3D scanning and printing
group assignment
test the design rules for your 3D printer(s)
from here you can see what we did on the group assignmentindividual assignment
This assignment has diferent parts
- About the tweezers
- About the modeling software
- About the slicer
- About scanner
- About the hinge
- Links and references
About the tweezers
A little more back ground
this makes the process expensive and hard to purchase
What i choose?
for the individual asssignment i choose an easy replaceble tweezer using polylactic acid PLA as it is the most common and cheap printable material.
why i choose it?
sustractive vs. aditive
so sumarized the commercial tweezer may not be able to exist without any of this two processes.
As a lab tech on fablabqqro i'm against printing knicknacks that ends up in the garbage bin.
About the modeling software
So i modeled a pair of tweezers for smd components using solidworks
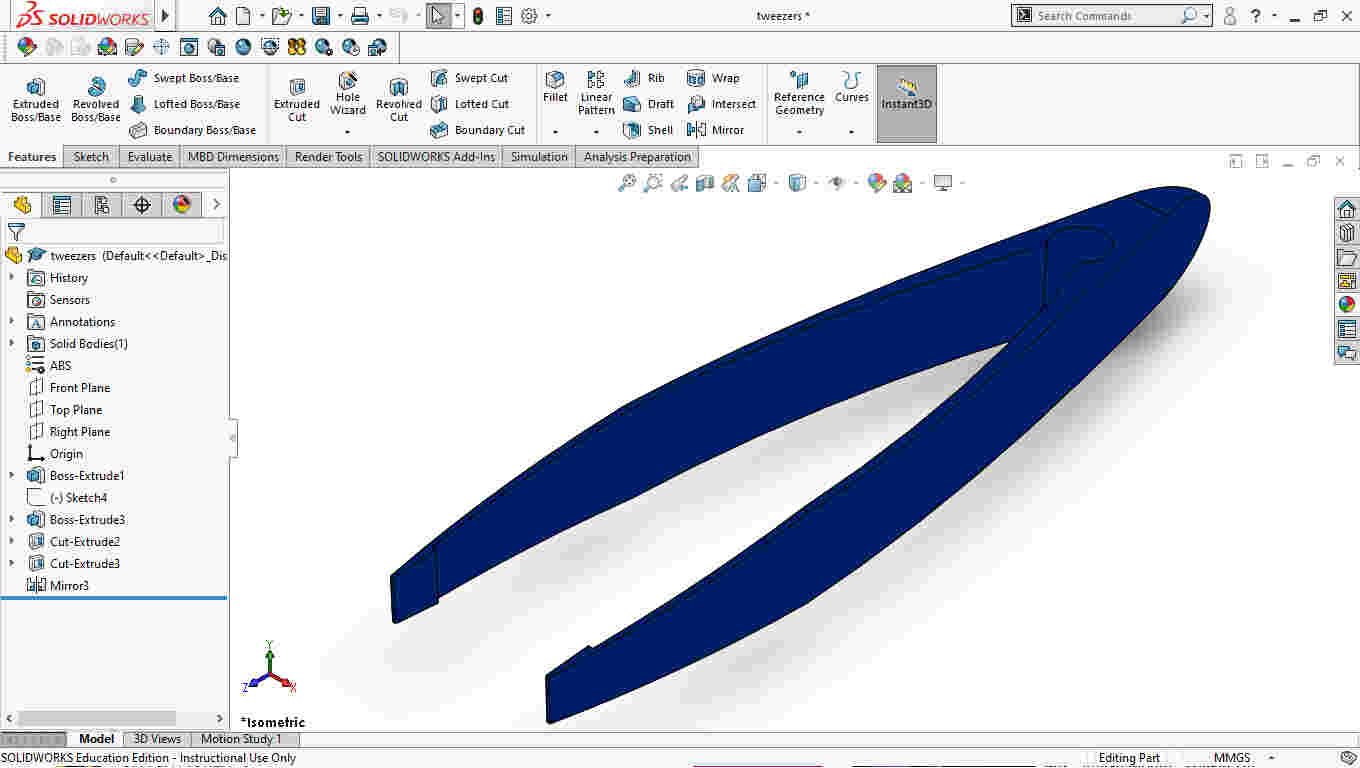
picture directly taken from solidworks
i used some basic geometrical constraints and dimensions considering the diameter of the extrusor wich is about 0.4 mm using expresions on solidworks
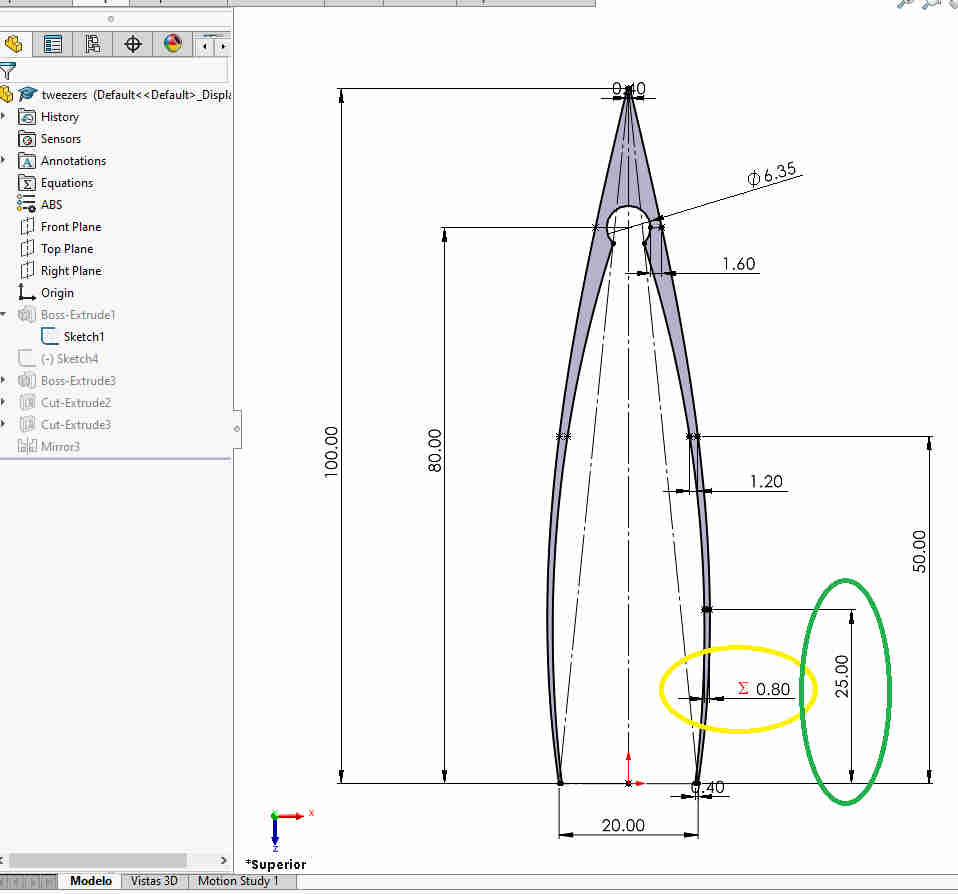
this is a pic from the first sketch
i just wanted to control the diammeter of the nozzle wich i'm using to print it.
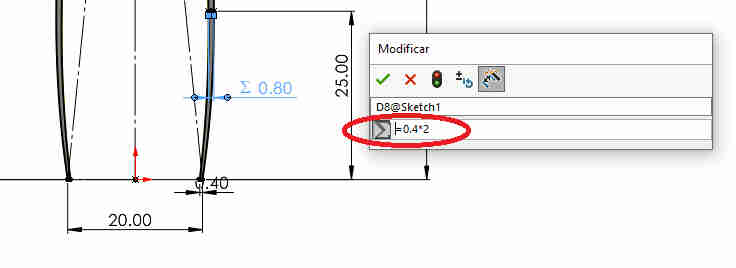
this is a pic on how i parametrized the value i wanted
then i wanted that the hole of the tweezer were at 80% of the overall length
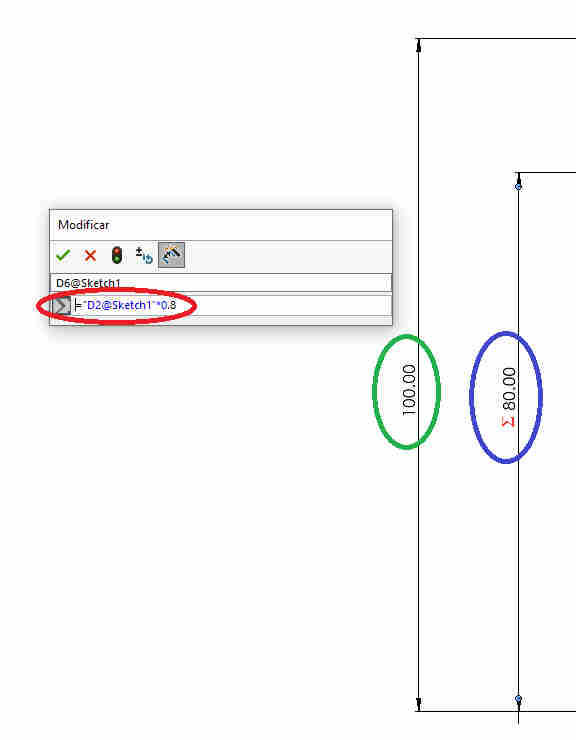
this is how you make a dimension referenced from another dimension
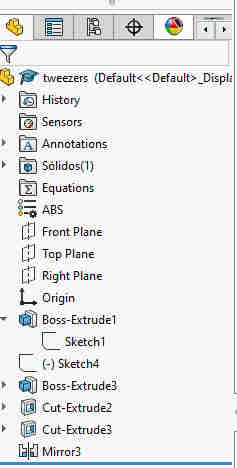
the entire operations tree in solidworks is really simple as you can see.
