Computer Controlled Machining
Make (design+mill+assemble) something big.
Group assignment:
Group Assignment
Choosing and measuring the material
I choose MDF 12mm for the assignment.

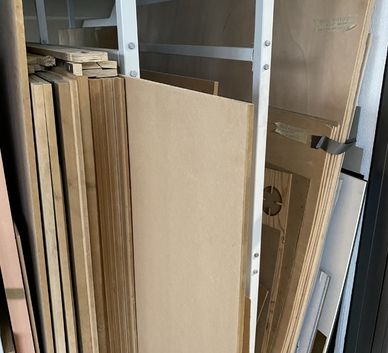
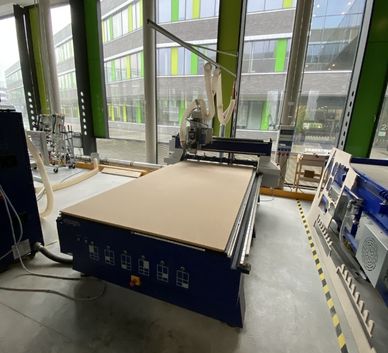
CAD and CAM in Fusion
Creating the test files in Fusion and preparing the toolpath:
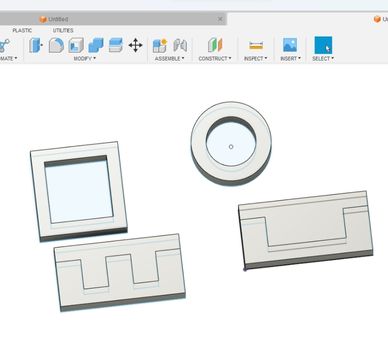
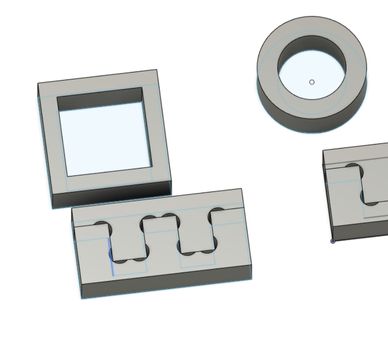
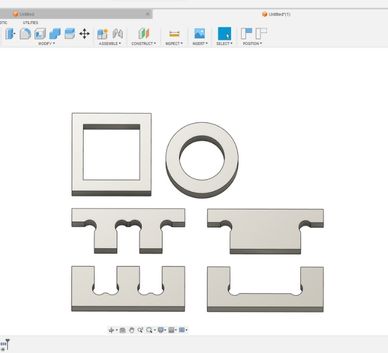
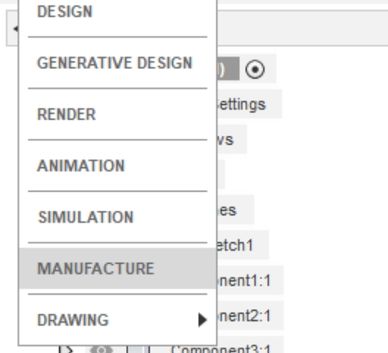
