Seonghee Kim | |
4. Computer Controlled Cutting | |
HOME | ABOUT | ASSIGNMENTS | FINAL PROJECT | CONTACT | |
Week4
Assignment
-group assignment
characterize your lasercutter, making test part(s) that vary cutting settings and dimensions
-individual assignment
cut something on the vinylcutter design, lasercut, and document a parametric press-fit construction kit, accounting for the lasercutter kerf, which can be assembled in multiple ways
Hardware and Softwares used
-Fusion 360
-Graphtec Studio
-GoldenLaser Cut & Scan control
-Makercase
-Graphtec cutting pro
-K2 laser JG10060
Outcome
Vynle cutting was first time to me. The pressure value is ciritical to make good result. And for laser cutting with good presfit was challenging. So I have to know about the kerf. I made lots of mistakes to make correct presfit. Parametic design was really helpful to find right kerf value. For the vynle cutting, I used svg file I made last week with Inkscape.
Vinylcutter
Graphtec Studio
I only had to know sevral menus to cut the vinly sheet. It has very simple interface. But to find a right value, I had to try many times.
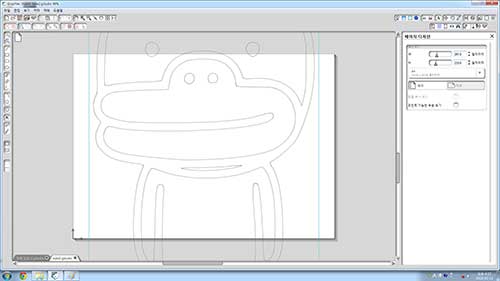

-click size button and change to appropriate size.

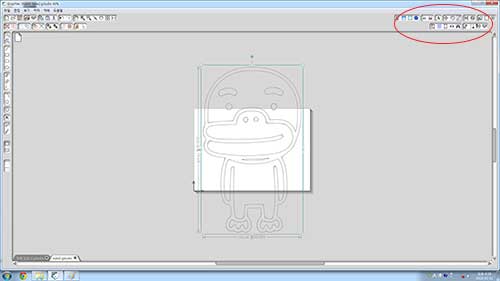
-this tool makes you the border line and cut.

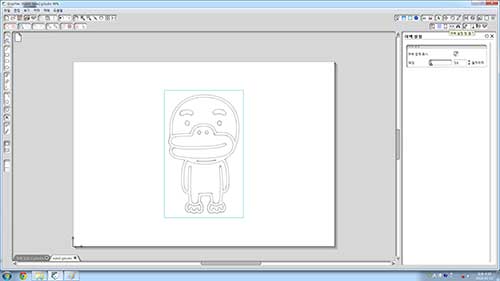
-send Gcode to machine.

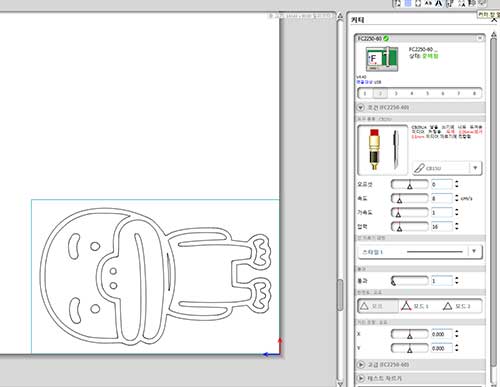
-I choosed 16 for pressure value.
Graphtec cutting pro
To hold the vinyl sheet, I had to use vacuum, but becusee of the maintenace, the pressure was week, so I stick the masking tape to hold firmly.
