Mechanical Design, Machine Design
Group assignment: Part 1
Group assignment: Part 2
Individual:
Group Assignment
Idea: Polargraph
Polargraph controller Copyright Sandy Noble 2018. http://www.polargraph.co.uk/Our team member Dorian
had the idea for a wall drawing machine.
This wall drawing machine, sometimes also known as a polargraph , is a type of robot that uses two
stepper motors to move
a pen or marker along a vertical surface,
such as a wall or a large sheet of paper. The motors are controlled by a computer program that
sends commands to adjust the length of two strings,
which are attached to the pen and run through pulleys. By varying the length of the strings, the
motors can move the pen in any direction
on the surface. The computer program can be controlled by a user, who can draw images or text
using the machine.
The special feature about our wall drawing machine is that it can be put onto windows/glass via
two vacuum lifting tools on each side.
Making it useful for reating any glass art and especially for
writing text or art on the display windows of shops.
Work distribution
Since we're all living very far apart (France, Australia, Germany) we can't work on the machine together in person. Therefore, we're building multiple versions of it at our own Labs with our own small twists to it. Throughout the process we did several meetings and collaborated on a Fusion project. We shared our progress and ideas for the project and it's outcome. That's why we don't have clearly divided tasks, but we are all helping each other throughout the whole process.
Design & Assembly
