Composites
This week assignment was to design and make a 3D mold and produce a fiber composite part in it. For this task I decided to make a Paleta frontón, Paleta frontón is a Peruvian sport that was born in the capital, Lima, in 1945. This sport has its roots in the "pelota vasca" brought by the Spanish conquerors, and the domestic "pelota mano", called "handball" at that time due to English influence. Paleta is typically played on the higheat peaks of their mountainous terrain.
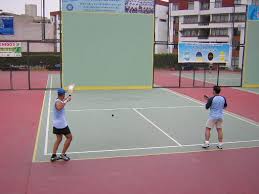
A. Design and cuts
The process plan for manufacturing the paleta frontón is as follows: • Design autocad shape paleta frontón in two dimensions, to keep in DXF format • CNC Court in a mold in HDPE 18 mm thick with the shape of the shaped blade inside, along with a tab that serves to placing a lid on top and also define the thickness paleta frontón that I believe in 14 mm. • Cut in a mold CNC acrylic 10 mm thick with the shape of the blade including the width of the tab that serve as cover. • CNC Court in a rectangular piece 3mm acrylic serve as the basis of the main cast. • Cutting the CNC acrylic mold 3 mm thick in the shape of paleta frontón minus 2.5 mm to serve to cut the gasket to form the interior of the pallet. • Cut fabric fiberglass increasing 14 mm to how to shape the edges of the paleta frontón, with this form 3 piece cut. • Cutting the glass fiber fabric according to the shape of the pallet to place at the top, with this form three pieces are cut. • Cutting the FRISA 10 mm thick acrylic in the mold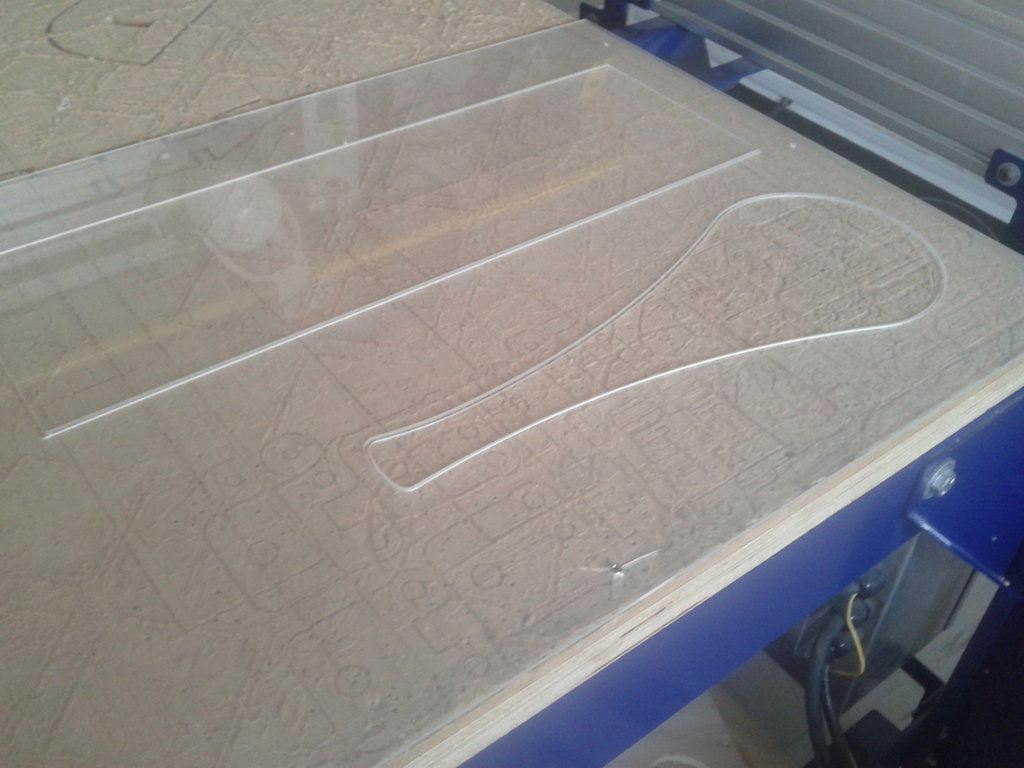
