Week 10: Machine Week
Here is the group assignment link for this week!
This week the Fab Lab cohort sectioned off into different groups to design different machines. I was part of the group that worked on an automatic tuning stringed instrument. My main focus was the gearbox and relating the design of the gearbox to the resonant chamber that was being designed by another peer, Christine.
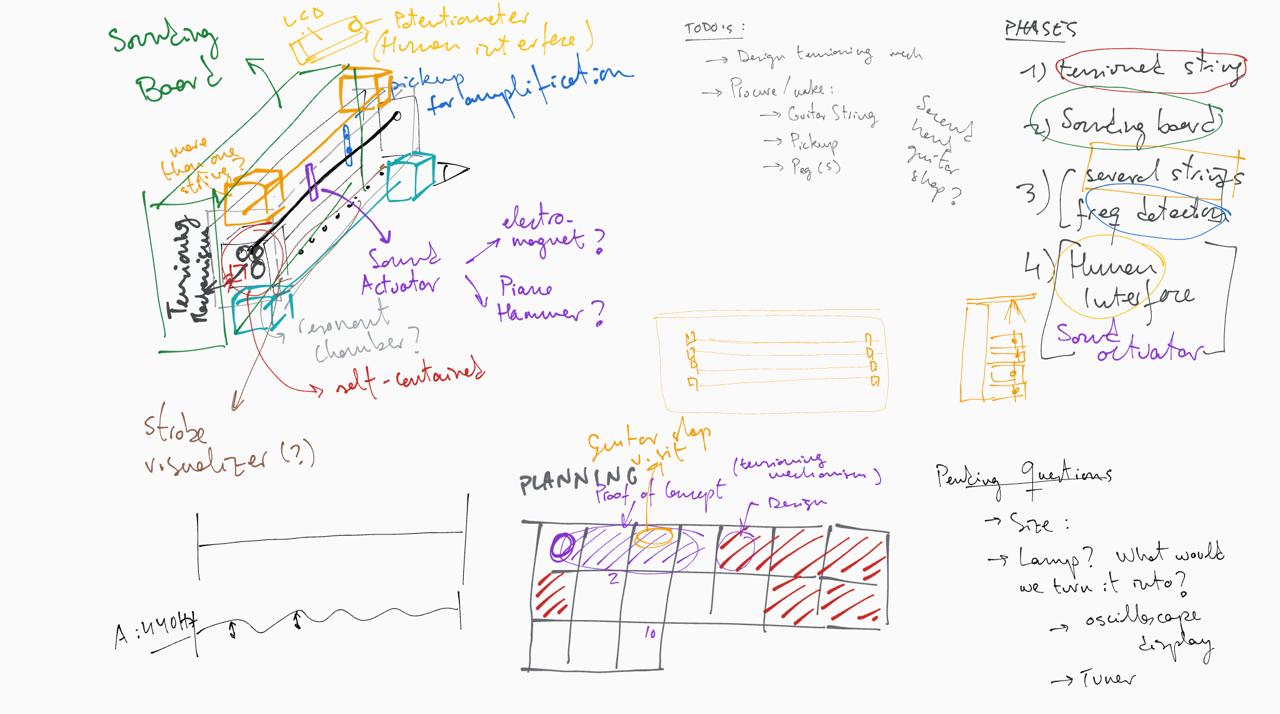
I worked off of Danni's prototype for the gearbox, which used a 9V DC Pololu motor. I worked to produce a tighter design and increase the torque of the stepper motor in order to tension a guitar string successfully. In the redesign, I worked with a 35mm stepper motor.
