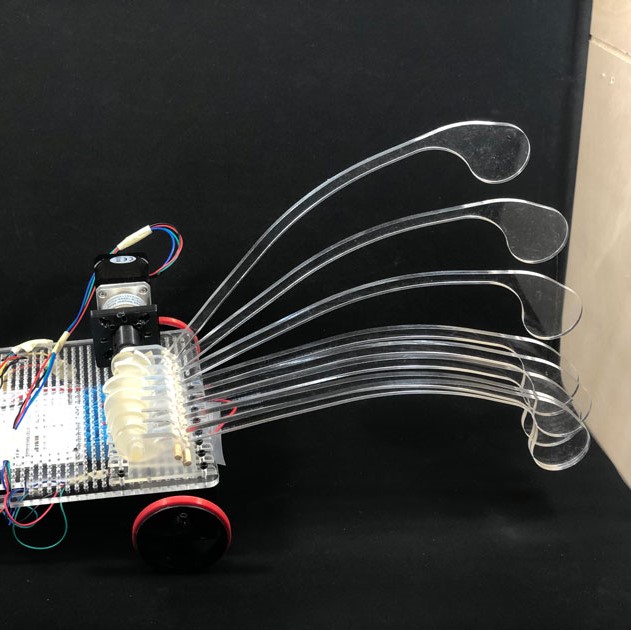
machine
common part for all teams
The body was the core part of our machine design project as it had to comply with all the rules we've defined as a group and at the same time leave some room for each group to add its individual and "secret" touch.
Here he define explain the process of the different parts that were developed. As explained before other Team's members also contributed in this part. Therefore I'll be explaining all contributions as well.
Find here the instructions:
WHY? Interface FTDI-USB* Fabbable Yes CNC Shield Compatible Yes
common part for all teams
Our way of disabling other bots
back to home page