Workflow of assignment:
Group Assignment
CNC Machining:
Computer Numeric Control, CNC Machining is a process used in the manufacturing sector that involves the use of computers to control machine tools. Tools that can be controlled in this manner include lathes, mills, routers and grinders.
Types of CNC Machines:
1. CNC Mills:
The programming employed for a mill machine could be based on either G-code or some unique language developed by a manufacturing team.
Basic mills consist of a three-axis system (X, Y and Z), though most newer mills can accommodate three additional axes.
2. Lathes:
In lathe machines, pieces are cut in a circular direction with indexable tools. With CNC technology, the cuts employed by lathes are carried out with precision and high velocity.
CNC lathes are used to produce complex designs that wouldn’t be possible on manually run versions of the machine.
Overall, the control functions of CNC-run mills and lathes are similar. As with the former, lathes can be directed by G-code or unique proprietary code. However, most CNC lathes consist of two axes — X and Z.
3. Plasma Cutters:
In a plasma cutter, material is cut with a plasma torch.
The process is foremost applied to metal materials
but can also be employed on other surfaces. In order to produce the speed and heat necessary to cut metal, plasma is generated through a combination of compressed-air gas and electrical arcs.
4. Electric Discharge Machines:
Electric discharge machining (EDM), alternately referred to as die sinking and spark machining,
is a process that molds work pieces into particular shapes with electrical sparks.
With EDM, current discharges occur between two electrodes, and this removes sections of a given work piece.
5. Water Jet Cutters:
In CNC machining, water jets are tools that cut hard materials such as granite and metal with high-pressure water. In some cases, the water is mixed with sand or some other strong substance. Factory machine parts are often shaped through this process.
ShopBot CNC Wood Router:
The ShopBot PRS Alpha is a CNC machine that allows users to cut, drill, carve and machine wood, plastic, aluminum and other materials along 3 axes, X, Y, & Z. With enough production capability of manufacturing, ShopBot PRSalpha tools are tough and gantry-based CNC routers.
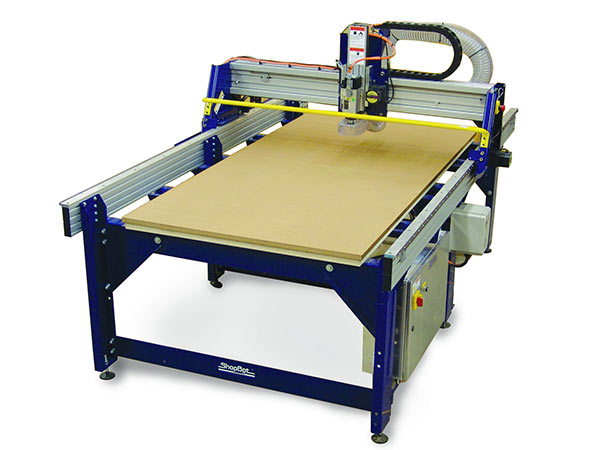
1. Specifications of Shopbot:
A. Sheet Material upto Size: 4'x 8' with machining depth (Z axis) of 6 inches.
B. Table Size: 6'x 10'
C. Step Resolution: 0.0005' or better depending on the gear ratio
D. Positioning Accuracy: +/-0.0005" or better(No load)
E. Positioning Repeatability: +/-0.003" or better(No load)
F. Cutting Accuracy:+/-0.015" or better for heavy cutting applications
G. Simultaneous Linear Interpolation:3 dimensional
H. X,Y Cutting MOvement Speed:240"(standard)/600(Alpha) per minute
I. X,Y Rapid Positioning Speed: 600"(standard)/1800"(Alpha) per minute
J. Z Axis Move Speed:360" per minute
K. Linear Force:60-75(standard)/150-200(Alpha)lb. at 60° per minute, depending on gearing.
2. Test Parts on ShopBot:
A. Design and toolpath on PartWorks:
On PartWorks chose the bed size as 2400 x1200mm and drew basic test parts circle, square, pentagon etc.Generated toolpath and under edit options we set the parameters.
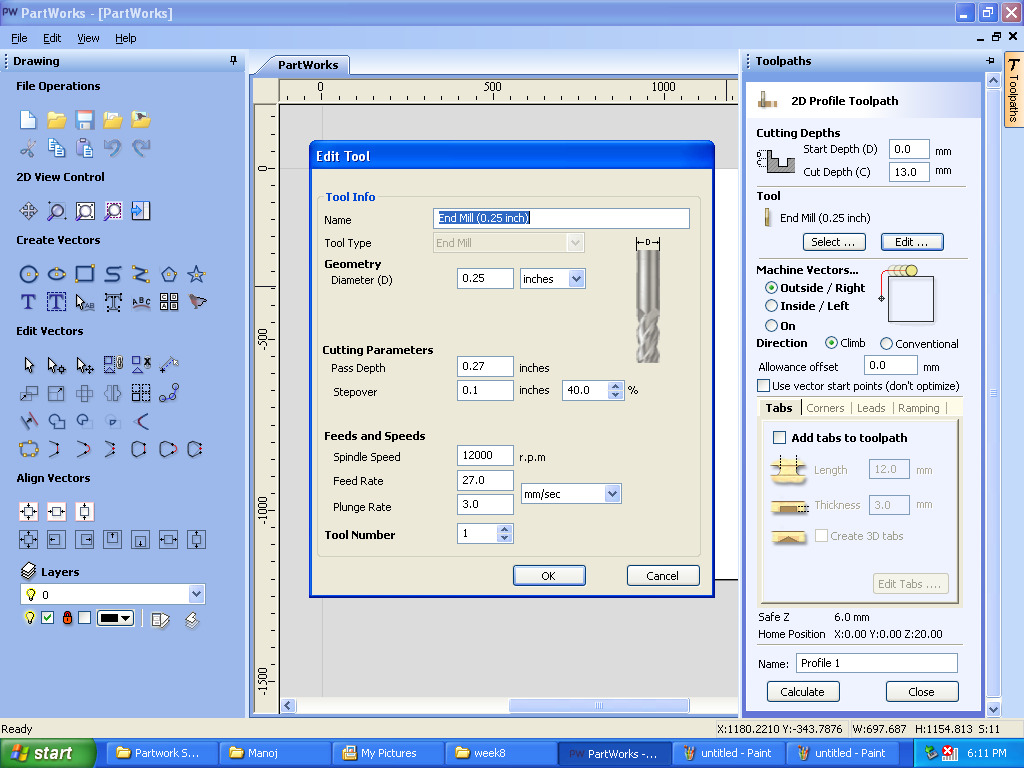
B. Settings and Parameters :
a. End Mill : We used bit size 1/4" for cutting.
b. Plunge Rate : It is also known as stepdown. The distance in the z direction per pass that a cutting tool is plunged into the material.
c. Spindle Speed : Rotational speed of the cutting tool in revolutions per min.
d. Step Over : The maximum distance in the x/y direction that a cutting tool will engage with uncut material.
e. Feed Rate : Surface speed at the center of the Rotating tool.
f. ShopBot3 editor : Opened the editor and using the keyboard keys adjusted the X,Y,Z position.
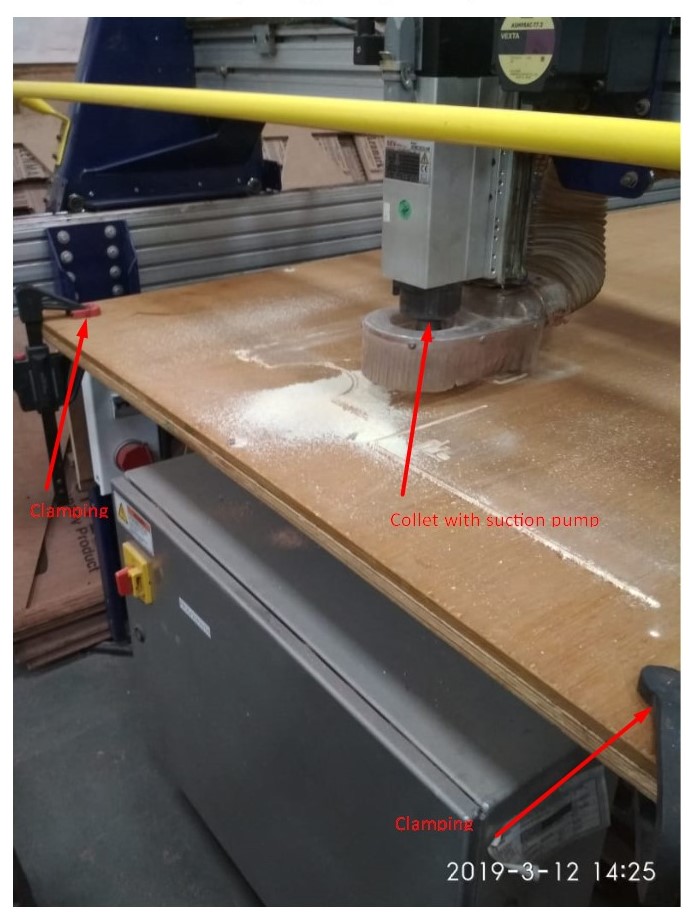
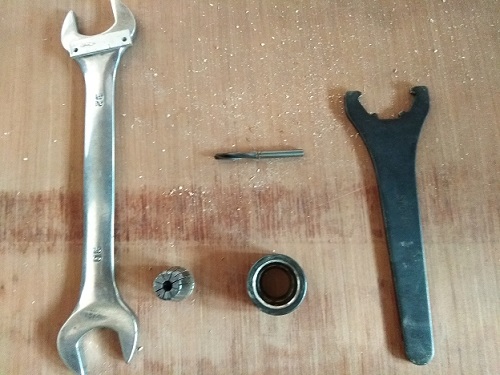
C. Test parts:
After bed setting, instructed the machine to cut the test parts. We also measured the "Kerf" values for the test parts.