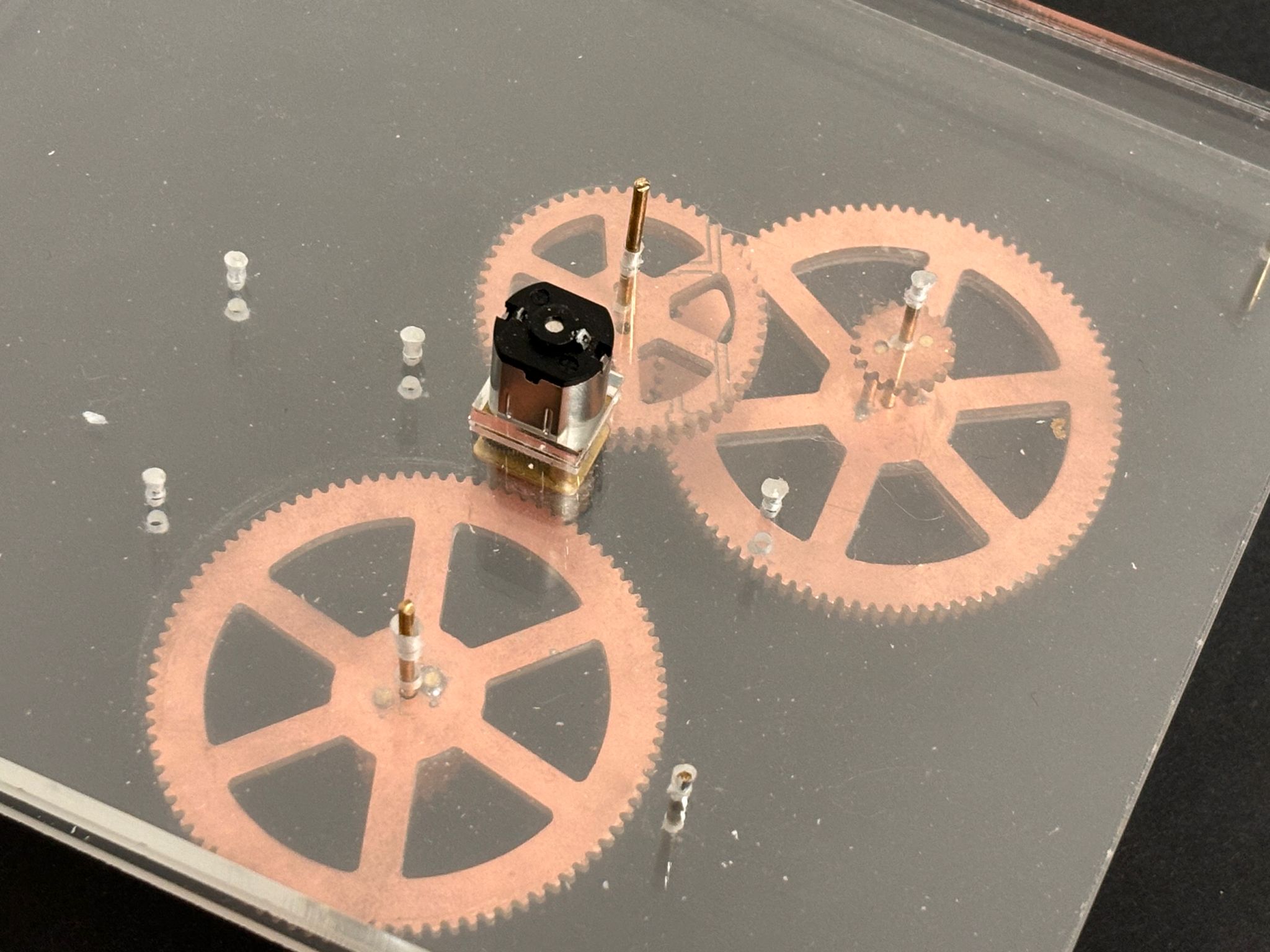
Because we set out to work with strings, I also took the opportunity to go to a guitar shop and get my hands on some