7. Computer-Controlled Machining
We are already in week 7, i have learnt many machines and electronics basics, today im learning the one CNC big projects, unlike laser cutting the big CNC that we are going to use work as a drill that allows you to work on the Z axis easily. Because of their complexity and size these machines require extreme safety and to always be on the lookout.
The task for this week in order to take advantage of this machinery is to make something big, the fablab will provide us a full size wood board (4x8 ft), obviously we need to learn how to operate the CNC, design the object having in mind the new rules and take a safety tour, as always the full documentation will be in the Group assignment.
Security training
The equipment needed to be around and work with industrial kind of machines consist of: bat, boots, lenses and earrings, there isn't need of helmet for the instalations here in puebla, also we received orders for safety use of the machine, to avoid tragedies.
During the journey we where shown the location of fire alarms, medic emergency buttons and the different extinguisher, as well as instructions on how to react in case of emergency and the names of the security team here at the IDIT.
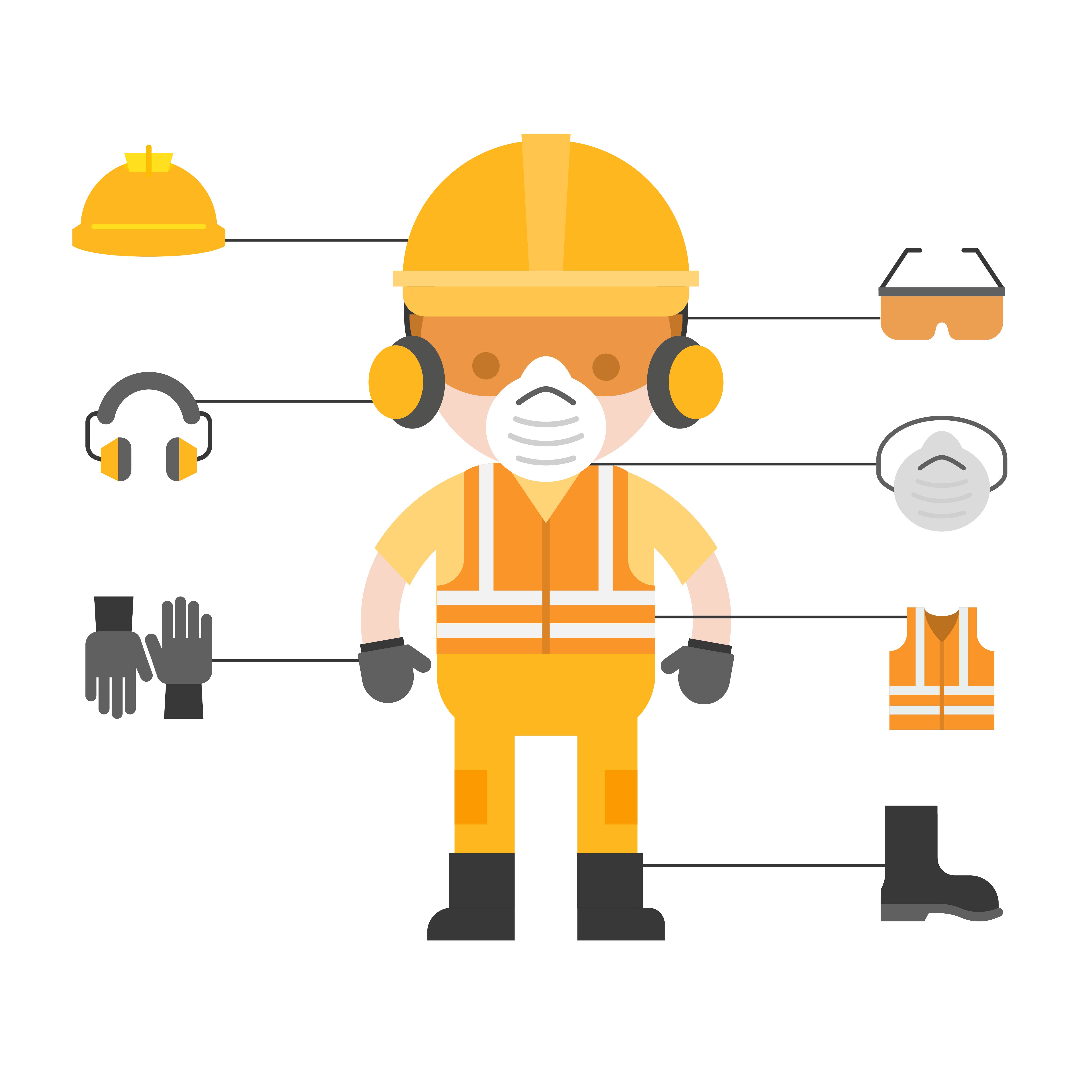
The machines
Match by Ibero
- Dimensions: 3x1.8x1.7mts
- Motor Power : 4 HP at 24000 rpm´s
- Power Supply: 220v/2F/3.5KW
- Material Fixtures: Nails
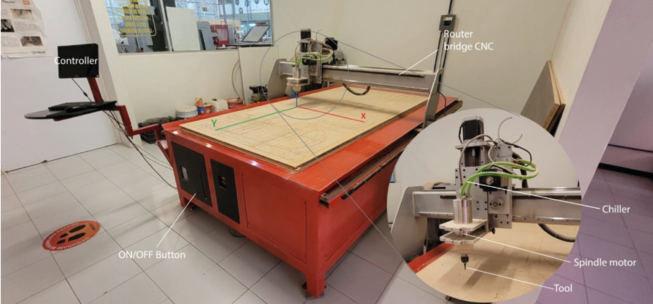
Asia Robotica shop-1325
- Dimensions: 3x1.8x1.7mts
- Motor Power : 4 HP at 24000 rpm´s
- Power Supply: 220v/2F/3.5KW
- Material Fixtures: Clamps
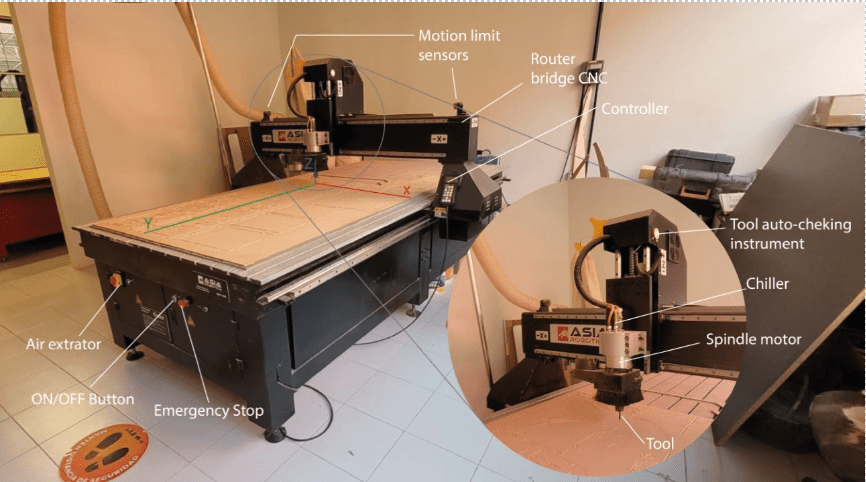
Material Machining Recommendations
Material | Description | Machining Recommendations |
---|---|---|
ABS | Durable, strong plastic used widely across industries. | Use sharp, single-flute tools for a smooth finish. |
Acrylic | Clear, plastic material with excellent clarity and weather resistance. | Use carbide tools and coolant to prevent melting or cracking. |
ALUCOBOND / DIBOND ® | A composite panel with two aluminum sheets bonded to a non-aluminum core. | Use sharp tools with high cutting speed for clean edges. |
