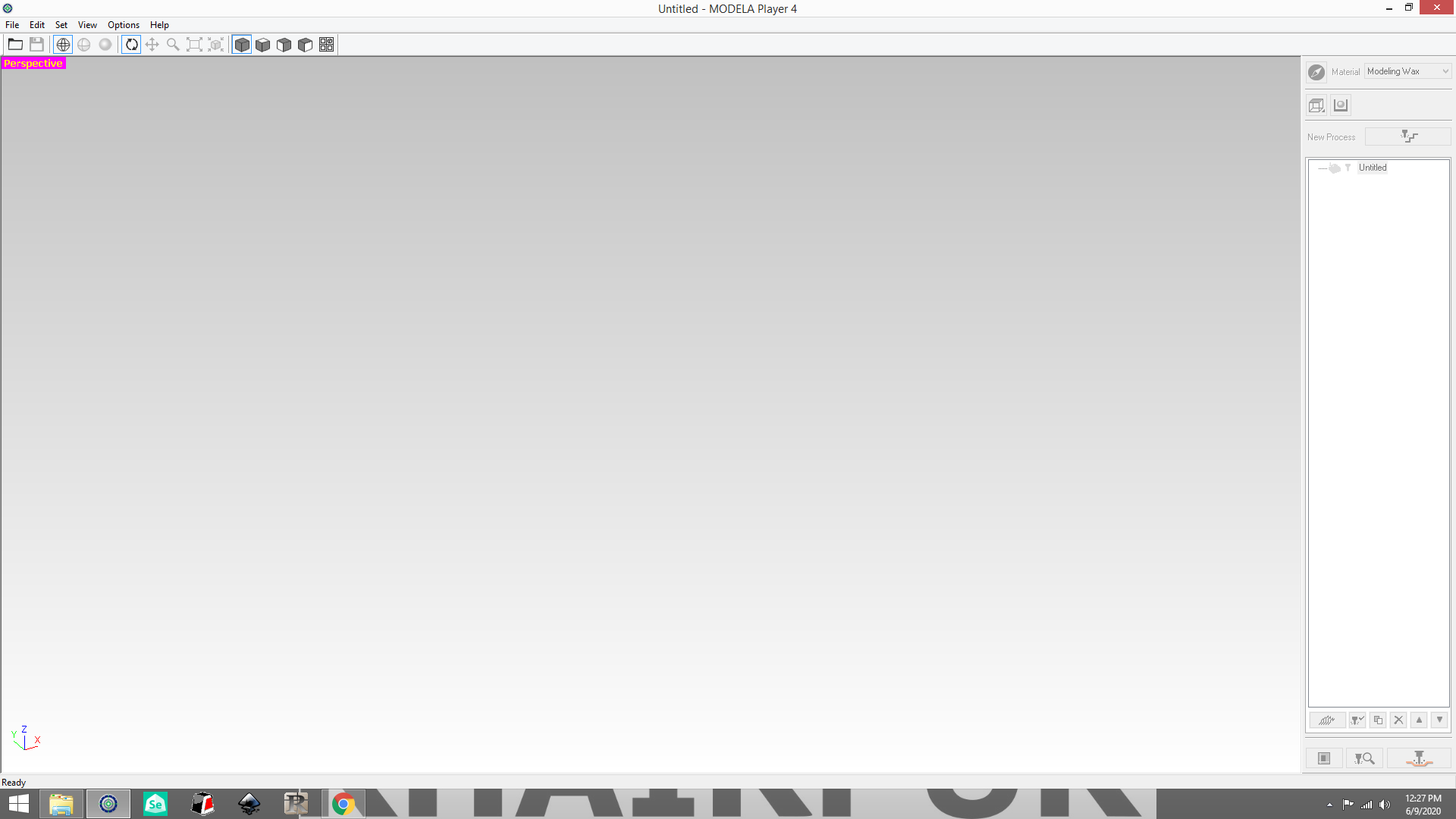
Go to file and select Select Machine.
