Molding and Casting
Design a mold around the stock and tooling that you'll be using,
mill it (rough cut + three-axis finish cut),
and use it to cast parts
Group assignment:
Group assignment
The molding and casting materials I used for this assignment summed up:
Smooth-On Ecoflex 00-30
Ecoflex 00-30 is a platinum-catalyzed silicone rubber that is soft, strong, and stretchy. It is
mixed 1A:1B by weight or volume and cures at room temperature (negligible shrinkage). It is
translucent and can be
pigmented for color effects. Ecoflex is suitable for making prosthetic appliances, orthotic
cushioning, and special effects applications. It is also certified as skin safe.
Here's a summary of the main points for using Ecoflex 00-30 silicone rubber :
- Use in a properly ventilated area and wear safety gear.
- Cure inhibition may occur with certain contaminants, so test compatibility with a small-scale application.
- Applying a clear acrylic lacquer or release agent can help prevent inhibition and make demolding easier.
- Mix Part B thoroughly before starting. Combine Parts A and B in a mixing container at a 1A:1B ratio by weight or volume. Mix for 3 minutes, scraping the sides and bottom of the container.
- Vacuum degassing is recommended to remove air bubbles. Use a vacuum pump that can pull at least 1 Bar / 100 KPa and leave space for material expansion. Continue vacuuming until the material rises, breaks, and falls. Vacuum for 1 additional minute after the material falls.
- Pour the mixture in a single spot at the lowest point of the containment field and let it seek its level over the model.
- Cure at room temperature (23°C, never less than 18°C) and post cure for attaining maximum performance properties quicker (After curing at room temperature, expose the rubber to 80°C for 2 hours and 100°C for one hour).
- If using as a mold, no release agent is necessary when casting wax or gypsum, but a release agent is recommended when casting polyurethane, polyester, and epoxy resins.
- THI-VEX can be used to thicken Ecoflex for vertical surface application, and Silicone Thinner can be used to lower the viscosity for easier pouring.
- Clean and dry the mold before storing it on a leveled surface in a cool, dry environment.
NEUKADUR ProtoCast 105
Main characteristics
- Very good flowability
- Very impact resistant
- Very good colorability
- High heat resistance
- Cures to white color
- Only suitable for vacuum casting
Component | Color | Mixing Ratio by Weight | Density (20°C) g/cm³ | Viscosity (25°C) mPa∙s |
---|---|---|---|---|
NEUKADUR ProtoCast 105 Component A | Slightly yellowish | 100 | 1.05 | 650 |
NEUKADUR ProtoCast 105 Component B | Slightly yellowish | 200 | 1.16 | 160 |
Mixture Properties (approximate values) | PC 105 A / PC 105 B |
---|---|
Mixing Viscosity (25°C) mPa∙s | 325 |
Density (20°C) g/cm³ DIN 53479 | 1.13 |
Processing Time (25°C) Minutes | 5 |
Demolding Time (70°C) Minutes | 60 |
Hardness Shore D DIN 53505 after storage 2 Hours at 70°C | 82 |
Cured Color | White |
Recommended Layer Thickness mm | 5 |
Processing Instructions:
NEUKADUR ProtoCast 105 Component A must be thoroughly homogenized prior to processing. The
containers must be carefully sealed after each use. After 30-60 minutes, the cured material has
not
yet achieved its full impact resistance (which is achieved only after approximately 1-2 hours at
70°C), so cautious demolding, especially for thin parts, is recommended. It's recommend pouring
NEUKADUR ProtoCast 105 Component A/B into preheated molds at 70°C (e.g., made of ProtoSil RTV
245)
and tempering for at least 1 hour at 70°C before demolding. Recommended casting thickness: up to
a
maximum of 5mm.
It's recommended evacuating NEUKADUR ProtoCast 105 Component A for 15 minutes at the highest
possible vacuum, then relaxing to 20-25 mbar before adding NEUKADUR ProtoCast 105 Component B.
If the vacuum drops below 20 mbar, severe foaming may occur when both components are mixed.