Aluminum | Lightweight, corrosion-resistant metal used in various applications. | Use sharp, multi-flute cutters and a coolant to prevent buildup. |
Copper | Highly conductive metal used in electrical components. | Use sharp, single or double-flute cutters for clean cuts. |
Estirene | A brittle, transparent plastic used in model making and prototypes. | Ensure proper clamping and use sharp tools to avoid chipping. |
Tin | Soft, malleable metal often used as a coating for other metals. | Use lower feed rates to prevent galling on the cutter. |
Solid Wood | Natural wood, used for its aesthetic and structural properties. | Use sharp, two-flute spiral bits for efficient material removal. |
Softwoods | Lighter, less dense wood types like pine or cedar. | Use upcut spirals for chip removal and to prevent fraying. |
Hardwoods | Denser woods like oak or maple, known for durability. | Use downcut spirals for a smoother surface finish. |
Plywood | Engineered wood made from thin layers of wood veneer. | Use compression cutters to prevent delamination. |
MDF | Engineered wood product made by breaking down hardwood or softwood residuals. | Use high-speed steel (HSS) or carbide bits to reduce dust. |
Veneered MDF | MDF covered with a thin layer of real wood veneer. | Use downcut spirals for a clean cut that won't tear the veneer. |
MDF Laminate | MDF with a plastic laminate coating on one or both sides. | Use carbide-tipped bits for smooth cuts through the laminate layer. |
Melamine over agglomerate | A composite material of wood chips bonded together, covered with a melamine layer. | Use a triple-chip grind (TCG) blade for clean cuts without chipping. |
Nylon | Durable, synthetic polymer with high strength and flexibility. | Use single or double flute end mills at high speeds to prevent melting. |
OSB | Oriented strand board, a type of engineered wood similar to particle board. | Use carbide-tipped blades for durability and to avoid wear. |