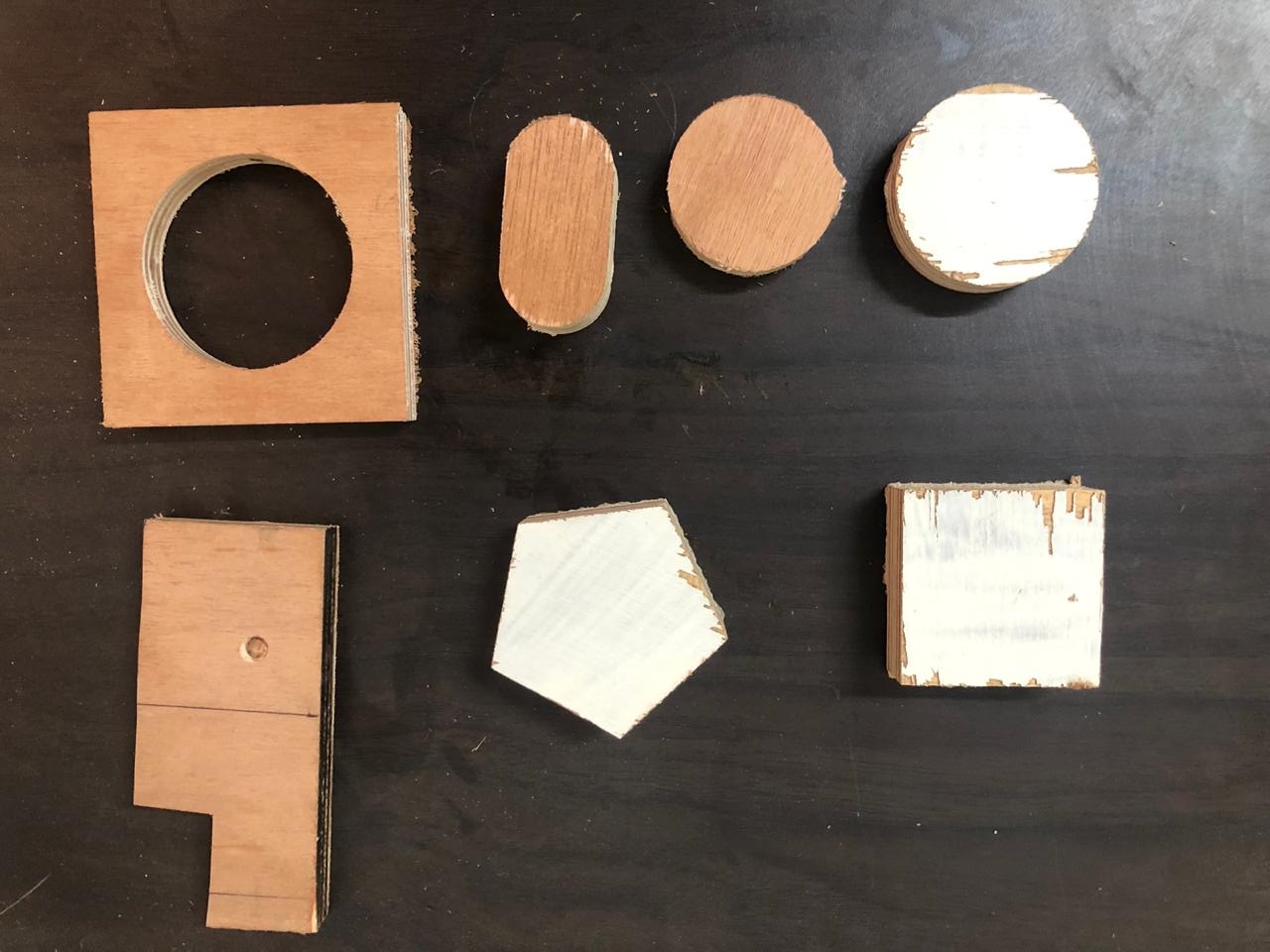
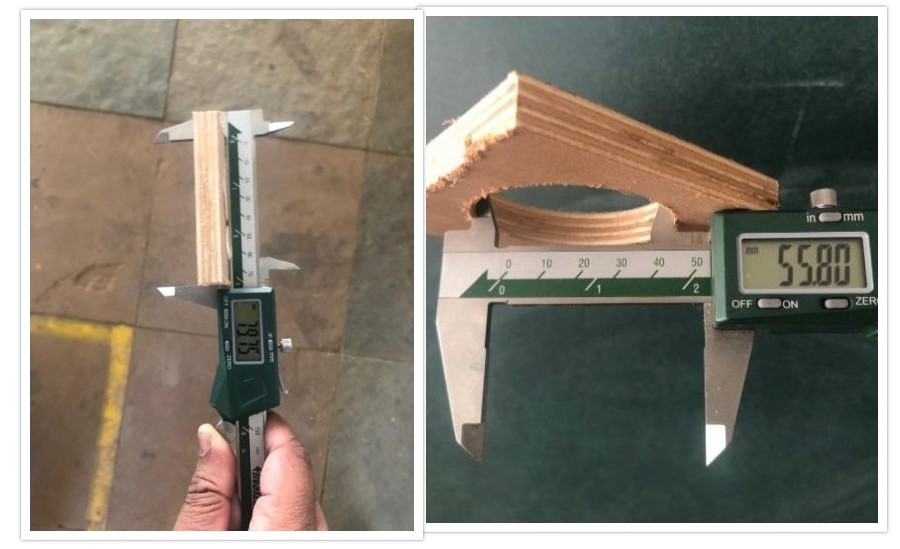
Individual Assignment:
About "NUMAC HITECH -6090" Computer-Controlled Machine:
The wide range of products is a result of intense quality analysis of raw materials at the initial stages of production. With stern checking, the products are examined with utmost precision. As we have an efficient supply chain network, our company is able to fulfill bulk orders with ease and make deliveries on time.
Features :
Advanced mechanishm
Low maintenance
High productivity
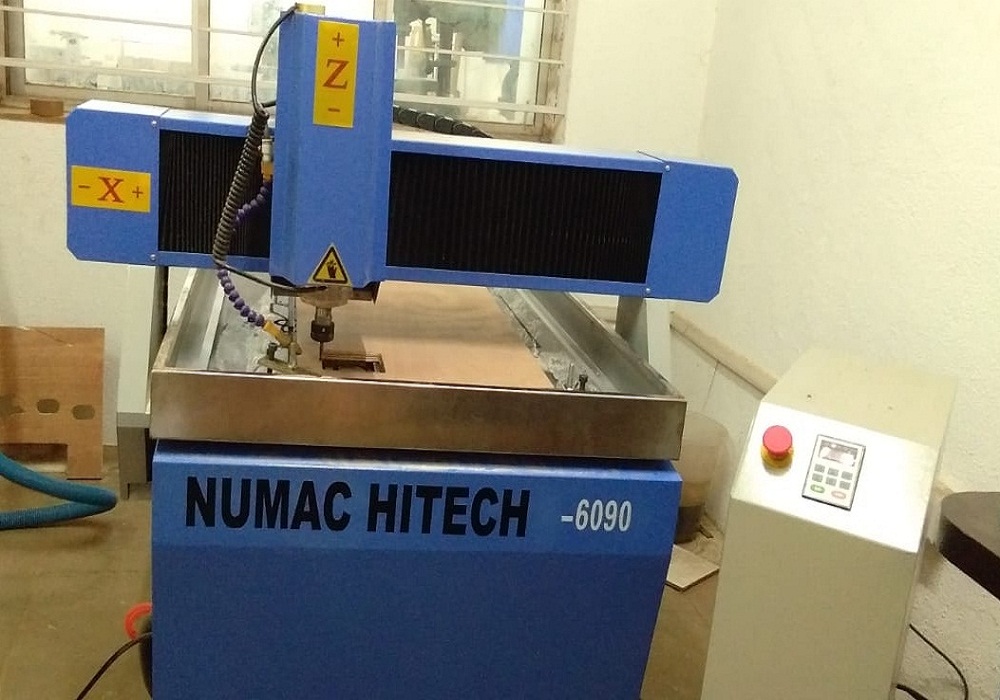
In our fablab we have "NUMAC HITECH" Milling Machine. SRM-20 have more features than the MDX-20. like user-define origin etc. Now I am going to mill my pcb and make the group assignment.
I am going to make laptop table for 'Head of Department' of our Innovation hub.
Designing:
I am going to design laptop table in solid works software. I decided dimensions of laptop table would be 450mm X 300mm.