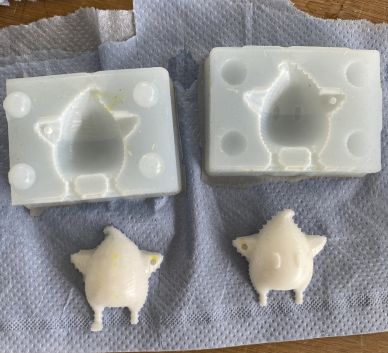
ProtoSil RTV 245
Main features
- Shore hardness A 40
- very good flow properties, translucent
- shrinkage-free vulcanization at room temperature
- can be made thixotropic
- high resistance to initial tearing and tear propagation
Properties in the non-crosslinked state | ProtoSil RTV 245 Comp. A | ProtoSil RTV 245 Comp. B 1 (dry surface) |
ProtoSil RTV 245 Comp. B 2 (oily surface) |
NEUKASIL Thixotropic Agent SN 200 |
---|---|---|---|---|
Colour | colourless | colourless | colourless | colourless |
Mixing ratio p.b.w. | 100 | 10 | 10 | 0.1 – 0.3 |
Density 20 °C (approx.) g/cm3 | 1.1 | 0.95 | 0.96 | 0.98 |
Viscosity 20 °C (approx.) mPa·s | 60,000 | 320 | 400 | 1,000 |
Properties of the mixture (approx. values) | Mixture A/B |
---|---|
Mixed viscosity | 35,000 mPa·s |
Pot life (1000 g) | 80 minutes |
Demouldable after | 12 hours |
Shore A hardness points | DIN 53505 40 |
Service temperature | 200 °C |
Minimize air incorporation during stirring. To achieve a bubble-free vulcanized material, evacuate the crosslinker-containing formulation prior to processing. Expect the mixture to expand 3-4 times its original volume and form bubbles during vacuum creation. Processing is complete once the bubbles have collapsed and the mixture