15. Wildcard week
For this week, I want to show a bit about bacterial cellulose, a project from the biomass laboratory at IDIT in IBERO Puebla. Various experiments are being conducted with it.
What is it?
Bacterial cellulose (BC) is a polymer composed of β-glucose, a metabolite of the bacteria or the process itself, linked by covalent bonds forming a linear chain. The linear chains of the polymer associate through hydrogen bonds and Van der Waals forces [6]. Therefore, this association of chains forms a nanometric network of ribbons capable of absorbing water (> 90% of its weight), with a porosity of 200 µm and biocompatibility [7]. Additionally, BC has been chosen as a biopolymer due to its ease of purification, control of cultivation parameters (pH, temperature, and Brix degrees); and it can be produced from the reuse of agro-industrial waste or leachates [5].
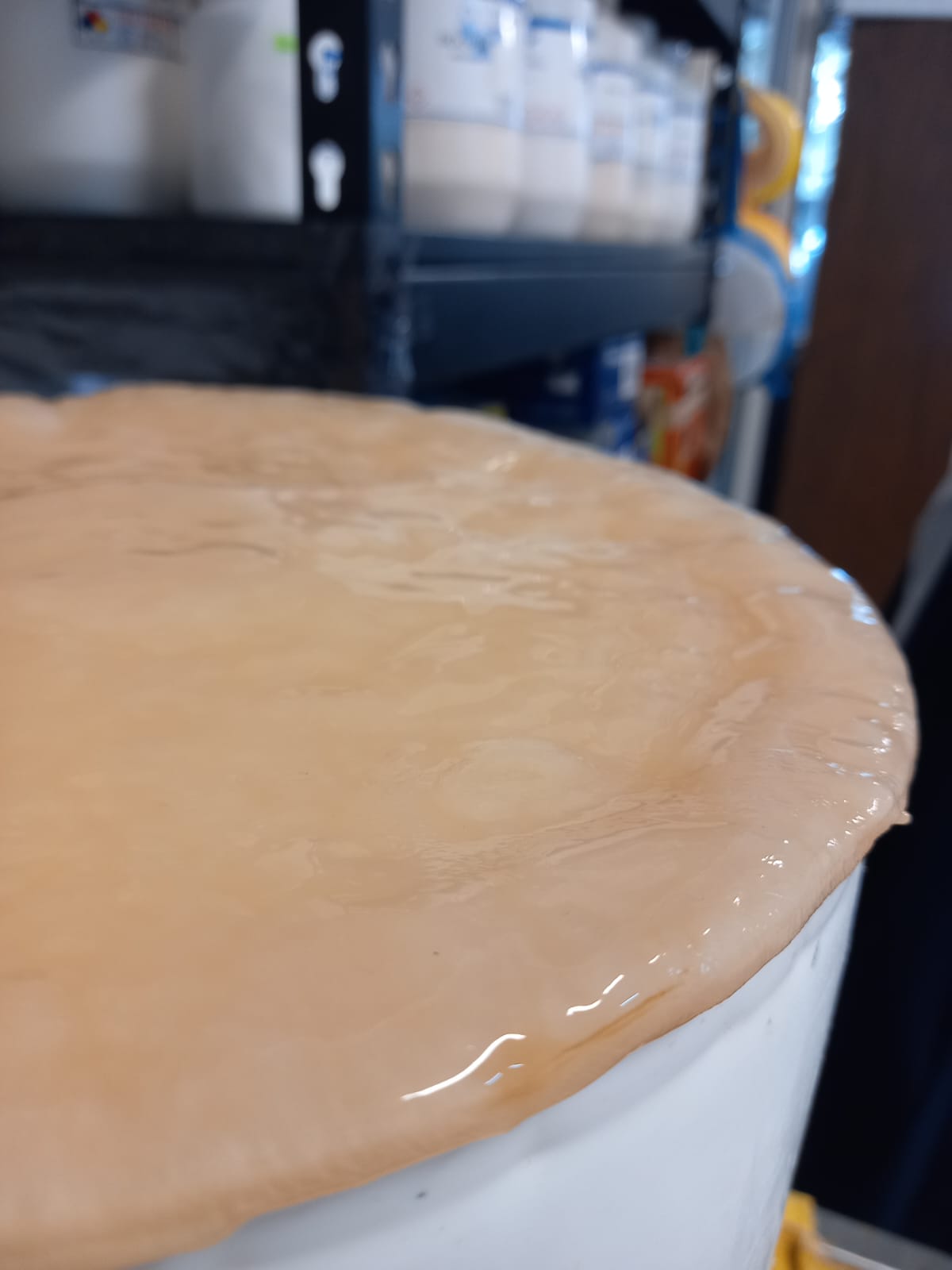
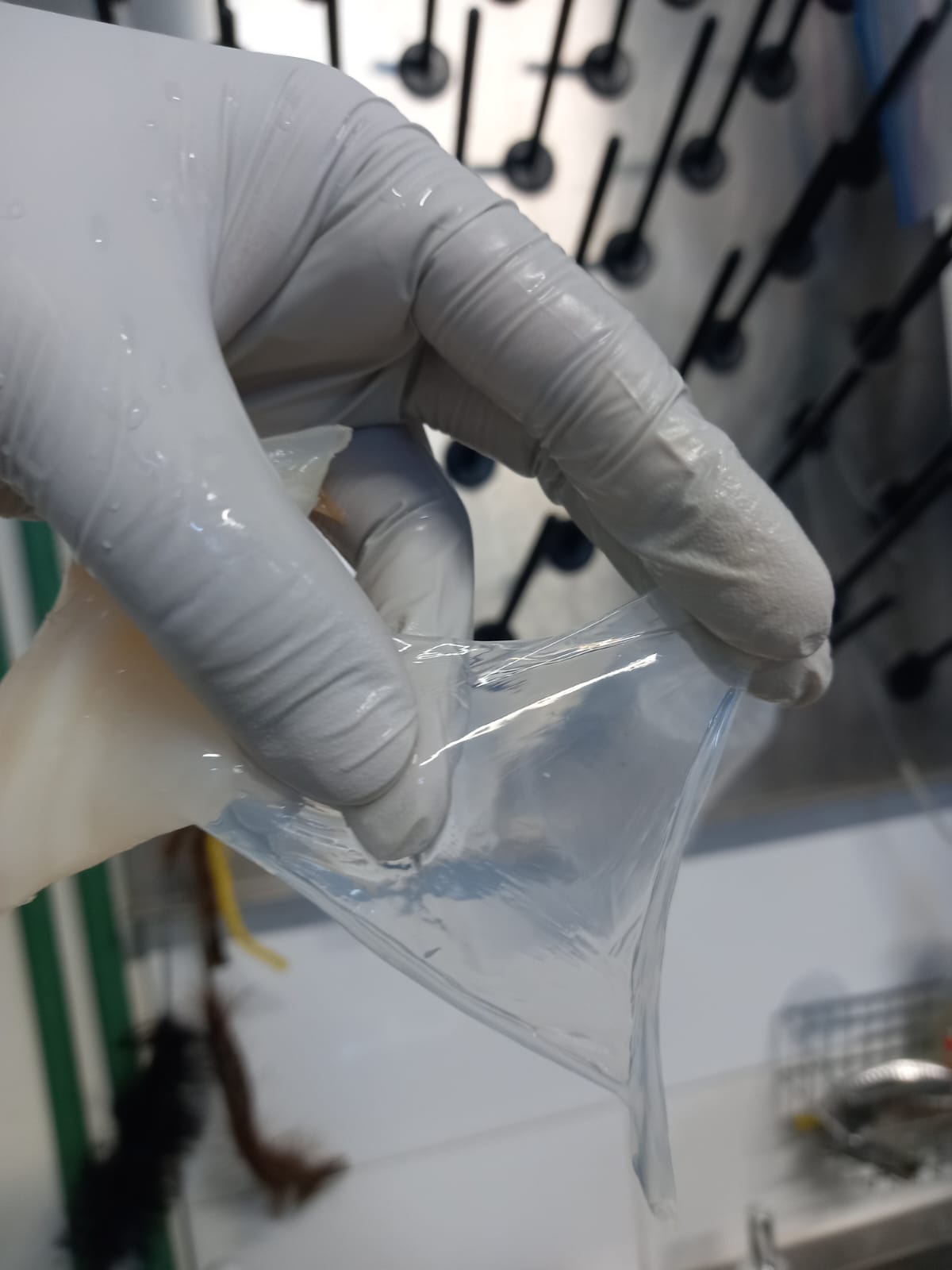
BC presents advantages over plant cellulose because it is lignin-free and has a 3D network woven with nanofibers that increases the surface area-to-volume ratio, providing strong interaction with neighboring components. It offers relatively exceptional mechanical strength, a high degree of polymerization, and crystallinity (around 90%). Similarly, it has an advantage over synthesized materials due to its lack of toxicity and biodegradability [7]. This generates interest in the biomedical field.
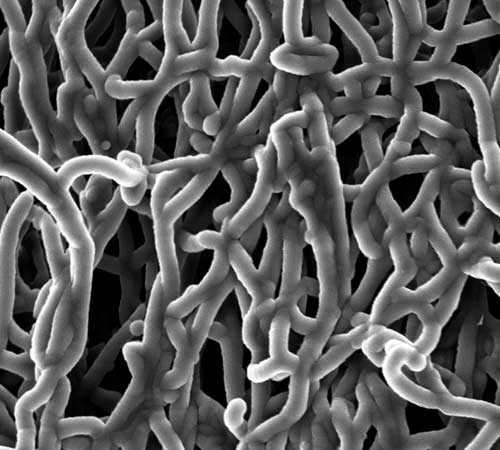
Commercially, it has been used in the development of membranes for wound healing, scaffolds for tissue engineering, artificial blood vessels, and transdermal drug delivery [8].
Preparation of Bacterial Cellulose
Bacterial cellulose was obtained from static bioreactors based on whey provided by Dr. Gregorio Romero de la Vega (professor at Universidad Iberoamericana and academic at IDIT). bioreactors require at least a 15% solids concentration (15°Brix), an initial acidity of 4.9, and are inoculated with 200 ml of the bacteria-yeast consortium at a concentration of 1x10^8 CFU/ml. It is worth mentioning that achieving this minimum concentration requires a period of 20 days under environmental conditions of 1 atm and 25°C without agitation.
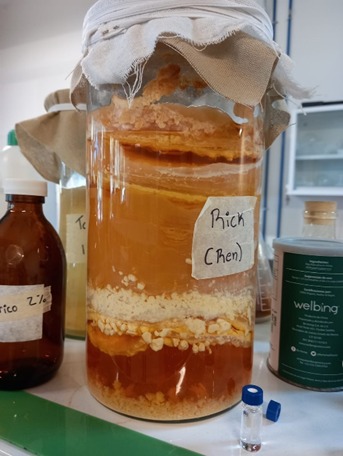
Checkpoint
If a layer is forming on the surface of the bacterial broth, it means the bacterial inoculation was successful. If not, proceed to check the broth according to the previously mentioned parameters.
