Assignment 10_molding and casting
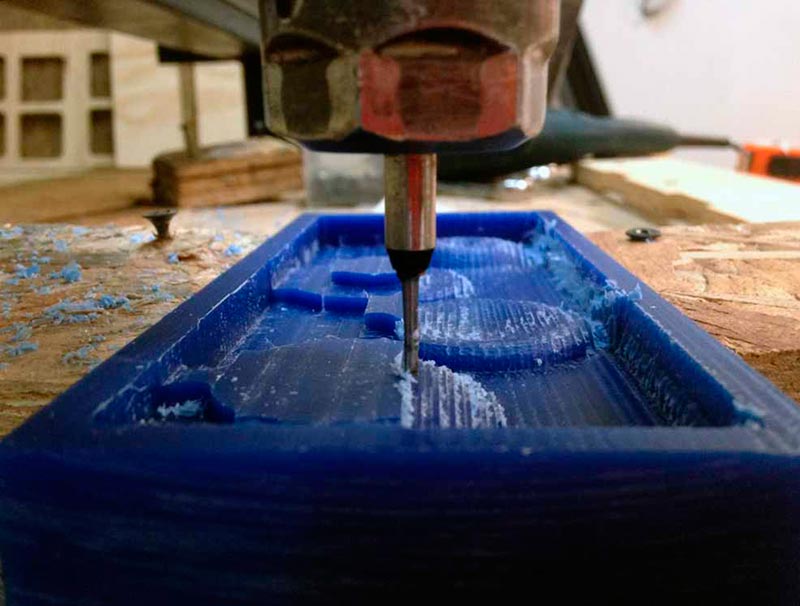
01 review the safety data sheets for each of your molding and casting materials (group)
For the group assignment, we test different types of materials in a polymer mold, using an ice cube mold that worked very good.
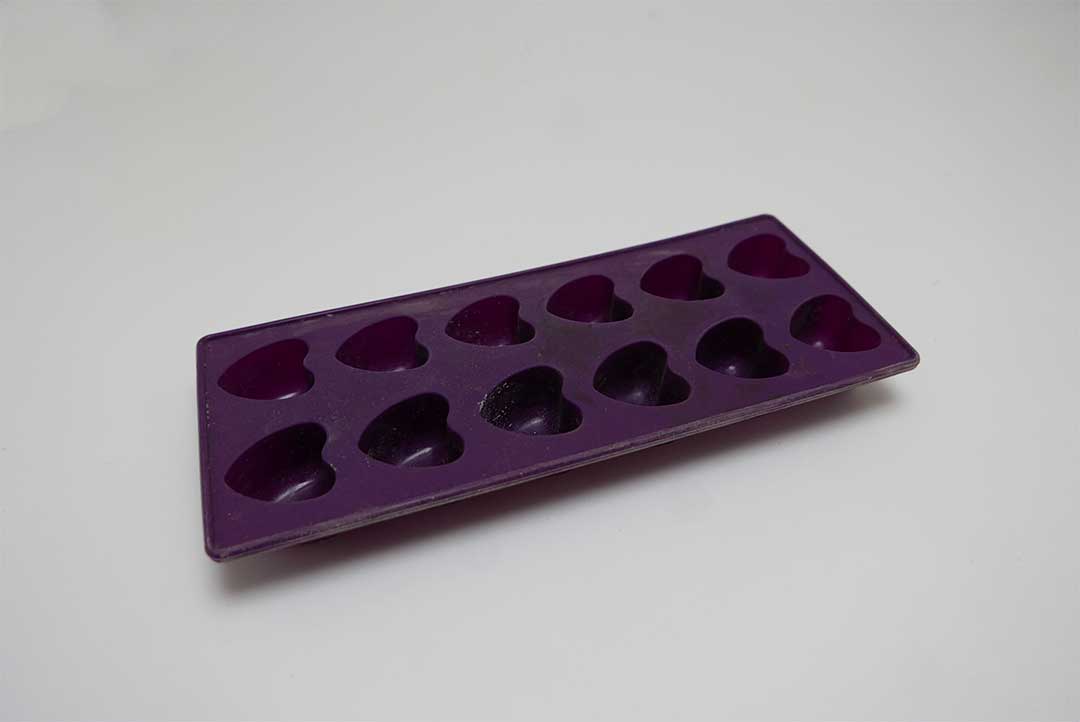
The first test was cement; we were curious about how will work this material because is a very nice material for all type of products. The mix was: 2 cups of cement + 1 cup of water. This was the result.
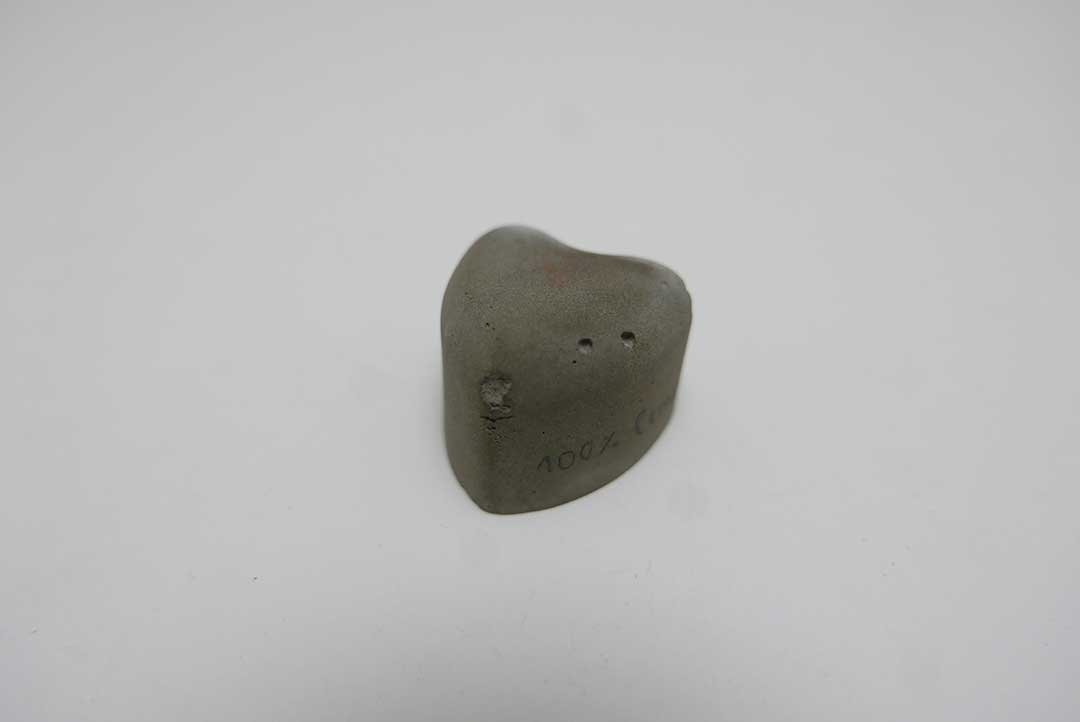
For the second test, we use cement again, but we add some ink to observe how the material behaved. The result was very similar to the first one but was interesting to search for new looks for the cement.
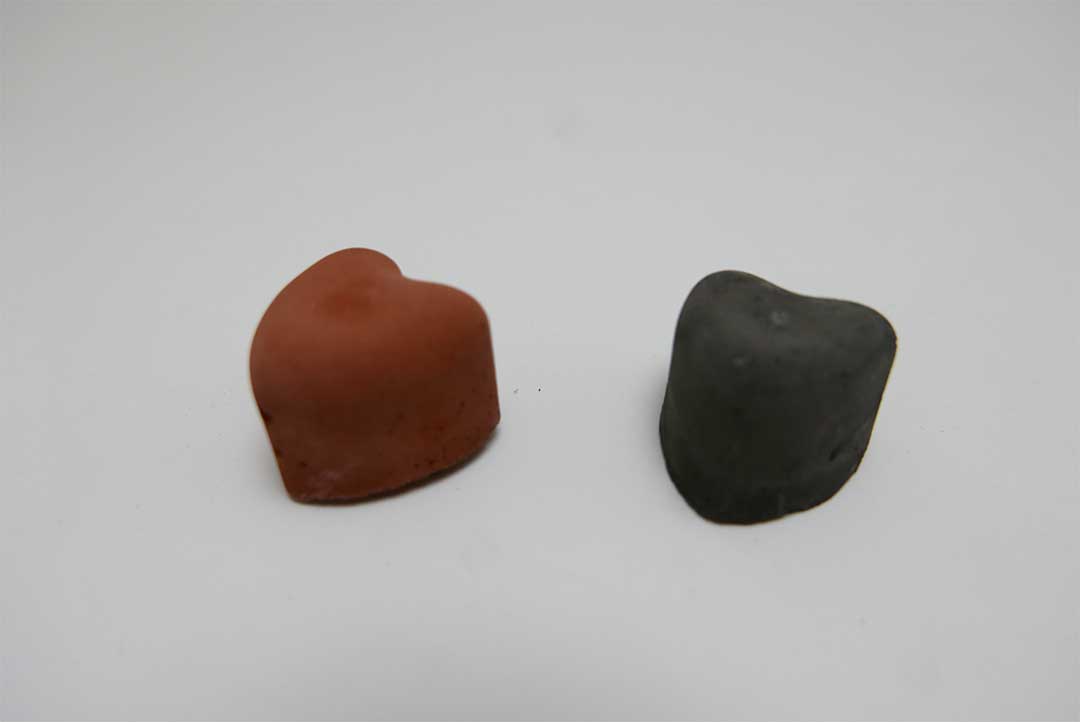
In Fab Lab Santiago we have a Bio-Lab, Materiome, which is an investigation area that studies the development of different biomaterials and their qualities. So we thought that would be nice to understand how these new materials will work in molding and casting, for future projects/products, or maybe even for my final project.
First, we use coffee + pine resin. The result was a lovely smell (of coffee) but had a lousy resistance when we applied and moderate adaptability of shape
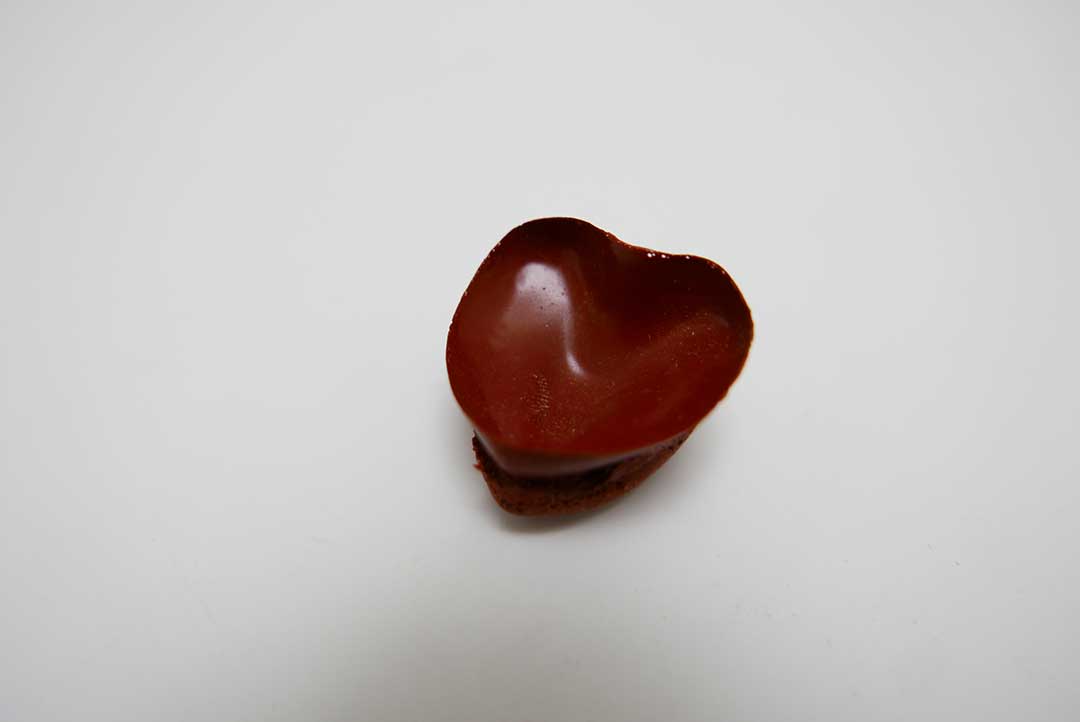
Second, we use silicone, where unlike the previous test, had an excellent resistance and good adaptability. We made a wrong mix because you´re supposed to use 50% / 50% of component A and B, it had a lousy contraction but a right end.
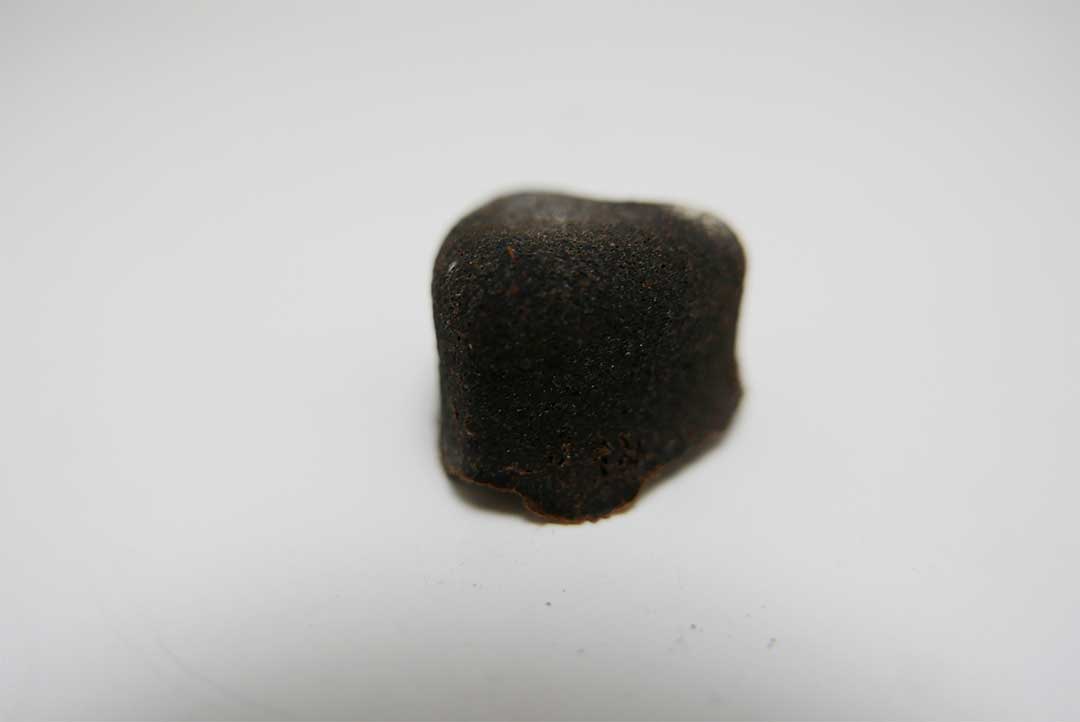
Finally, we made: paraffin + eucalyptus. The mix had a great ending but little resistance to the heat.