returns to its original volume. Pour the prepared material over the object to be cast with care.
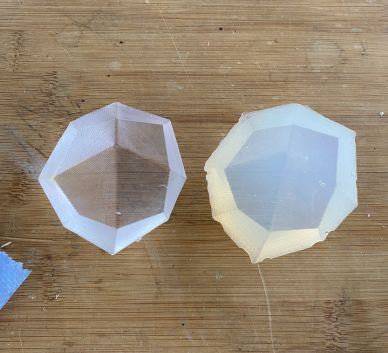
- Evacuate component A for 15 minutes at maximum vacuum and then relax to 20-25 mbar before dosing component B.
- Mix NEUKADUR ProtoCast 105 components A and B together at the recommended ratio (2:1 by weight).
- Make sure that the mixing is done as thoroughly as possible.
- After casting, allow the material to cure at 70°C for at least 1 hour before demolding.
- For thin sections, use caution during demolding, as the material may not have achieved its full toughness yet.
- Recommended casting thickness is up to 10cm.
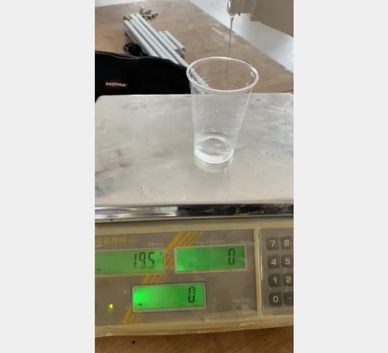
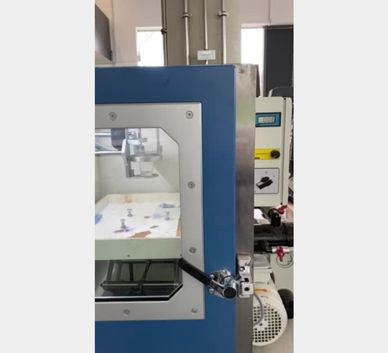
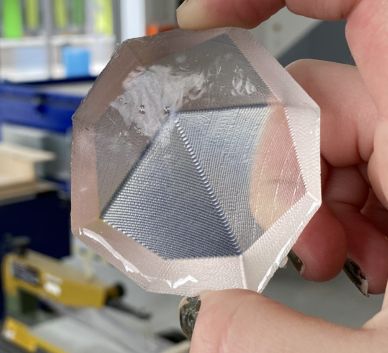
Operating the vacuum chamber
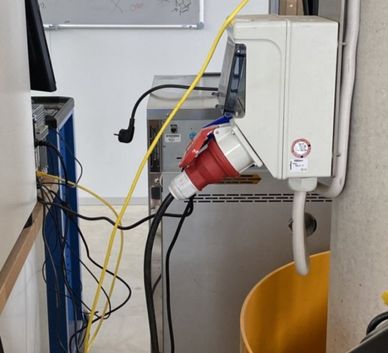
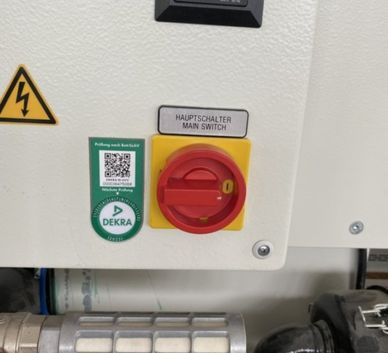
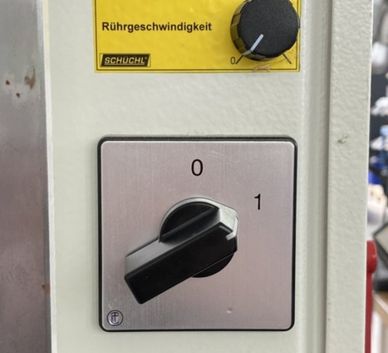
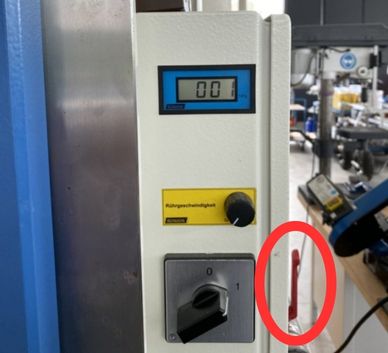
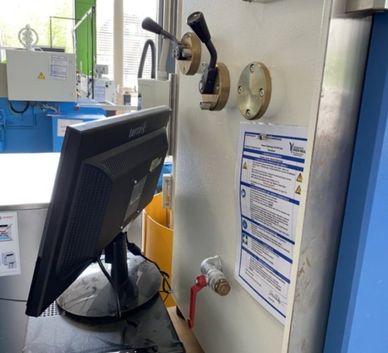
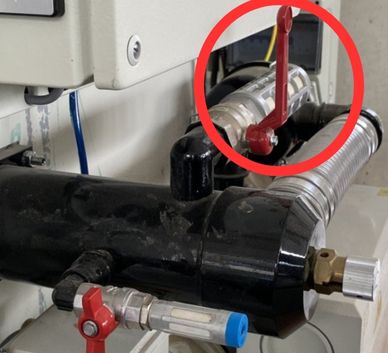
Designing a mold in Fusion360
Download my Fusion project file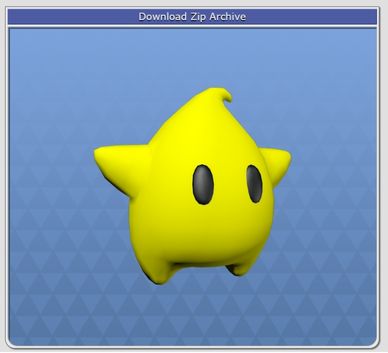
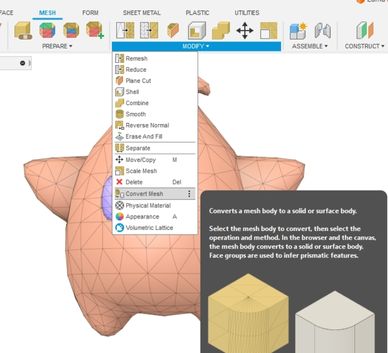
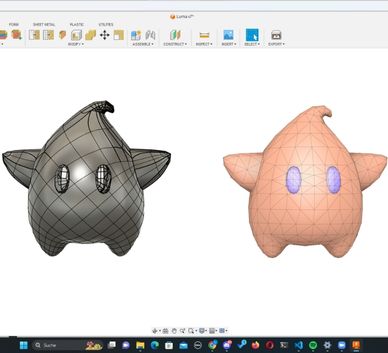
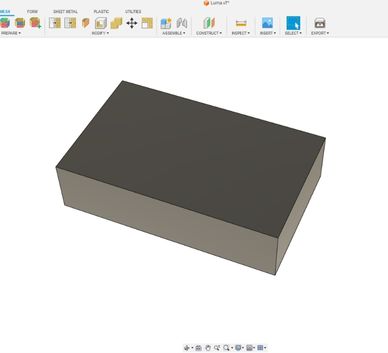