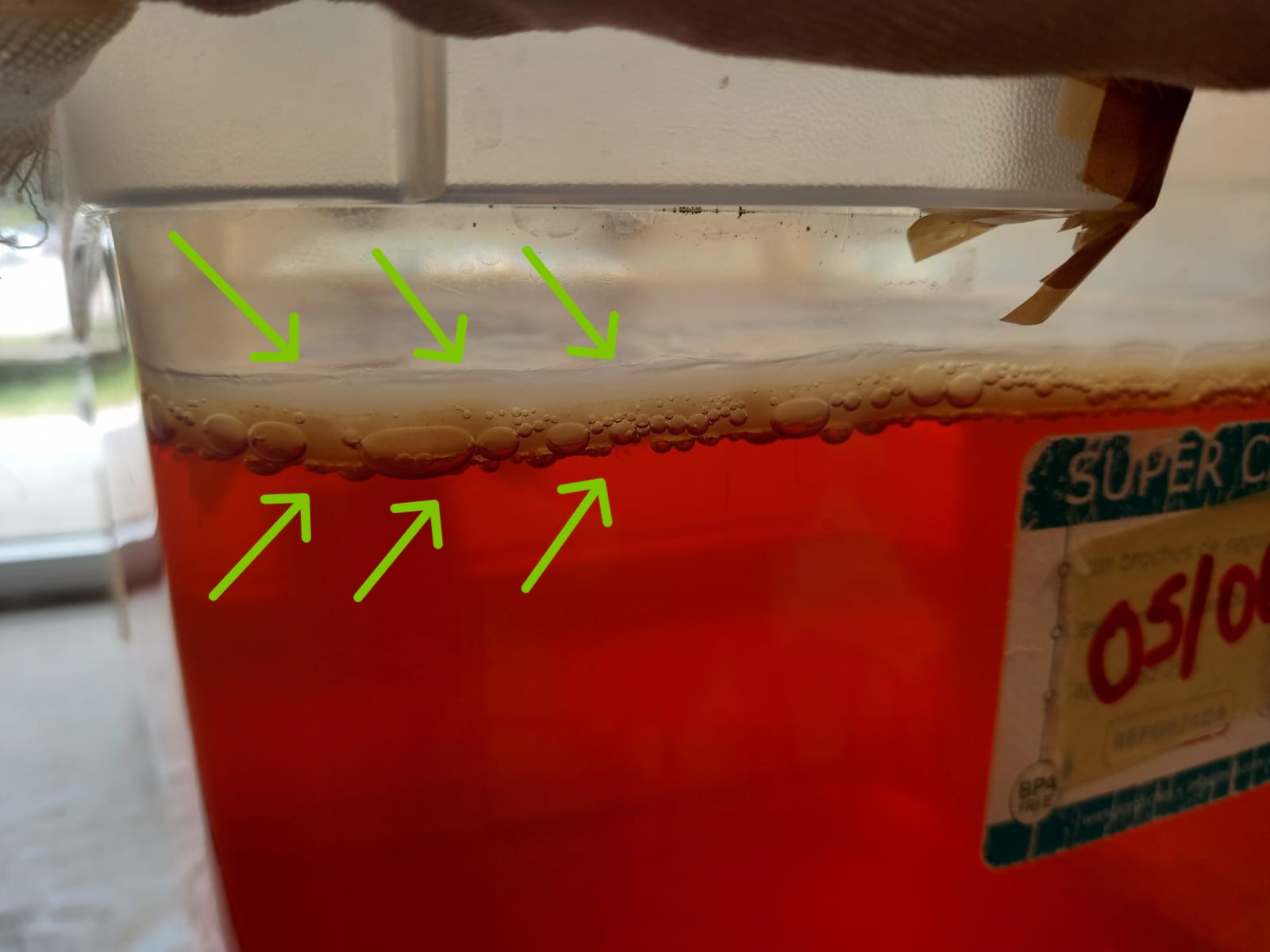
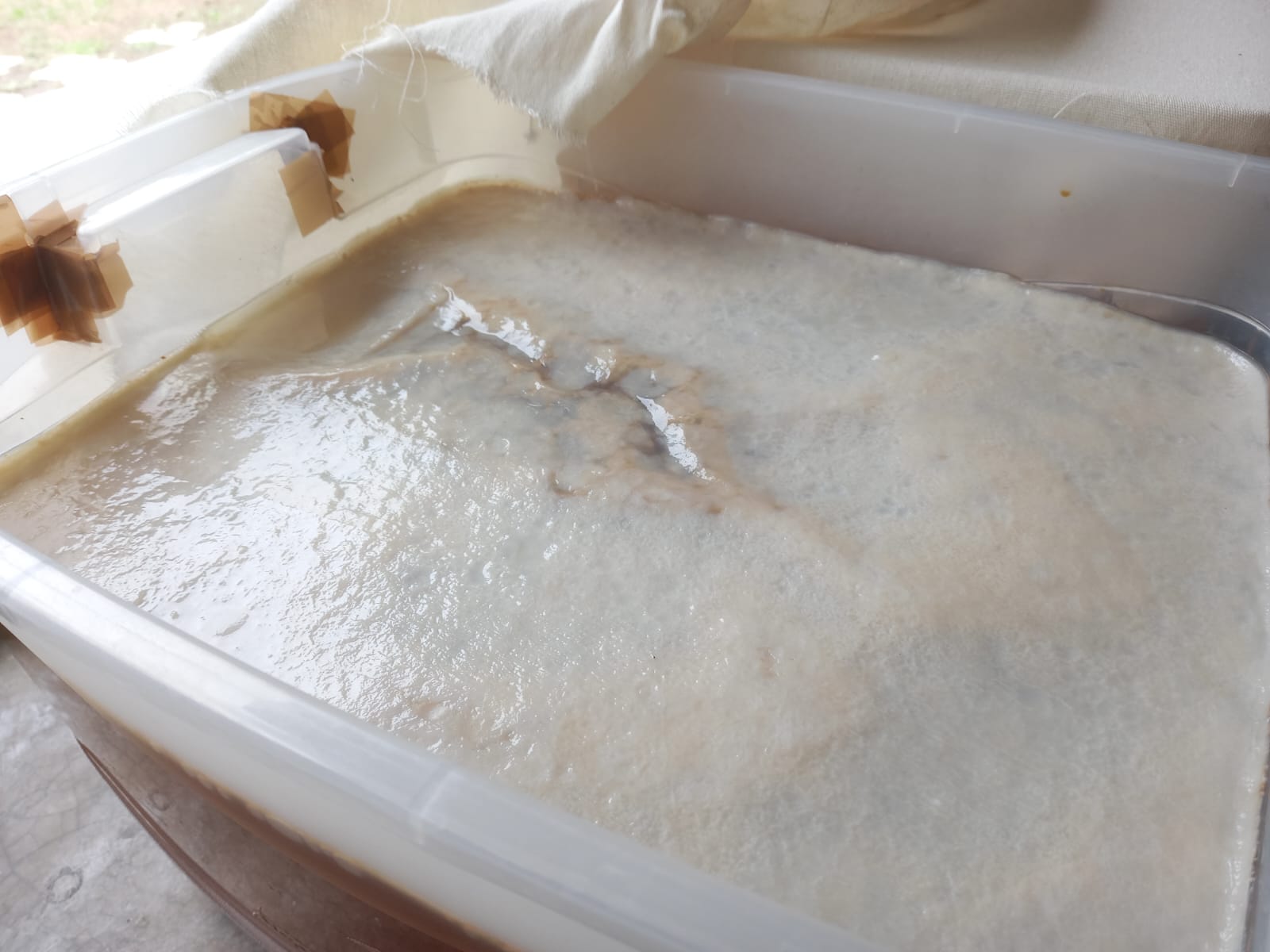
Washing Process
The bacterial cellulose harvested from the static whey-based bioreactors retains residues, such as fat globules and lactose. Therefore, it is conditioned by washing the BC with water and soap.
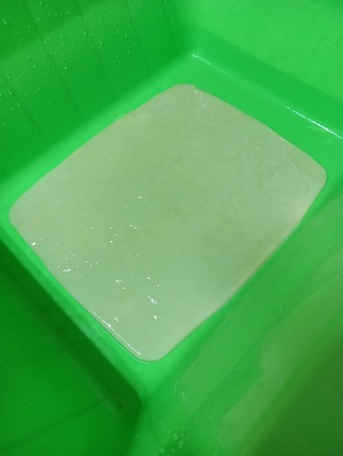

The batch was purified by immersing it in a 10% NaClO solution to remove the residues from the culture medium and the reducing sugars for a period of 4 to 6 days.
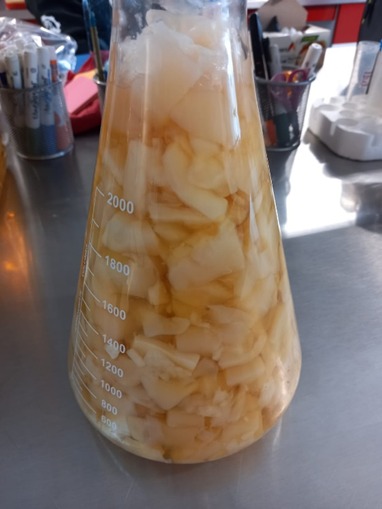
Subsequently, the BC was rinsed with distilled water until the hypochlorite was completely removed. In other words, until the cellulose no longer smells like chlorine. Usually, after 3 washes.
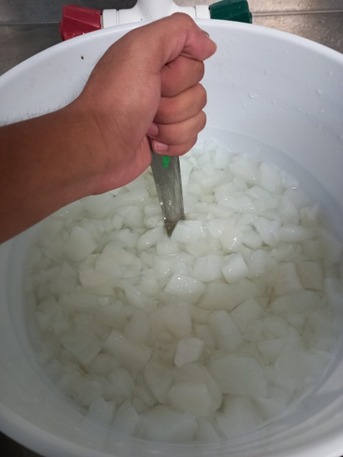

Checkpoint
When the cellulose turns white and no longer has an unpleasant or chlorine smell, in other words, it becomes odorless, it means the previous steps were done correctly.
Grinding process
Later, it was ground, so, I decided to use a hand blender. It is also important to remove the excess water from the bacterial cellulose in preparation for the next production process. In this step, I squeezed the cellulose using a screen-printing fabric, as its fine mesh allows only water to pass through.
