15. Wildcard
Week asignments
Individual assignment: Design and produce something with a digital process (incorporating computer-aided design and manufacturing) not covered in another assignment, documenting the requirements that your assignment meets, and including everything necessary to reproduce it.
CNC Lathe
I visited my alma matter for producing a metal part by revolution and substraction
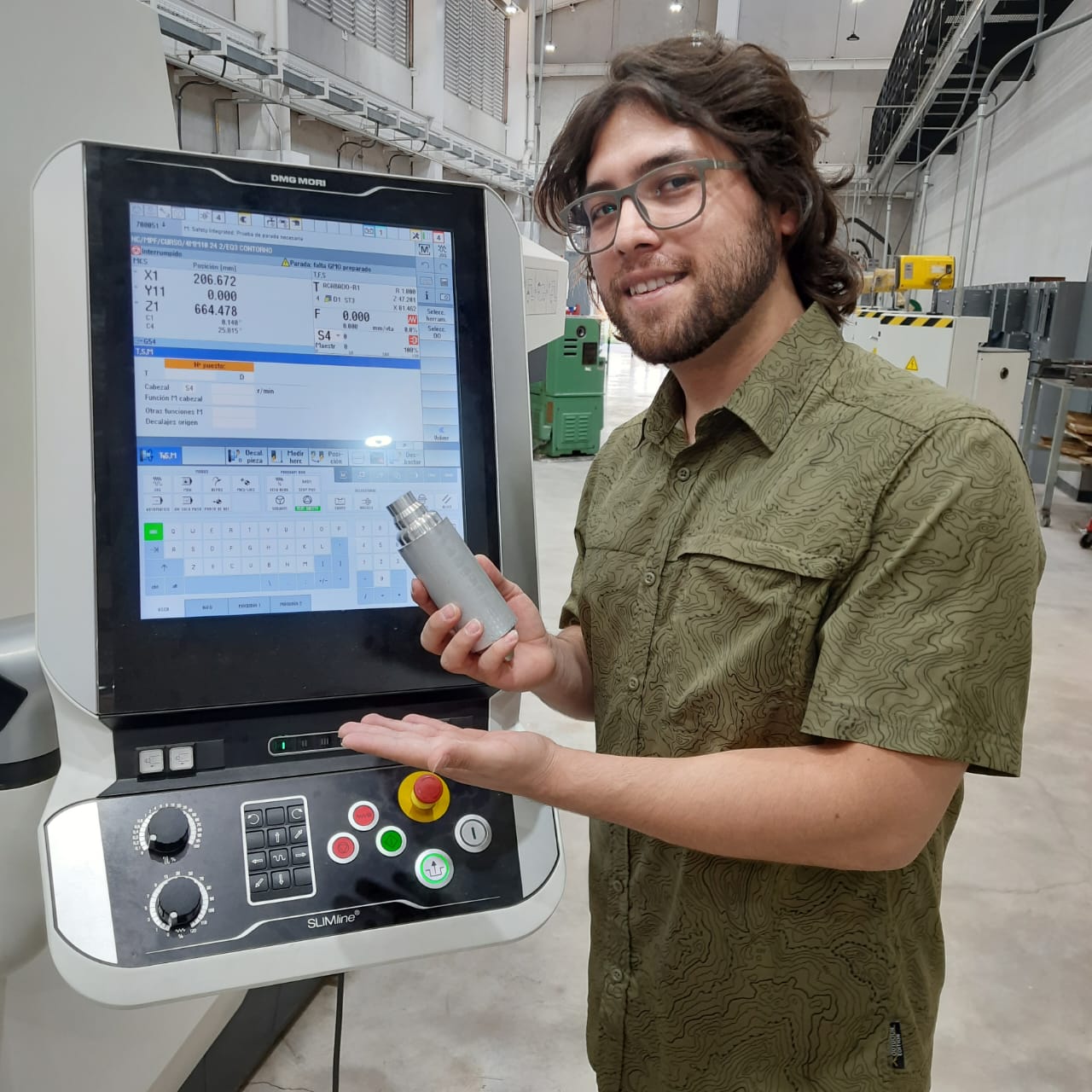
HOW DOES IT WORKS?
A CNC lathe automates machining operations by rotating a workpiece (usually metal or plastic) on its axis. This piece normally has a cylindrical shape. I will be using Aluminum. Then the cutting tool, controlled by computerized commands, moves in different directions (X, Y, and Z axes). It removes material from the workpiece.This process creates precise features like threads, grooves, or contours.
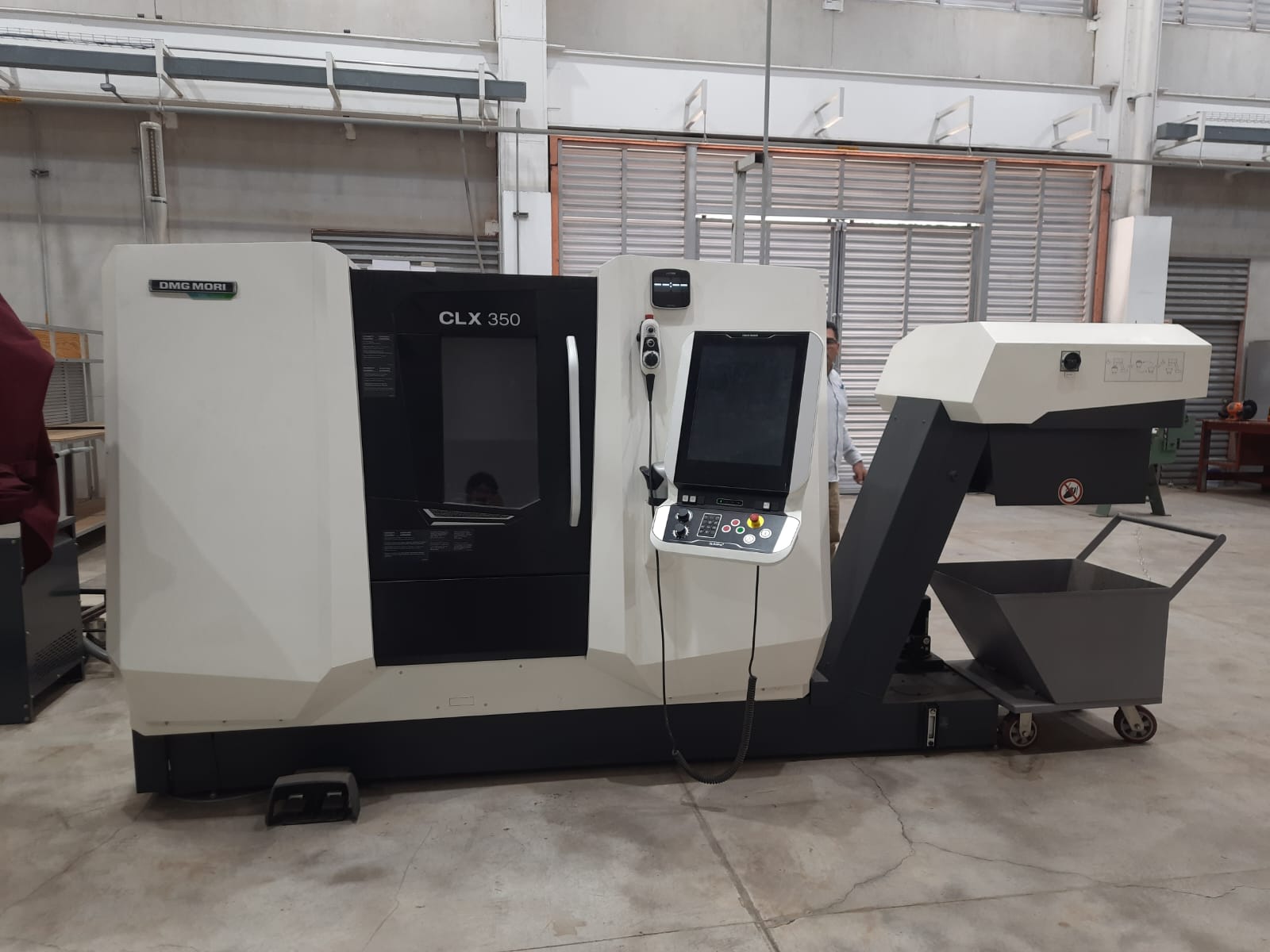
HOW CAN YOU PROGRAM IT?
Most common practice is to program with G-codes and M-codes. They sound different but they are not separate languages; they are different commands within the same CNC language. G-code focuses on movement, while M-code handles various machine functions.
1. The old school mechanics know them by heart and move the tools in the desired position using an incremental or global coordinates. They created long lists of directives and errors were very common.
2. The new generation of mechanics uses CAM software (like MasterCam) to turn a 3D model into a list of G and M codes. Errors still exist but the relate to improper axis origin settings.
