✨Molding and Casting but cute✨
Hey there sis, welcome to this week's assignment where we were challenged to make a mold that is perfecty designed for your 3D model design and then cast it to perfection.
Get ready for some really cool molding stuff ahead lol.
For a better knowledge, feel free to check the molding and casting🎀 week below
⬇️
🎀All about molding and casting🎀
Alright girl so let’s keep it real, diving into mold and cast design is like unlocking a whole new level at craftmanship. Essentially, it's all about mastering the art of creating a negative impression (the mold) of your design, and then using that mold to cast replicas in various materials, which, believe me, it’s as difficult as it sounds.
Learning about mold design means getting cozy with concepts like draft angles, parting lines, and gating systems, basically, understanding how to create a mold that's not only accurate but also easy to release your cast.
Then, when it comes to casting, you're getting into the nitty-gritty of material selection, pouring techniques, and curing processes. It's all about bringing your design to life in a tangible way, whether you're whipping up prototypes or churning out a bunch of identical widgets.
Soooo amazing baeeeee... now how did you approached it gurl?🧸
So for this assignment I decided to make a mini scale lamp (that I would like later to make in real size super pretty in plaster for my house) and 3D print it to try my design.
-
☀️So like, first things first, I kicked things off in CATIA by throwing down two lines to map out the base dimensions.
-
🌟 Then, I got all artsy with it and busted out the spline tool to whip up this super organic shape, all this flowing curves and all that stuff.