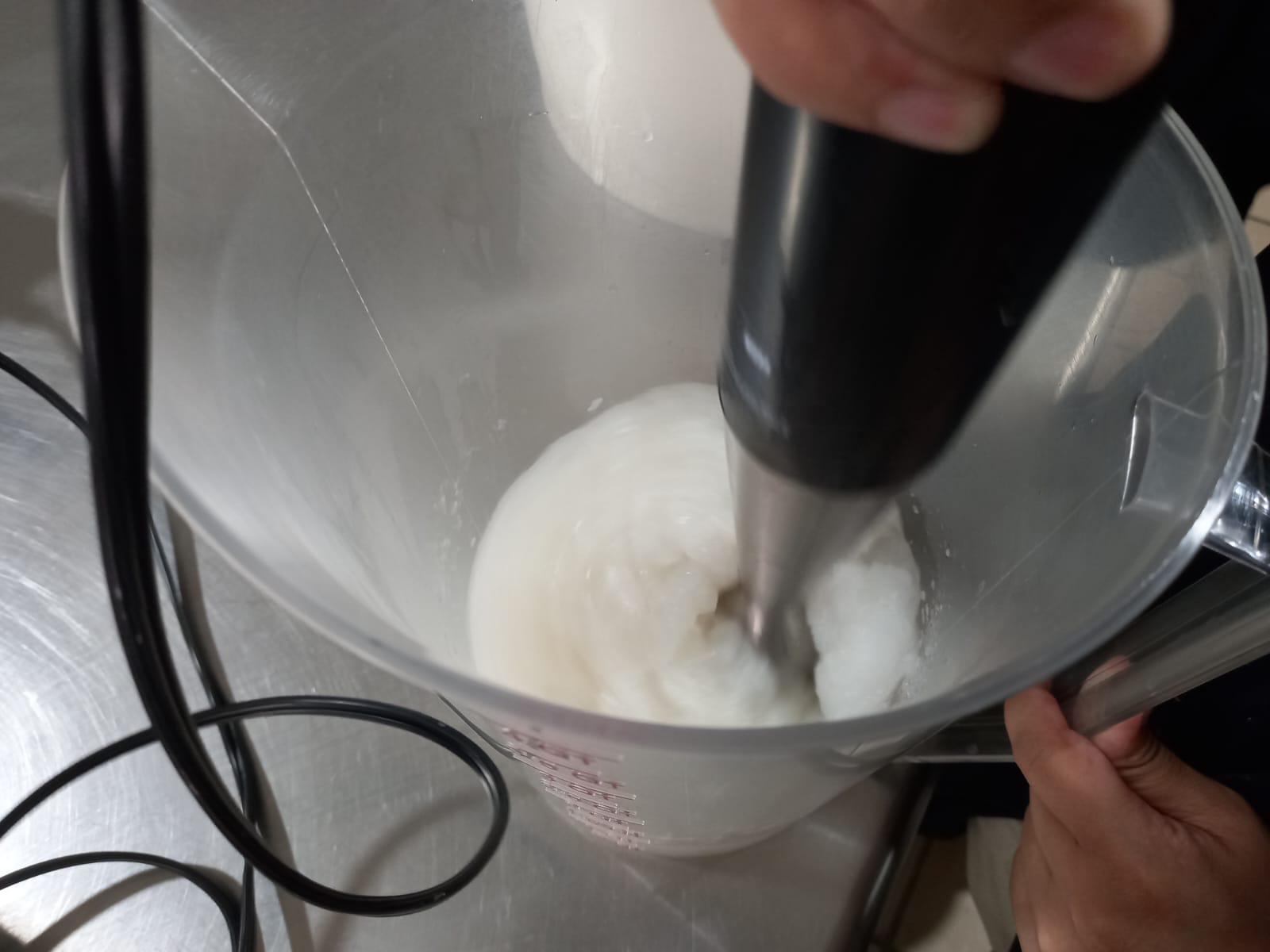
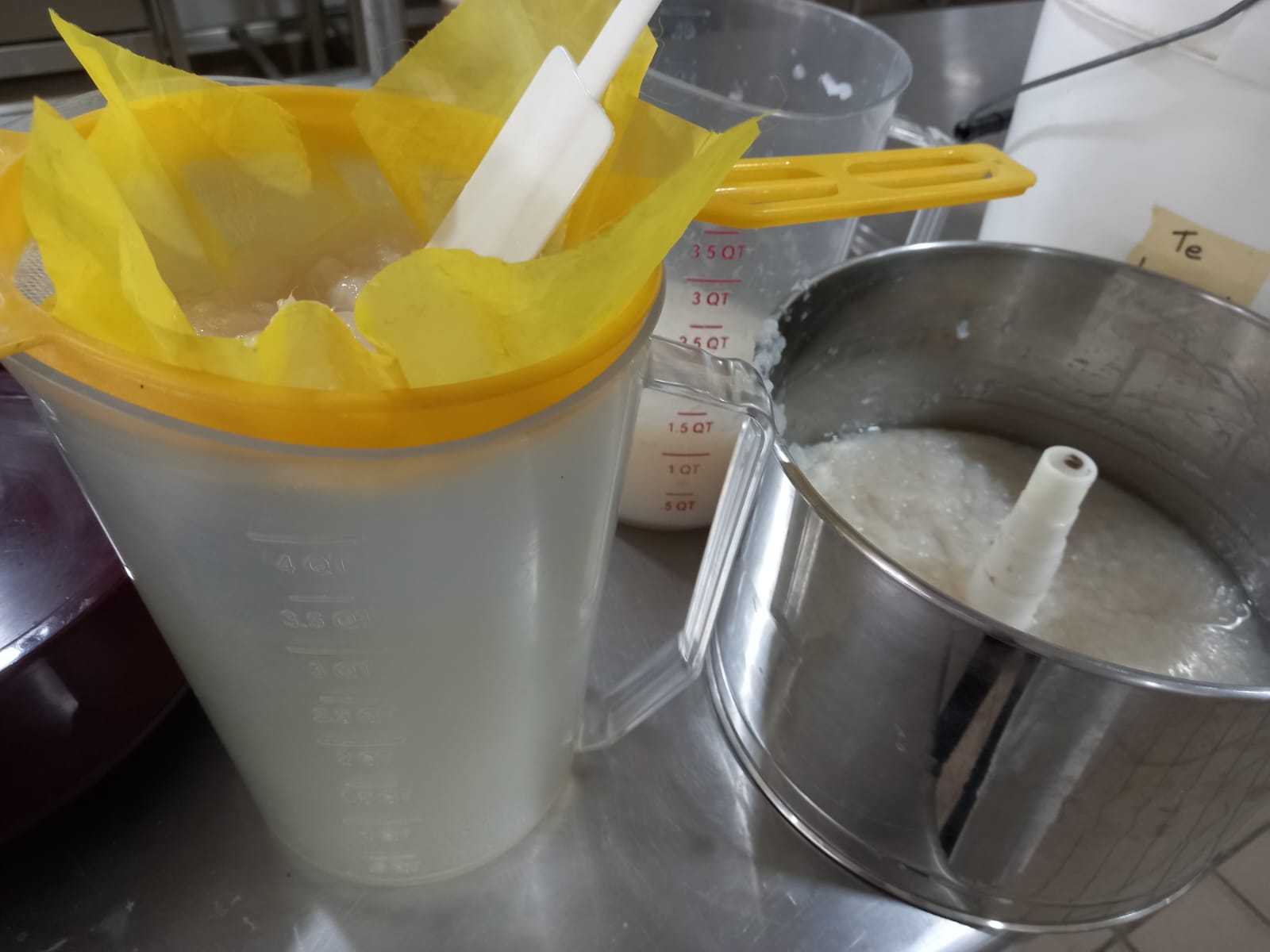
Subsequently, I prepared aluminum trays lined with polyethylene film to prevent the cellulose from seeping through the holes when pouring it with a spatula, and to facilitate easy removal of the cellulose sheet.
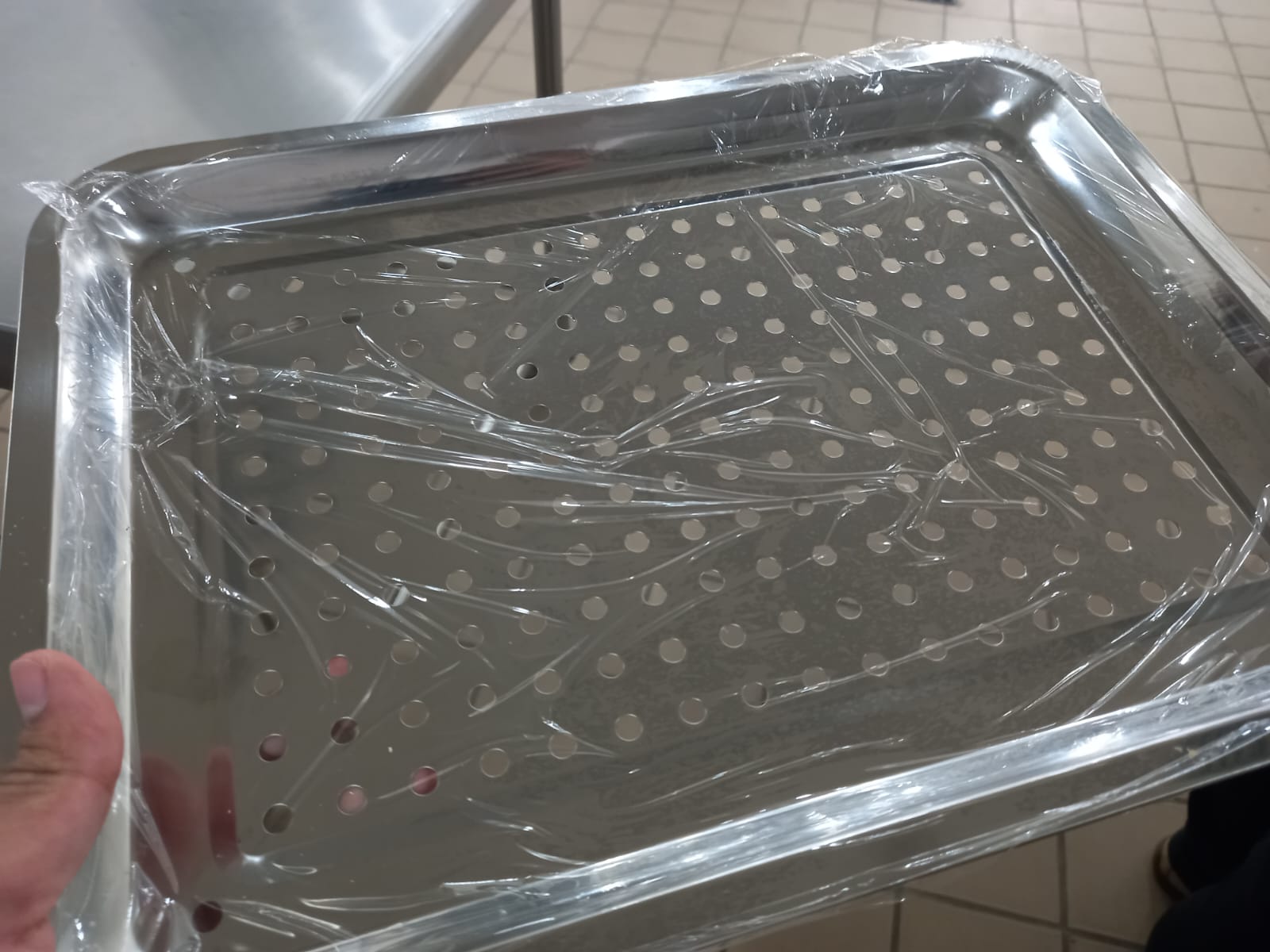
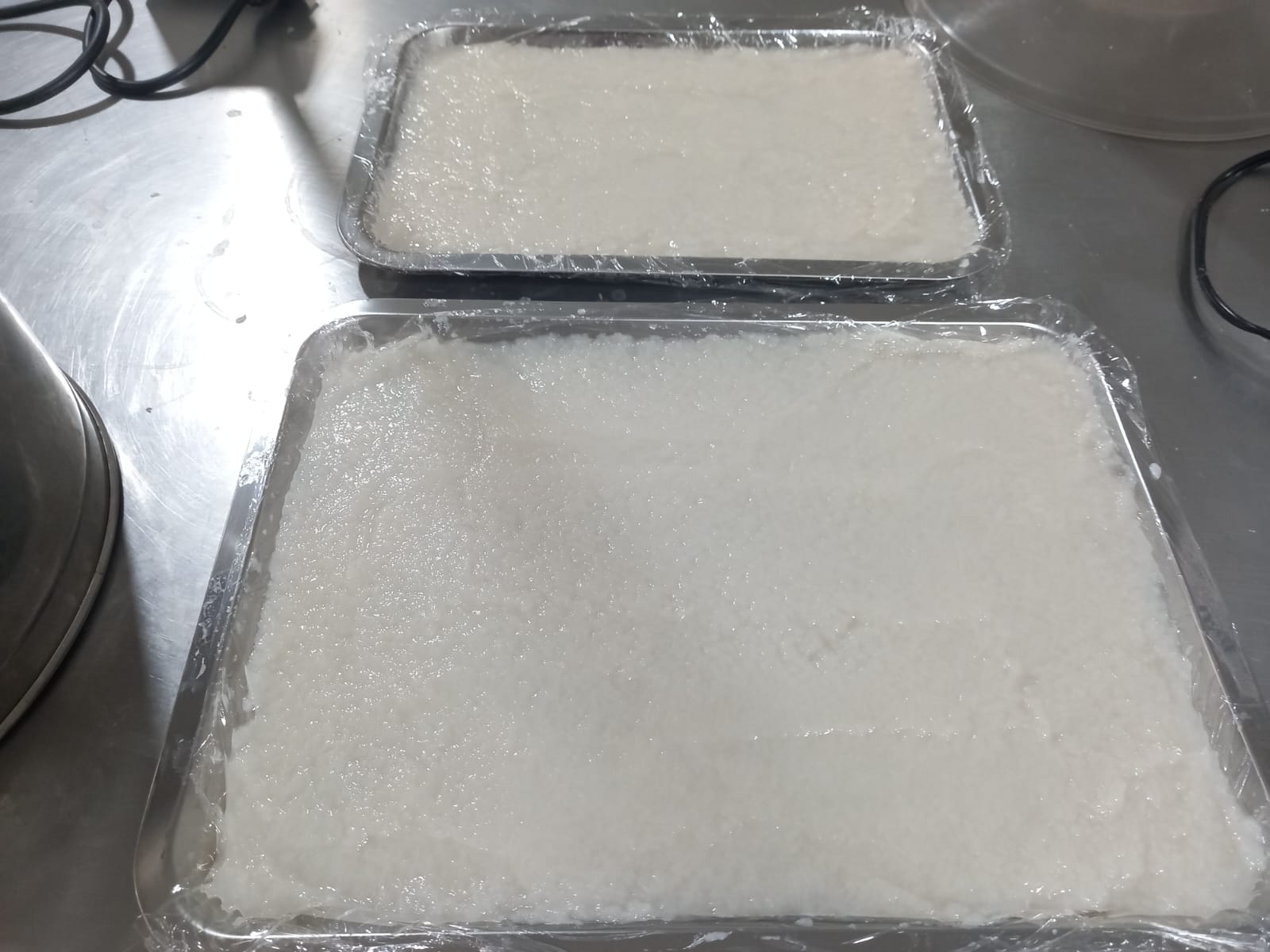
Checkpoint
The cellulose should be like a watery paste, with no large clumps or pieces of cellulose. This ensures a uniform final appearance.