components that would help with the sound and ease the design process.
Components:

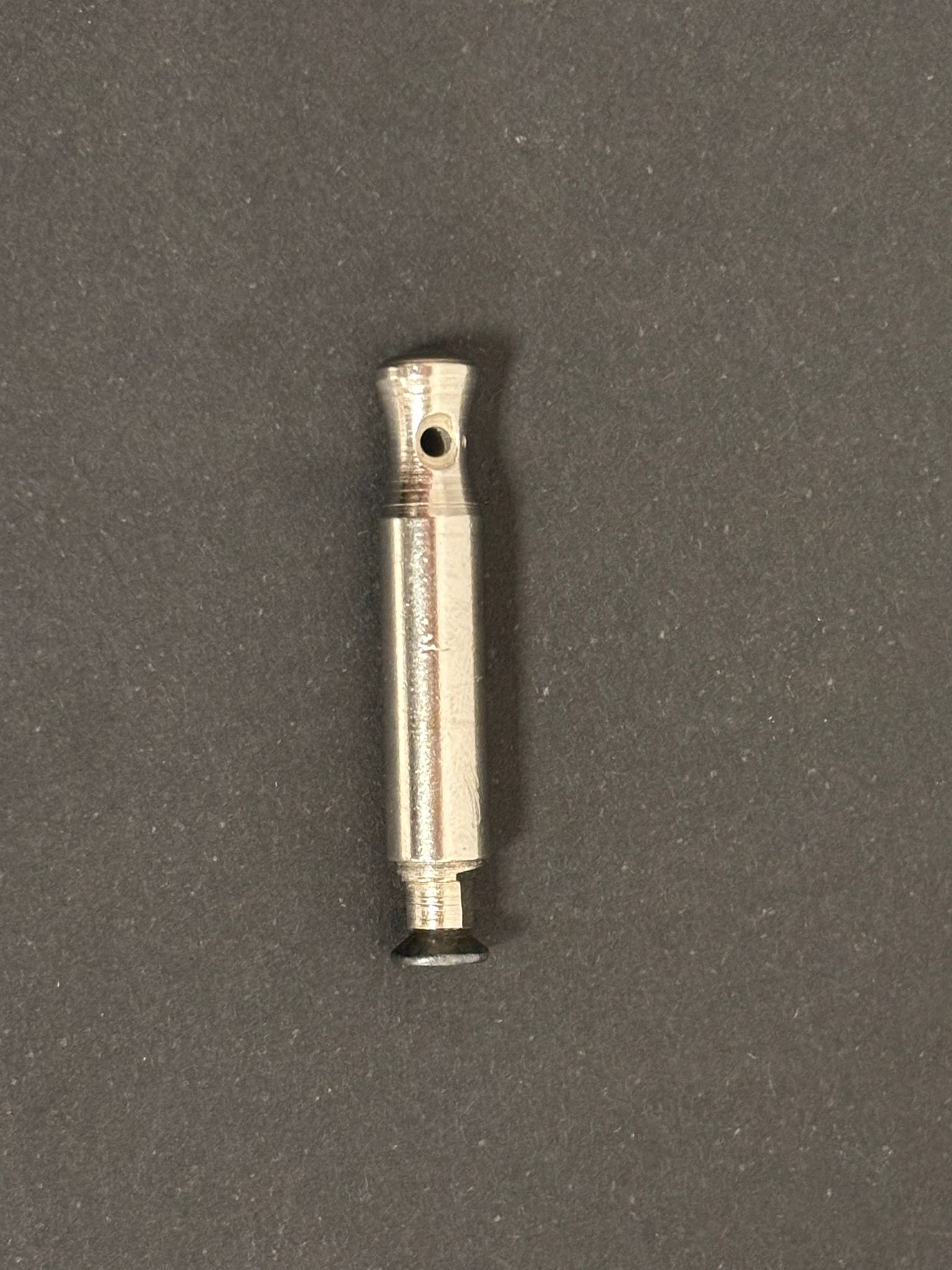
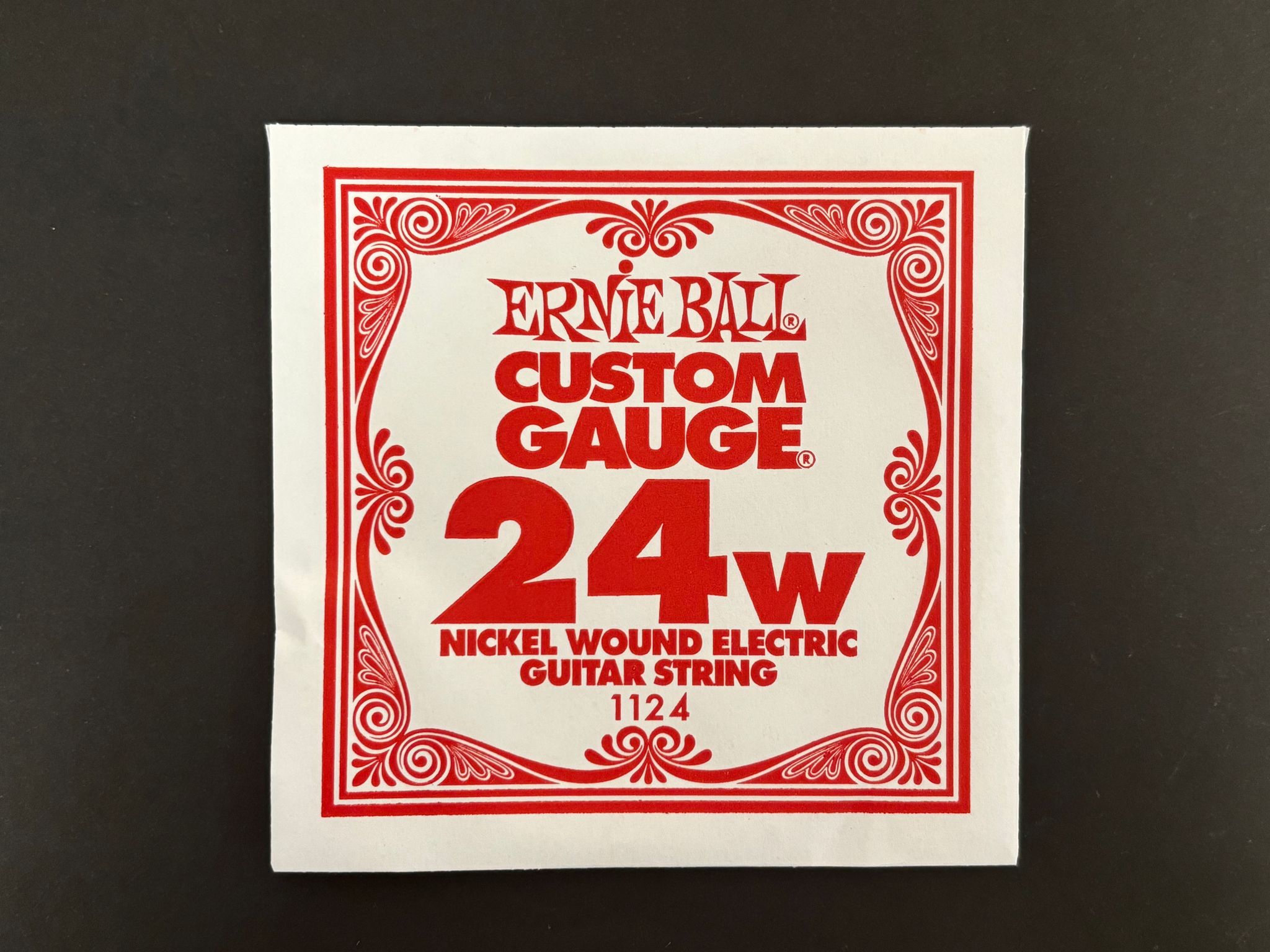