Note: Dorian and Uwe created a 3D design of the plastic part of the vacuum lifters which already has an integrated stepper motor bracket. I have slightly different sized vacuum lifters plus I also wanted to produce the prototype as fast as possible, so I used existing 3D models for the brackets and the gondola from the web and mounted them using screws.
Component | How Often Needed |
---|---|
Arduino UNO | 1x |
L293D Motor Drive Shield | 1x |
L293D Motor Drive IC | 2x |
Nema 17 Stepper Motor | 2x |
MG90S Servo Motor | 1x |
GT2 Pulley 20 Teeth Set | 1x |
GT2 Rubber Belt 5mm 20T (3-5M) | 1x |
9V Power Supply | 1x |
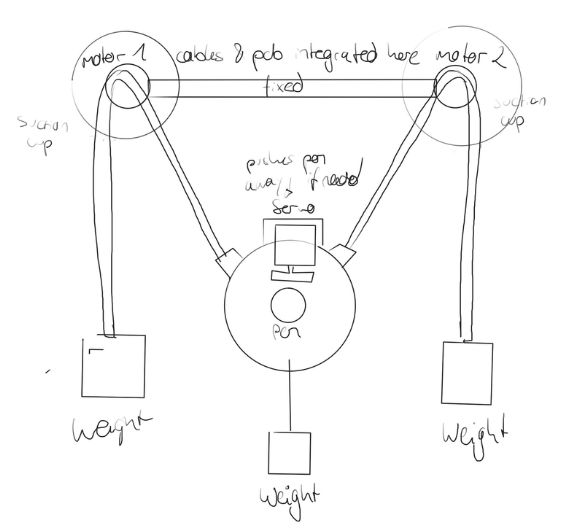
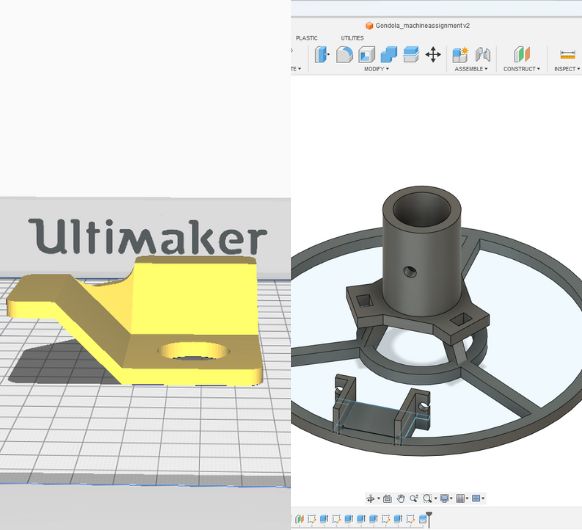

Fusion file
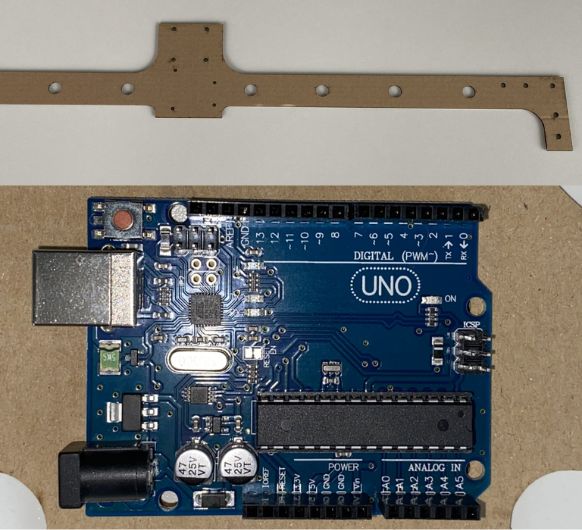
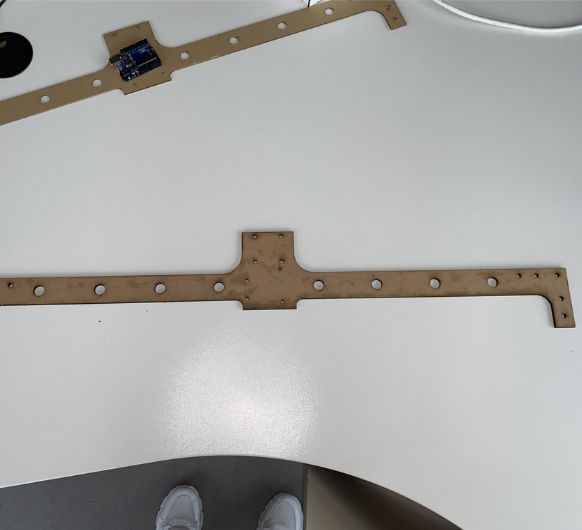
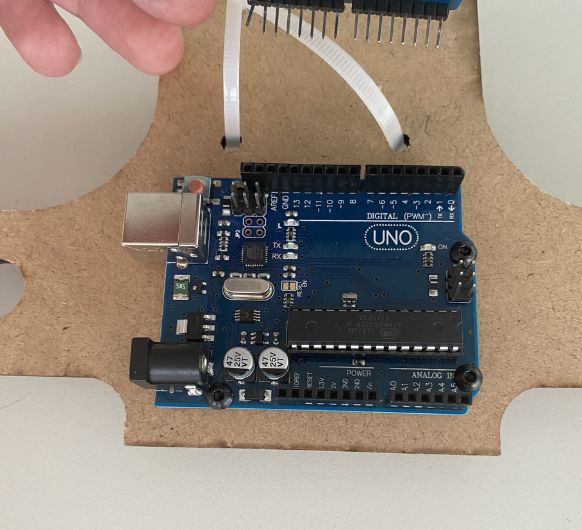