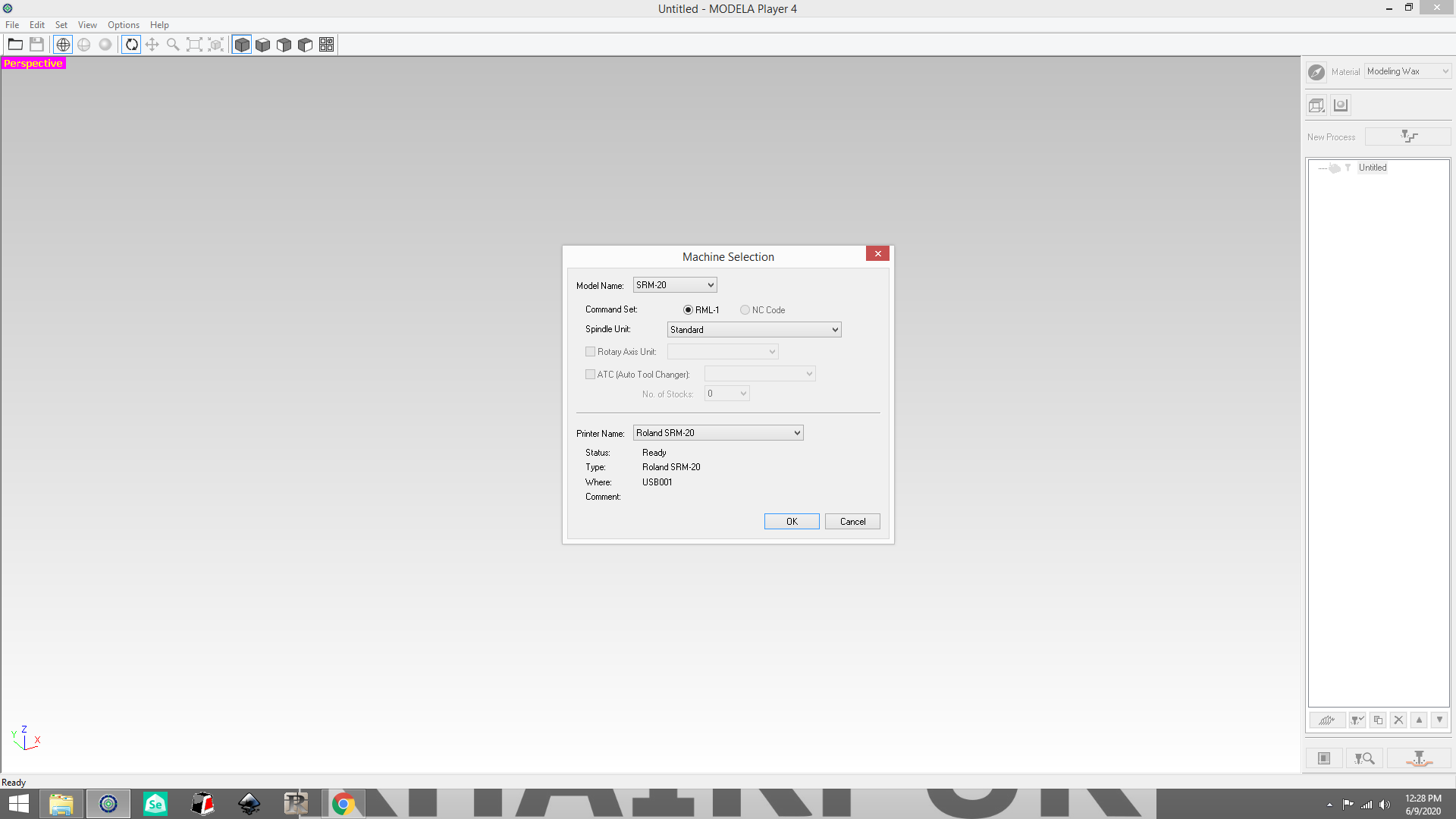
Go to Set and Model.
Check on Origin .
Go to Set and Modeling Form then check on Manual.
Go to Set and New Process then check on Roughing, then Next.
Check on Top [+Z] then Next.
Select 3 mm Square then Next.
