The task of this week was: Make the FabISP in circuit programmer. I was asked to mill, stuff and program the Fab ISP board, The FabISP is an in-system programmer for AVR microcontrollers, designed for production within a FabLab. This task which allows to program brand new AVR microcontrollers with the desired firmware.
FAB ISP
The FAB ISP design we decided to build in the lab is the Neil’s version. The first thing we do is install the Fabmodules, for this we continue the tutorial of Anna Kaziunas
A. Milling the board
I milled the board starting from the PNG design available on the class webpage, using the Fab Modules on the lab’s Roland MDX-20 Modela mill. I never used such tool before so took some time to understand its operation, especially regarding the homing and fitting the different milling bits for proper operation. The process was quite straightforward, and the integration with fab modules made it very smooth.
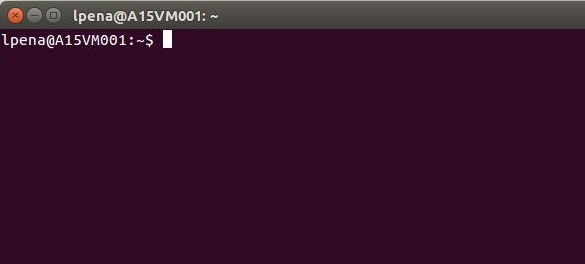
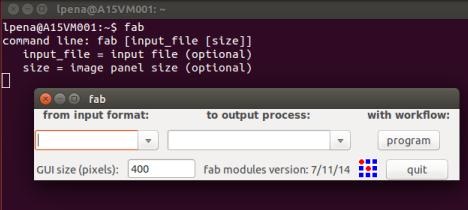
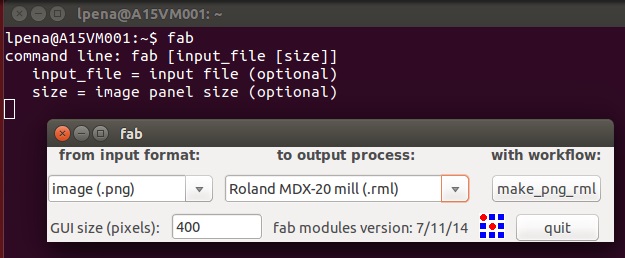
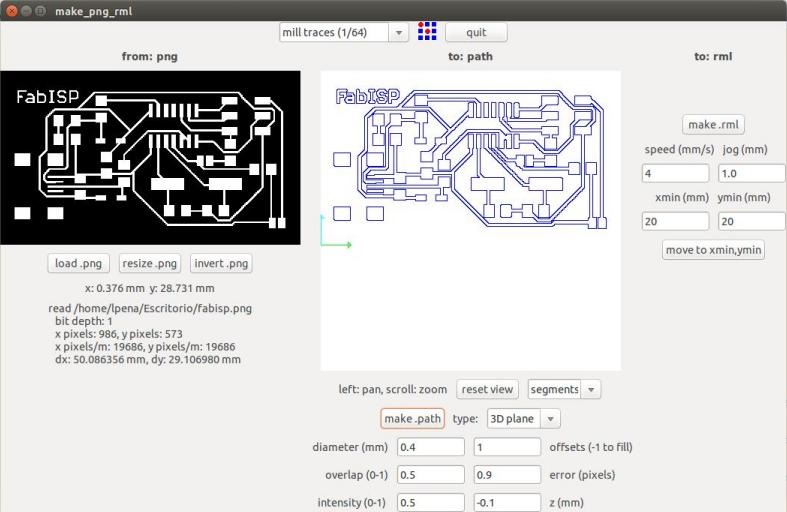
For milling the traces I used the 1/64’’ inch bit, while for cutting out the board I used the 1/32’’ inch bits. The machine settings I used are:
- Speed 4, Jog Height 1.0 for milling the traces
- Speed 2, Jog Height 1.8 for cutting the board
I experimented with different settings for the jog height, homing the mill in different places of the board to get the lowest possible setting. This finally resulted in a properly milled board. A very interesting fact is that even after several times switching to view mode, and milling attempts the Modela totally respected the homing coordinates, resulting in no displacement of the resulting traces. Cutting out the board took almost the same procedure, and worked quite immediately. This was done by removing the wooden block and putting under the milled board another sheet instead, which made the calibration process much easier thanks to the uniform surface.
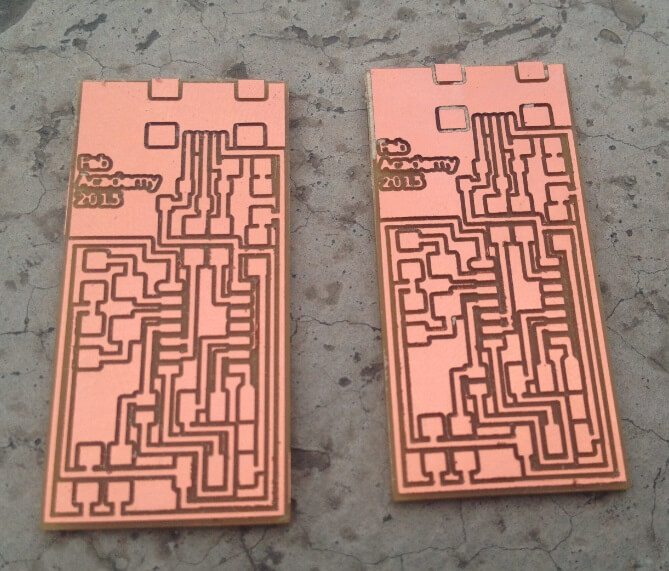