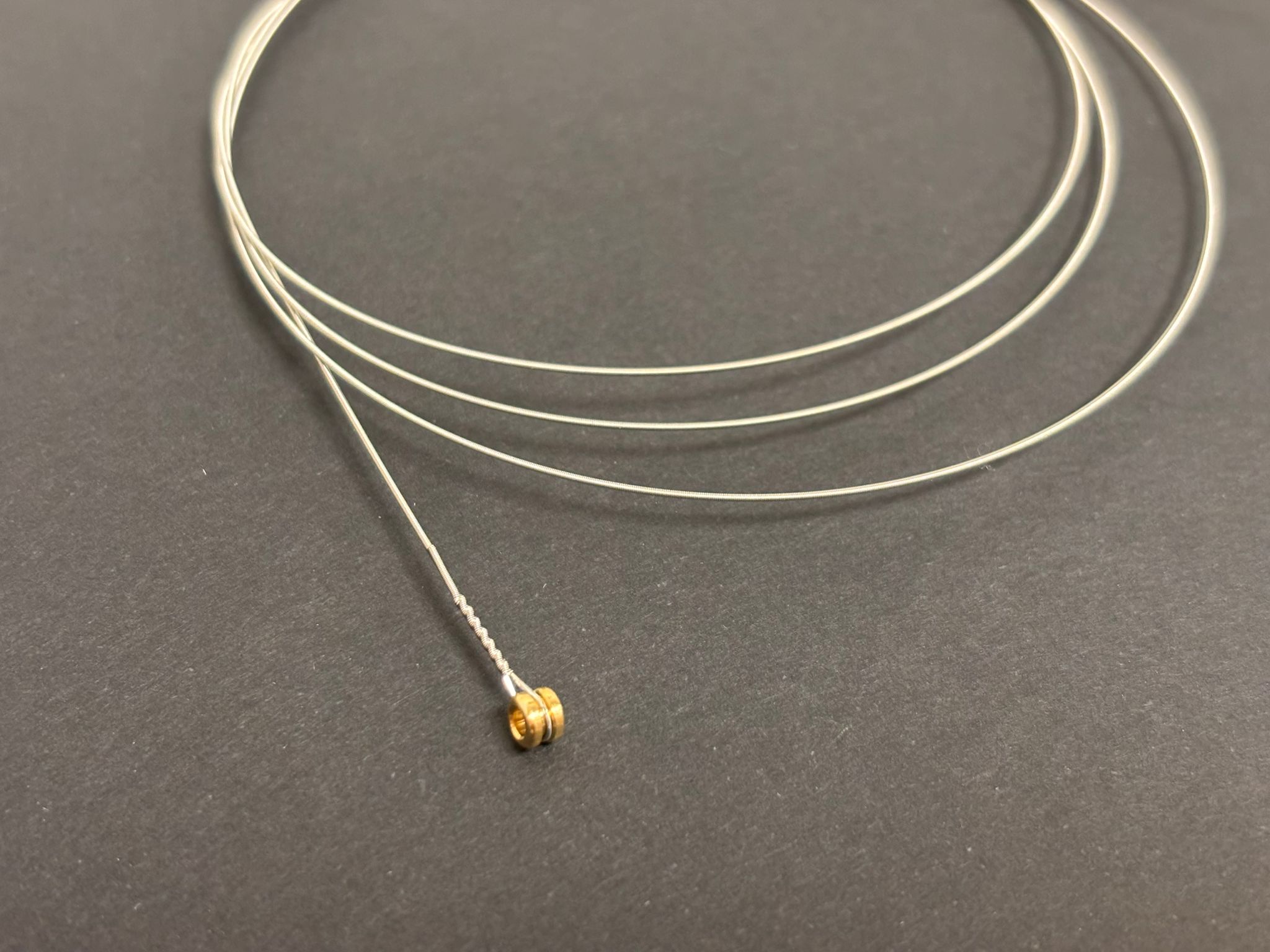
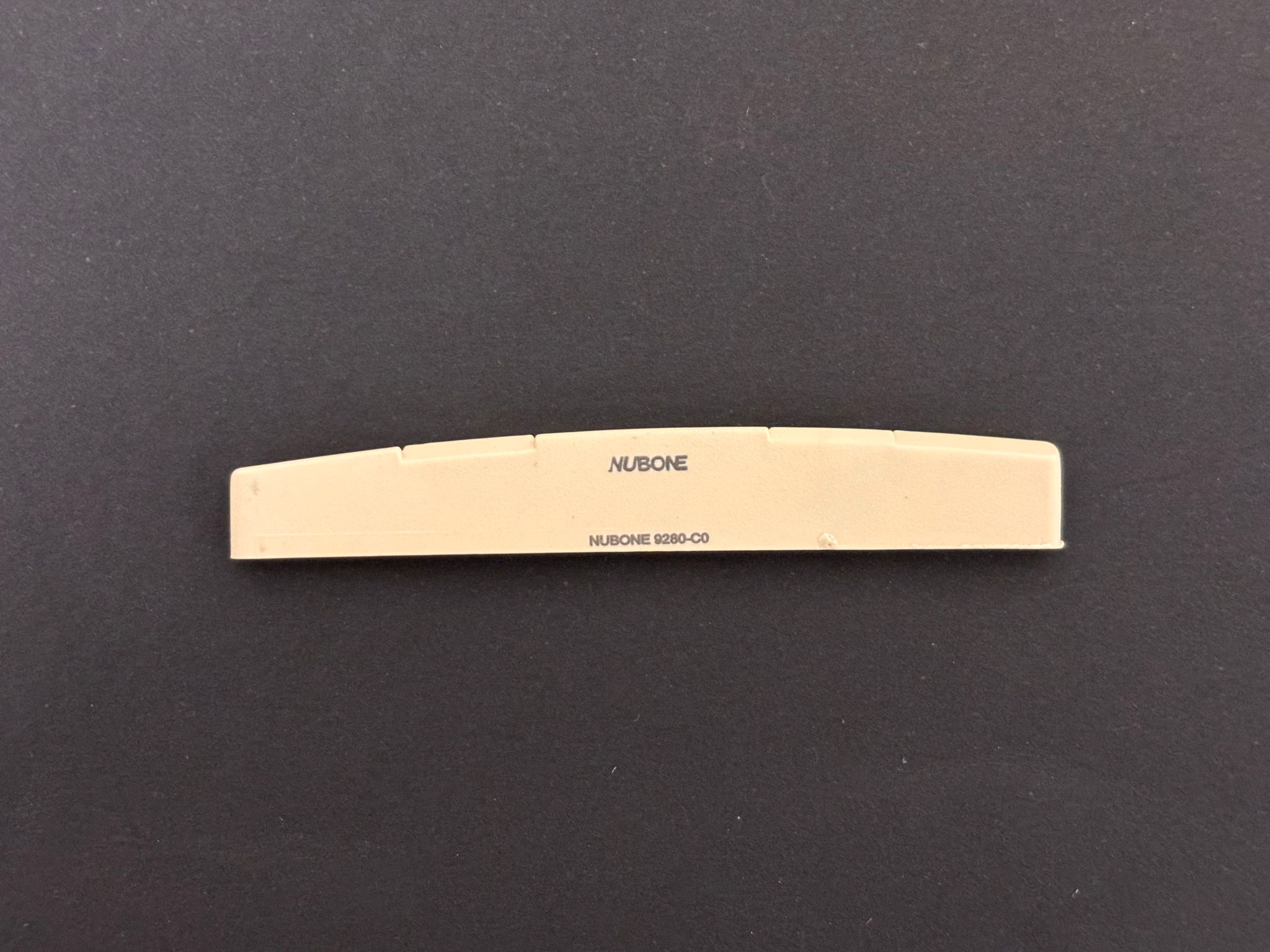
Back at the lab, I started working on the gearbox and learned more about the concept of gear ratios/relationships. It was good to make gears for the first time and to work on a non-programming related aspect of fabrication.