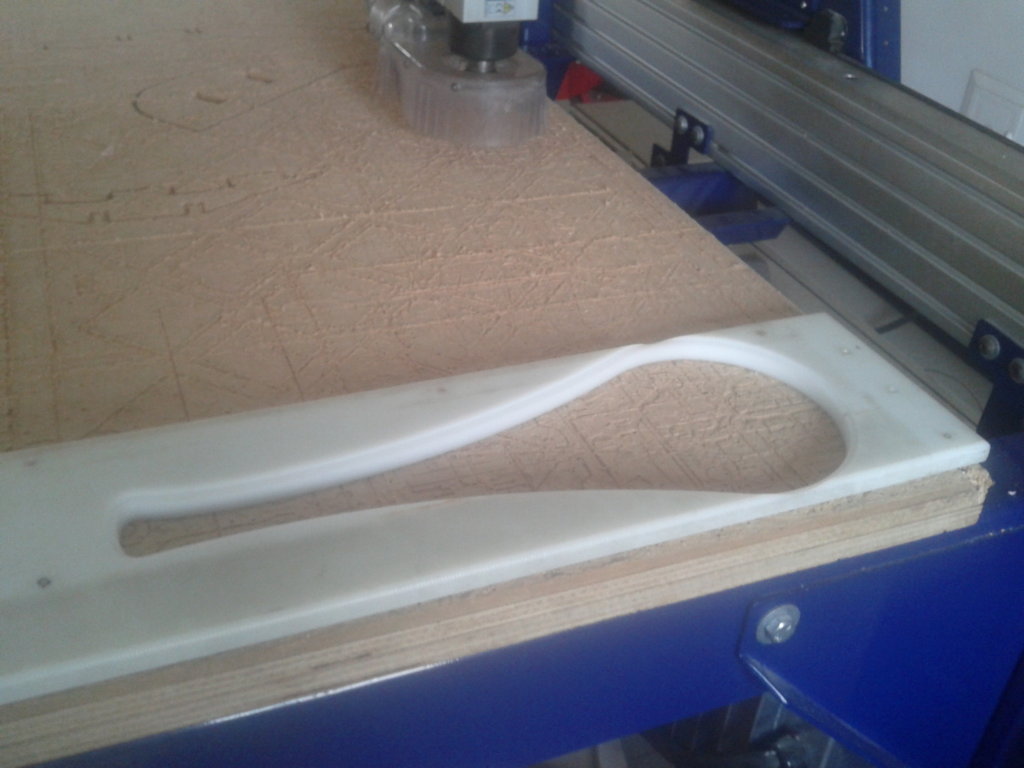
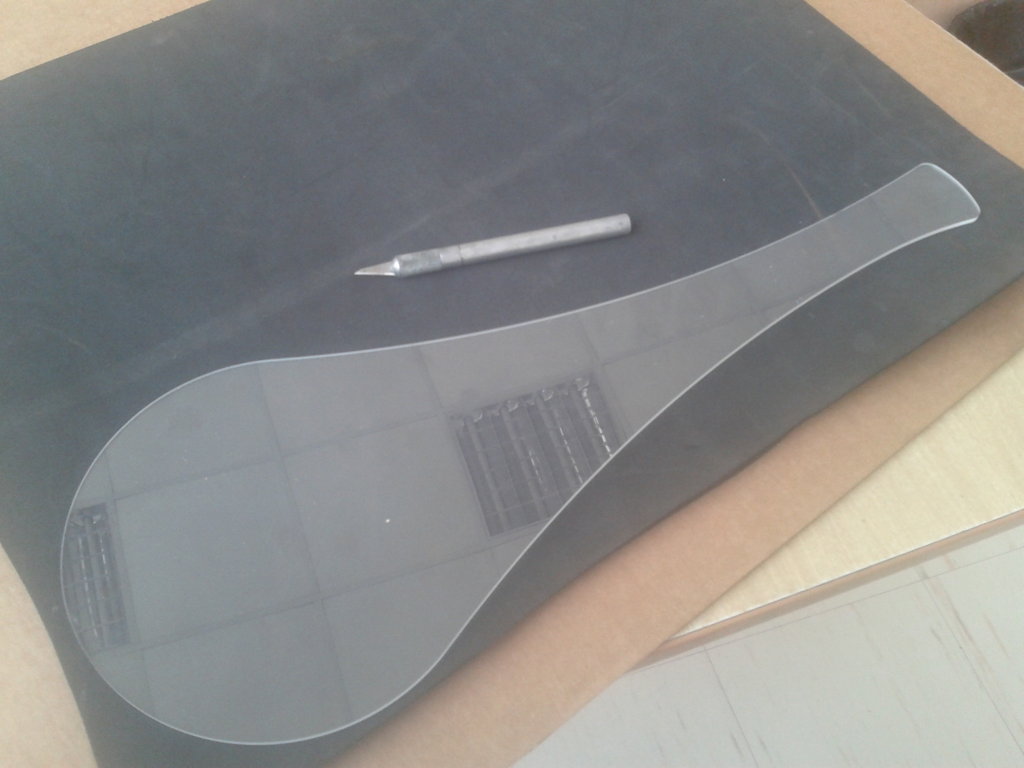
B. Manufacture
The main cast in polyethylene and acrylic base put together by the press and apply mold release wax leaving them dry and repeat the action. I applied a layer of resin POXBAK 1206 mixered with catalyst ratio 100: 20 weight. On the basis and the inner edges of the mold and place the first layer of fiberglass cloth arranging it evenly, repeating the action until placed 3 glass fiber layers at the base.The gasket 10 mm thick was placed and followed by the application of alternating layers of fiberglass resin to place the three layers of the top. Acrylic lid previously greased with release agent wax and pressed causing any excess resin is spread over the desired height was placed.The frame was allowed to stand for curing the resin is performed approximately 24 hours. It is demolded with relative ease the frame and the palette to which you had to remove residual fiber was also was found in the upper face small areas where needed complete the atura resin.The corresponding filling was made and allowed to dry for 4 hours and then sanding and smoothing the edges.accessory elements as EVA foam was placed anatomical shape for the handle of the trowel and the corresponding grip halyard.