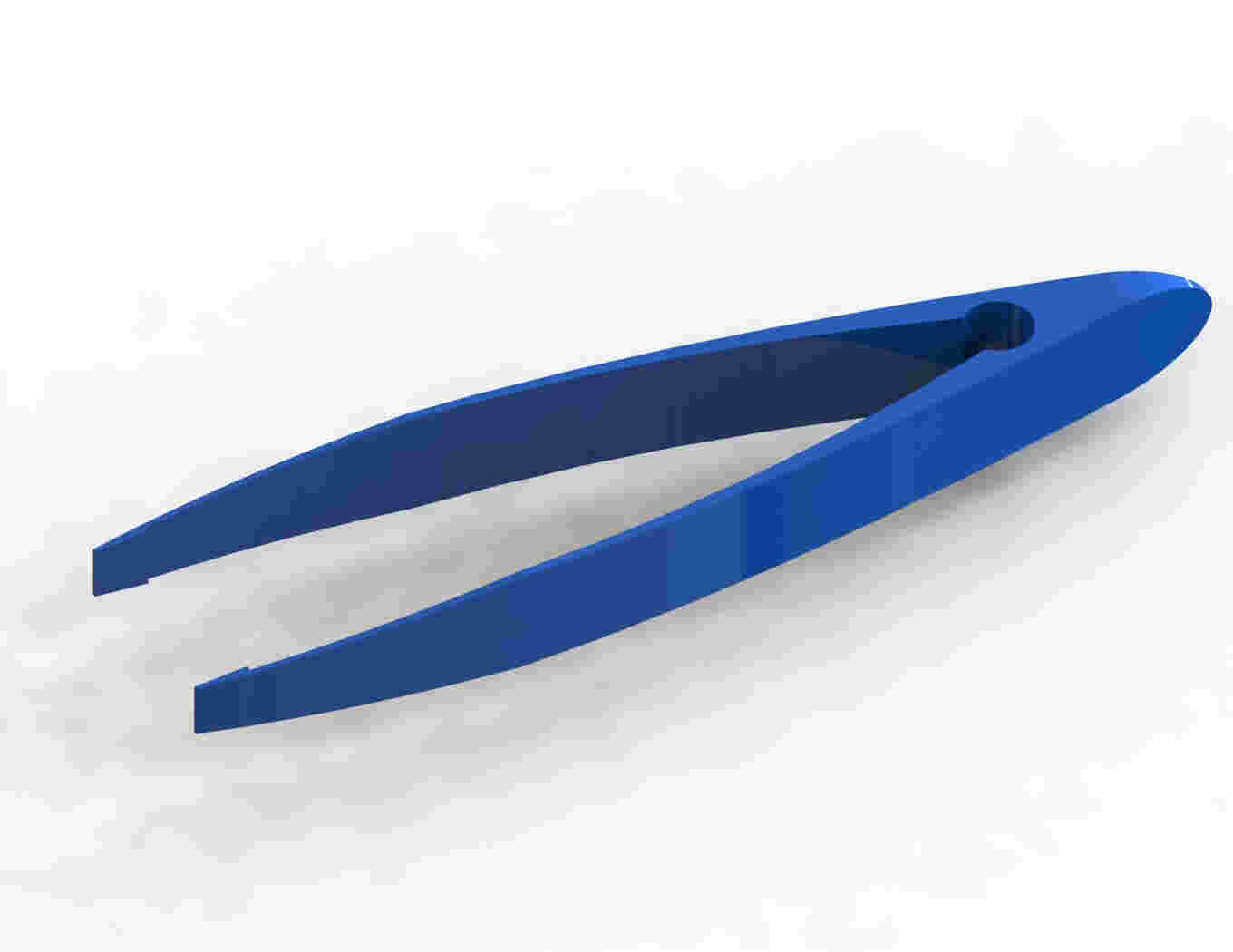
about the slicer
then i imported into ultimaker's slicer software named cura
HERE you can download the most recent version of ultimaker's cura
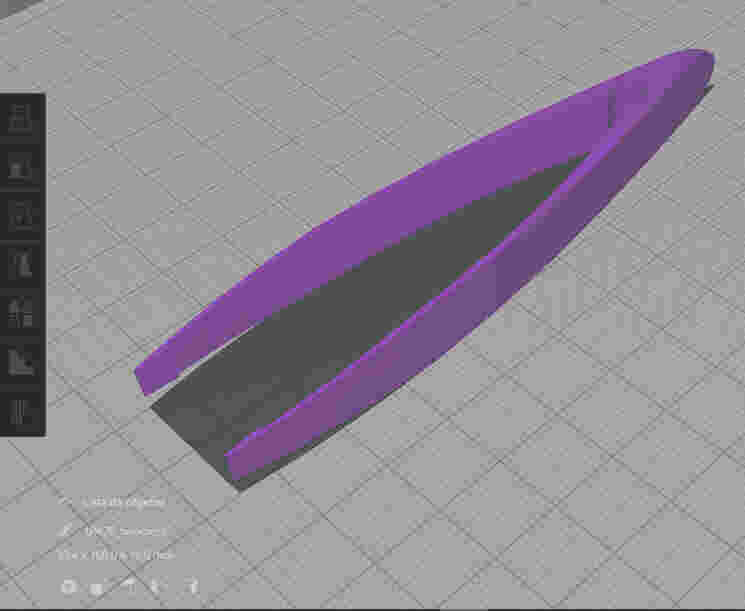
where i twitched a little the default presettings to rush it a little, i set the layer height to 0.2 mm the speed to 60 mm/s and 10% infill.In the future i'd like to experiment with the formalbs flexible resin to make a 3 fingered gripper using the same principle of compliant mecanisms
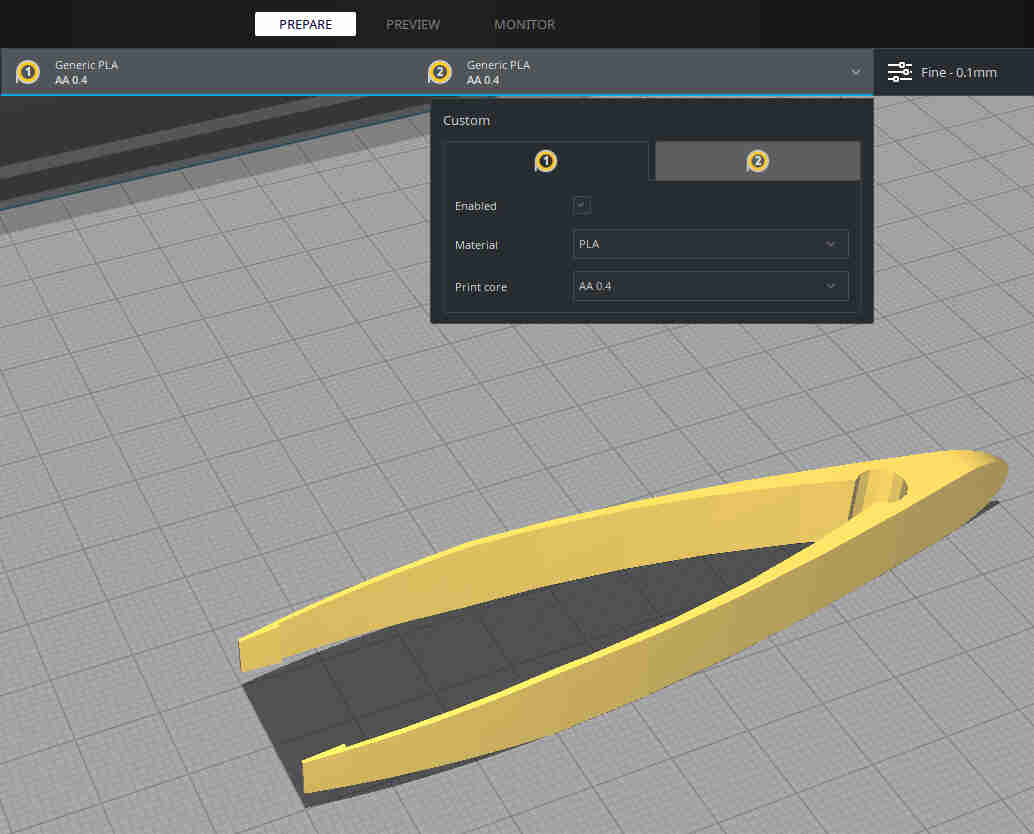
this is a screenshot if all of diameter of the nozzle i used to print this
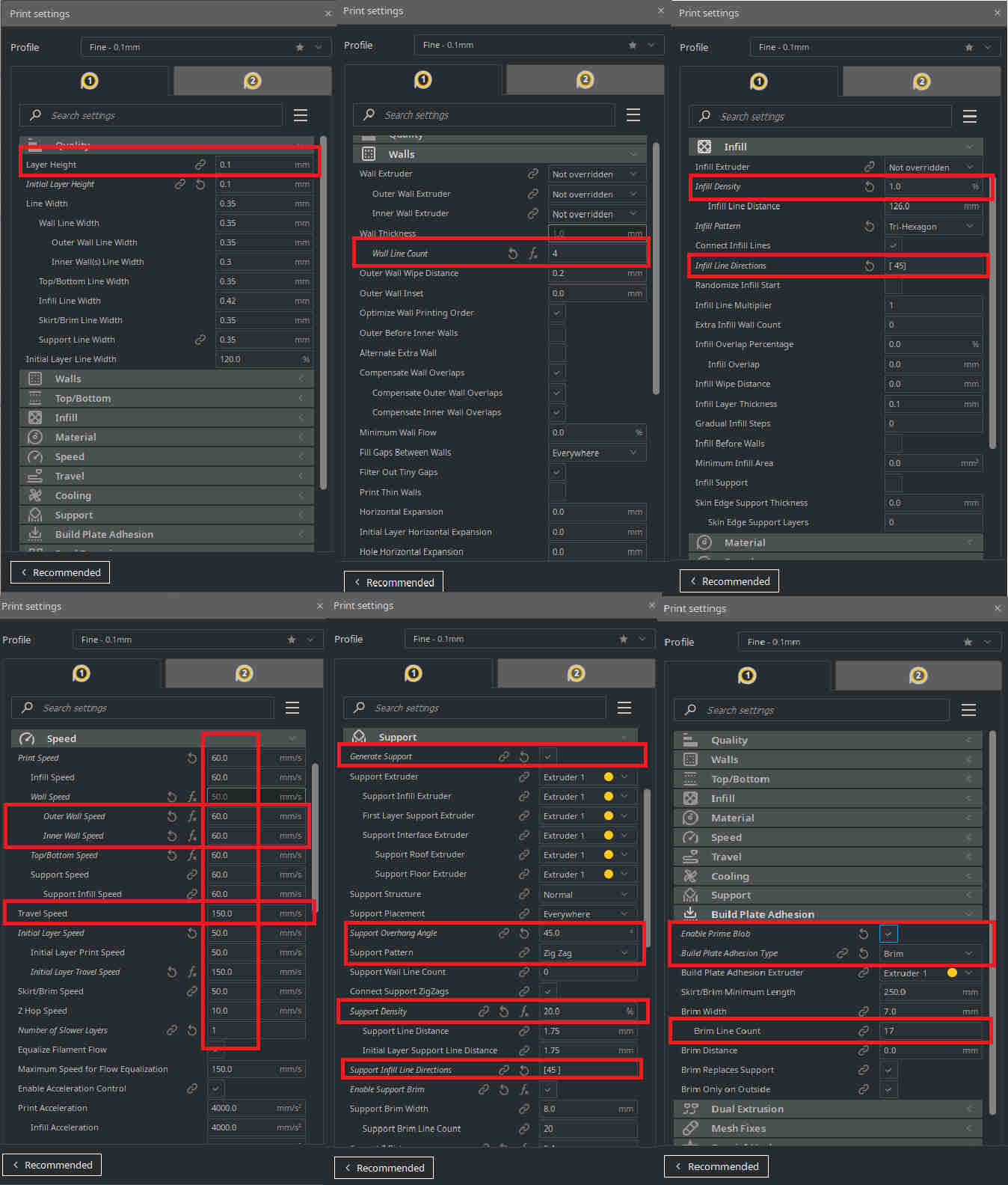
this is a screen shot of the parameters i used on the ultimaker 5s we have in the lab.