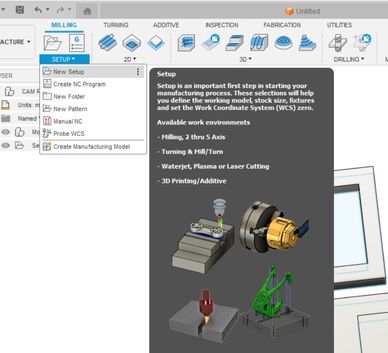
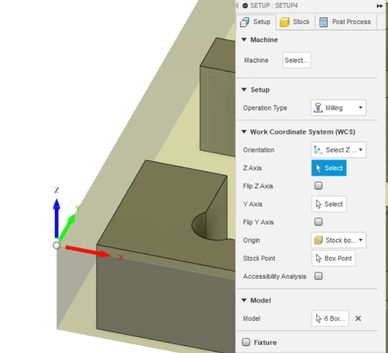
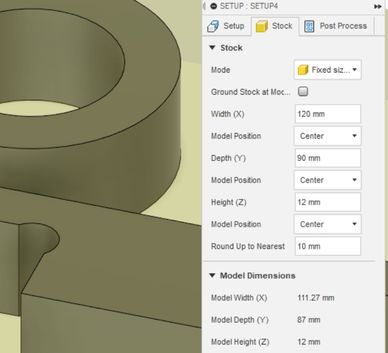
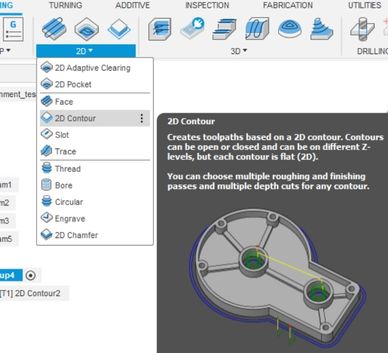
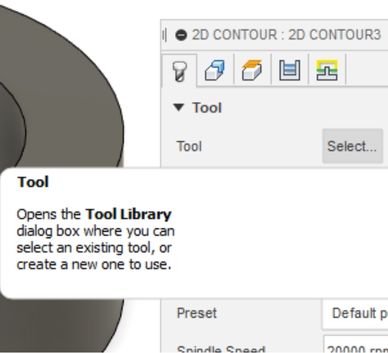
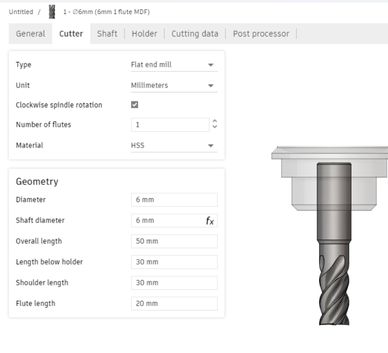
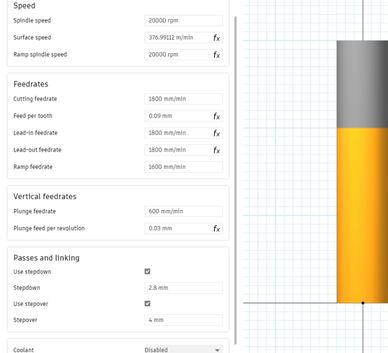
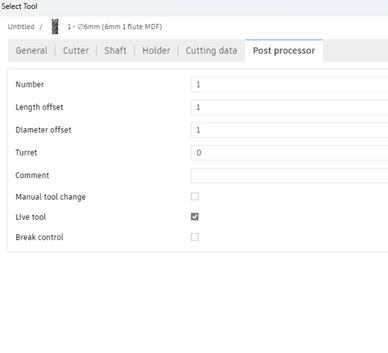
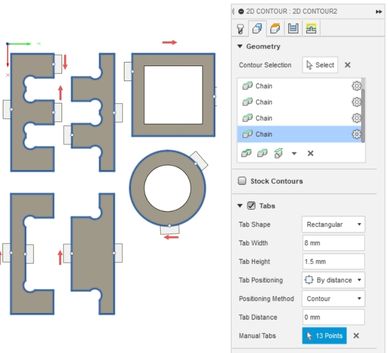
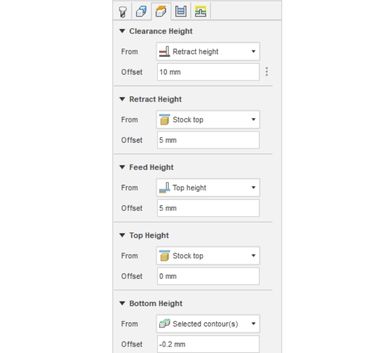
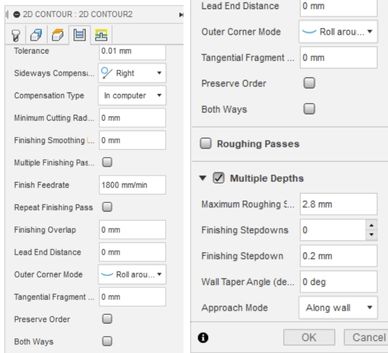
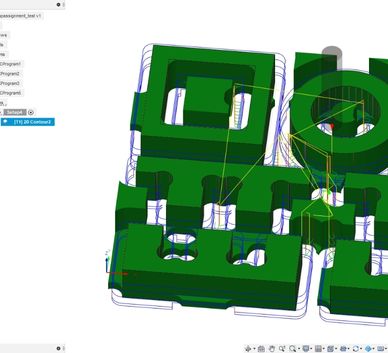