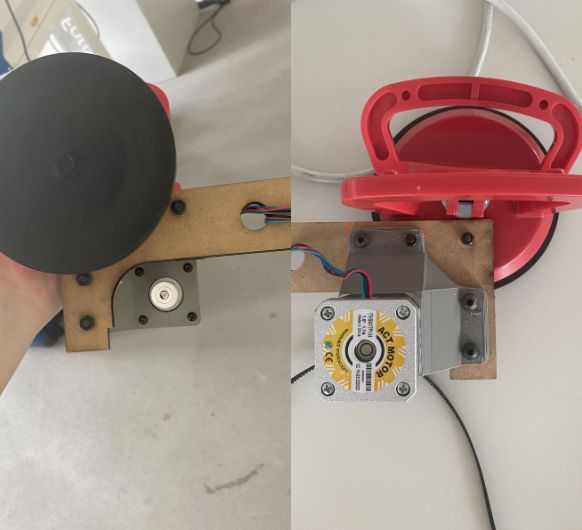
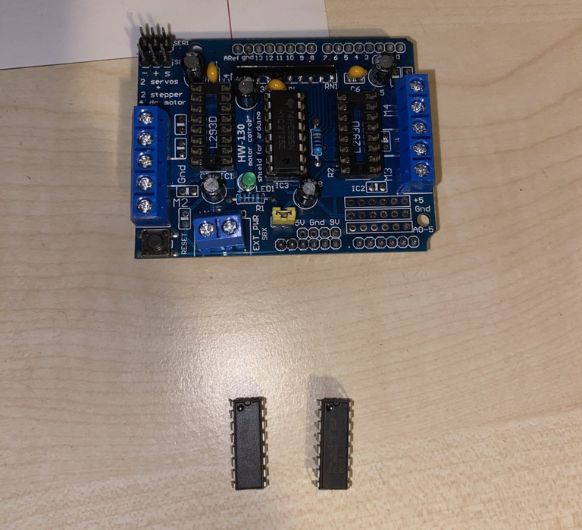
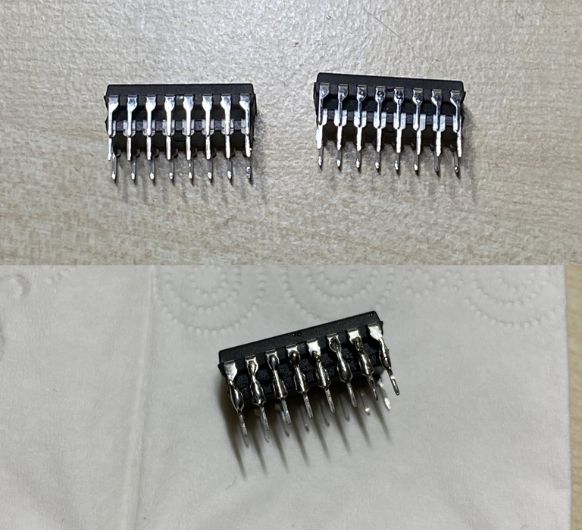
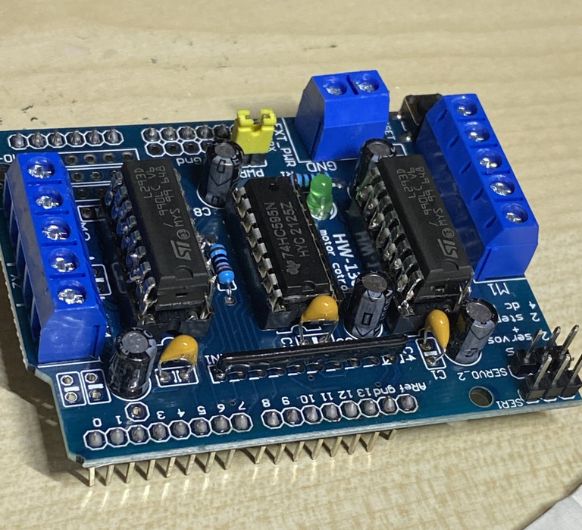
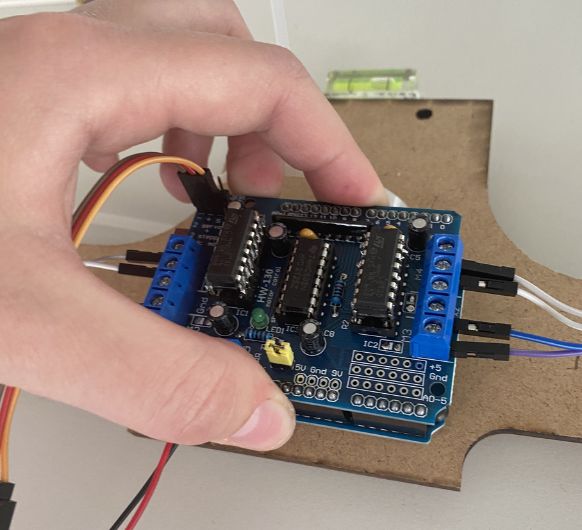
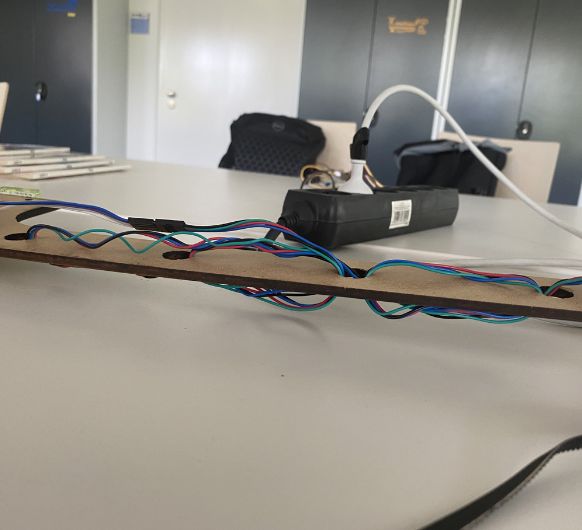
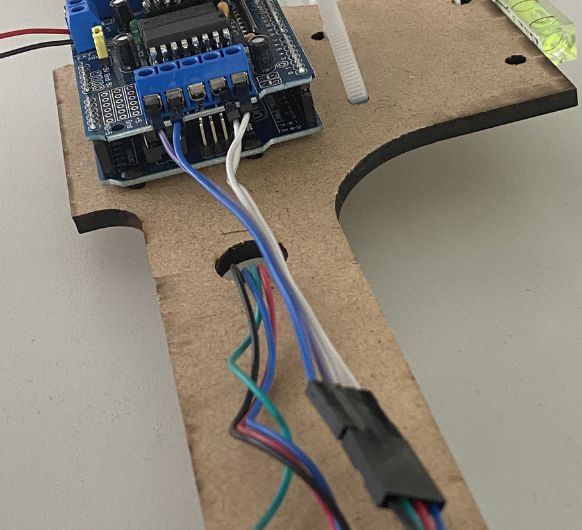
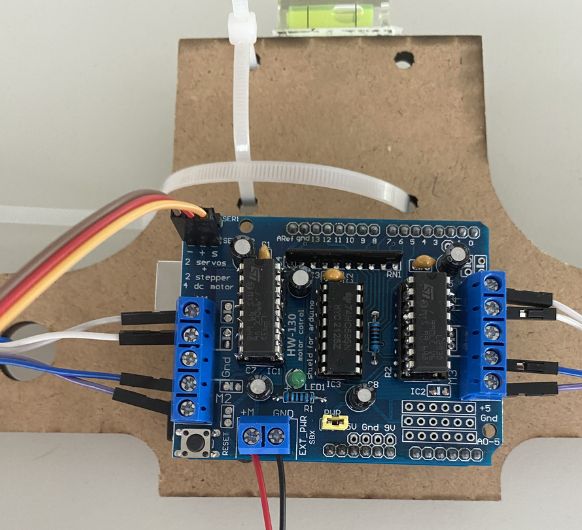
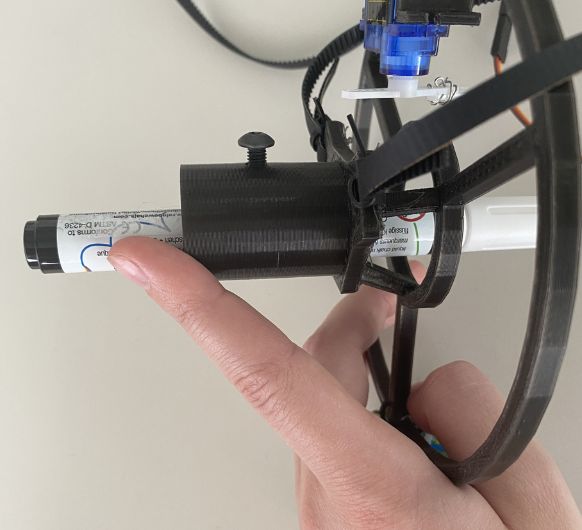
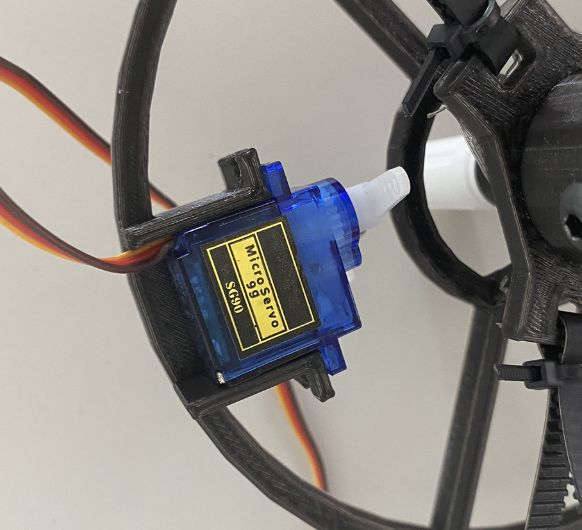
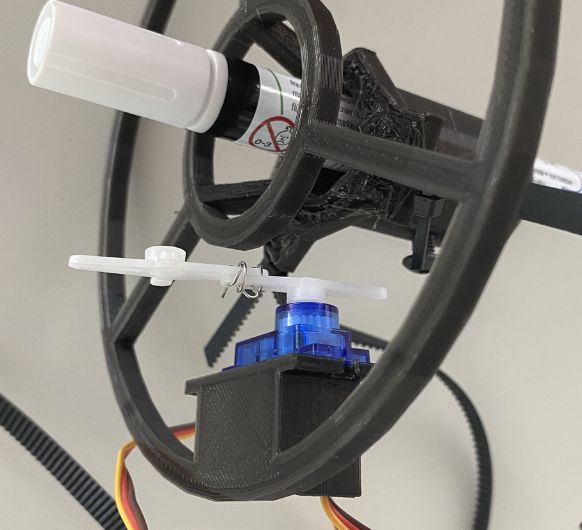
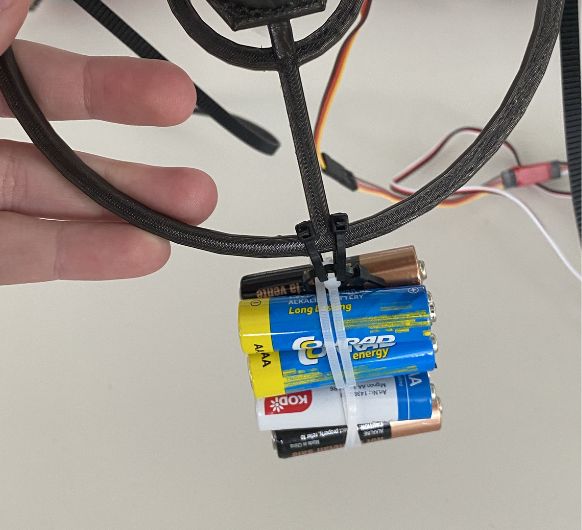
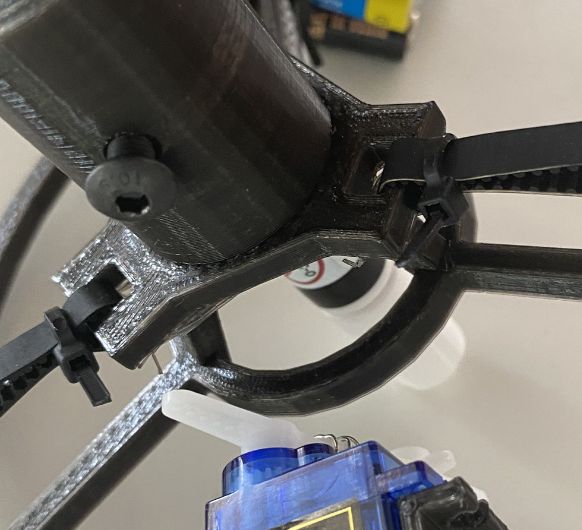
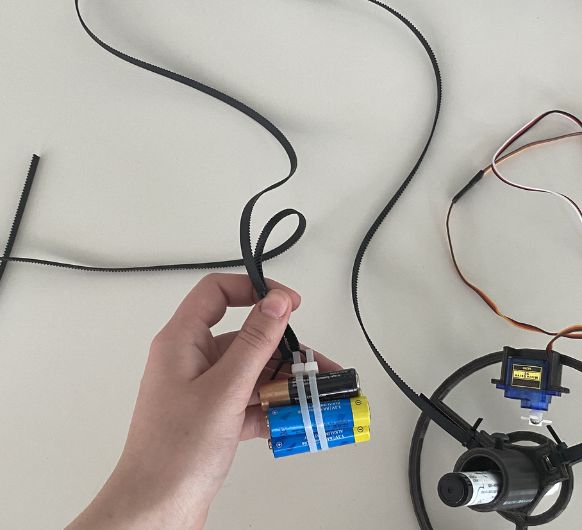
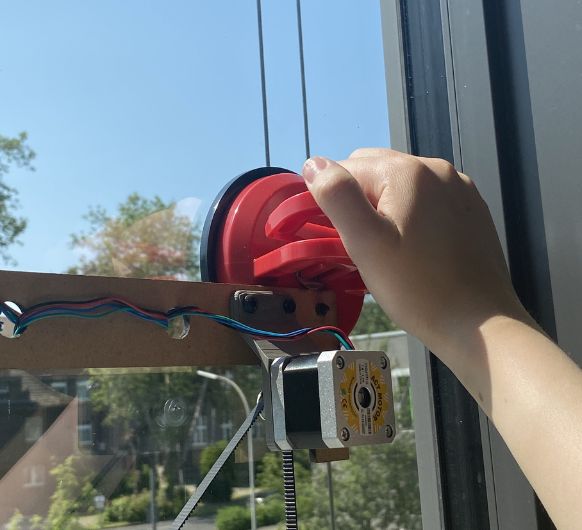
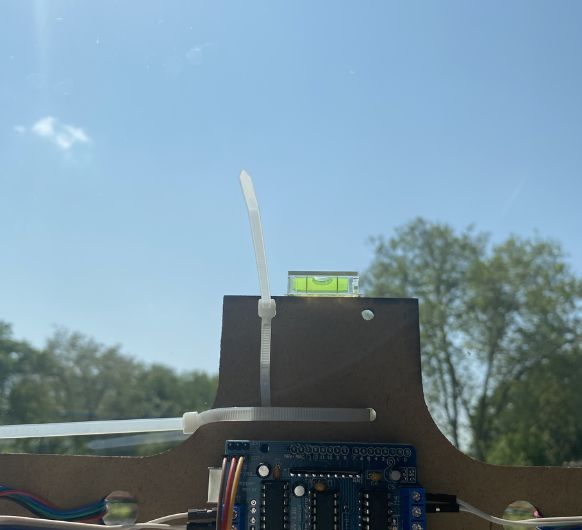
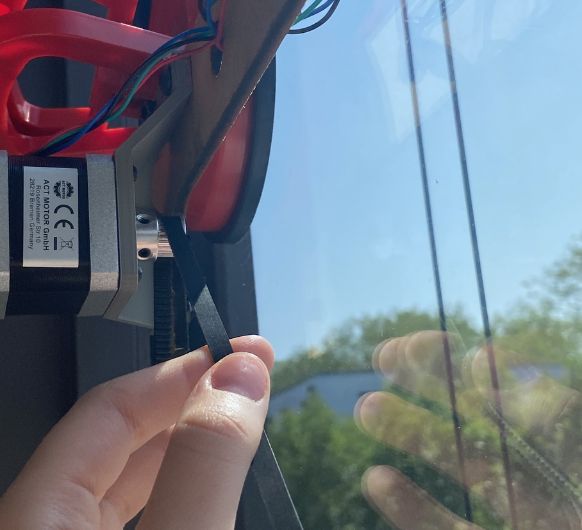
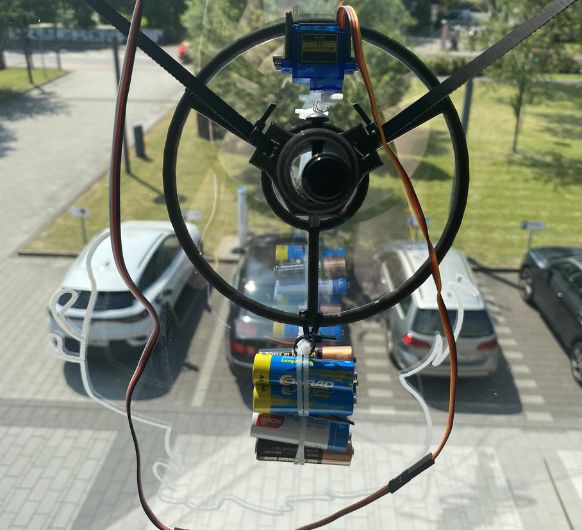
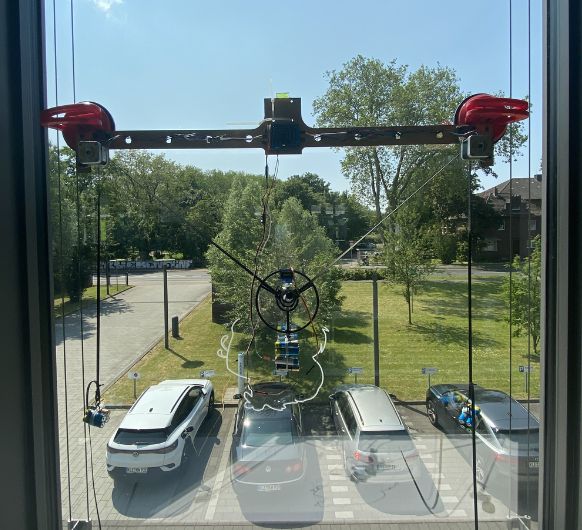
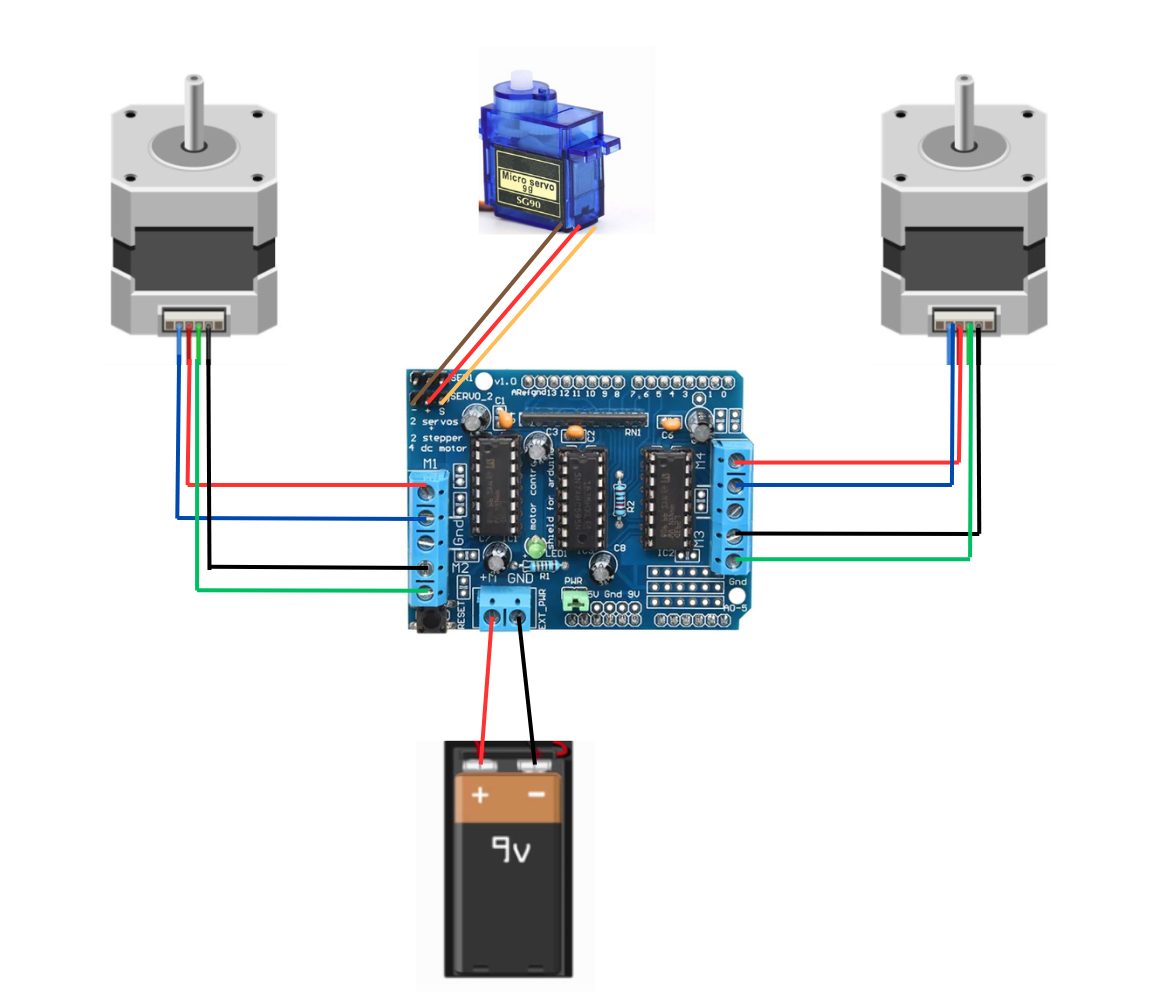