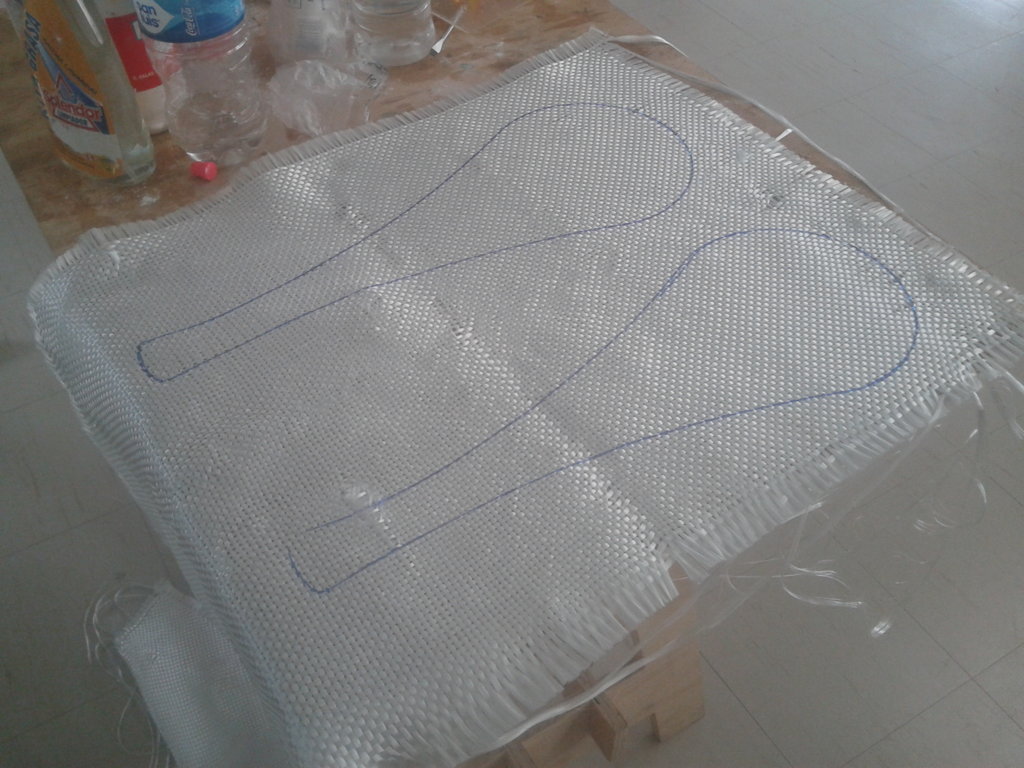
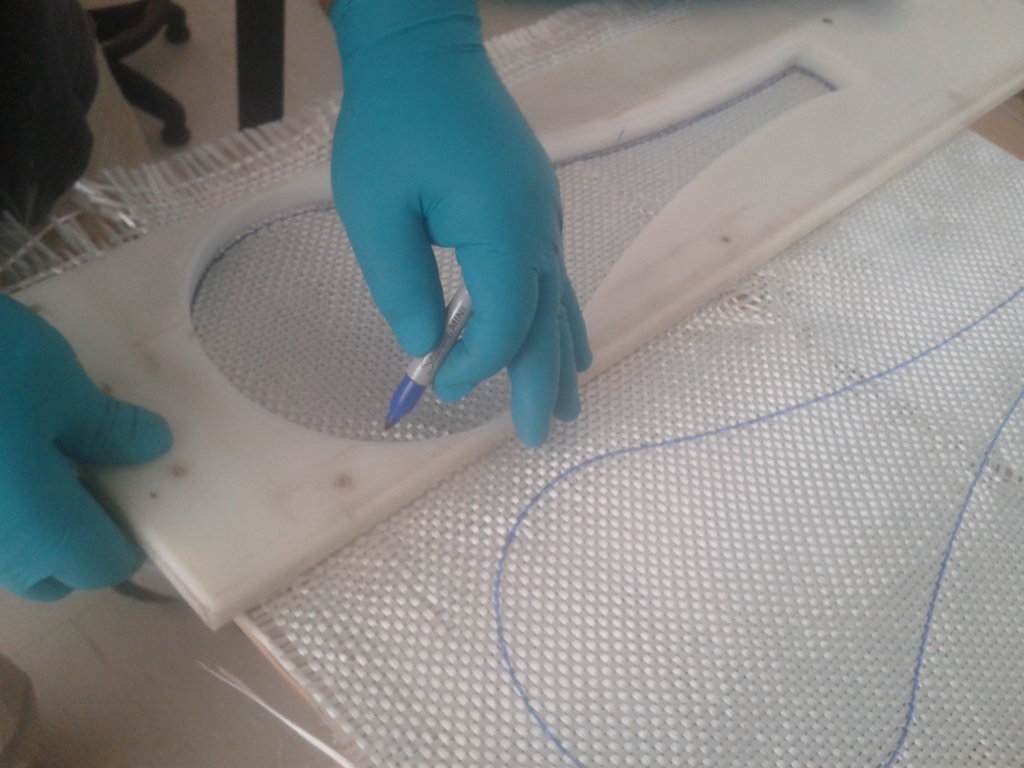