Then...
We leave the material in an ultrafreezer for approximately 2 days at -80°C or -112°F in preparation for lyophilization.
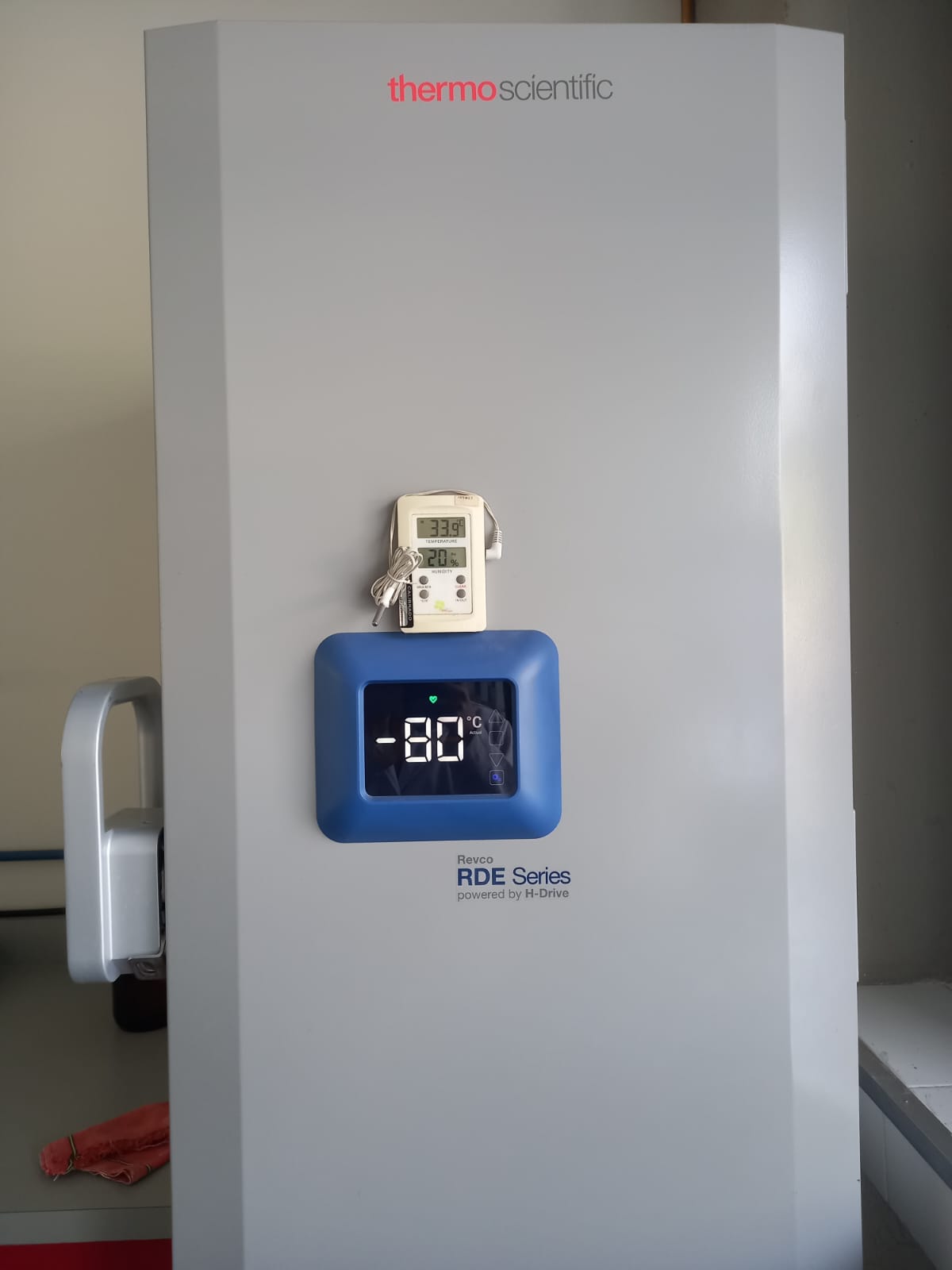
Lyophilization
Lyophilization, also known as freeze-drying or cryodesiccation, is a dehydration process primarily used to preserve perishable foods or make materials easier to transport. This method involves freezing the material and then reducing the surrounding pressure to allow the frozen water to sublimate directly from the solid phase to the gaseous phase, bypassing the liquid state.
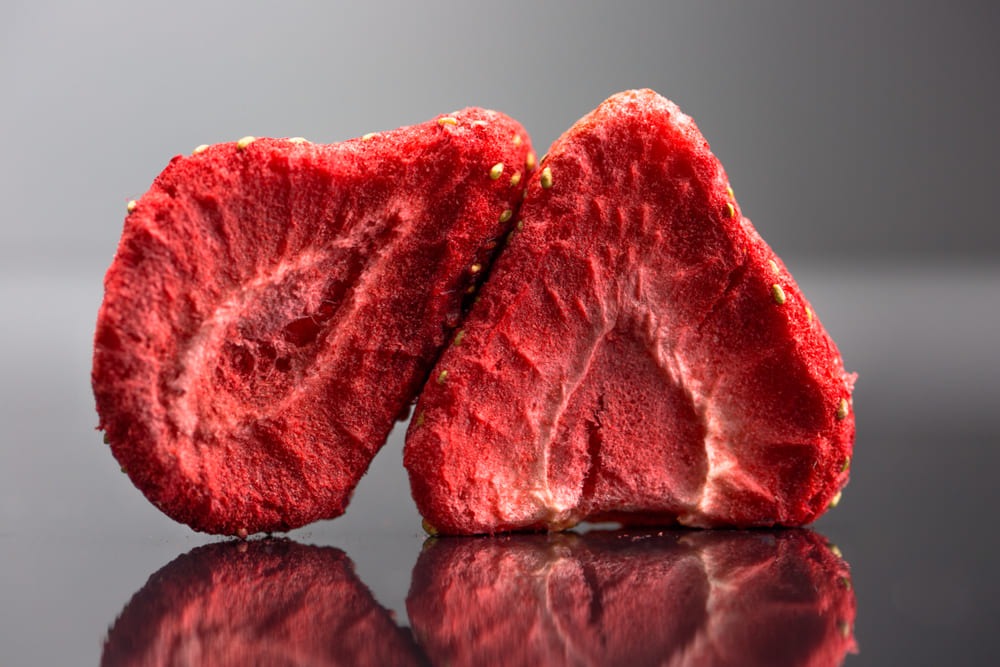
So take your sample and prepare the machine! In the University we have the Lyophilizer Freezone by Labconco.
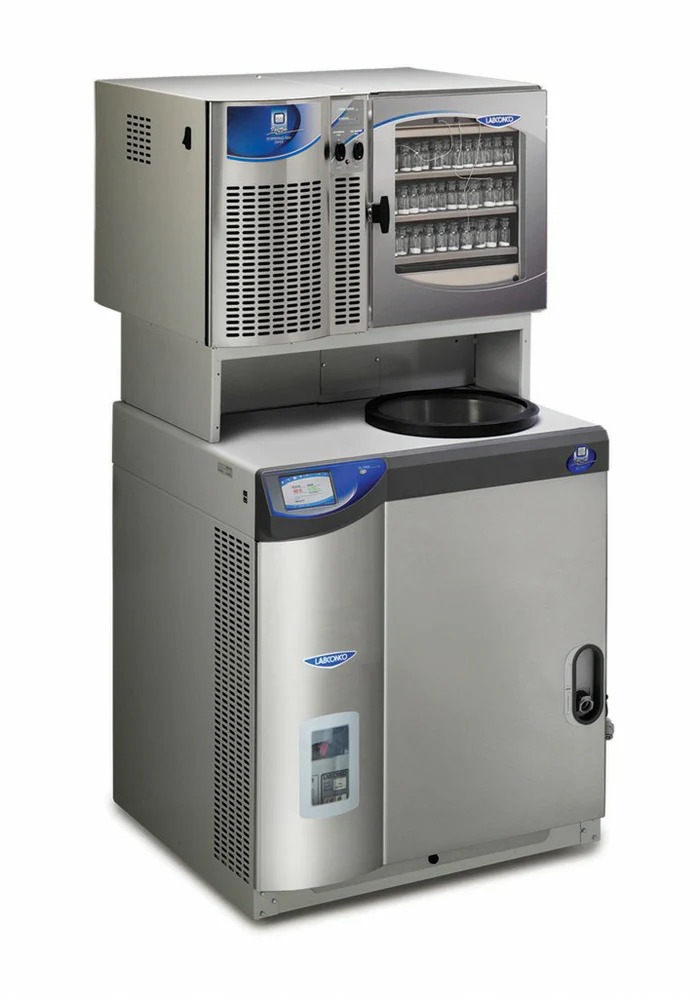
Close the air intake valve (marked in green) and turn on the switch on the side.