Programming
Please note that this section was carried out on Windows. Peculiarities of other operating systems will not be addressed.External sources used for this section: YouTube: Make Arduino XY Plotter Drawing Robot | Instructables: XY Plotter Drawing Robot | Arduino | Polargraph
Polargraph with Processing and Arduino UNO
Whats Polargraph?Polargraph is originally a particular brand of CNC plotter machines. It is often used in a generic way to describe any of these kinds of machine, but it's not the official name for machines like this.
Currently, the Polargraph brand/project is on hiatus, but it's source code is still available. The latest bundle (2017) is available on Github. It includes the polargraph-controller, which is a desktop application for controlling a polargraph machine, communicating using ASCII command language over a serial link. But we'll see what that means later.
To run the polargraph-controller, we need a certain version of Processing . Processing is a flexible software sketchbook and a language for learning how to code. (links and explanation down below) Links to the stuff you have to download: (The listed versions are important, polargraph-controller is likely to not work if you are using the wrong Processing version)
- Polargraph: Polargraph.2017-11-01
- Arduino IDE: Arduino 1.8.16 (this version works for me, other versions might also work | another version you can try if this doesn't work: Arduino 1.8.5 )
- Processing:
Processing
2.2.1
- You might need to install Java Development Kit 5.0u22 for Processing to run
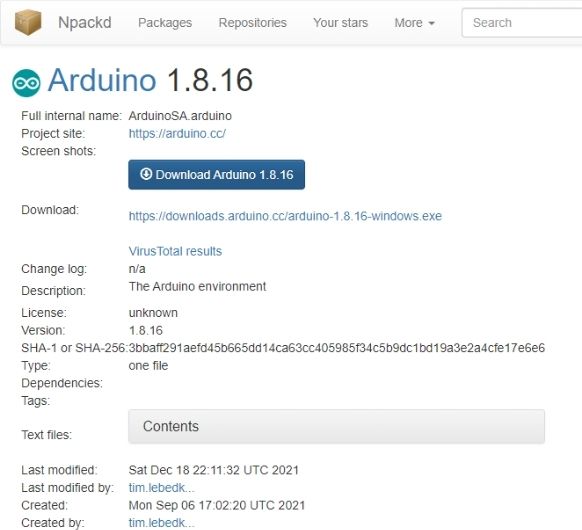