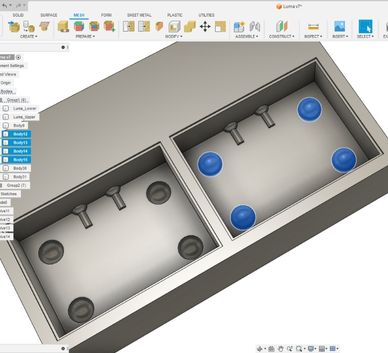
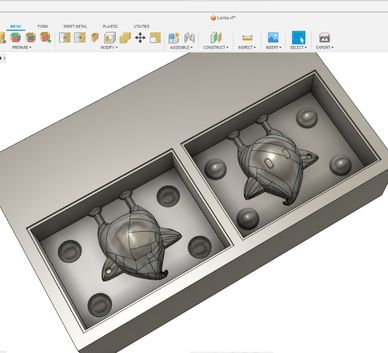
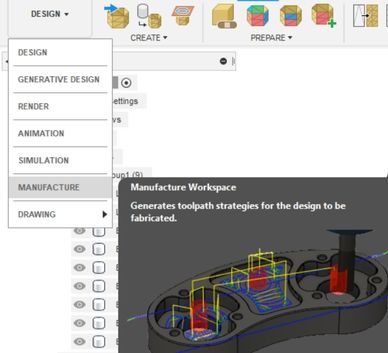
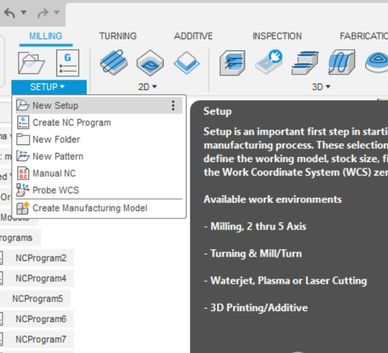
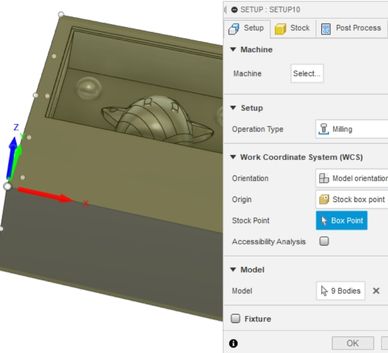
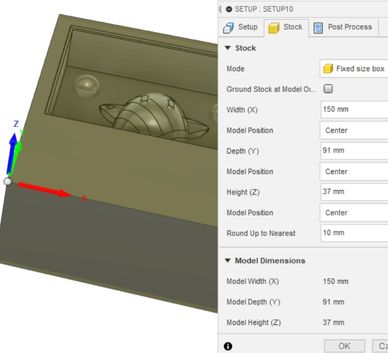
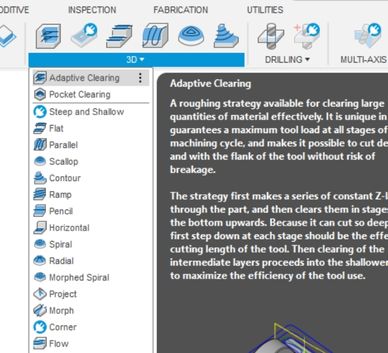
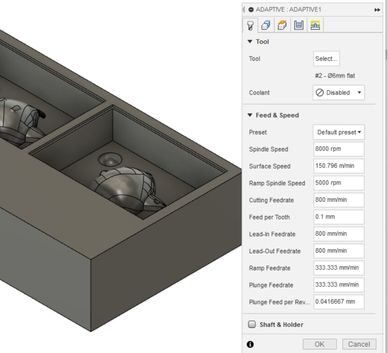
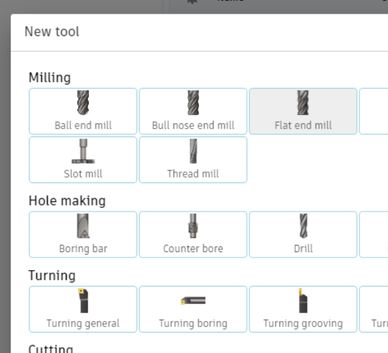
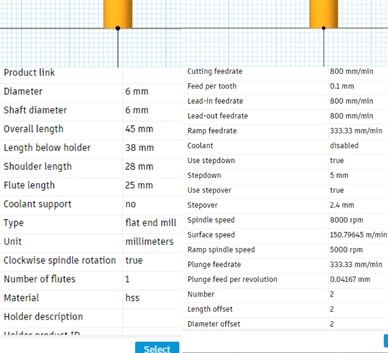
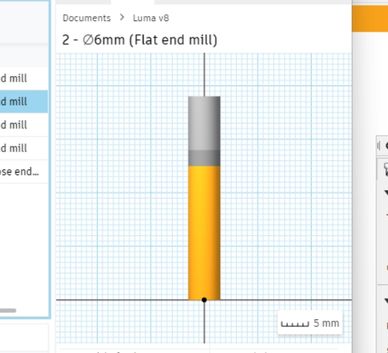
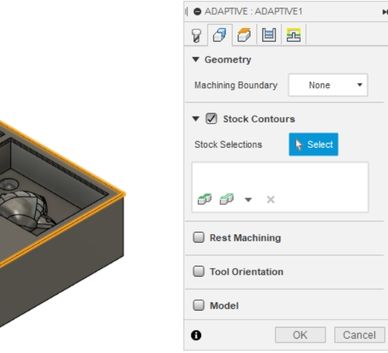

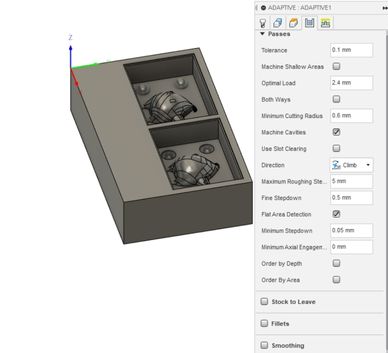
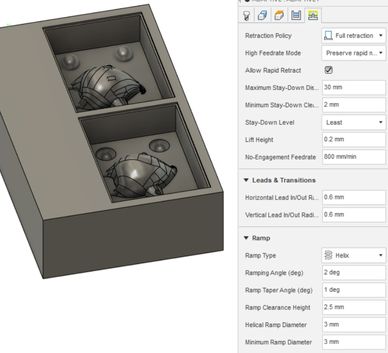
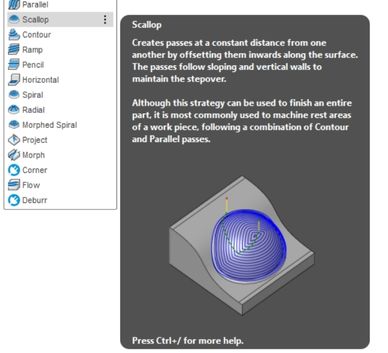
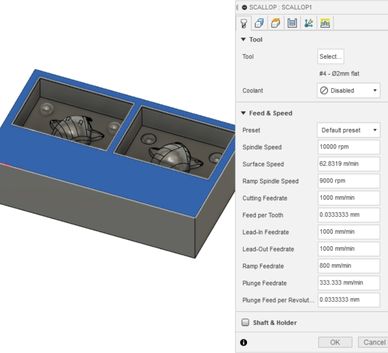
