2. Computer Aided Design
This weeks assignment is to model the final project through verious methods. The my focus will be on 3D modelling as I sketched the 2D design in Inkscape last week where I did my first digital sketch of my final project using Inkscape. The pen tool can be used to draw b-spline paths which is very useful when trying to draw 3D in a 2D program.
This drawing raised some questions about how the motors would interact as the spun wool needed to move to wind on to the bobbin smoothly.
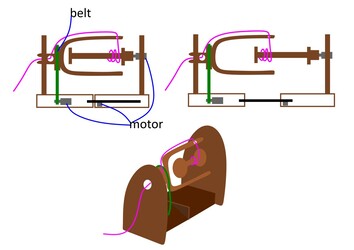
I then redrew it incorperating a fork sliding coupling to move the bobbin.
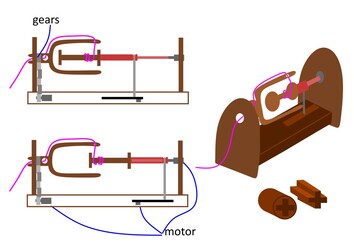
2024-01-31
Following the live I leaarned about some new software that I would like to investigate. Particularly onshape as it is a web design software. I would also like to look at making a rendor within Fusion 360 and possibly have items rotating.
2024-02-01
Instruction with John on 3D modelling basics.
I have a decent amount of prior knowledge on 3D modelling. Majority self-taught after buying myself a 3D printer. I started with freeCAD due to it being free, however it was quite daunting and only relly explored the scetch and part design work bench. I moved over to fusion 360 once I discorvered the free personal use plan existed. I find it to be a easier workflow and cleaner interface and while it is still a hobby for myself it is perfect.
As Fusion 360 is my go to I wanted to find a way to have it running on my linux os, however it ended up being fruitless. I tried Thermionnix's github guide and cryinkfly's however I am not proficient enough to debug the problems.
I decided to use onshape instead as it works on every os.
We modelled a part of a project John is currently making, I had to google to find where to find specific tools as.
Opinions on Onshape
Overall it seems to have the main modelling tools you expect and need and quite a nice interface. However, on a relativly small latop screen you feel the reduced space as you have the clutter of a search bar. Another problem is when you want to pan around the model you use shift + right click
however this brings up the general dilogue box when you rightclick on a website. This was very frustrating to randomly take screenshots and open new tabs.
I will use fusion 360 mainly to model my project but on shape is a decent alternative for quick mockups.
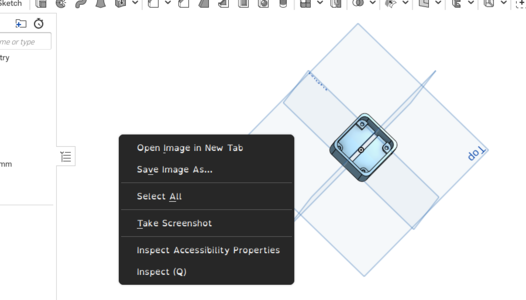
Modelling Project
I modelled a basic model of a motor that could work well for the project. Its a VELOX V2808 drone motor.
.jpg)
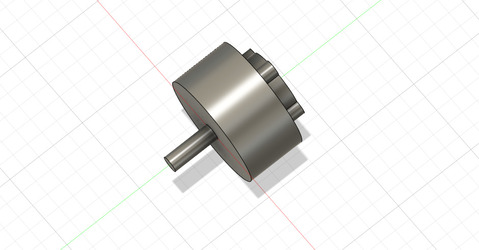
I started looking at modelling my final project however I had some difficulty imagining how the motor attaches to the section that is interchangable depending on the part of the spinner. I was thinking the rod which extends across the amchine was in line with the motor however that can be a issue due to missalignment can put too much stree on the motor bearings. It was suggested to use a shaft coupler or to not make it in line. The shaft coupler allows the shaft some room for movement to lower stress on missaligned bearings.

I started sketching and modelling a alternative design which used gears to transfer the drive sideways.
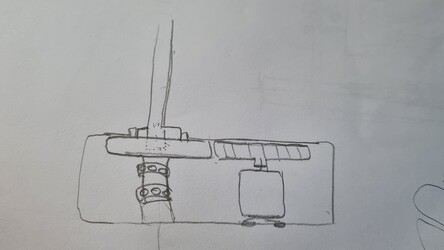
However we reached a issue that we wern't sure how to ensure the tools stayed attached. Could possibly use a thread however theres is a chance it would unscrew itself whilst it spun.