-
☀️After that, I slapped on some dimensions for the height and stuff, and then I got into the mirror section to outline it inside, using that handy tool tucked away there.
-
🌟And for the next move? Padded that bad boy for some depth. But here’s where it gets real juicy
I pulled off this slick boole operation to carve out a rectangle and chomp away at the model,
turning it into this negative mold vibe.
-
☀️And then, oh, major game-changer, crafting the pour spout and figuring out how to seal up the mold (I went all in with screw measurements to lock it down tight). It is the best way to close a design like mine, look how amazing it looks:
Remember to smooth that mold, look at mine before and after a nicely smoothing session:
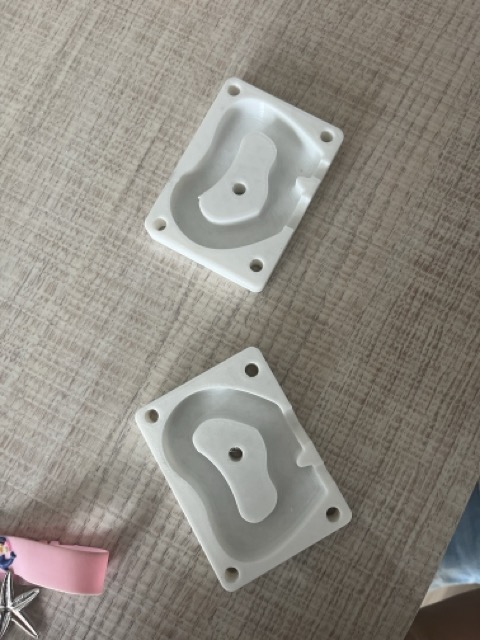
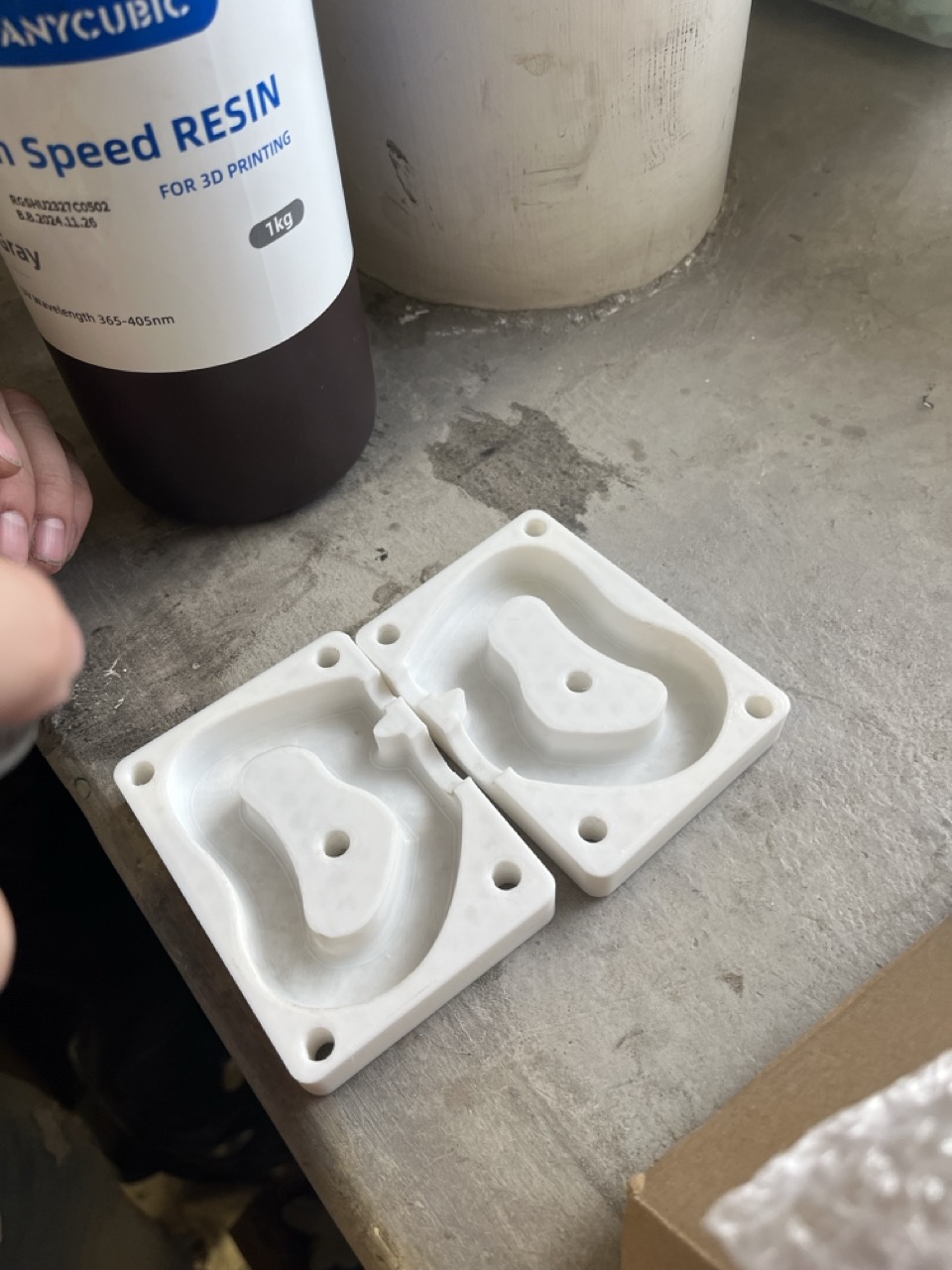