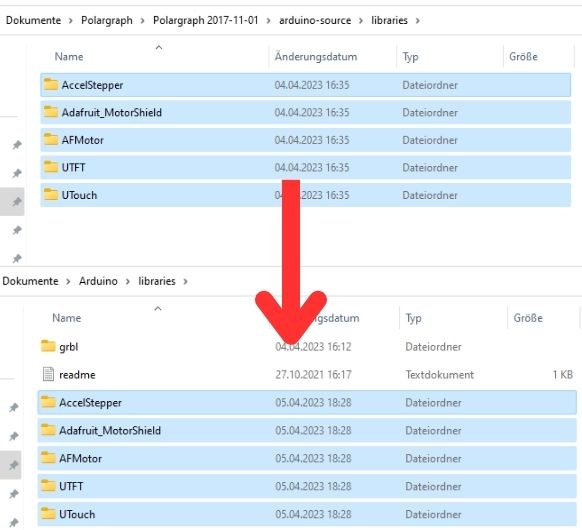
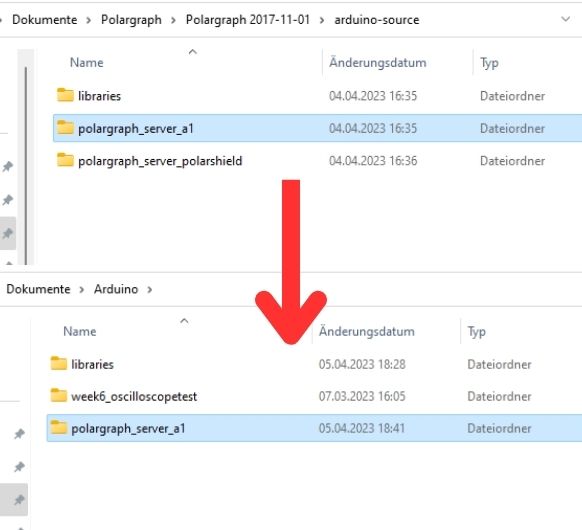
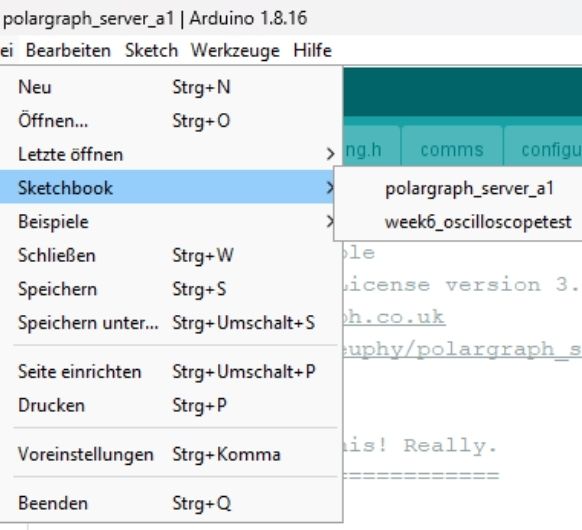
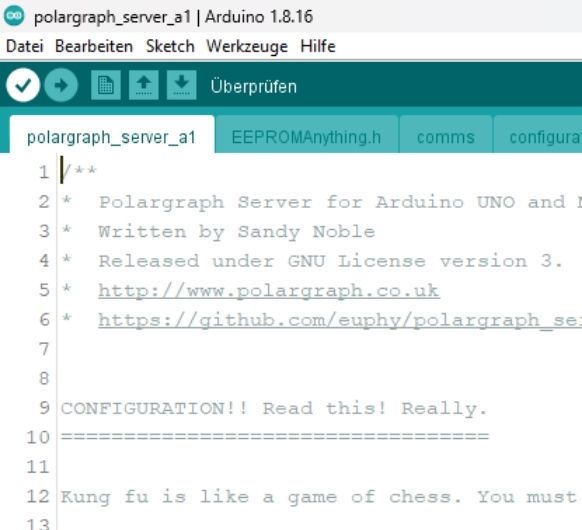
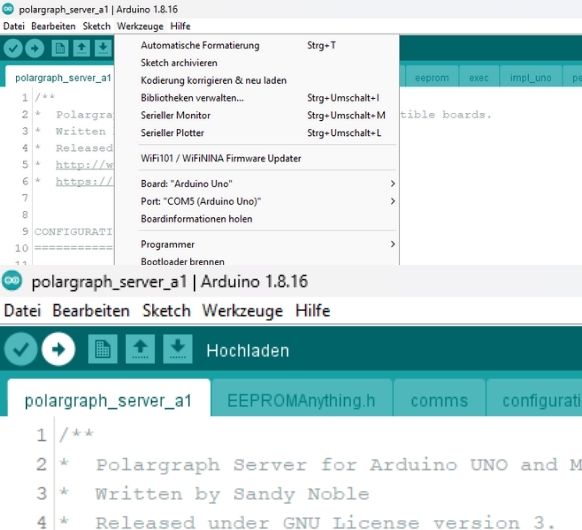
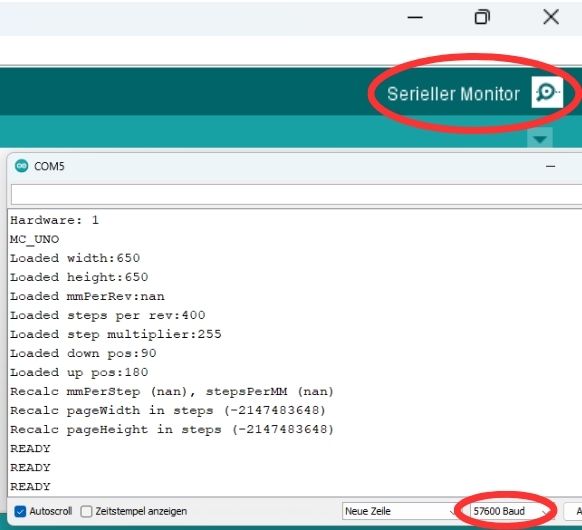
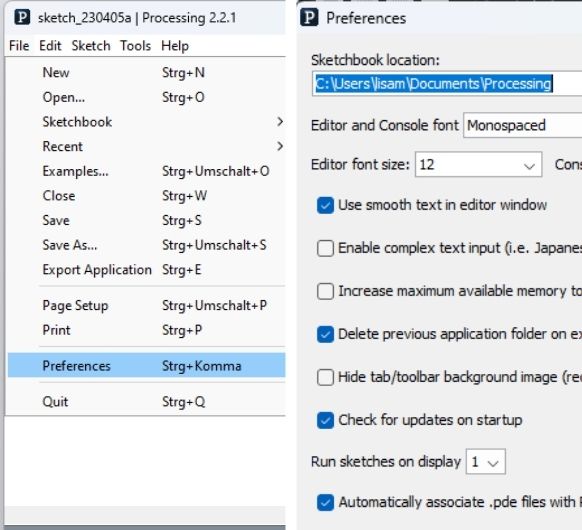
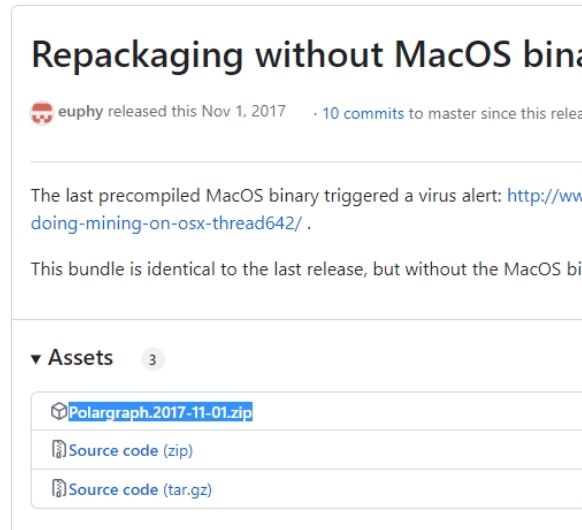
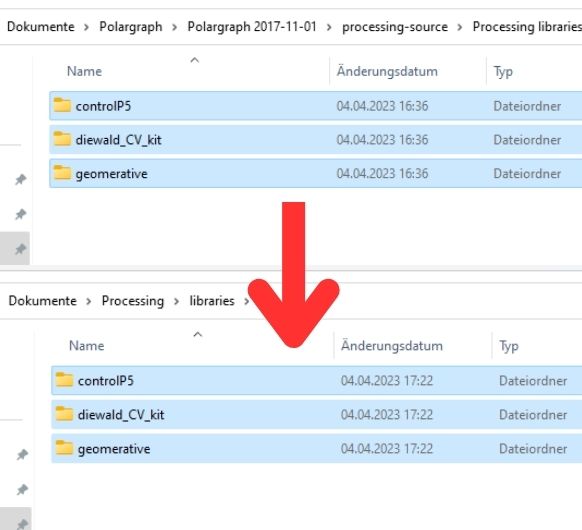
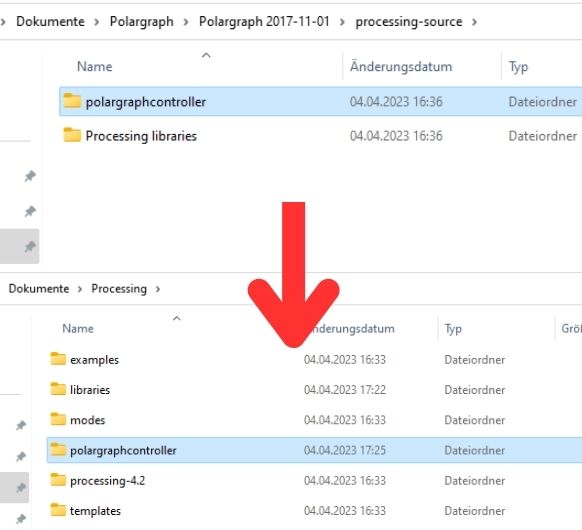
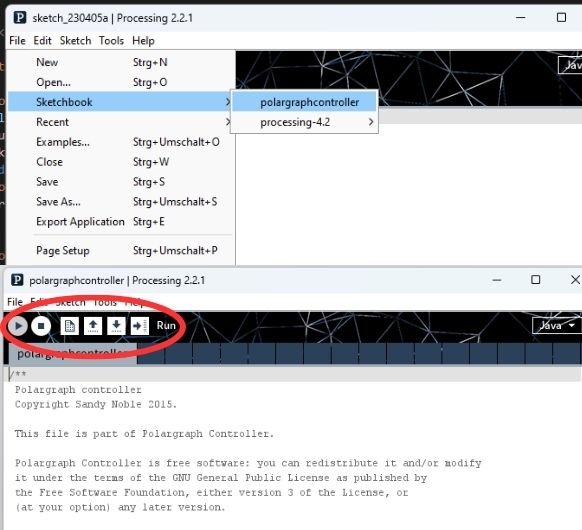
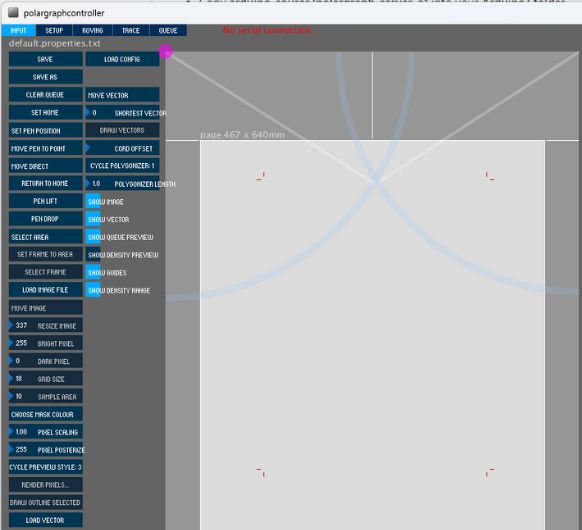
Machine dimensions
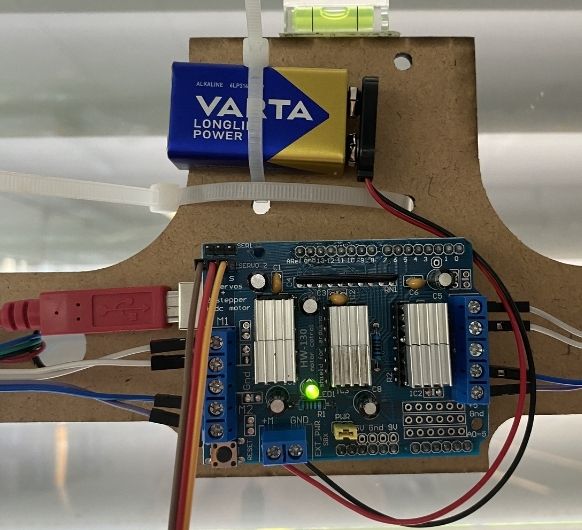
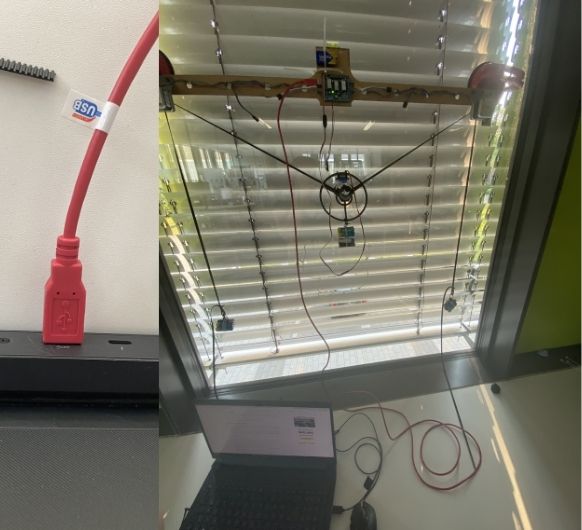
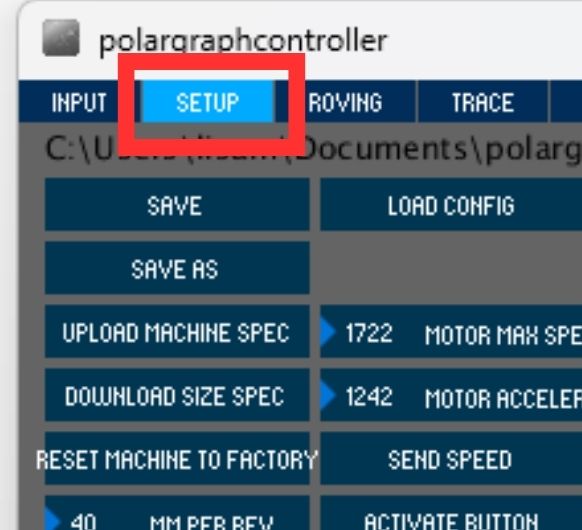
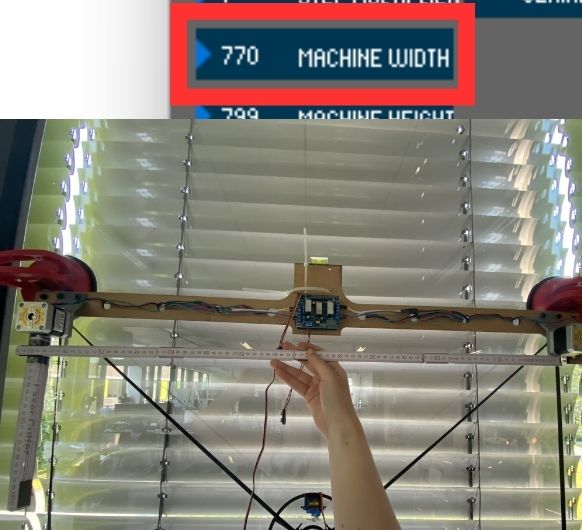
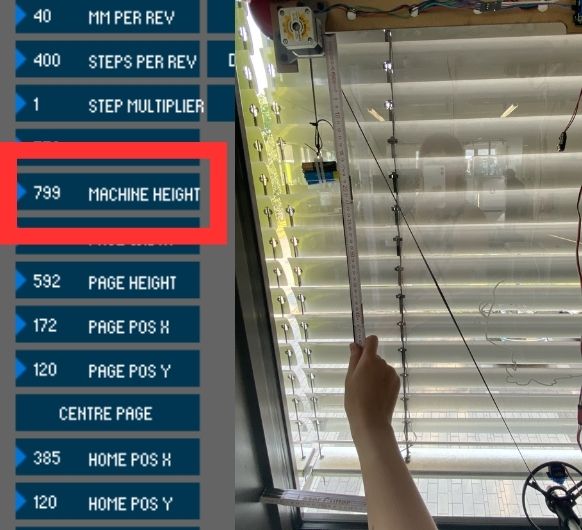
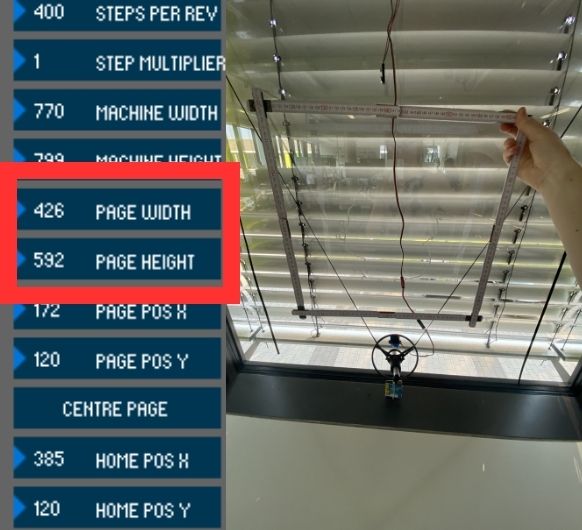
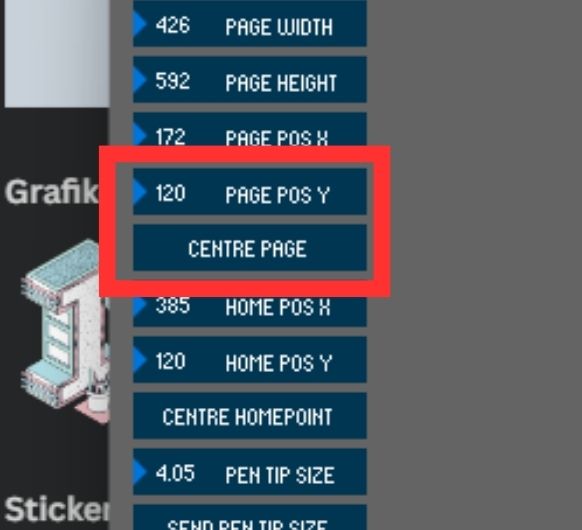
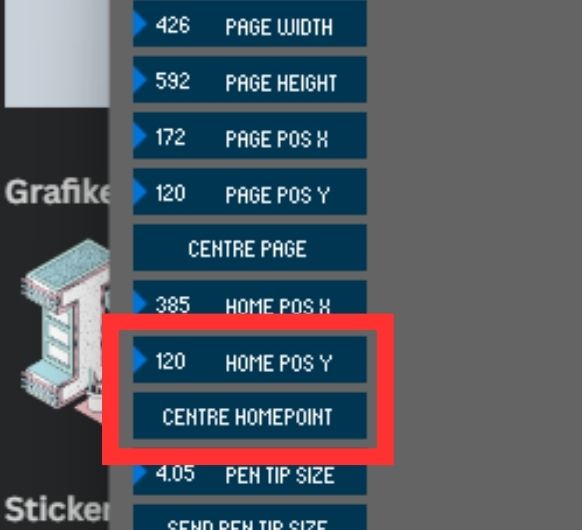