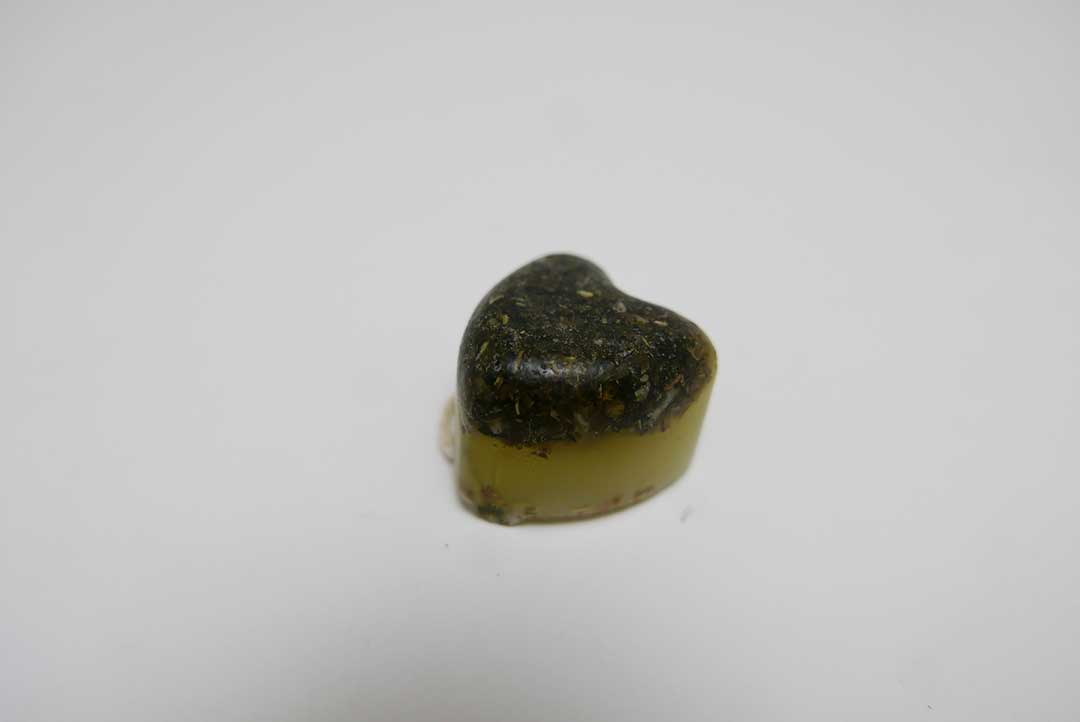
It was amusing to try different materials and understand the main characteristics to manufacture good quality of molds and products.
02 design a 3D mold around the stock and tooling that you'll be using, machine it, and use it to cast parts
I seize the March’s break to rethink my final project, so I could use the weekly assignments to fulfill the development of the project.
I am going to take advantage of this assignment to test how the silicone would work on the cover of the basic module of my final project.
3D MODEL
First, I model in Fusion 360 the three objects of the basic module (of my final proyect): the cover, the rail and the base. I Export the three elements in STL.
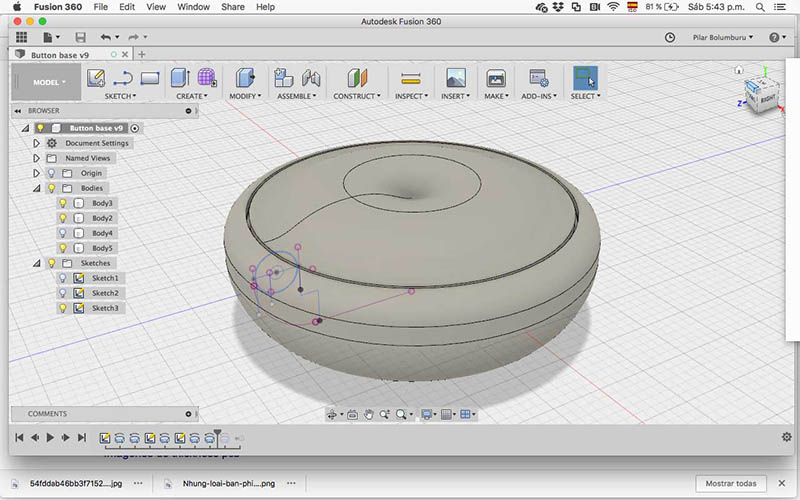
Then, I generate two sides molds of the negatives of the cover. I add four semicircumferences to guide the mods and a canal to load the silicone when the mold is closed.
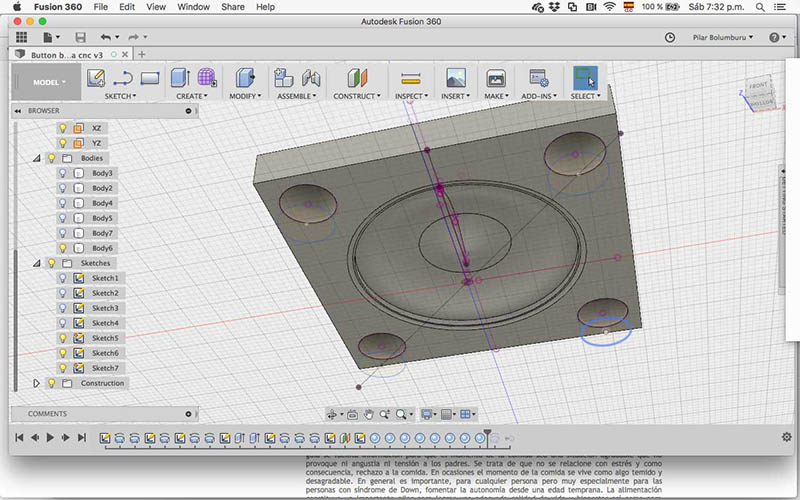
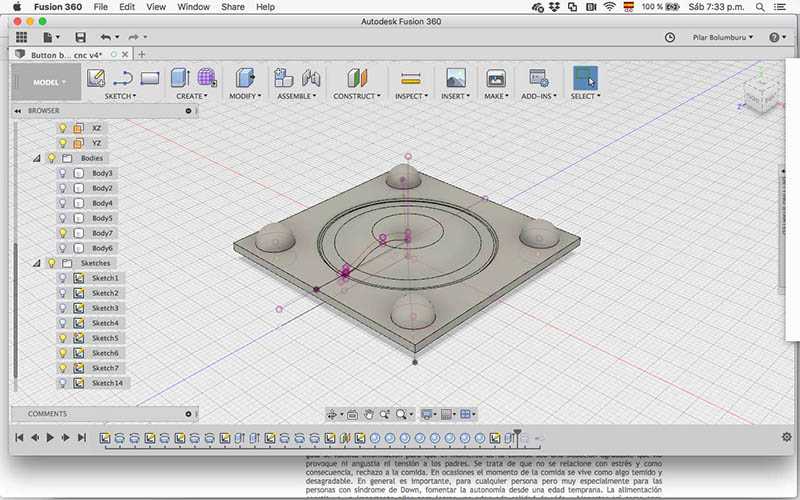
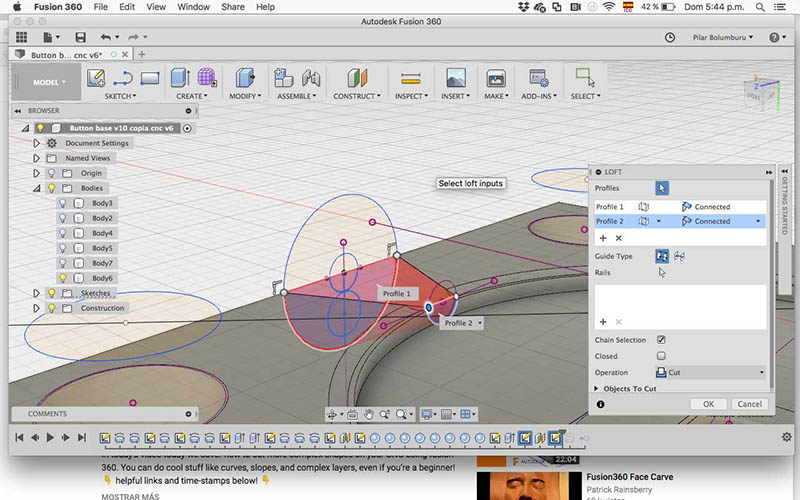
I thought in to fabricate the molds in the big router CNC of the lab, but the elements were too small, and I need it more precision. So I decide to use the monoFab SRM-20. I had used the monoFab only to fabricate my PCB, so I start to learn how to do it on this machine.
For milling in the monoFab SRM-20, I try to use mods, but I couldn't find the program for molds, just for PCB. I search in the fab academy archive, and I found some people that had use fab modules, I still don’t understand how to generate the file and preview the results.
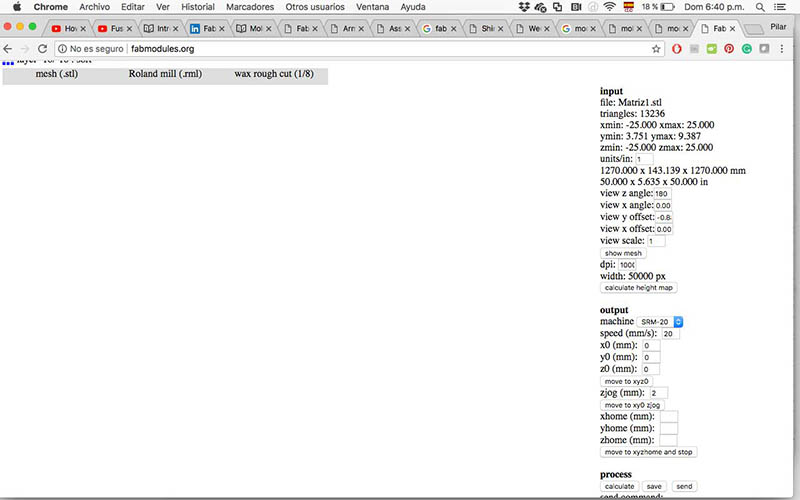
Finally, for saving time, I decided to fabricate the mold in the big Buca CNC we have. This router generates the code files in ArtCam (CAD), but you control the machine and send the files through Match 3(CAM).
For the file, I finally model 4 different types of “buttons”(the cover of the module)—for my final project—to test with kids which one they prefer and is more attractive. So I modelate four buttons, and I create the negative mold for, later, fabricate the positive mold in silicone.
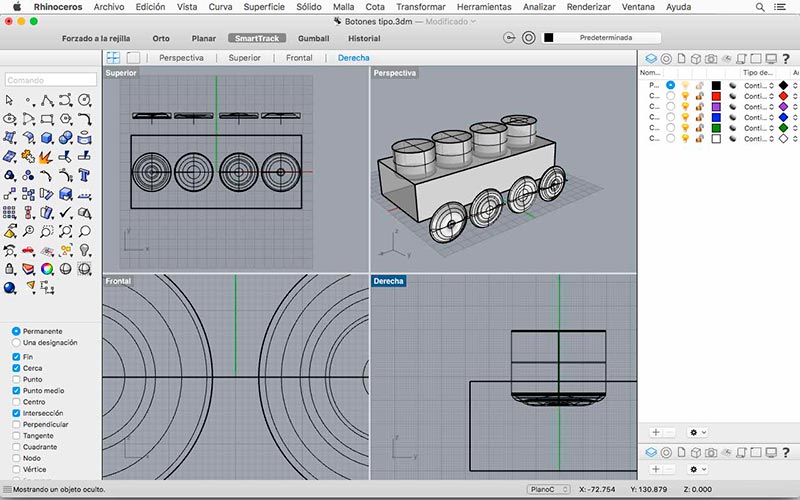
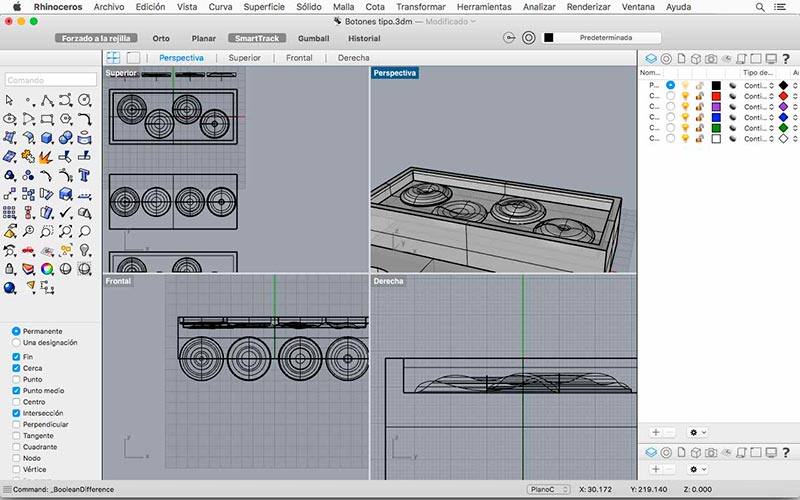
ArtCAM
In ArtCam I need the .dxf and the .stl file because you need to link the 3D file to a 2D. Once I import everything I create the first Roughing Toolpath with a 6.3mm flat end mill (two flutes), to carve material faster.
