Computer-Controlled Machining
Week seven was about Computer Controlled Machining, making or operating machine called ShopBot which is controlled through computer numerical. Fundamentally, designs were made in the software Fusion360 and tool path is generated based on designs so that the machine can cut following this path ultimately producing the product.
Group Assignment
For the group assignment, we were required to attend safety training, test the runout, fixturing, alignment, speeds, feeds of the machine. The link to group assignment is Bhutan FAB23 group.
Safety Protocols
Under safety protocols there are two aspects to be taken care of which are Safety of Machine and Operator(User). For user/operator safety, it mainly deals with Personal Protective Equipment (PPE) and they are mandatory to put on when operating ShopBot for it being heavy duty and accident prone machining if not taken care as listed below :
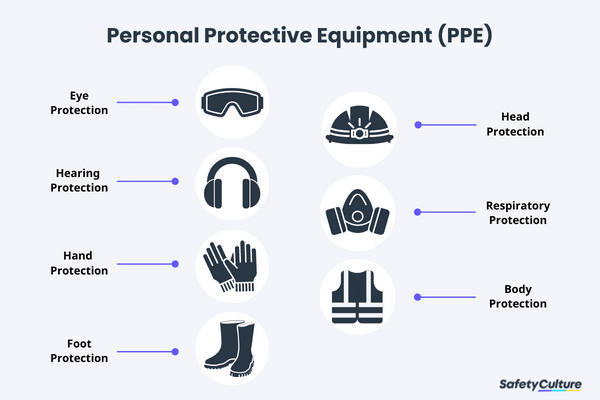
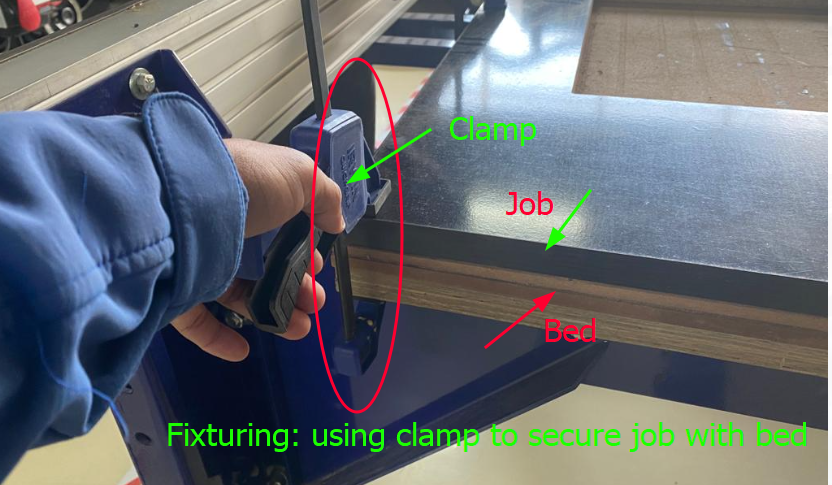
An Image from Google
Run-Out
To check the run out of machine in JNWSFL, we tried cutting 3 square boxes with parameter setting, (1) outside cut (2) On the line cut (3) Inside cut. Theoretically, the box of outside cut has to fit in the slot of inside cut, but in reality our outside cut box did not exactly fit. Therefore, we found out that there is run out of approximately 1mm. We also tried using dog bone, which made it easier to fit journal in the slot.
Optimizing Speed and Feed Rate
We followed the manual for characterizing this or you can get information from SHopBot Manual. Started off using an RPM derived for the chip load for the material being cut (Material was MDF-Medium Density FiberBoard). Increase the cutting speed (feed rate) until the quality of the part finish starts to decrease or the part is starting to move from hold downs. Then decreasing speed by 10% and decrease RPM until finish deteriorates, then bring RPM back up until finish is acceptable. We tried for 1/4" end mill for up cut (Up cut bit is designed to quickly move chips up and away from the surface being cut. The grooves in the bit will pull the debris up so that it will not stay in the area being cut. The design of this tool means that it is able to be used at a higher speed than some other tools) and down cut (its method of chip removal is to push the chips down into the surface, which can make it less effective and you will need to consider some form of vacuum to clear them away. Down cut bits require lower speeds to produce quality goods and will produce a fantastic finish on the top of the piece).