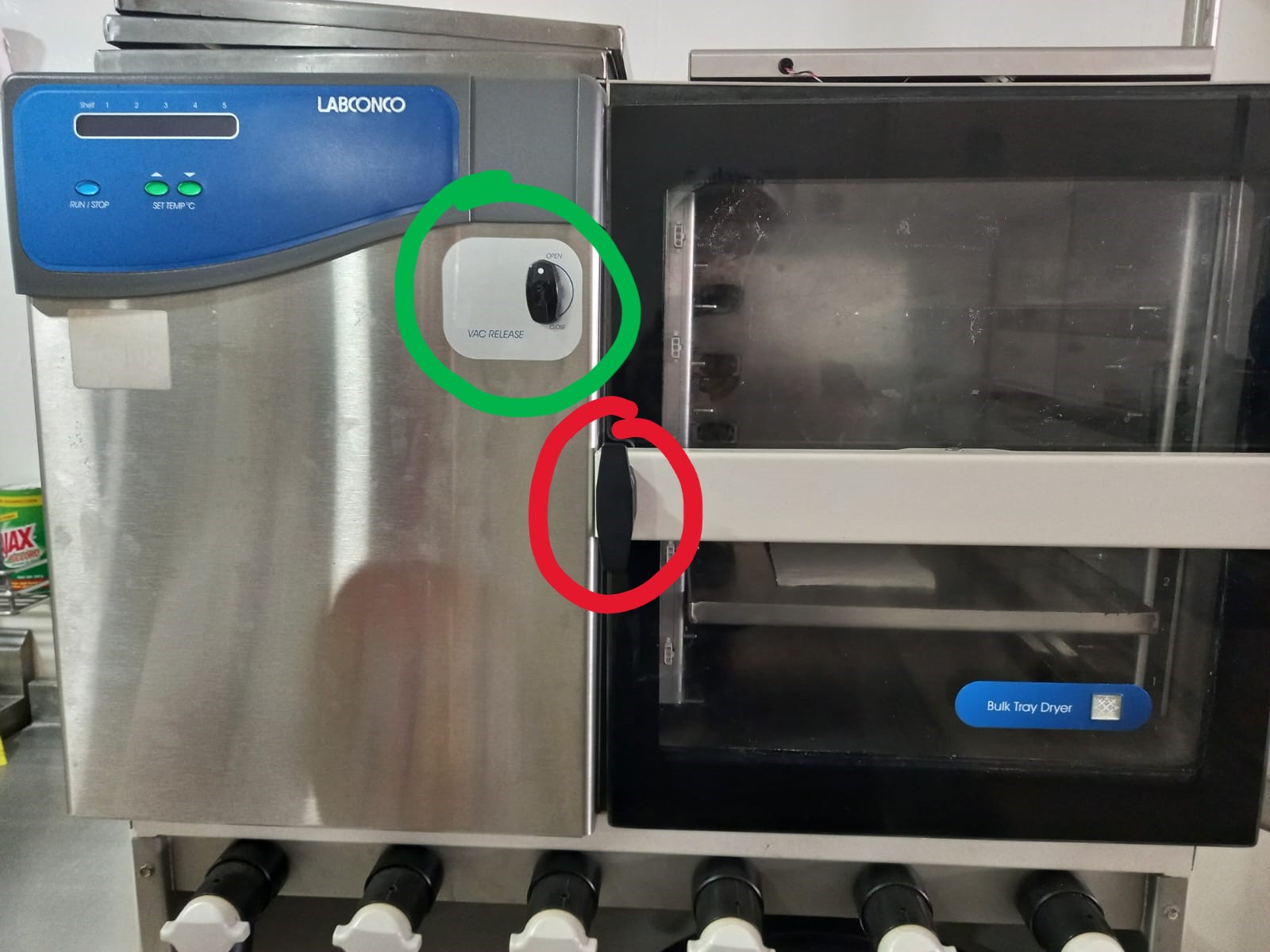
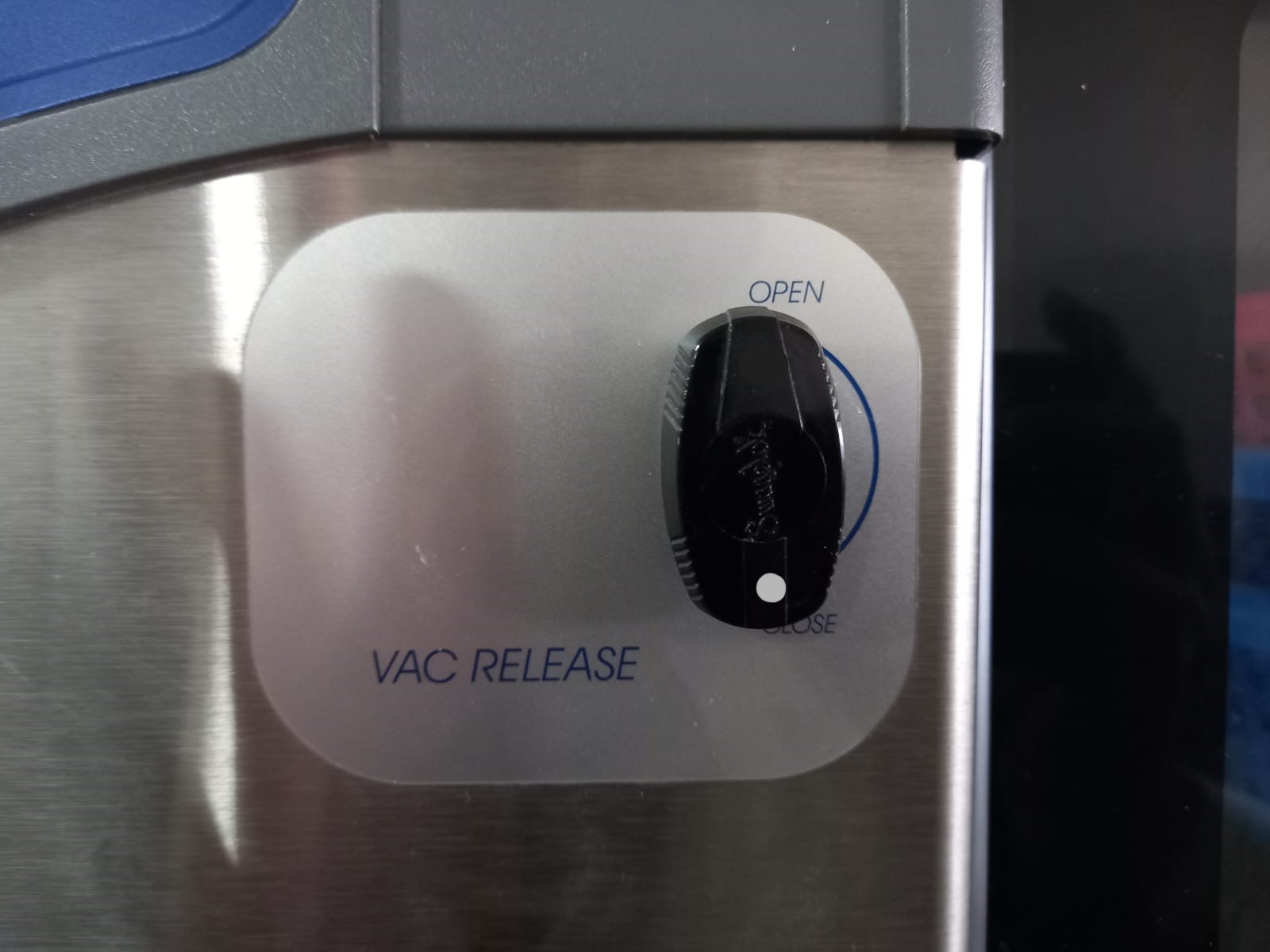
Turn to close.
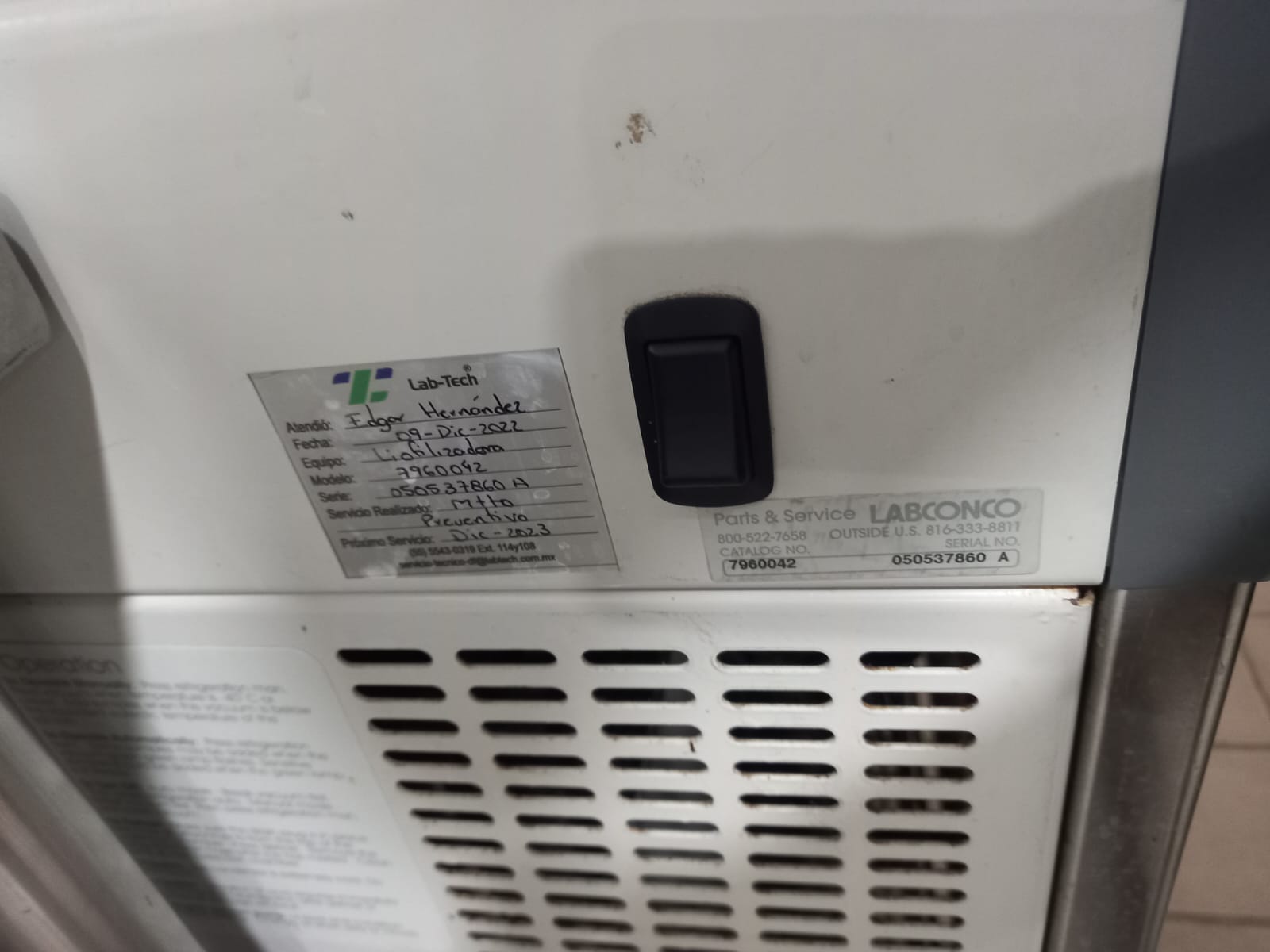
Once the screen lights up, open the drying chamber by turning the valve (marked in red), place your sample inside, and close the chamber by turning the same valve. Note: Ensure that the lid is properly attached to the drying chamber.