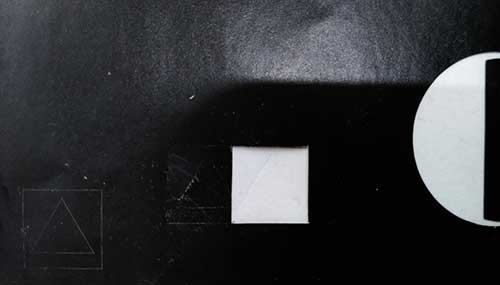
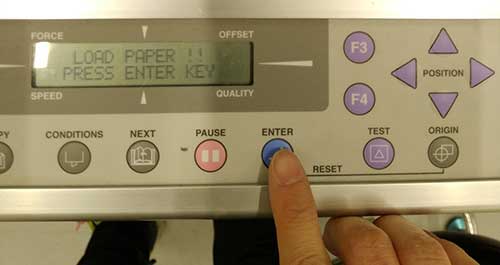
-press enter.
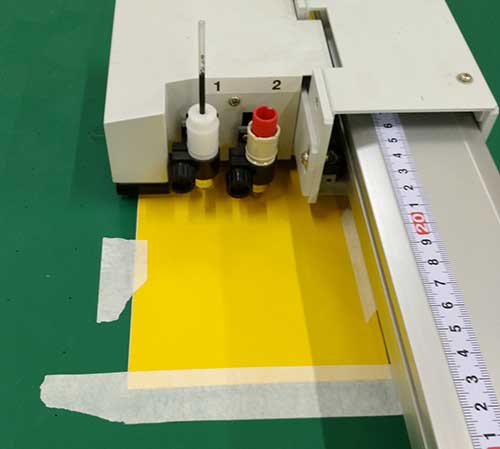
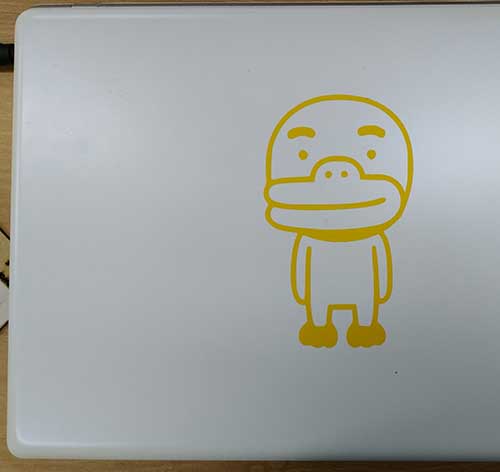
-click here to download the svg file
Laser Cutter
GoldenLaser Cut & Scan control
GoldenLaser control software has simple interface. Easy to understand. But same to vinyl cutter, to find a right value, I had to try many times.
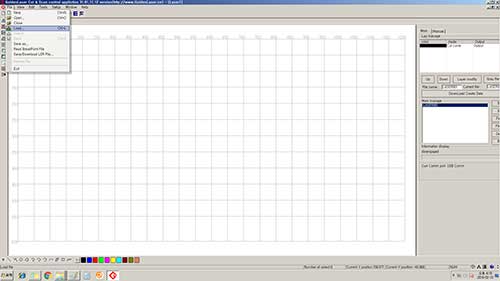
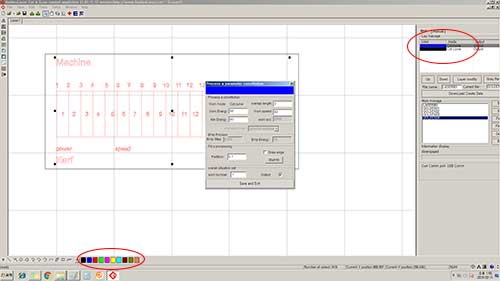
-Power 85, speed 15 for cutting.
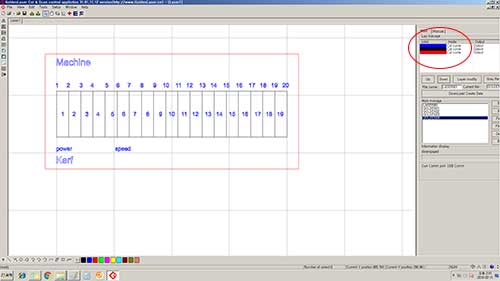
-power 65, speed 65 for lineing. but it showed cutted.