I also made place for cofee-mug, mouse, mobile keeper and mini things keeper in my design as shown below:
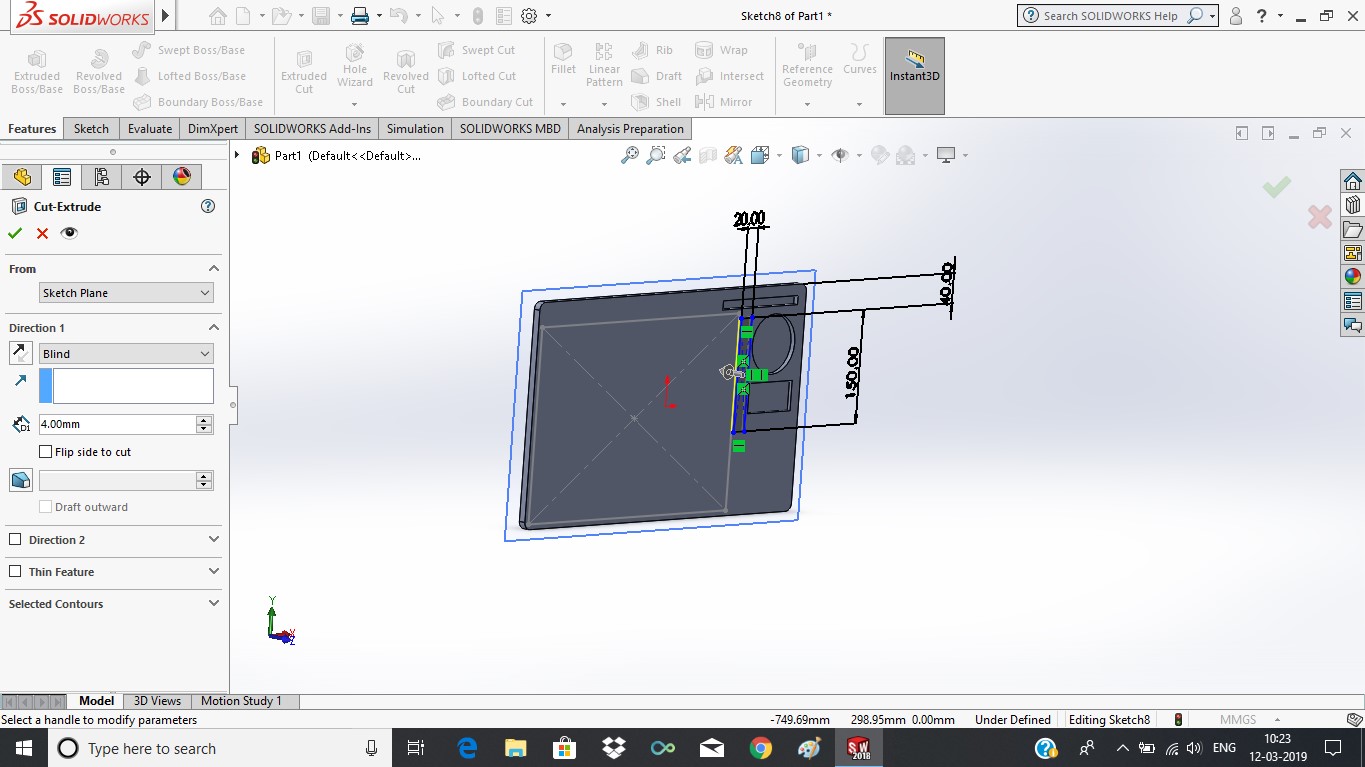
Next step is design legs for table and attachments should be 'Doggy bone' type. I designed slot on surface with doggy bones type. Design file attached below this page, you can find it there.
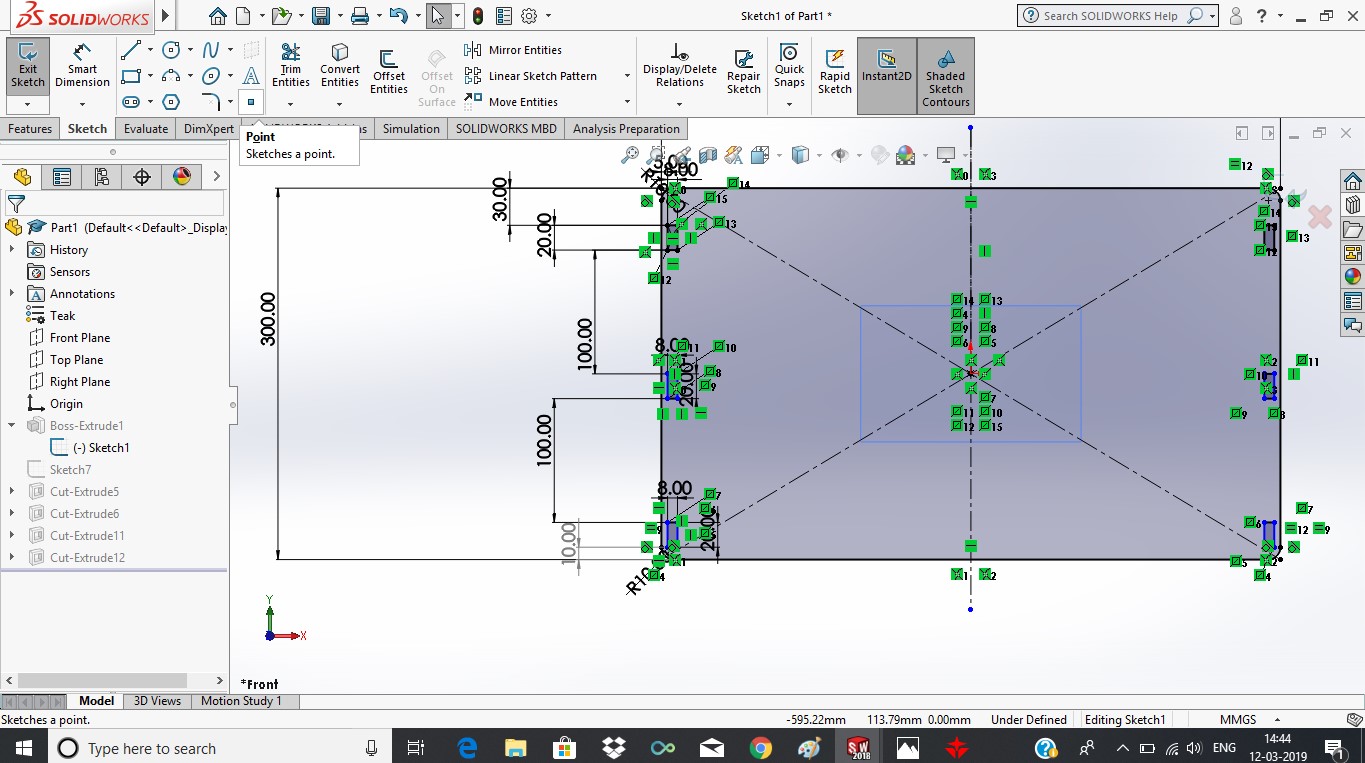
Milling Process:
For milling I need to make 'G-code" (Toolpath) file from the '.DXF' my design file. There is a "Art Cam Pro" software for making 'G-code' file form '.DXF' file.
Art Cam Pro:
ArtCAM Pro is a program that lets users create or import designs for the purpose of rendering them into 3D blueprints for computer-aided manufacture (CAM).
The software has both 2D and 3D design tools, so users do not actually have to begin with base drawings or images made with other programs or media. The modeling process (the transformation of image designs into CAM-ready 3D designs) is carried out through a novel layer management scheme. It has 3D rendering tools for previewing designs, special utilities for embossing and other mint-related styles, a tool for sculpting 3D profiles out of facial profile images, specialized texture tools, and support for hundreds of manufacturing machines. It is also exclusively for Windows computers.
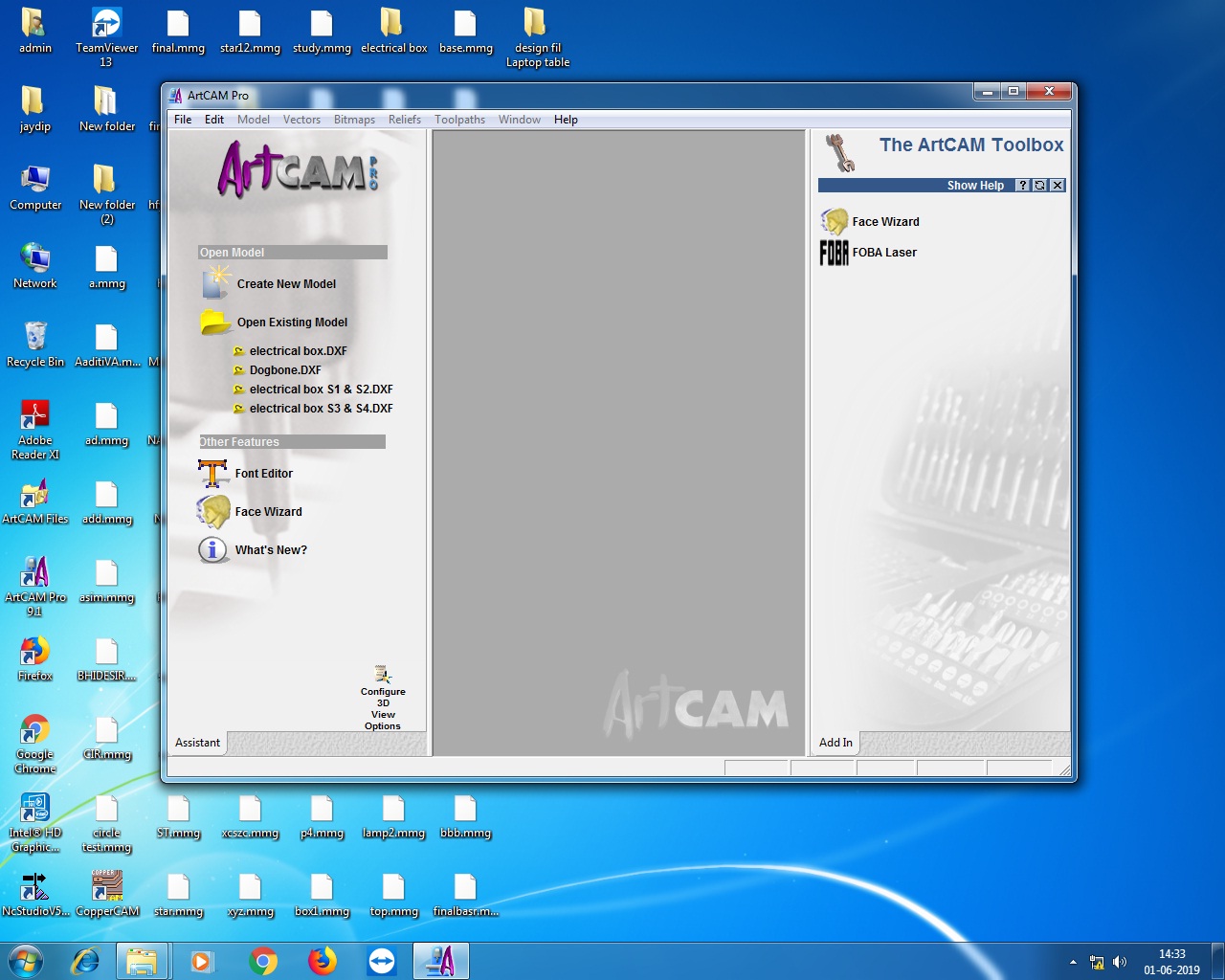
Next step is the entering the dimension of oject.