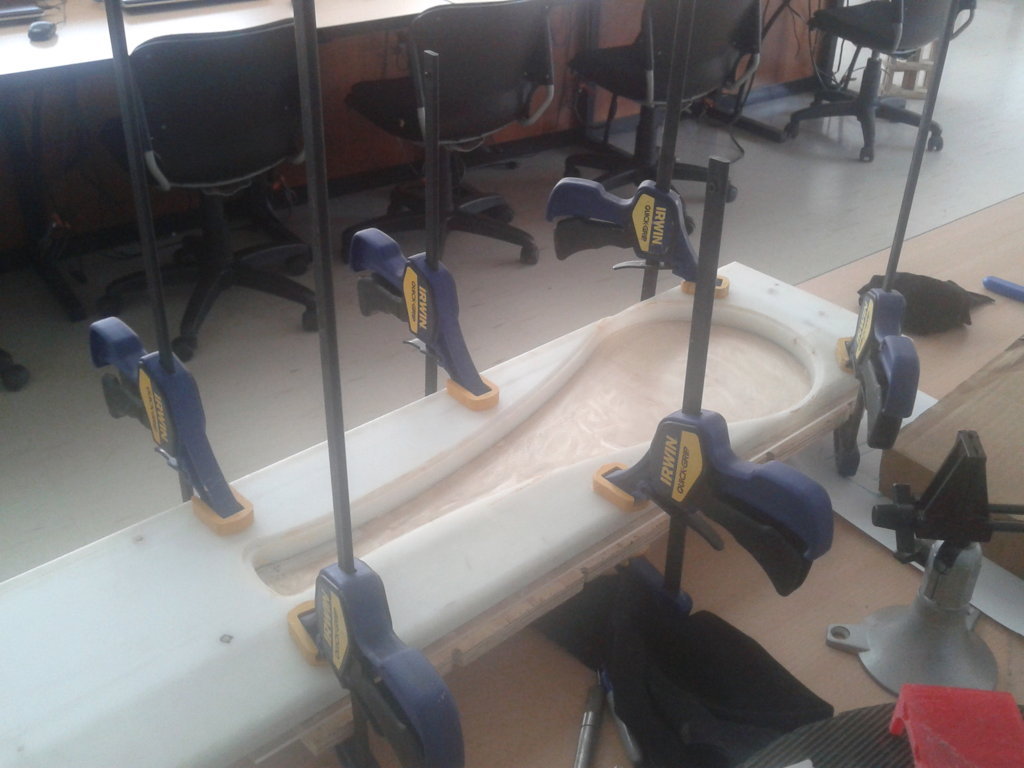
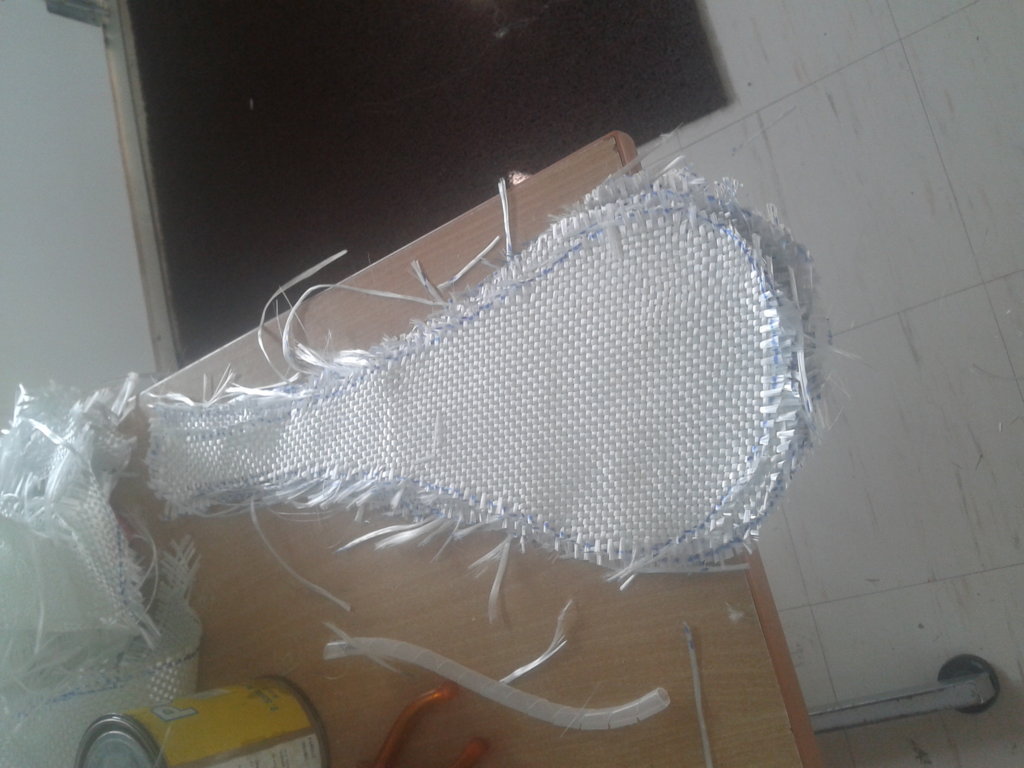