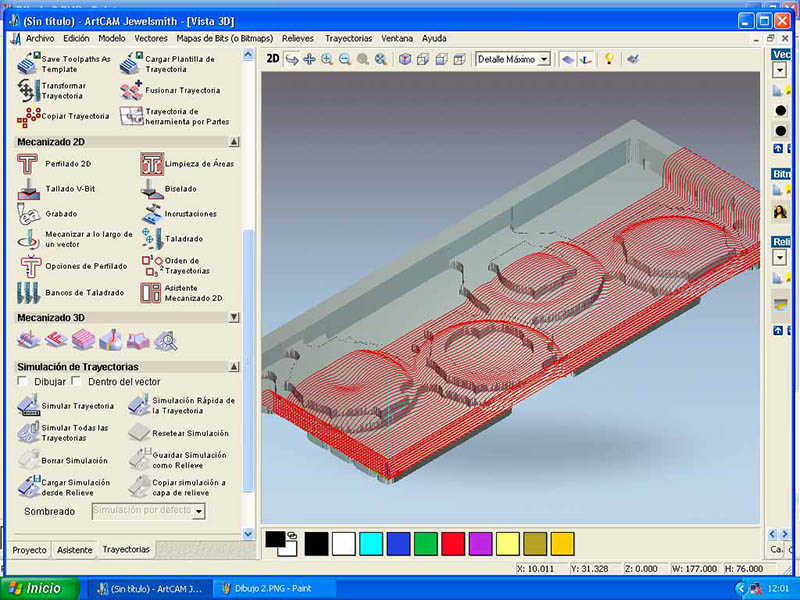
Then, I create two Machine Relief Toolpaths, the first one horizontally to the wax and the second one vertically to the wax, to generate a smoother surface. I create both of the toolpaths with different end mills to compare the results with the visual simulator. First, I create one with a curve end mill of 6.1mm (Left image), but was too big and couldn’t cut very well the details of the corners (leave a radio) and the small spaces. Then I try a 3mm flat end mill(right image) and the result in the visual simulator look with a very high definition compared to the other end mill, so I decided to use that file.
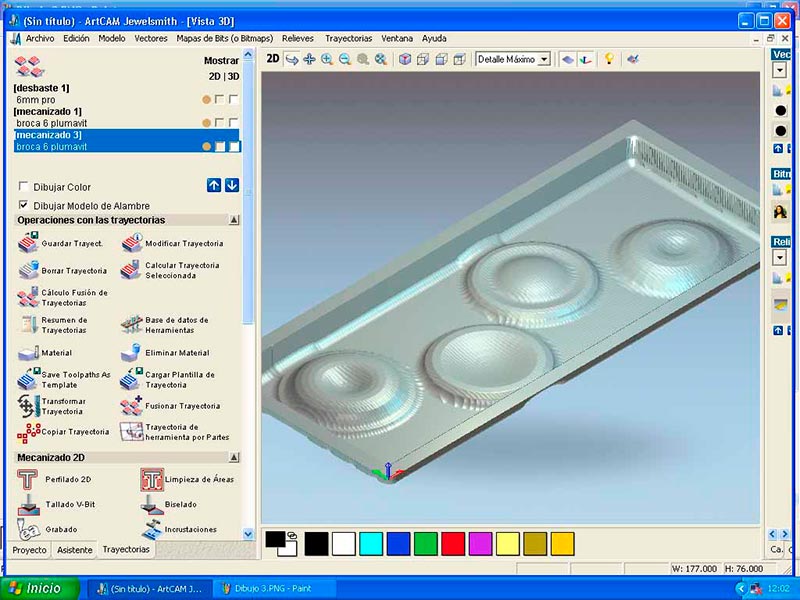
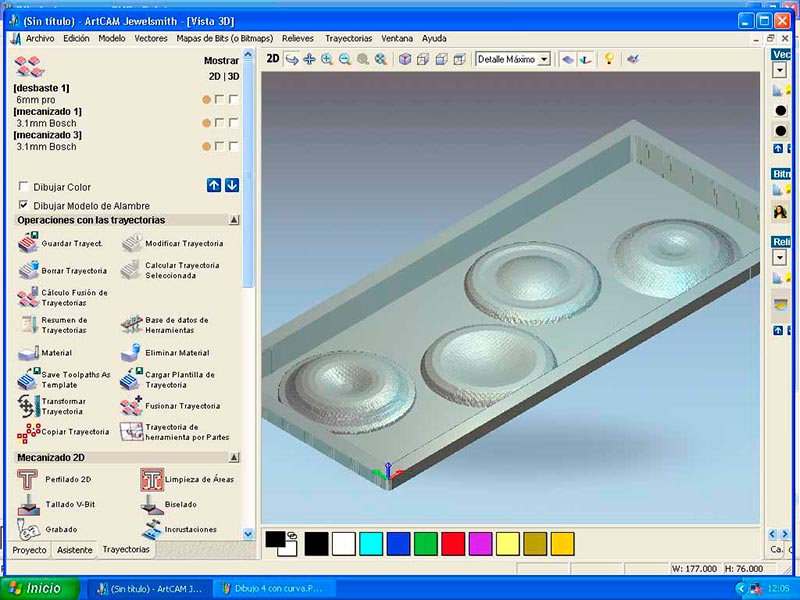
MACH3
I had to create two different gcode files for the different end mills (.TAP files), and pause the machine after the roughing because I had to change the end mill.
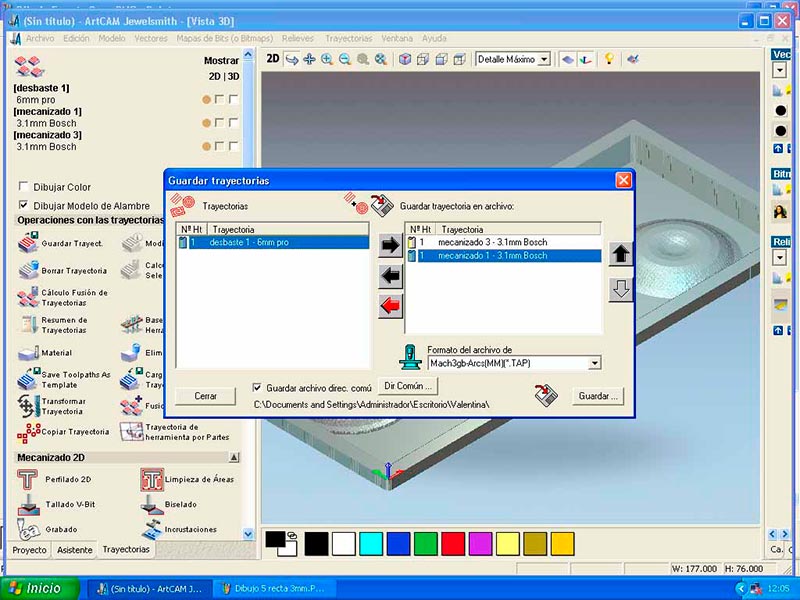
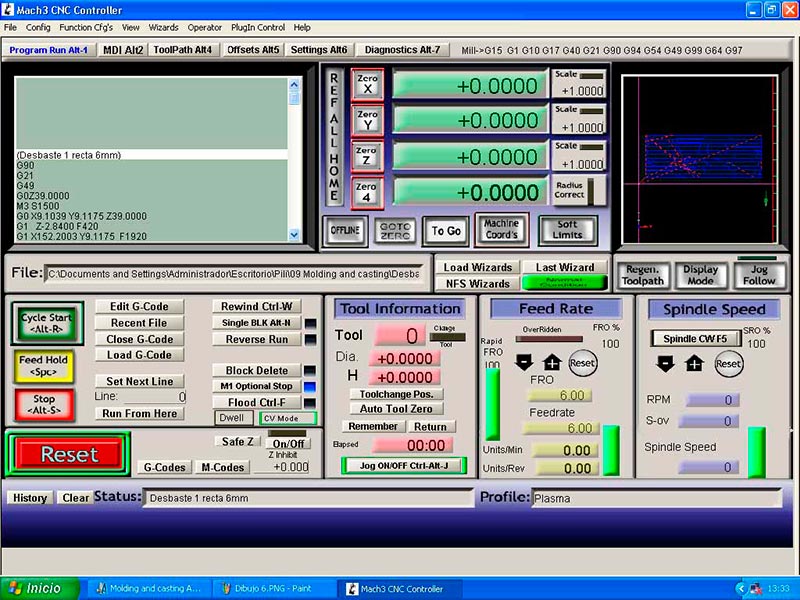
ROUTER CNC
For adding the material to the machine I used double sided tape but didn’t attach very well, so I add wood blocks to the sides so the wax couldn’t move.
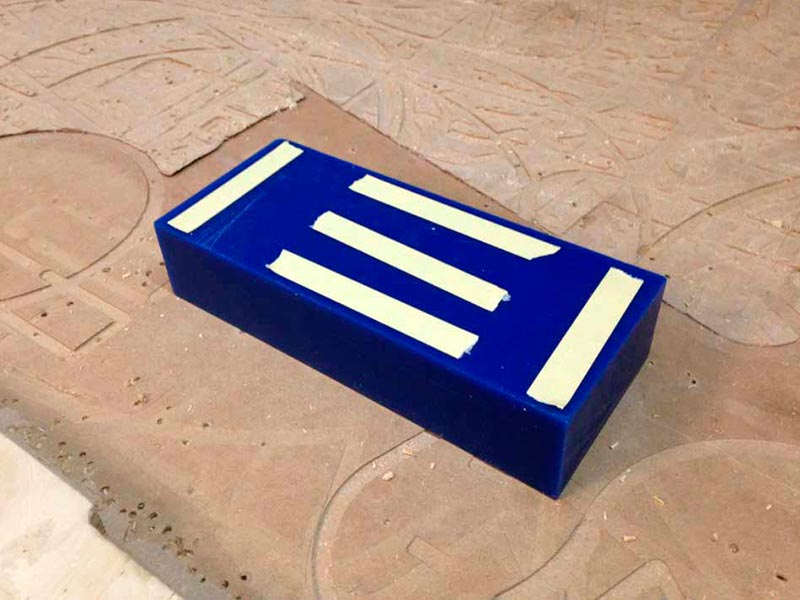
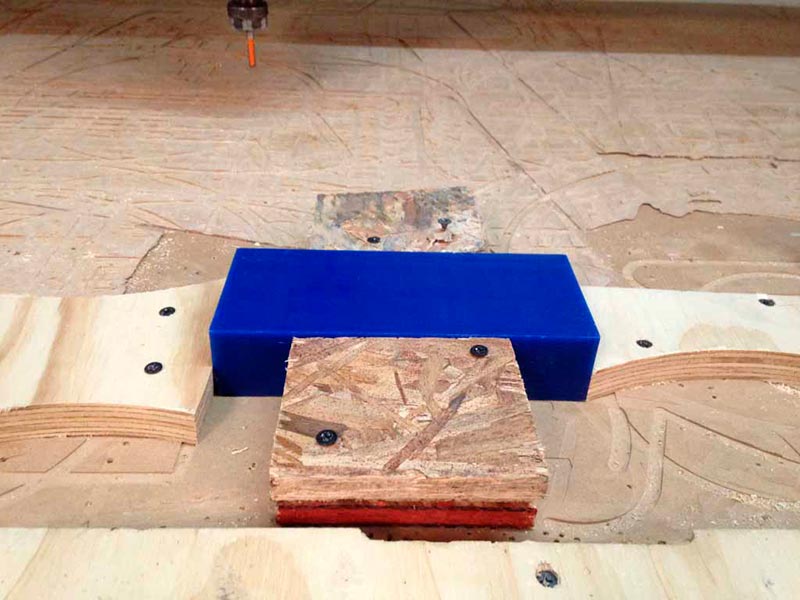
With the first toolpath, there was a lot of waste of the wax; I decided to save the waste for the jewellery area of the fab lab.
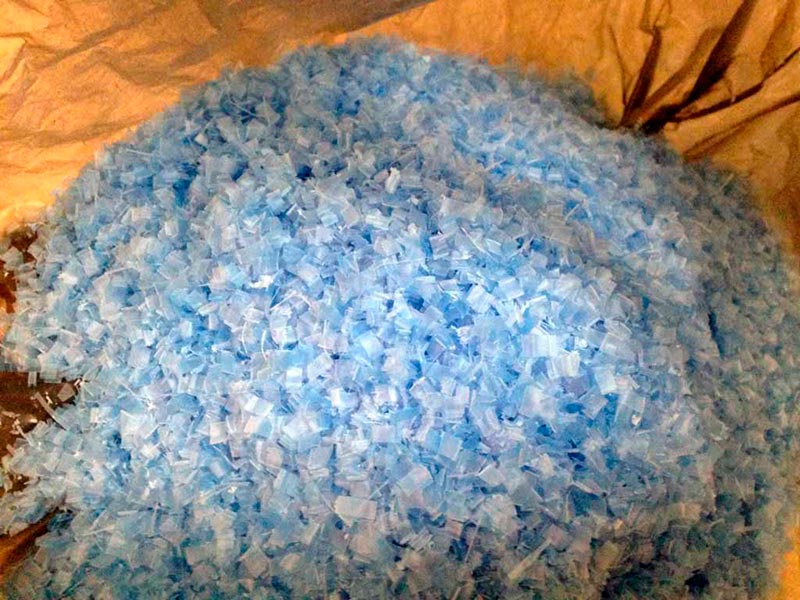
The wood blocks and the double sided tape work, and the wax didn’t move when I start with the rought cut.