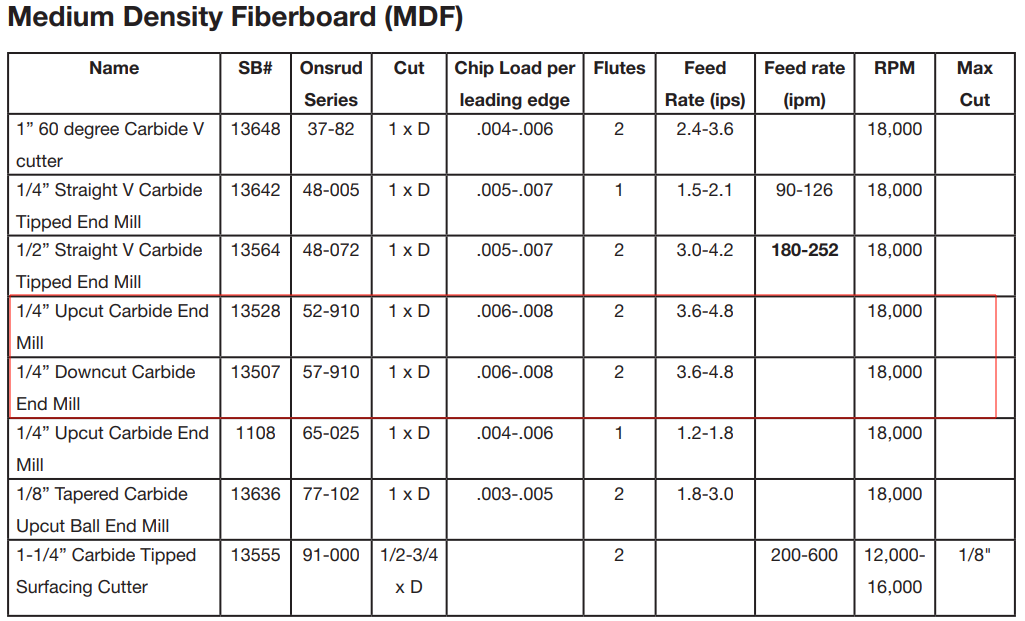
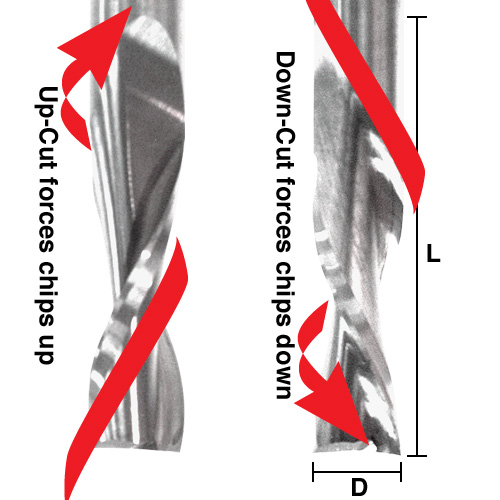
Individual Assignment
We were required to make (Design+Mill and Assemble) the product of minimum one meter using ShopBot. Therefore, I designed a half-radial shoe rack with exterior diameter of 1000mm with three layers in Fusion360. We were given a job of 8*4 sq.ft from which we can make our product.