💫And that´s how you can make a organic shape 3D lamp model. Cute right?✨ Look at it down the slicer omg.
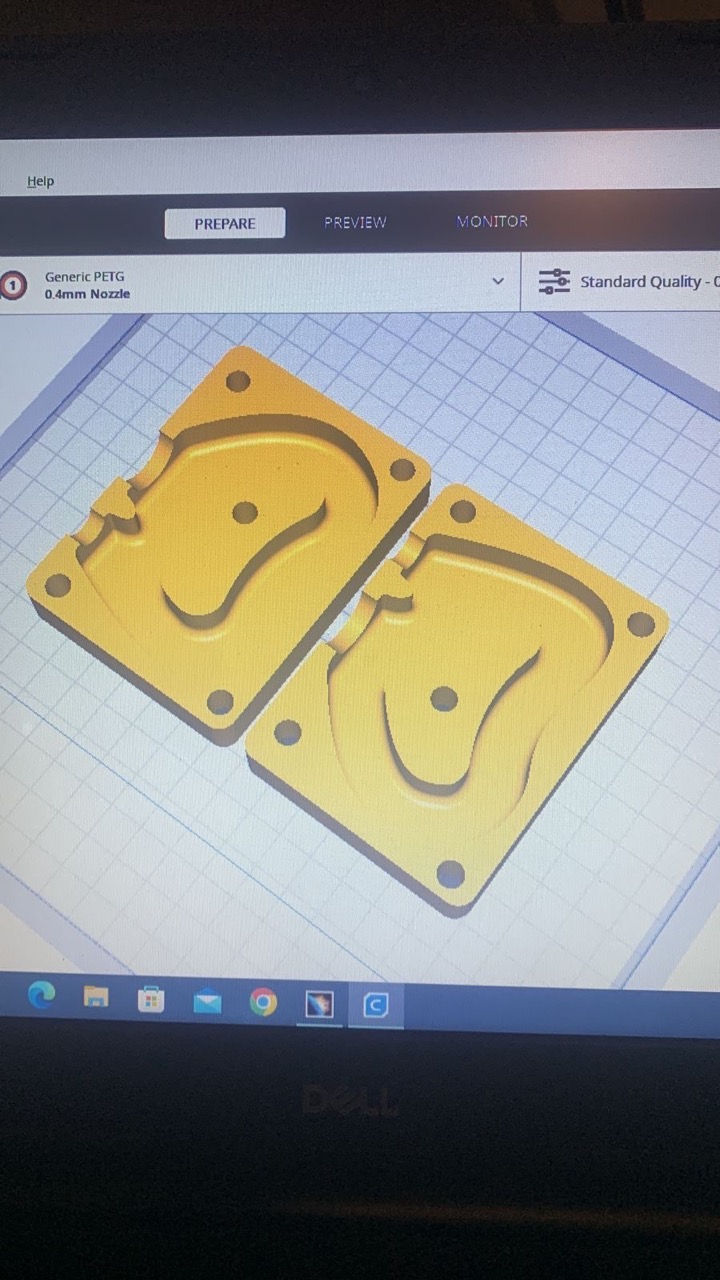
Take a look at my pretty process carousel
Soooo why silicone gurl?
Soooo silicone is super flexible, so it's a breeze to release your cast without any drama. No shattered molds here! It also can handle complex shapes and intricate details like a champ, ensuring your final product looks just as awesome as your design.
Silicone molds are durable and long-lasting, so you can crank out replicas like nobody's business without worrying about your mold falling apart. It can handle high temperatures like a pro, making it perfect for casting all sorts of materials without breaking a sweat. Silicone is easy to work with and forgiving of mistakes, so you can focus on bringing your design to life without any added stress.