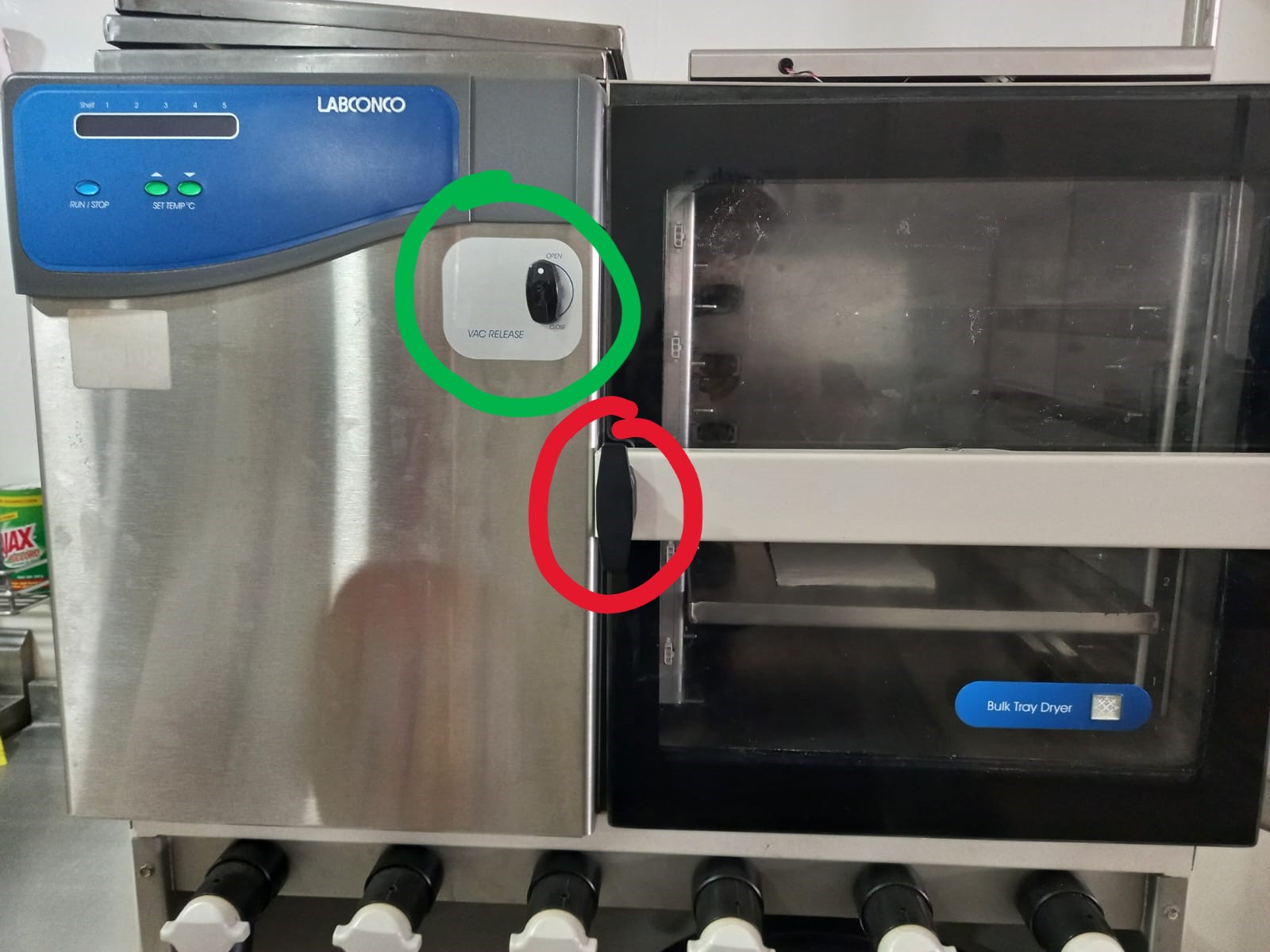
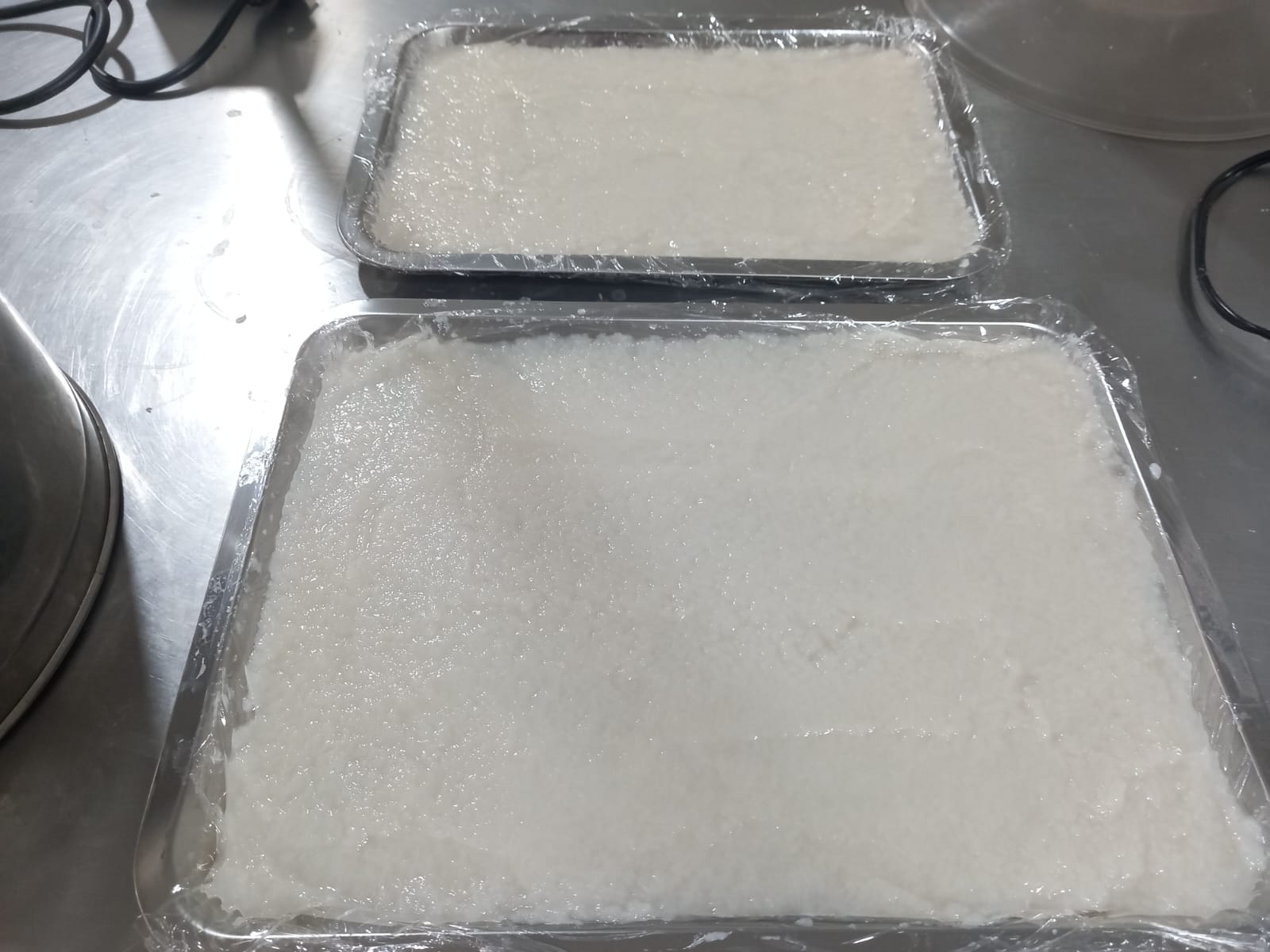
Additionally, the condenser does not have a lock but uses a rubber seal to create an airtight closure. The seal must be tight to maintain a good vacuum.
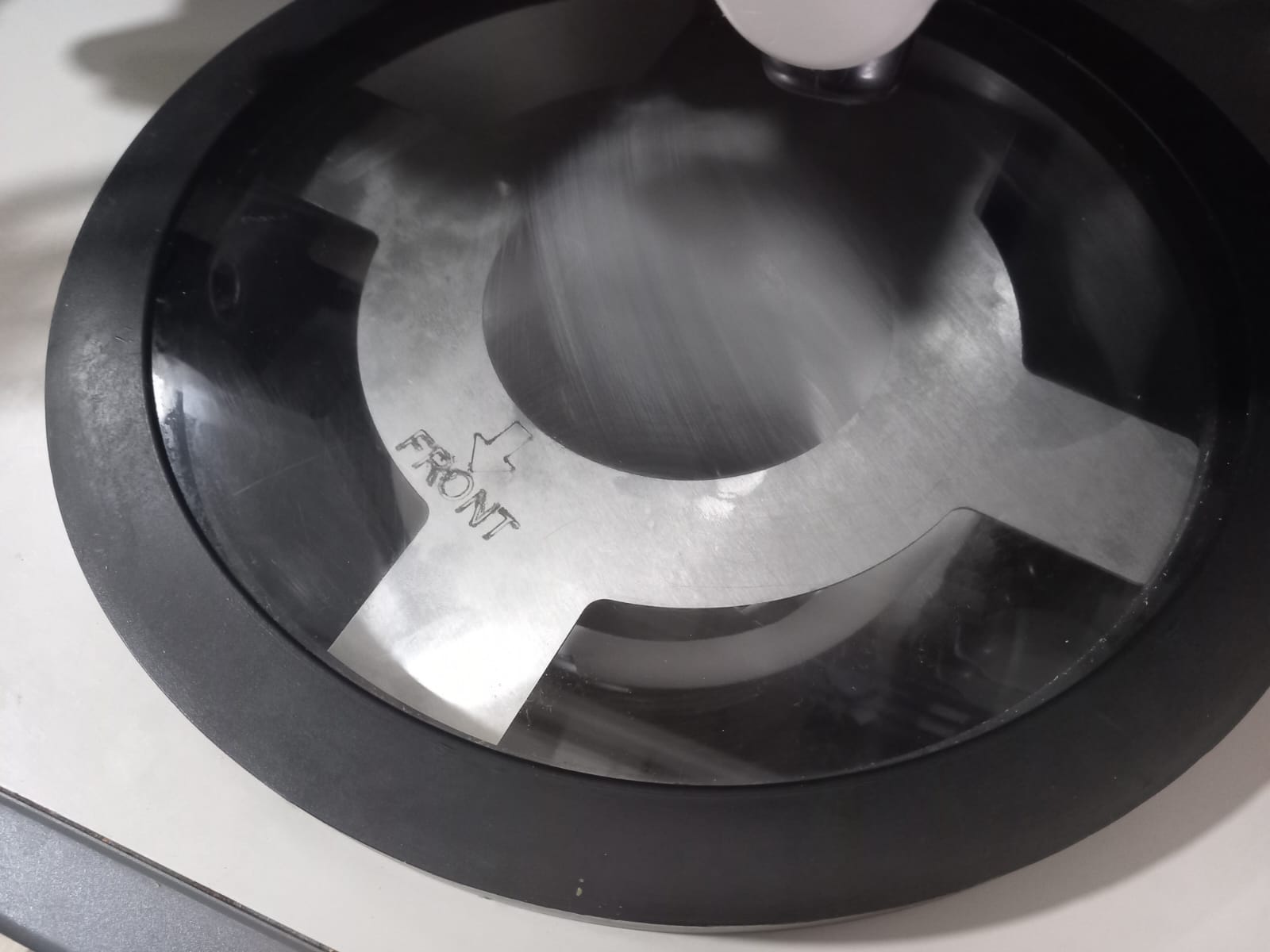
Next, set the refrigeration to "auto" and turn on the vacuum. You should hear a sound like the door sealing tightly, indicating the vacuum is working. The indicators will light up as the vacuum increases and the temperature decreases. The vacuum should reach 0.0035 millibars, and the collector temperature should drop to -60 degrees Celsius. Once these conditions are met, which takes approximately 15-20 minutes, the lyophilization process will be in optimal conditions, although it starts earlier.

After 24-36 hours or when you are ready to remove your sample, turn off the refrigeration and the vacuum. Then, open the air intake valve (marked in green) and let the air in. Once the air has entered, you can open the chamber by turning the valve (marked in red) and remove your sample. My advice: Store the sample in a zip-lock bag to prevent it from rehydrating, as it will be hygroscopic and should have lower moisture content than the ambient environment.