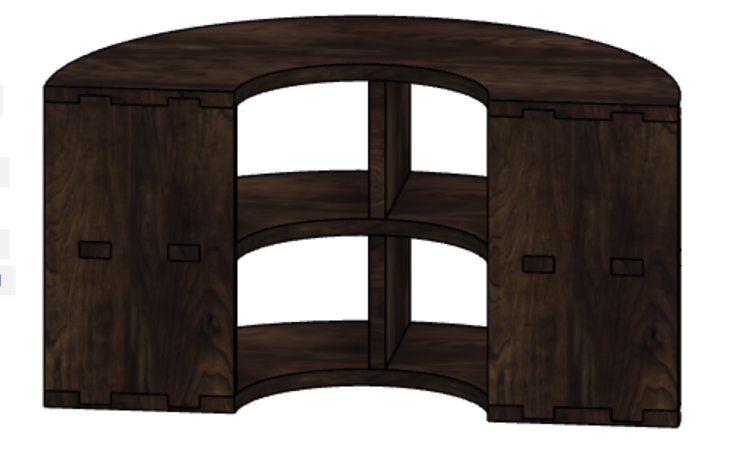
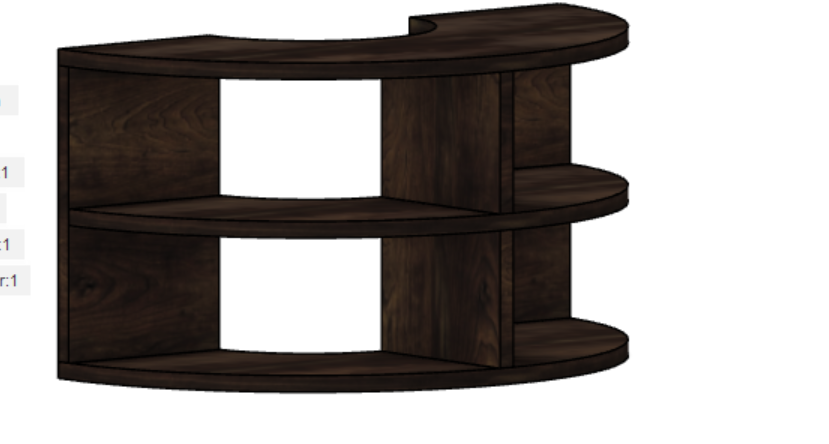
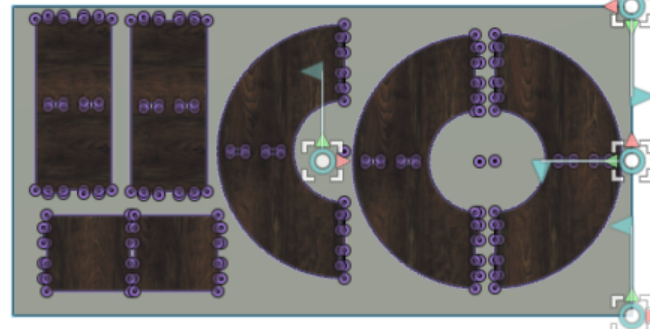
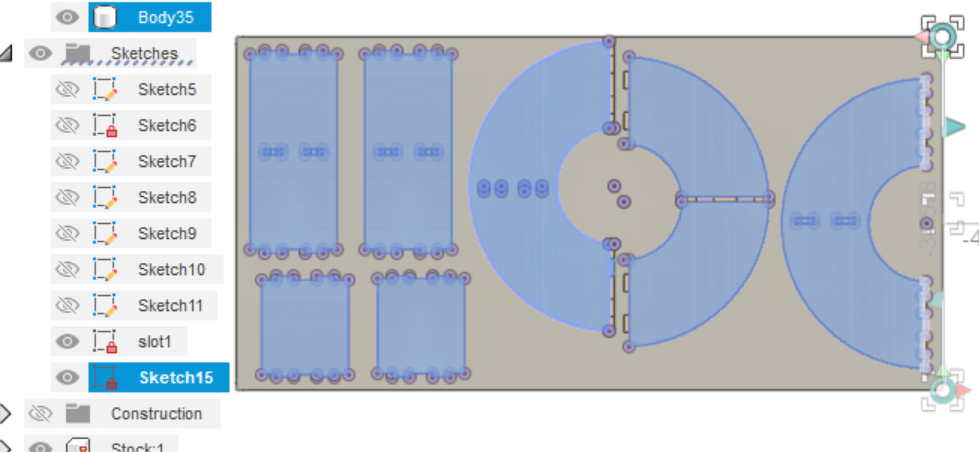
WorkFlows of operating ShopBot
After your design is ready, it is time to operate ShopBot to machine your product. Before directly operating, there are certain settings which should be set.