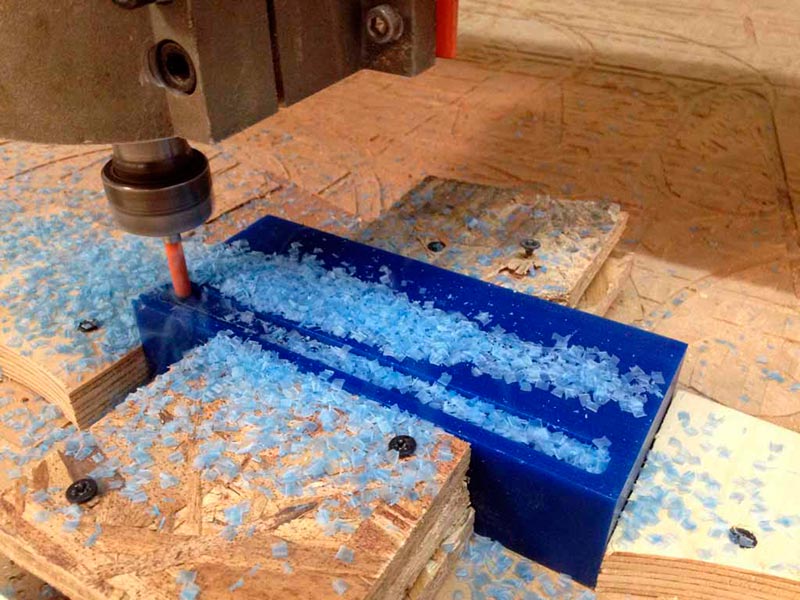
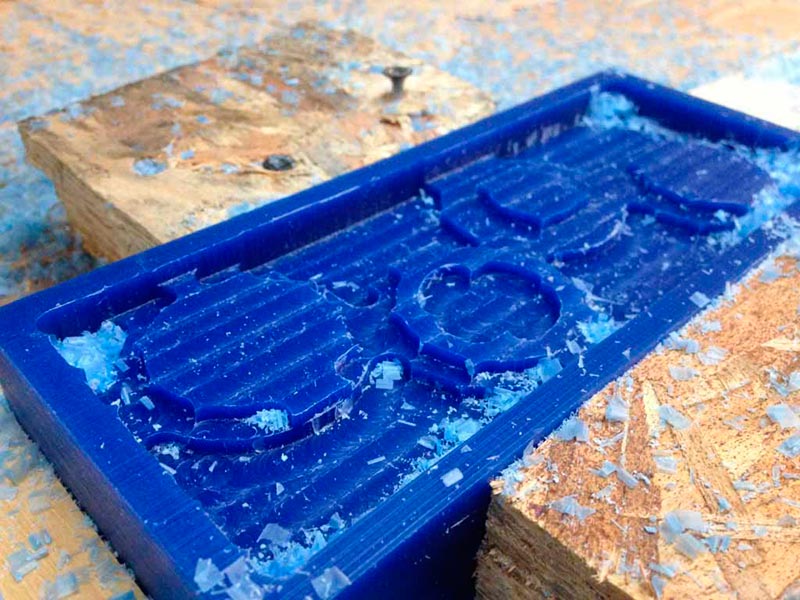
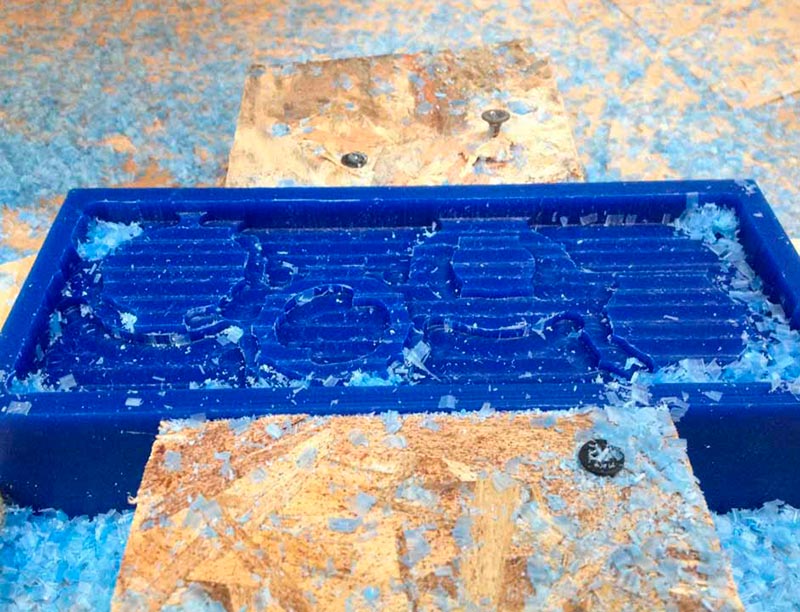
I change the end mill and continue with the next toolpaths (horizontally and vertically). I was very satisfied with the results of the machining.
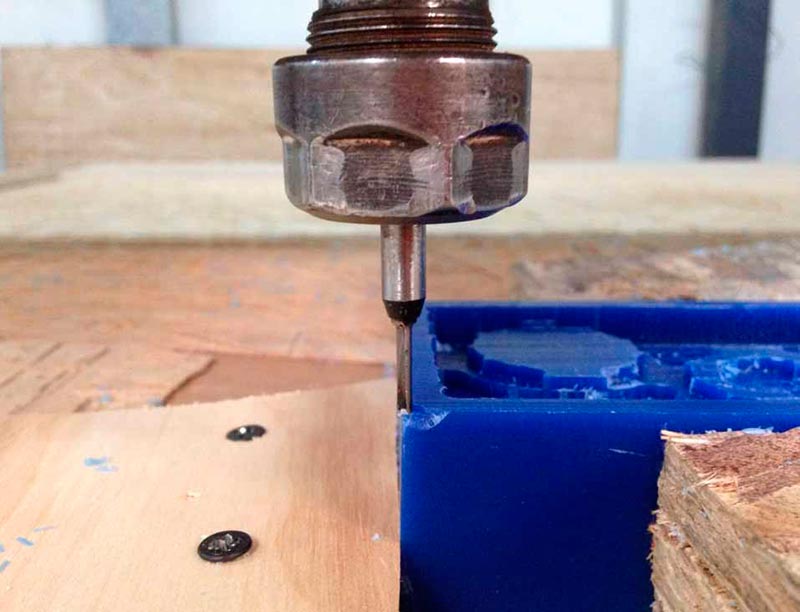
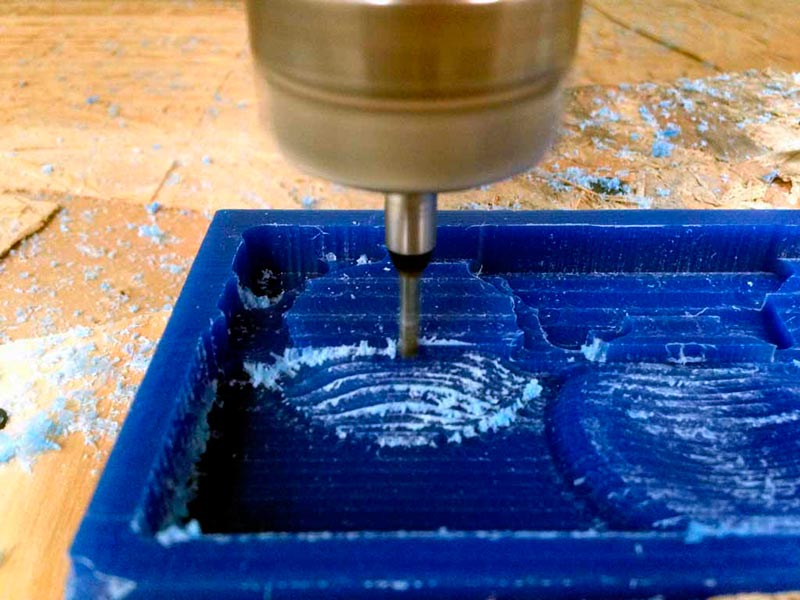
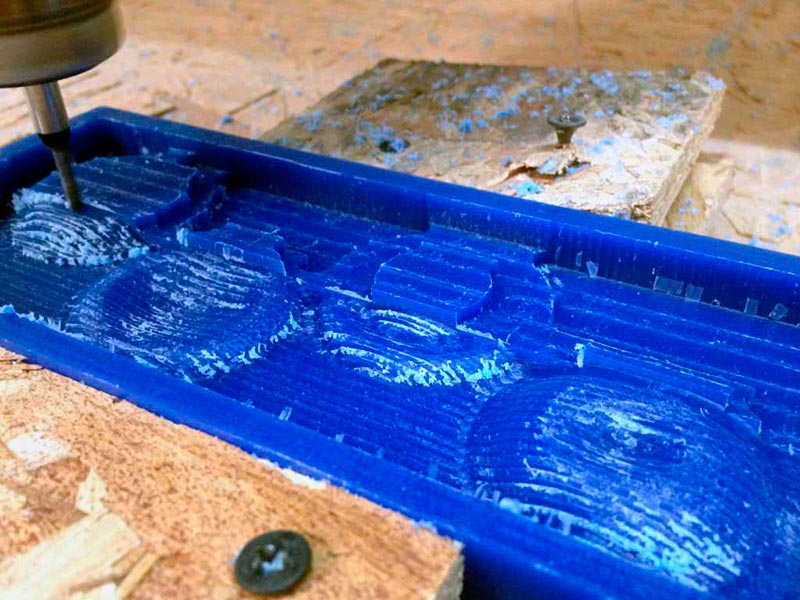
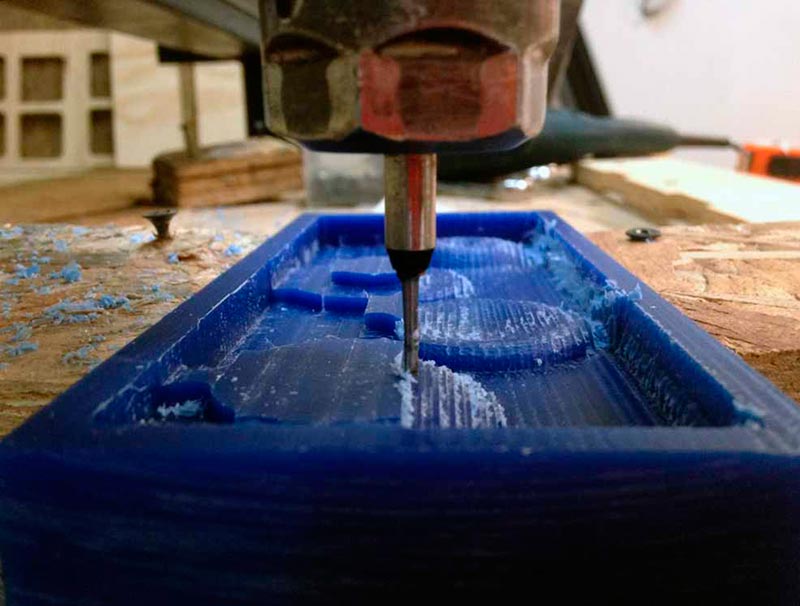
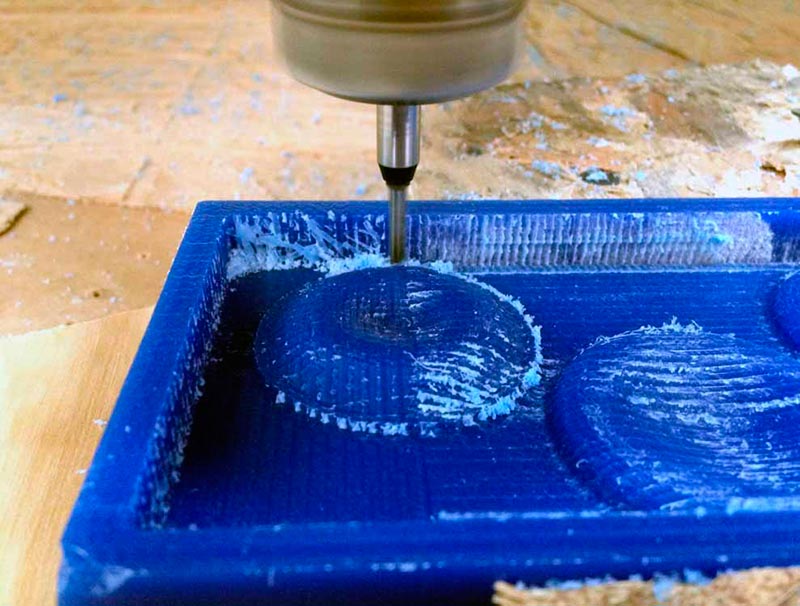
I had never cut in wax, I the smoother finish that you can achieve. Also, I like that you can notice more the difference between the conventional or climb cutting, something that in wood sometimes is not very easy to observe.
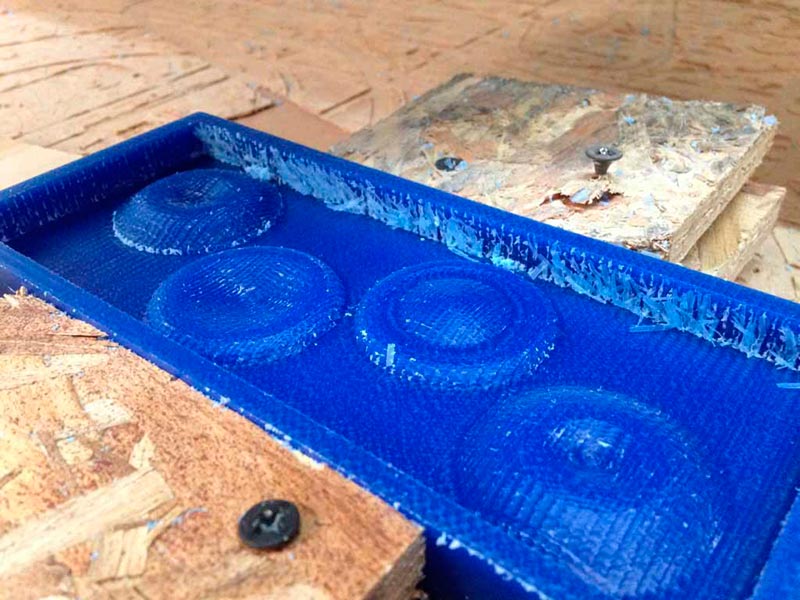
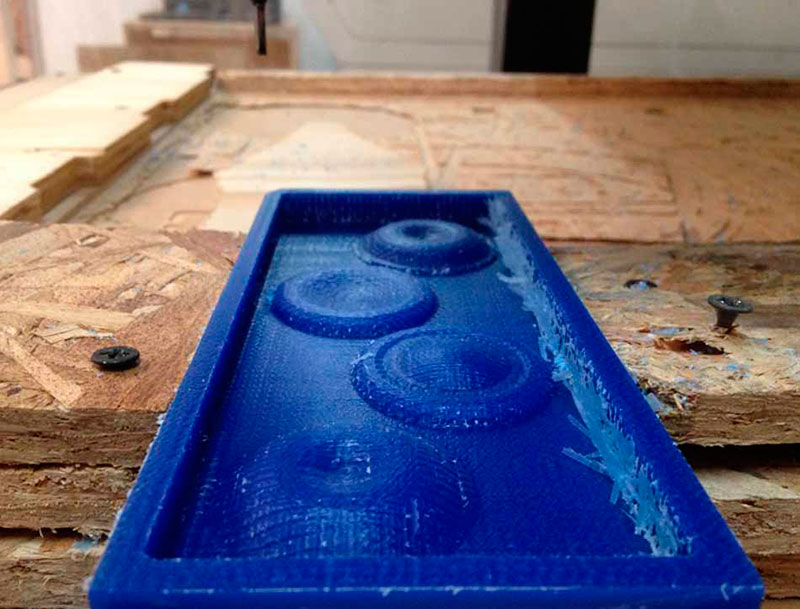
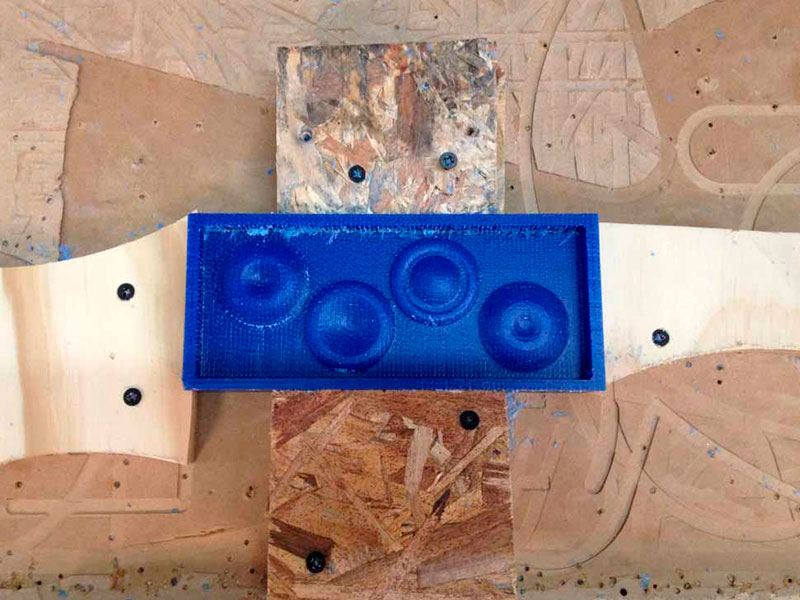
SILICONE MOLD
For my individual moulding and casting, I use a Low Viscosity Tin-Cure Silicone Rubber that I bought in Plastiquímica. I review the datasheet to understand how to use it, where I follow the instructions to prepare my model, measure & mix, pouring and - finally - curing.