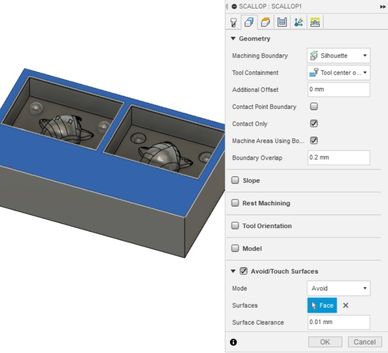
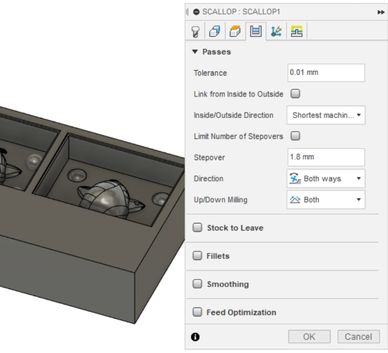
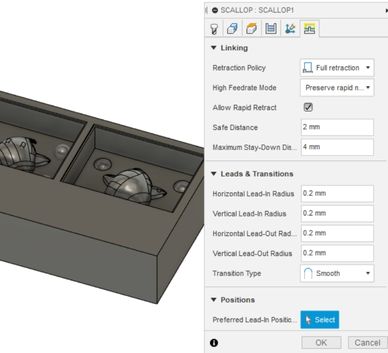
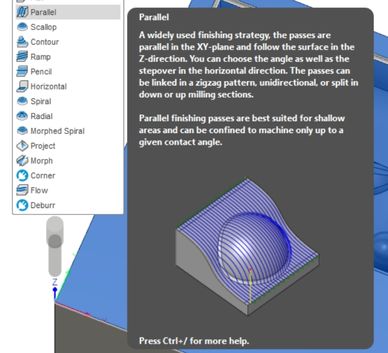
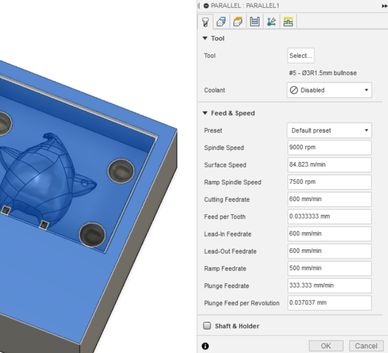
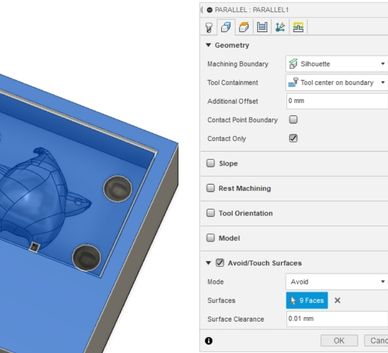

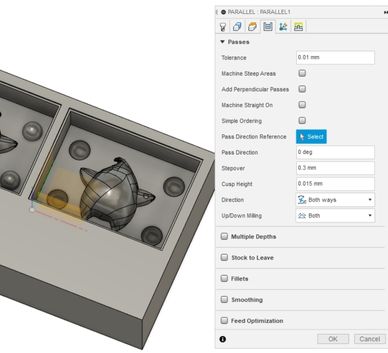
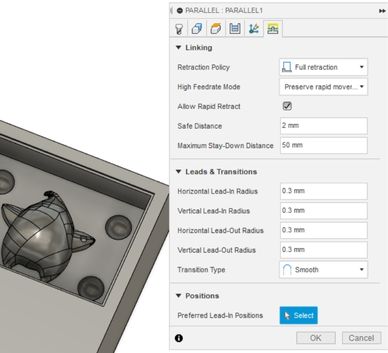
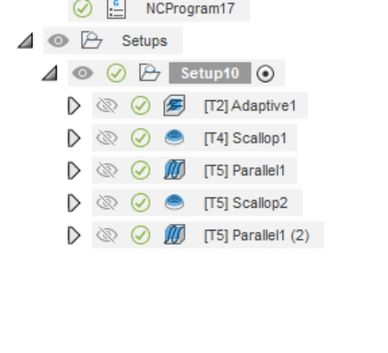
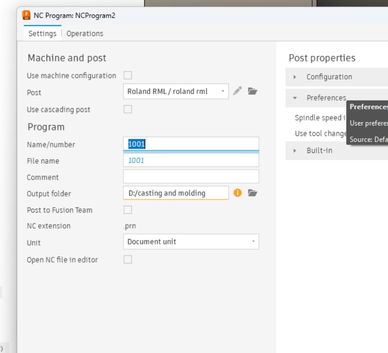
3D Milling
I used 3 different end mills during the whole process. 6mm flat end mill, 2mm flat end mill and 3mm bull nose end mill. Wax block is 15 cm x 9,1 cm x 3,7 cm (LxBxH)
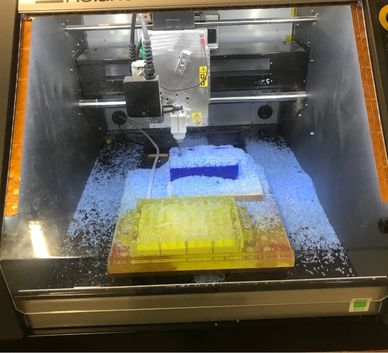
