Week 4: Computer-Controlled Cutting - Cam & Gear Box
As a side project, I've been working to miniaturize and create in
acrylic a cam and gear box I ran across in a book on automata and
mechanical movements.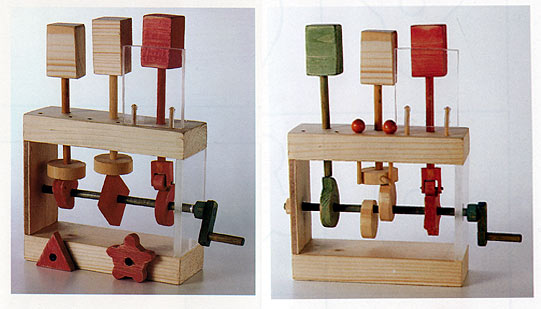
Tabs in the original plans accounted for the actual thickness of the acrylic (.220"); tab-depth was adjusted accordingly to ensure none of the tabs extended past the edge of the joining sides. The first prototype was cut from paper-backed display board. Not an ideal material for prototyping: the laser cut cleanly through the top layer of paper but not the bottom. Additional attempts were made using slower speed, higher power, and/or multiple passes -- however, the foam core tended to melt anywhere from 1/16" to 1/8" into the pieces, raising concerns that they would not give me a true sense of fit, due to compromised structural integrity.
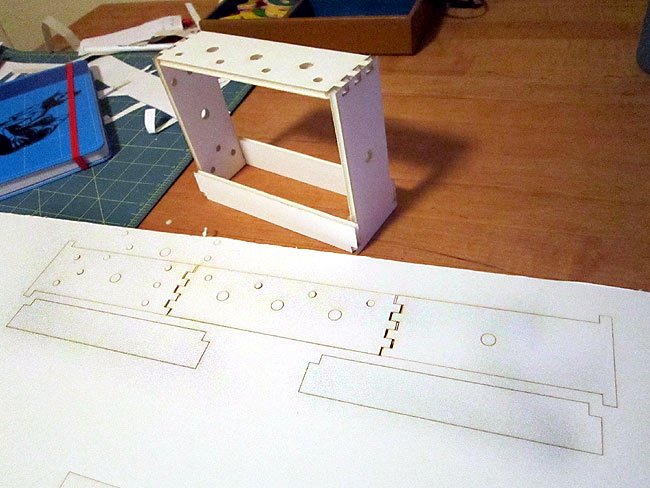
for the press-fit exercise, I modified plans for the bottom support beams to make them fully inter-lockable.
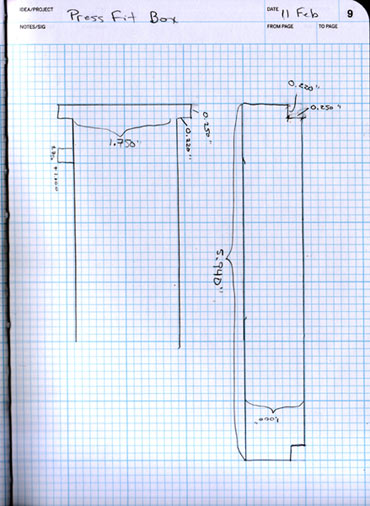
Comparison of original and press-fit SVGs
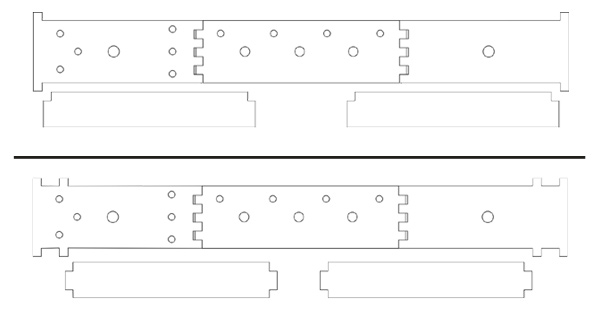
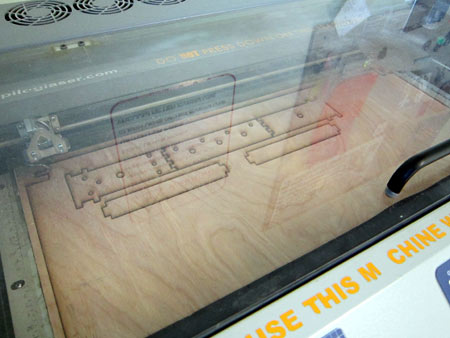
The Masonite trial was my first experience with Flaming Things In The Laser Cutter.
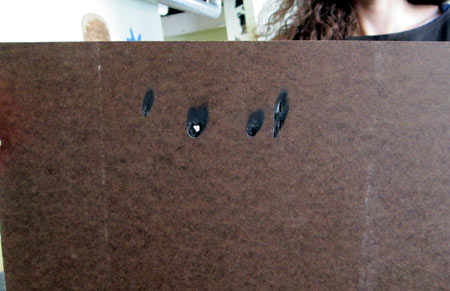
Root cause -- a previous student had used a plywood with high sap or glue content. Thorough cleaning of lens and mirror eliminated the charring, but no luck with full-depth cutting (1/8" masonite, so well within tolerances of the Epilog). Inspection of the machine suggests that a full maintenance cleaning and calibration is due.
While I do not have a box to show, I did learn this week that the word "kerf" comes from the Old English cyrf, a cutting, and has been used to designate the amount of material lost during cutting since pre-industrial times. Early sawmills used large cutting blades with kerfs exceeding 6 inches. Spontaneous explosions due to a saturation of airborne sawdust was common.