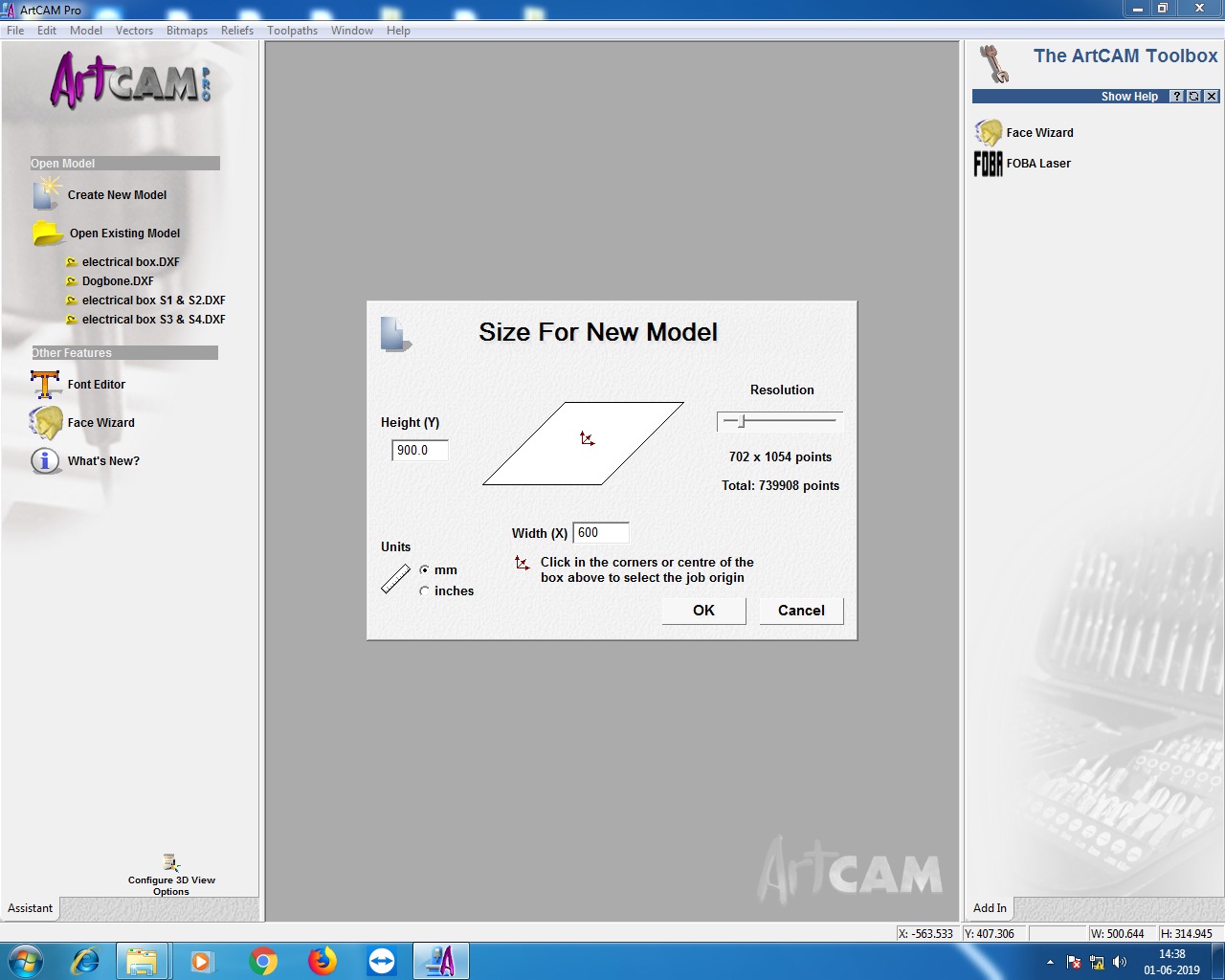
Next step is importing '.DXF' file into software and generates toolpath.
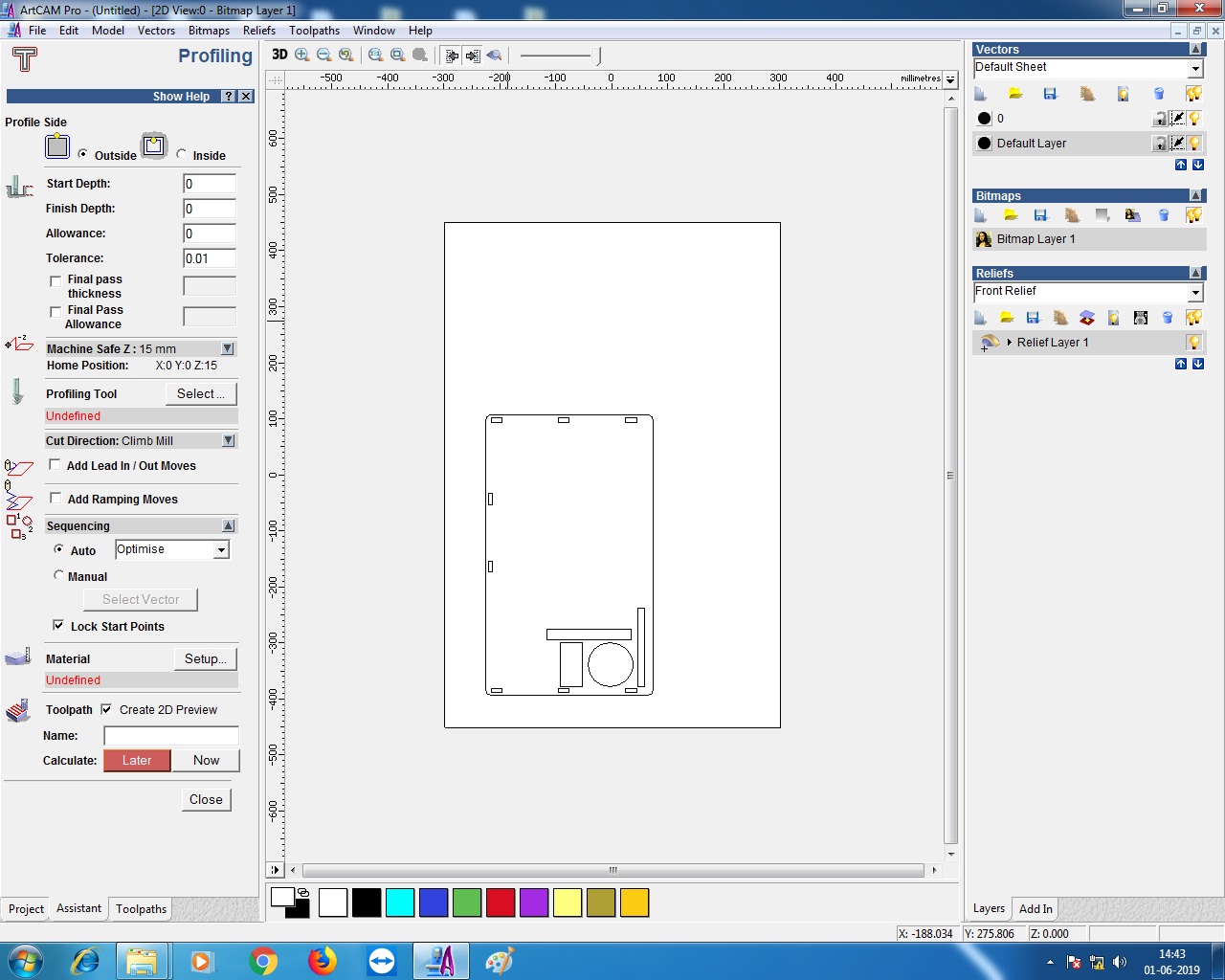
Making two different profile for toolpath.