3. 3. The last option is only offered by state of the art CNC machines like the DMG-Mori which is the one that I’ll choose: Descriptive coding using graphics for basic operations.
WHAT ARE THE PARTS OF A CNC LATHE?
Headstock (holds the material to always be centric). Lathe bed (where everything is resting without movement). Chuck (Clamps the material in the center of rotation). Quill/Tool center (All the tools are located here). Control Panel (Emergency/Start/Movement buttons and control keys are placed here)
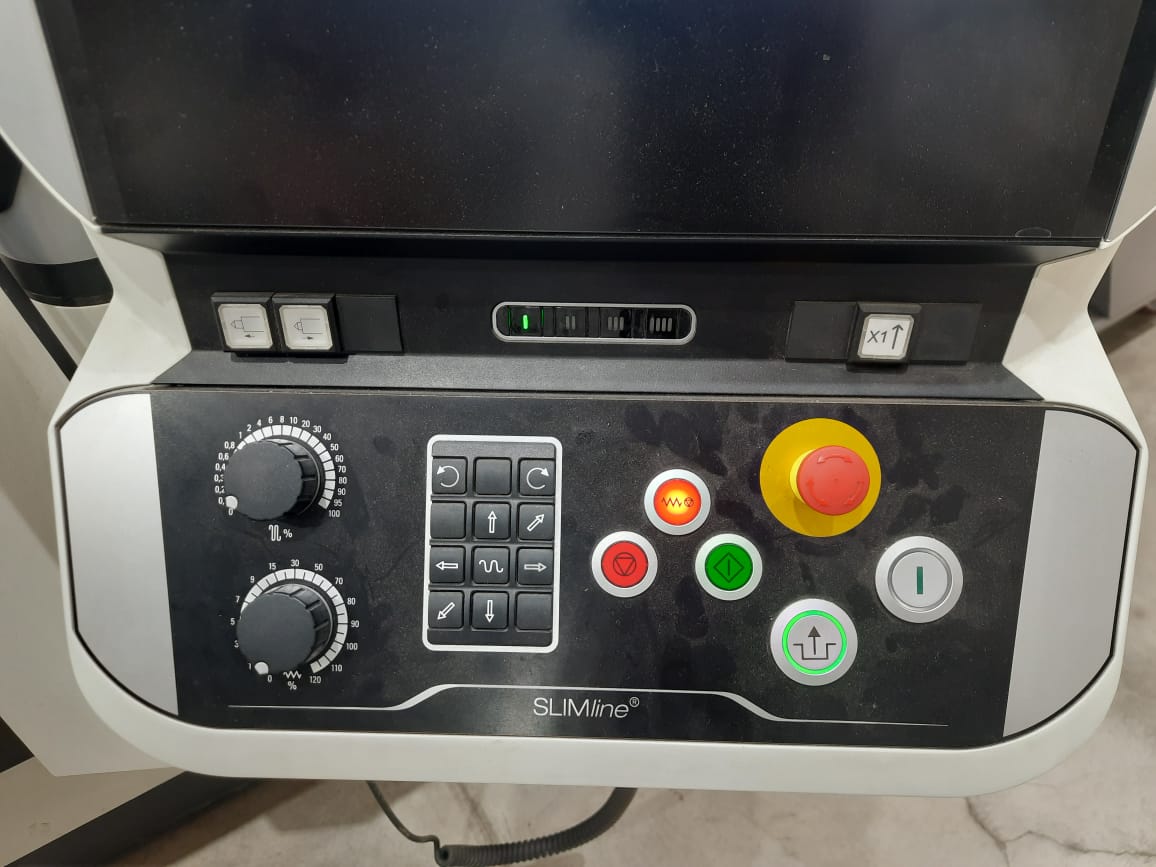