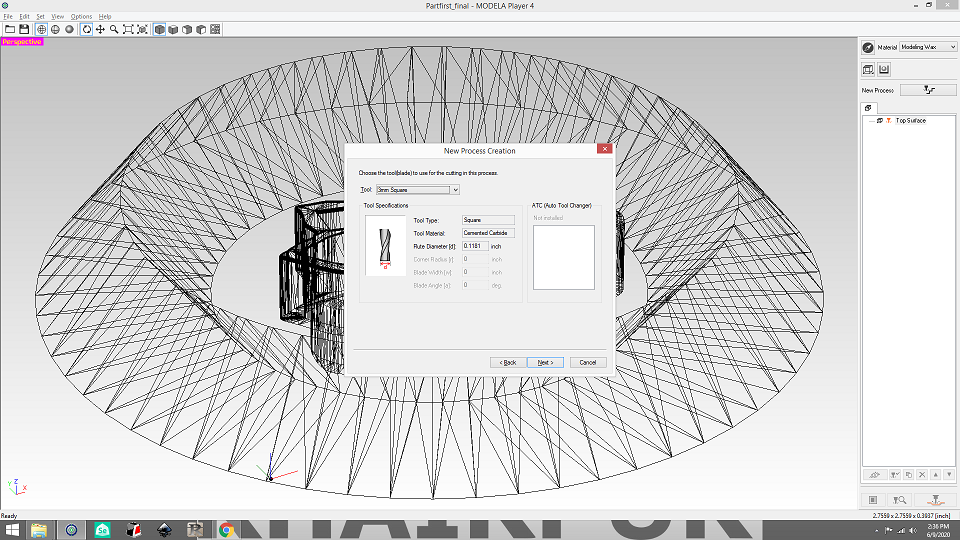
Check on Partial then resize the red boundary line inside the box then Next.
Check on Contour Lines Up Cutthen Next.
XY speed as 24mm/sec, then Next
after that save the .prn file and then click to Finish.
Now Process of the Finshing
Go to Set and New Process then check on finshing, then Next.
Check on Top [+Z] then 'Next'
Select 1 mm Square then Next.
Check on Partial then resize the red boundary line inside the box then Next.
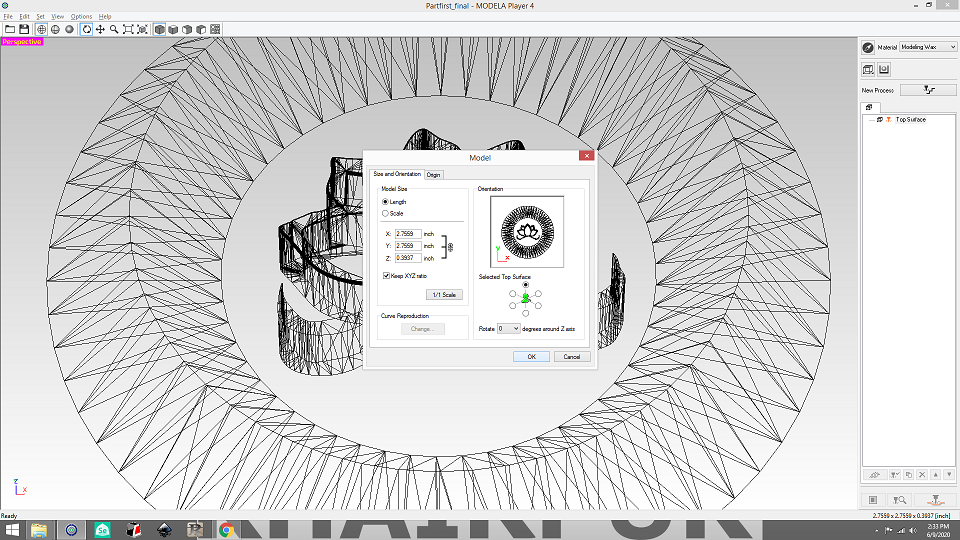
Check on Contour Lines Up Cutthen Next.
