3D Scanning and Printing
Group Assignment
The group assignment was about testing design rules of the 3D printers at lab. Therefore, we downloaded the testing model from the link Design Rules Test Model to check on parameters like:
1: Overhang Test- What could be the highest degree that printer can print hanging parts
2: Bending test-What could be the maximum length machine can print good
3: Micro-engraving -minute engraving or writing on models
Link to Group Assignment work: Bhutan FAB2023
Observation/ Learning
Overhang test- From this test I came to know that support is required after an angle 60 degree. However, giving support from 45 degree can be better but it increases material cost and post-processing. Bending Test- From this, bridging was not that good after distance of 3cm. However, it can be good to avoid bridging failure by giving support.Micro-engraving- Minute letters weren't printed good, therefore, it is advisable to avoid using letter size below 5mm. Note: This experiment gave us a good point of reference as to what expectations that our printer in our lab will be working as per design rule.
Individual Assignment
The fifth week of Fab Academy 2023 was about 3D scanning and 3D Printing which I was quite familiar with. Therefore, it did not look intimidating unlike other weeks. However, 3D scanning machine at SFL was non-functional and we were asked to download & install Kiri Engine on phone and scan 3D objects. For 3D design & printing, we were asked to design and 3D print an object (small, few cm3, limited by printer time) that could not be easily made subtractively.
3D Design and Printing
3D design was made in Fusion360 and the procedures are as given below.
1: Started 3D design from sketch which I always prefer for it being precise and can be manipulated in case of error. The image below was designed in AutoCAD as design guide to my 3D design, which can be replicated in Fusion 360 to convert into 3D. This guiding design is for quarter of my original design only. Started with Top view 2D Sketch of frame.
2: Extrude the sketch to convert it to 3D and then mirrored the object.
3: Now design another component and align or join with frame which can be rotated.
4: Joining the components and aligning
5: Exporting the design in OBJ format so that can be read in PRUSA SLICER.
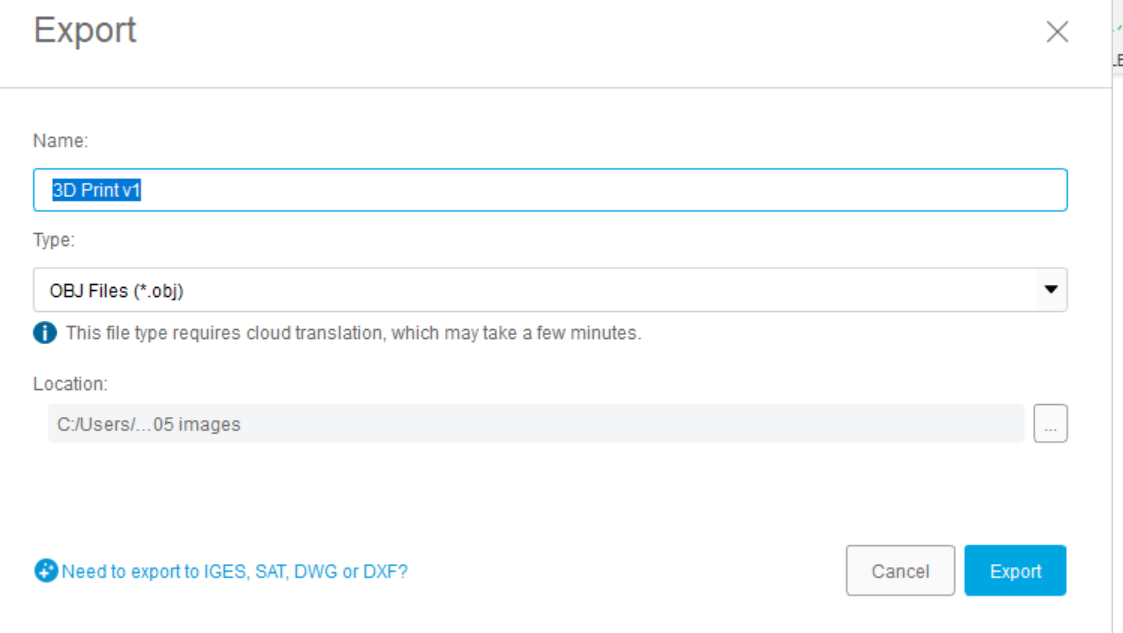
Design is completed, it is time to use this design file in the slicer to generate G-Code and also to check compatibility with the printing machine.
Using Prusa Slicer
1: Open your design file with Prusa Slicer by right clicking on file.
2: Your file opens up in slicer window. Here, you can change parameters of design and that object to be printed. If you look at the left side of window as demarcated by red rectangle, you find options to Move, scale, Rotate, Place on face, Cut, Paint support and Seam paint. These are used when you need to modify your object orientation, size manipulation, giving support when printing and to draw your seam line.
3: First we select 3D machine type/printer selection, indicated by red rectangle. Then choose the quality of print that you want on your object. And select the filament type that you have with printer. Generally, we use PLA for trials and readily available.
4: Infill check depending on requirement of strength in your product. If you need strong, you can use more than 80% infill. Support is not used because my object does not require. Then slice to generate G-code.