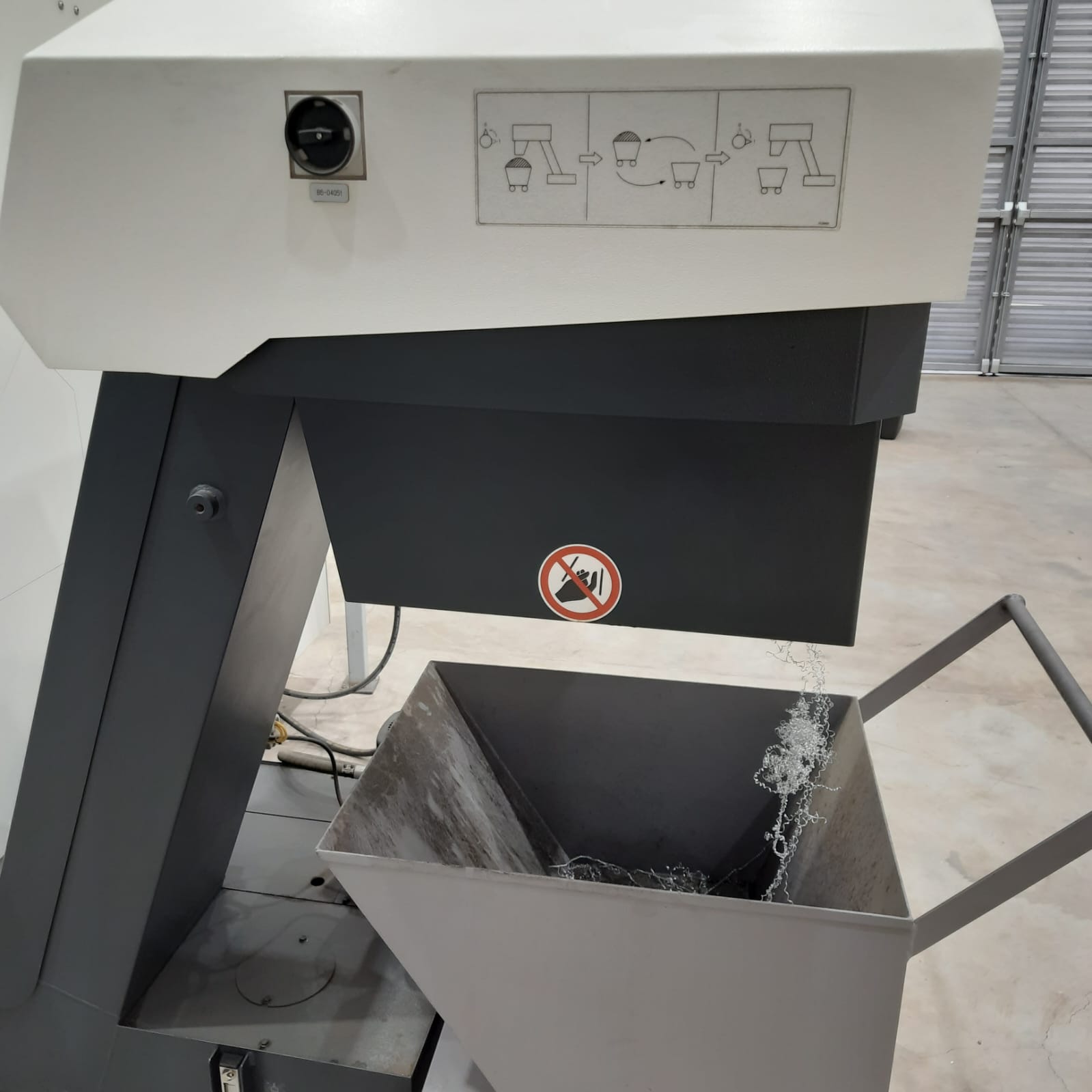
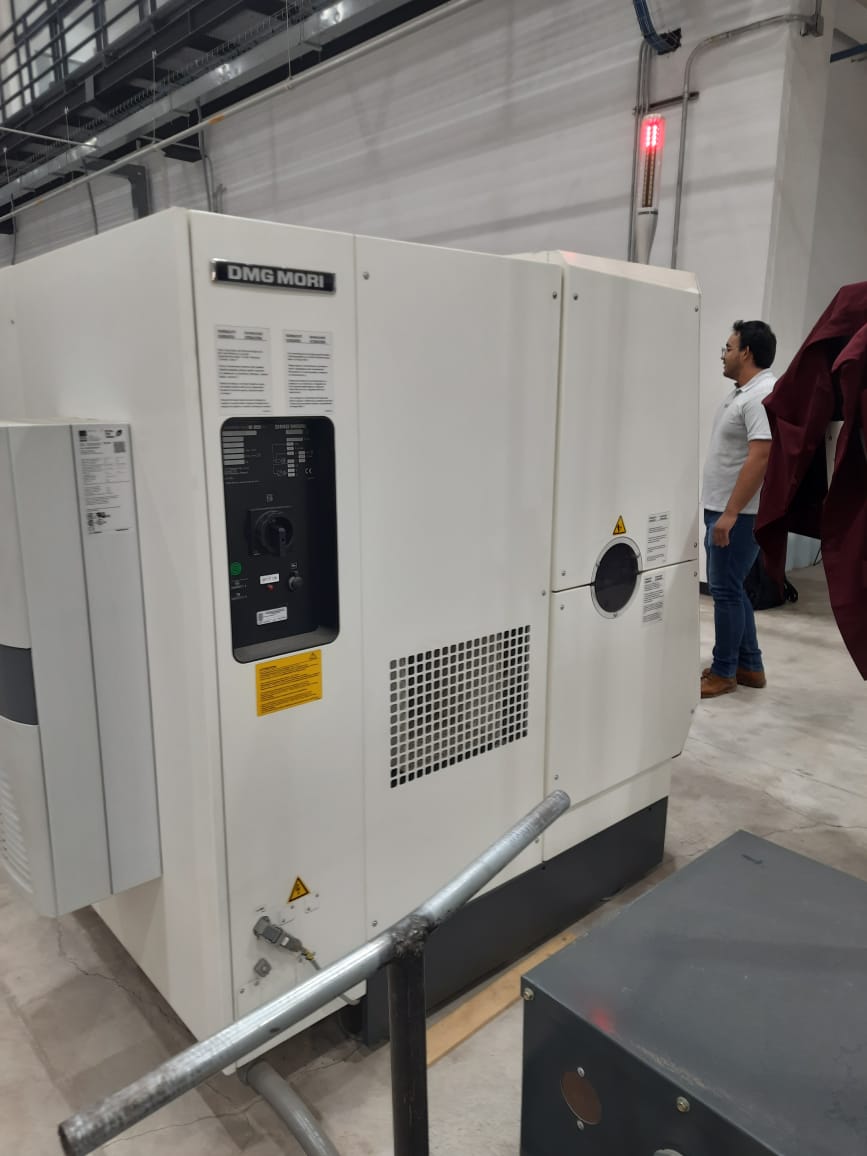
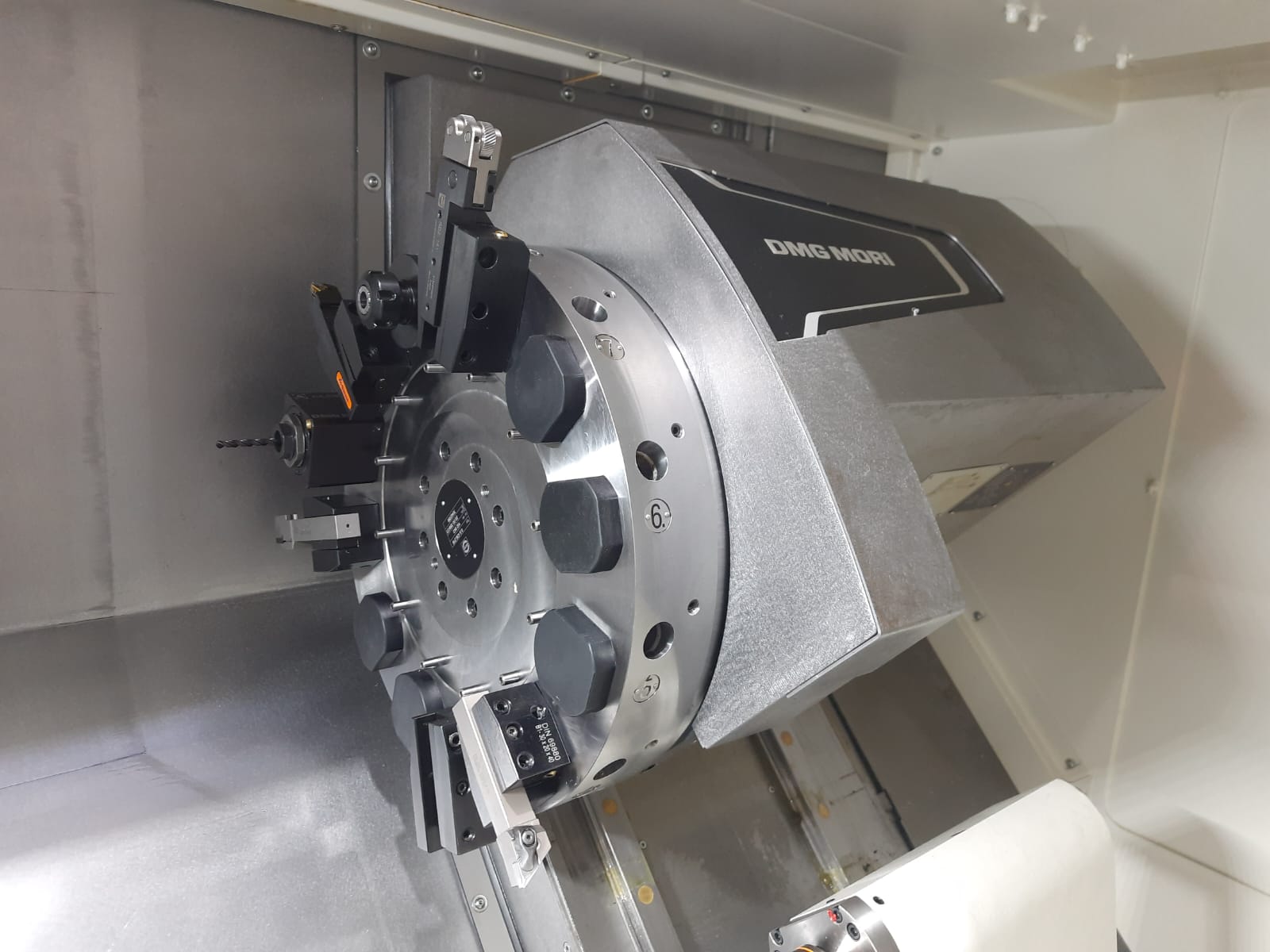
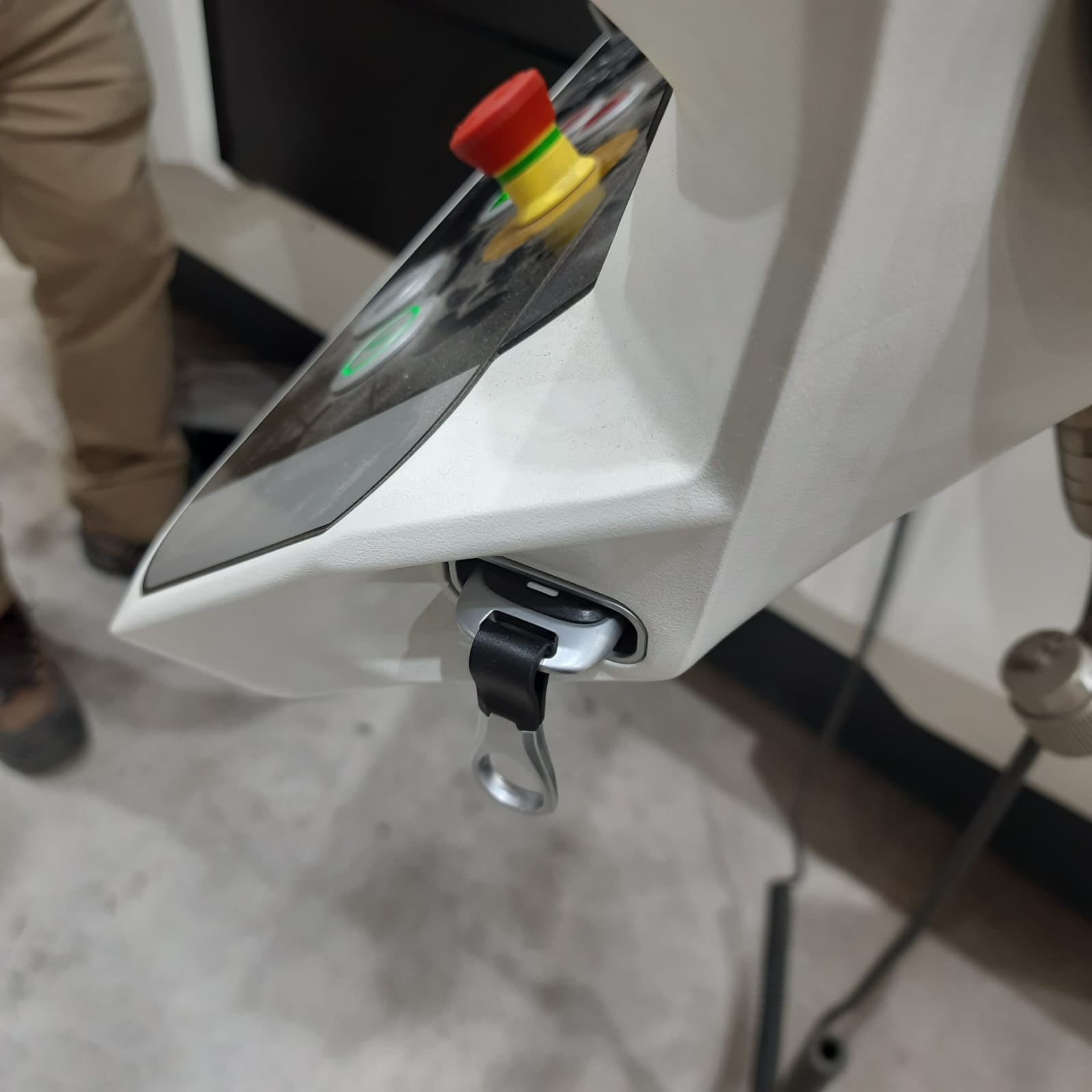
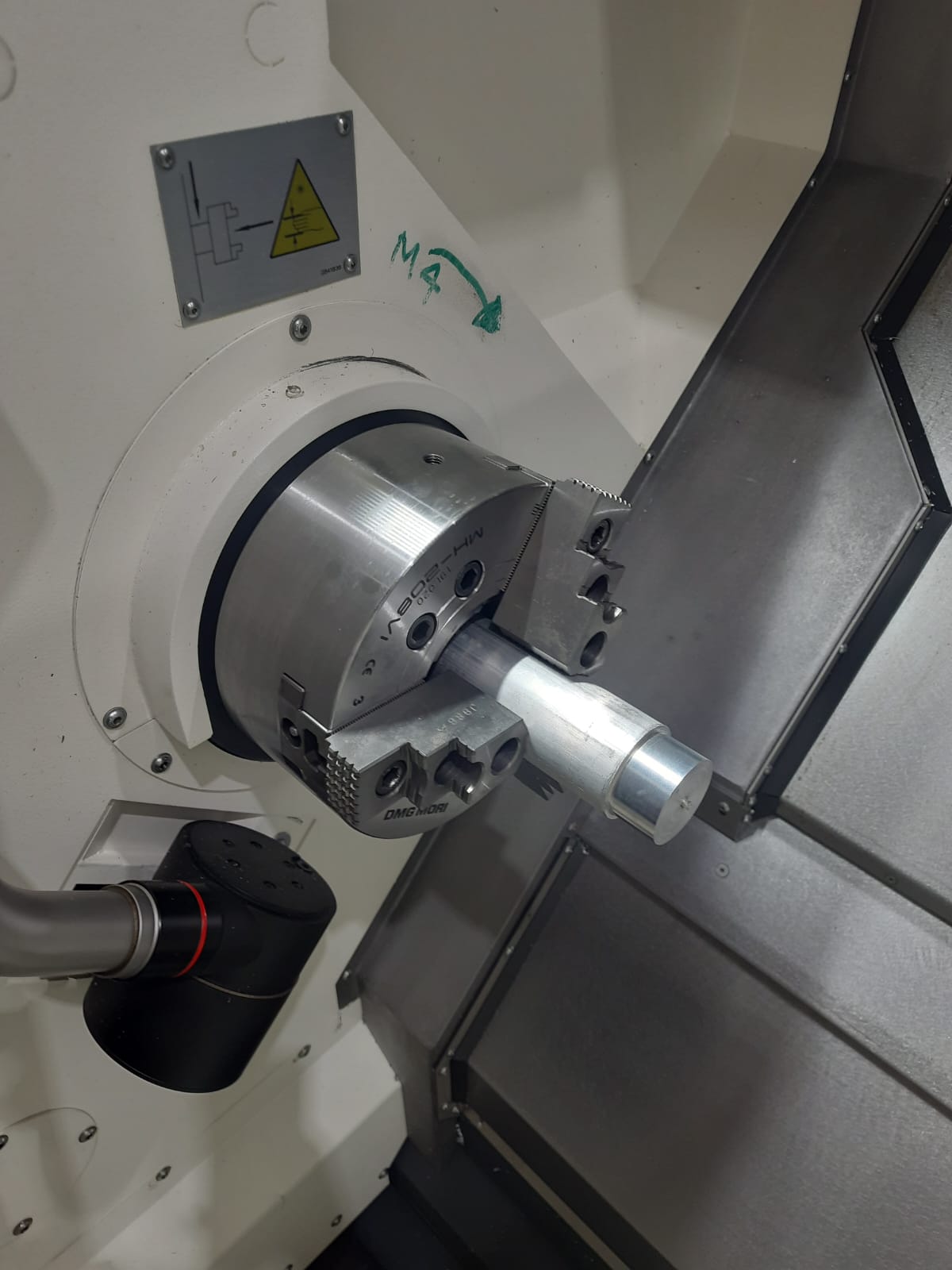
WHAT DOES THE PROCESS INVOLVES?
Material setup: The length and the diameter of the material must be measured and declared in the software. It also should be clamped in place by stepping on the respective pedal. This system uses a hydraulic chuck.
Tools setup: The tool center must contain all the tools needed to give the shape we want. Each tool