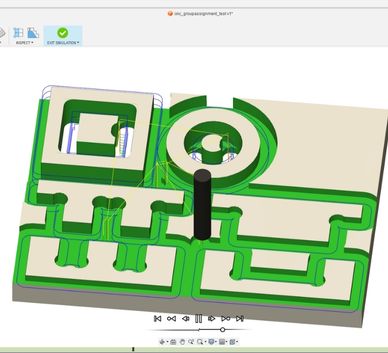
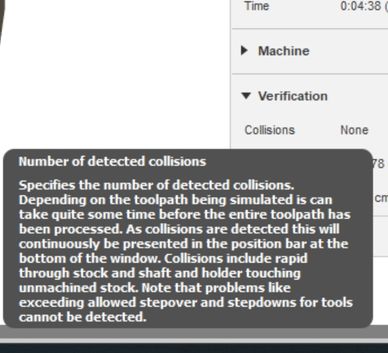
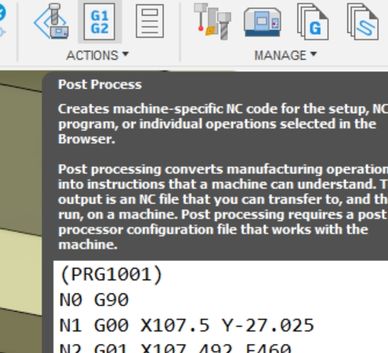
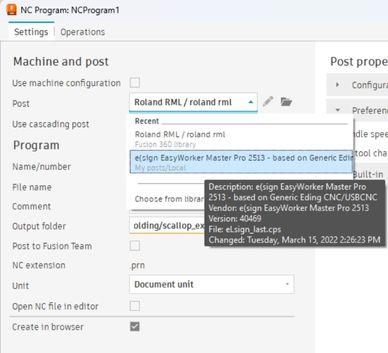
Test results
Now that the models
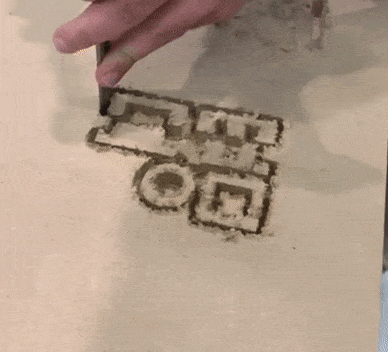
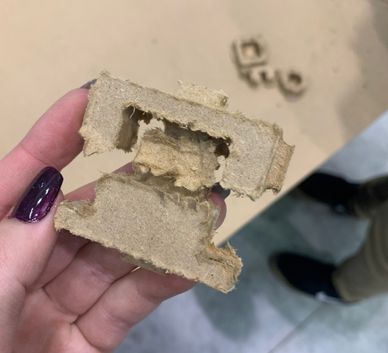
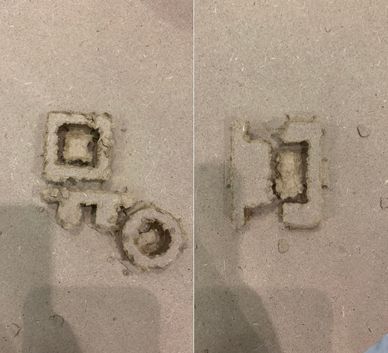
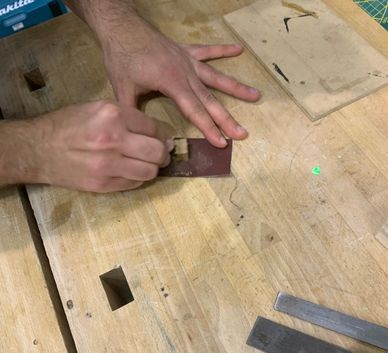
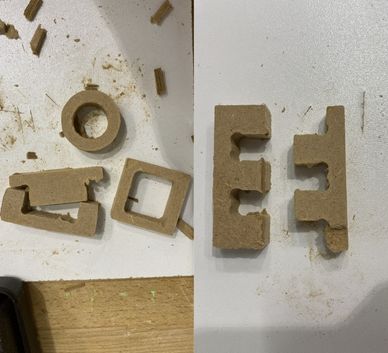
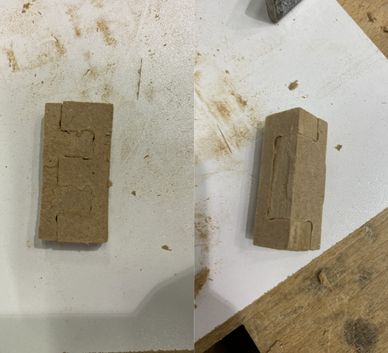
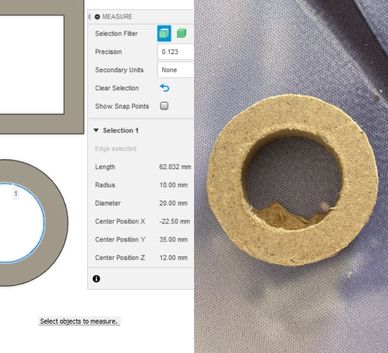
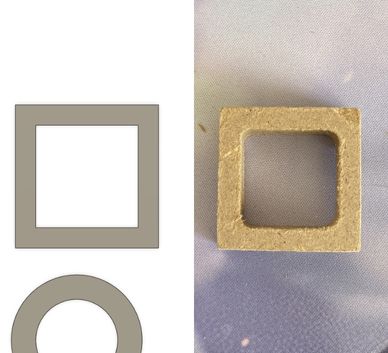