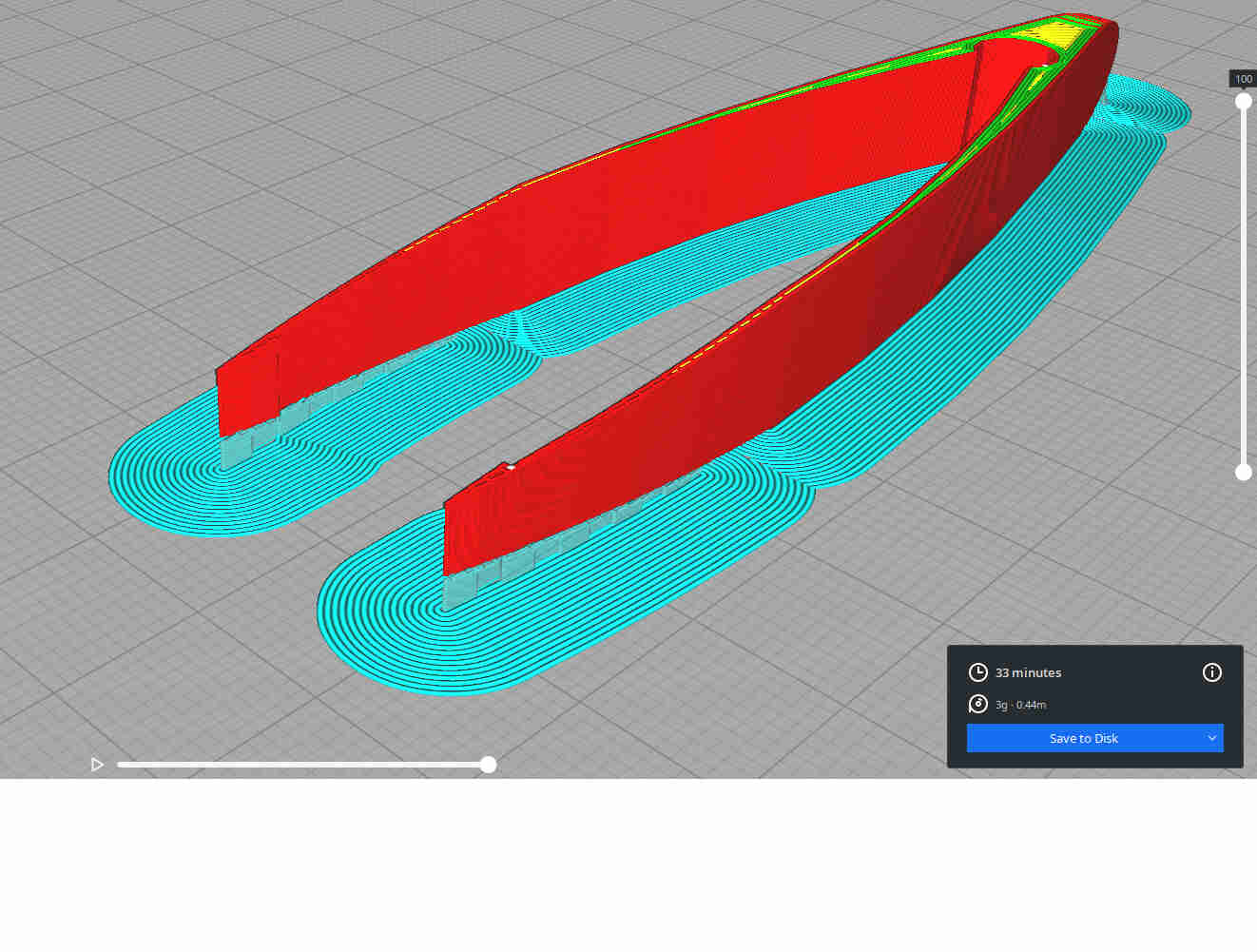
after setting the parameters i clicked on the slicer button and saved it as G-code
here you can download my G-codeHERE you can download all of the files (solidowks native,stl,g-code for ultimaker)from the tweezer
then set the printer making the tweezer
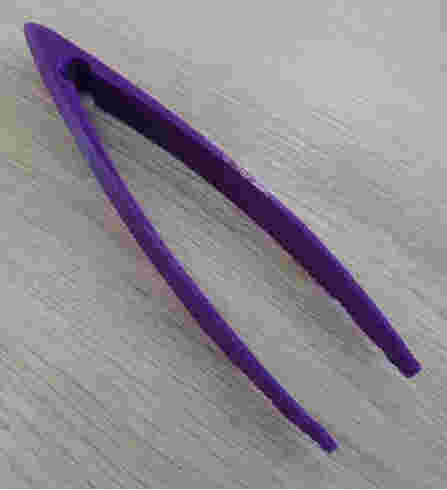
About the scanner
For this part of the assignment i used the microsoft kinect and usb adapter to 3D a printed part that i had near and made a video tutorial out it however i previously installed the kinect driver and a software called skanect that has a really nice freemium version. here you can go to download the driver i used on windows 10