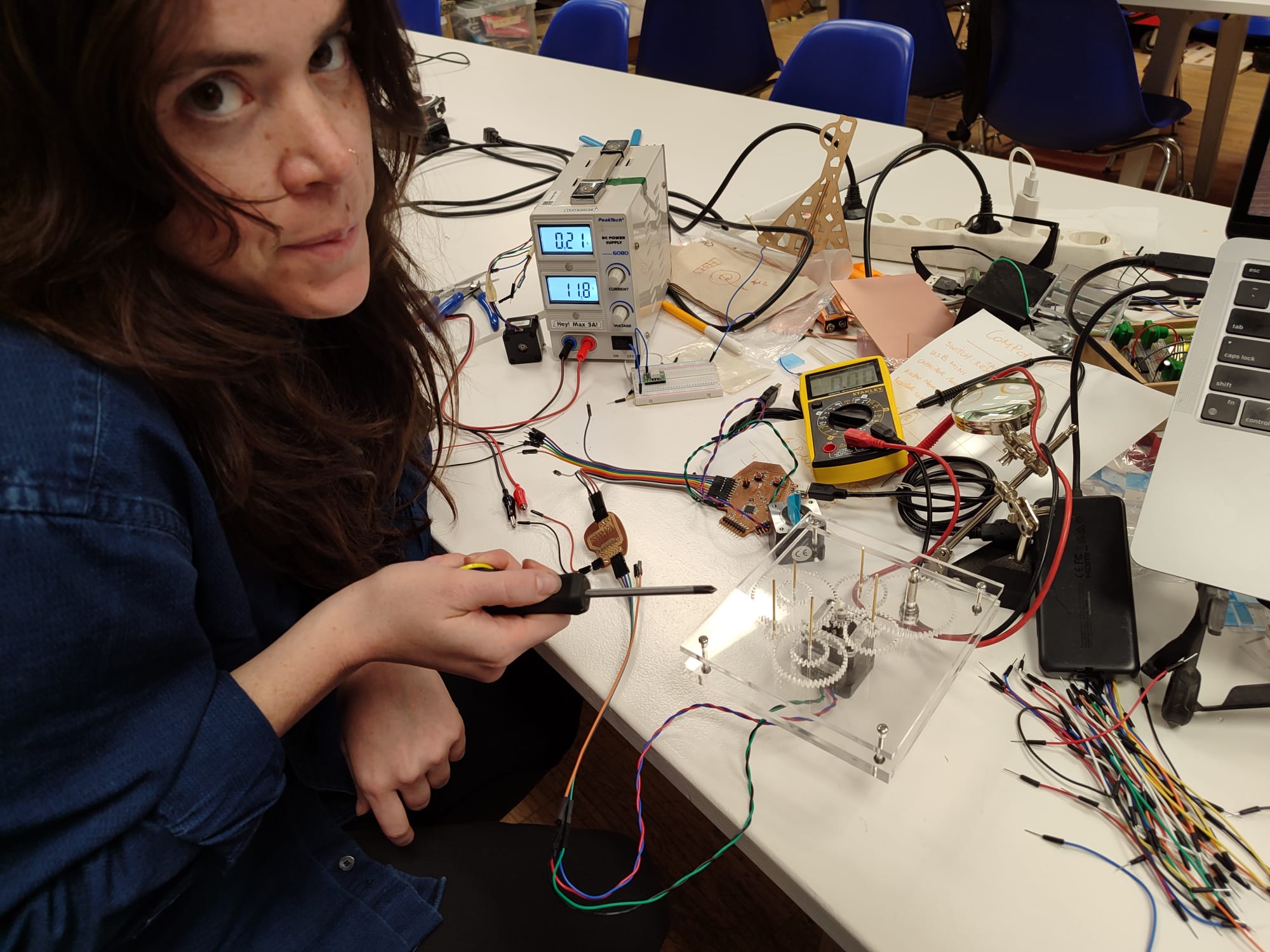
A considerable amount of time was spent testing two different laser cutters and calibrating the machines correctly. After several cut tests, we were able to cut new gears in the acrylics modeled directly after Danni's designs. A couple of things that were not necessary were the cutouts, since it wasn't a mold and laser cutting is a subtractive process regardless.
Another detail that had to be changed was the number of teeth on each gear - the laser's kerfing was