1. Outside profile
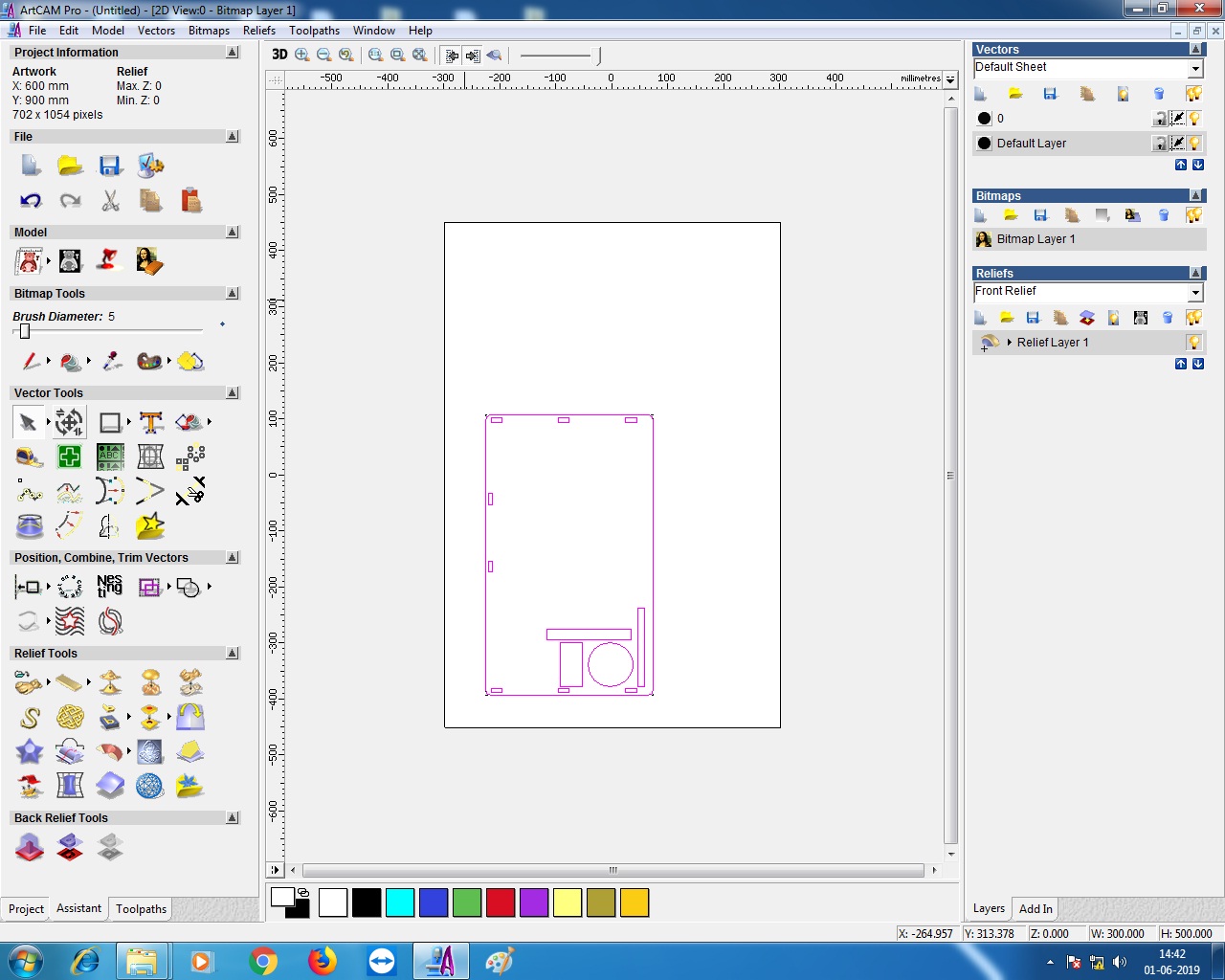
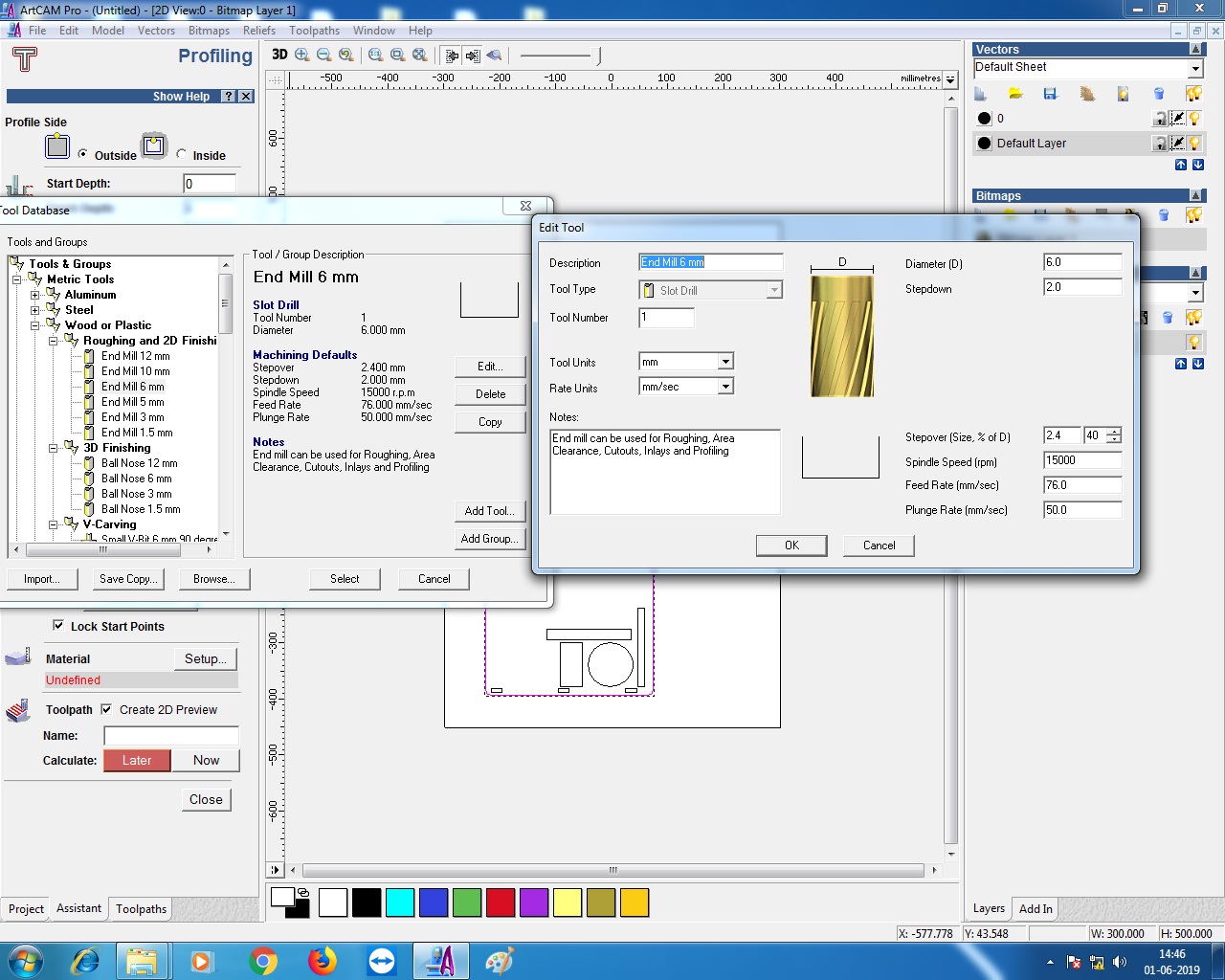
Making another profile for toolpath. And also did the for milling Bit selection for inside profile.
2. Inside profile
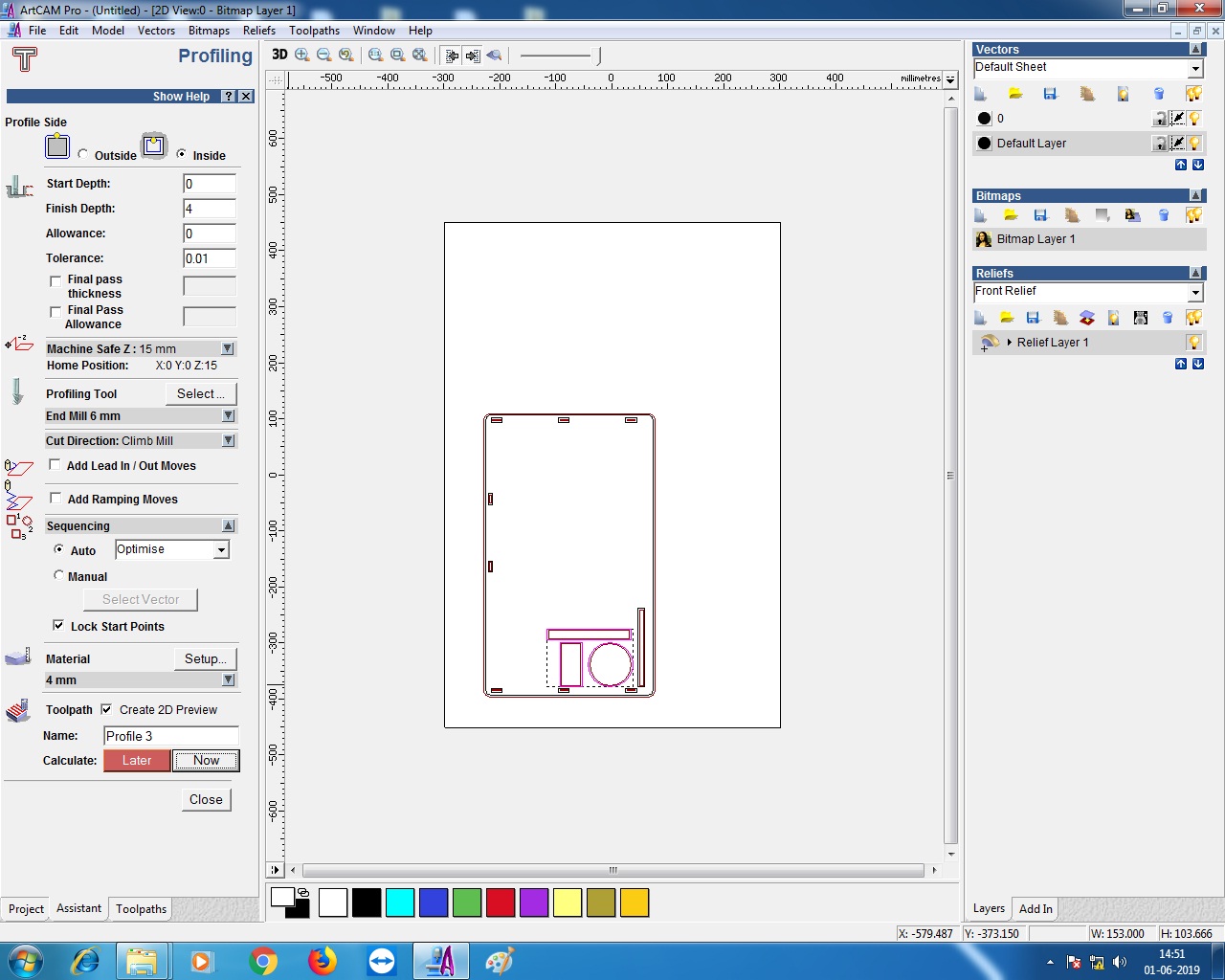
Now, Combined both profile for generating toolpath.