here you can download skanect software
HERE you can download all of the scaning project files
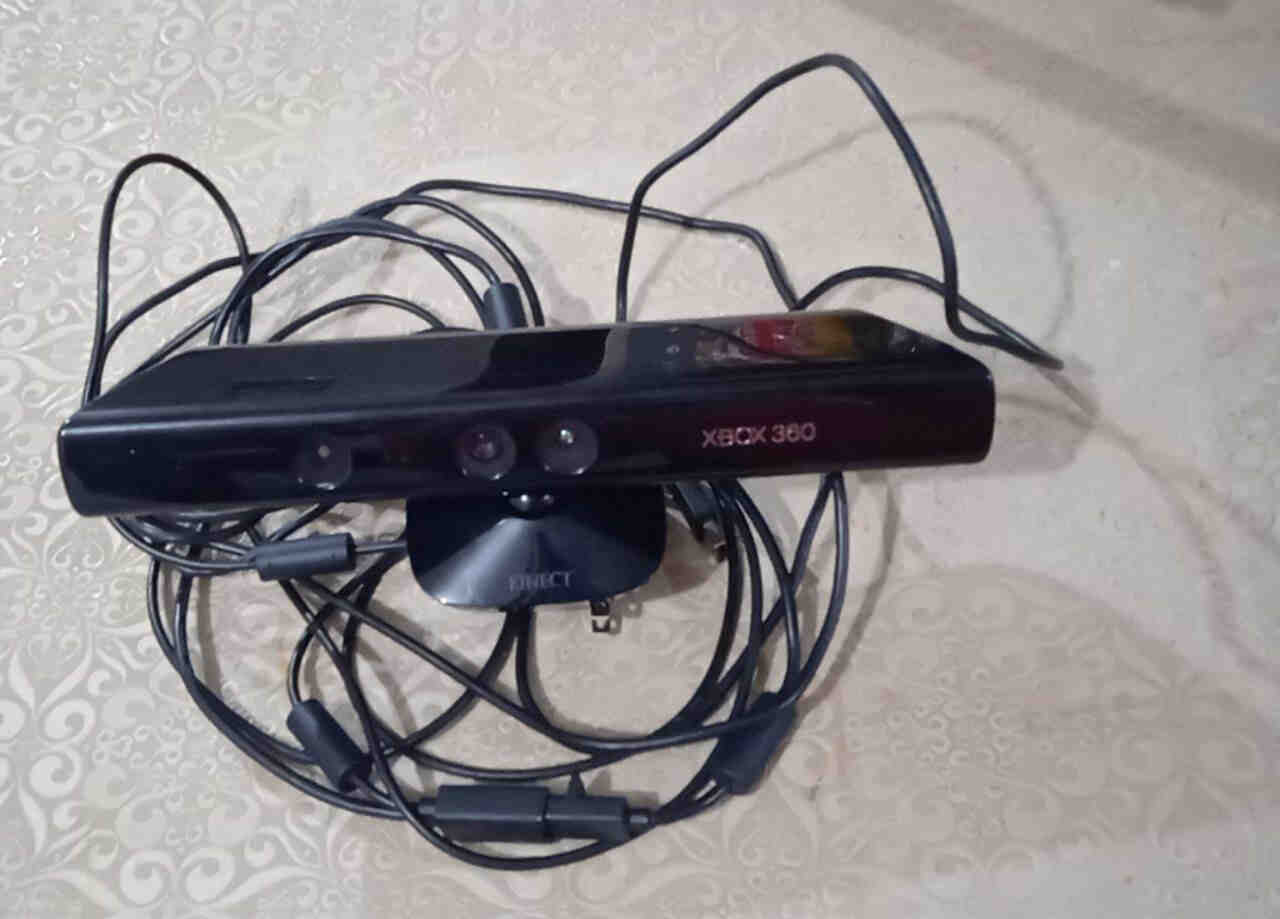
a litle step by step tutorial
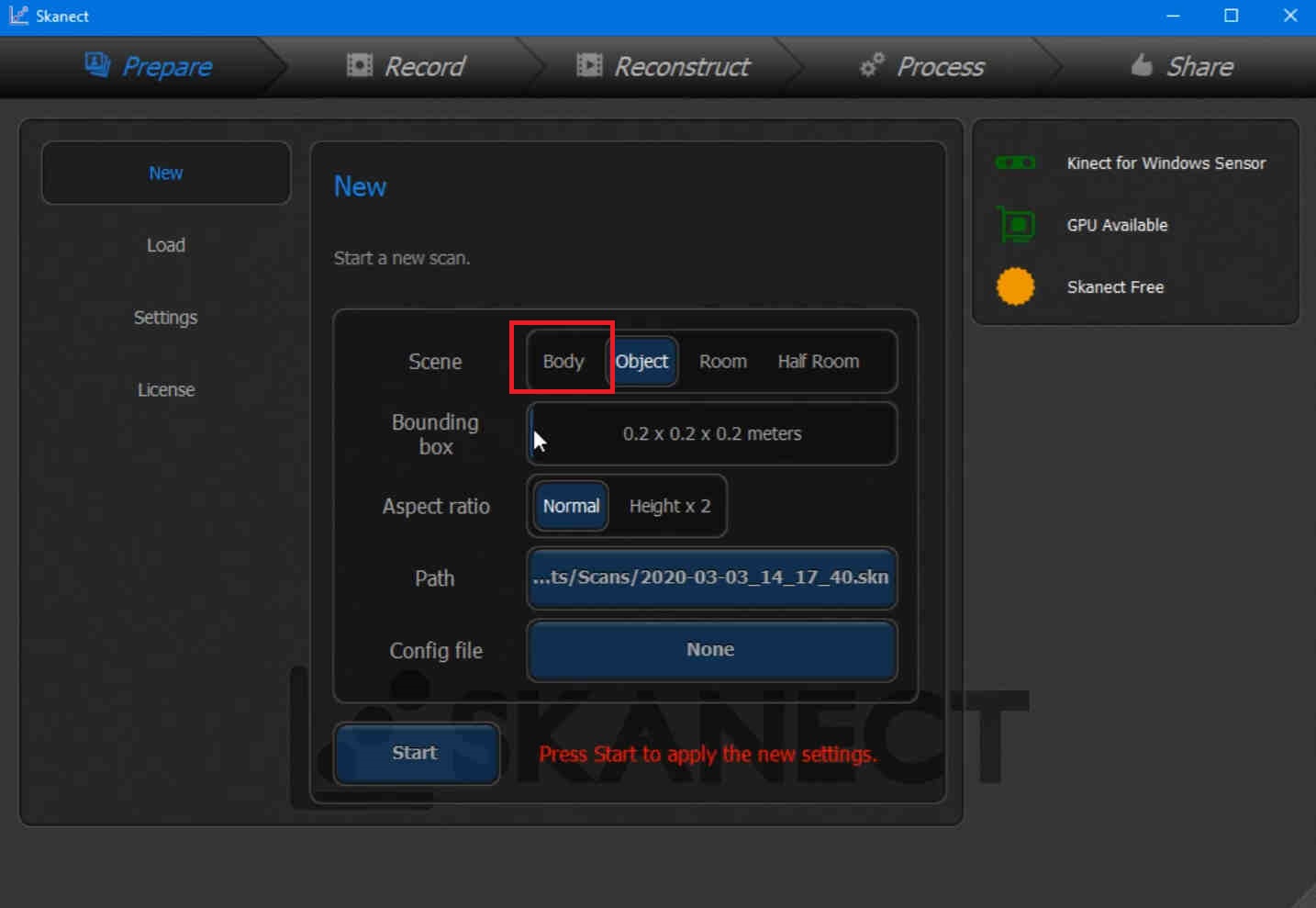
since we´re running the free version of the software we are just using object for this tutorial
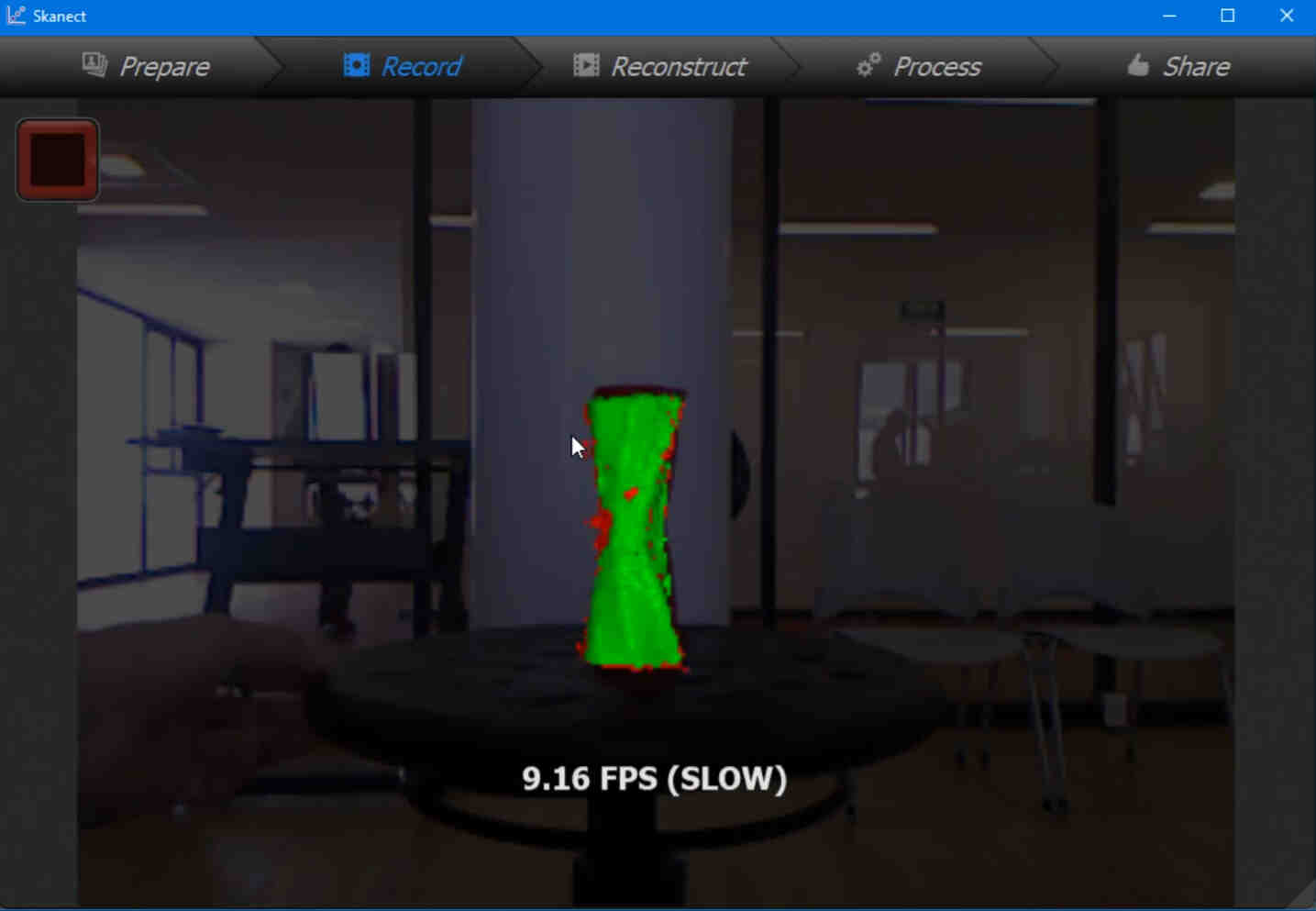
after that you should start recoding the scan while you rotate the object in front of the scanner.
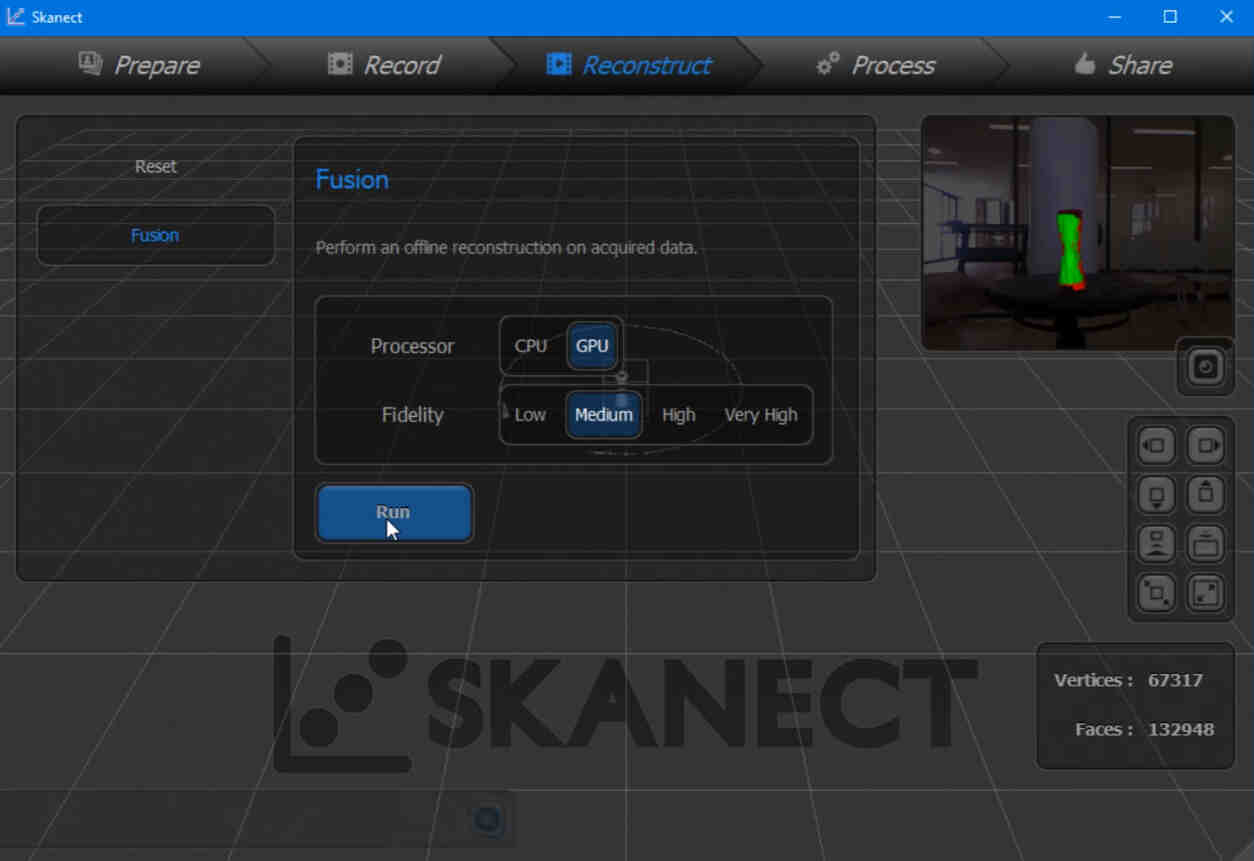
since i was using an alienware laptop i choosed GPU.