proving to be too much for the original number of teeth and made for weaker gears.
This Rhino plug-in was great to produce gears in the 3d model: Rhino Gear Plug-in
Here are the finished gears and gear plates. They were all laser cut in 5mm acrylic, with axles in 1.6mm
thick brass. I countersunk the screws to the bottom base plate so the stepper motor could be mounted nicely flush with the base plate.
And here are the gear plate layouts. I ended up using three:
Base plate:
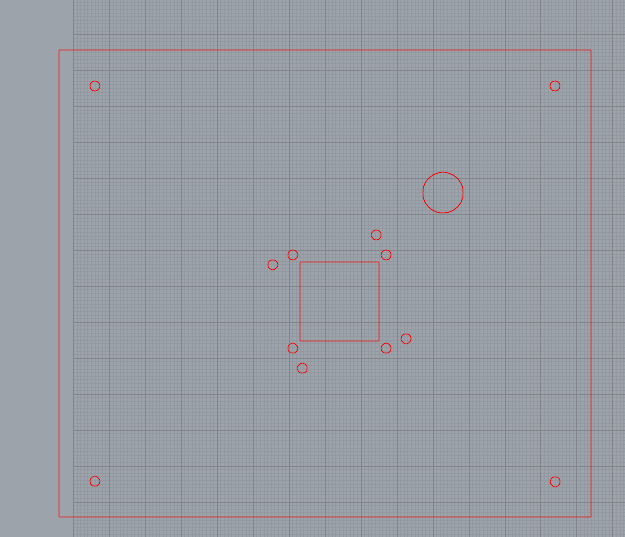