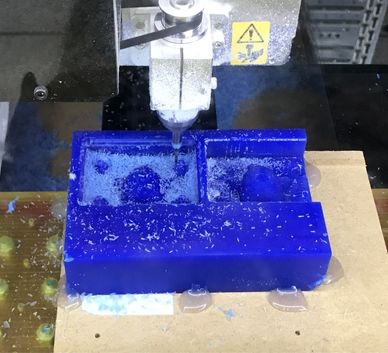
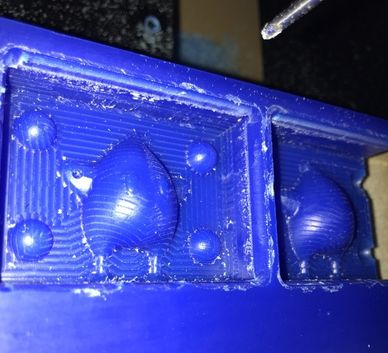
Molding and casting
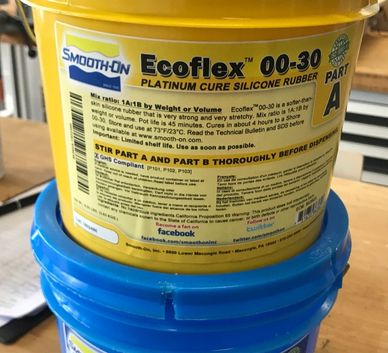
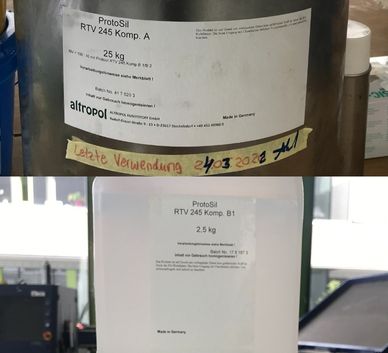
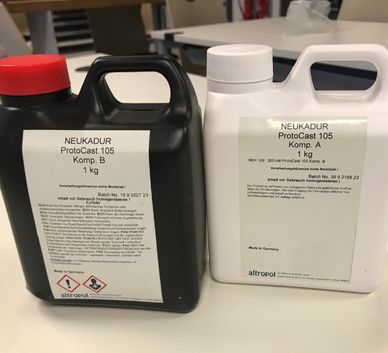
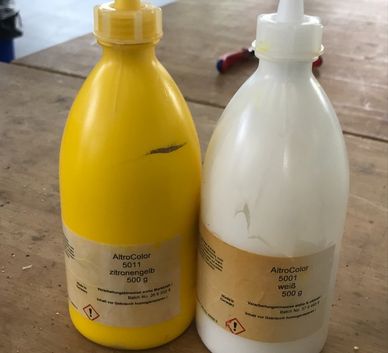
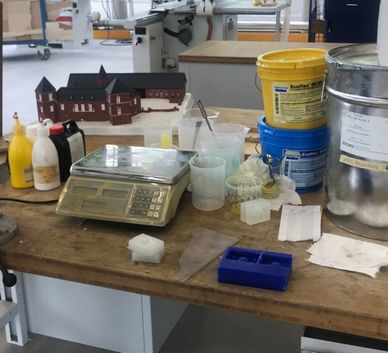
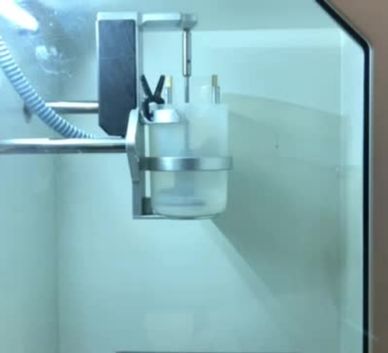
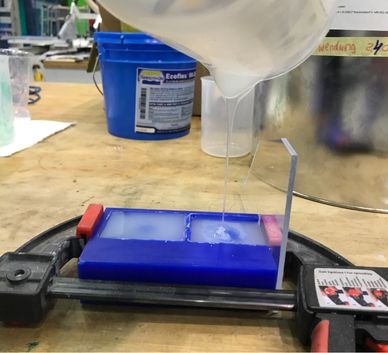
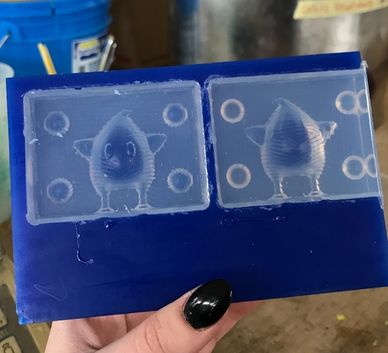
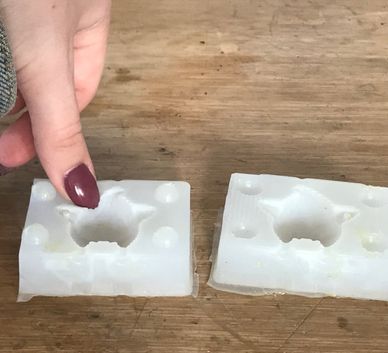
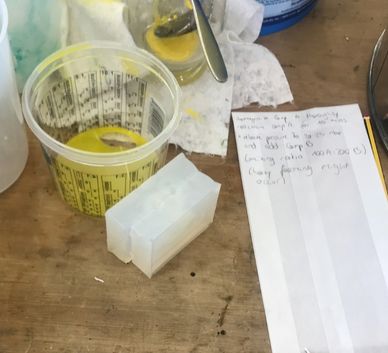
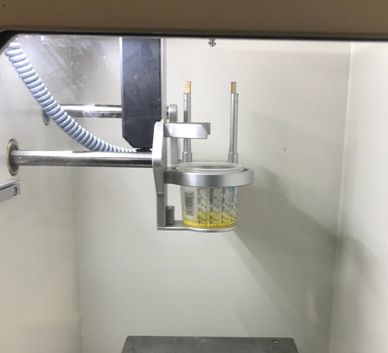
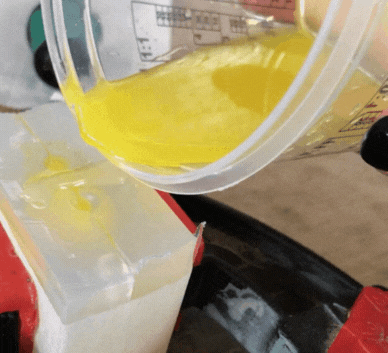
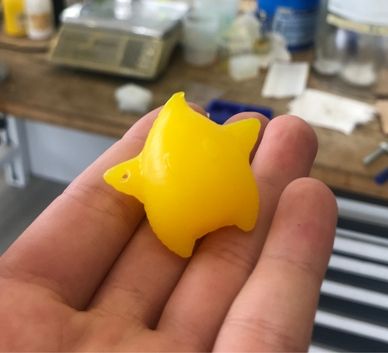