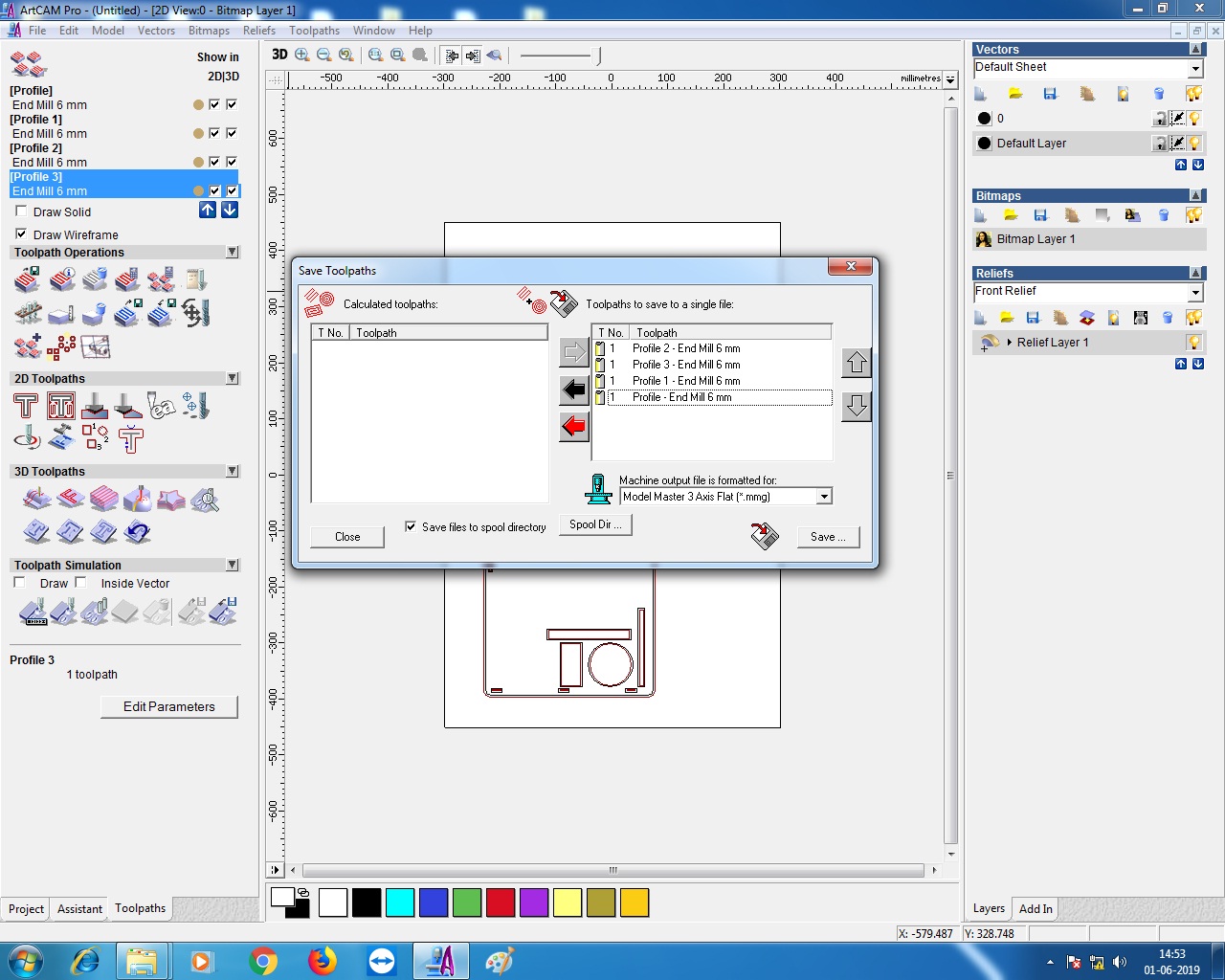
Now, need to be generate last toolpath for legs of laptop table.
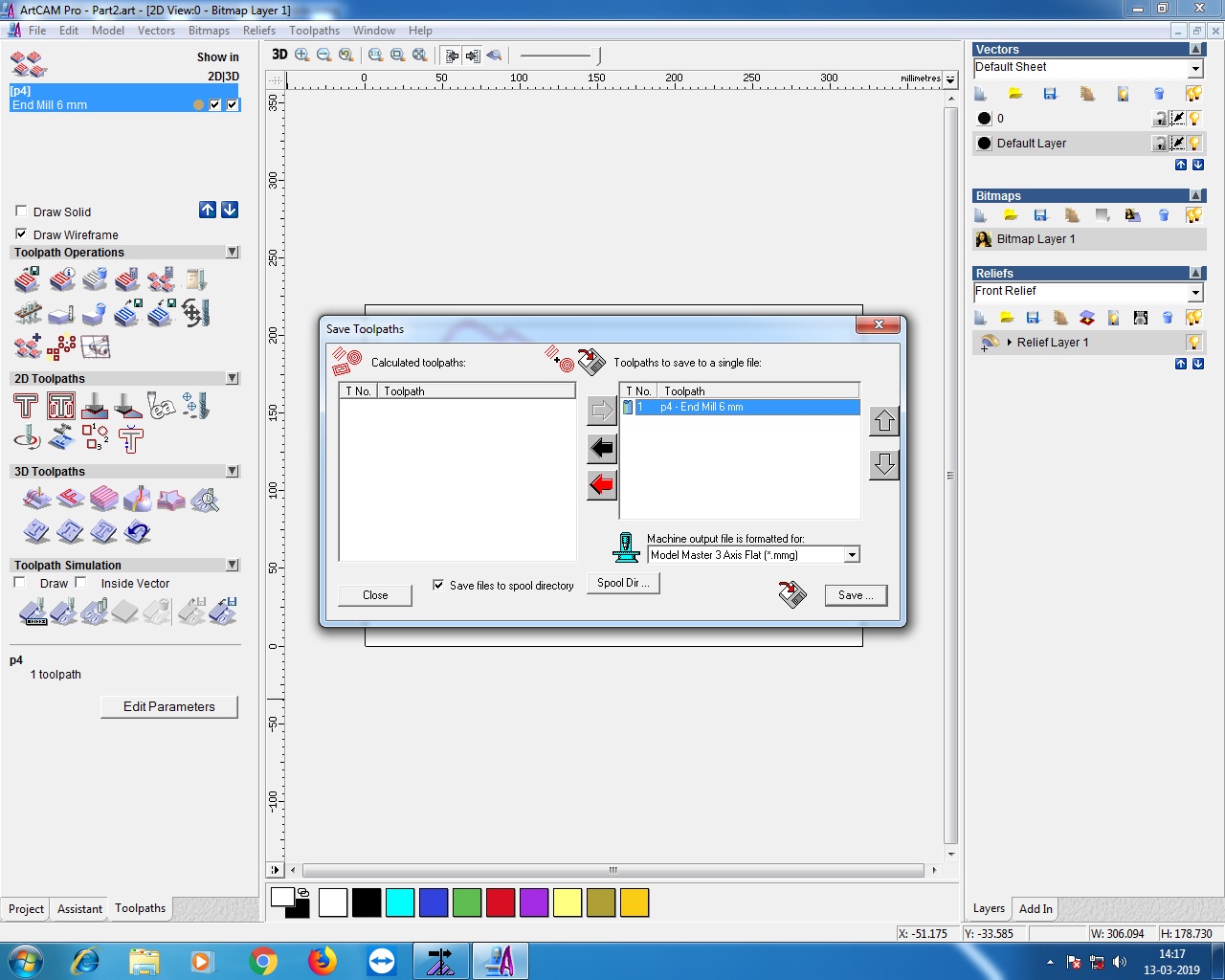
All toolpath generated successfully. Now, going to machine software 'Nc Studio AD. Engraving Machine Control System'.
Nc Studio:
NC studio is a software to control Chinese CNC machines and not only. Well, there a different type of Wood working and Metal working CNC machines. If you already using NC studio then you know that this software controlling CNC through special control card that connected to your PC.