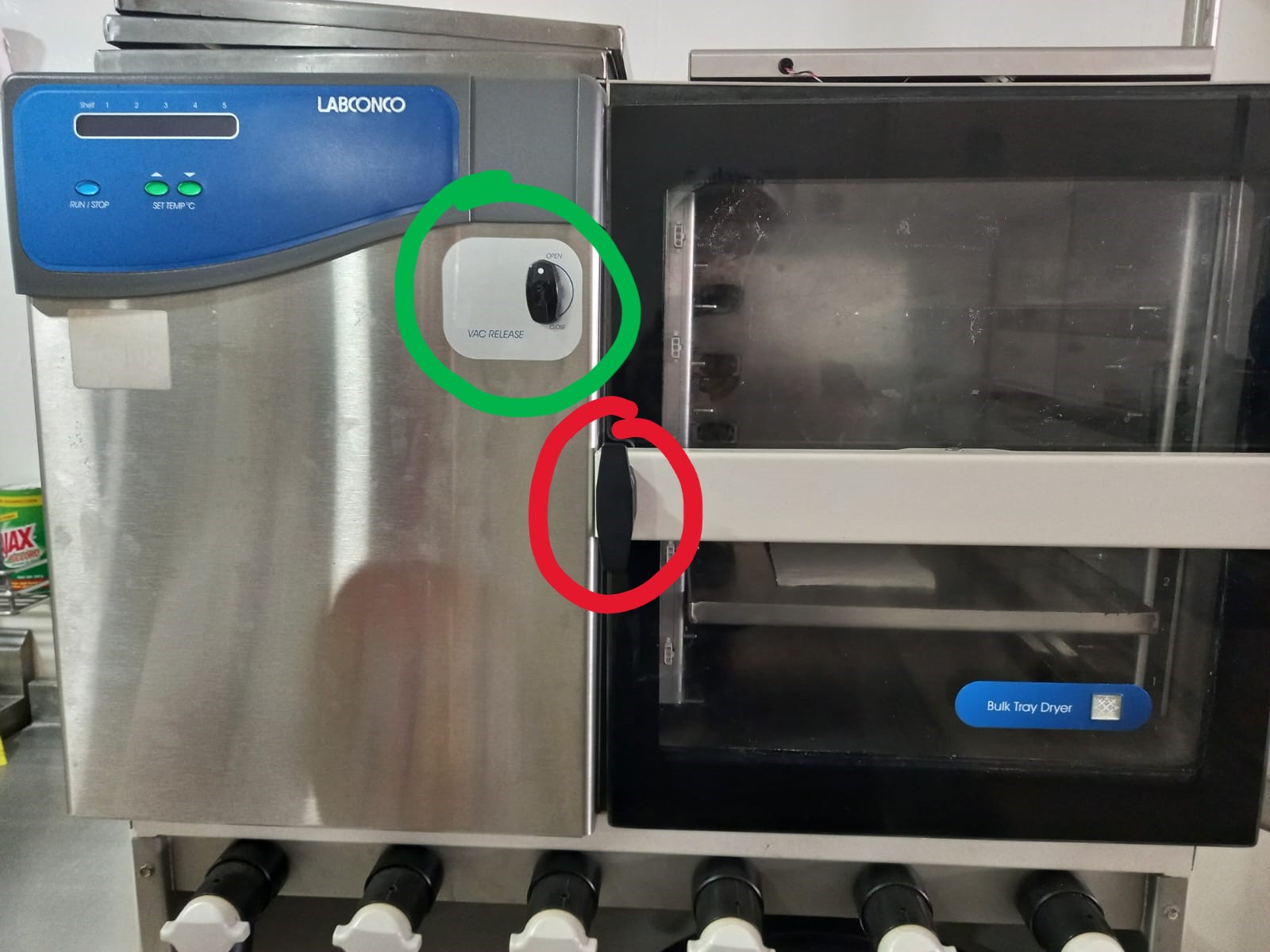
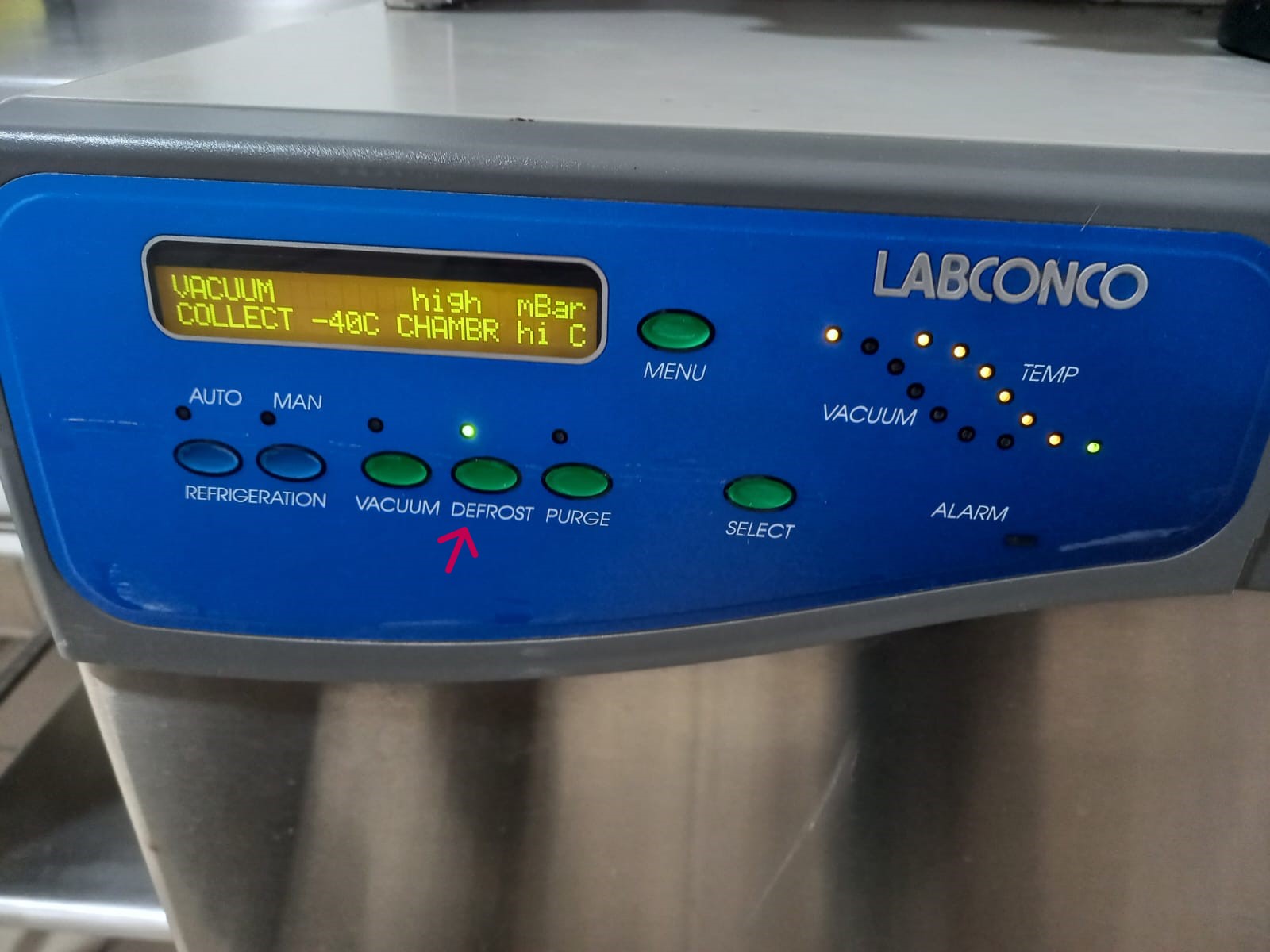
Finally, set the lyophilizer to defrost. The defrost function melts any remaining ice on the coils by running hot water through them, allowing you to clean the unit properly. Don't forget to close the air intake valve (marked in green).
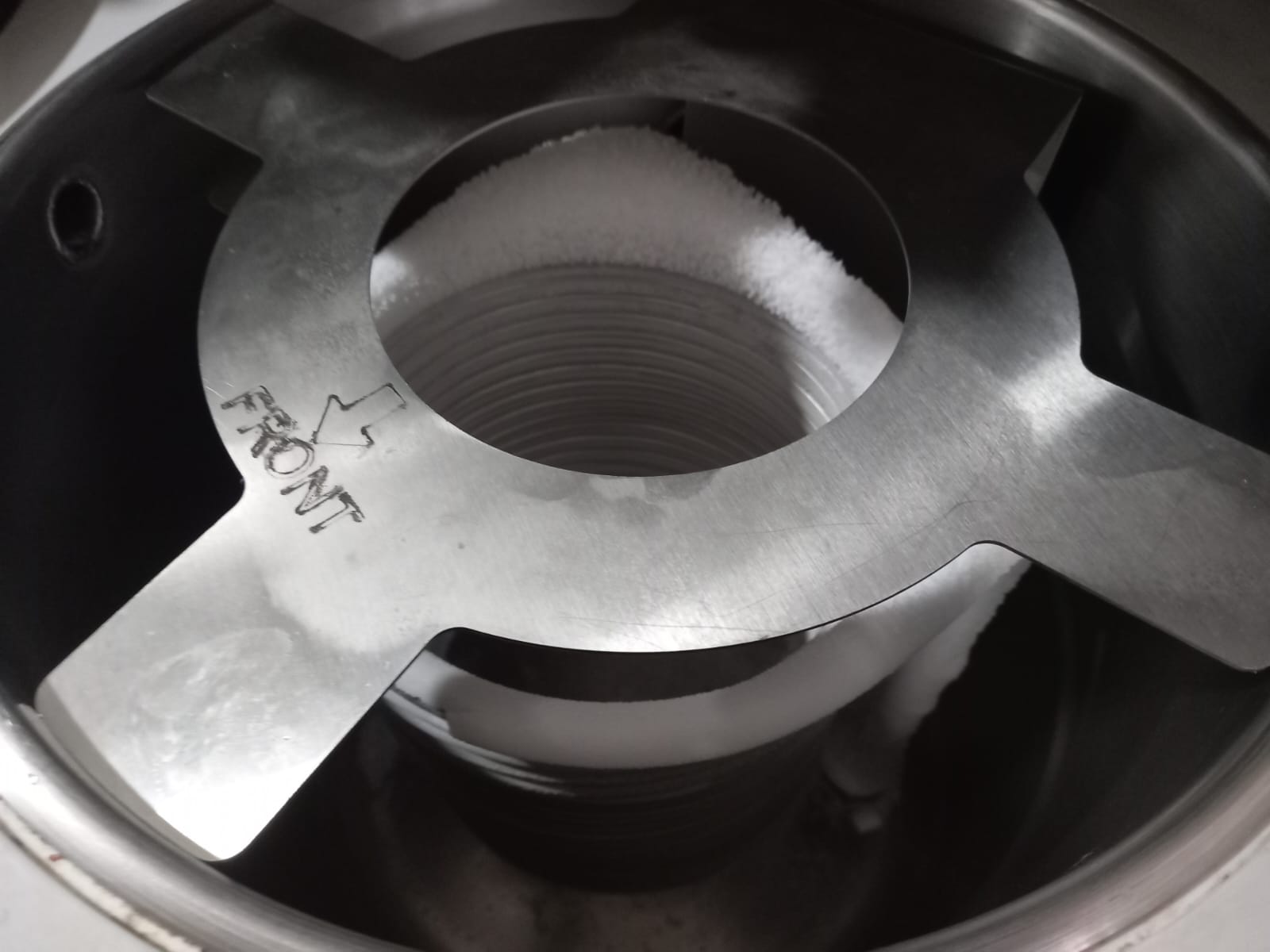
Checkpoint
As mentioned, the cellulose is capable of absorbing more than 90% of its weight in water. Therefore, after freeze-drying, it should be completely dry, as shown in the following image.
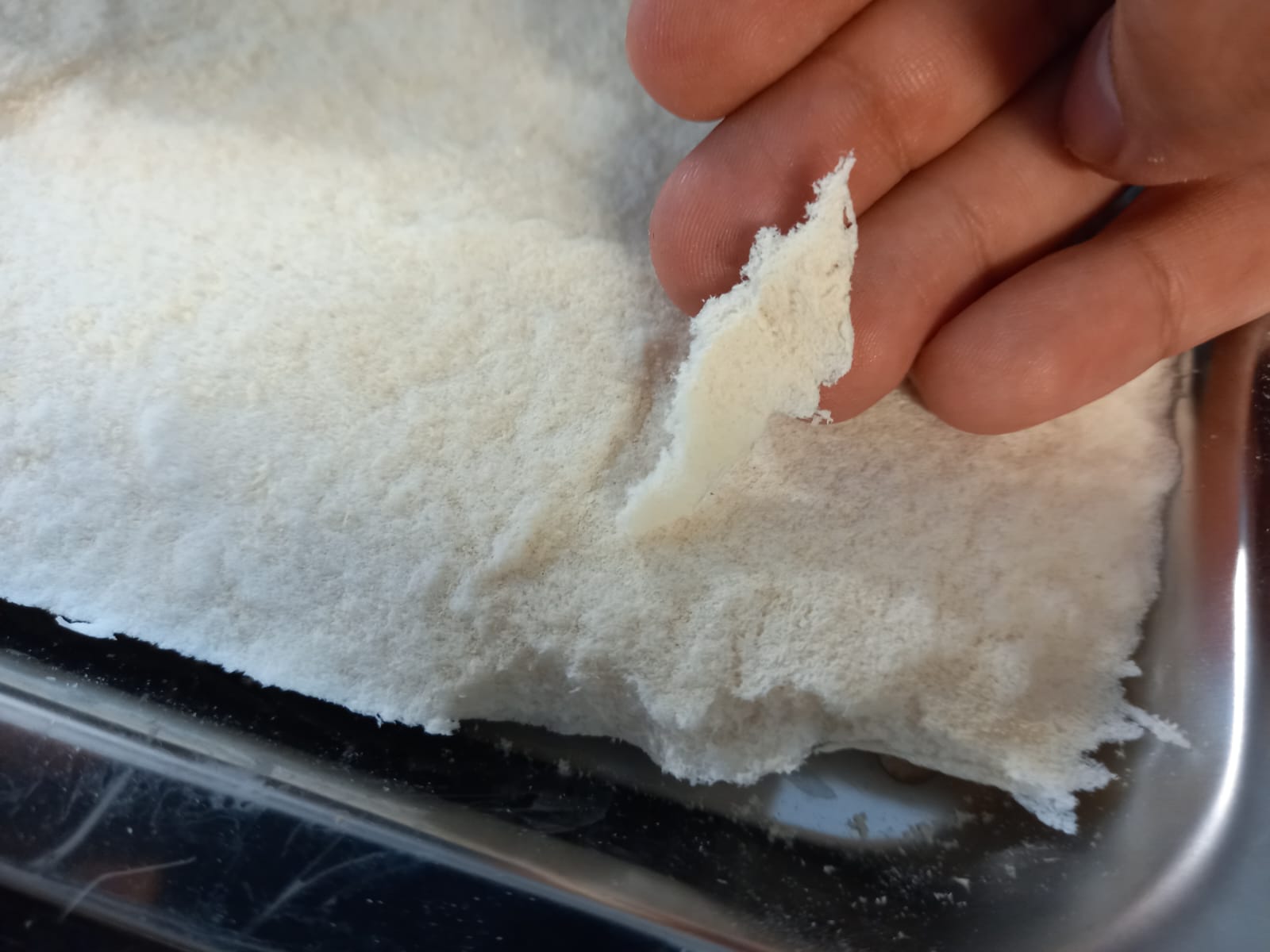
Final
Our goal is to obtain cellulose and store it for a long time. If the cellulose is left in water without proper care, such as a sterile environment, fungi can easily grow around the bacterial cellulose, rendering it unusable for laboratory purposes. Thanks to the freeze-drying process and the careful review of each step, we confirm that the product has been made with the quality needed for long-term storage. We recommend storing it in an airtight bag.