K2 laser JG10060
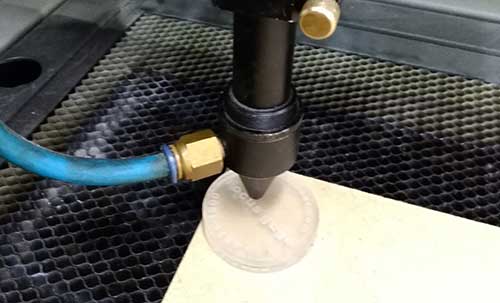
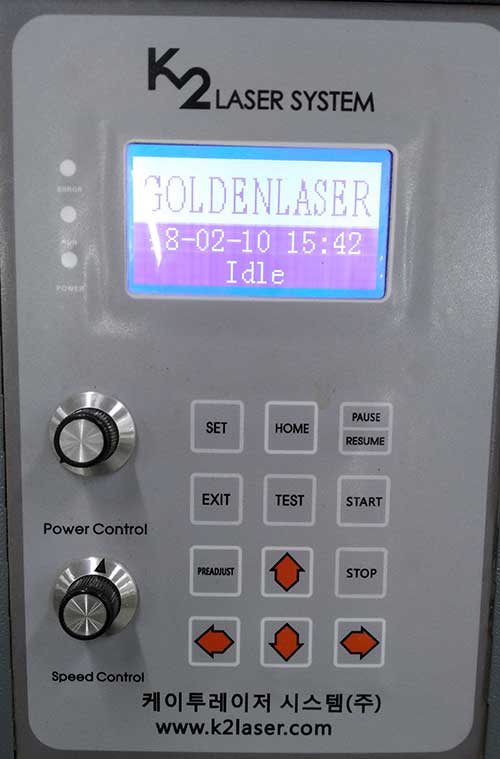
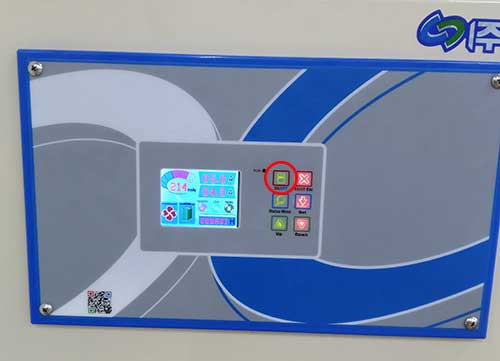
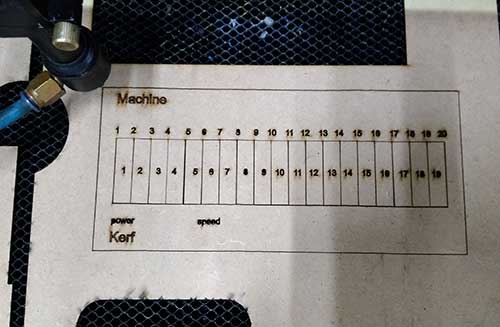
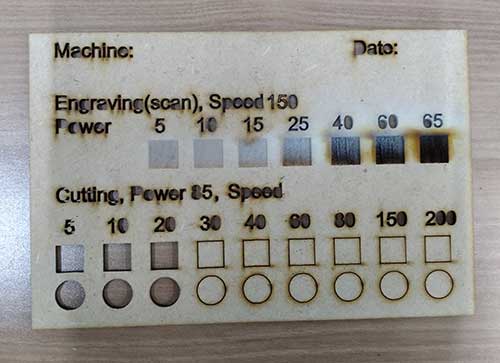
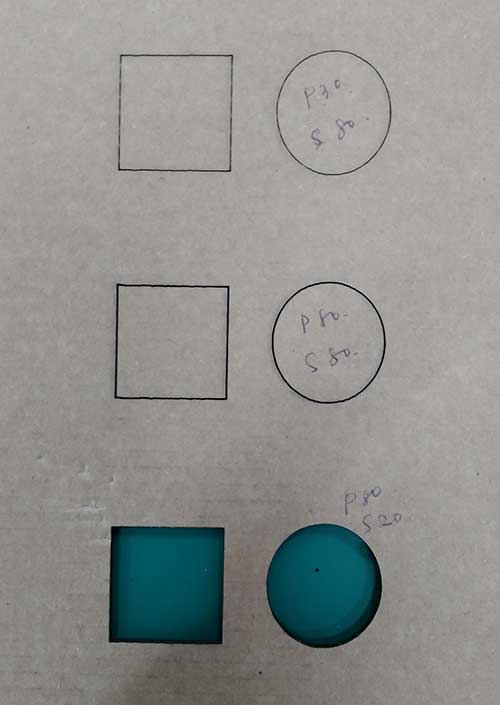
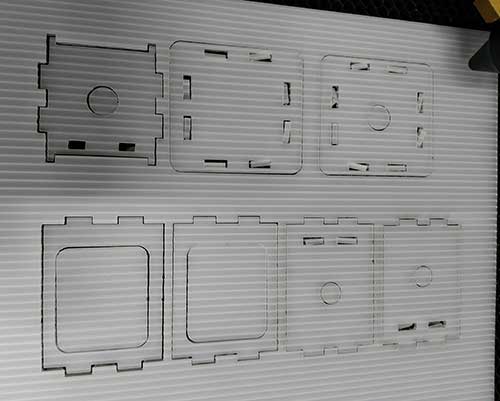
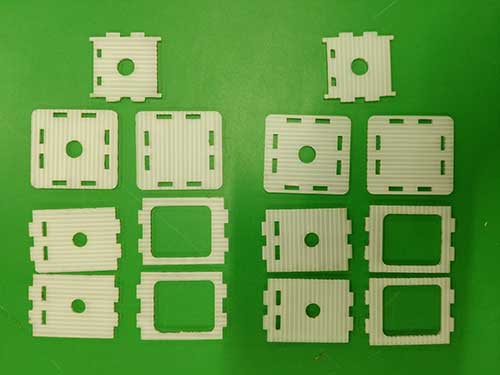
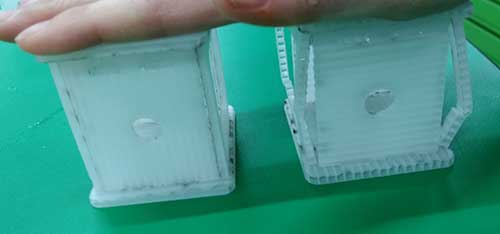
Find Kerf
Kerf is defined as the width of material that is removed by a cutting process.I tried to find the kerf matching K2 machine and some materials.