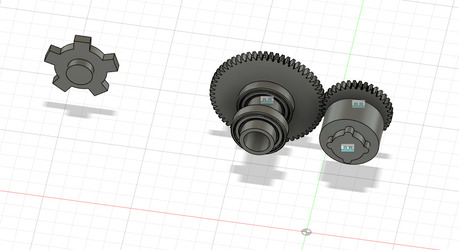

2024-02-02
Whilst helping a local maker in our fablab space I created a parametric mould box design in fusion 360. Although it was lasercut, instead of 3D printed, I find the sketching tools in fusion to be very useful. You can then export the sketch as a DXF file. We needed 3 sizes to parametrics allowed me to scale up the dimentions easily.
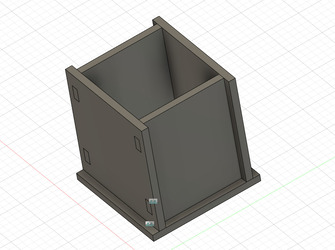
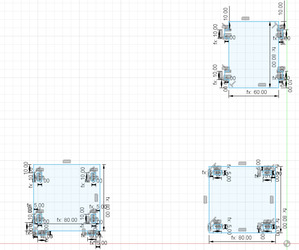
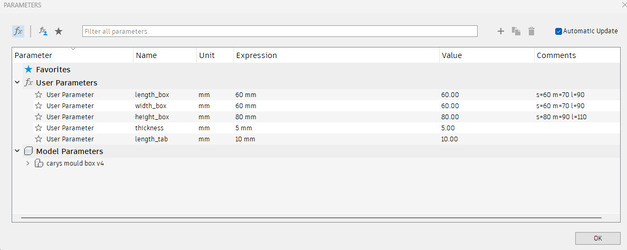
2024-02-03
John suggested a alternative design that uses belts but overall pretty similar. In order to keep the atachements connected we use a nut on the other side of the case.
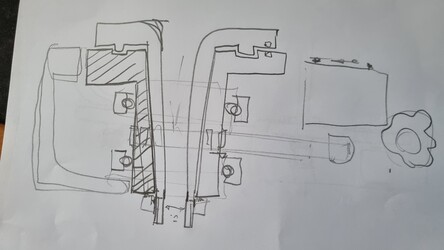
I started modelling this new version in fusion 360. I imported the same motor model in.
In this design I will use 40x68x15 bearings which range from £5-10 on ebay. As well as a polyurethane round drive belt 8mm diameter, for about £5 a meter. There is also a square metal rod to support the bobbin.
Creating a 3D render
I started modelling a basic container for the motor set up, however it was difficult to consider all the dimentions with everything being digital.
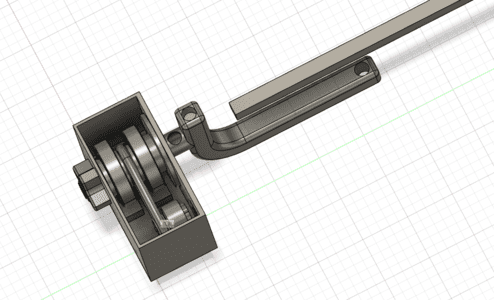
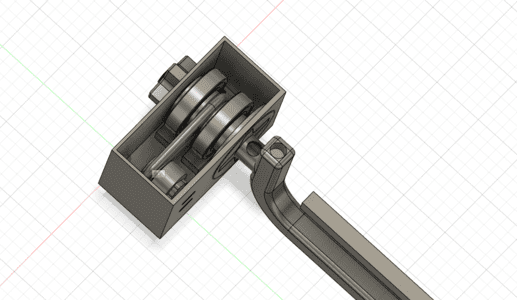
I therefore decided to make a new model which doesn't relie on actual measurements as that was stopping progress. It still allows me to visualise relative proportions between sections.
I used the Render workspace in Fusion 360 to add material and colours to the various components in my design.