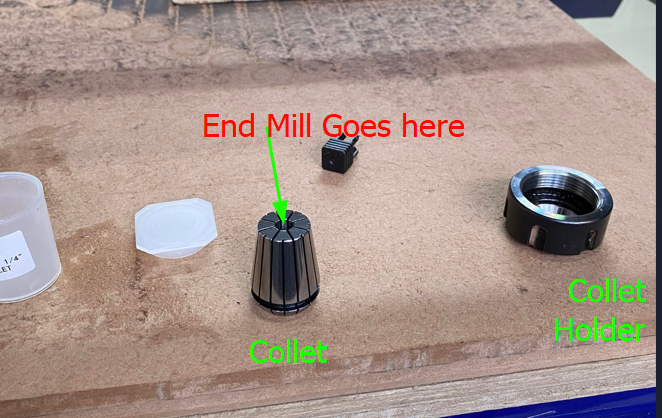
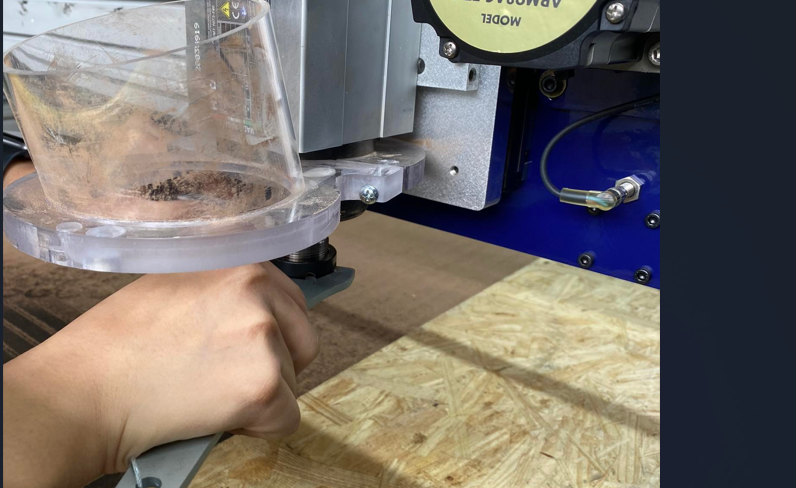
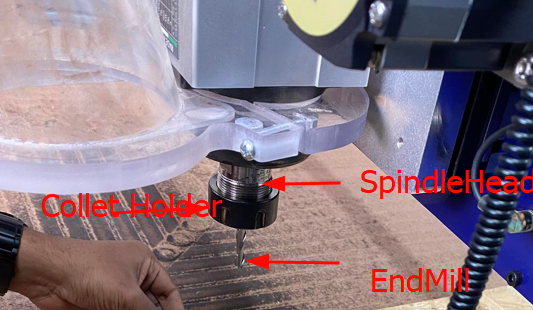
Note: Its important to see that the collet and end mill sizes are same when fixing end mill to collet.
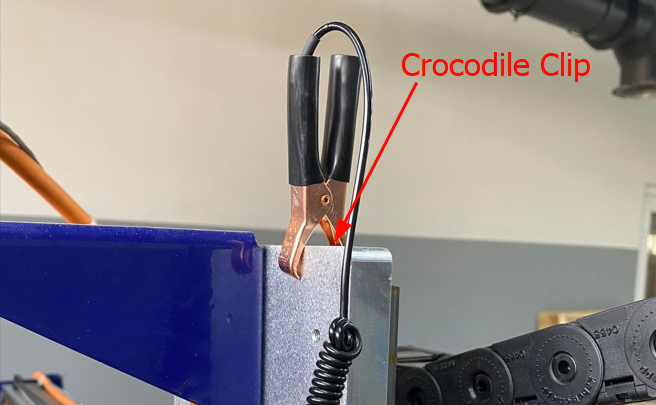
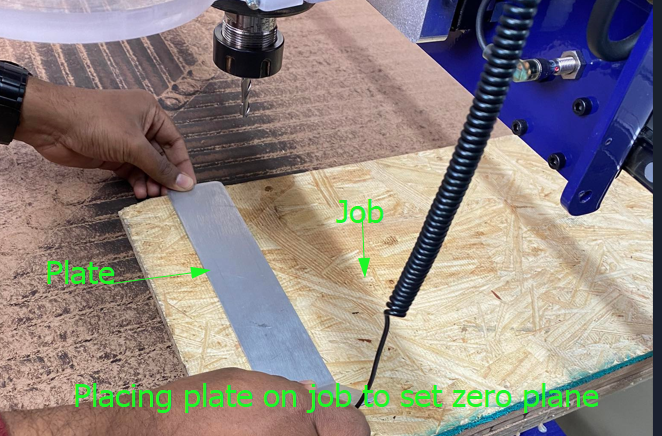
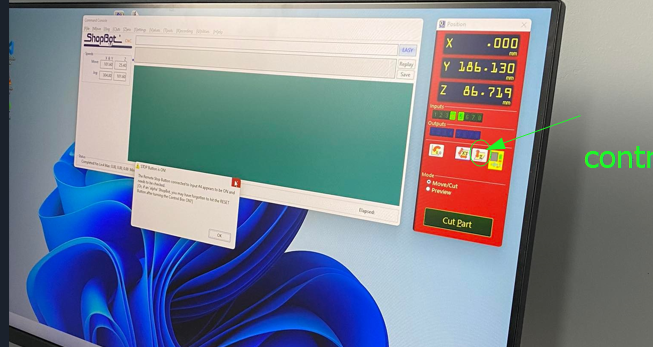