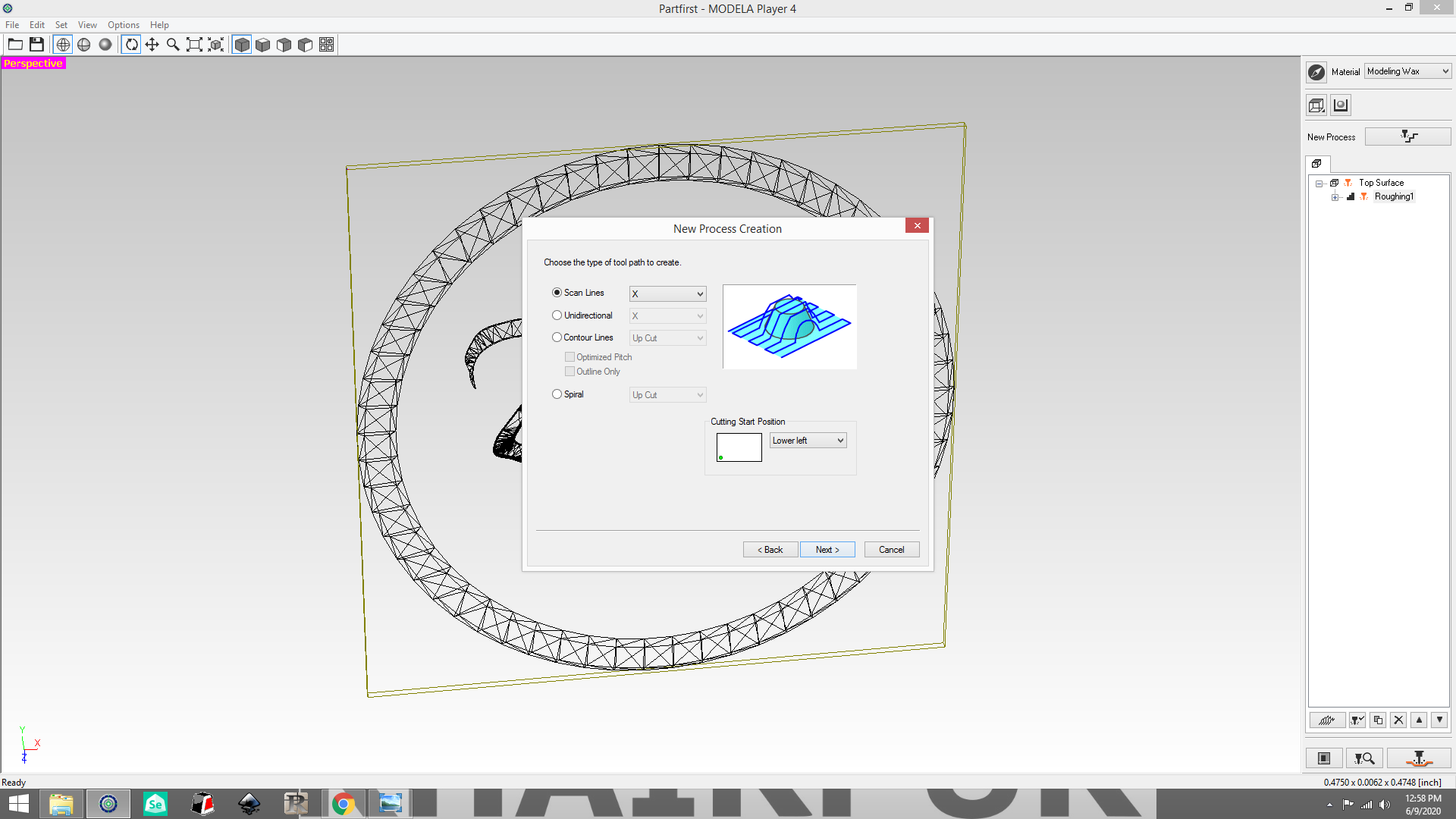
XY speed as 16mm/sec, then Next
So now save the file and then Finish.now click on Cut ,to save the .prn files.
the Final look of the mold design file .
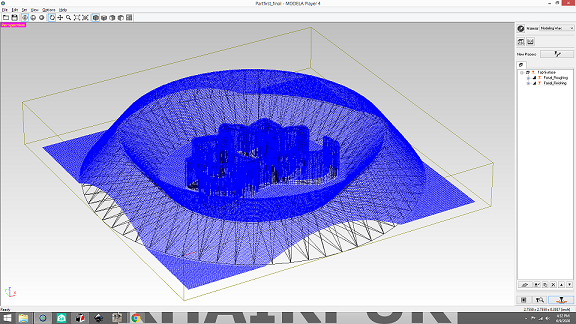
Milling Process:
First I have change the wax,now open the Vpanel for SRM-20 the set the Origion of the Machine x,y,z on zeros,for the roughing 1/8 tool bit we will use.