Design in Fusion360
I designed a chair, following this tutorial.
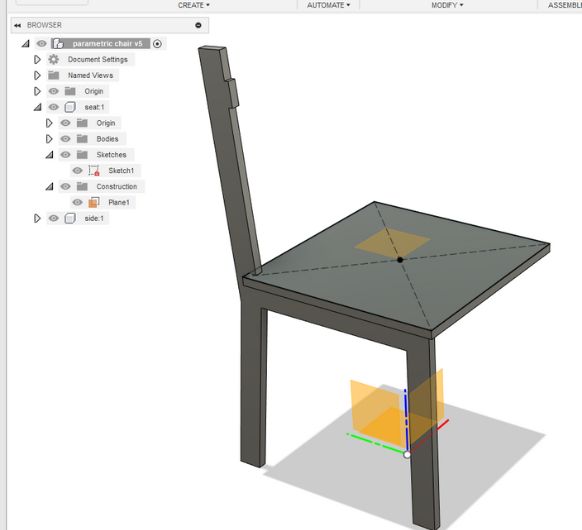
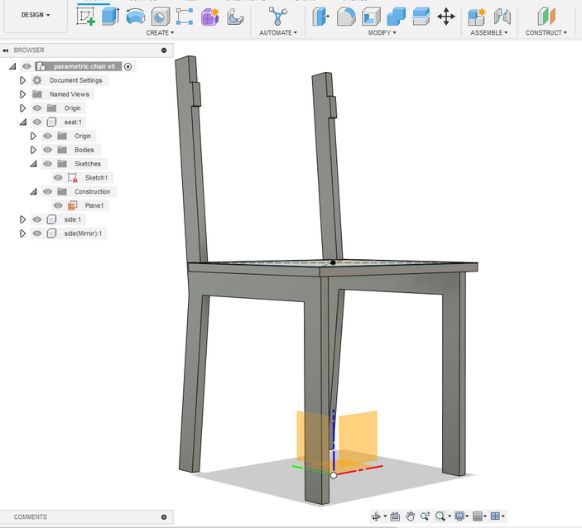
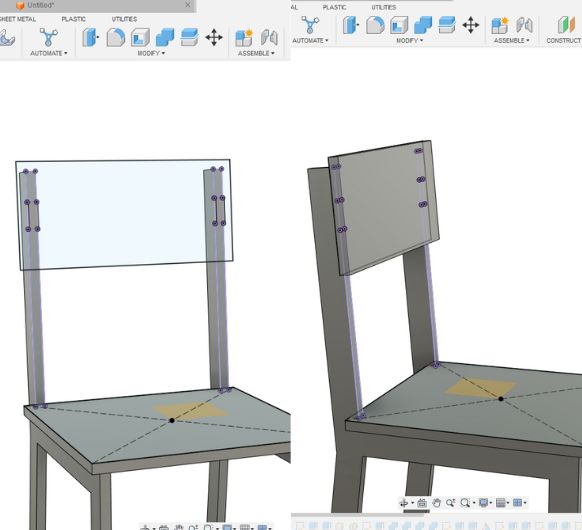
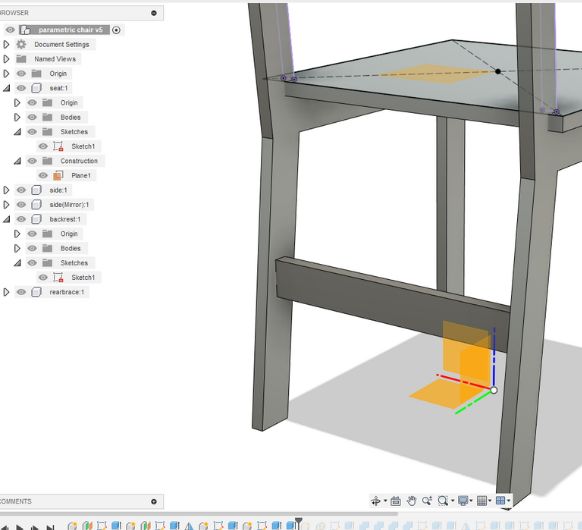
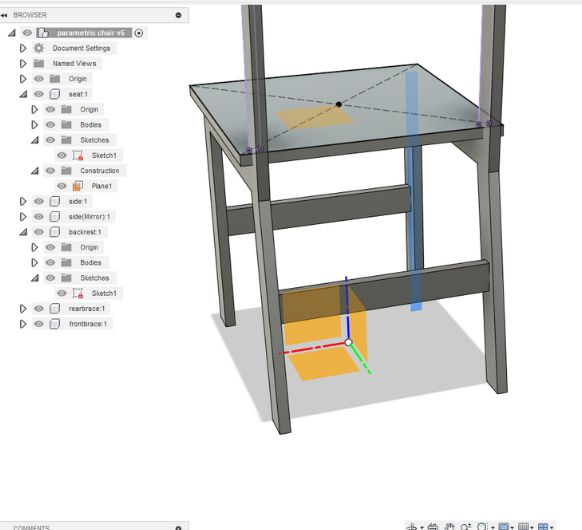
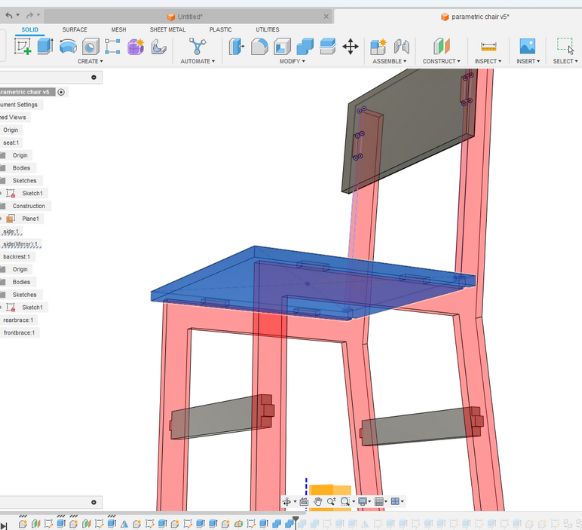
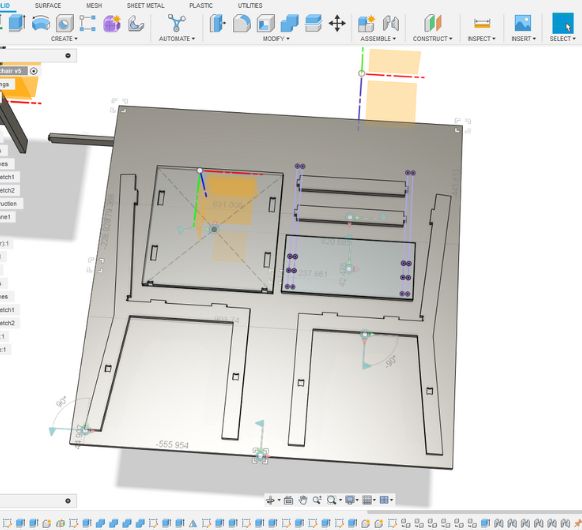
Adding dogbones
Now we I need to add dogbones to all my inner corners. This needs to be done, because the milling tool has a cylindrical