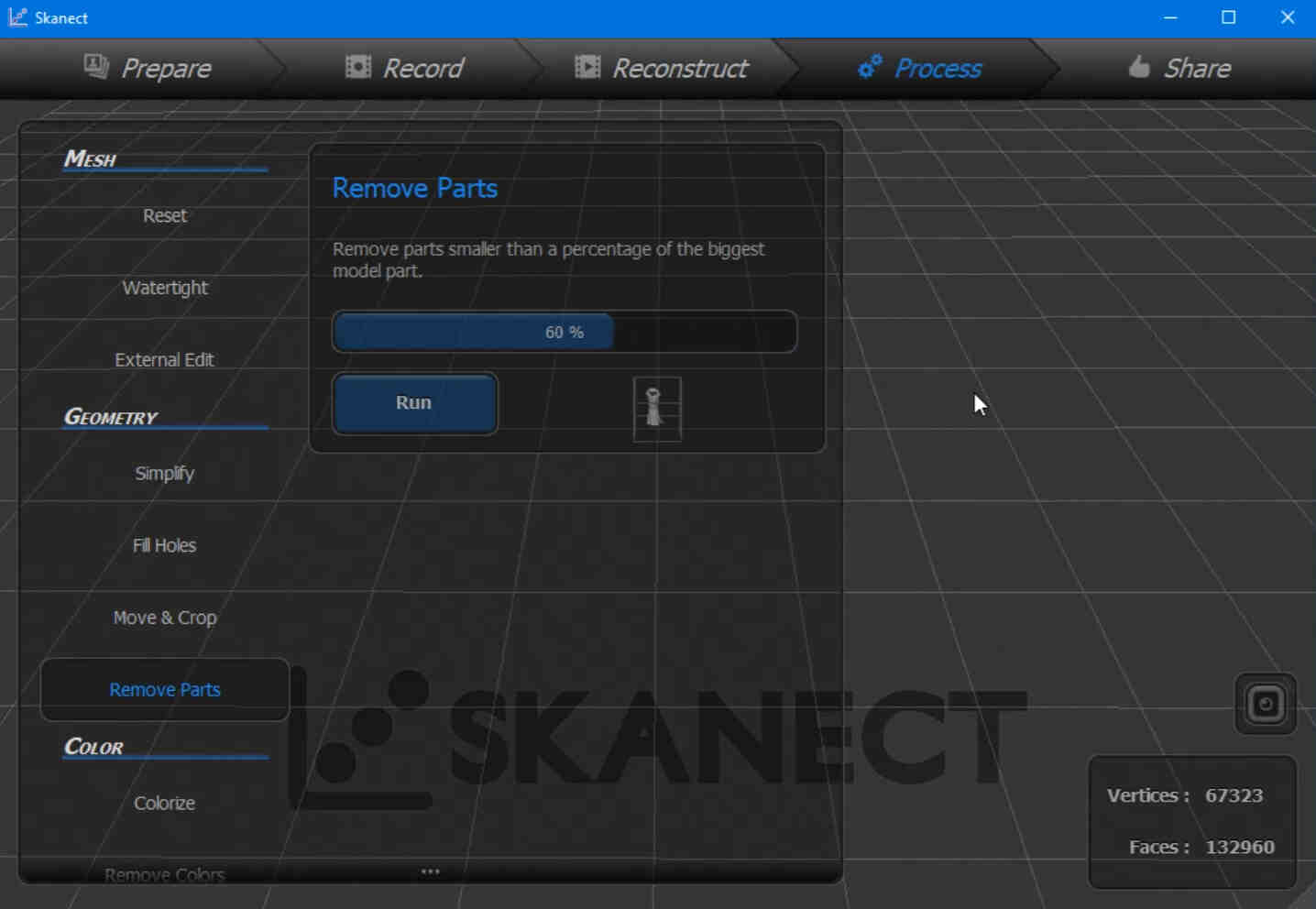
and here you'll tell the software. that you want a watertigh obj, stl,ply or anotherfile type
since this is just a tutorial i selected a stl in millimeters.
this video is hosted from my youtube account
and this video is hosted on my repo.
About the hinges
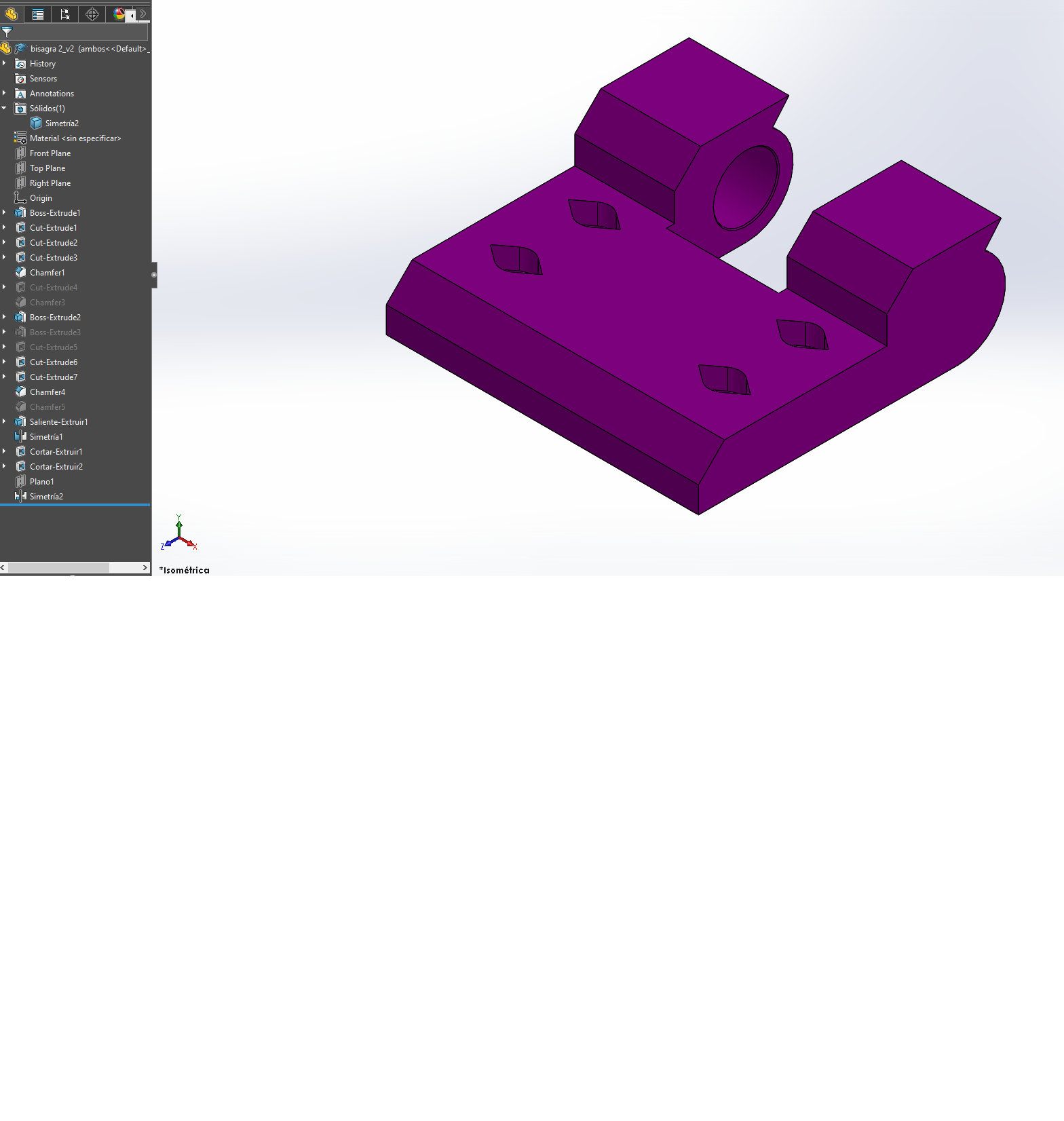
just used a mirror feature in solidworks just to make it symetric.