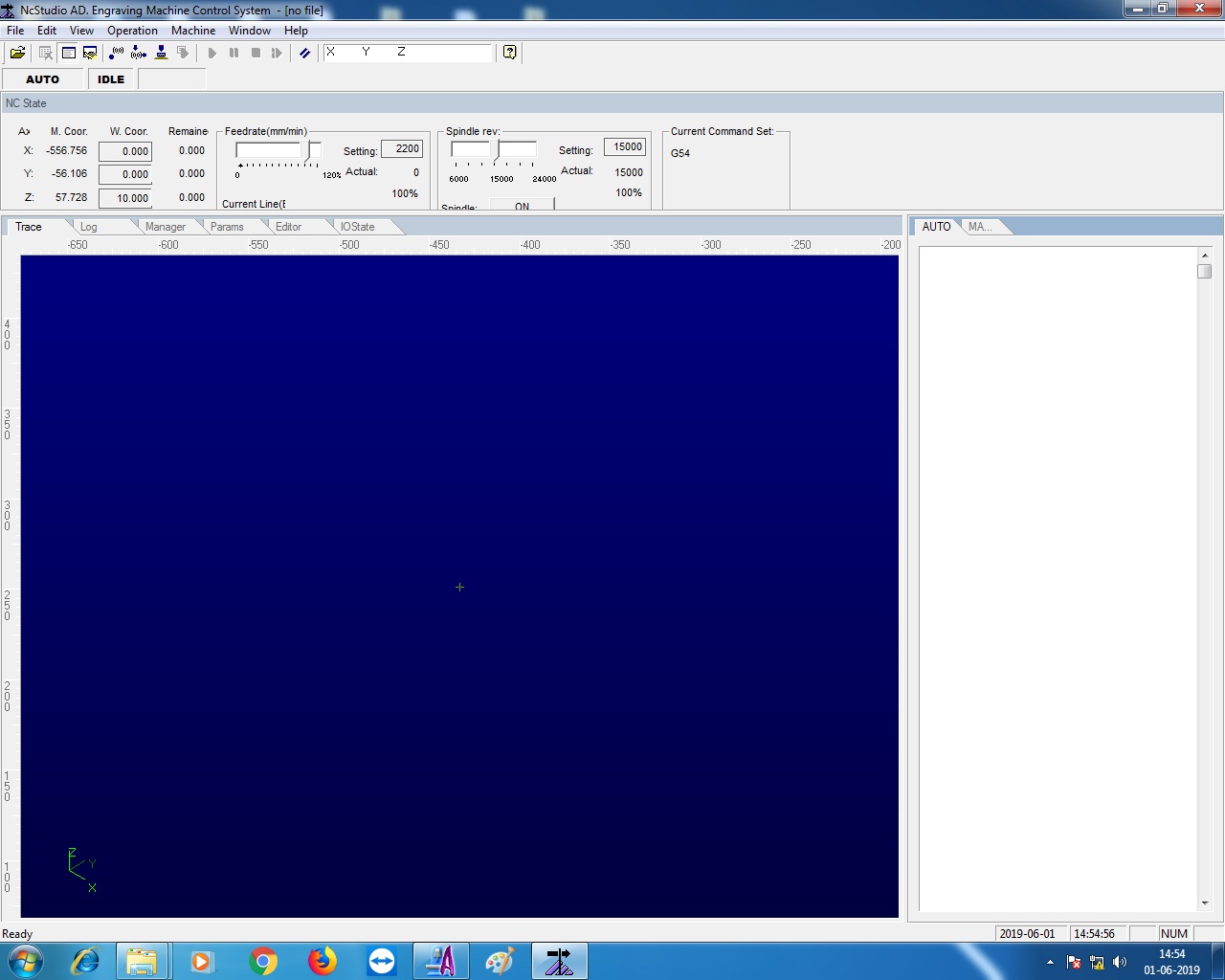
Next setp is the importing 'toolpath' file of laptop table into'Nc Studio'.
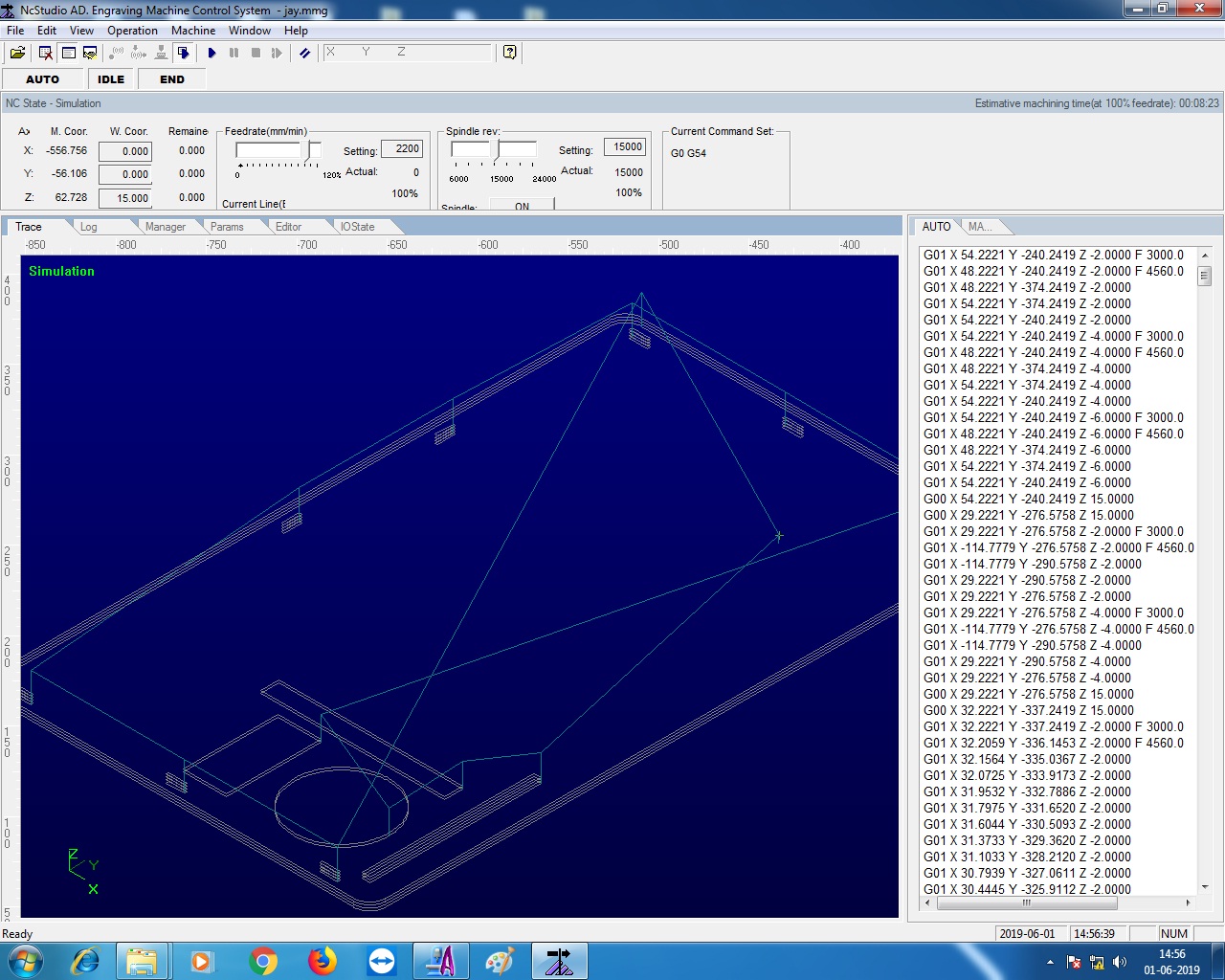
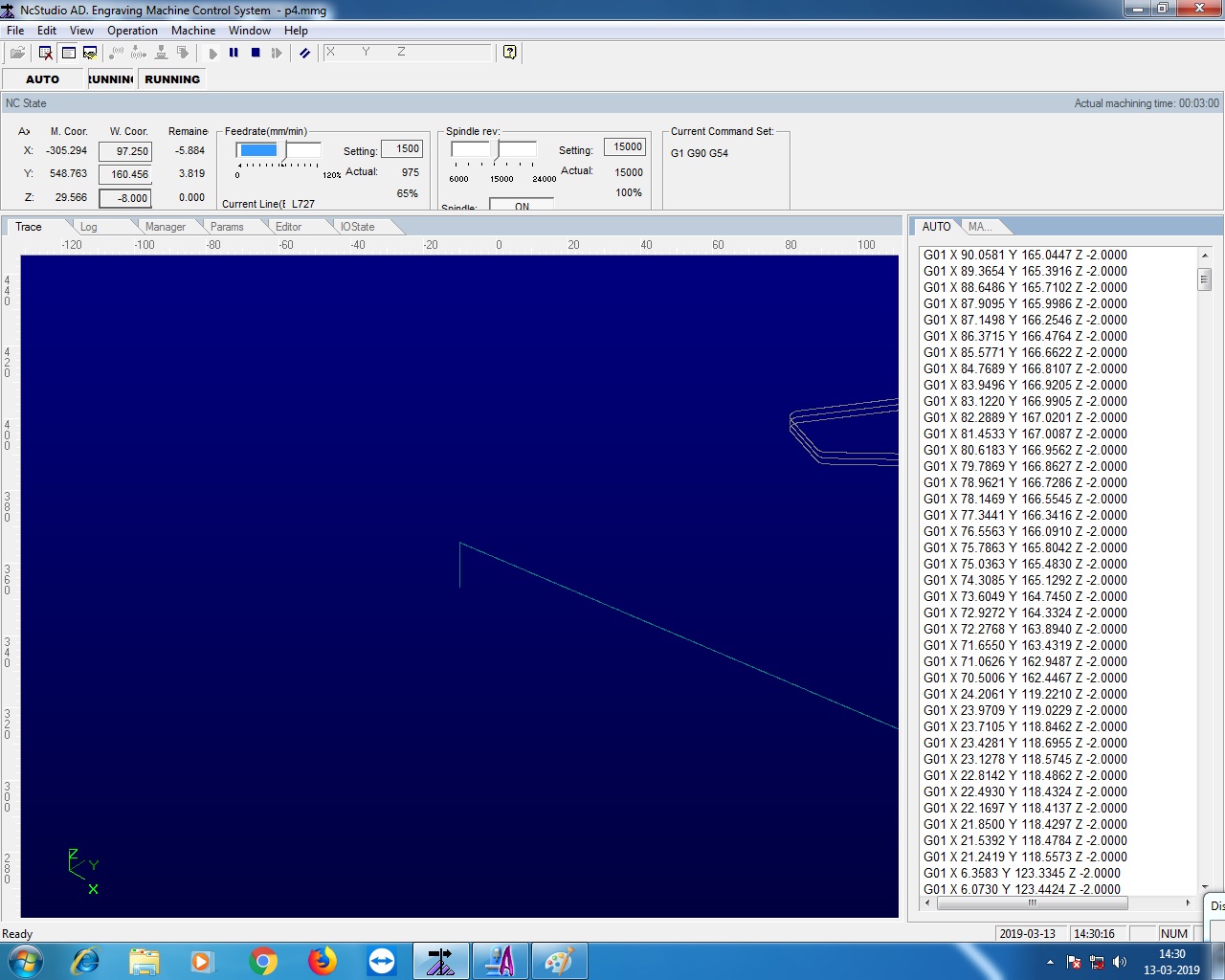
Cutting bit Assebly:
before starting cutting, I need to fix 'cutting bit' to the manchine.