shape and a certain diameter, therefore there cannot be any sharp inner corners in the design. I followed this tutorial to install a add-in for fusion which adds dogbones automatically. Follow this link: http://tapnair.github.io/Dogbone/ and install the add-in:
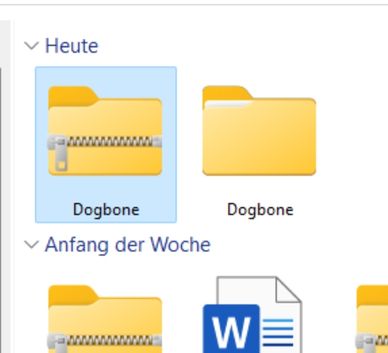
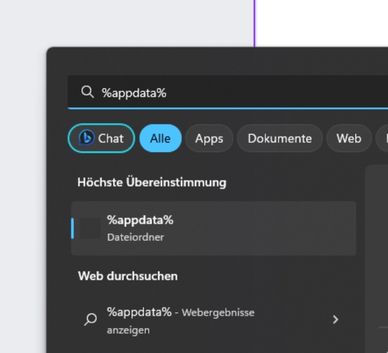
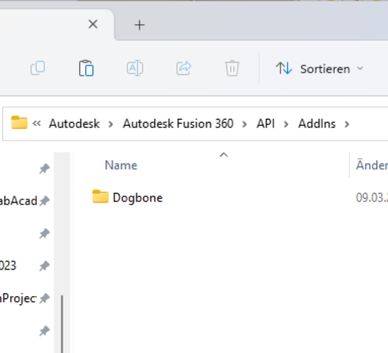
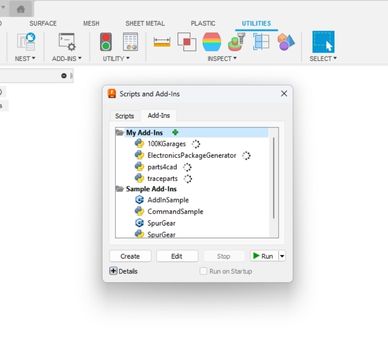
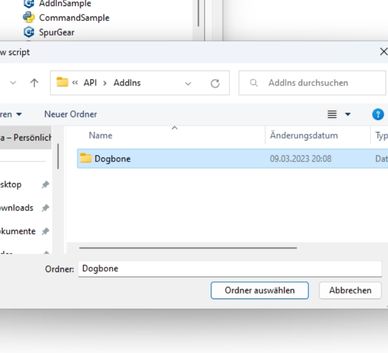
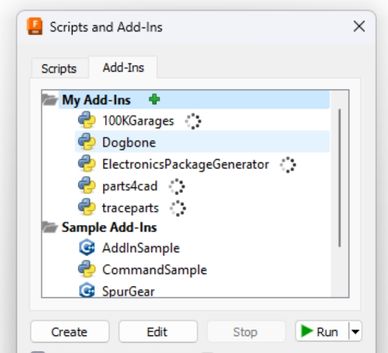