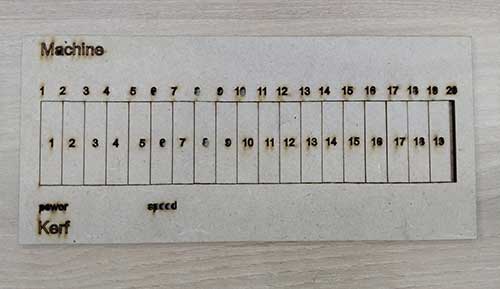
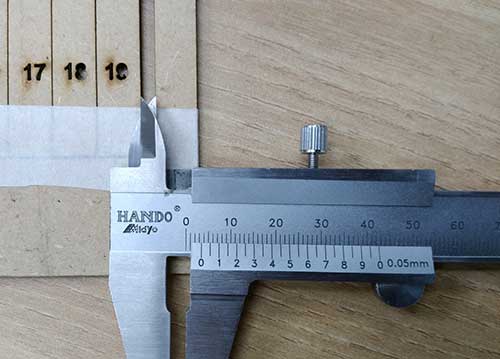
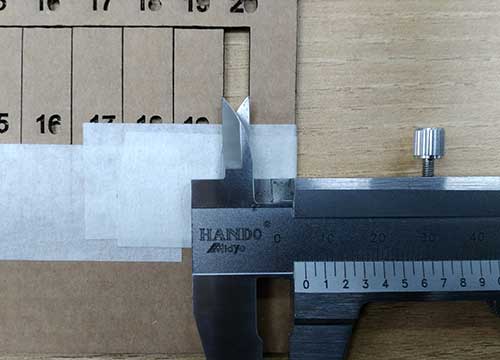
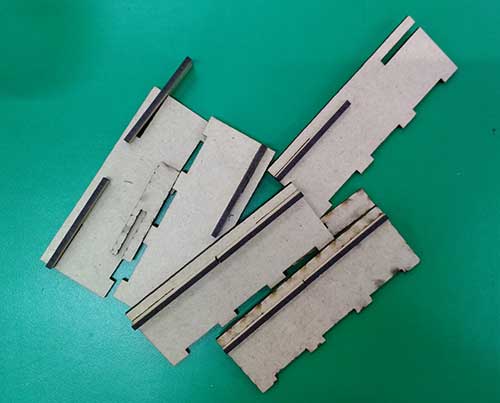

Parametric Design
Fusion 360
Parametric design is based on algorithm. I tried to make an small marble machine kit which allows to organize the marble road. Comparing the marble box which is non parametirc design(I showed end of this document), Parametric design was really useful to make change the thickness of material and matching kerf value.