Non-ferrous metals | Metals that do not contain iron in appreciable amounts, like aluminum and brass. | Use lubrication and specific non-ferrous geometry cutters. |
Solid polycarbonate | Durable, transparent plastic with high impact resistance. | Use sharp tools and coolants to prevent overheating and melting. |
Polyethylene | Flexible, durable plastic used in a wide range of products. | Use sharp, single-flute end mills for clean cuts. |
PVC (solid/foamed) | Durable plastic used in construction and piping. | Use a low flute count bit and cooling techniques to prevent melting. |
Bakelite | An early plastic made from phenol and formaldehyde, known for its heat resistance. | Use carbide tools at moderate speeds to avoid chipping. |
Resins | Synthetic or natural compounds often used in composites and coatings. | Use sharp, high-speed tools for a smooth finish. |
Creating the Set
For this week big construction set i wanted to build two in wall cat House to then joint them with some kind of fabric kind material, for the design, i've used different joints to provide good resistance against gravity and my cats weight to be sure it worked i used the solidworks simulation side.
It's important to notice the dog bones in each corner, also for the wall pieces is needed a boxed operation for the joints.
Files links:
You can get all the documents needed just downloading this zip House cat.zip.
Creating the Gcode
Using the software provided by the university, and just found in select computers i imported the .sldprt as .dxf to make the array and indicate the inside, ofside and box cuts, once we have created all the traces we need to postprocess the data to the specific type for the machine to operate.
Controlling the router
As in every CNC we need to set the origin point with the controller once we set the material, then use an USB to get the document into the machine in this case we are required to stay next in order to constantly vacuum.
Building the house
With the pieces ready the only thing left to do is the assembly giving the pieces a little treatment with the help of a lime and joining them with the force of a hammer.
Days later!