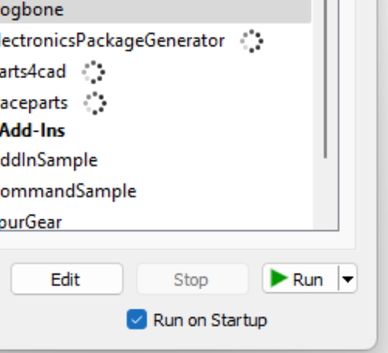
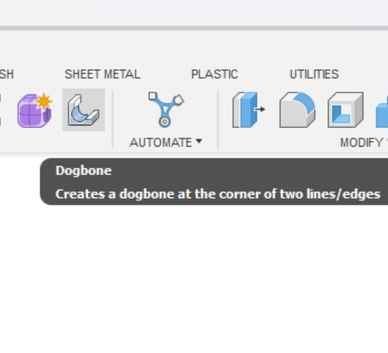
CAM Toolpath
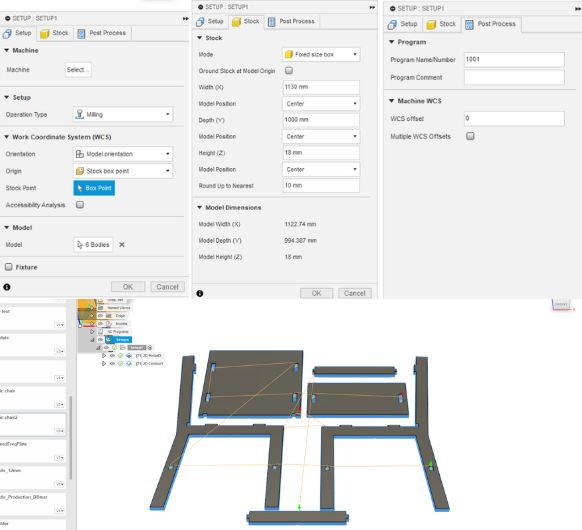
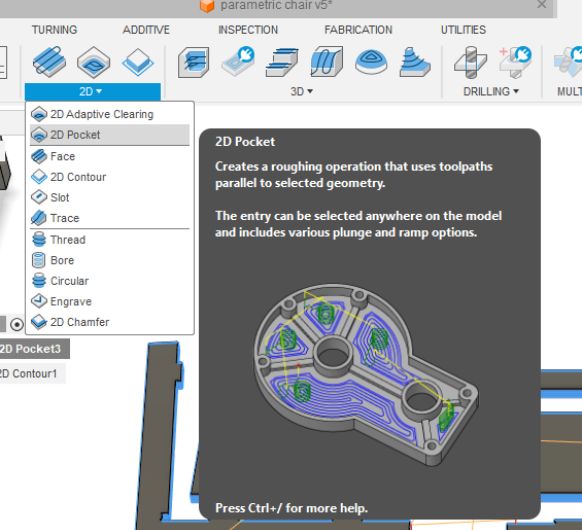
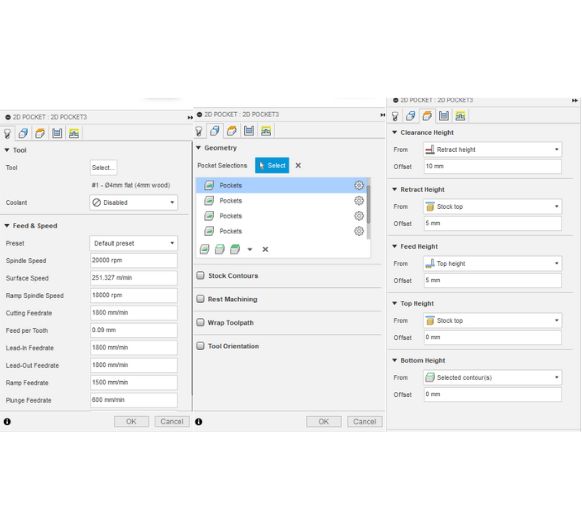
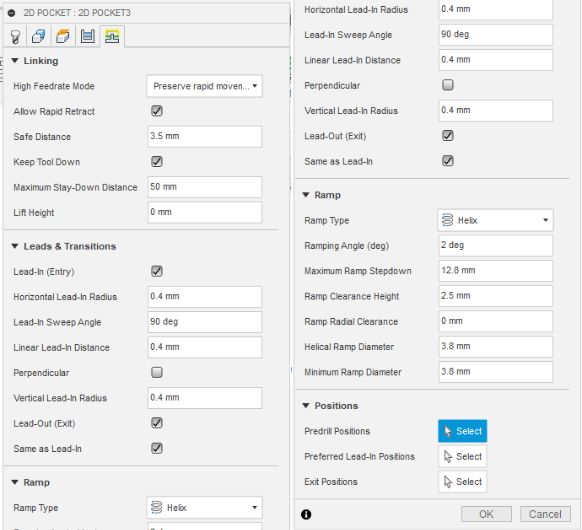
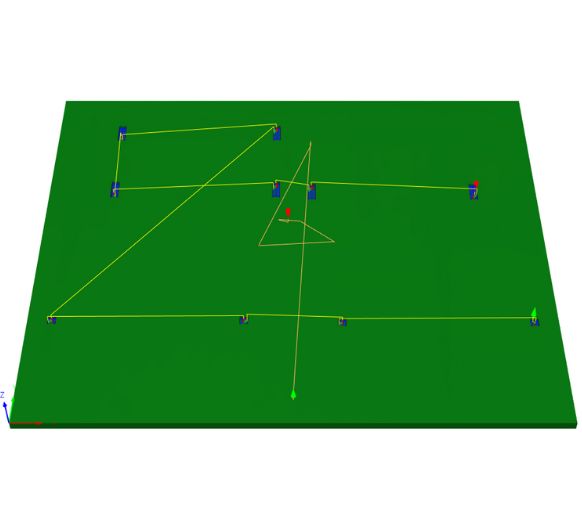
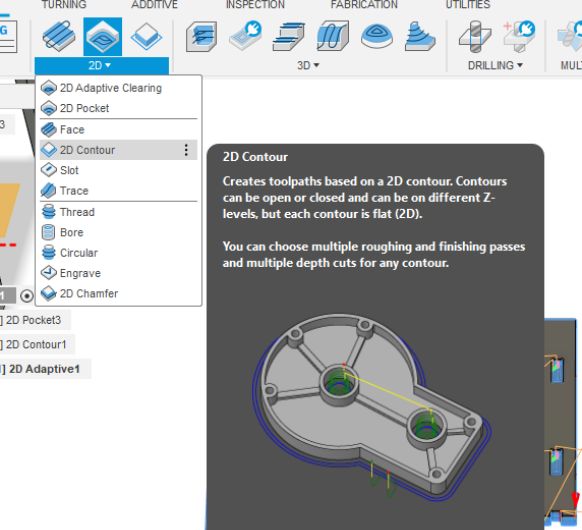
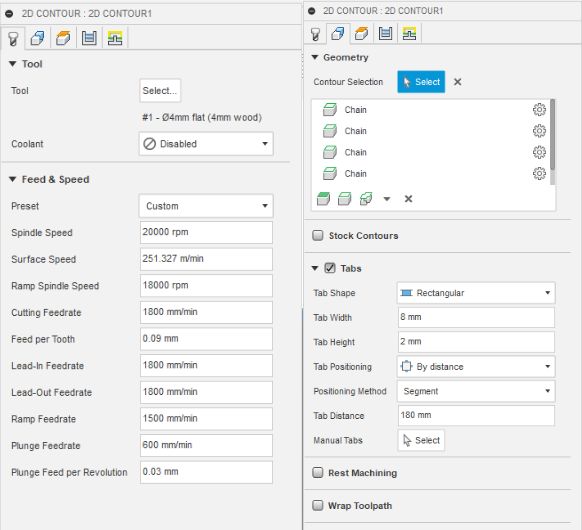
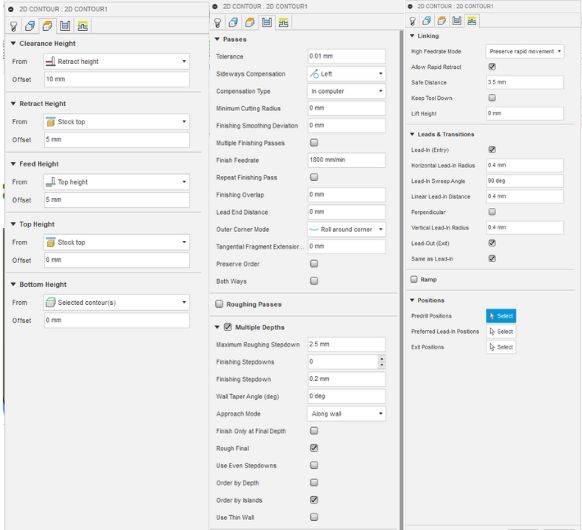
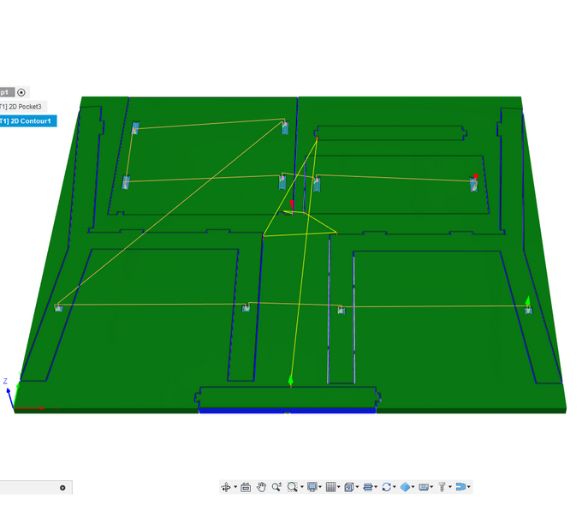
Export this and go to your CNC.