Middle plate:
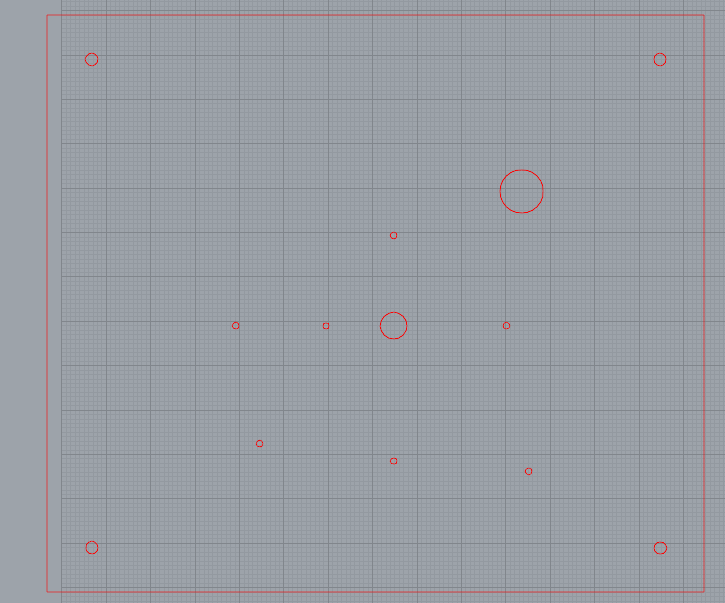
Top plate:
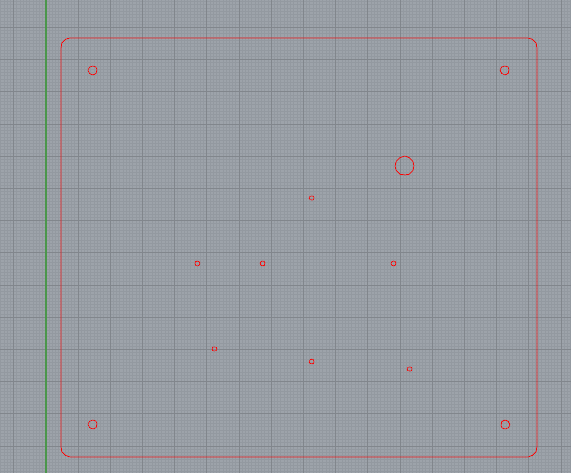
The major challenge here was fine tuning for the gears to function and move smoothly - the metal guitar head component was sandwiched between two layers of the acrylic, and therefore had to be motion tested, the gear plates adapted to account for the intro of ball bearings to reduce rotary friction.
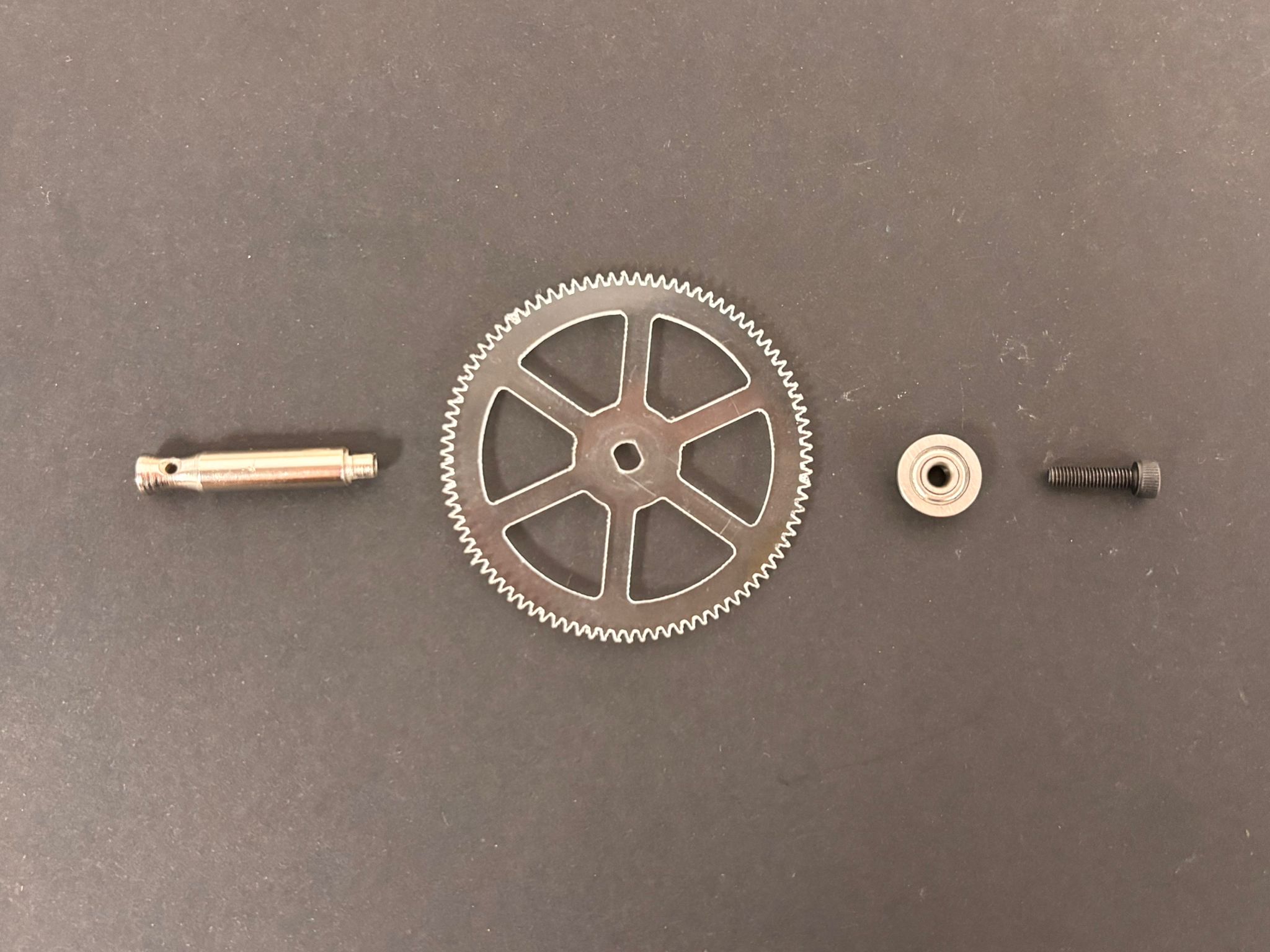
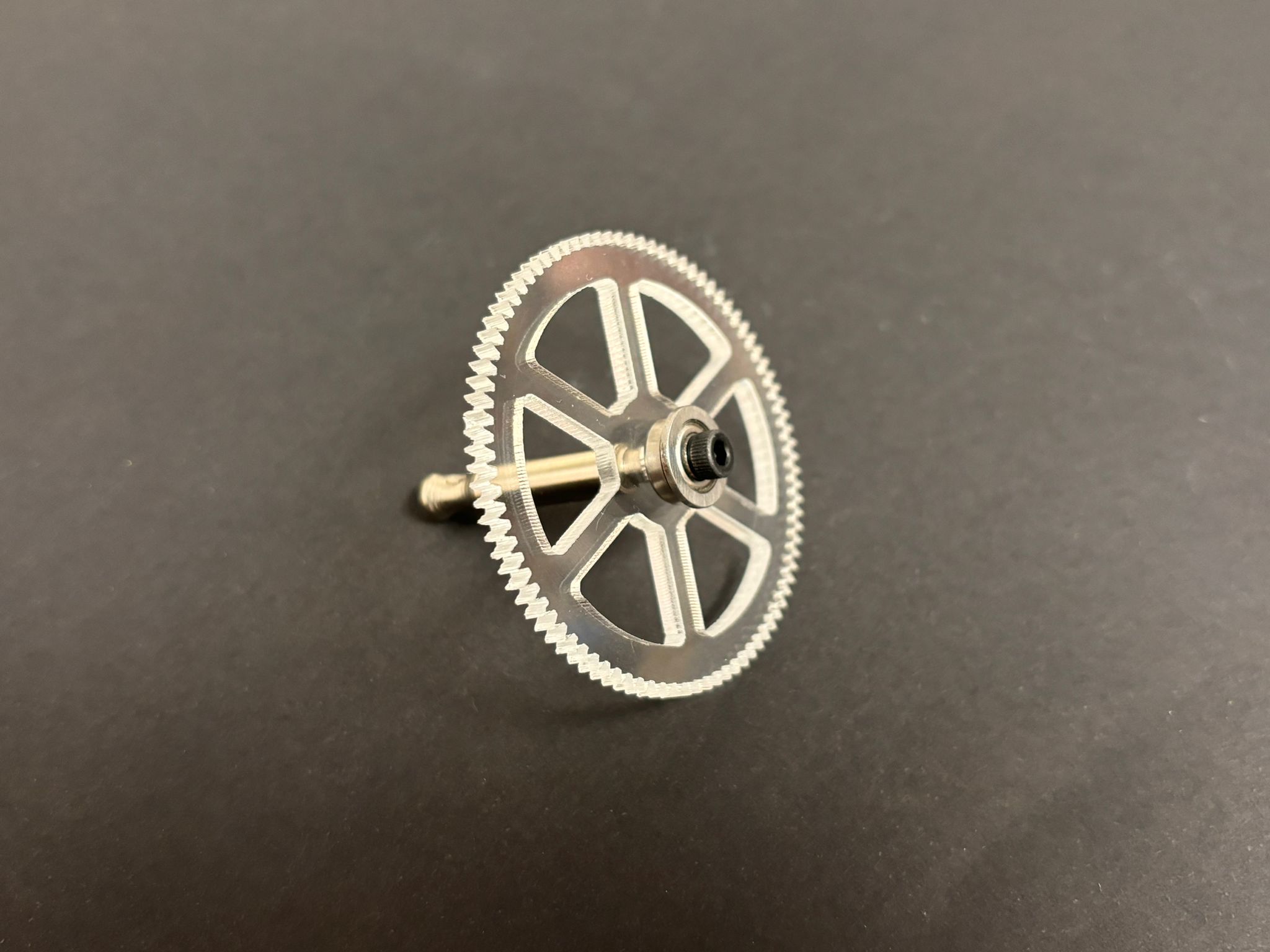
The end result: