Assignment Seven: Electronics design and simulation
This week's task is to design circuits, create boards for the circuit using KiCAD or Eagle, and then test
the connections. An additional credit will be to simulate the circuit - during the class I got
interested in
Falstad, and will try to use it.
The assignment in steps:
Group: use the test equipment in your lab
Design a circuit
Simulate the circuit using Falstad
Create an electronic board and test it
This week, the group project is led by Francis and is hosted on
his webpage. The task is to use the test
equipment in the lab to observe the operation of a microcontroller circuit board.
Our task for this week is to add a little changes to the
Hello
Board. For me, I wanted to learn about the circuit and what the different components do that make the board
work correctly. I learnt about the FTDI used in the Hello Board so as to get output results from a serial port, and
on Stack Exchange I learnt about the different between
resonators,
crystals and oscillators. Those were quite interesting for me.
Being from a mechanical background, I have mostly hated electronics. But I think I just need to be more open
minded and be patient to learn more.
I decided to use EAGLE, only because I think that as a paid product it would be easier to learn. Thankfully,
there were
beginner resources on
their website. Using this, I created a new project and opened a new schematic page.
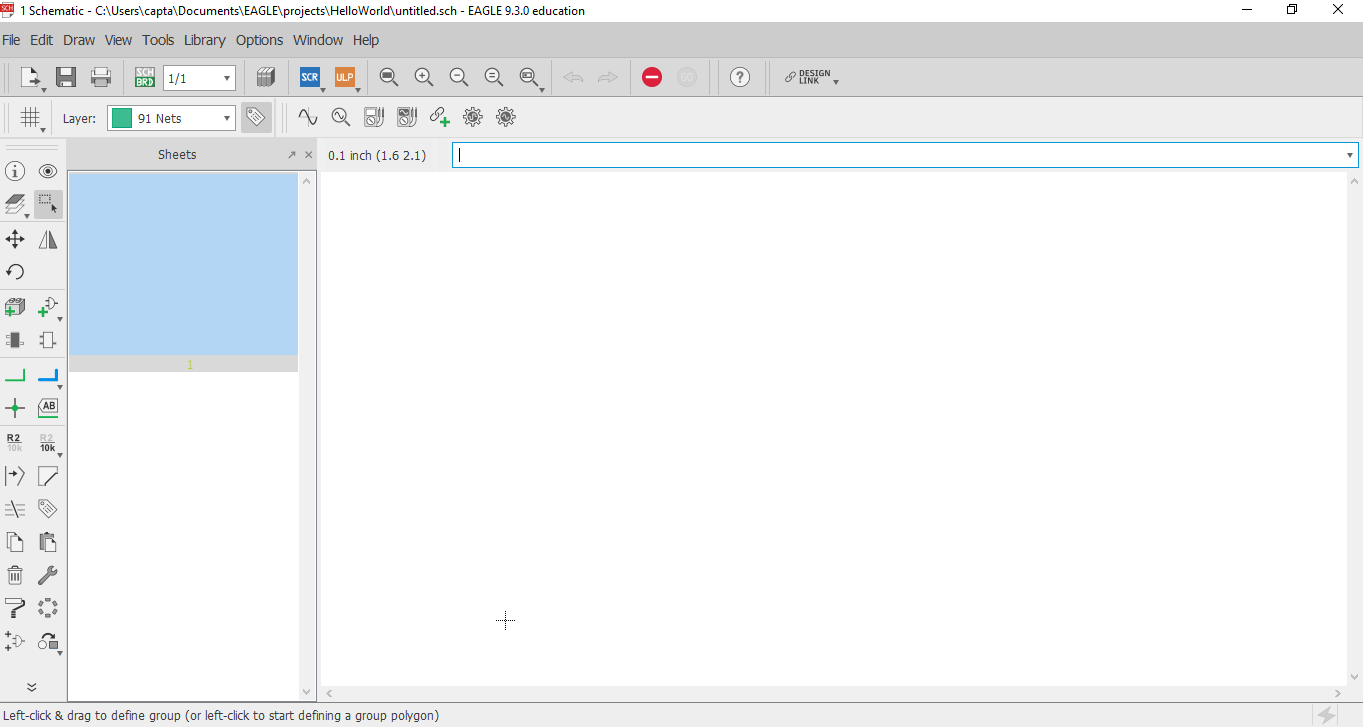
After this, I added the
FabLab
Eagle Library to my Eagle directory and changed the setting to
Use.
With this, I started to import the components one after the other into the schematic surface.