Cutting/Machining Using VCarve
Open the VCare software which is installed in the computer that is connected to the ShopBot
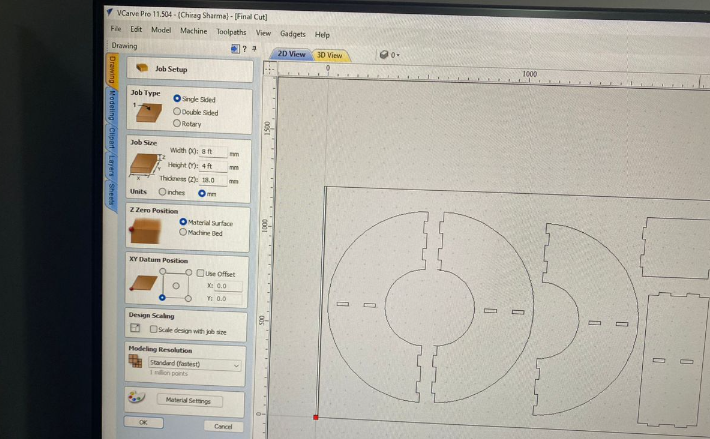
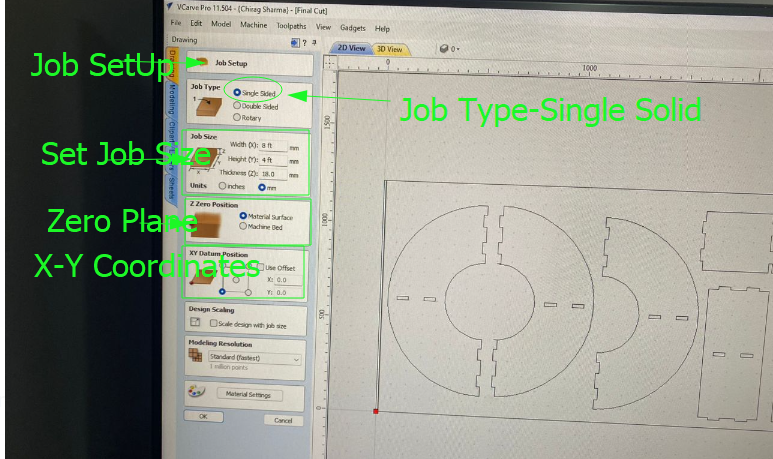
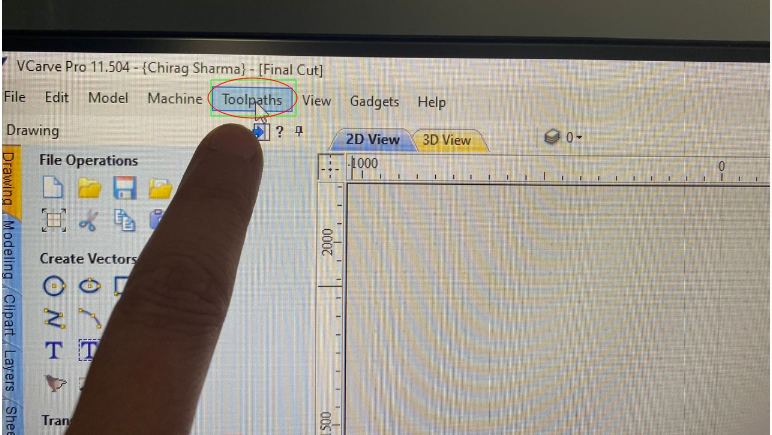
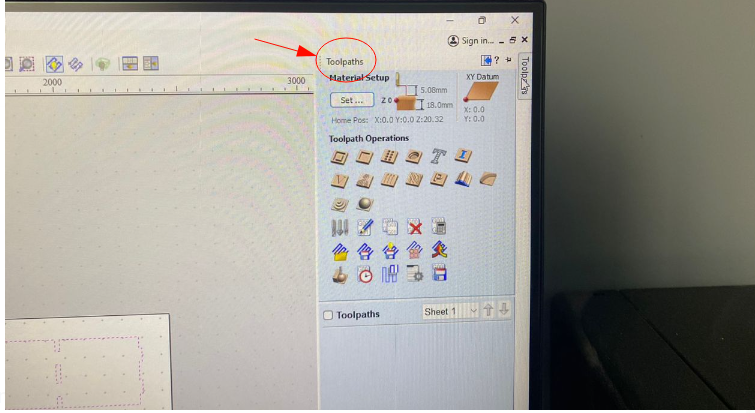
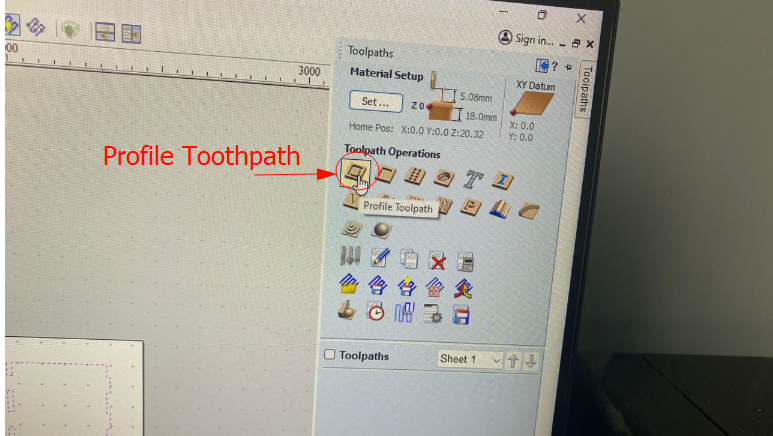
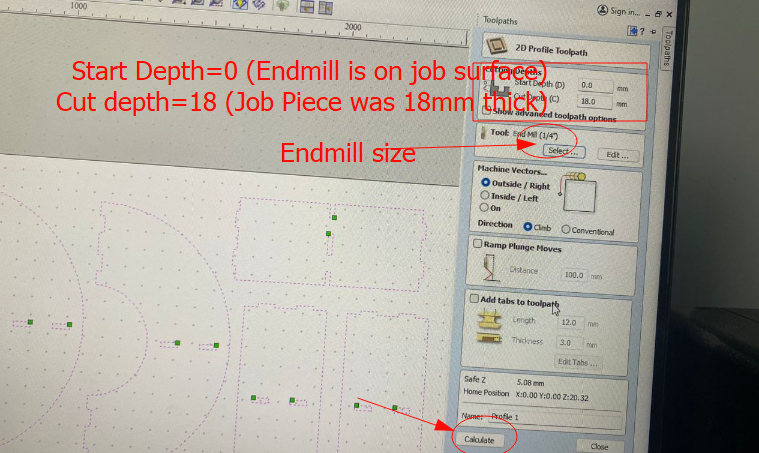