5: You will see estimated time, preview of printing, volume of filament to be consumed and so on as shown. You can click and drag as shown by red arrow to see preview of printing. Then if it satisfies, export G-code.
6: This G-code can be transferred to Disk of Printer machine and then Print. Based on my filament selection, 3D printer will pre-heat the bed and nozzle 60 and 230 degrees(PLA) respectively before really starting to print my object.
Useful Information
Z-seam
Z- seam is used to create a specific joint in one vertical line or as you desired (If not the joint in each layer will be distributed). Example given below is seam line and you can control that line on which face you want by drawing seam line as shown by next image.
None: tells your slicer to make no special preferences when choosing the starting point of a layer.
Hide Seam: places the seam on the inner corners of your model. With the seam on the innermost corners of the model’s shell
Expose Seam is the exact opposite of the previous one and places the seam on the outermost corners.
Cut option
The cut option allows you to print the object part by part if you really need bigger object which exceeds the total height of machine/(print area).After printing parts, you can join them with the help of glue and any paste material. Example as shown below:
After perform cut, you can arrange the objects or hide one and print alternatively. My product is printed with 0.2mm layer height, no support, 5% infill and the product came out as given below:
The individual components inside can be rotated freely, however, you need to remove some debris in between the axle and holder hole which is leftover from the support material. If you don't use support material in between then the individual components get attached to the base when printing. The individual component image as shown below and hero shot of the week.
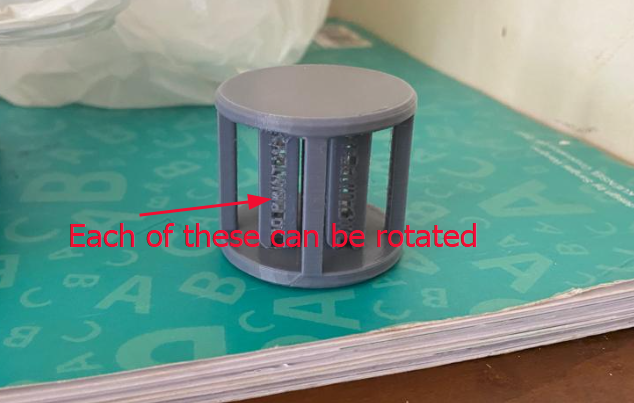
3D Printer and its parts
After inserting the disk in printer, rotate the Knob shown by red arrow to see options like drop down, press Knob to select your code. Filament is placed on holder and extruded through nozzle which gets printed on bed layer by layer. This process is additive manufacturing (Fused Deposition Method).
3D Scanning
For 3D scanning, we were to install KIRI Engine on phone and use the app to scan complicated 3D objects. After this document. Therefore, I have installed KIRI Engine 3D scanner in my phone and used it to scan the Statue of Buddha.
Process of scanning and Creating 3D
Step1: Opening Kiri App on the phone and you see a plus sign icon at bottom, and click on that.
Step2: Before that, place the object/product that you want to scan on the rotating chair covered with smooth white paper and also white background suggested by Ms. Yeshey.
Step3: Soon after you see the option to video record your object or to record by snapping photos are several angles. I chose to go with recording with video option.
Step4: Gradually/Slowly rotate the chair by pressing the video recording button and you see the options as shown below after recording where I have selected face count as Medium, Texture Quality as High, and File format as STL.
Step5: Then press on the Upload Button, where you see the status of your photos uploading
Step6: And you see upload successful notification in addition to queuing information meaning to generate 3D models from the photos uploaded. (It took around 30 minutes to get the scanned product after queuing which made me restless).
Step7: After waiting 30 minutes, your photos are compiled by the app, and your model gets downloaded automatically. Note: Unfortunately, my 3D model was not generated as it is expected of
Step8: Therefore, I repeated from step no. 2 but this time I chose to snap photos instead of recording video. Snapped photos from all the angles and from the top as well. Note: Maximum numbers of photos that you can snap was 70 for Kiri and I snapped 69 as marked inside blue rectangle.