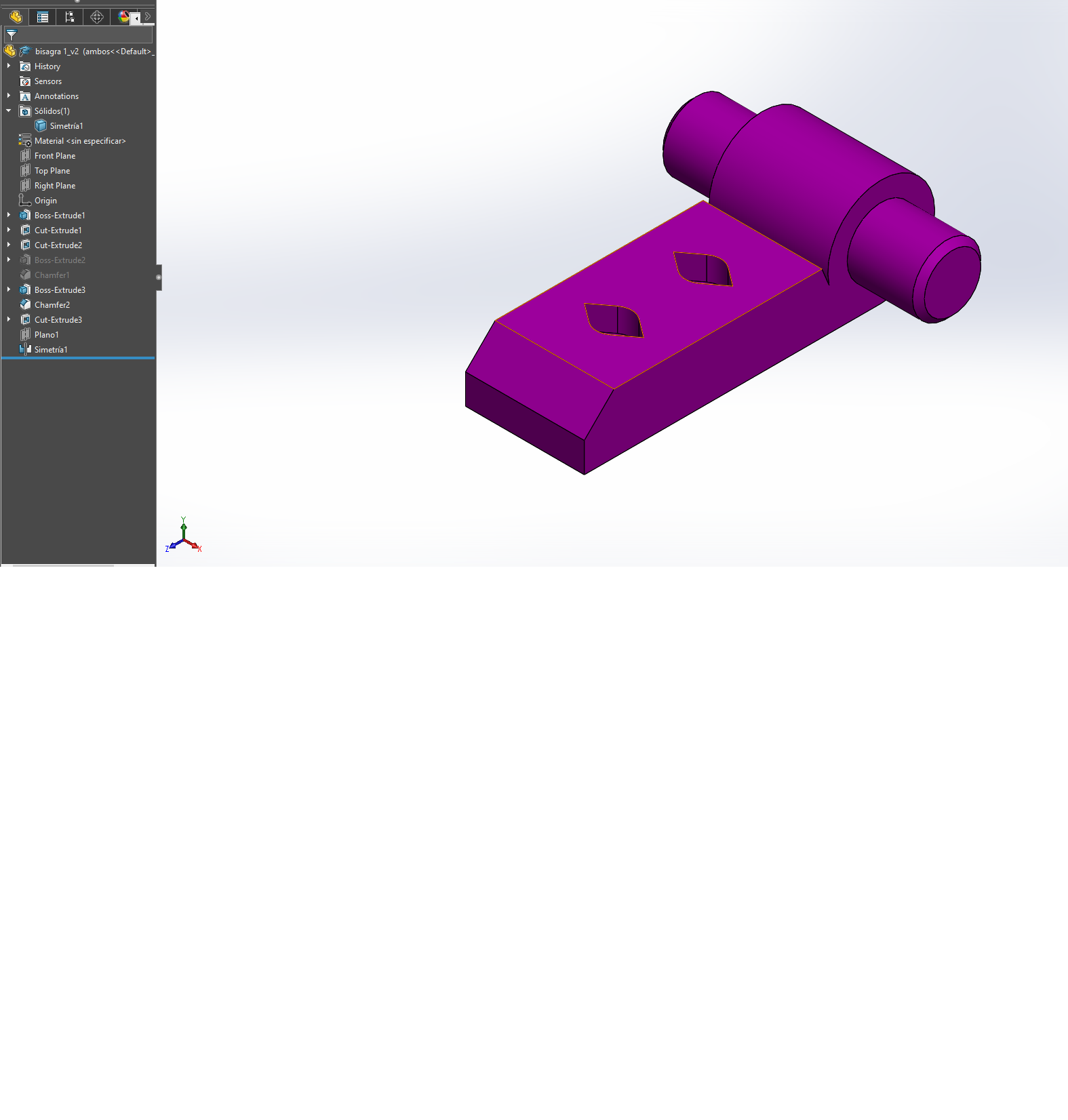
also with theese i'm using the same mirror feature.
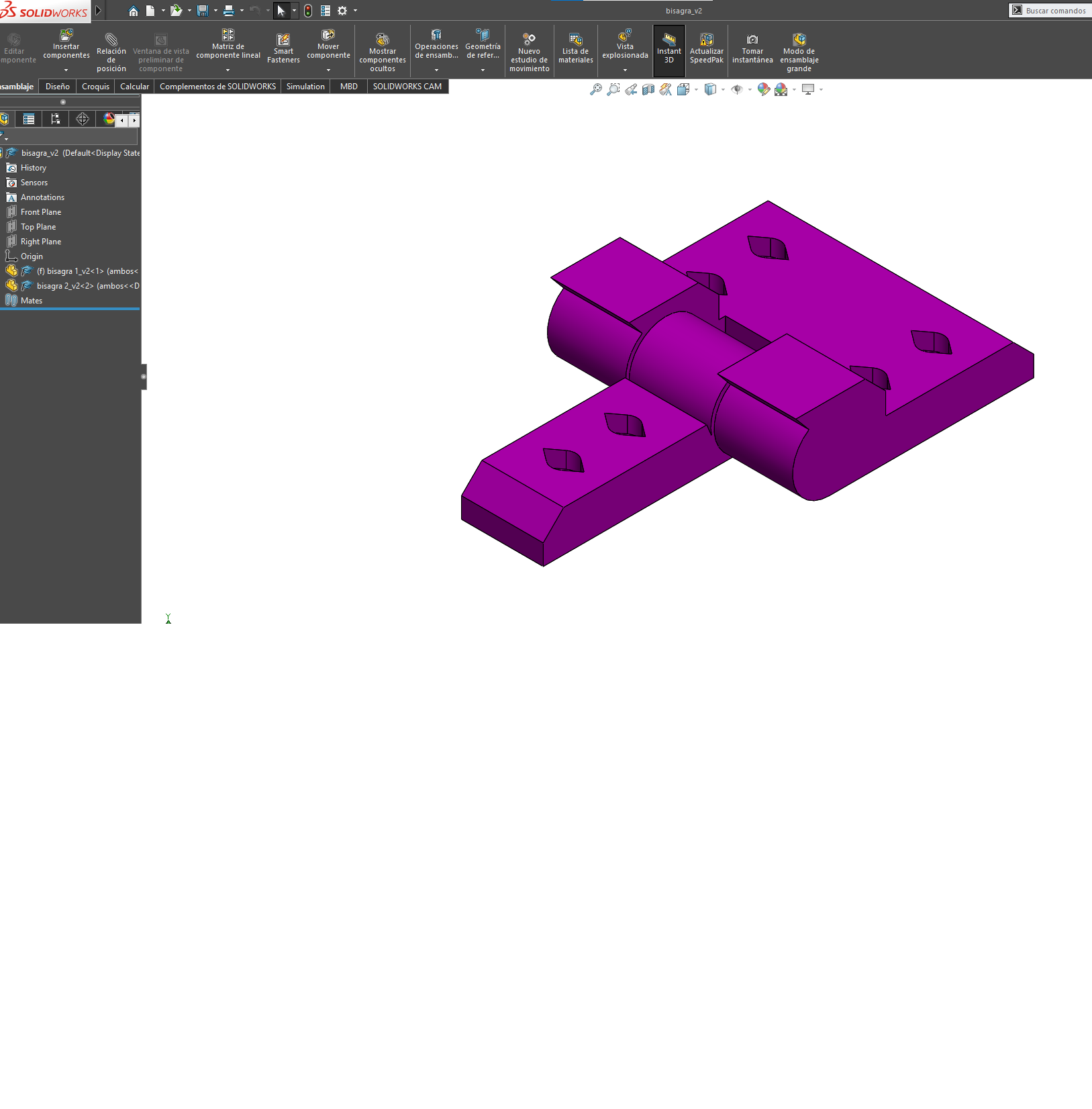
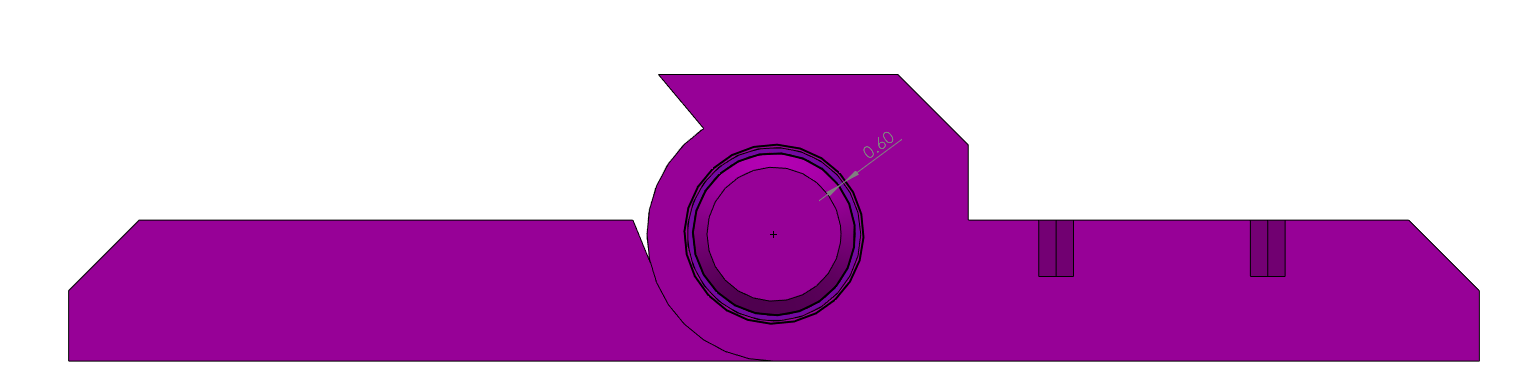
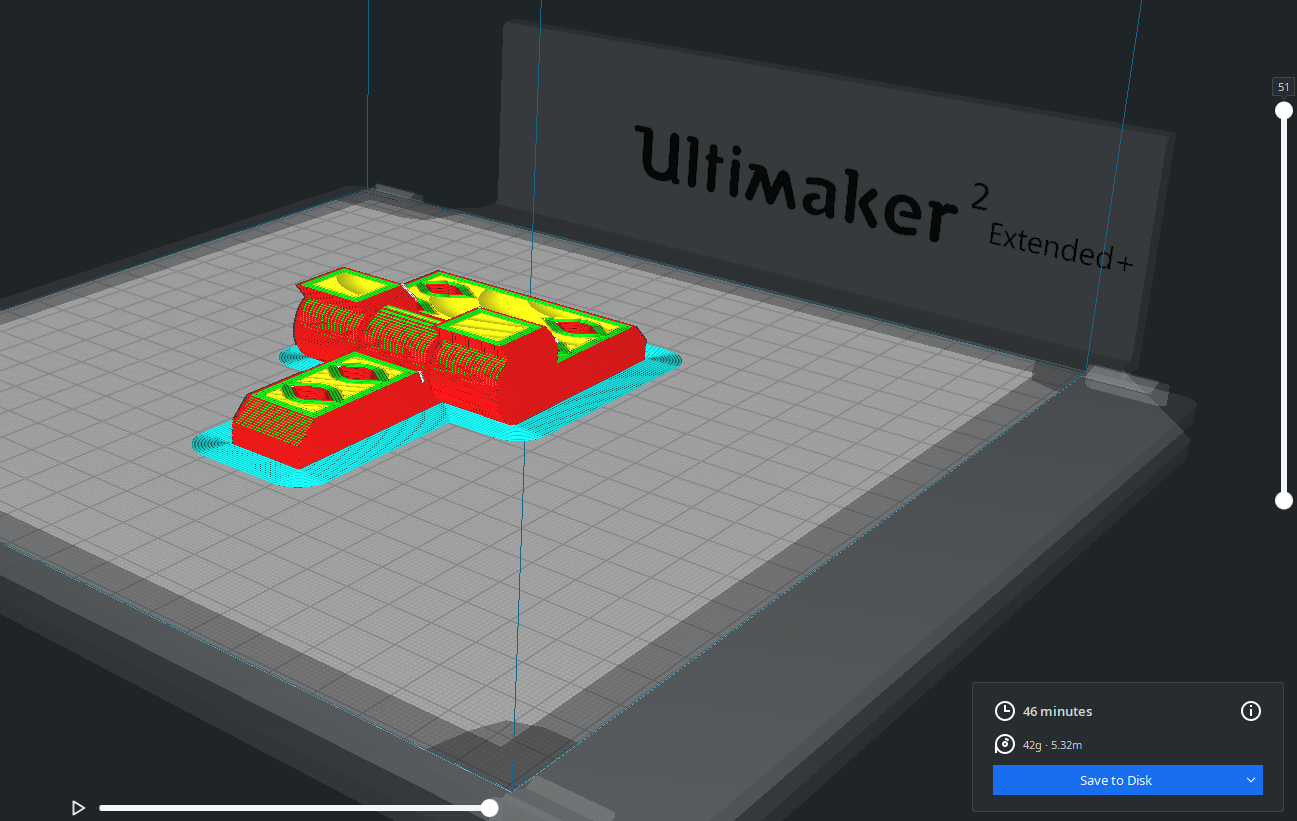
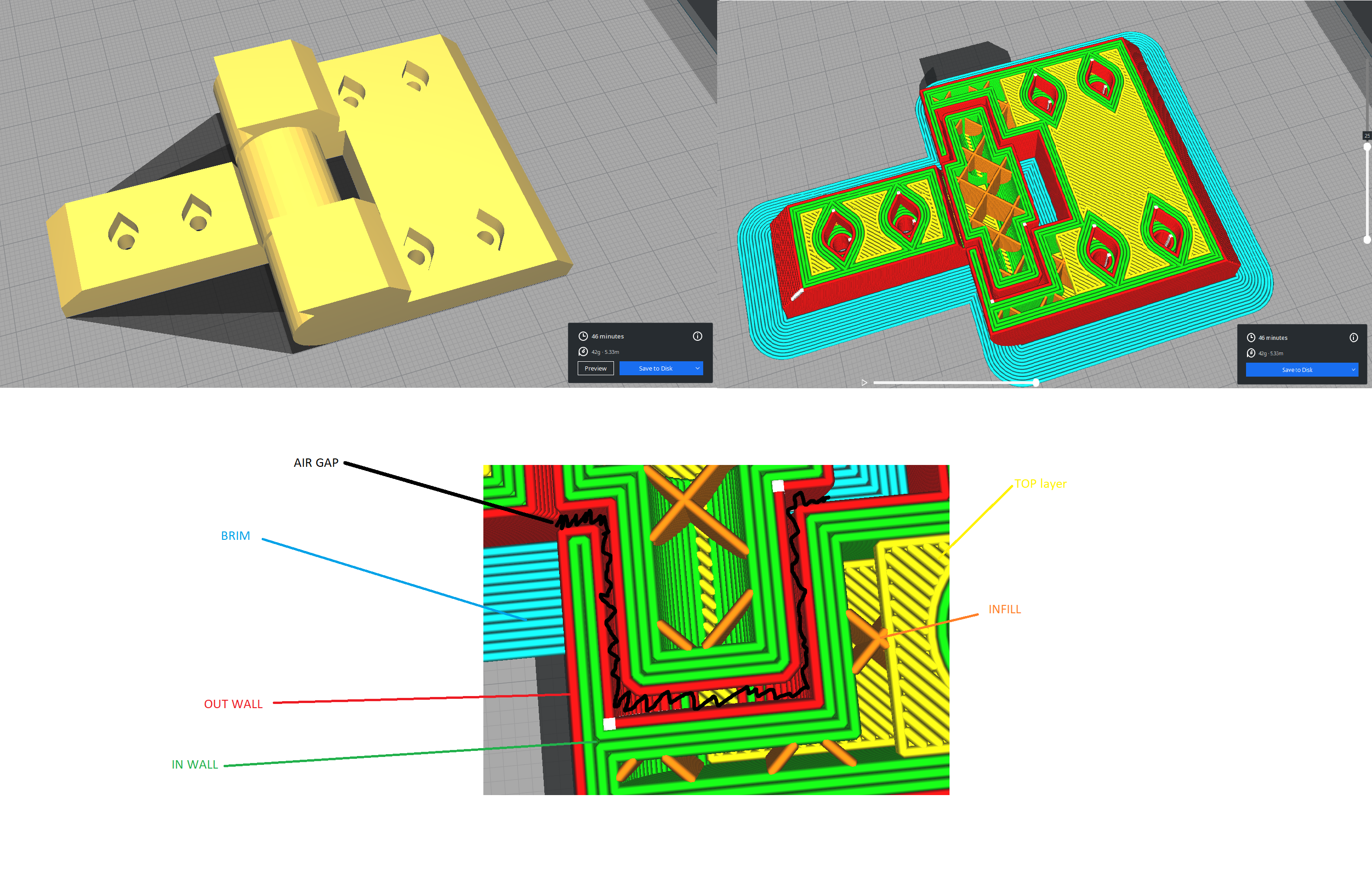
so the gap between parts looks like this
however if you print a little bit slower it will jam
if you print a little bit to print a little hotter than normal i'll jam
if you run the print to fast will underextrude.
it's just to irregular and odd to keep changing the parameters with every print.
and is better practice to print the files separatly
