Week 20: Project Developement
Assignment
☑ What needs to be done?
☑ What have you done already?
☑ What will happen and when?
☑ what have you learned?
What needs to be done?
I had work for a week right before my final presentation. I had 10 days left.
I had been trying to use my time wisely so that I could finish my final project in time,
but I still had to spend many sleepless nights.
I am going to make a smart helmet that knows when I stop to change the colors of the light to red
using accelerometer and neopixels.
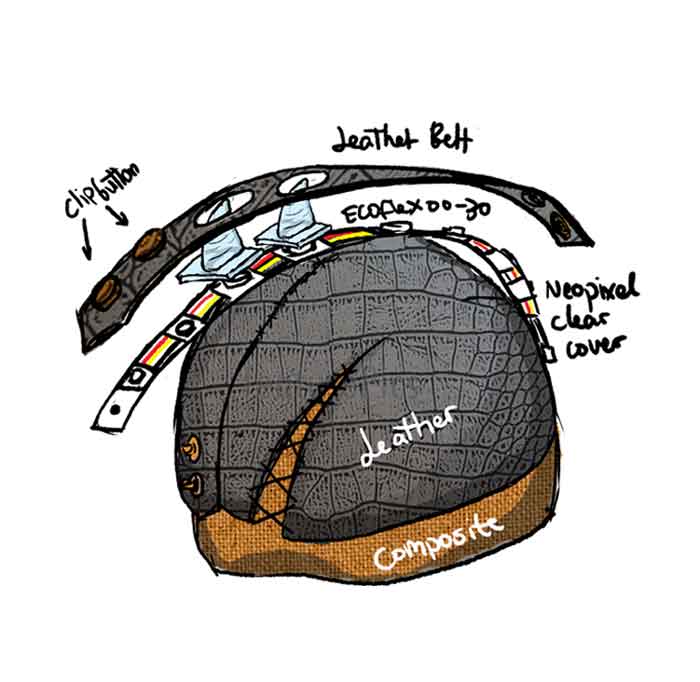
List of things I need to do and proper steps
- Make the Silicone spikes
- Make 3D
- Cut the wax for mold
- 3D print the inside mold
- Cast 7 spikes (and more just in case)
- Make the protective Helmet part
- Make mold for Composite
- Make resin composite
- Refine Helmet
- Make patter for Leather
- Cut and Sew Leather on helmet
- Connect Neopixels
- Cut up the Neopixels
- Solder them to Correct Length
- Clear cover for waterproofing
- Conncection
- NightFury PCB
- Connection check
- Design PCB
- Cut PCB
- Debug
- Accelerometer
- Connection check
- Coding
- Make 3D
- Cut the wax for mold
- 3D print the inside mold
- Cast 7 spikes (and more just in case)
- Make mold for Composite
- Make resin composite
- Refine Helmet
- Make patter for Leather
- Cut and Sew Leather on helmet
- Cut up the Neopixels
- Solder them to Correct Length
- Clear cover for waterproofing
- Conncection
- Connection check
- Design PCB
- Cut PCB
- Debug
- Connection check
- Coding
What have you done already?
Thankfully, I had made the hard part of the helmet during [Wildcard Week!]
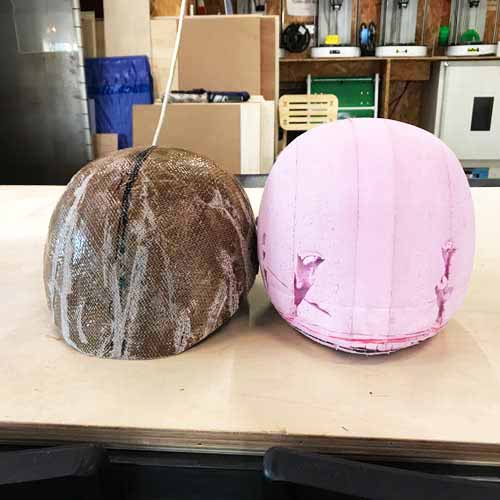
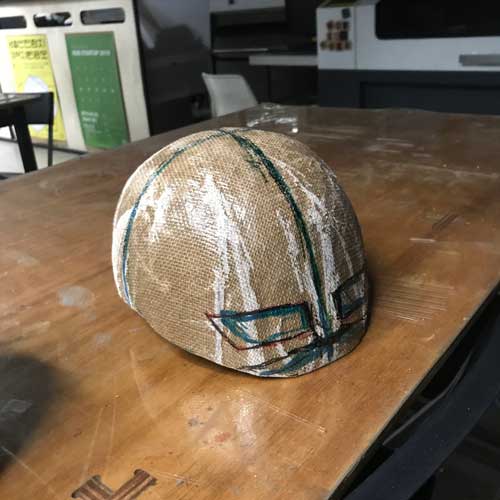
What will happen and when??