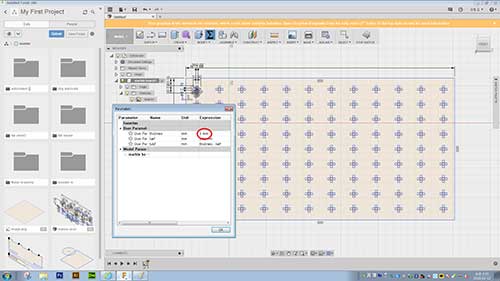
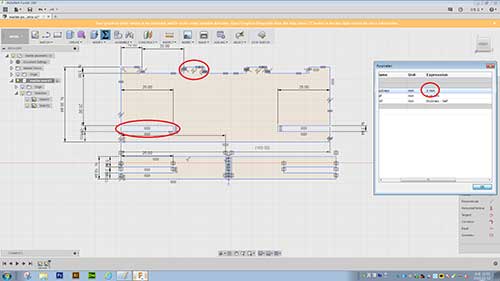
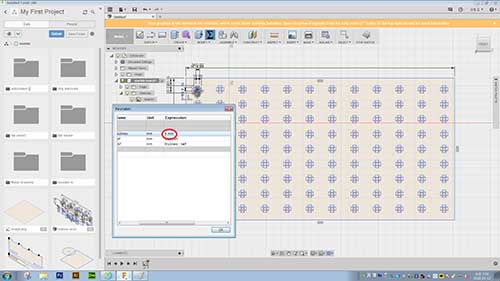
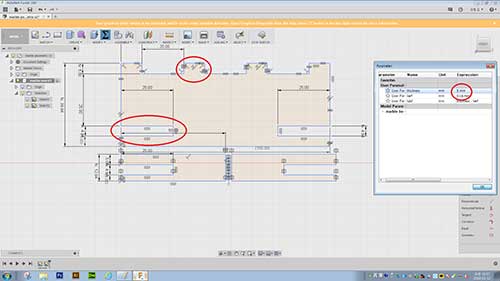
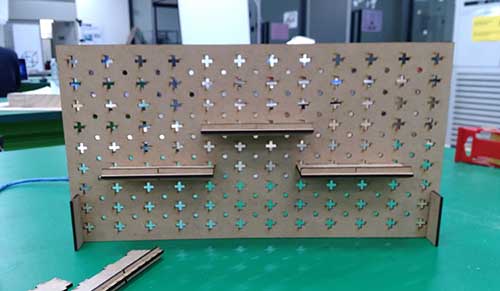
-K2 laser: power 85, limited power 80, speed 15
-MDF 3mm thick, kerf 0.17
Maker case
Maker case is the website software which allows to make box easily. It programed argorithm based. Simply put the numbers for height, width, and depth of the box. Then I can get the lasercutter plans calculate with value. But unfortunatly it was now work well.