belongs to a specific type of operation. We must ensure they are aligned and 100% functional.
Set origins: We must declare the origin only for Z, since X and Y are fixed values placed in the plane of the revolution part.
Check coolant: Since we are using angular speeds above 3000 RPM and we are working with metal, heat is going to build up. To increase the use-time of the tools, the coolant is highly recommended.
Coding: Before typing or clicking directives, we must know the shape and dimensions of our final product. A sketch was developed to define 3 types of operations, define dimensions, and have in mind where the tools are going to be during the whole process. Since this type of programming is mostly graphic, there is no code for me to share.
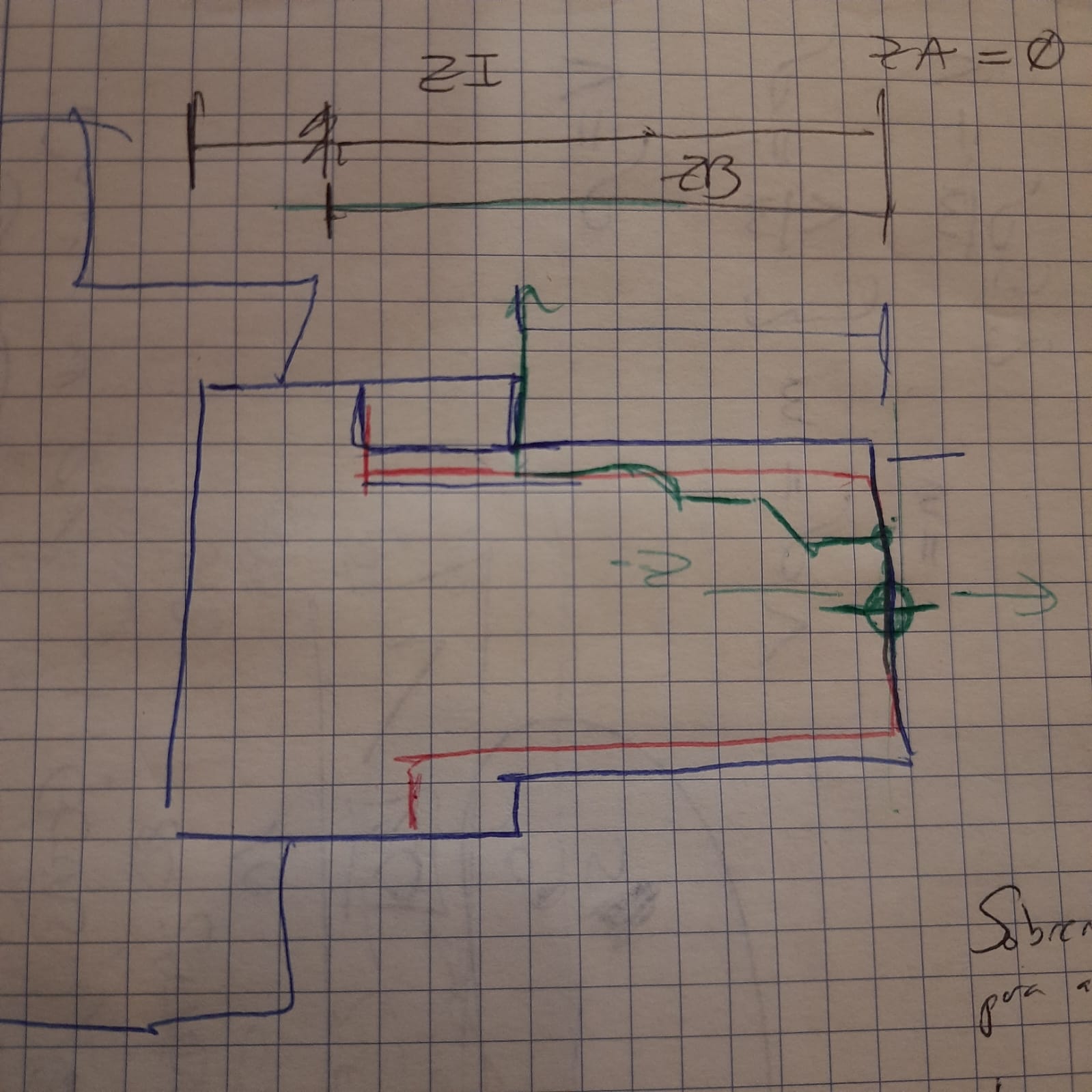
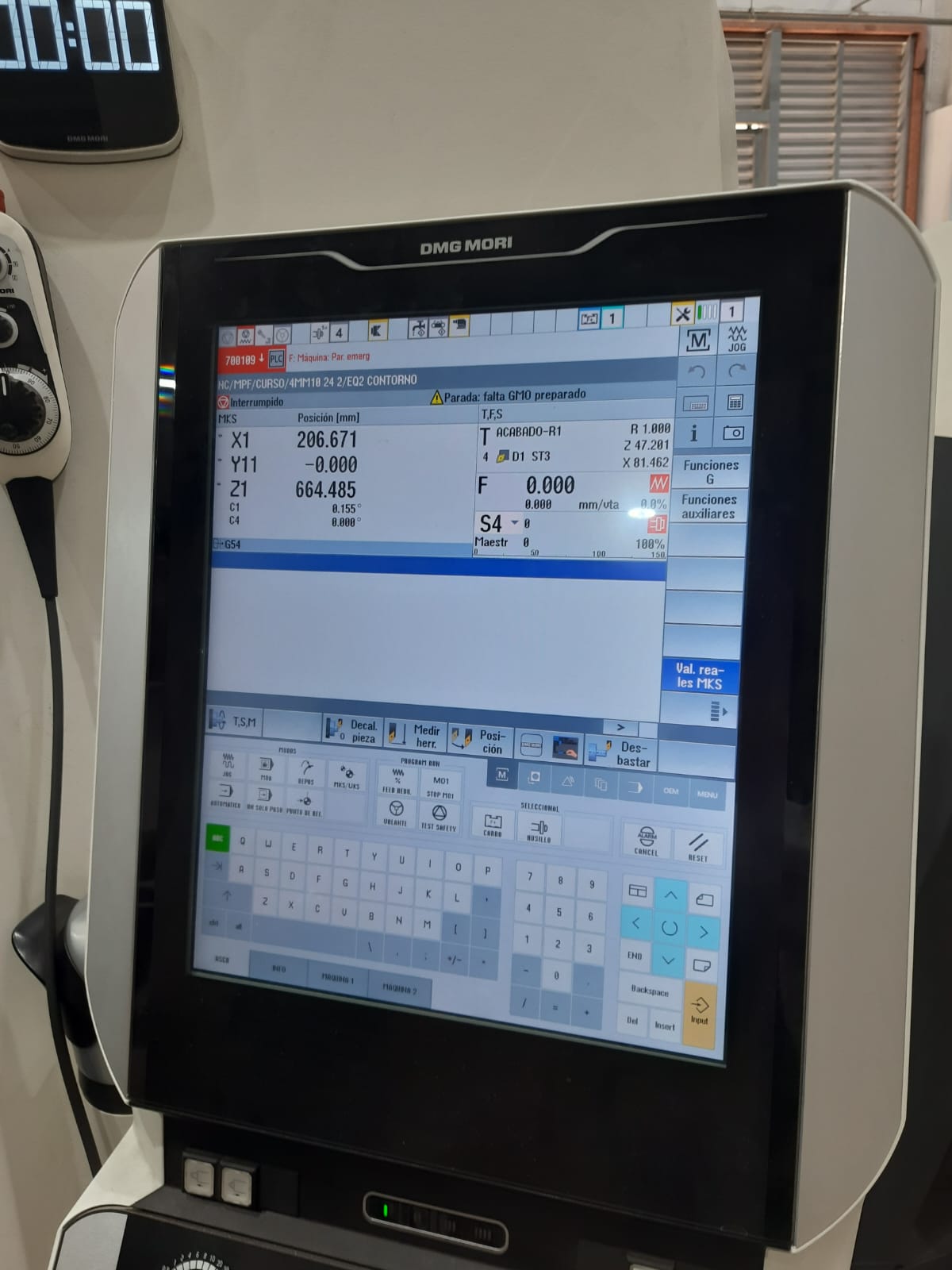
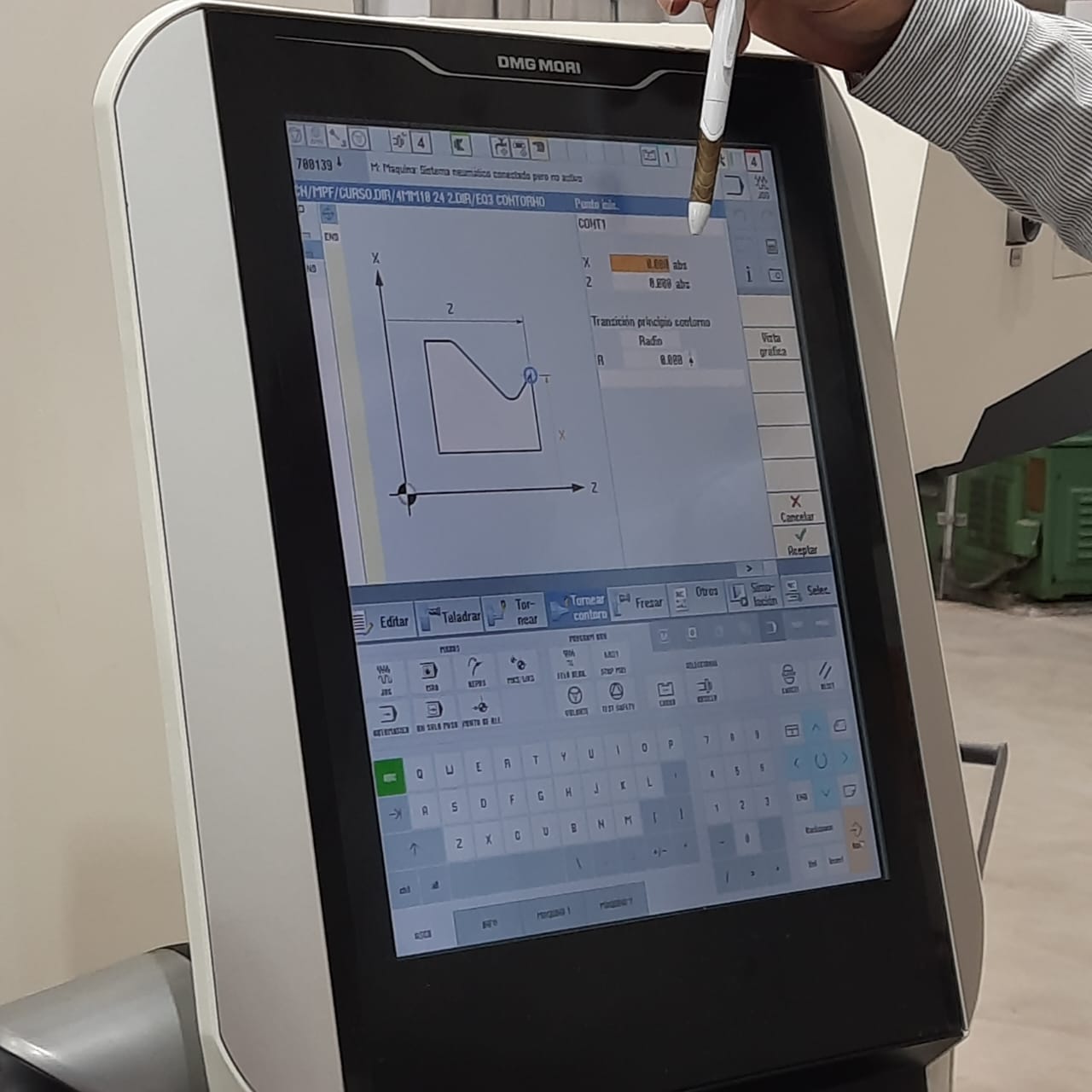
Simulation: The graphic tools update after any input from the operator. One must ensure that the proper tool is being used, and it is mandatory to avoid crashing the tool against the rotating chuck to take care of the equipment.