We learned about spiral developement from the beginning.
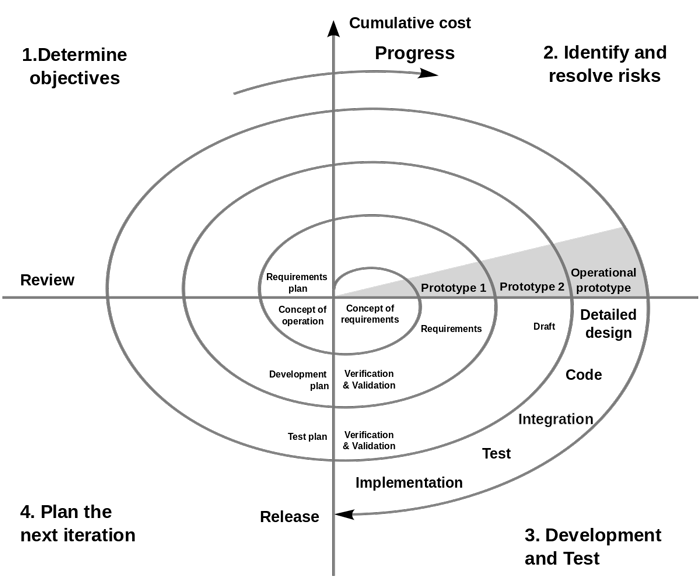
(picture from wikipedia)
I'm the type of person that focuses too much on one thing obssessively,which stops me from being efficient all the time.
So I put work all on one table and work a little bit everywhere at the same time.
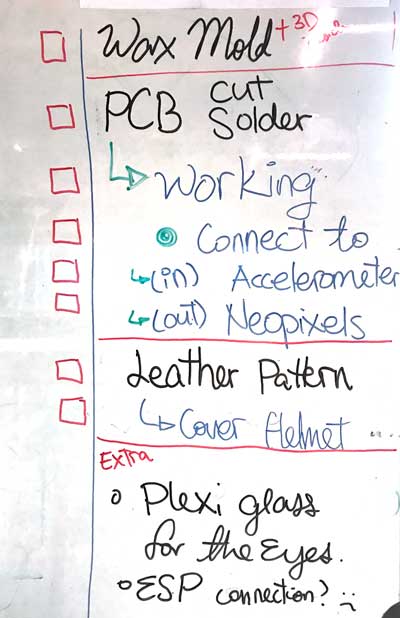