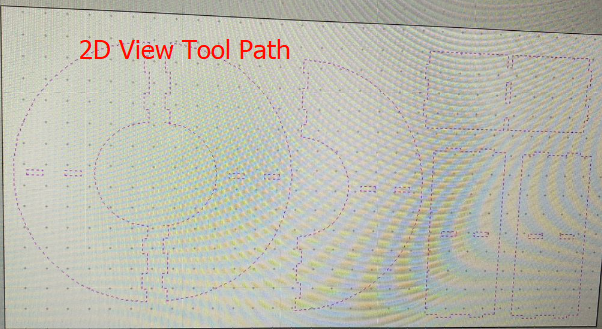
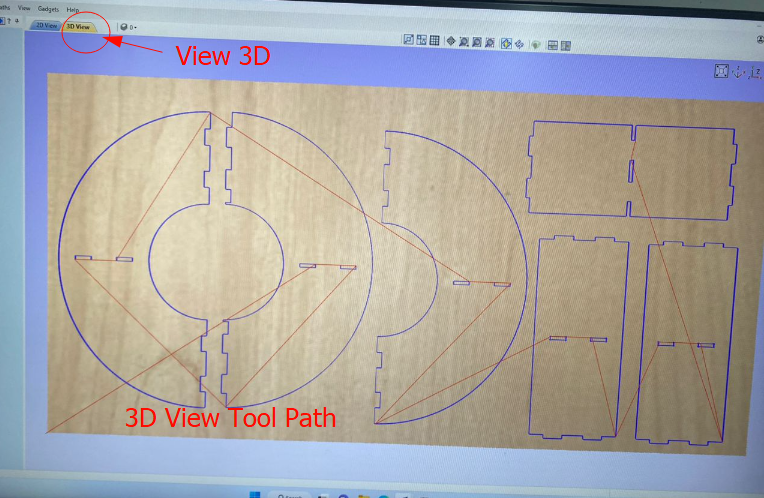
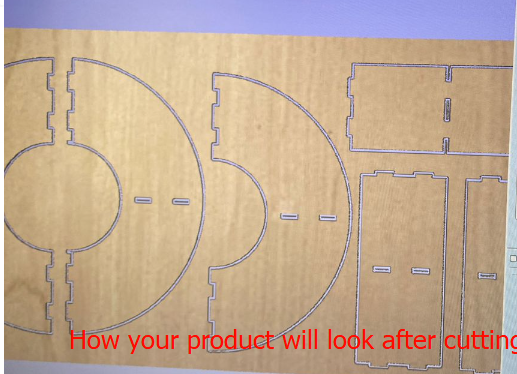
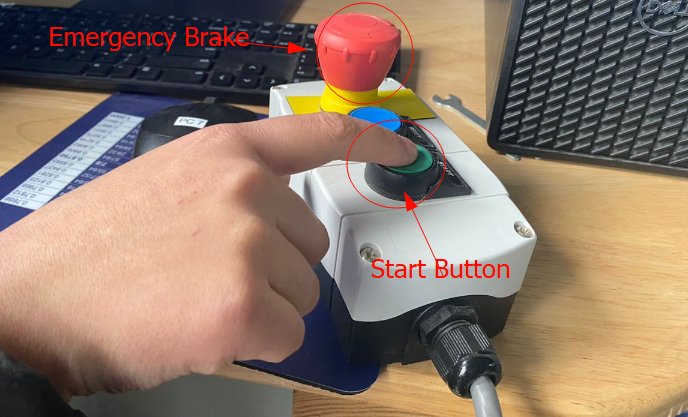
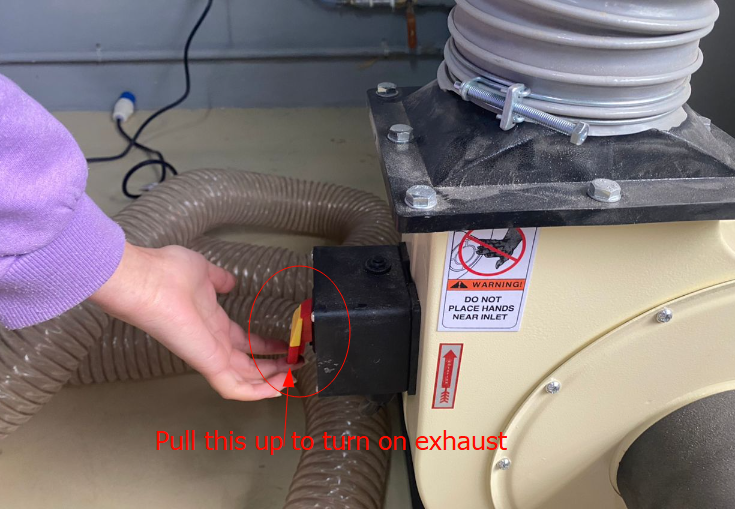
Setting Machine Parameters
Machine parameters like spindle speed and feed rate has to be set before really start machining. Therefore, to cut specific job material, there is certain speed and feed rate to be checked and I cross-checked with the manual of shop-bot and used the speed from MDF (Medium Density Fiberboard). That is using 1/4" up-cut carbide tool at RPM 18000 (Spindle speed) and 4 inches per second feed rate.The image below gives good idea of setting machine parameters relative to the type of job material.