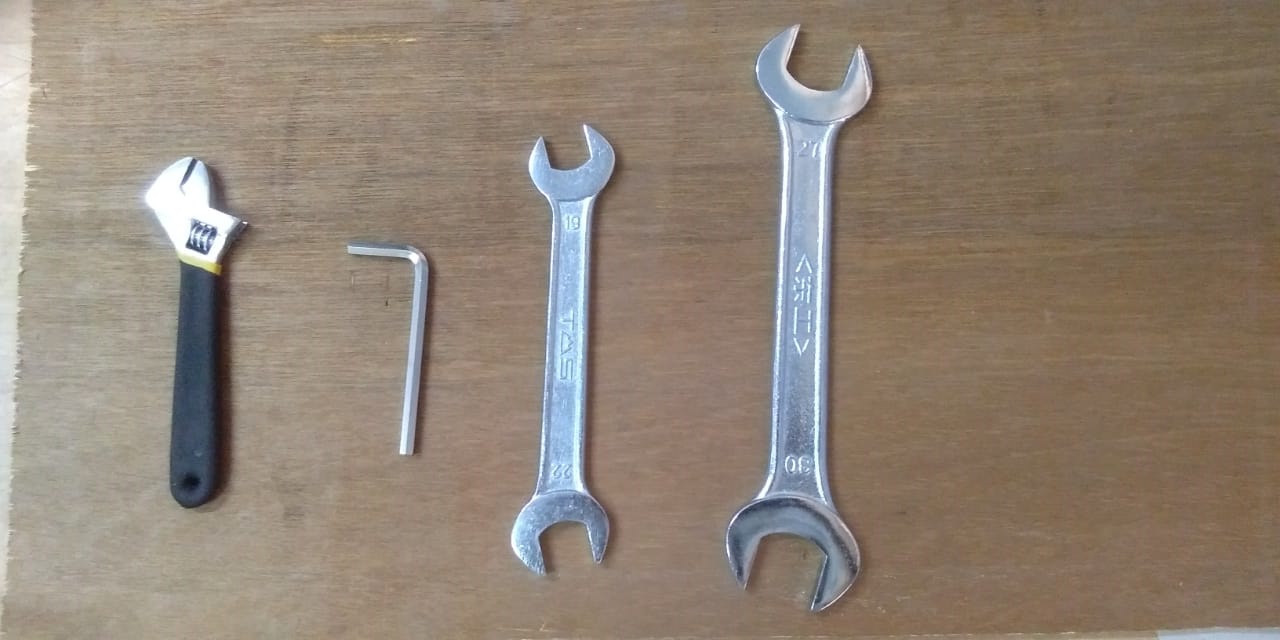
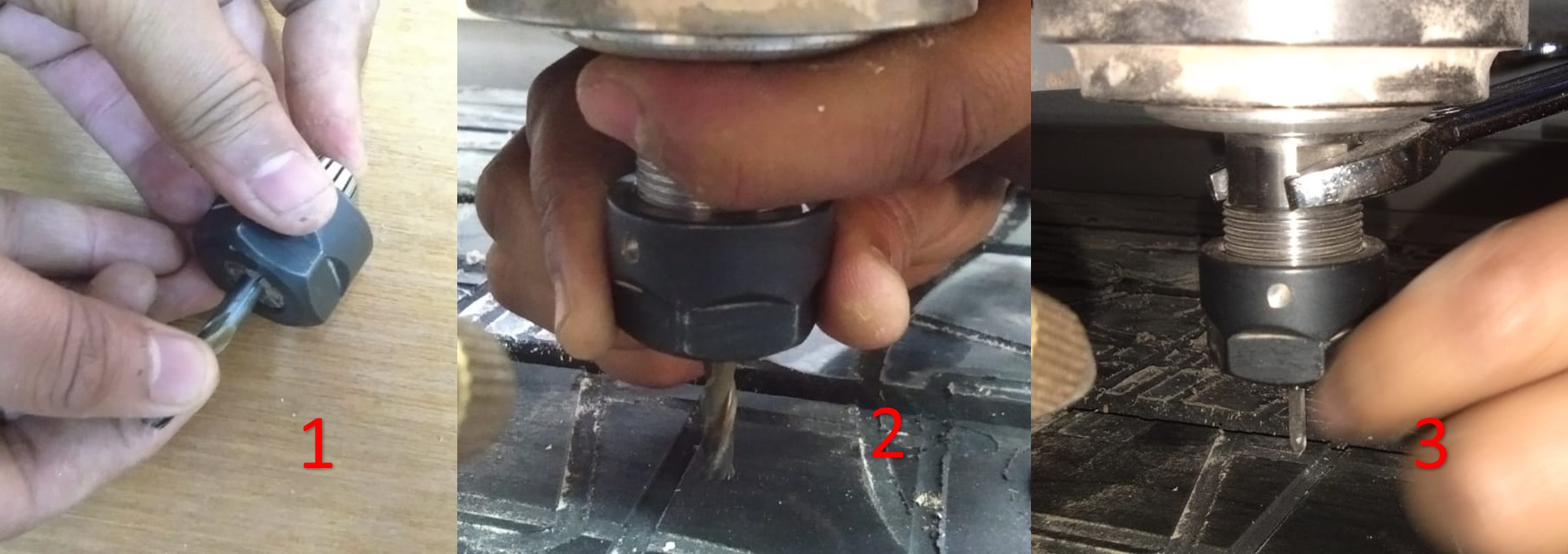
Assembly of parts:
Cutting and engraving done successfully. Now, remaining work is assembly of cut parts.
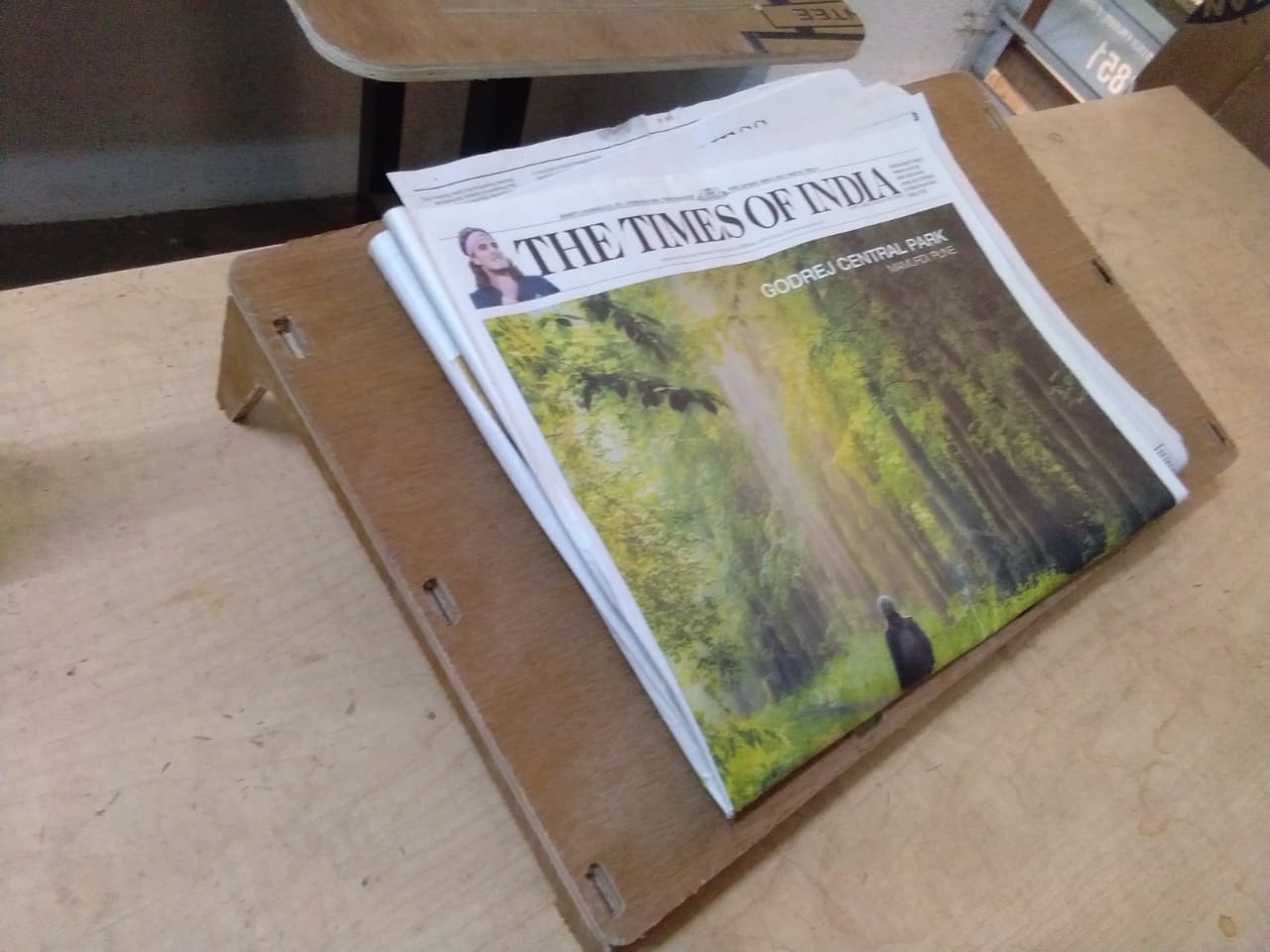
After done the assembly of parts, my instructor Miss. ARUNDHATI JADHAV was checking my work on laptop. Laptap is kept on laptop table made by me.
Final Shot:
Learning Outcomes
1. Learned 'how CNC machine useful in wood working'.
2. Understood the process of making toolpath for 'Numac CNC machine' from 3d design file.