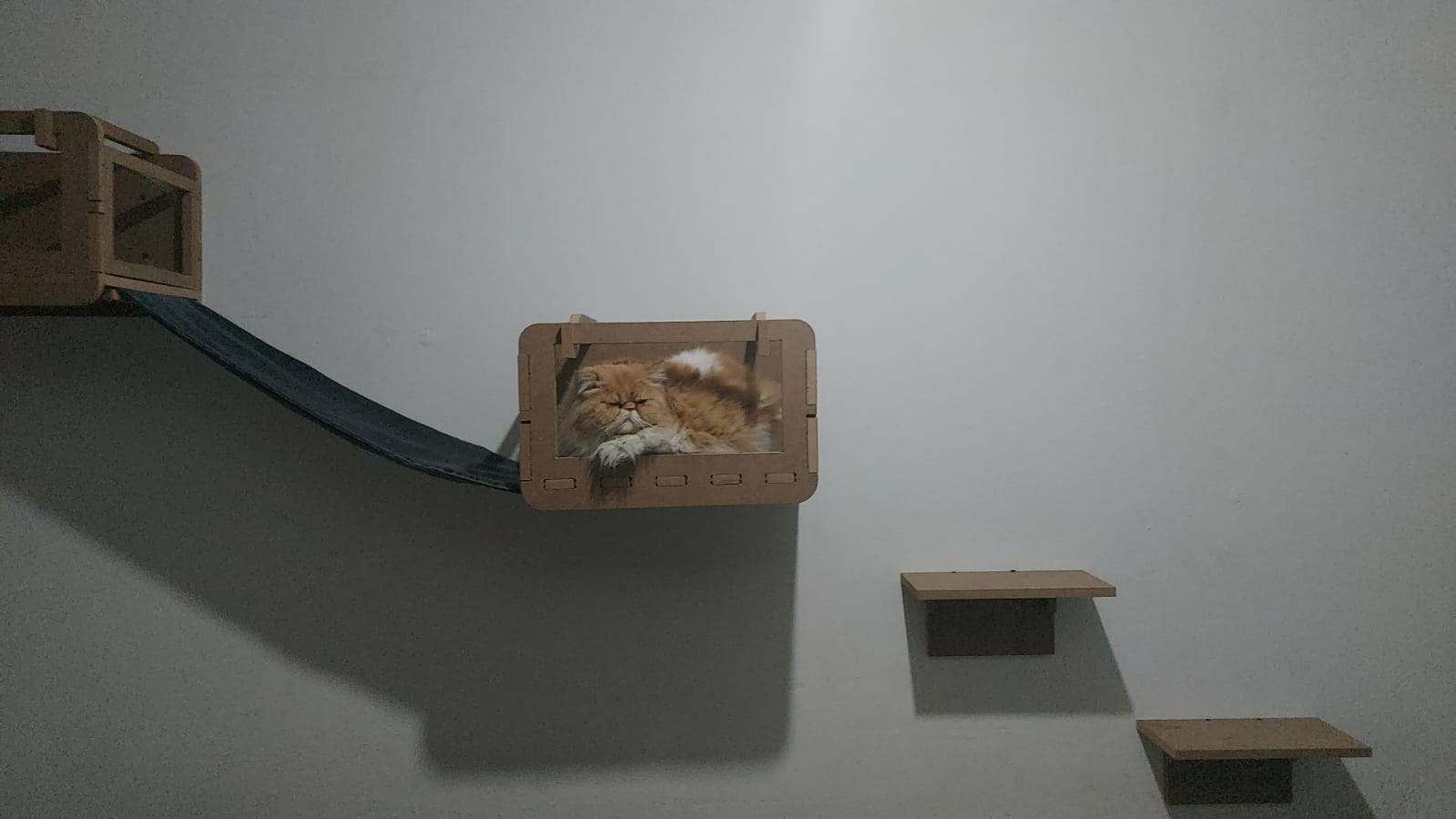
Final reflection
During the design it didn't occur to me to leave any assembly margin between the pieces, when I started to assemble it's true that it did require applying force but it resulted in a very robust structure, the way I modeled the house was not so optimal, it took me most of the time of the week, so in future tasks it is better to use the technique of designing the complete structure and then trying to modify it to get the faces but all in the same document, during my research looking for types of press fit joints I made dovetails but we didn't find the V tool in time, but they are certainly better looking and more effective.