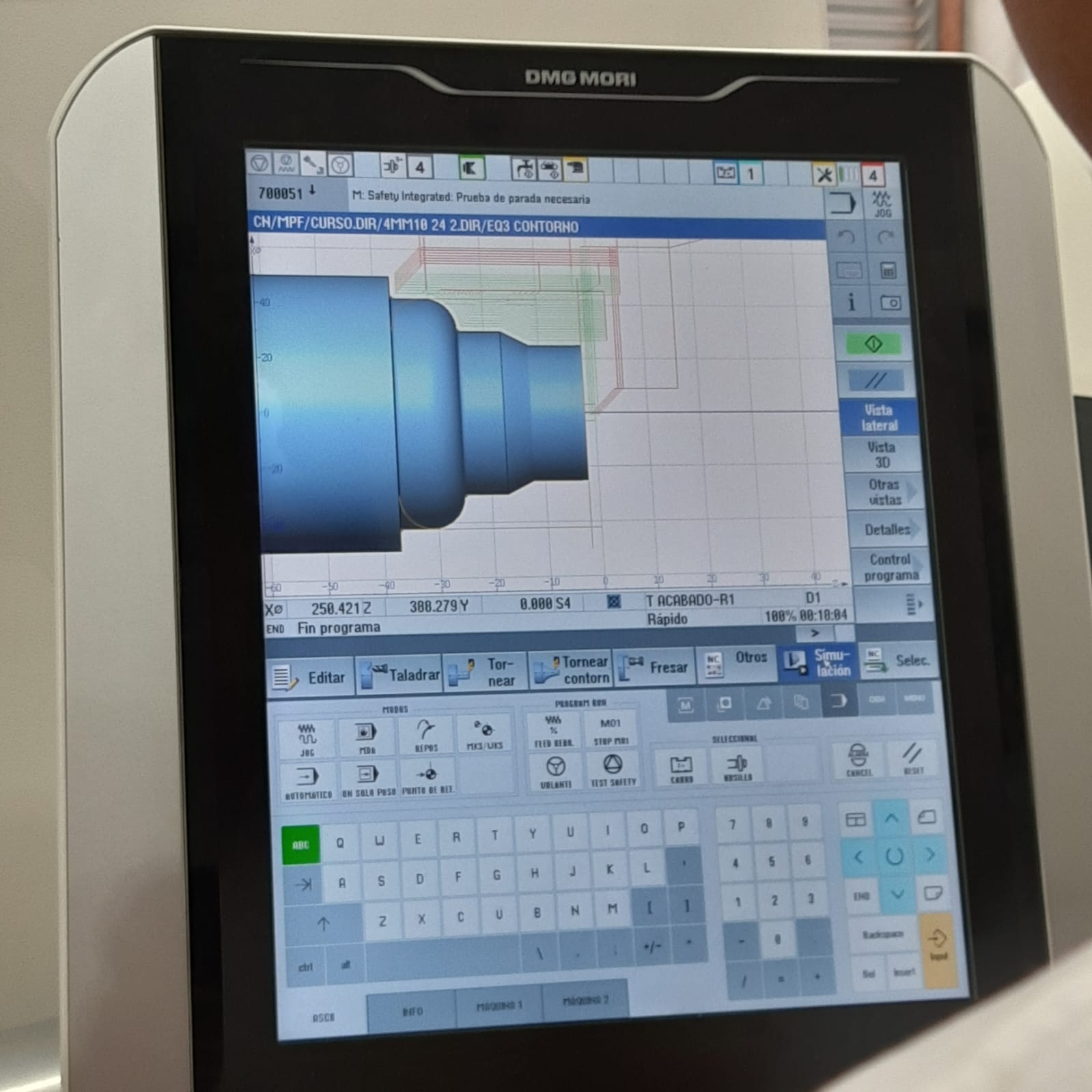
Execution: Once the simulation is complete and respects the constraints, we must press the run button and the operation will begin. Of course, there is no way this can start with an open door. Close the door.
Monitoring: If you hear strange noises, smell like burnt, or smoke starts appearing, hit the stop