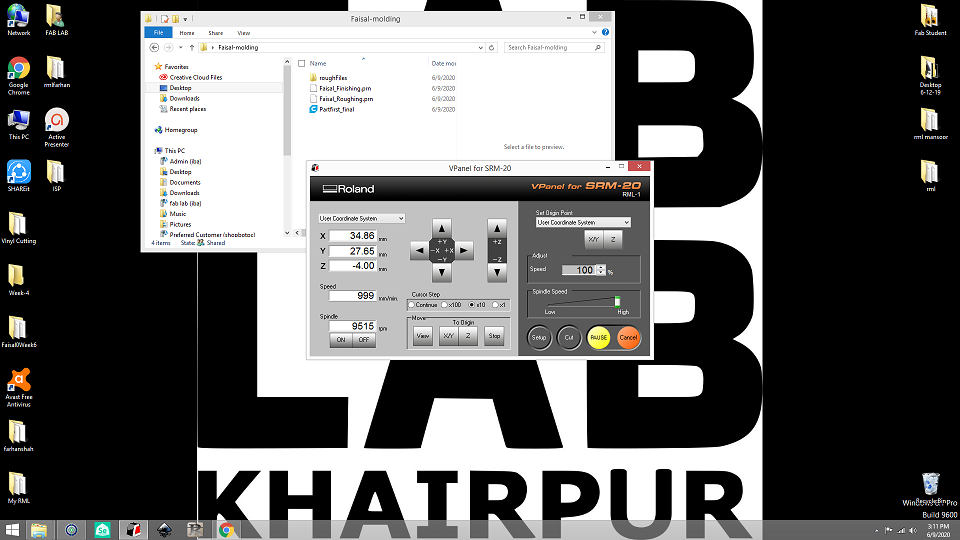
after the roughing my mold look like that.
Now I will change the tool bit 1/32 for the finishing the job and after the finishing my design look like this
Molding and Casting
After the SRM-20 job , now we have to use material for the mold and casting , first we use the material for the mold the cast.so first I have filled the water in my design to measure the the mixture level for the mold.
After the water measurement , I have found the that water is present about 2.5g.
Now time is to ready the mixture of material , so I decided to make the mold using Mold Max 60. The mold made of this material can also be used for metal casting.while adding the material A.
for the mixture , I took 100% part A material and 3% part B material and mixed them for 6 to 7 minutes and poured the material into the mold and filled the mold. and adding the material B.
Adding part A and part B of the material and then mixing them up.untill it become complete mix,and pure on mold, it take 30 to 40 mint.
After the fill up of material mold, is look like this, in design I have just filled the inner side of the mold,that is too much clear and valid for the mold, in my CAD , I have done 1 mistake that outer boundary, which is not useable for the mold, so that why i did not fill up mold material.
after that mold is look like this :
Casting material :
for the casting mold is ready to make the cast of my design, for that I am using "Smooth-On Smooth-Cast 305".Using the instructions written on the page available inside I made a mix of 1A:1B, which means both parts of material should be in equal proportion. 50% part A and 50% part B of the weight measured by pouring water inside the mold. After mixing it 3to 5 minutes I filled the mold with it.
Now mixture is ready for the casting , and I am puring the mixture on mold.After the fill up of casting material , it take 15 to 30 mint to complete the process.
Now time is to cast the metal in my design.As metal is given in a solid form so we first melt it using the furnace at 300 degree-centigrade and then fill our mold with it to make the cast. Note: We simply switch on the furnace and wait a few minutes untill temperature rises to 300+ degree-centigrade. Once the metal is melted into liquid form simply take the glass and fill the mold as following.
Now metal is melt and ready for the cast, so I have cast in my mold design.
it take few mints to cool and complete the mold.
After the few mints now mold is ready , so its look like this.
Conculsion
This week wad mold and casting in this week i have deign the mold of the lotus flower , image is import in solid work and design it in CAD after that, I have used the modela player 4 for the rml code , when all job is finish then have use the mold material for mold , when mold is ready then i have cast it metal and rubber.this week was very learning week.
Download All file of this week Here.

This work is licensed under a Creative Commons Attribution-NonCommercial-ShareAlike 4.0 International License
.