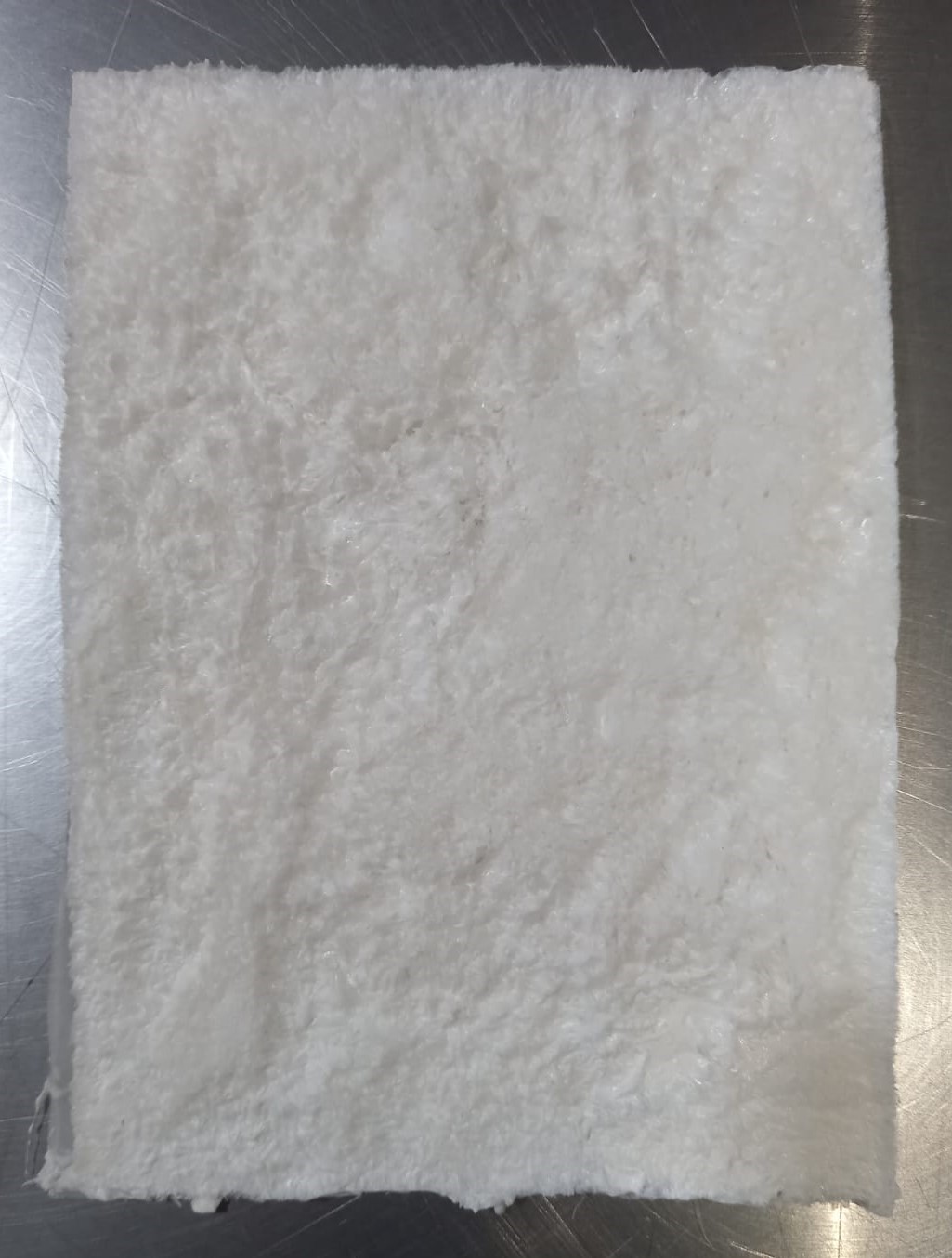
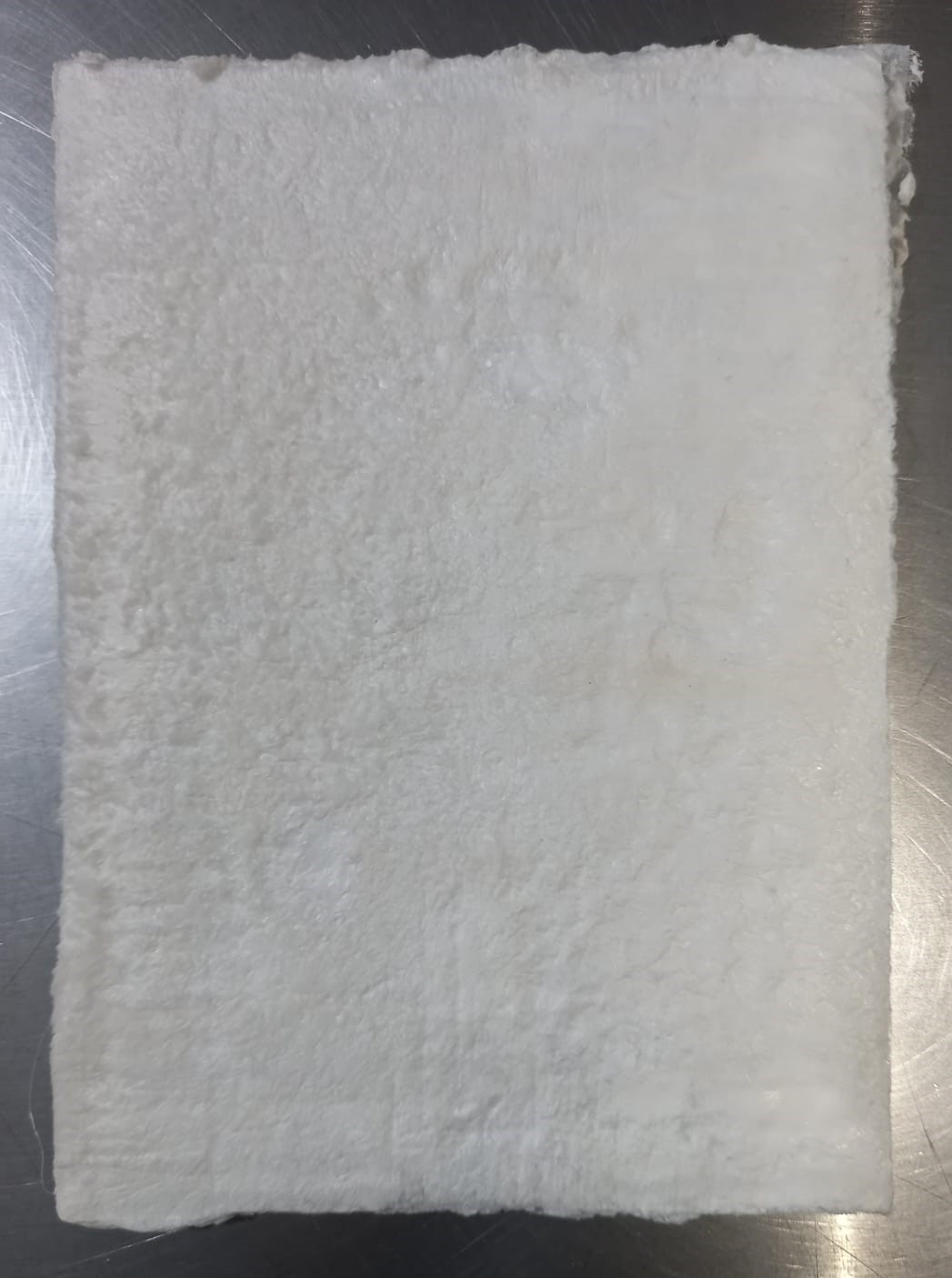
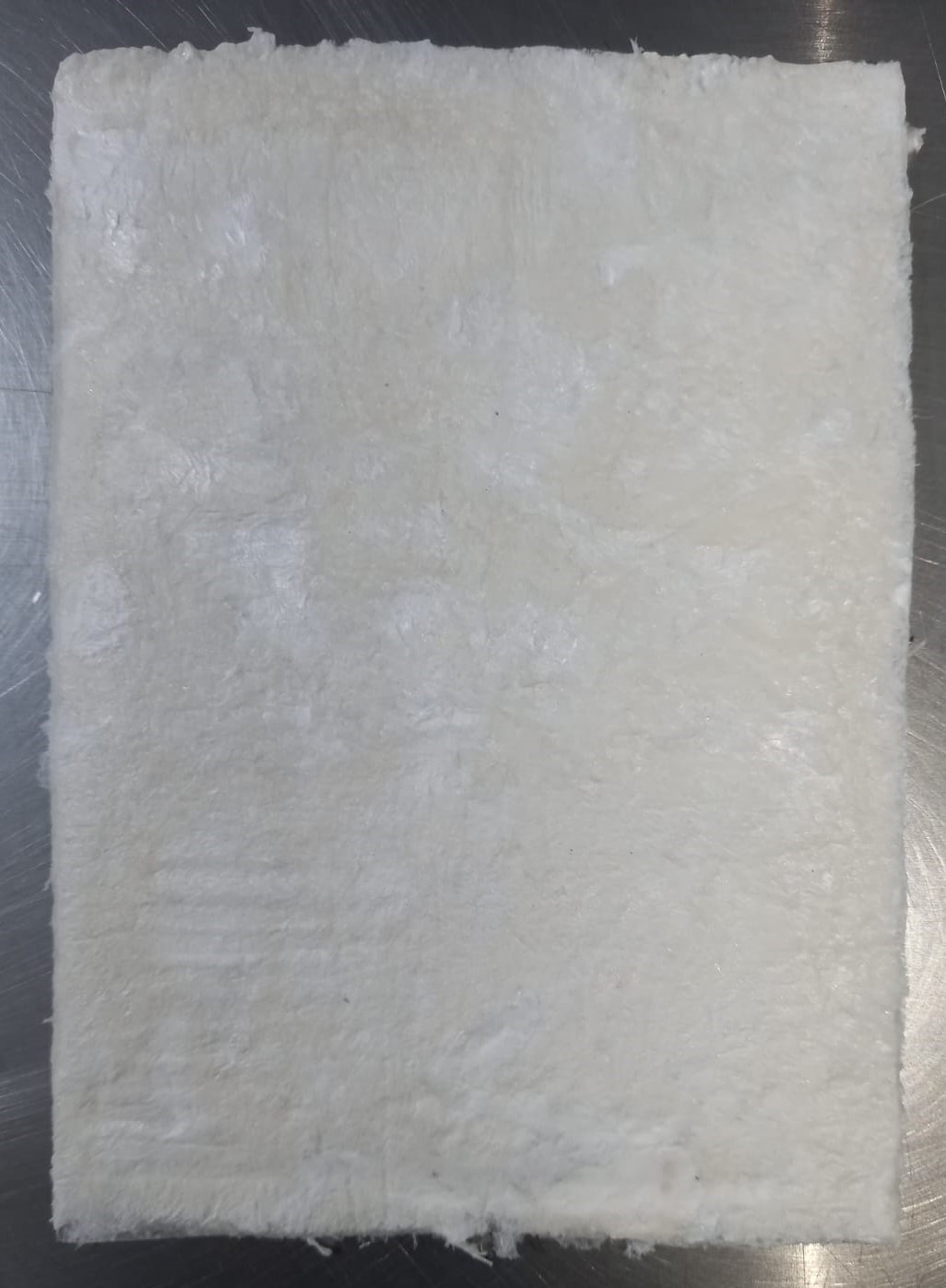