And why not using glass, wood or even plaster bae?
Amazing babe! but how did it went with the casting situation omg?🍒
Get ready for some serious cool tips ahead:
-
Alright, so, let's break it down. Here’s a super cheat sheet: I totally forgot to make a draft angle in my design, it's like the slick incline you add to your design's walls so you can slide your piece out of the mold with ease. It's all about giving your creations that smooth exit strategy, you know? So it’s easier for you to take it off once it’s ready.
-
Now, why silicon is the bomb for your lamp mold scale-up in 3D printing? It's all about that flexibility and detail capture game. Unlike other materials, silicon can handle complex shapes and intricate textures like a champ without losing quality. Plus, it's non-toxic and heat-resistant, making it perfect for casting and molding. This was the silicone I used for this assignment:
-
So first of all, when you know which material will be the kick ass for you design, always, always read the safety data sheet of it and which materials can and cannot interact with it, chemical reactions can be very dangerous bae. For the perfect consistency I weighted everything and then I made sure it was not going to loss any of the mix. Also remember to put some lube on your molds, so it´s easier for you to make it come out (as an extra tip I used tape for the mix not to get out of the mold lol)
Take a look of my pretty process 🌸pics🌸
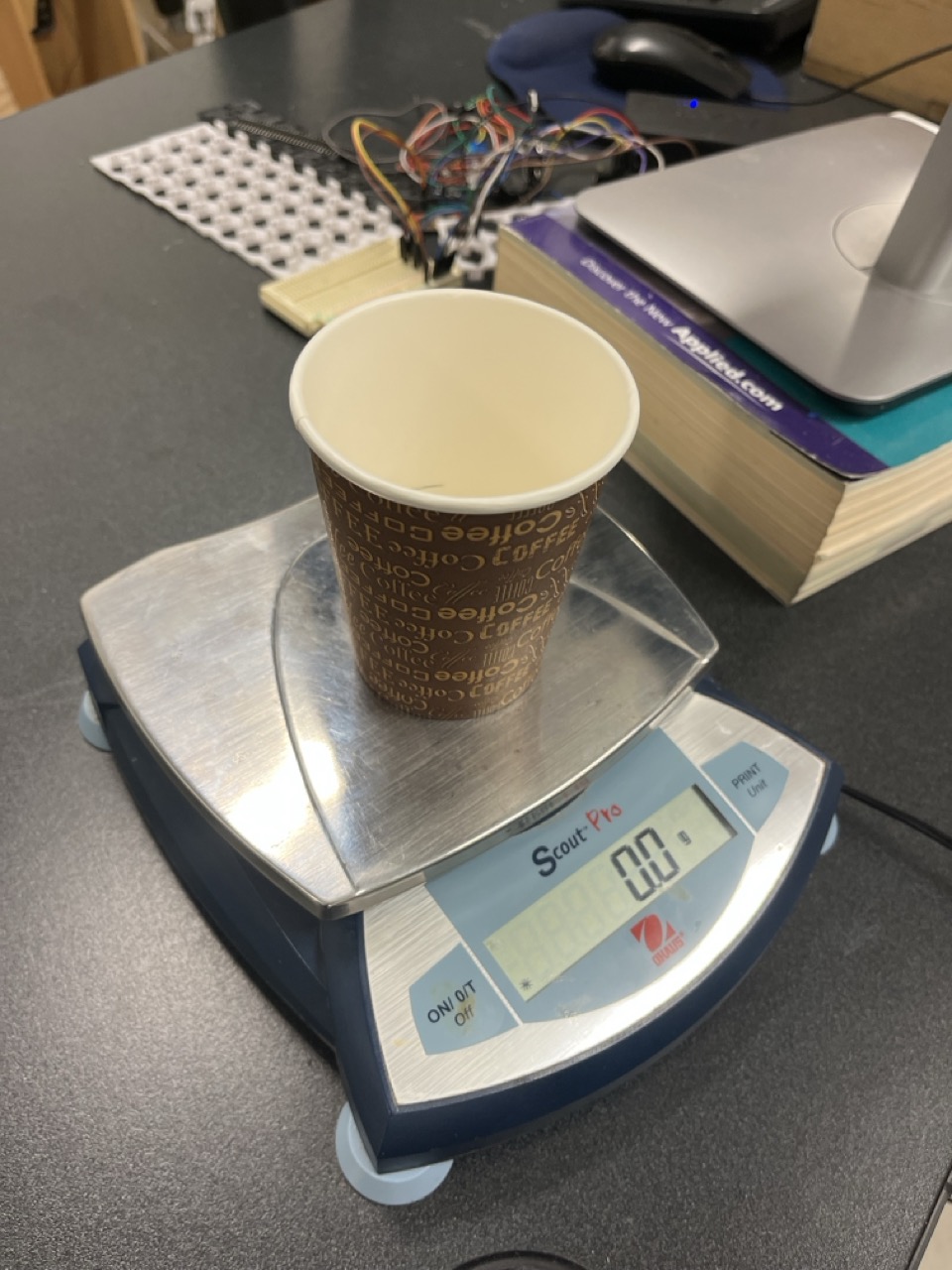
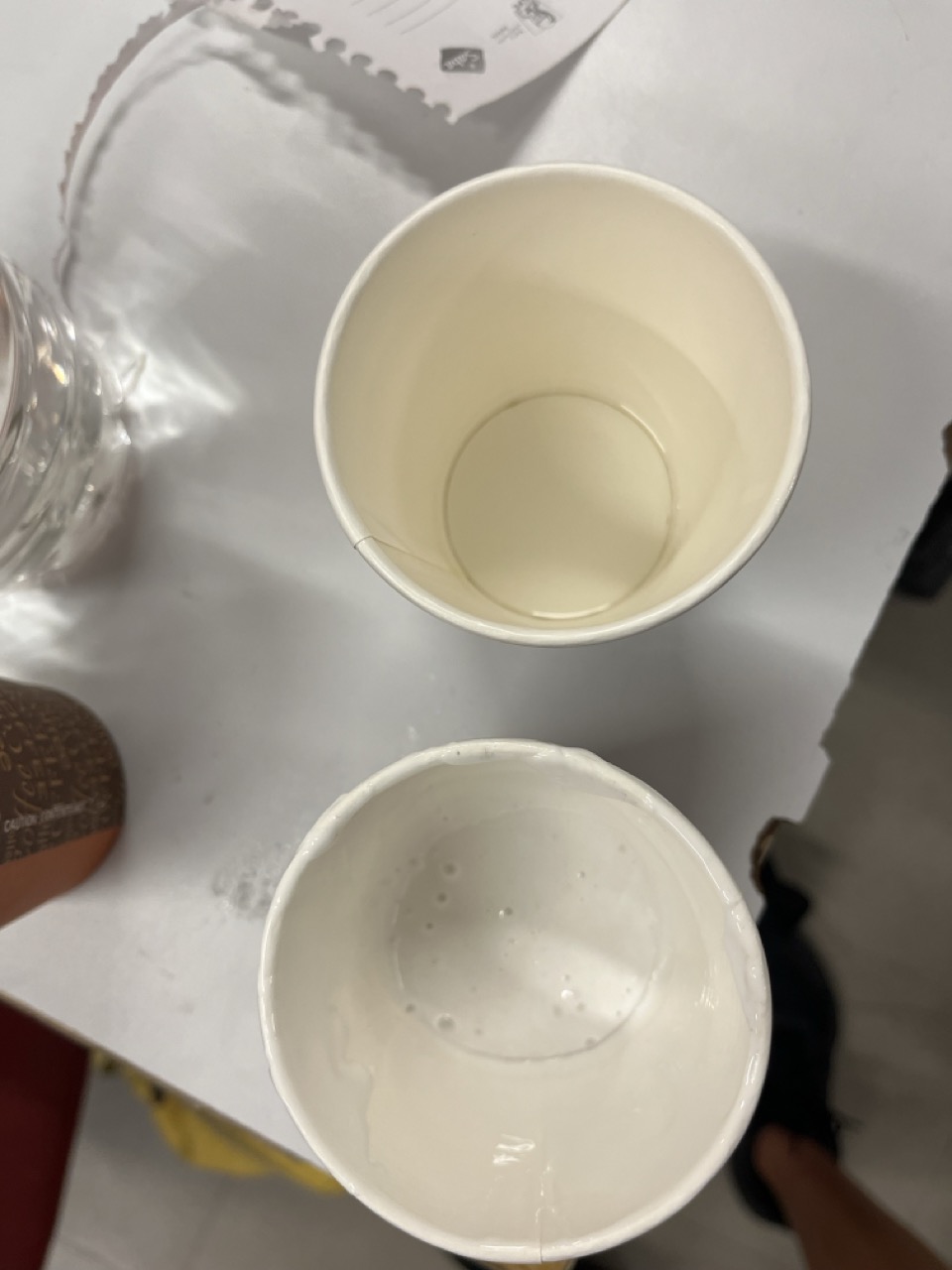
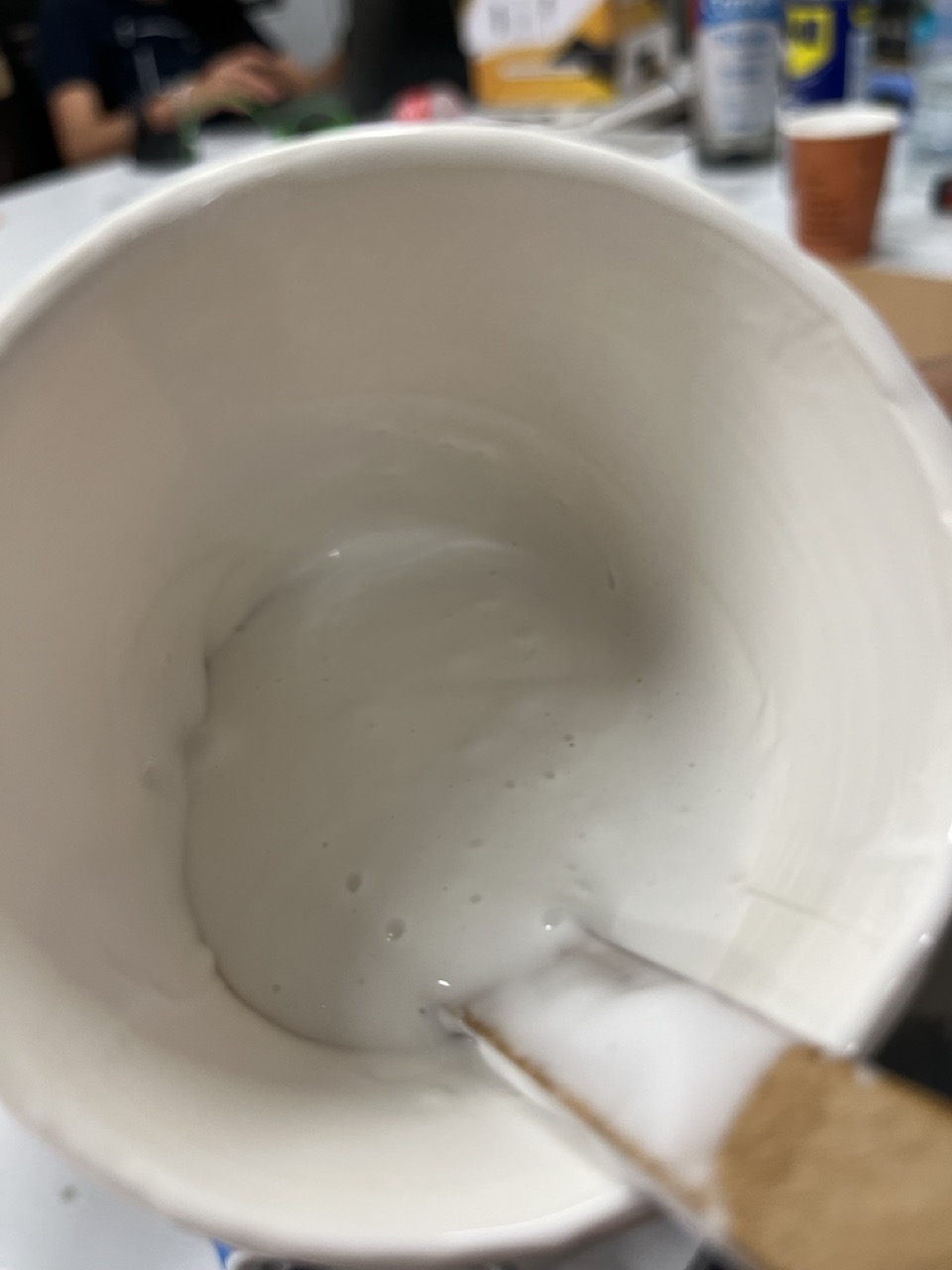
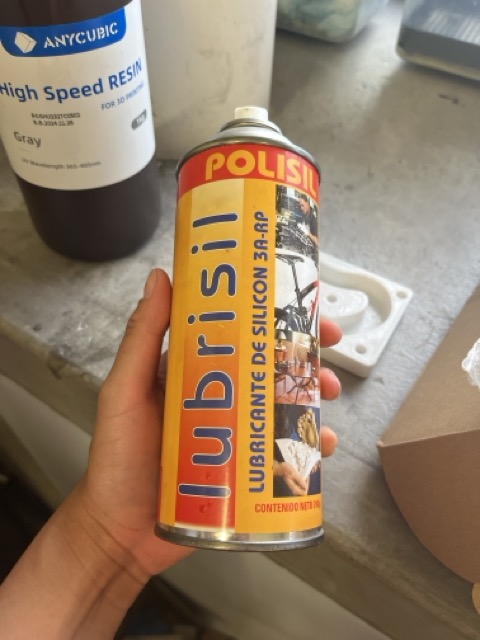
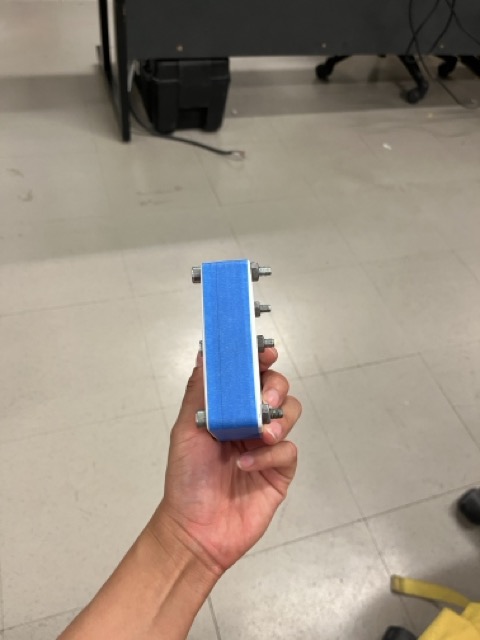