in this case the assgnment wouldn't met requirements if printed separatedly.
so i had to print a knickknack :(
g code for ultimaker 2+ extended
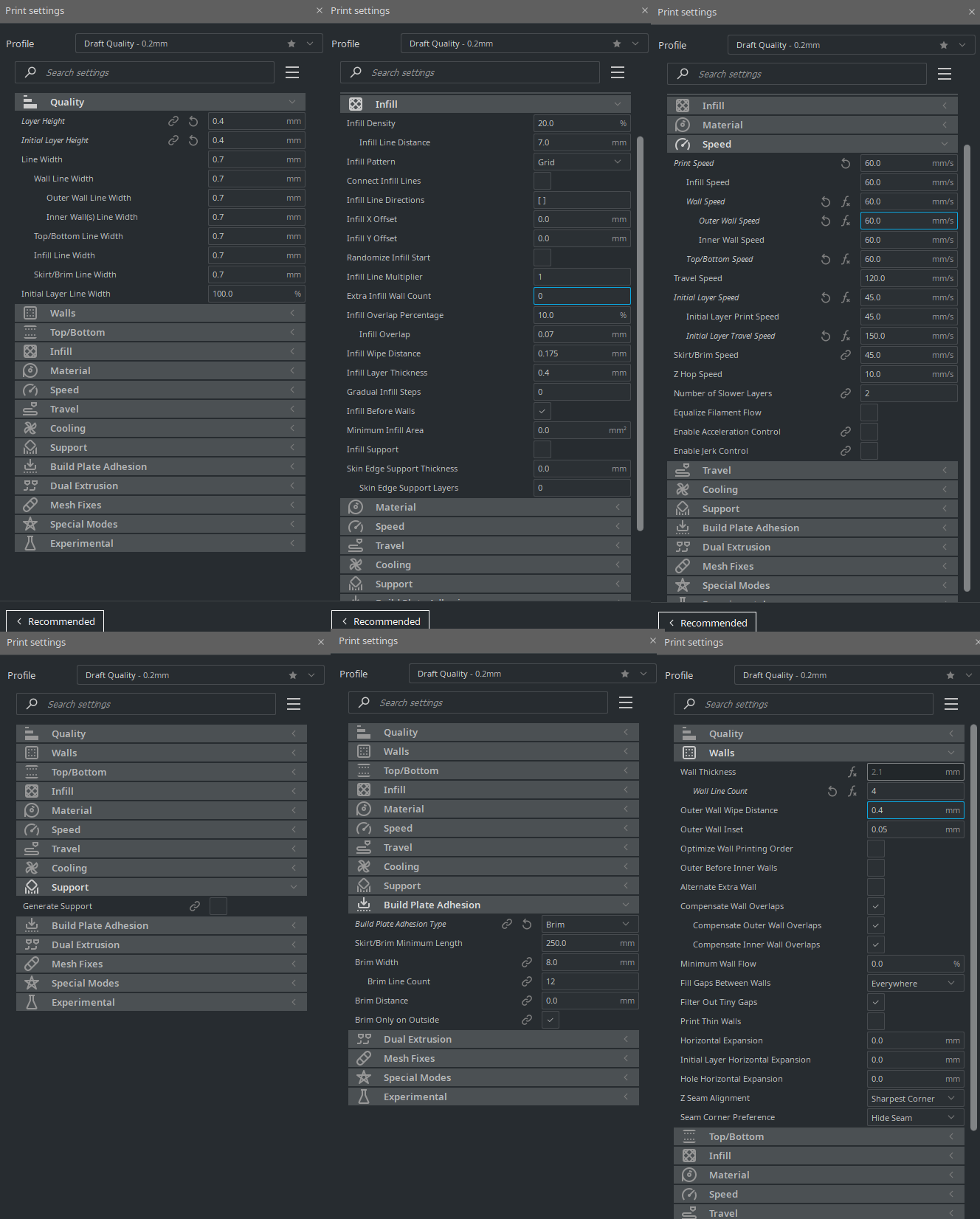
there are just way to many parameters that afect a 3d print.
ussually i never recomend print a mechanism in one go.
it's inefficient. it's harder to get it right.
and the result usually end up in the garbage anyways
LAYER HEIGHT settings should never be equal to the nozzle diemeter.
the maximum i recomend is 90% of the nozzle
same goes with LINEWIDTH not over 90%
but if it will get some stress you should crank it up to 100%
the use of support material. it kind of a big nono when 3d pinting.