button. If things get critical, hit the emergency button.
Part removal: After 20 minutes the piece was ready, we wait 5 more minutes for it to cool down. Opening the door and releasing the piece from the chuck are the final steps.
Cleaning: There is an integrated conveyor that removes the metallic burr, but coolant as small particles are harder to clean. Spend as much as needed to keel the system clean end operational for years to come. HUELUM!
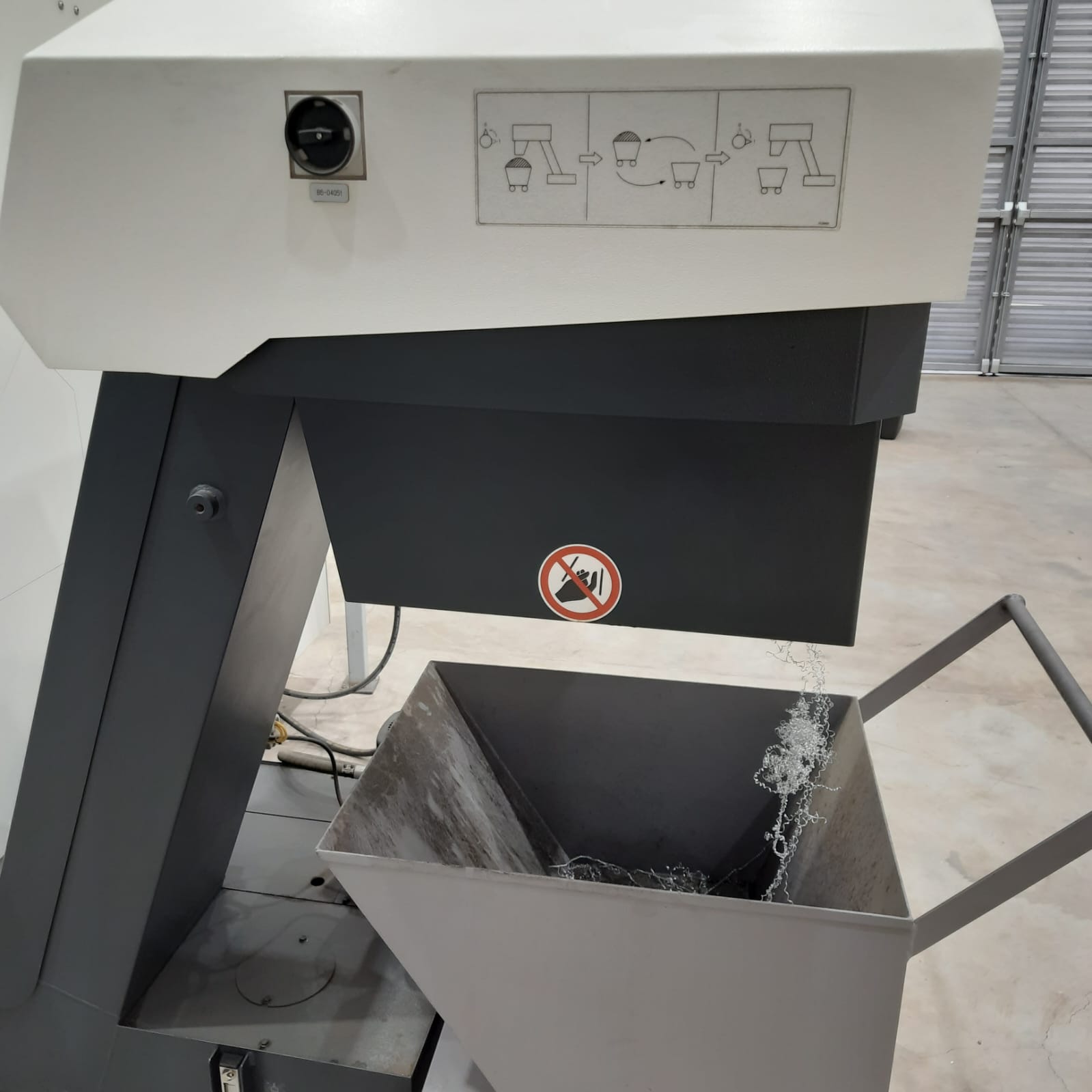
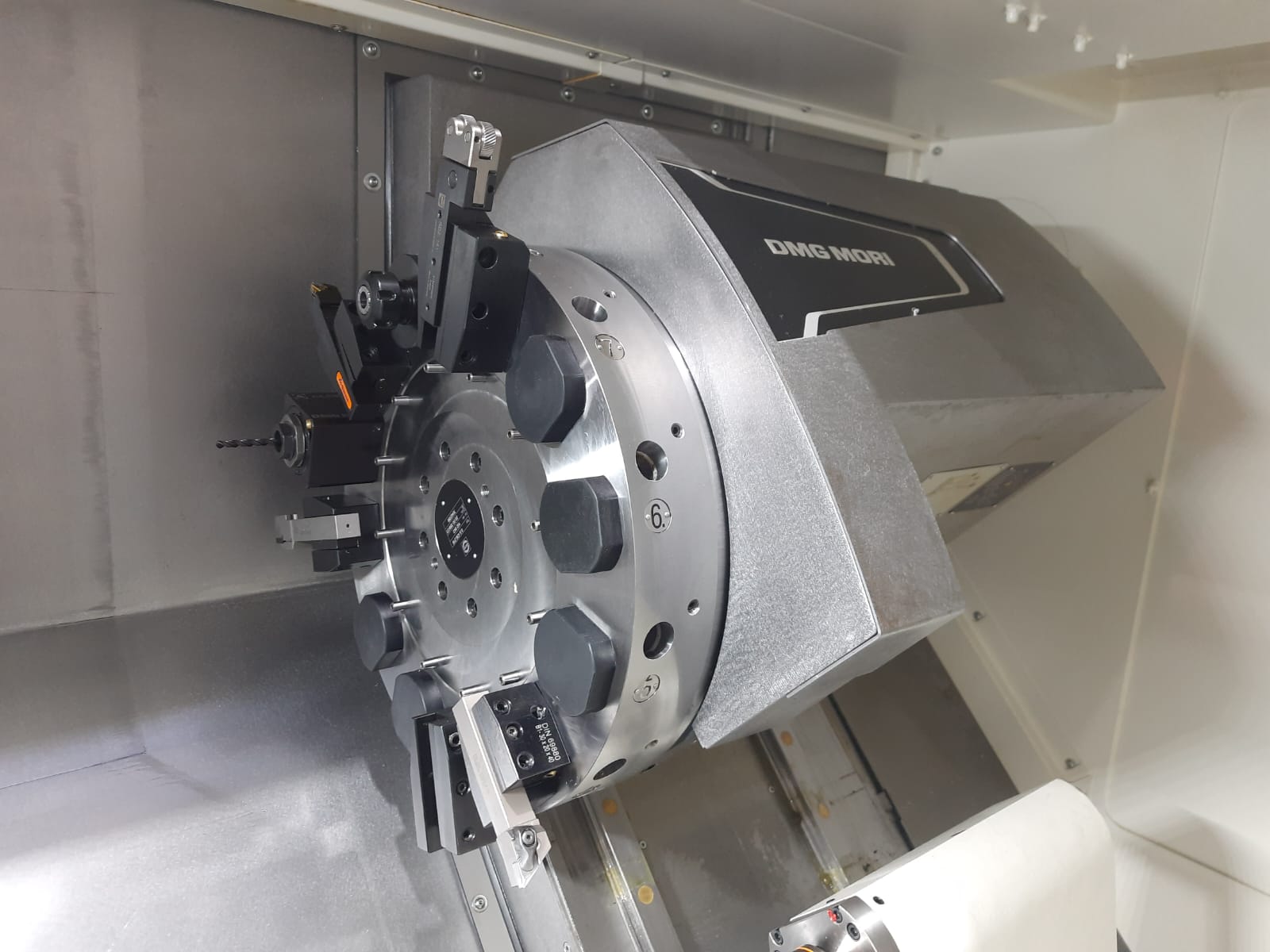
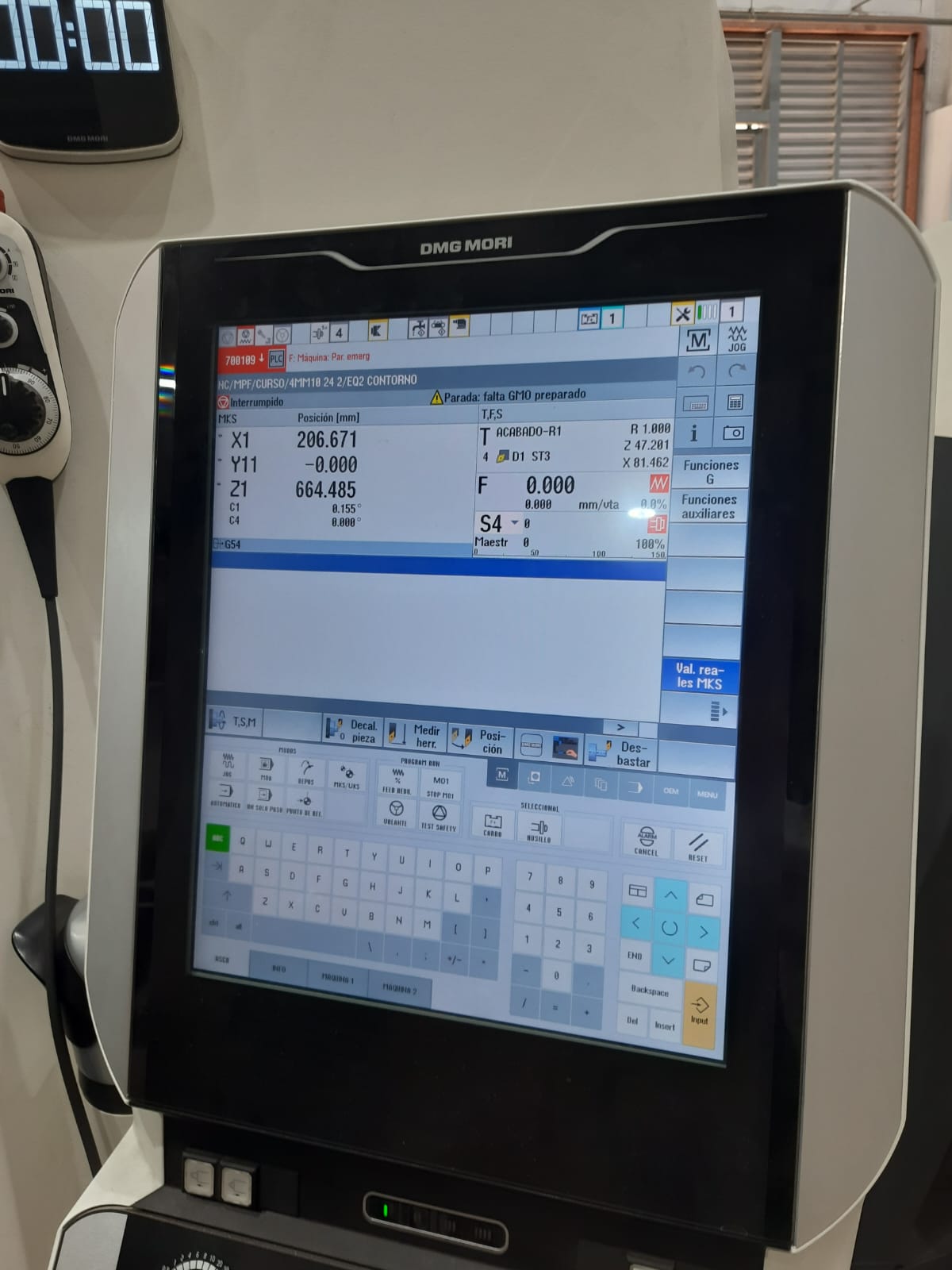
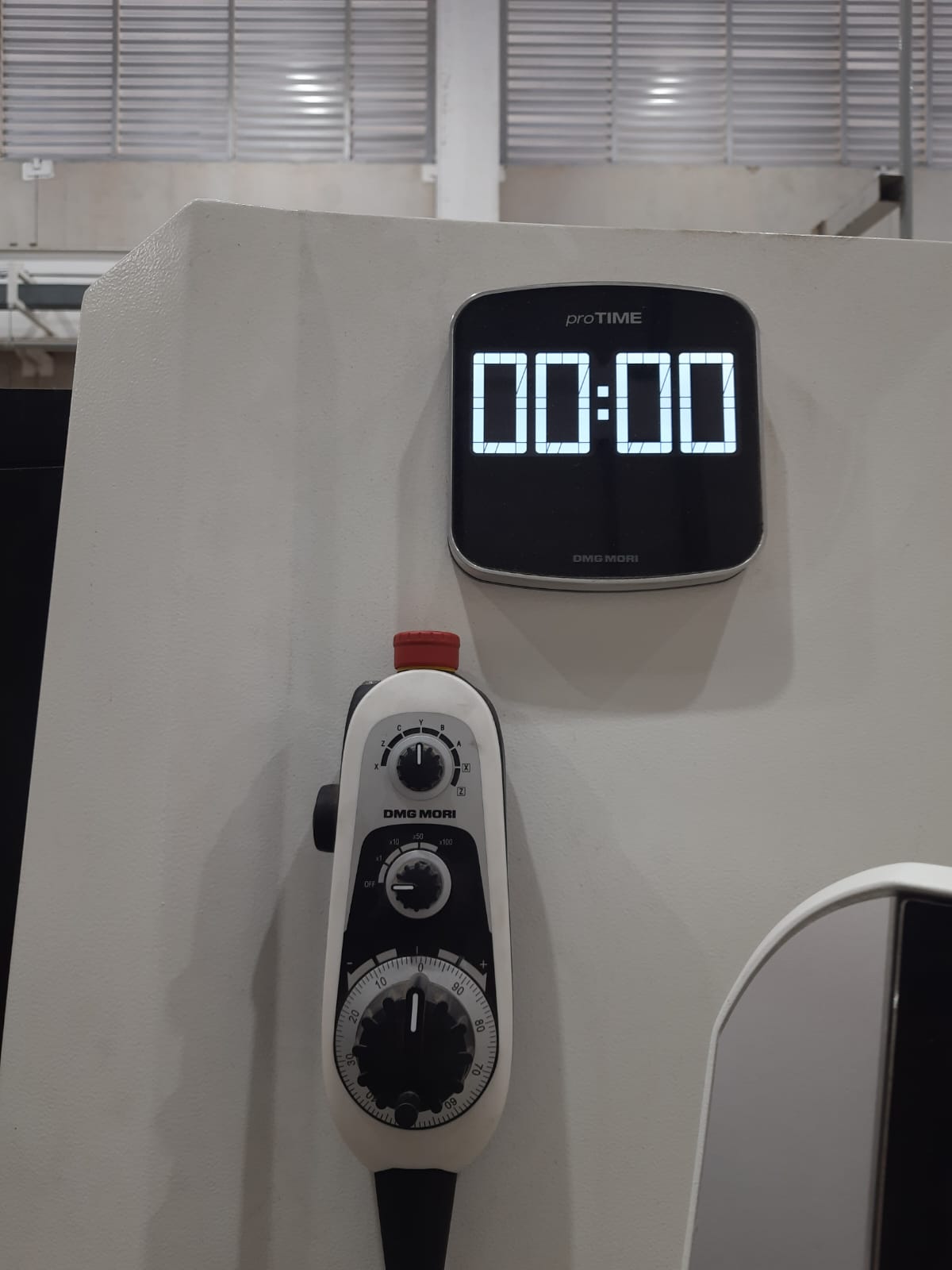
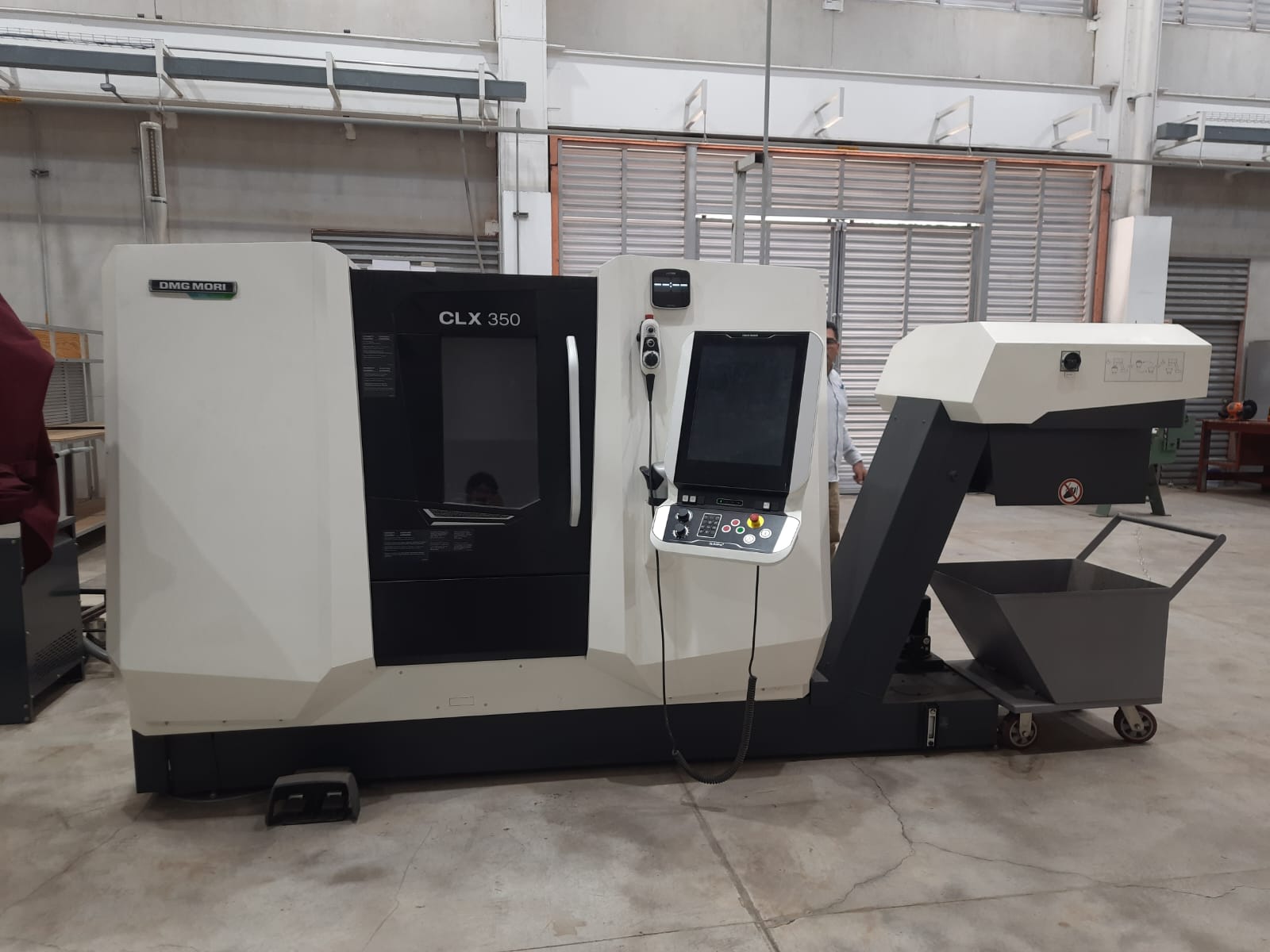
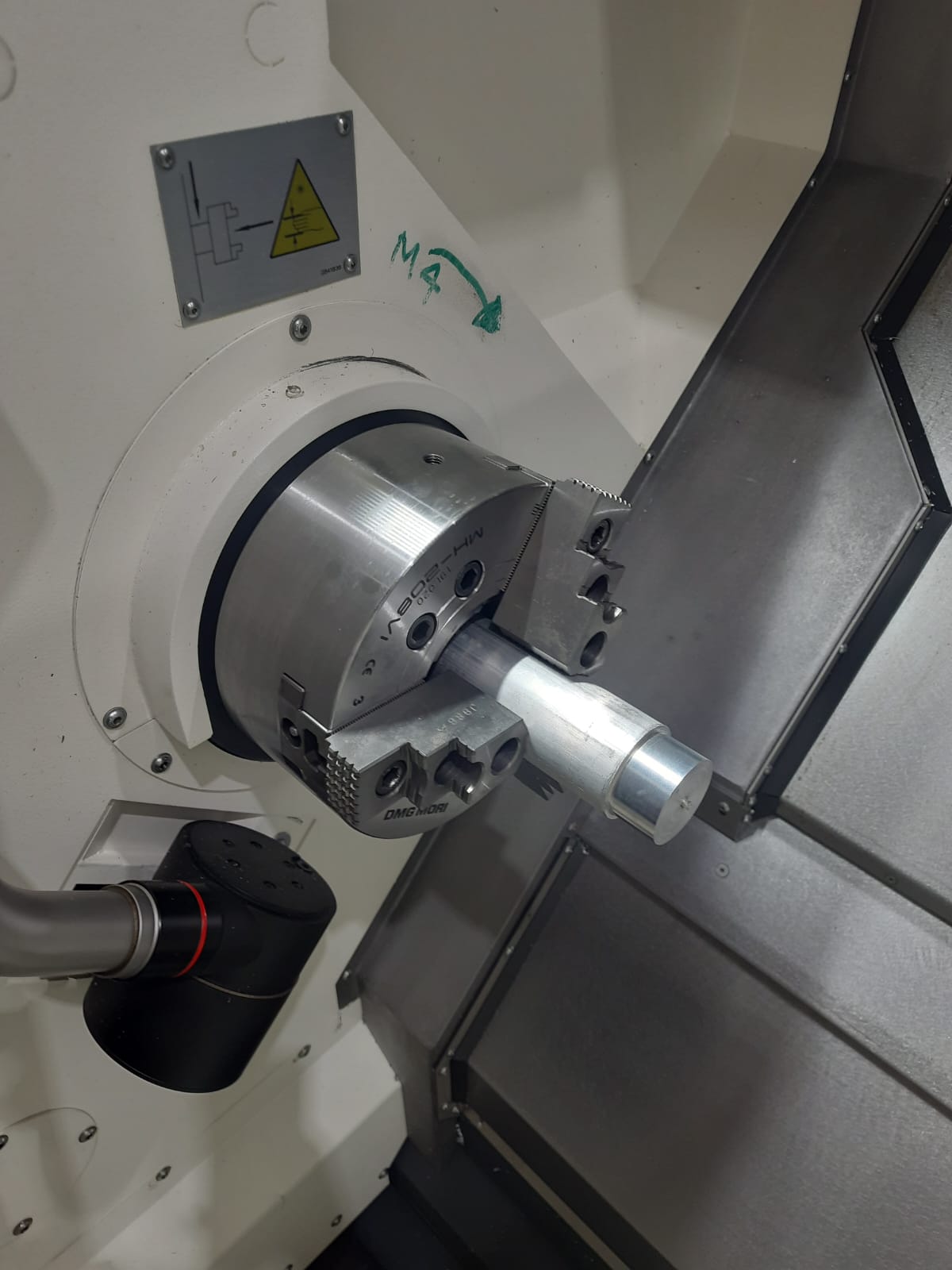