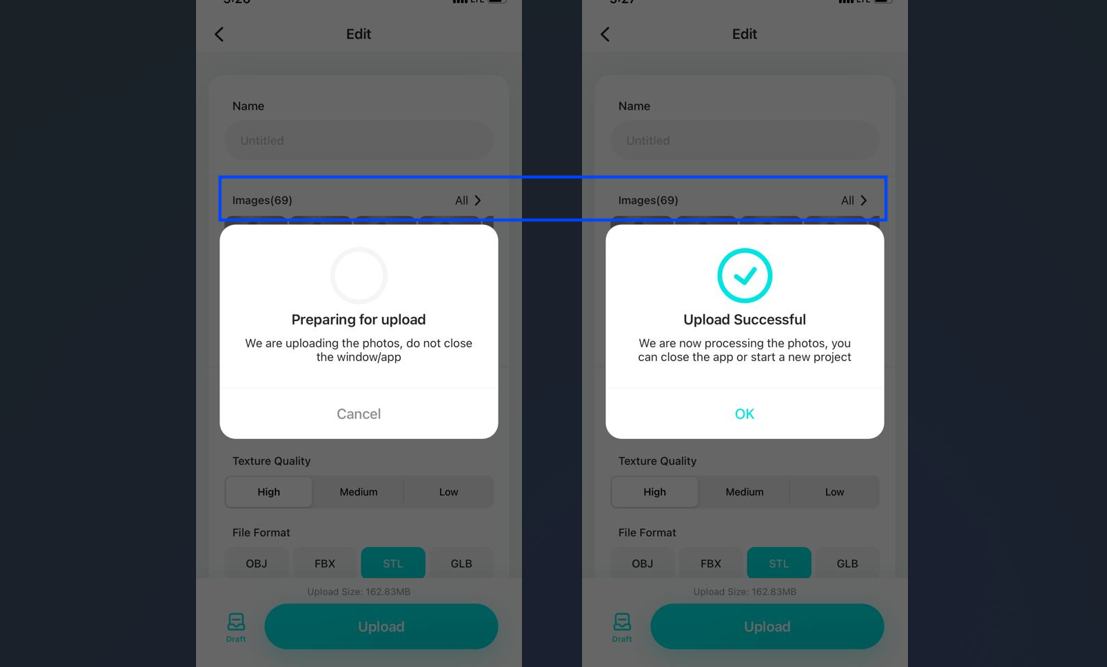
Step9: Now my model was generated after waiting another 30 minutes for queuing, following image says it was successful scanning.
Step10: The base of model (Circled by red mark) didn't look good and therefore, had to be removed. To do that played with Move boundary bar after selecting planes demarcated by red arrow one by one and click Apply.
Step11: Then click on export and you get option to send your file to the gmail account that you used to install Kiri engine. Then you get the Zipped file in your mail up on clicking get your model from which you need to extract the 3D model STL file. This 3D model STL is imported in Prusa Slicer to set the printing parameters as I have shown under Using Prusa Slicer.
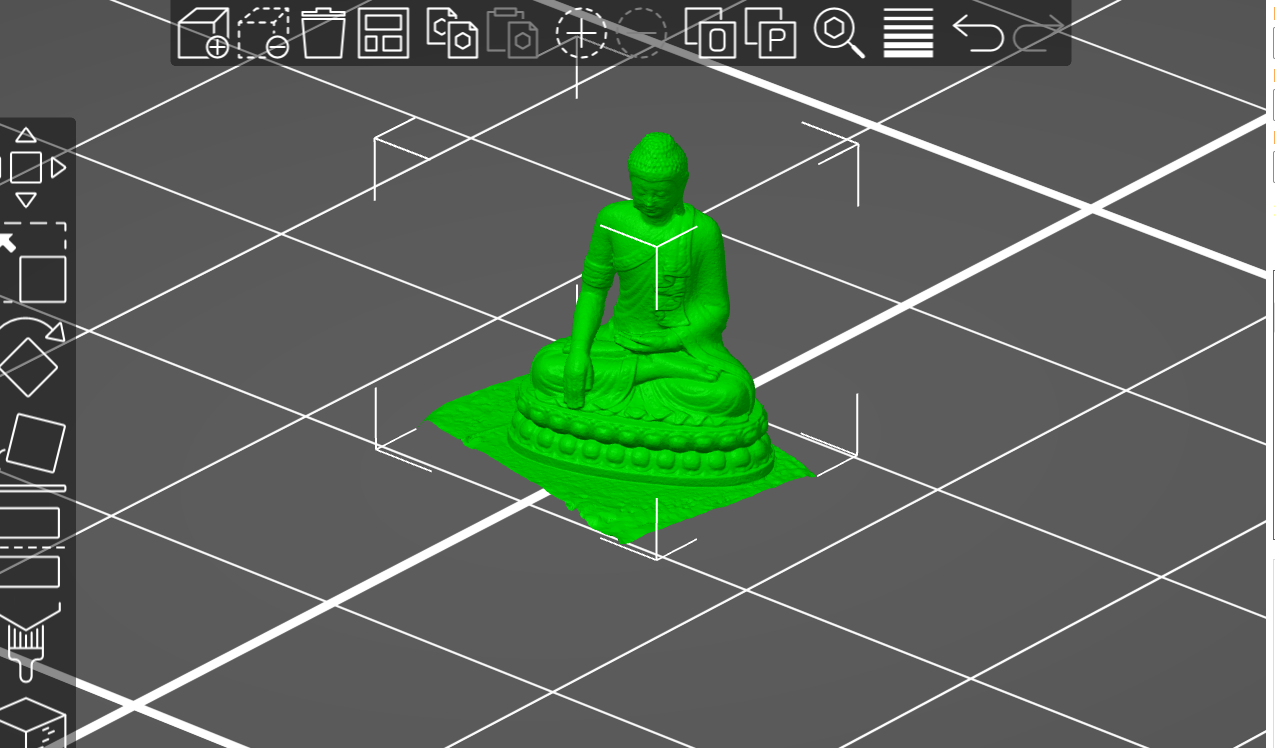
Now the 3D scanned model is ready to print.
Design Files
Designs Week 5