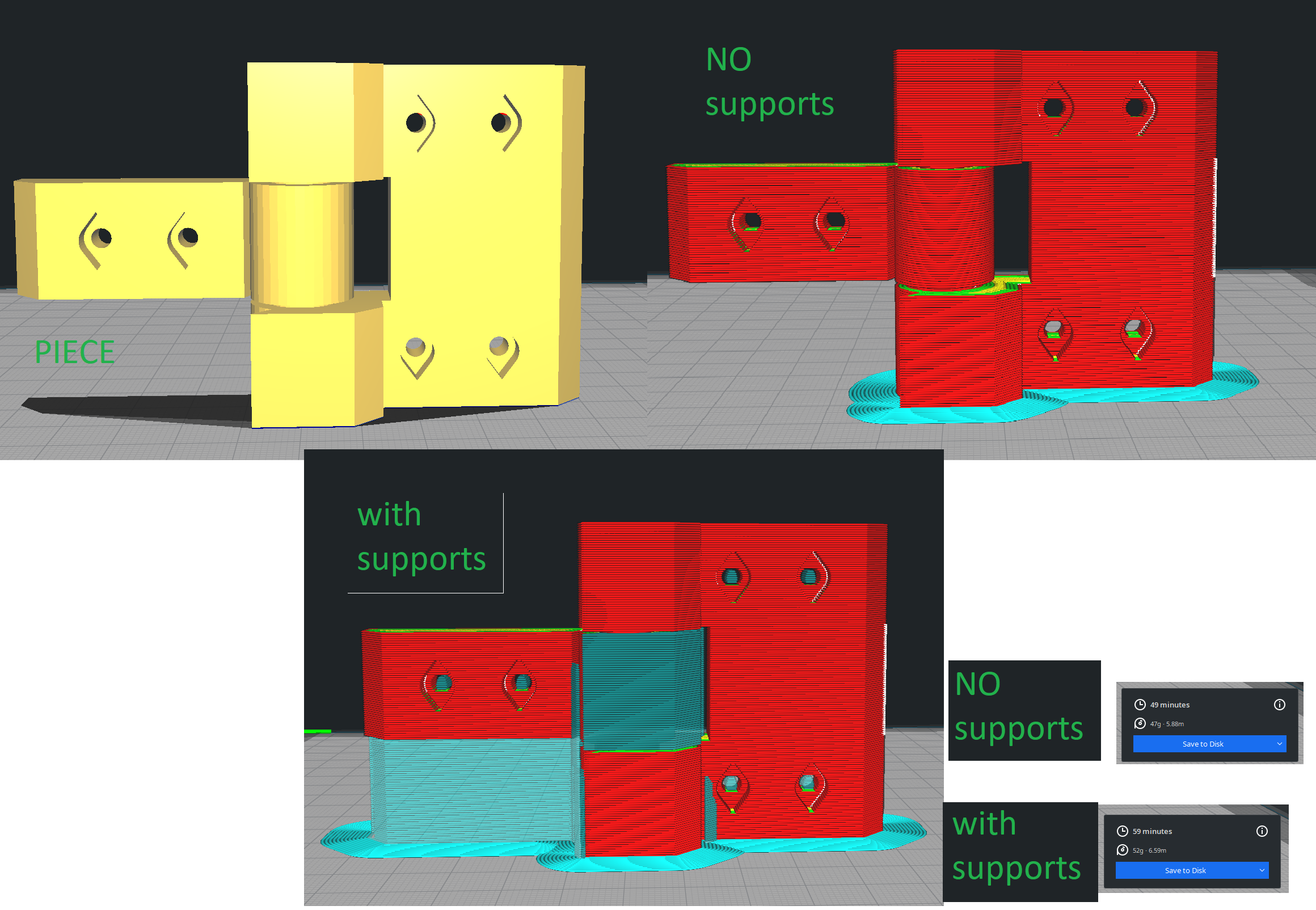
this is the diference in the same piece with supports and without supports.
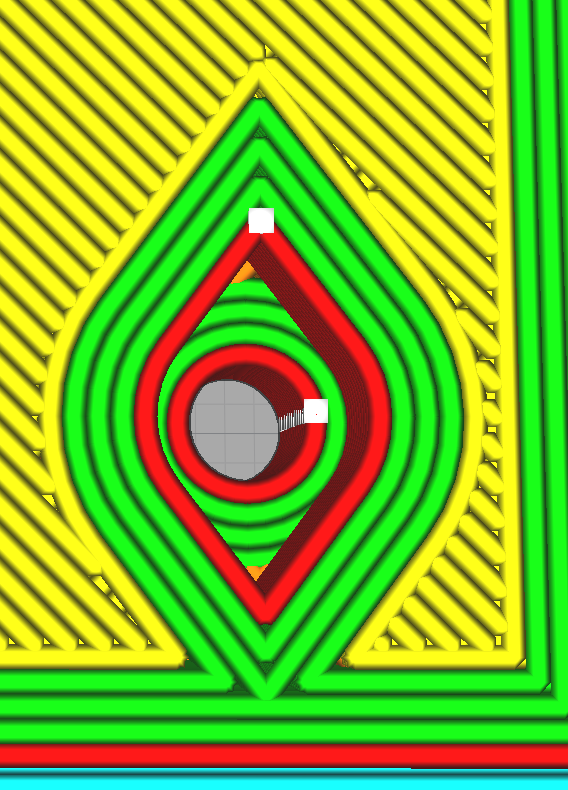
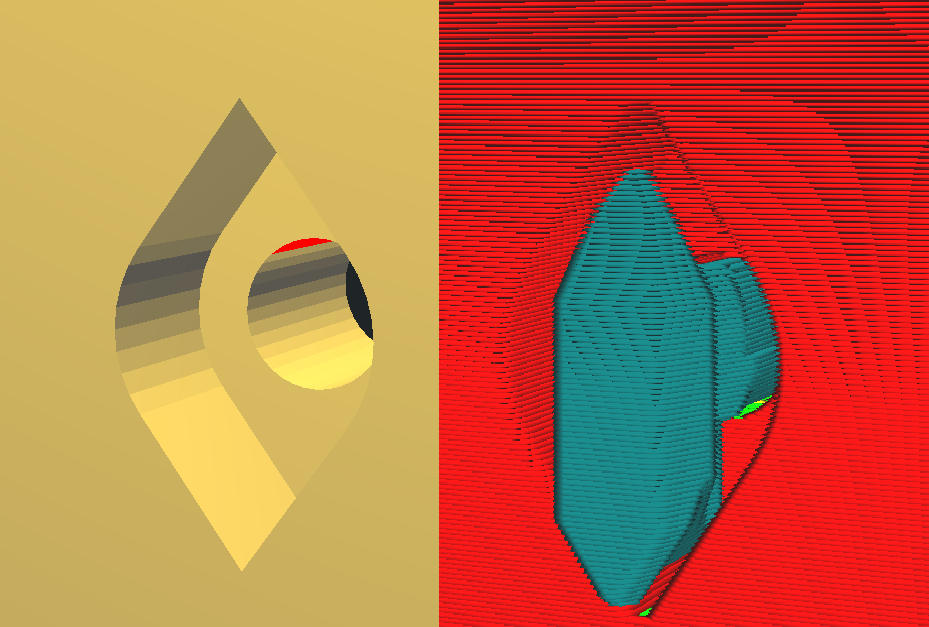
this is the diference between with and without support settings.
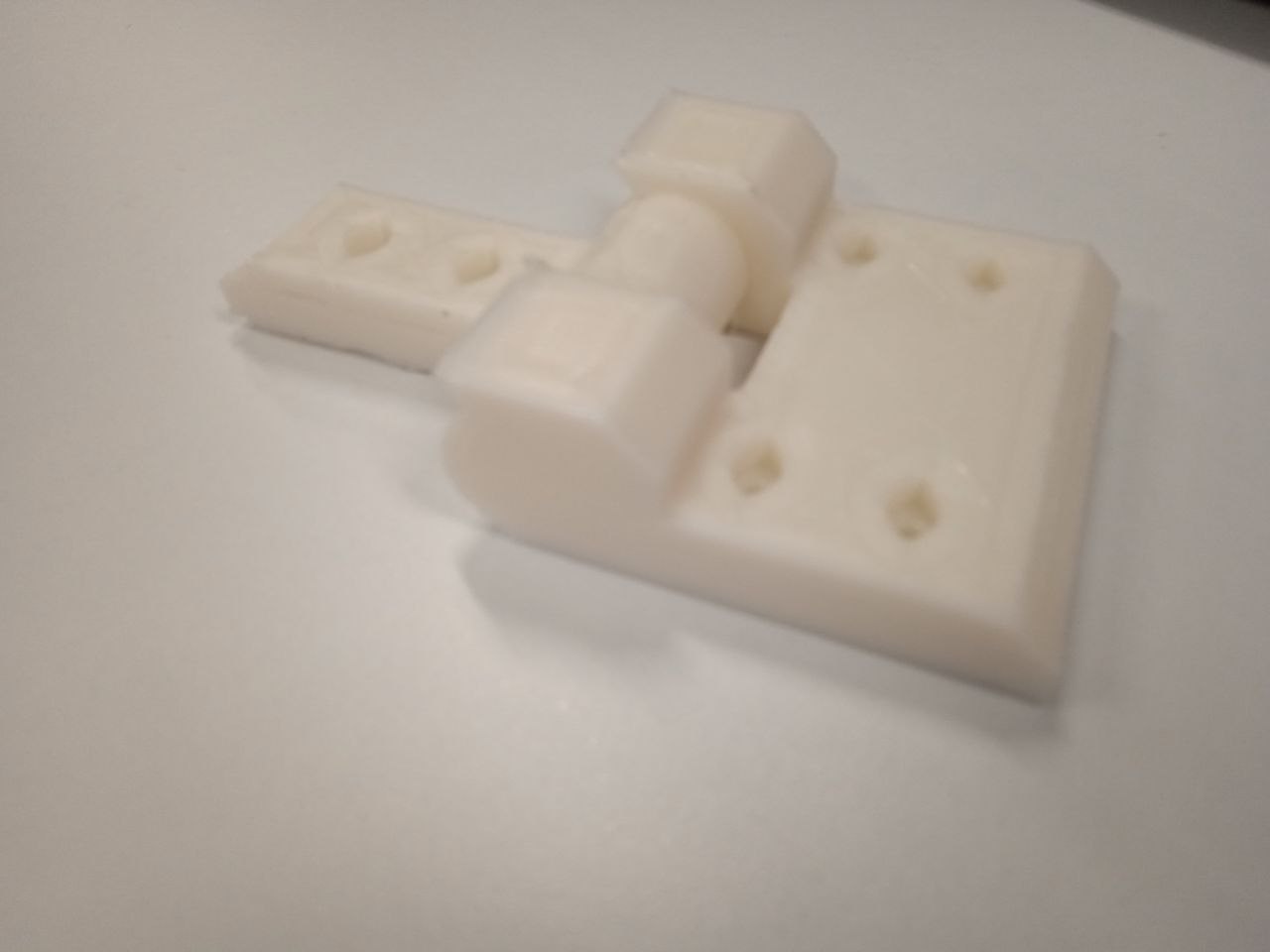
links and references
HERE you can download all of the files (solidowks native,stl,g-code for ultimaker)from the tweezer
HERE you can download all of the files (solidowks native,stl,g-code for ultimaker)from the Festos's bootleg
HERE you can download all of the skanect
here you can watch the video i was talking about the model he build