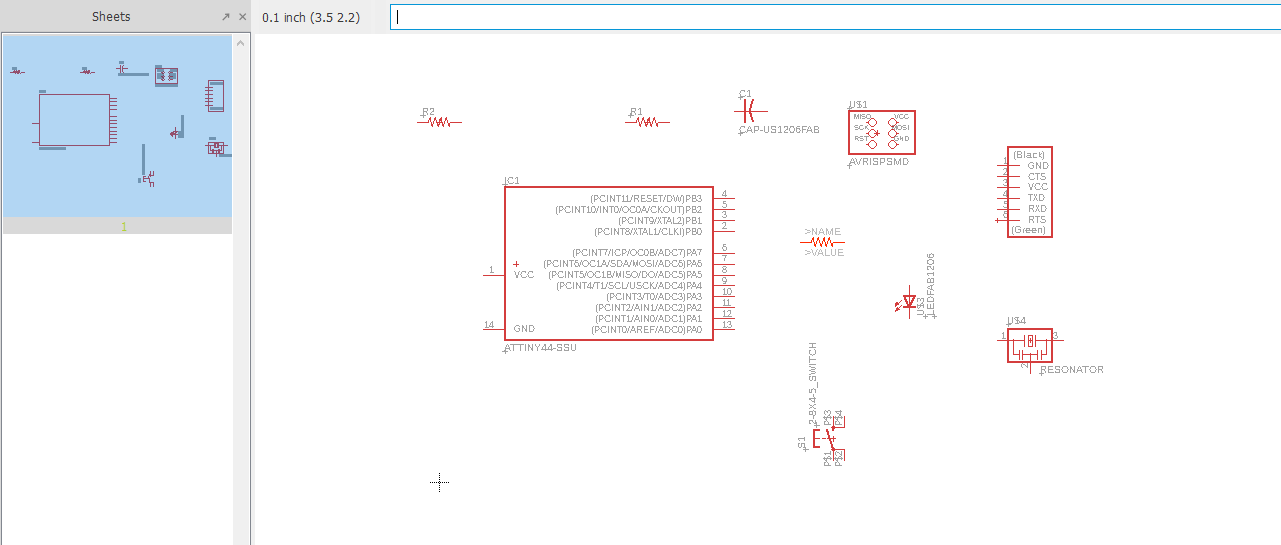
The parts there are: FTDI, ISP, Attiny-44, Resonator, two resistors (10K and another), a 1uF capacitor, a
switch, and an LED. In order to connect them, I changed the Pin Breakout setting as suggested in the tutorial
to use Pin names - this made it easier to connect. Once I was done adding the components, I then started
connecting them together in the schematic page. Eagle is pretty nice as you can connect two points by
using similar names - this was explained to me in the tutorial.
Another interesting thing is that we needed to include a pull-up resistor for the switch.
This tutorial
has a good explanation for this. My understanding of this is that a pull-up resistor helps
to reduce the current that passes through the input pin and also prevent shorts in the
circuit if it was connected directly to ground.
After connecting all the pins, it looked like this:
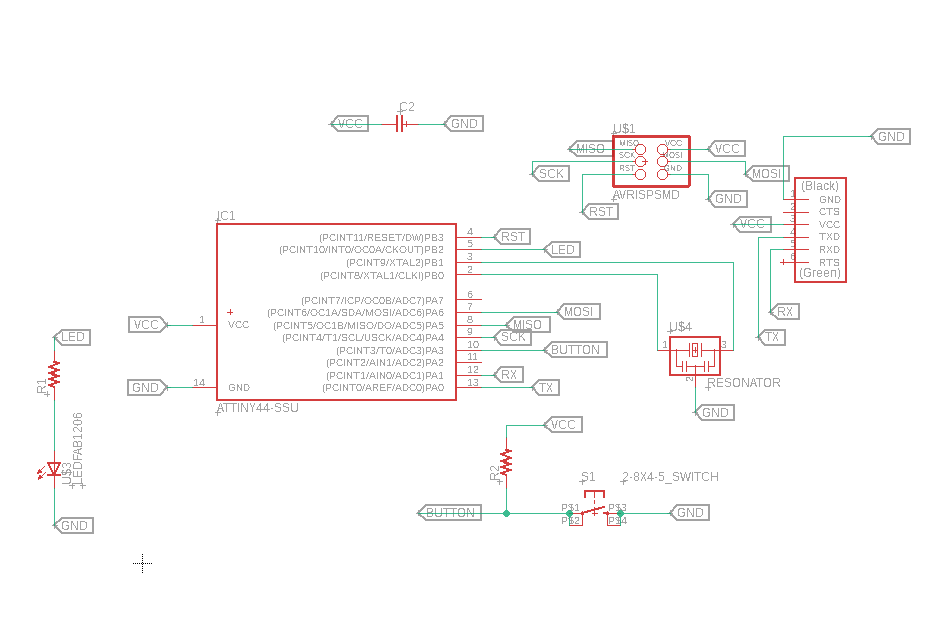
After this point, I had started watching
Jeremy Blum's
tutorial videos on Youtube. To assign the value of the resistance for the parts, I checked the
part's datasheet on Digikey
and was able to determine that for a supply voltage of 2.1V from 5V from the VCC to send 10mA of
current as wanted by the LED, the resistor should be 290 ohms. I also set a 10K resistor for the
pull-up. Once, I was done with this, I clicked the generate button to make the board layout.