My checklist I decided to use molding and casting the spikes as a kind of a timing check point.
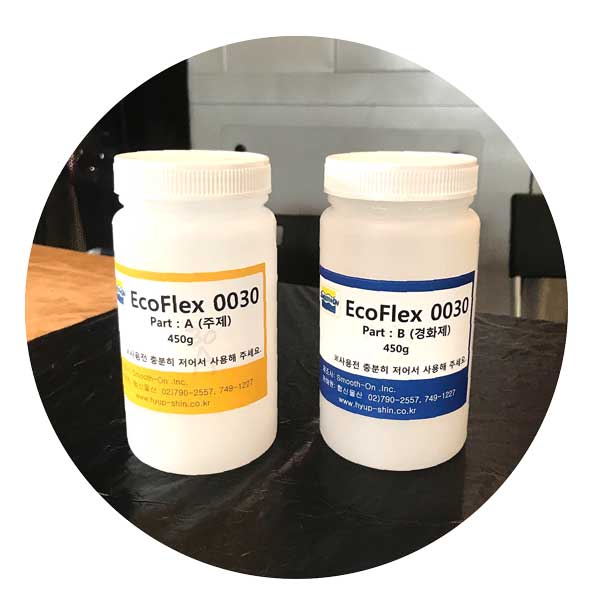
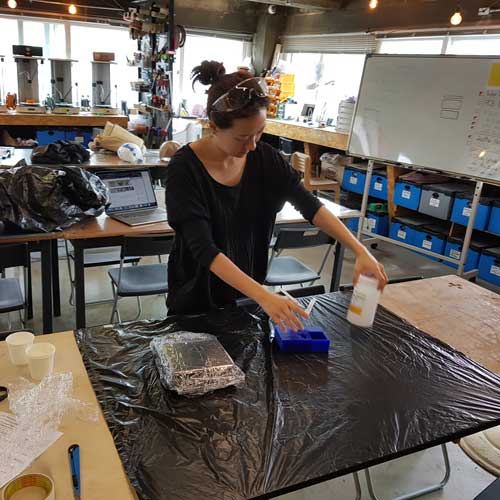
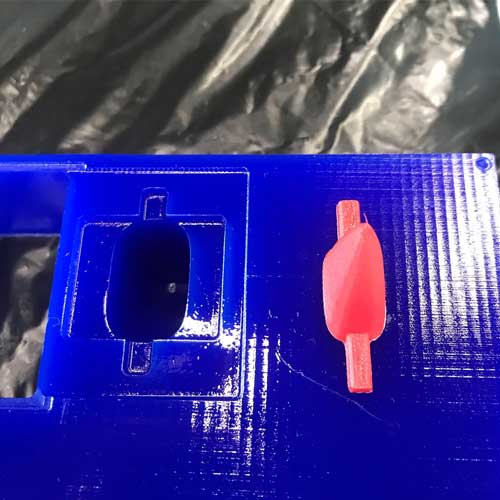
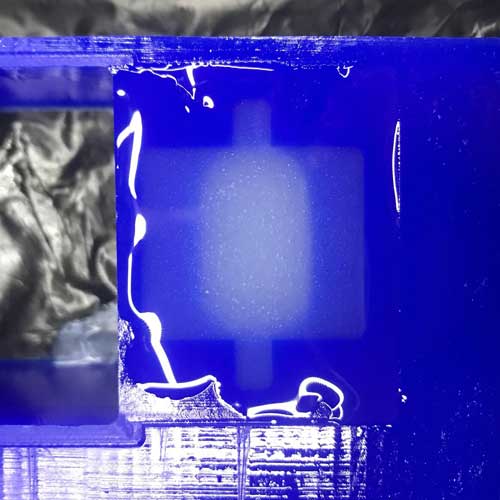
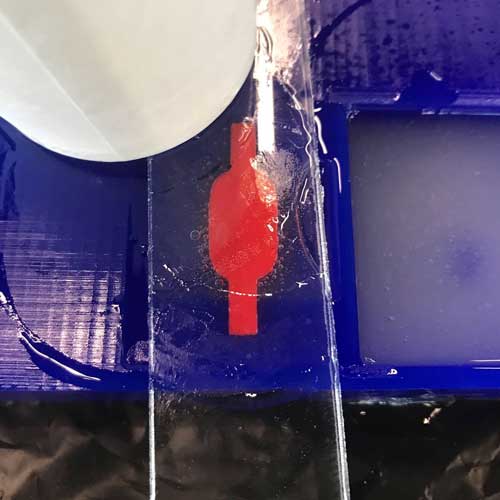
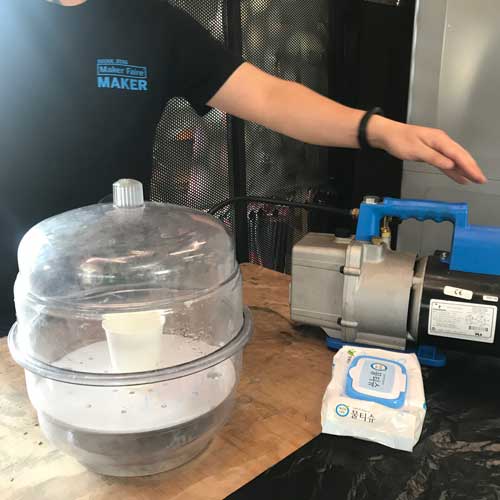
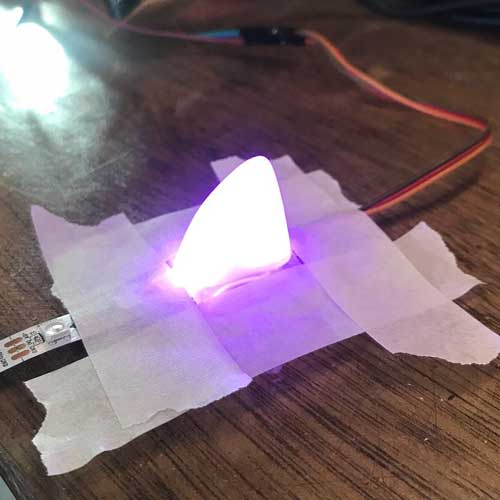