Download my Fusion project file
Operating the big CNC
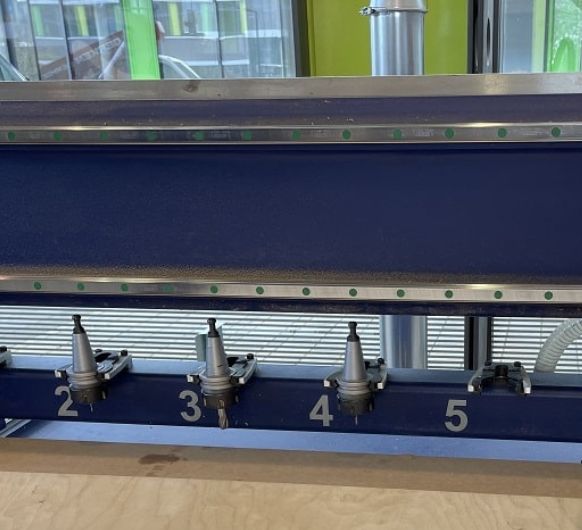
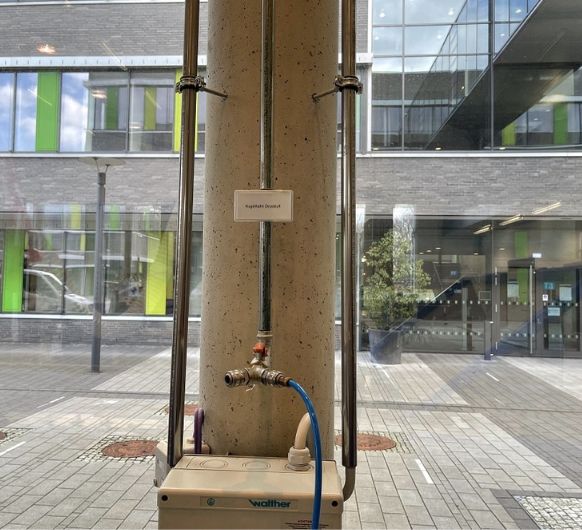
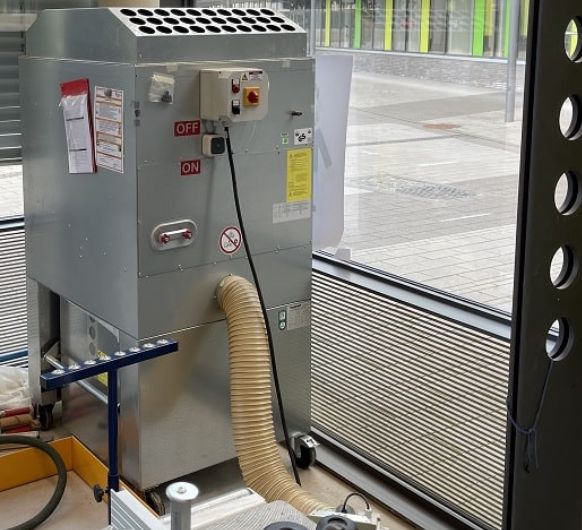
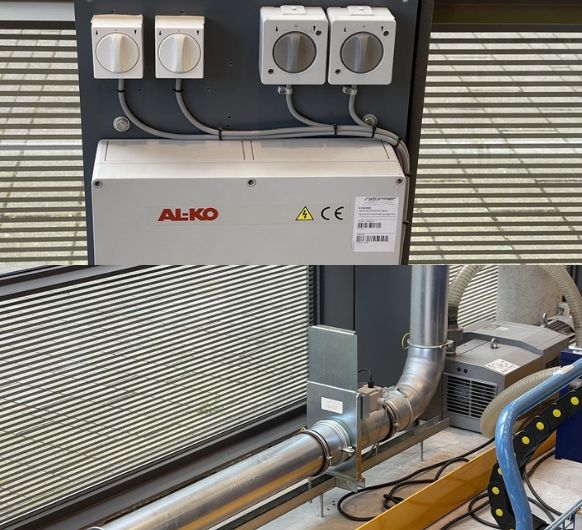
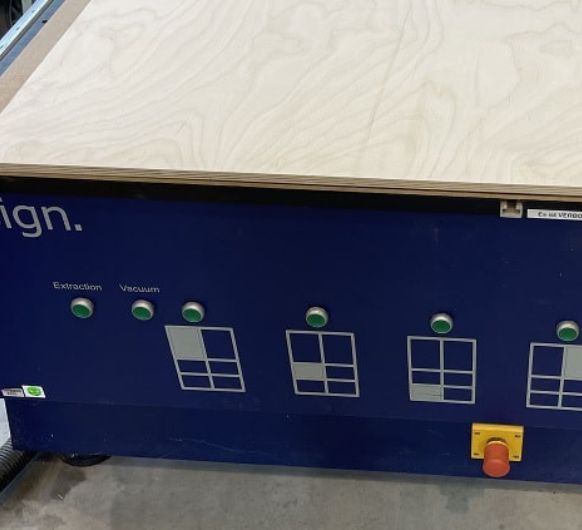
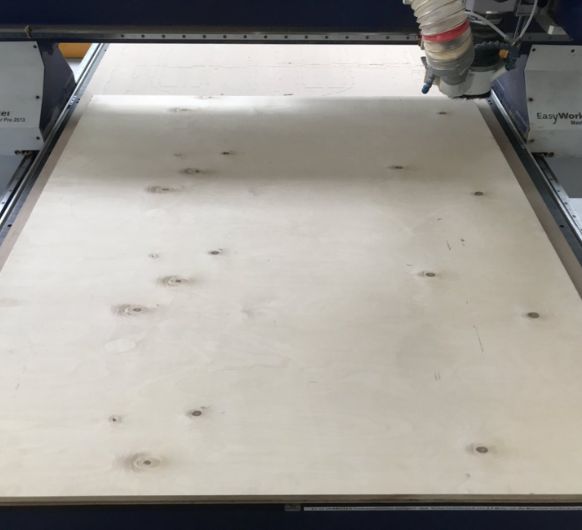
After
loading the stock, it's time to prepare the CNC:
- Start the PC.