Stepper motor and pulley settings
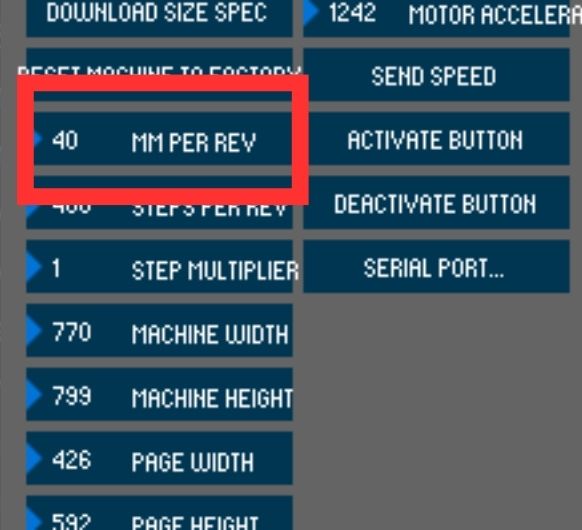
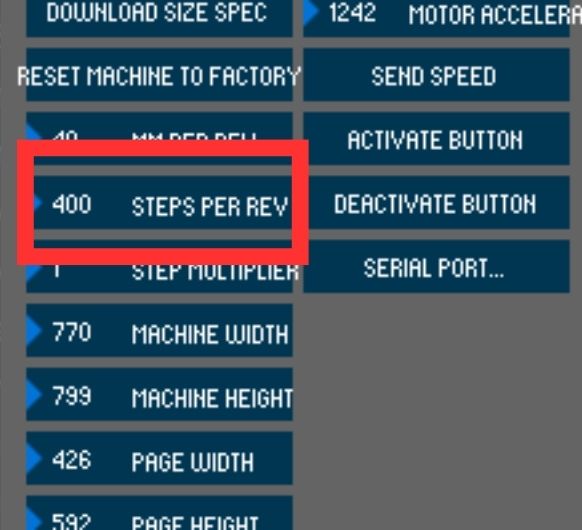
Servo settings
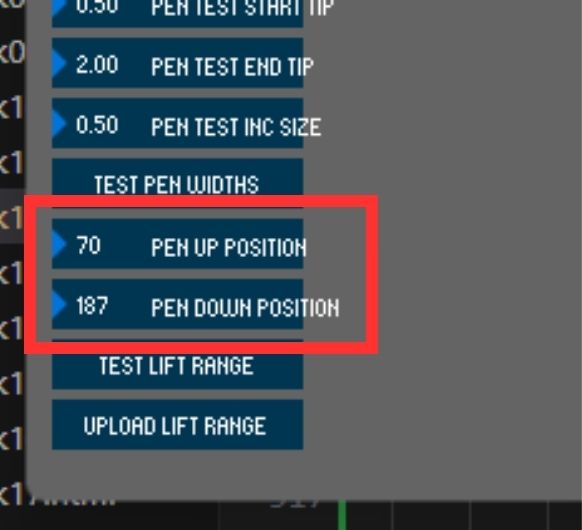
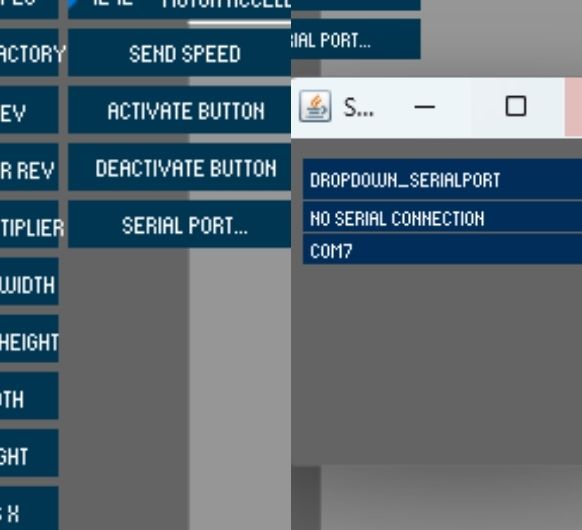
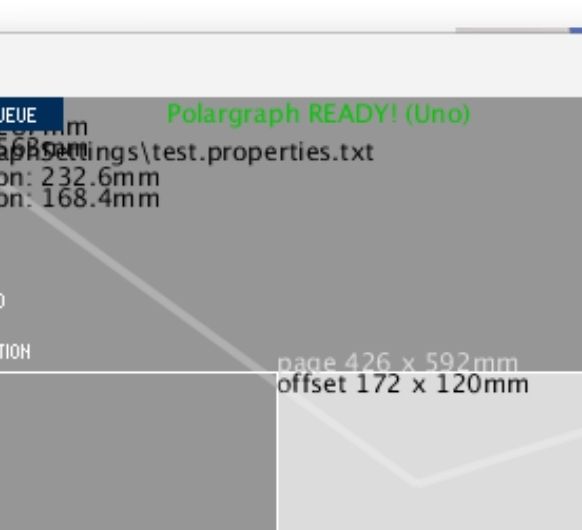
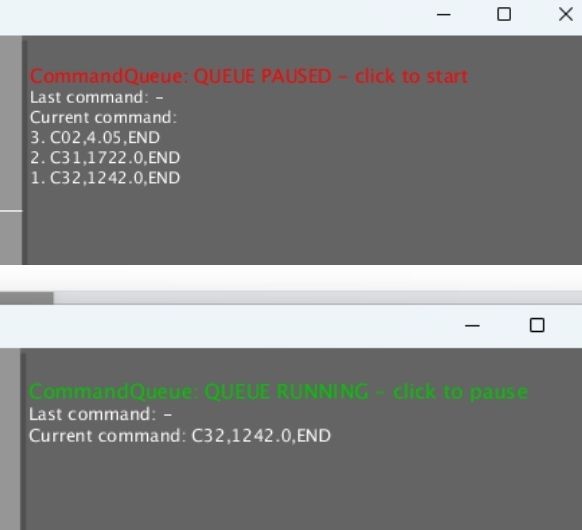
Save settings and home polargraph
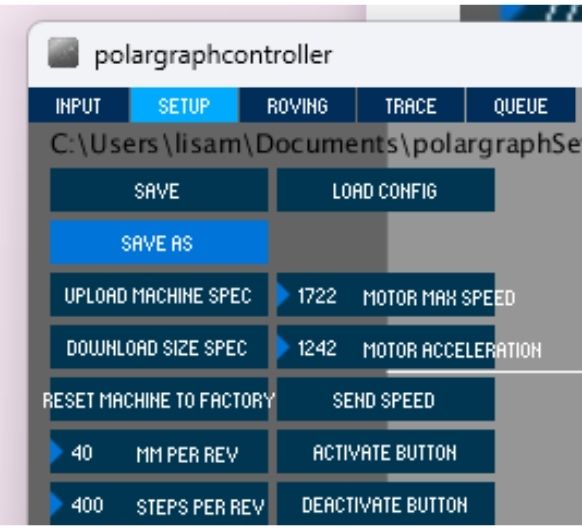
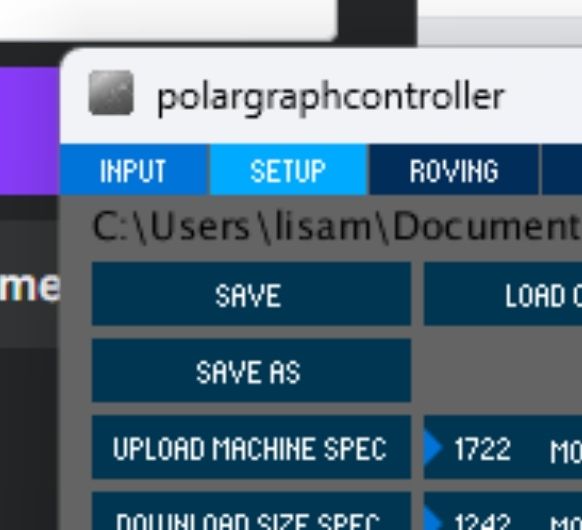
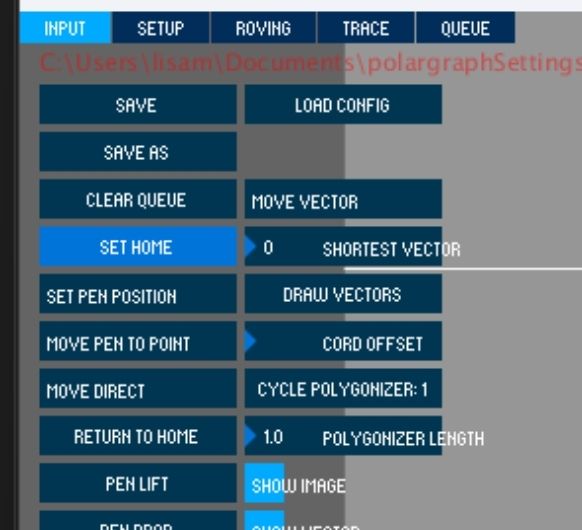
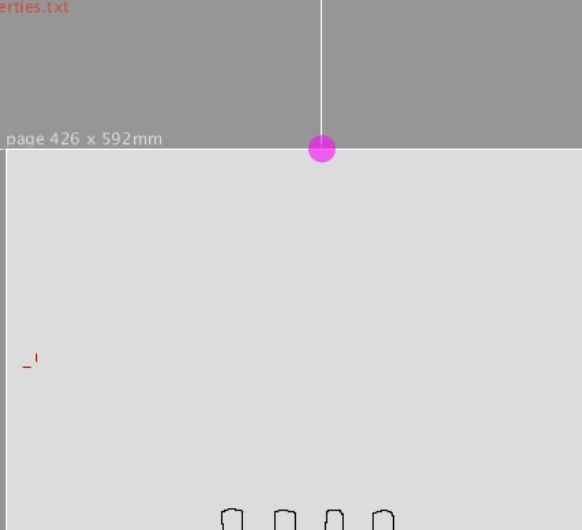
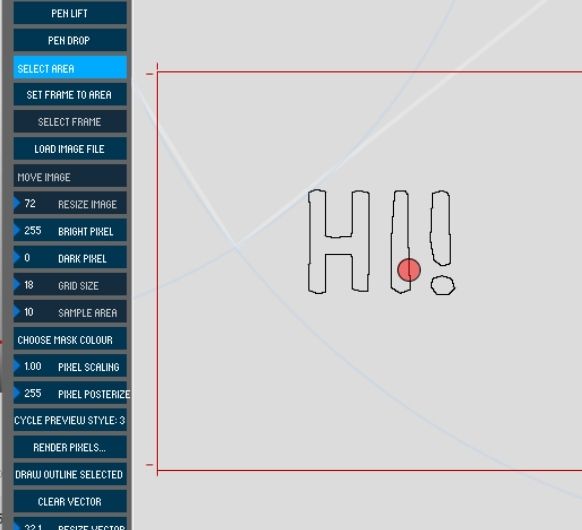
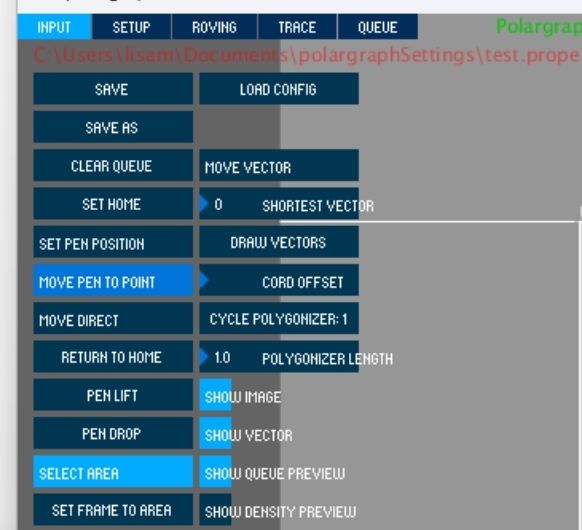
Upload an image
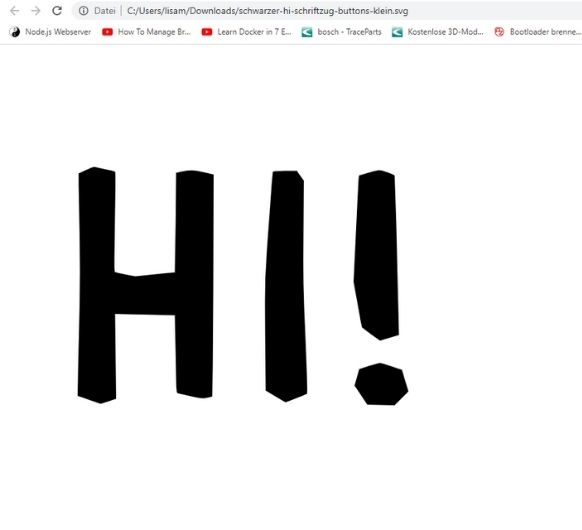
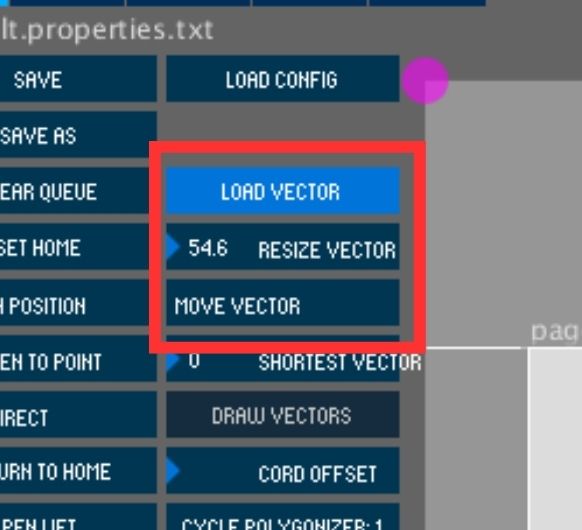
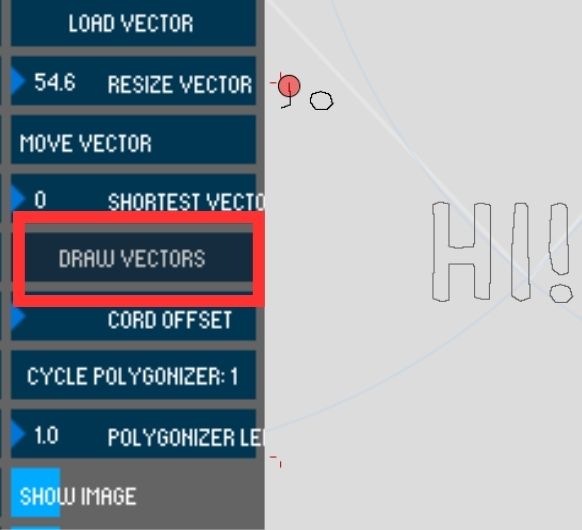
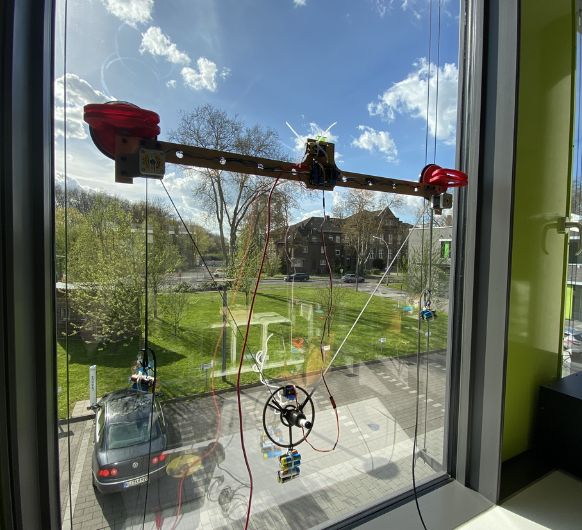
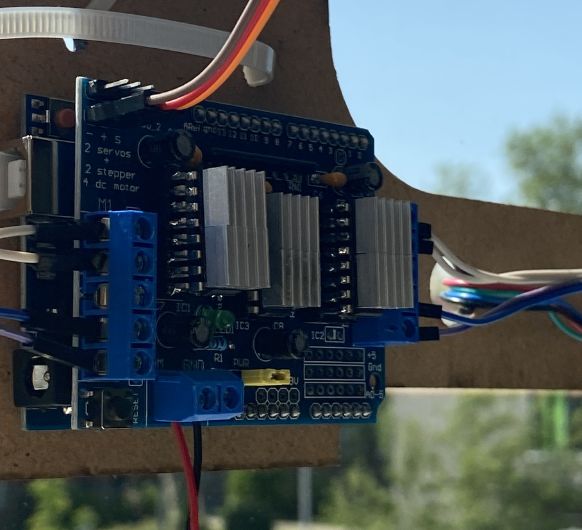