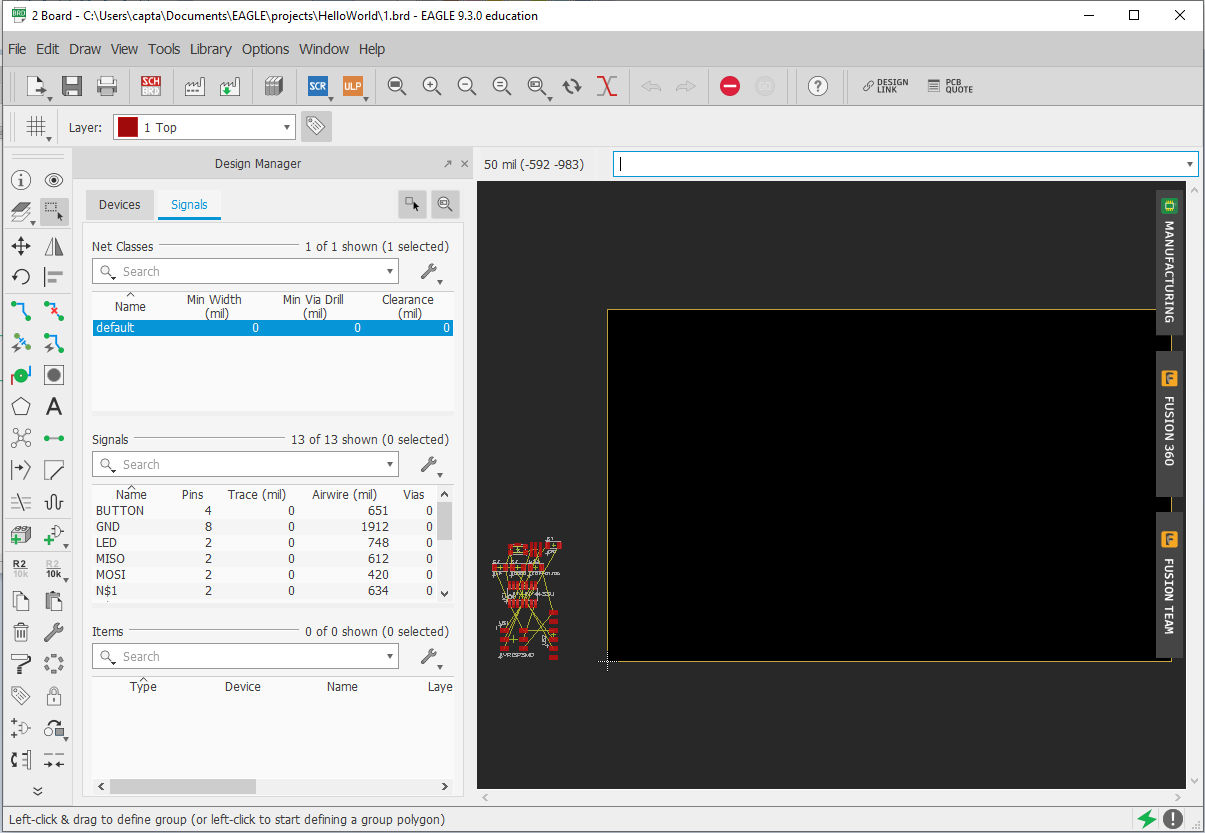
After moving everything to the board, I used the autorouter tool to connect all the parts. Before that though,
I changed the default net classes to 12 mill for width, 20 mill for drill and 10 mill for clearance.