- Press the green start button after the program has started.
- Start the machine after the program and stop the machine before closing the program to avoid information discrepancies.
- Incorrect order of operation can lead to the mill crashing into the tool swapping station. The CNC lacks collision detection and could be damaged in such a scenario.
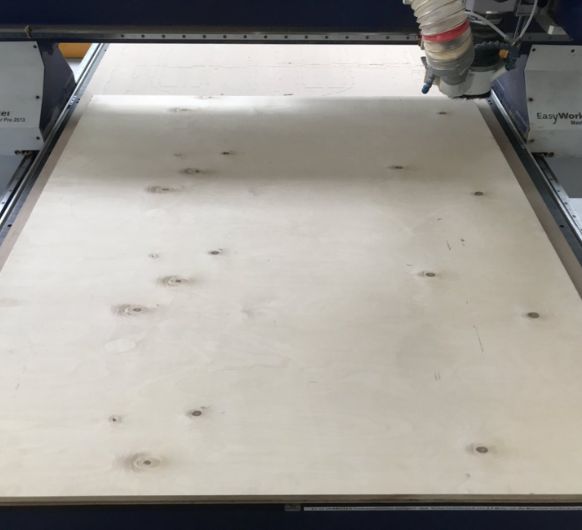
- Let's begin the milling process. Firstly, we ensured our safety by wearing earbuds and protective eye gear.
- Next, we proceeded to open the high-pressure air valve.
- Then, we started the vacuum bed with all neccessary vacuum zones active.
- Following that, we activated all the necessary vacuum zones to start the vacuum bed.
- Lastly, we initiated the exhaust system while confirming if the exhaust to the mill was either closed or open, considering that other connected machines might have been used.
- Once these preparations were completed, we loaded the toolpath that was created in Fusion360. After carefully reviewing the projected job in the software, we commenced the milling process either by clicking the "start" button in the program
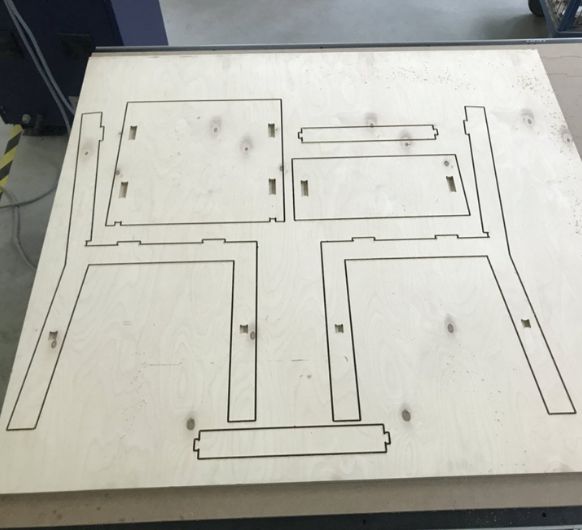
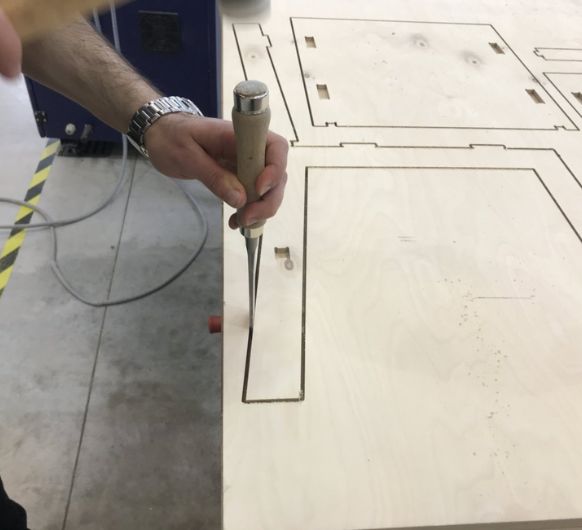
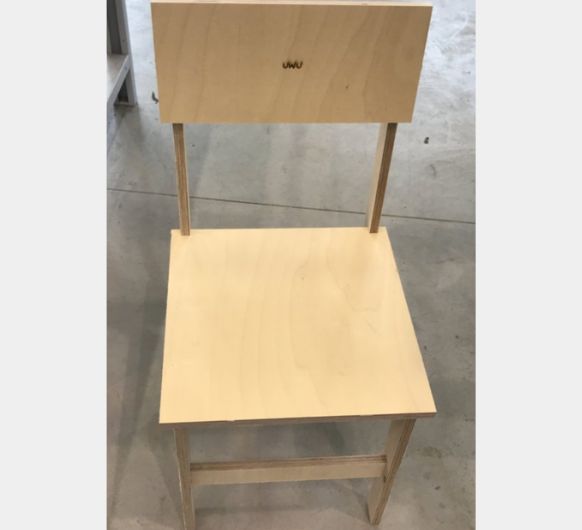