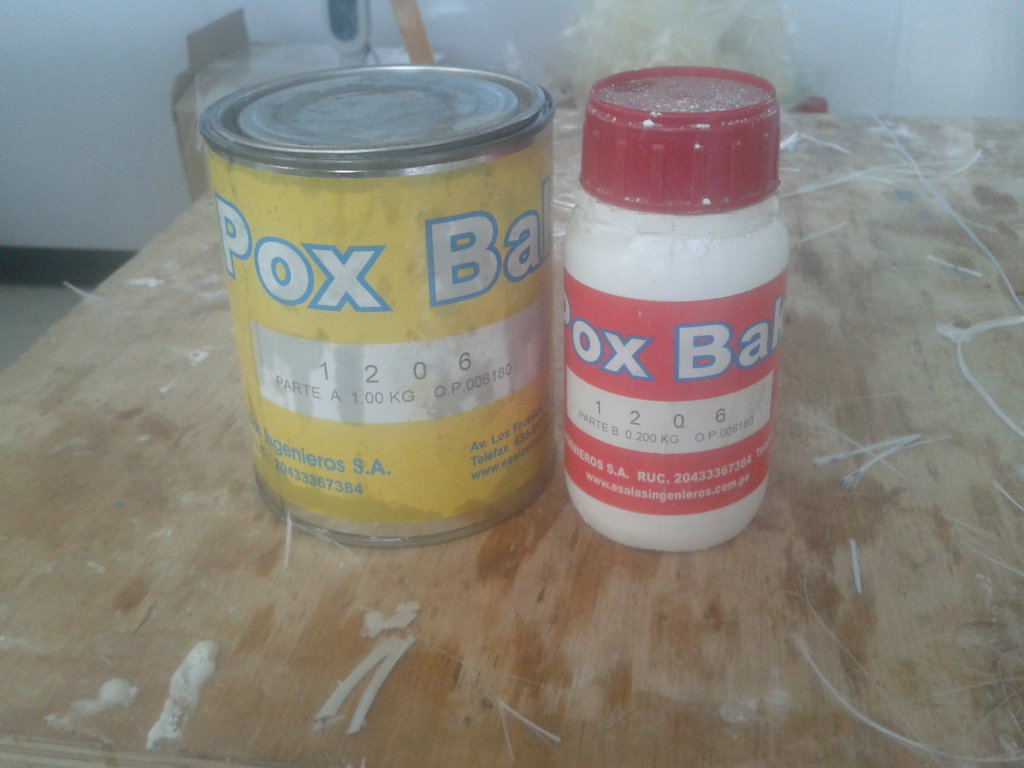
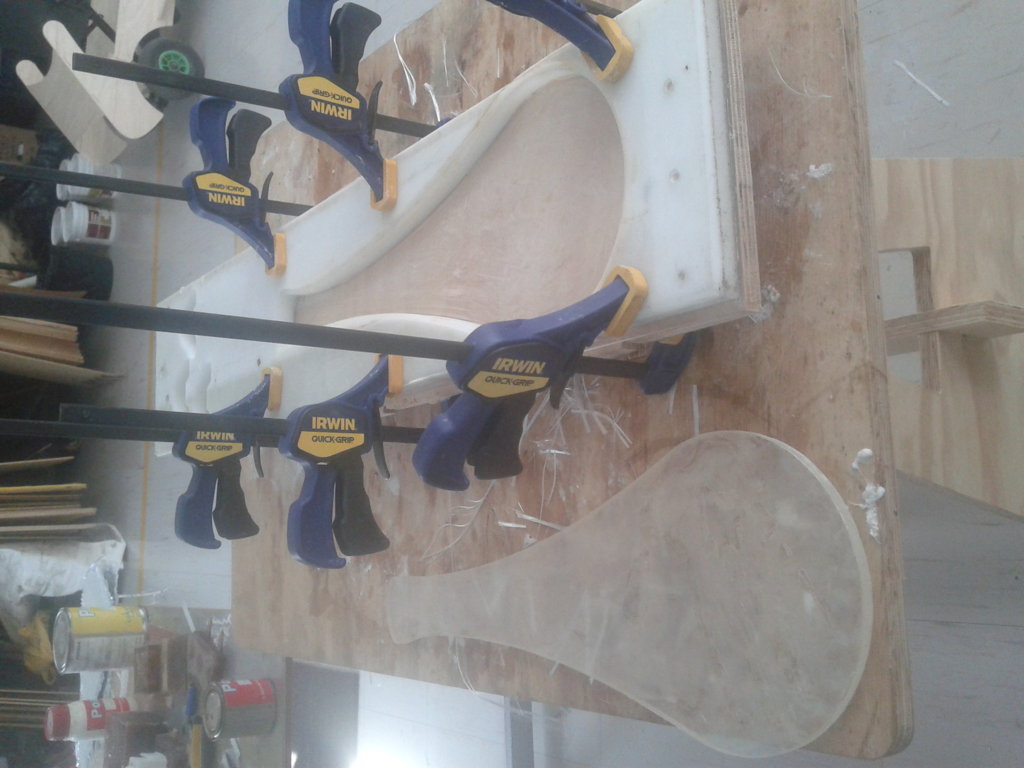
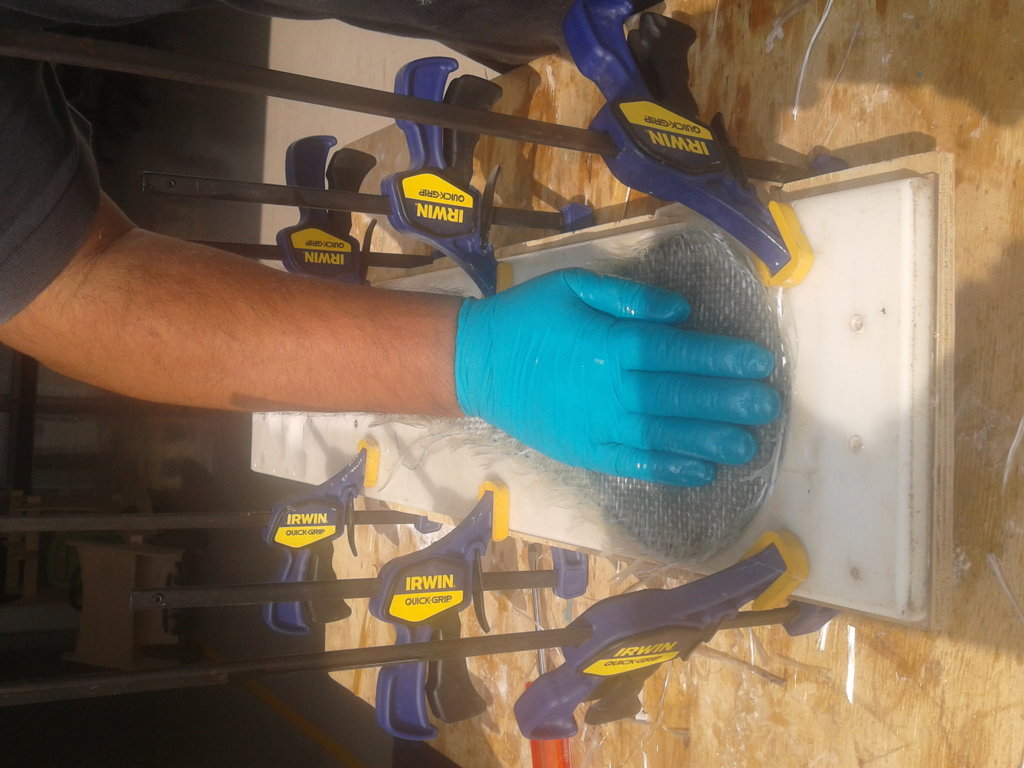
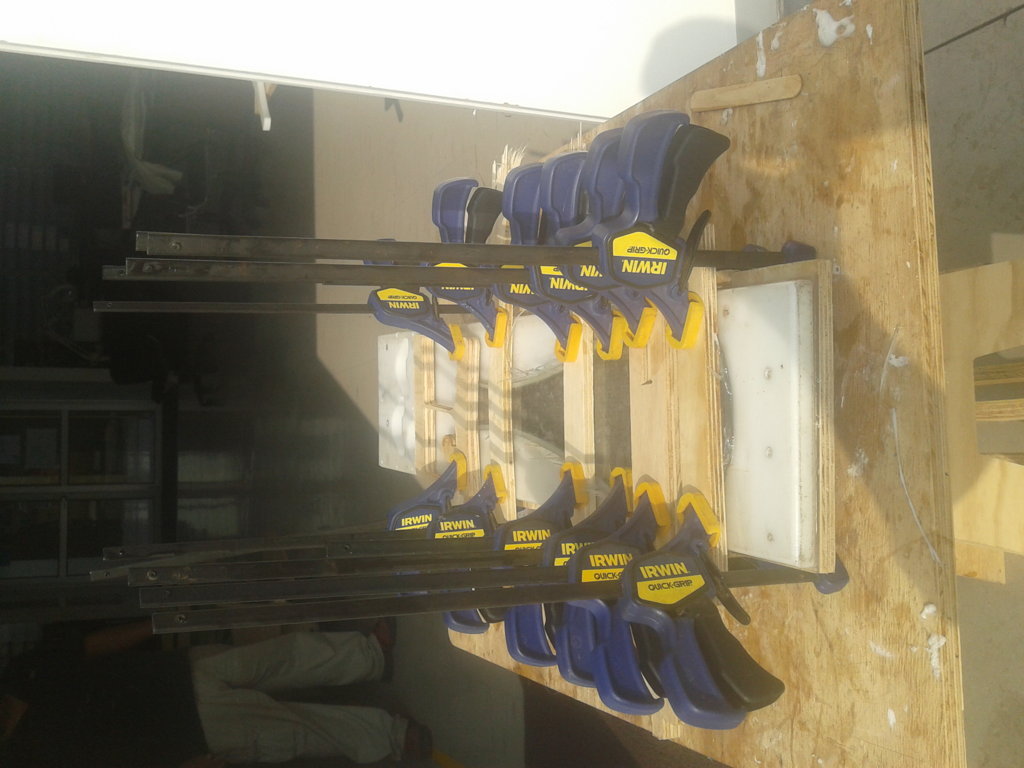
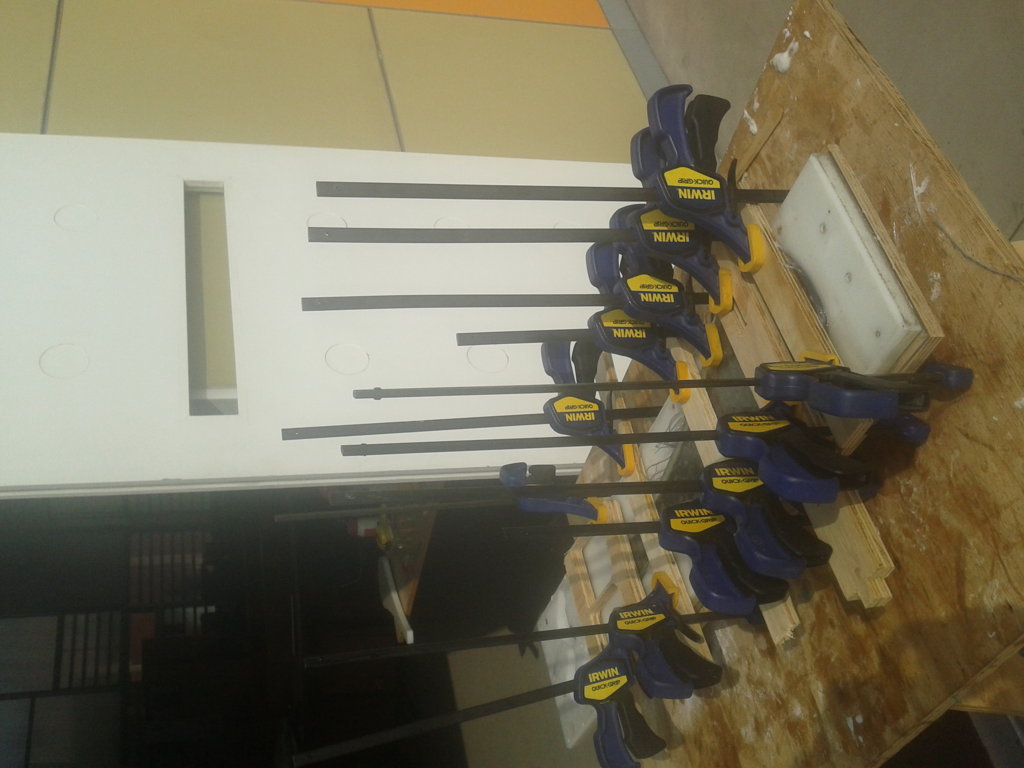

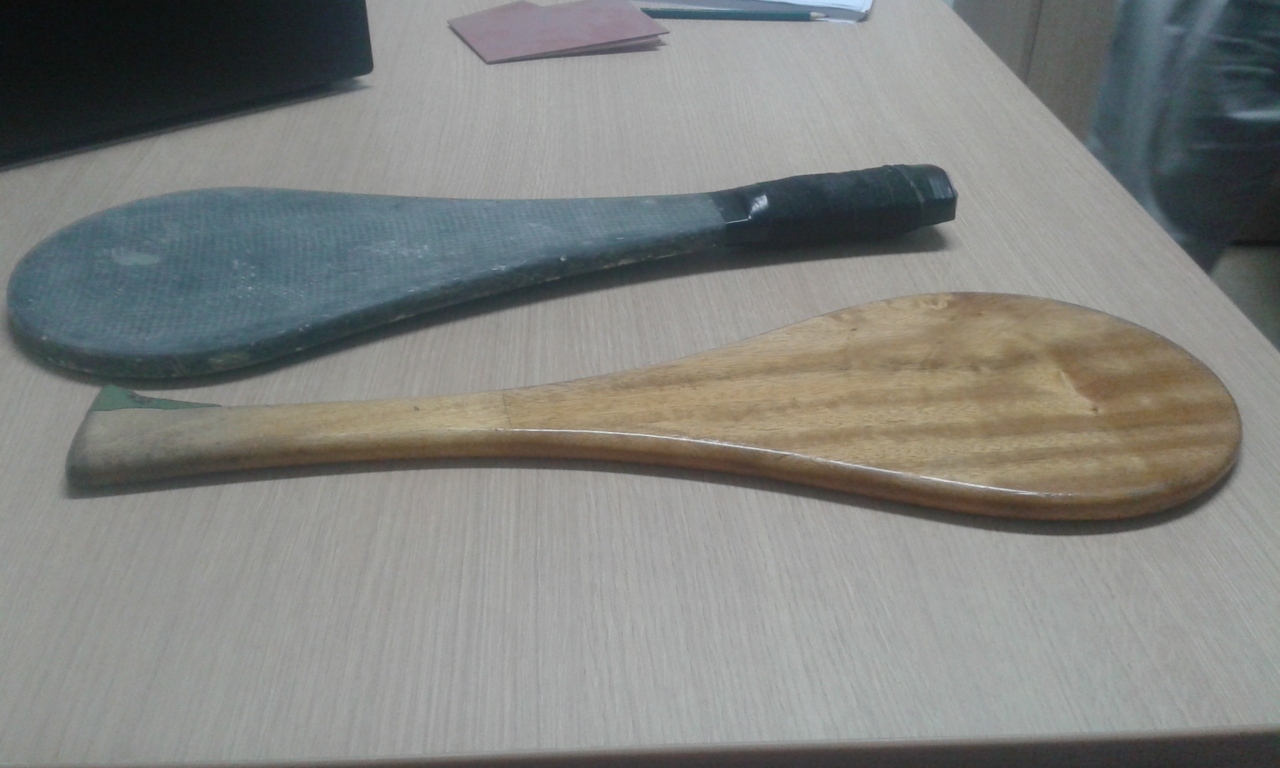
Downloading link for my archives: Archives