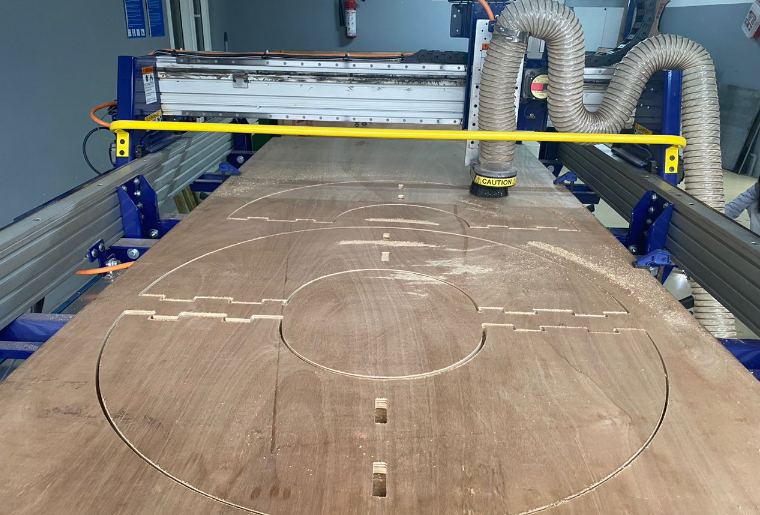
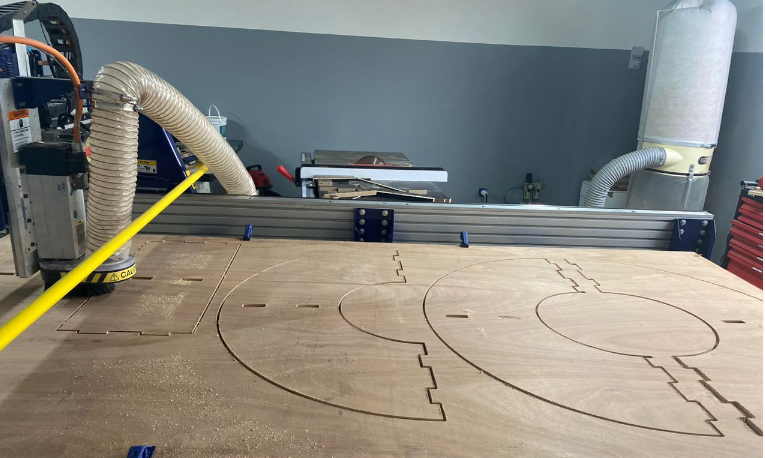
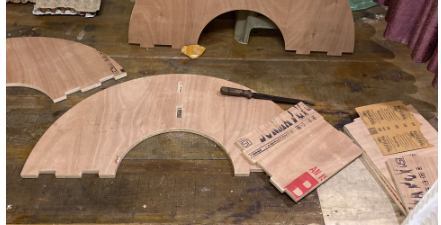
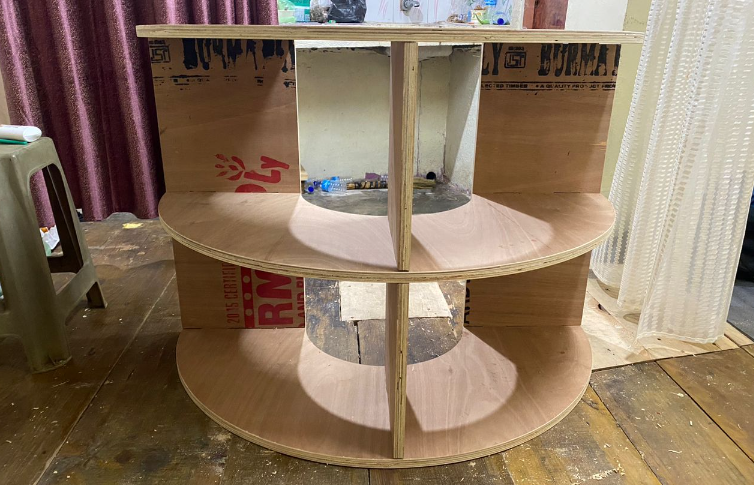
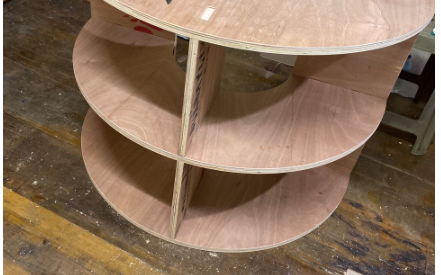
The hero shot of the product that I made can be seen as shown below. Initially, I planned to use it as a shoe rack but turns out it can be used to store egg trays!
Experience
I had the experience of using Shop-bot and and setting it up but it was my first time to use VCarve to edit my 2D sketch and control the cutting which further encouraged me to learning about the machine. I was bit afraid of using Shop-bot during FABZERO program but the experience changed marginally during FABACAD23 and I felt comfortable using the machine which indicated that I was much familiar with the safety procedures and use of the machine. Overall, I knew that this machine can build any product that best fits the requirement of every individual at home provided the safety of both man and machine is taken care of.