With Spike 1
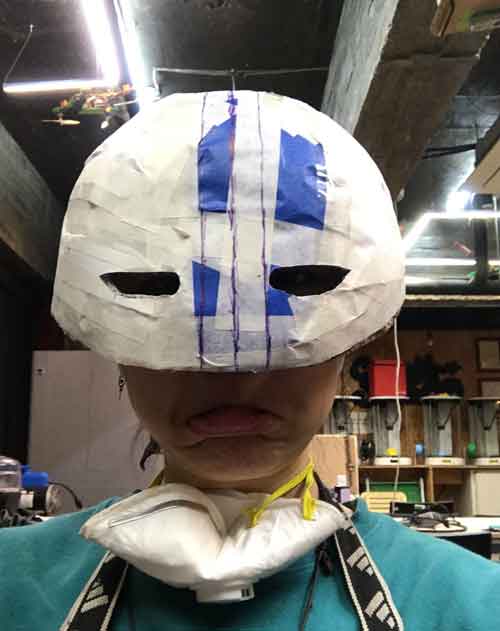
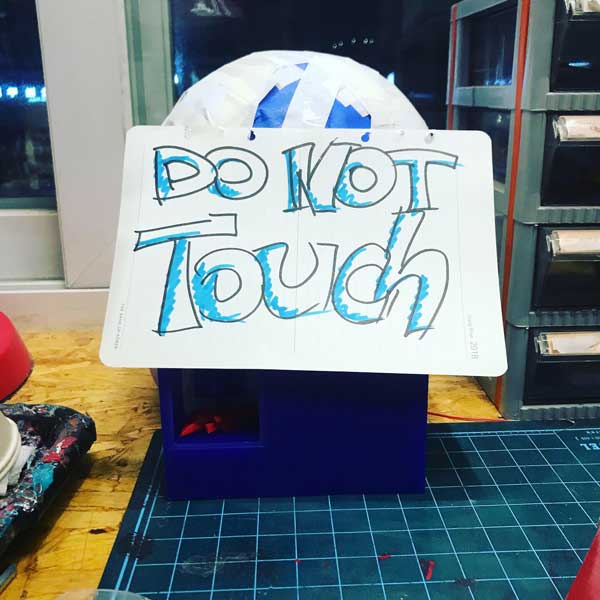
then covered it with tape to prepare to make a pattern for leather work.
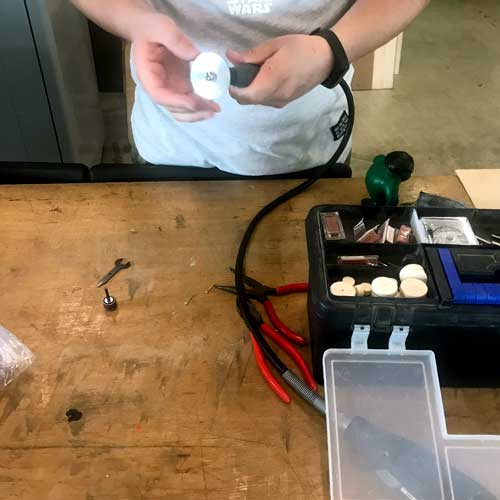
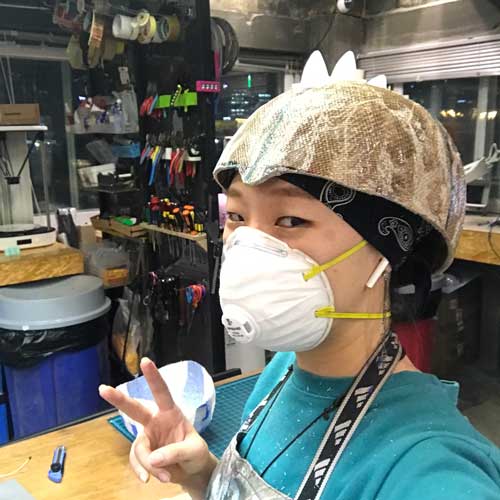
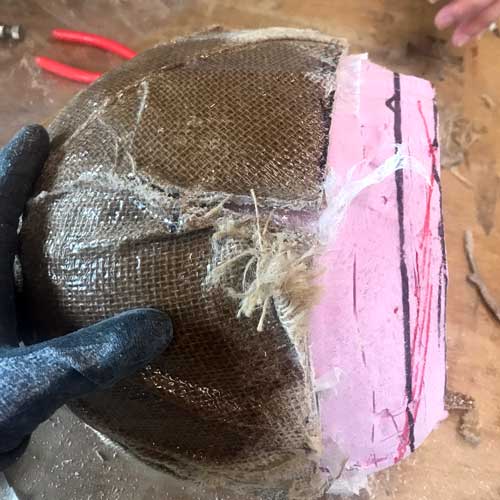
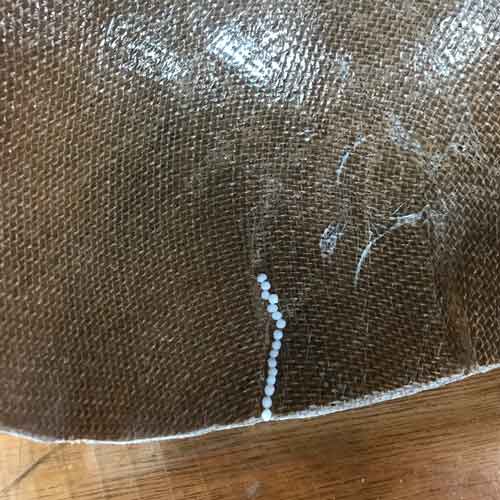
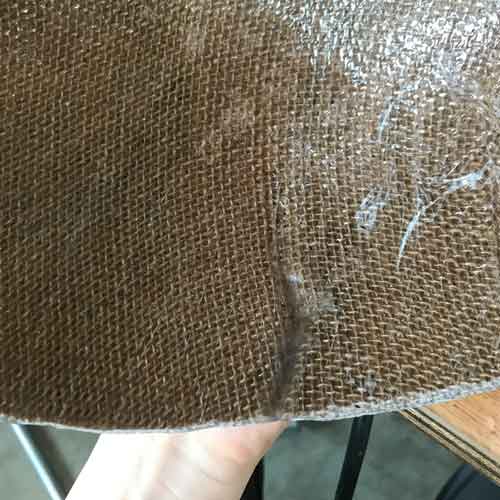
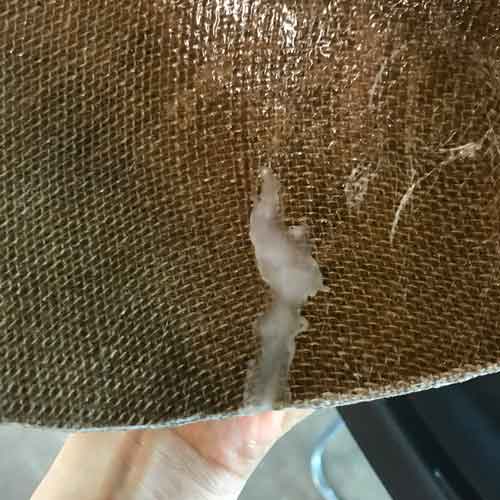
With Spike 2
With a spike done, I needed to design my board so that everything will work together.
I connected my accelerometer to my fabkit with neopixel as output, and worked from there. At first, I thought about using the tap demo from LIS3DH library sketch with my neopixels,
but it seemed too unreliable so I decided to work with the tilts.