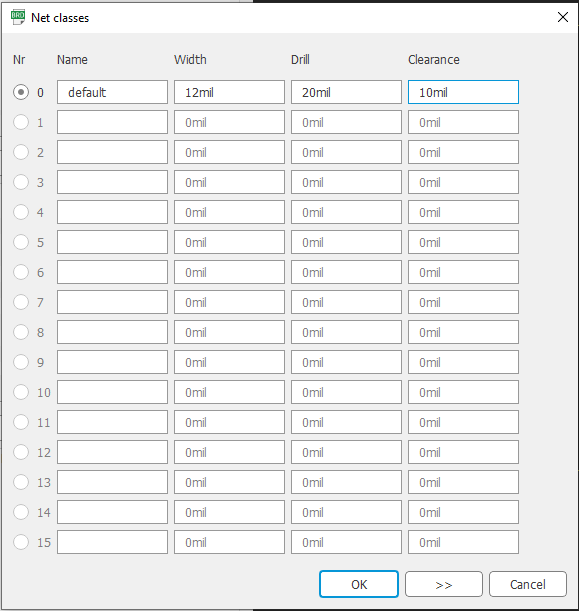
After a first wrong try, I got a 95.8% completetion with the autorouter, which connected the design below.
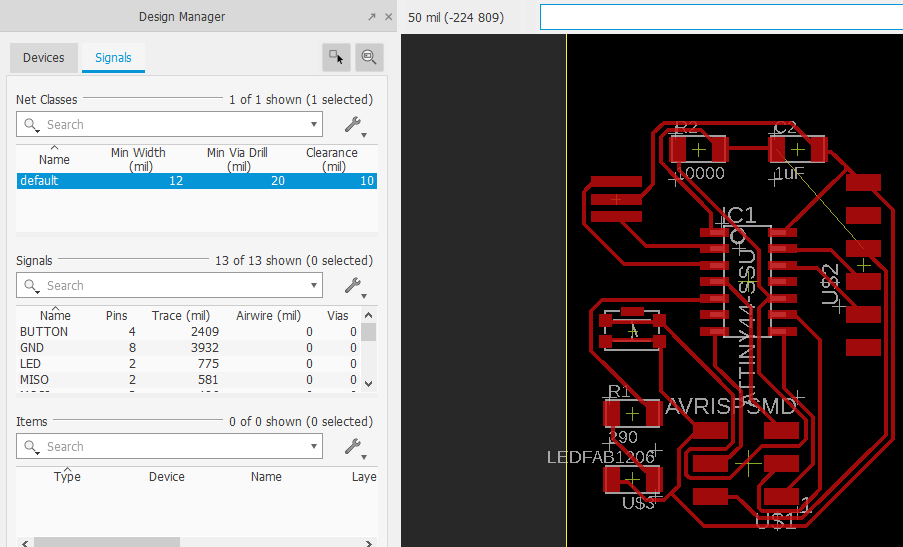
I discovered here, with the help of my instructor, that the issue was with the connection from the FTDI to
the VCC line. Francois advised that the best solution was to add a 0 ohms resister to serve as a bridge.
To do this, I added a 0 ohms resister to the schematic which generated immediately in the board diagram. Then
I connected it across in the board layout, made the dimension outline and voila!
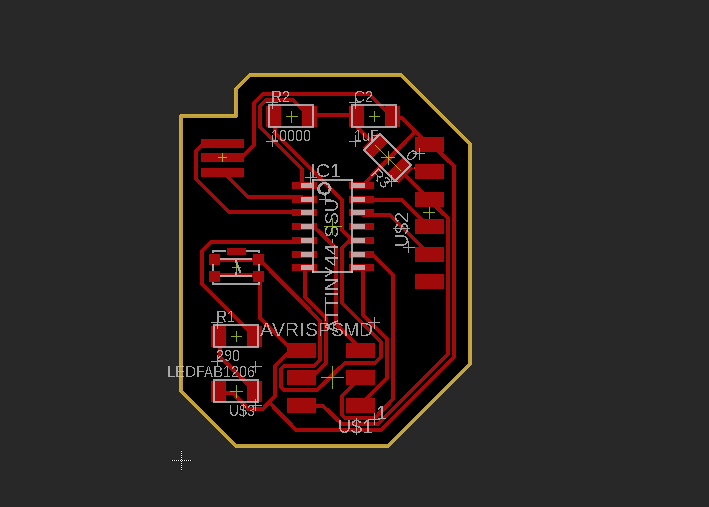
After this, I used the
CAM Processor to generate the Gerber Files
and loaded these files into FlatCAM to generate the GCode for the CNC Mill.
[more to come]
The GCode from FlatCAM is saved
here.
After making the board, I soldered on the parts.
Reflection: It turned out that I had used
the wrong switch in the Fab Library so I had to change it in my schematic and redo the board design. This
was easy enough as I had just gone through the whole process. This thought me to be more careful when
choosing parts in the library as I have to make sure that the parts I pick are actually available.