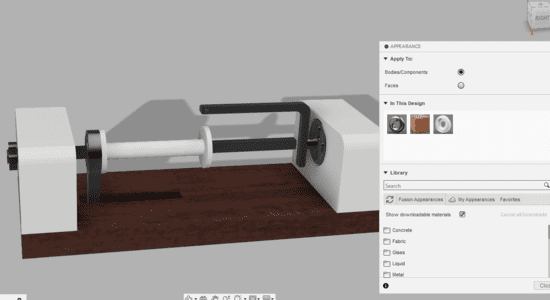
I then exported the renders. This is one section where the personal use version of fusion 360 is limiting. You are unfortunatly limited in the quality of the renders you can make.
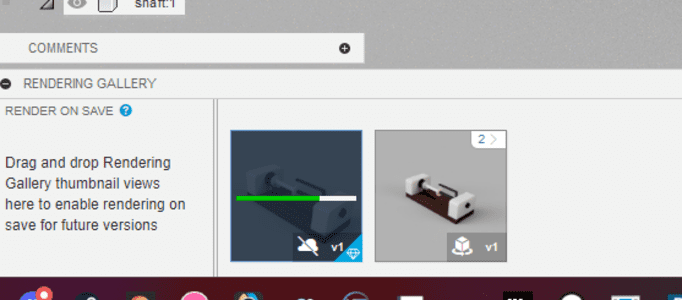
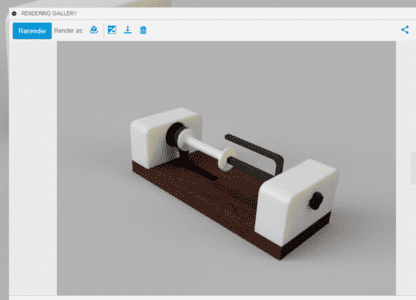
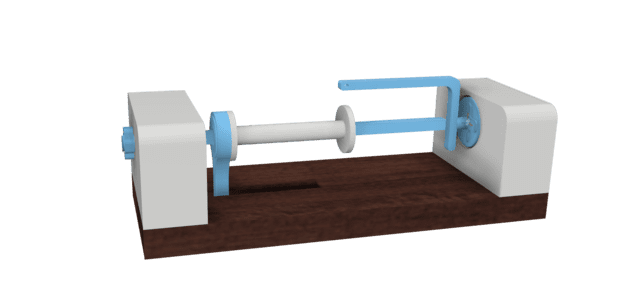
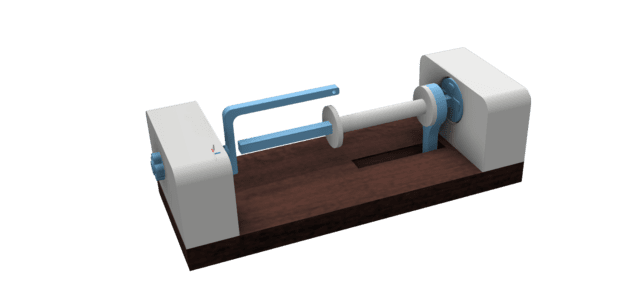
Click to download 3D render file
I decided to try have a embedded 3D viewer of the render. I asked chat GPT for html code which would work and it decided to use three.js. However the .obj export from fusion 360 did not include the textures so i imported into Blender to re-add some textures and then export as a .glb. I attempted to use this code instead from modelviwer it worked in the browser but could not set it up correctly. Although, I could not get this to work, it was interesting to learn about the process and use blender.
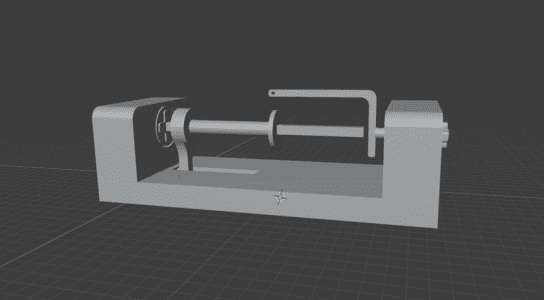
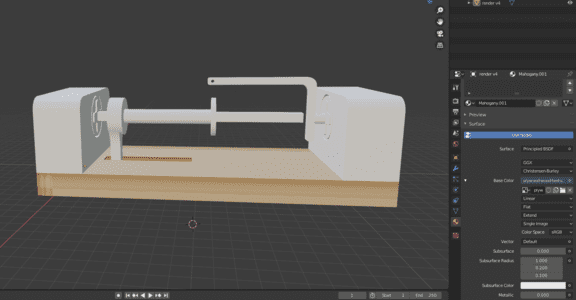