Following the instructions, I also had to wear safety glasses, long sleeves and rubber gloves to minimize contamination risk.
The rubber silicone contains 1 Kl of silicone and 100 gr of the catalyst. The proportion of quantities to be able to make the mould is 10: 1 (silicone: catalyst).
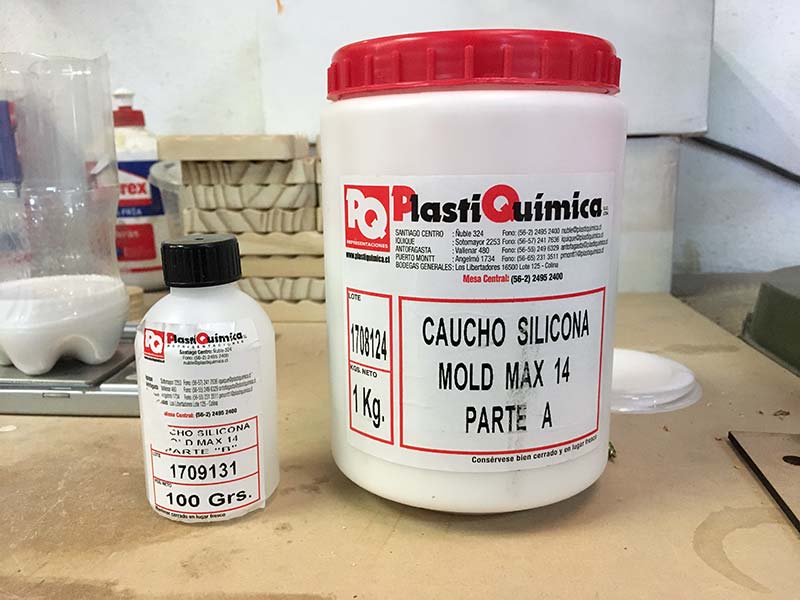
So, I first fill with water my wax to calculate how much silicone I need. I use 135 gr of silicone, and 13 gr of the catalyst.
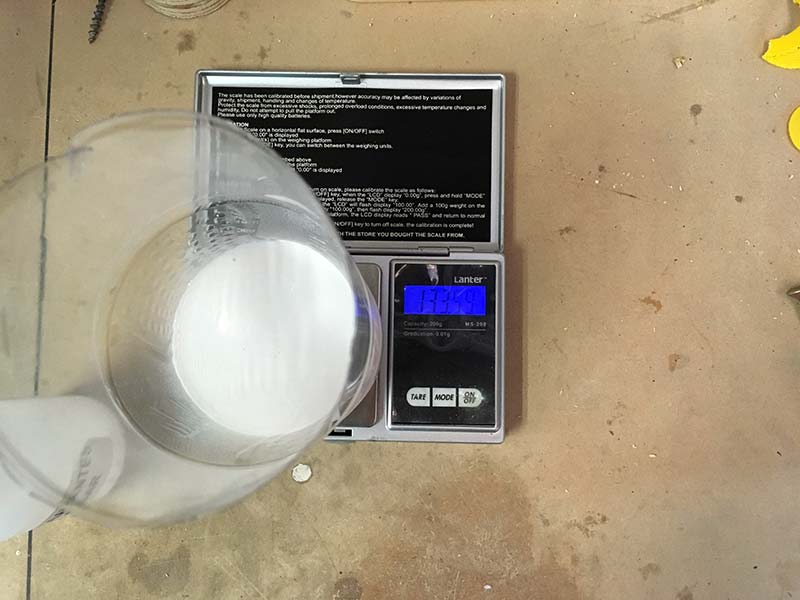

I turned it around for five minutes, worrying about it being very mixed. Then I put it in the mould.
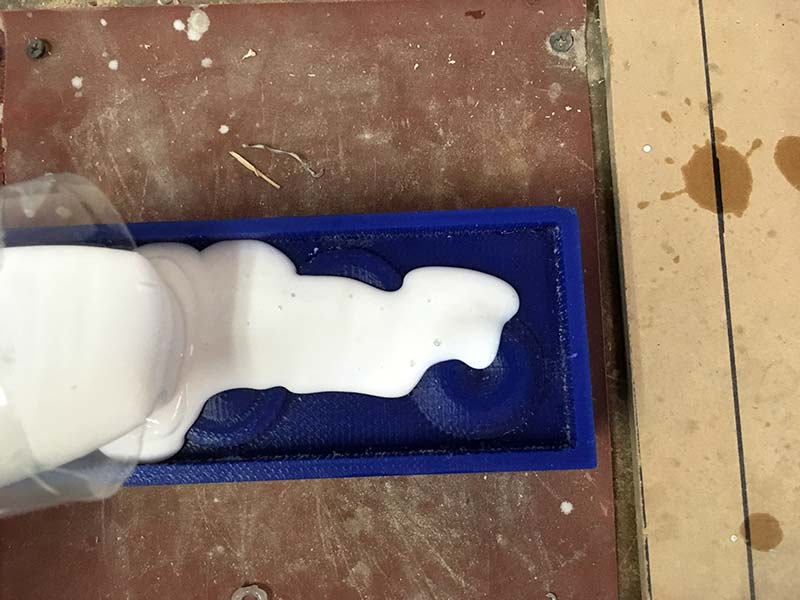
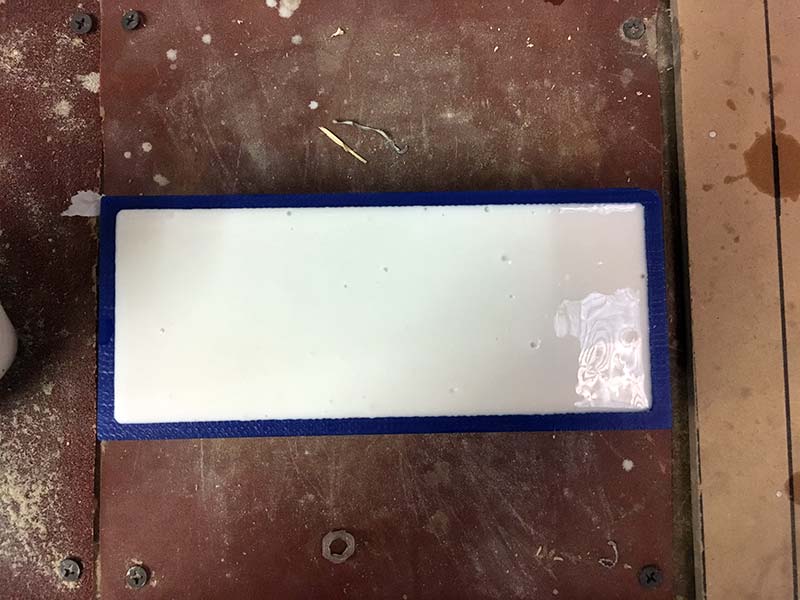
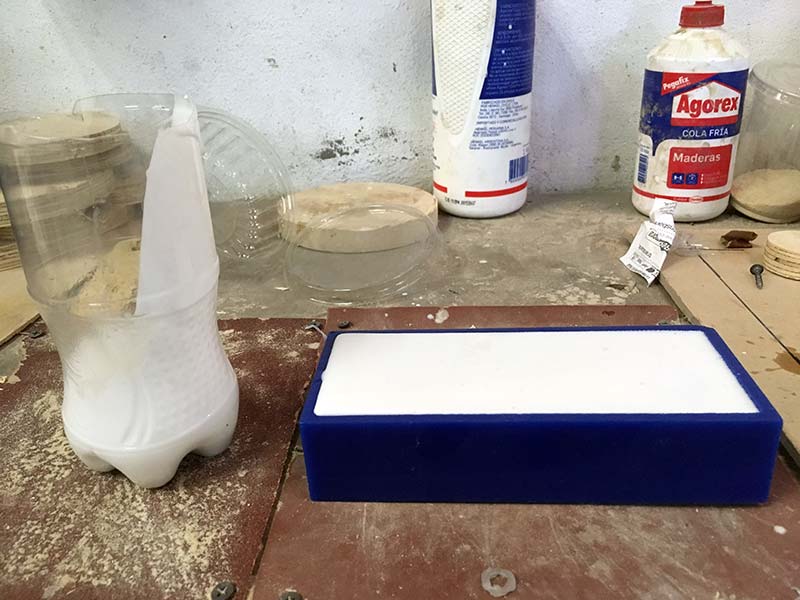
This silicone catalyzes in four hours. I made the mixture during the morning and in the afternoon I was ready.
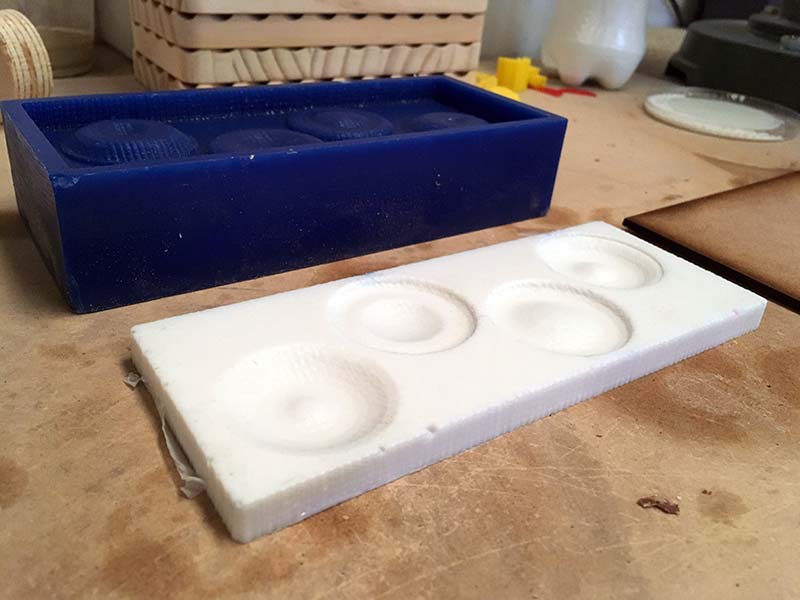
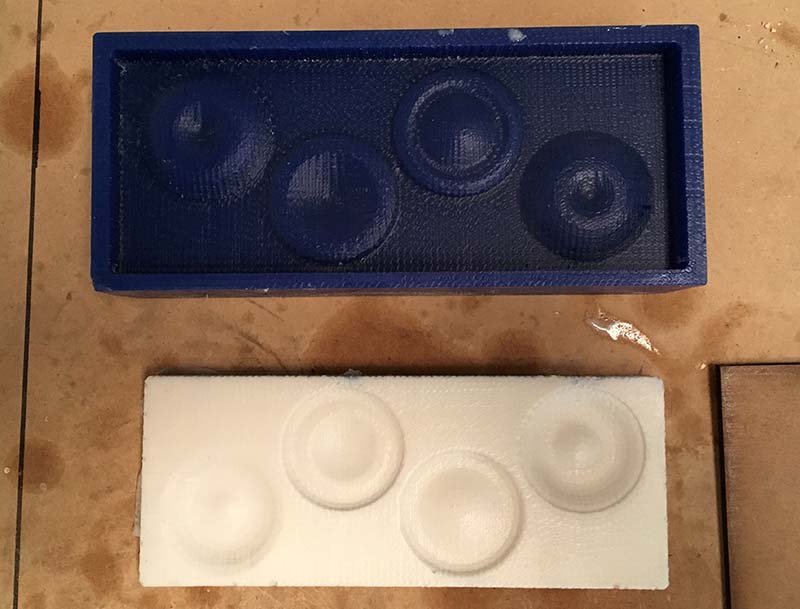
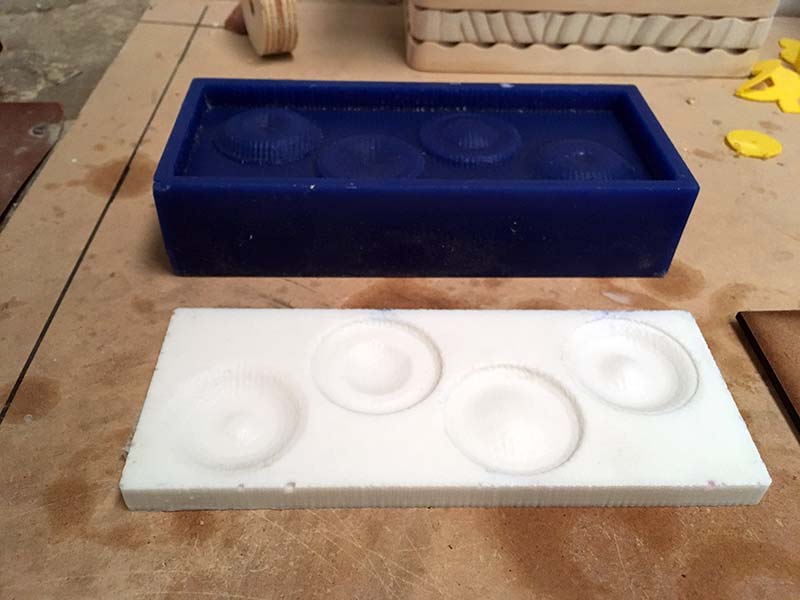
To test the buttons that I designed, I took advantage of filling the mould with the bioplastic that I am using for wildcard week (I had fallen behind in this assignment because I did not have the silicone).
The bioplastic that I made is composed of glycerin, jelly without flavour, water and cork. To review the exact composition and process of the bioplastic revise Wildcard Week.
BUTTONS
These are the tests I did in bioplastic with the mould:
(for more details of the recipes, check on Wildcard Week)
Test 1
Recipe:
- 240 ml Water
- 40 ml Unflavored gelatin
- 15 ml Glycerin
- 1/2 cup Cork
I made the bioplastic on Friday and I left the mixture to catalyze during the weekend.
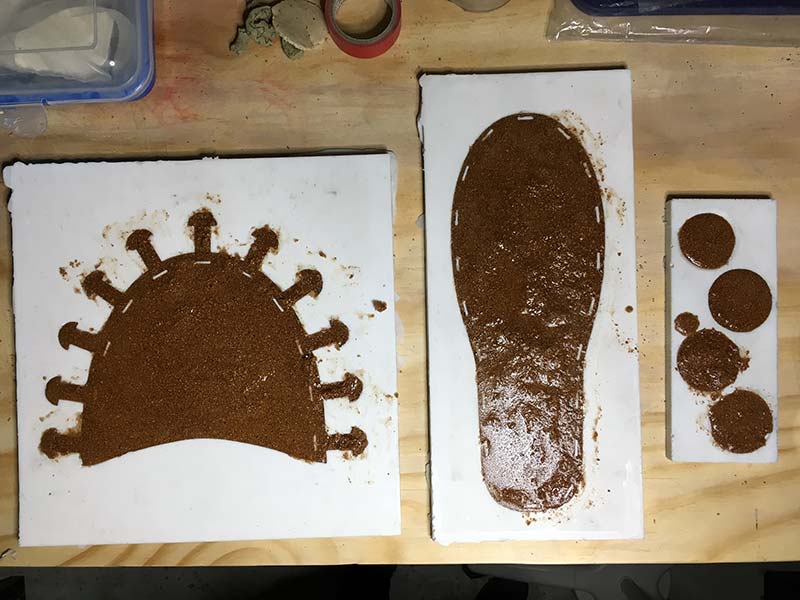
Test 1 results:
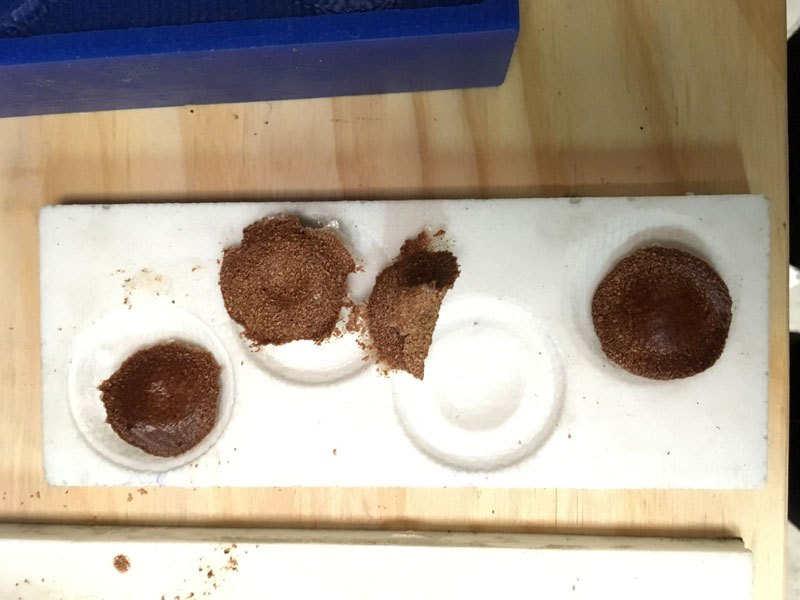
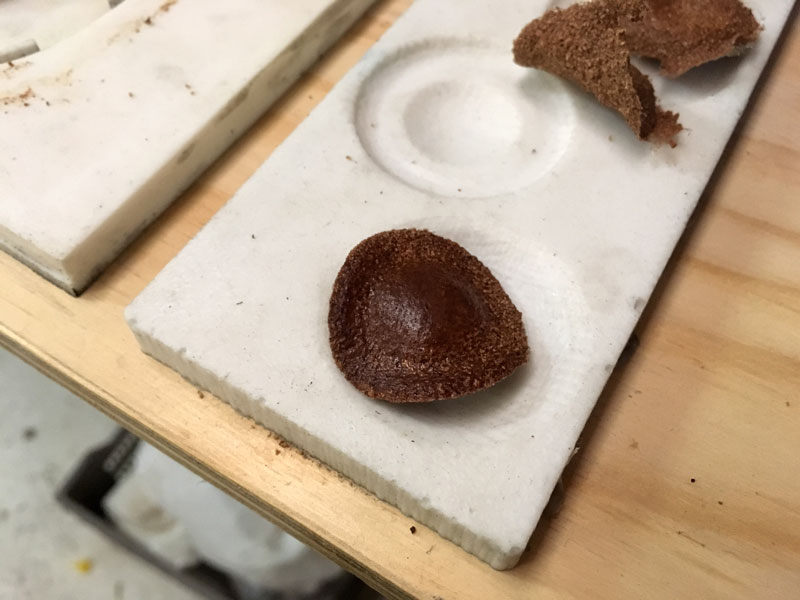
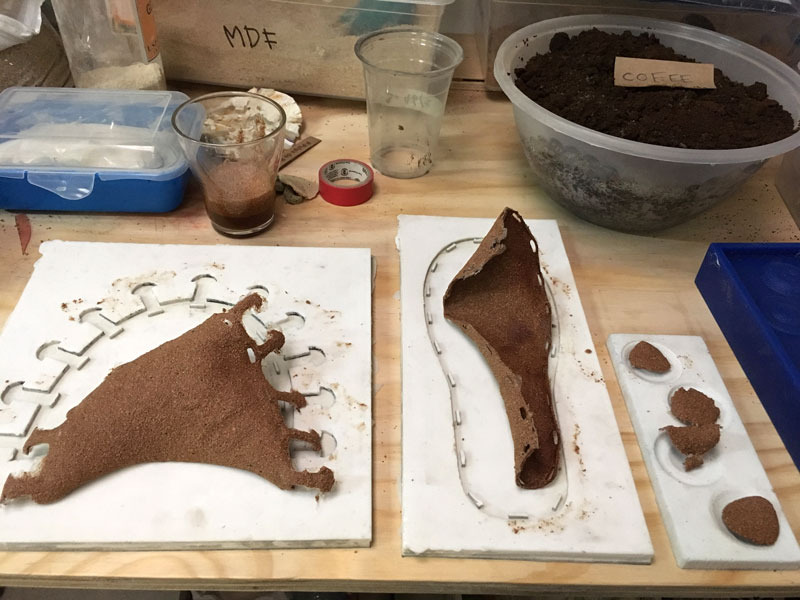
Test 2
Recipe:
- 240 ml Water
- 40 ml Unflavored gelatin
- 15 ml Glycerin
- 1/8 cup Coffee
The two on the left of the mould:
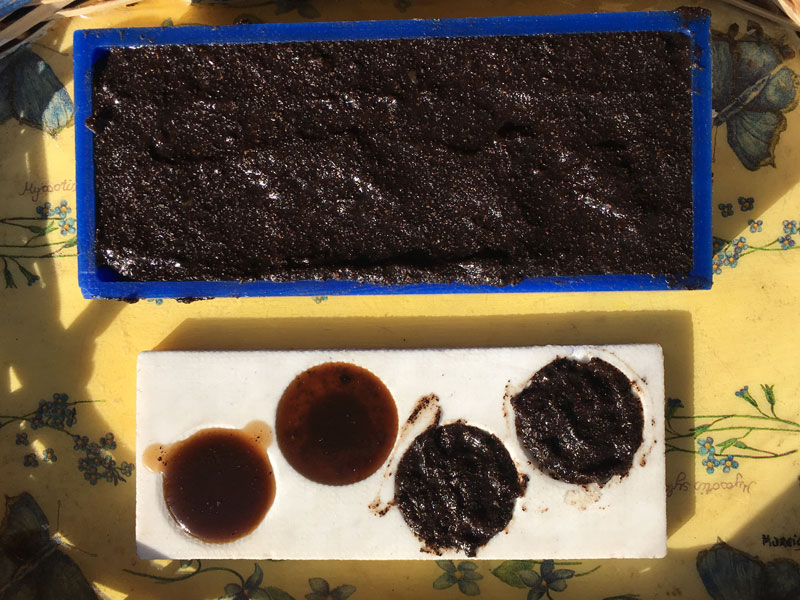
Test 2 results:
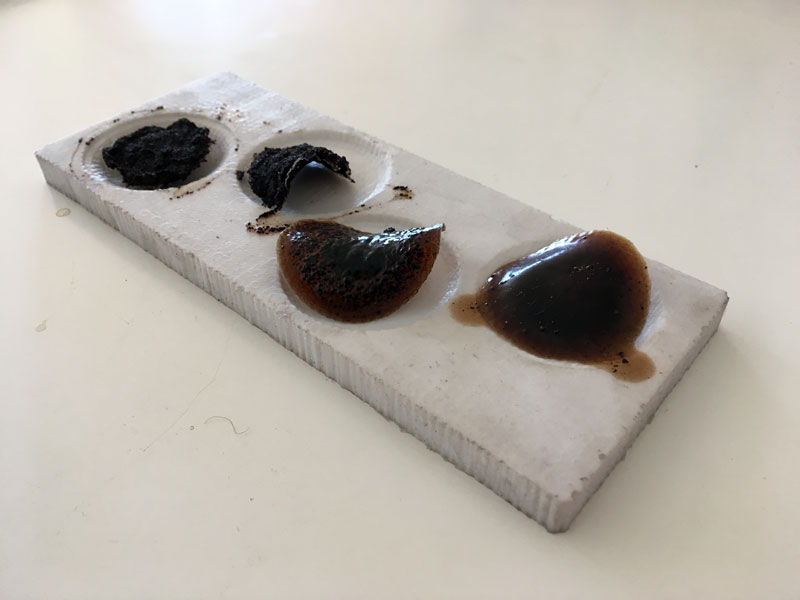
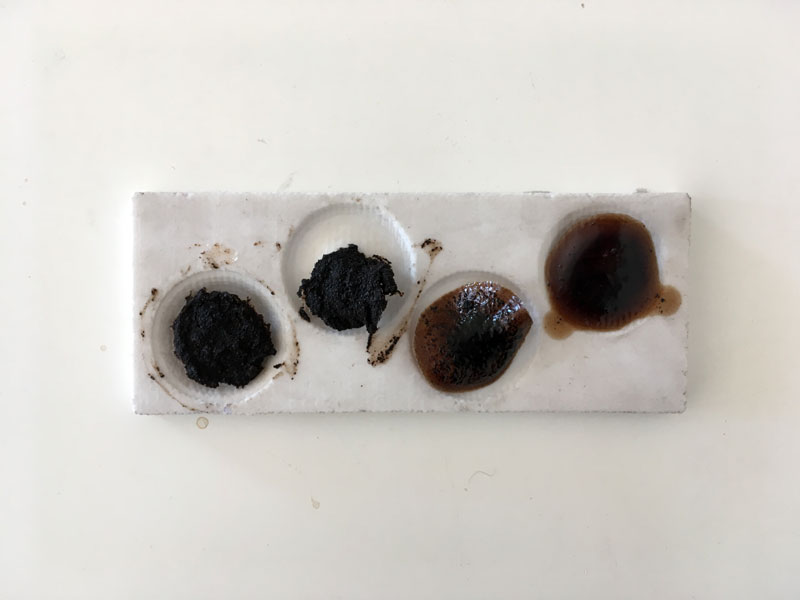
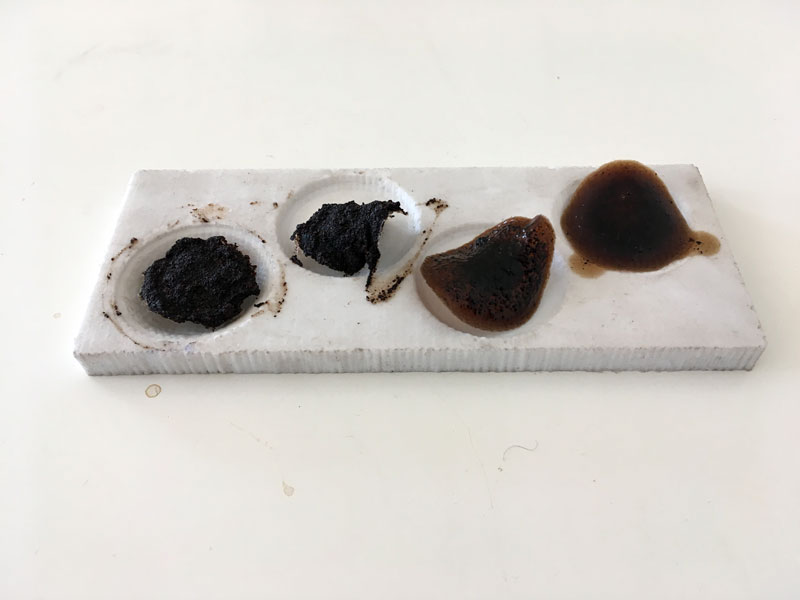
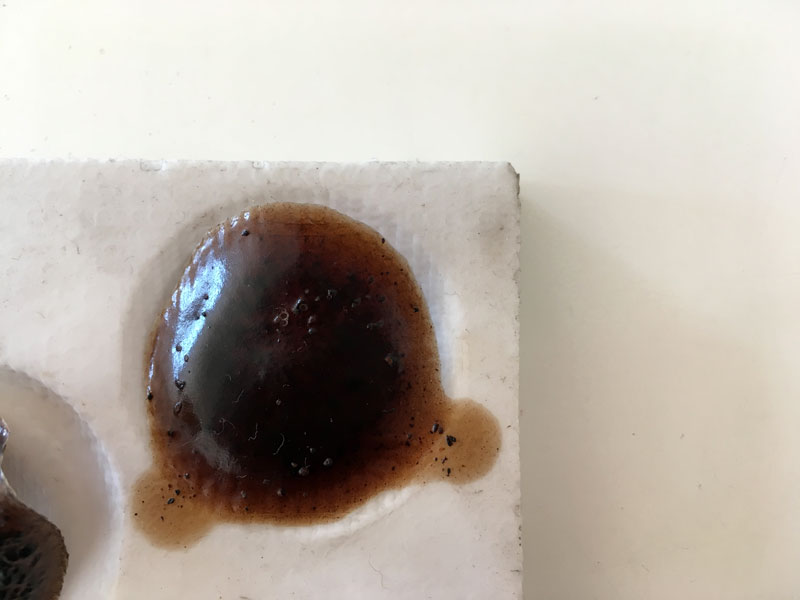
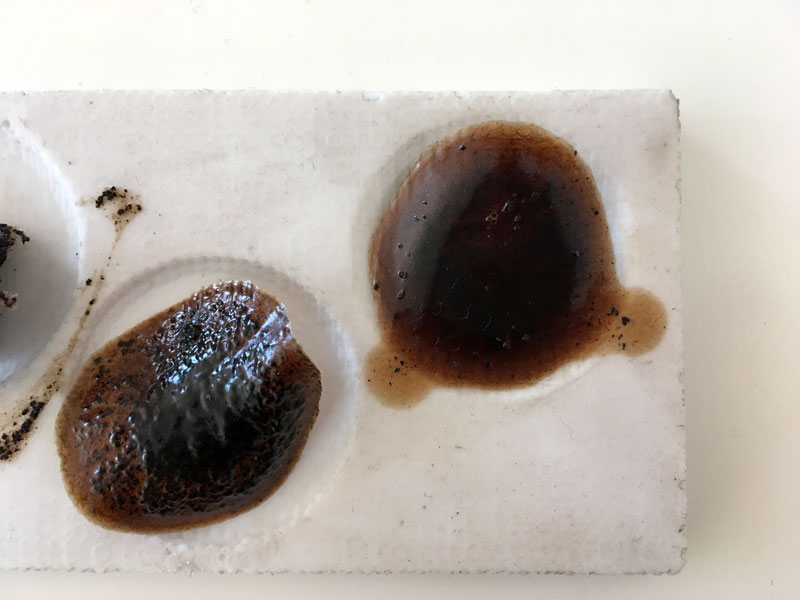
Test 3
Recipe:
- 320ml Water
- 50 ml Vinegar
- 75 ml Cornstarch
- 25 ml Glycerin
- 1 cup Coffee
The two on the right of the mould:
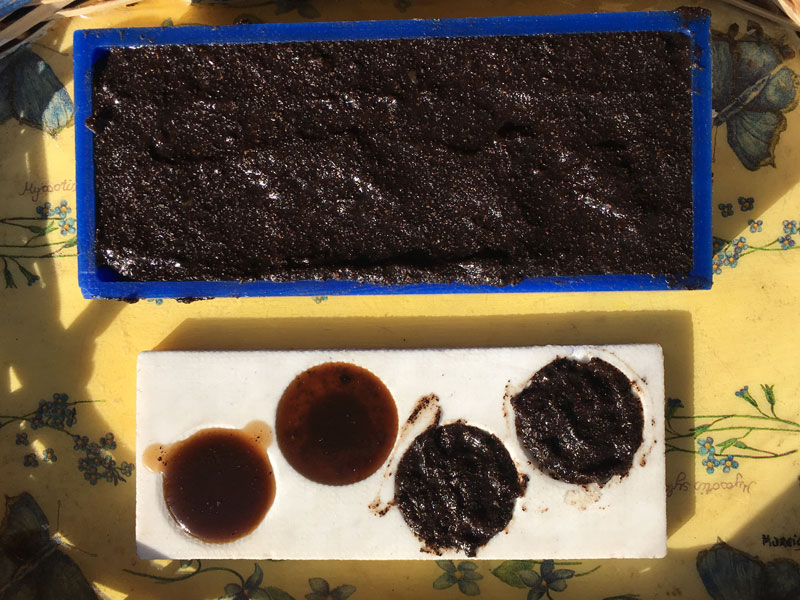
Test 3 results:
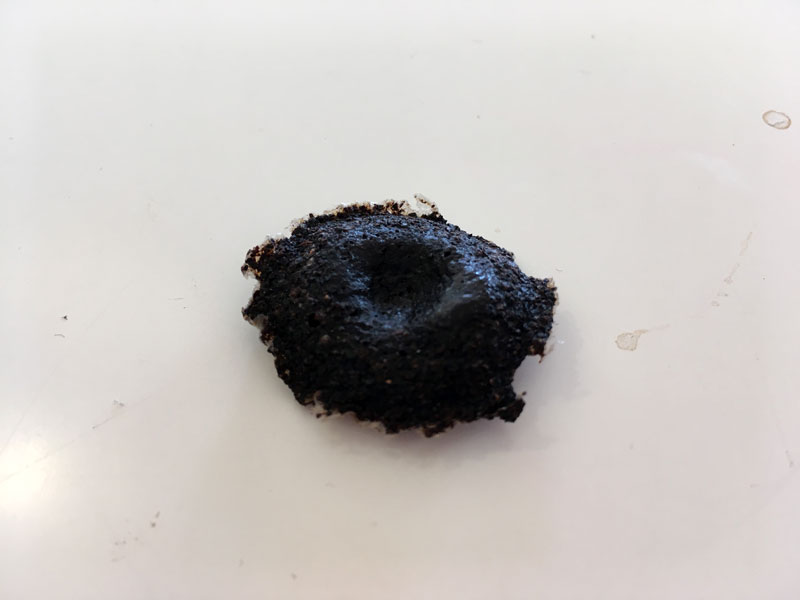
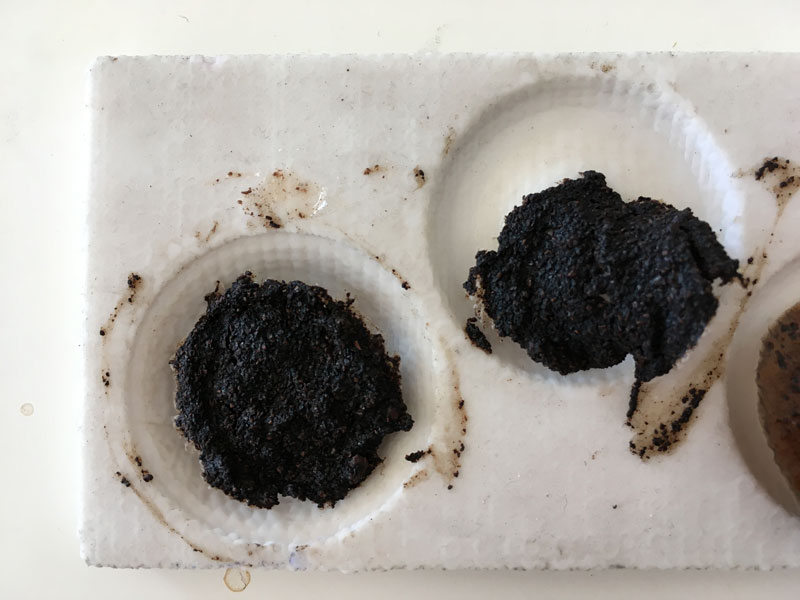
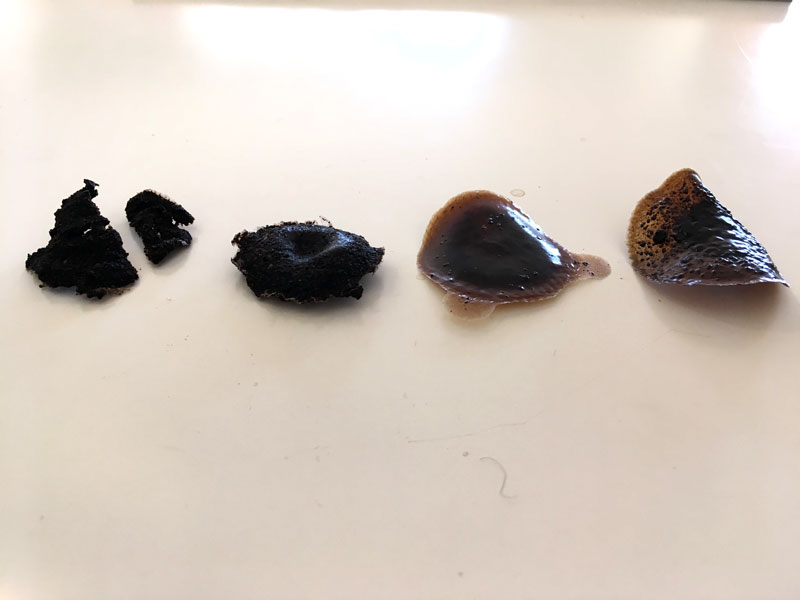
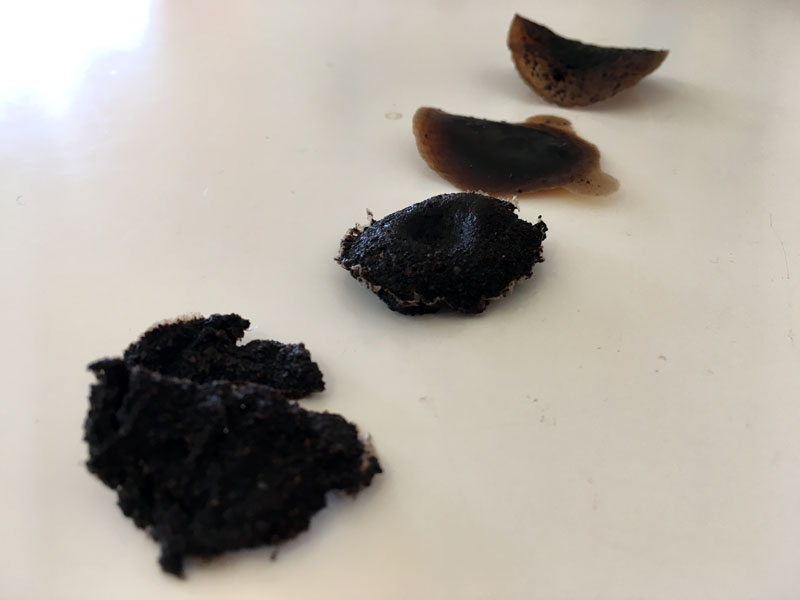
Test 4 | Back to basic
Recipe:
- 200 ml Water
- 20 ml Unflavored gelatin
- 20 ml Glycerin
In this test, I decided to simplify the recipe and just use the essential to make the bioplastic: Glycerin, jelly without flavour & water.
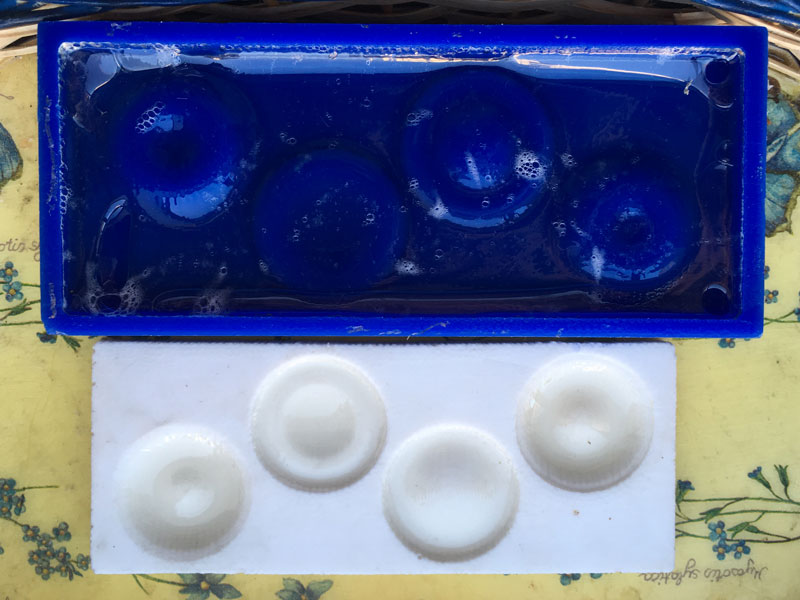
Test 4 results:
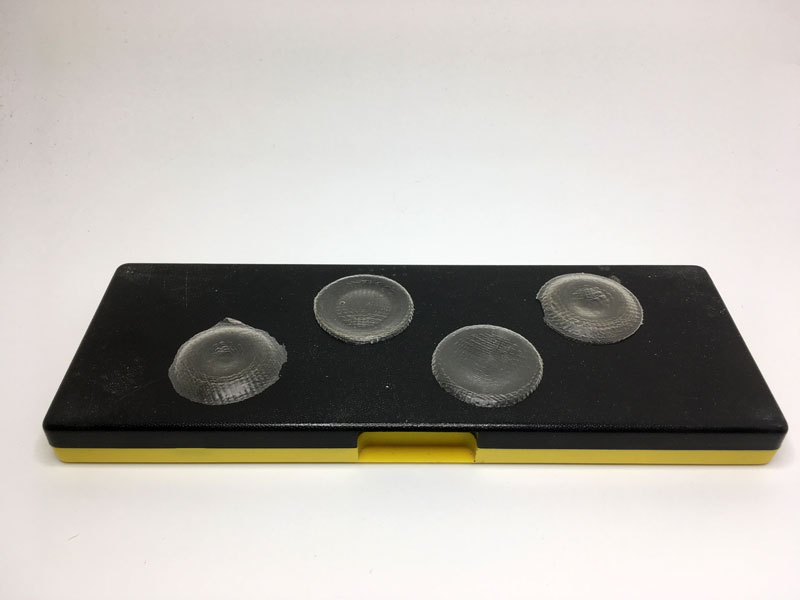

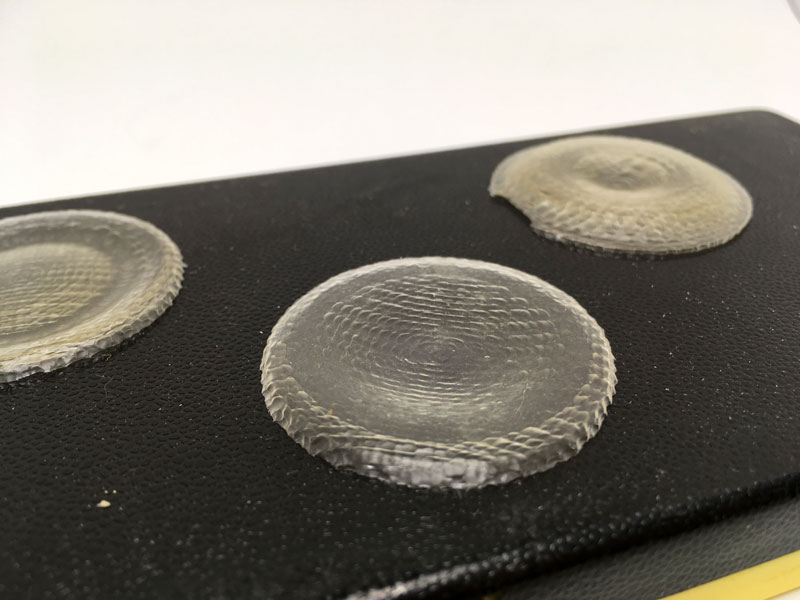
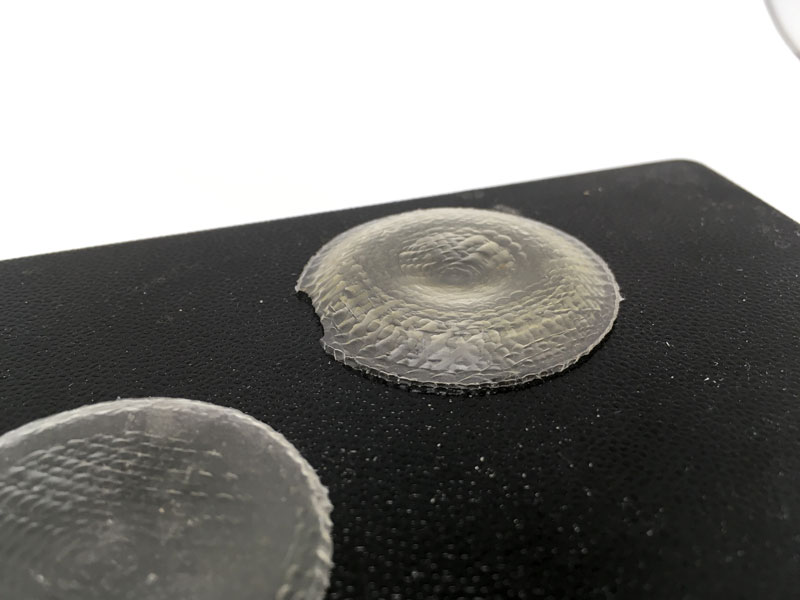
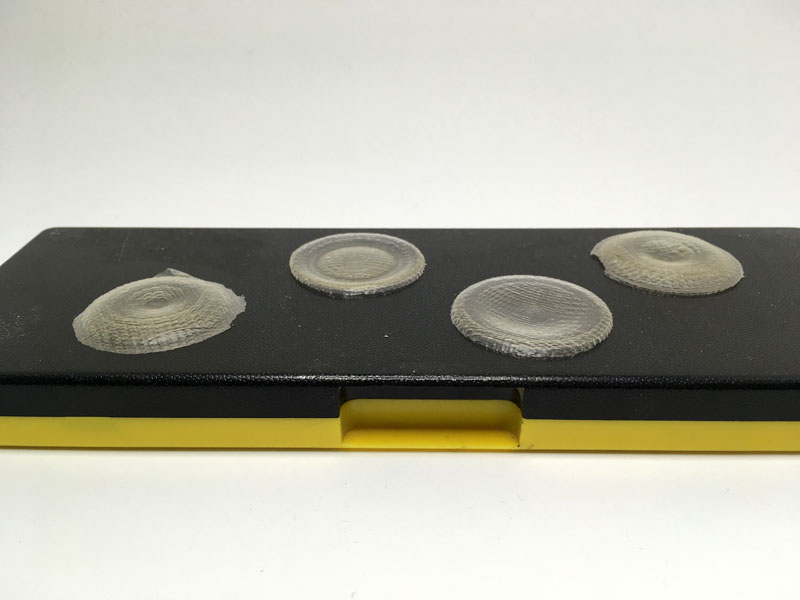
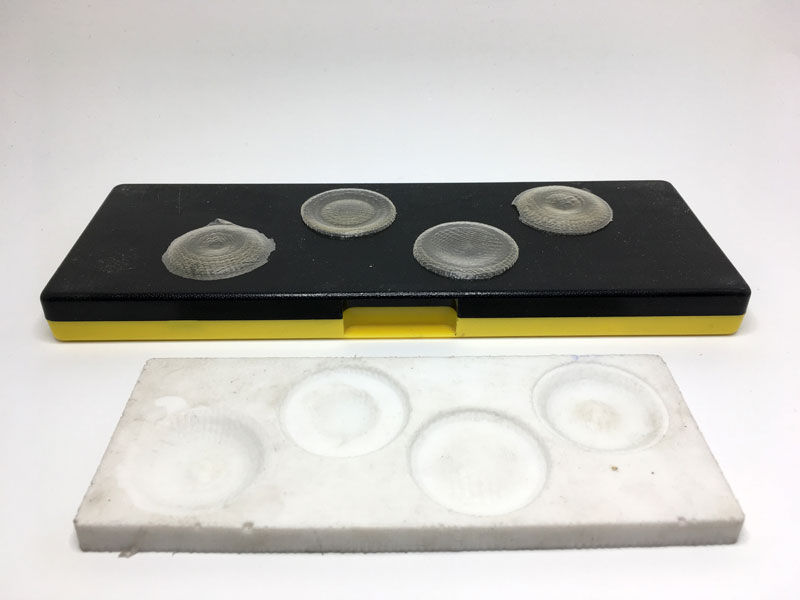
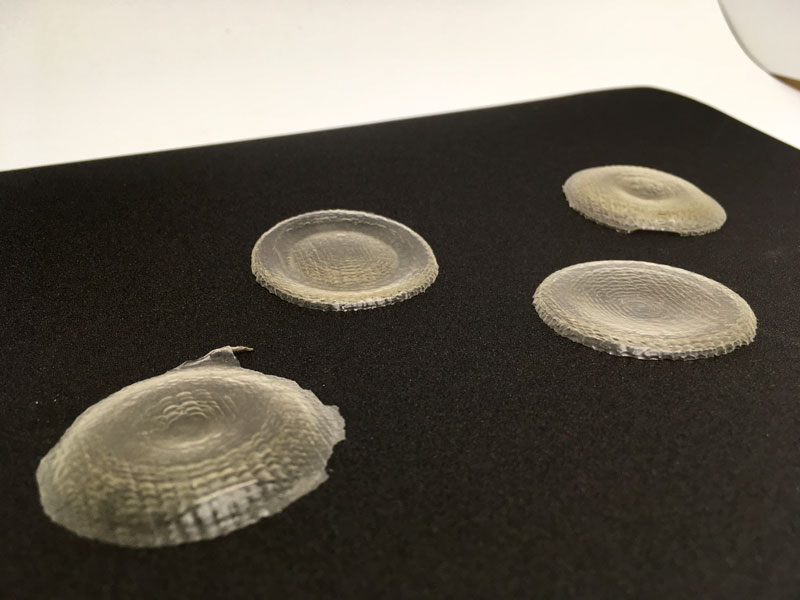
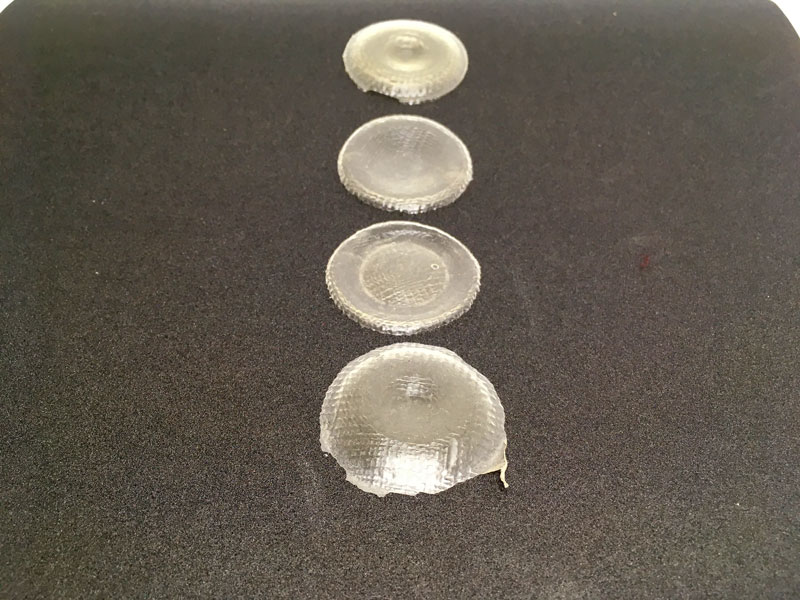
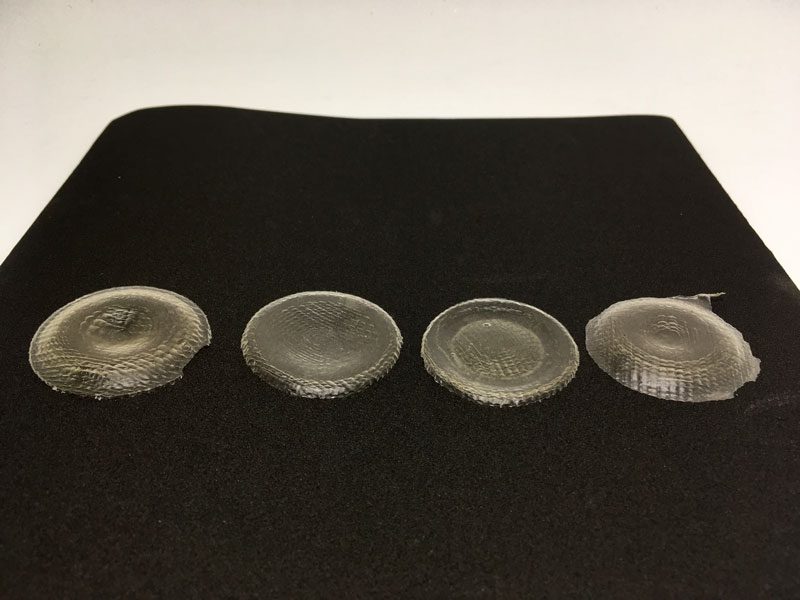
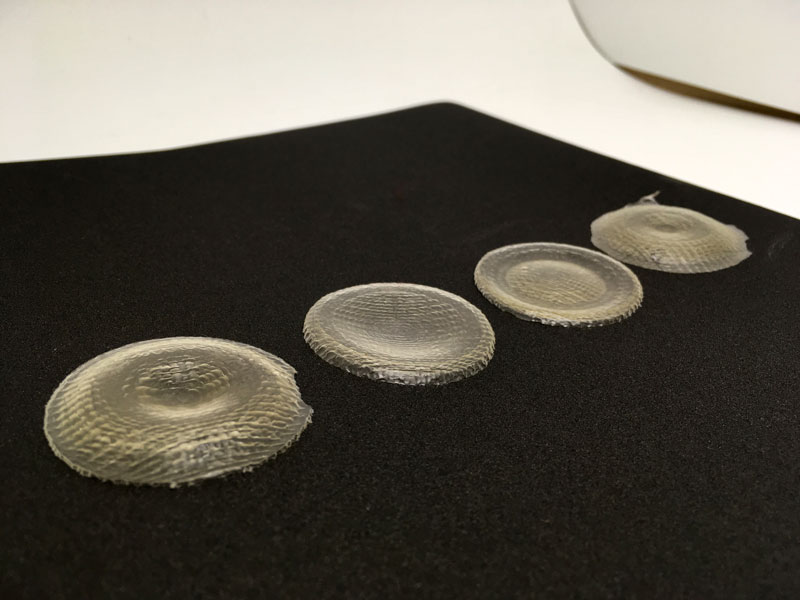
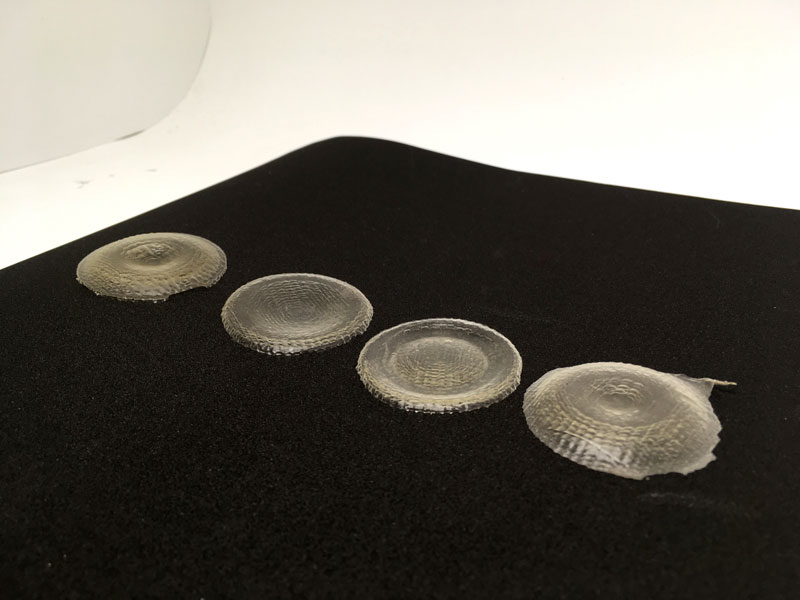
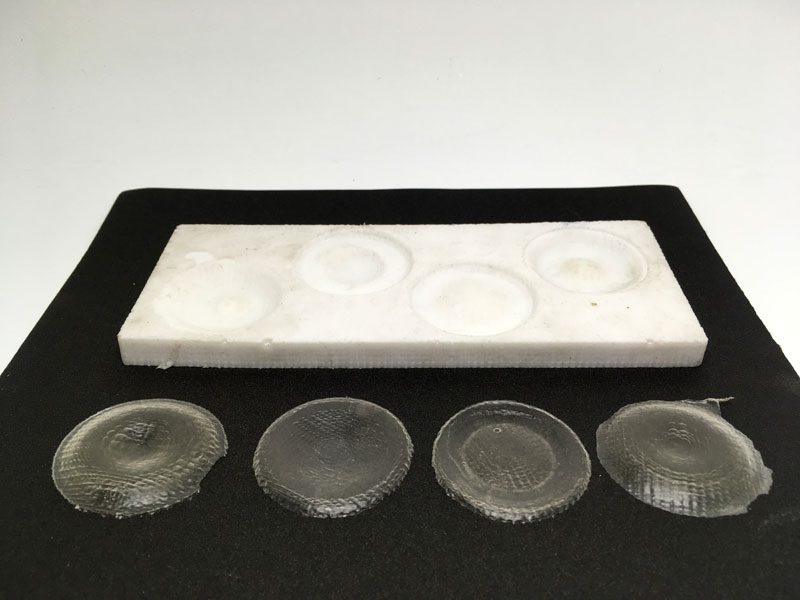

Este obra está bajo una licencia de Creative Commons Reconocimiento-NoComercial-CompartirIgual 4.0 Internacional.