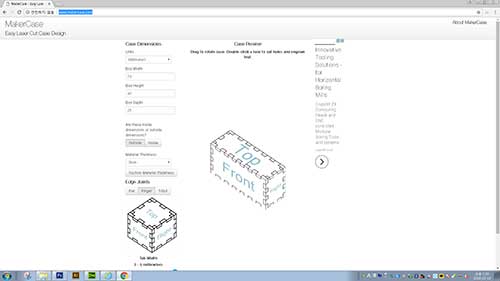
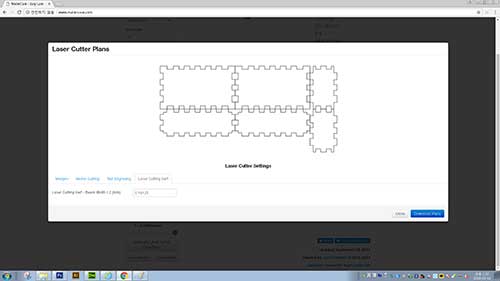
-I also tried to convert from illustrator dxf file and to fusion360. That time the size goes exactly but still kerf was not good. It does not look like changed even I changed the value at website. so I deciede to sketch my own.
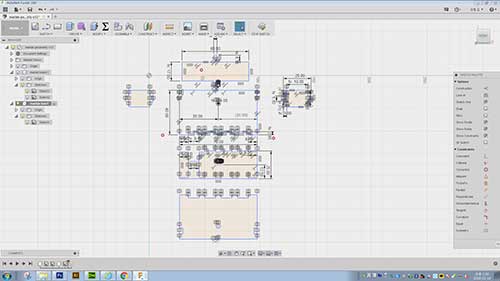
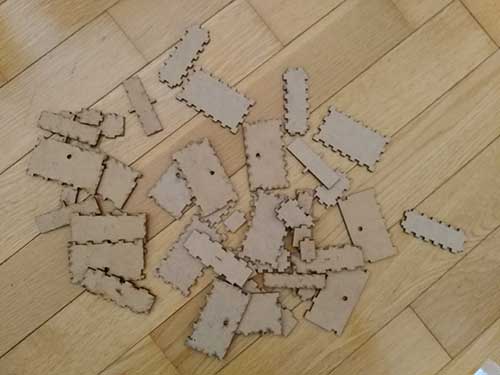
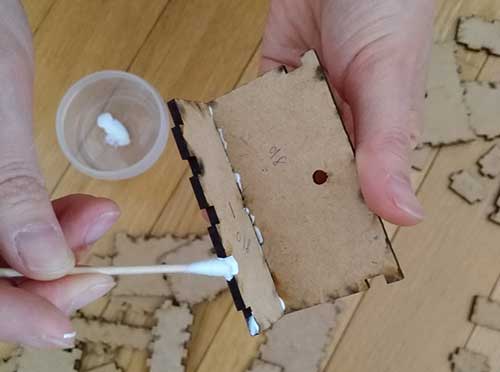
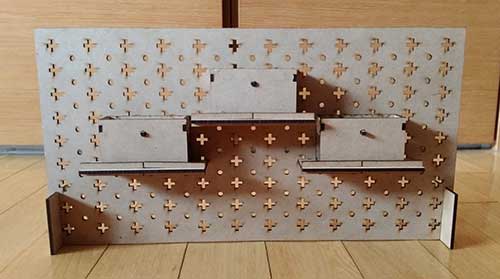
-click here to see movie how it works
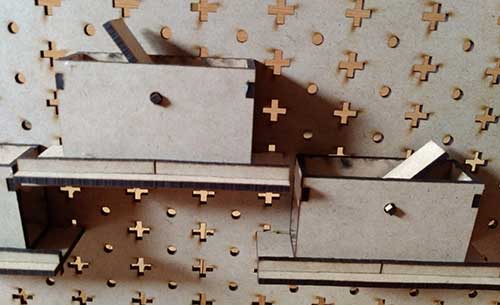
-click here to see movie how it works
downloads
-click here to download the f3d filereferences
-Kerf
http://www.esabna.com/us/en/education/blog/what-is-cutting-kerf.cfm
Date: 2018-02-013 Author: Seong Hee Kim @ Fablab Seoul