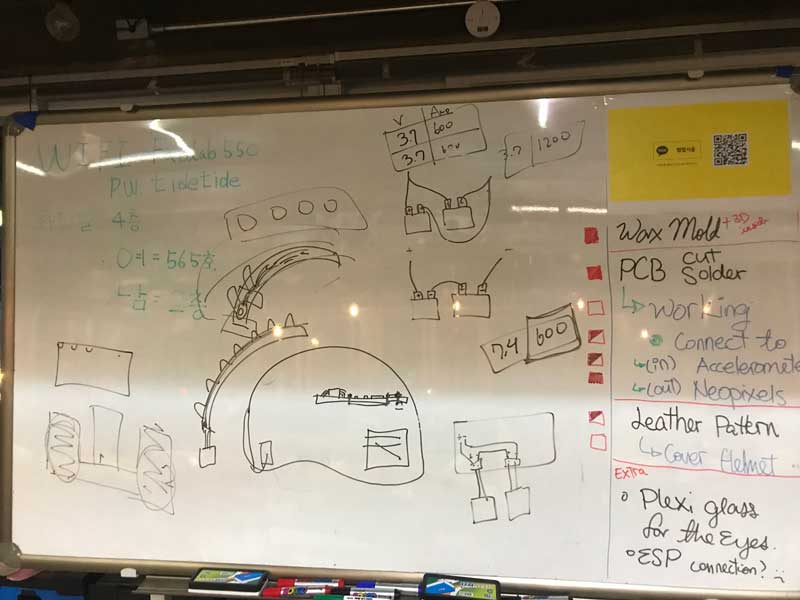
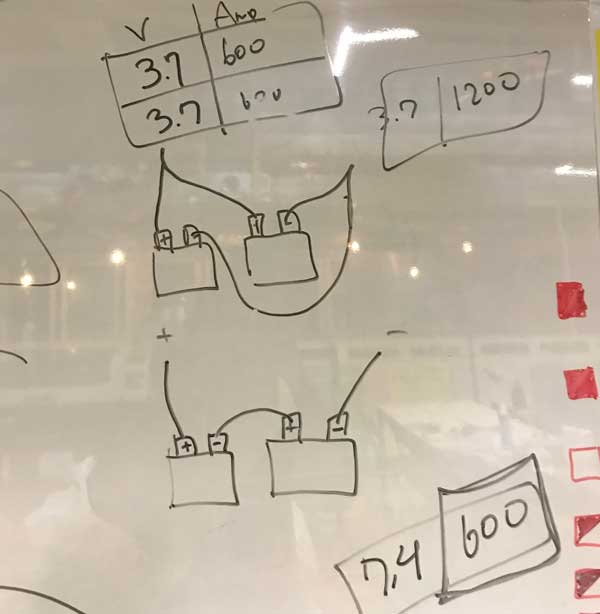
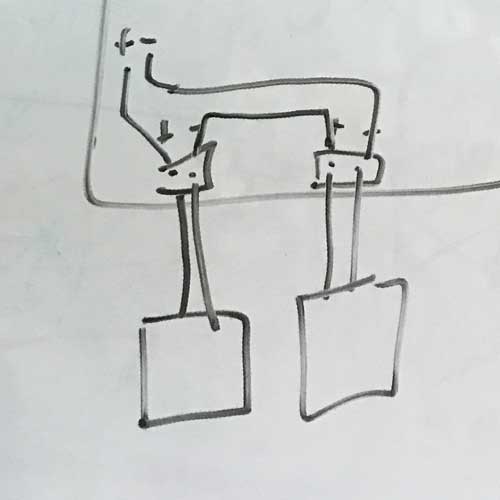
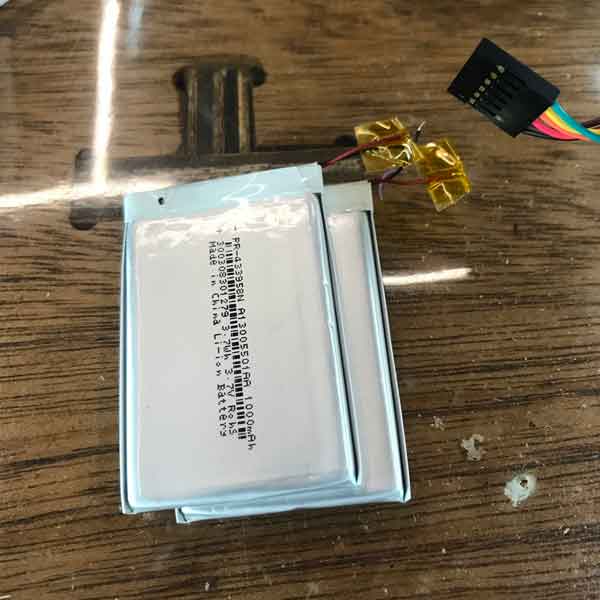
With Spike 3,4
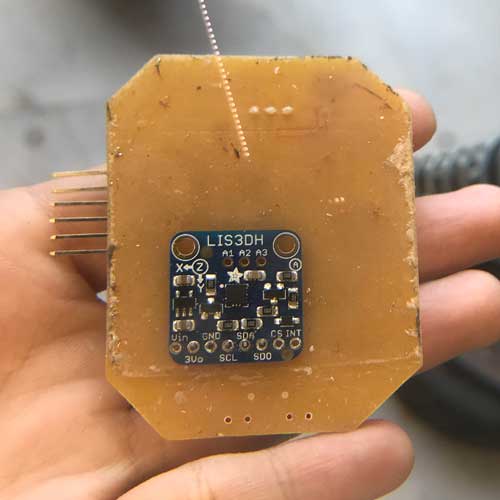
when I install it in the helmet, it would be right side up.
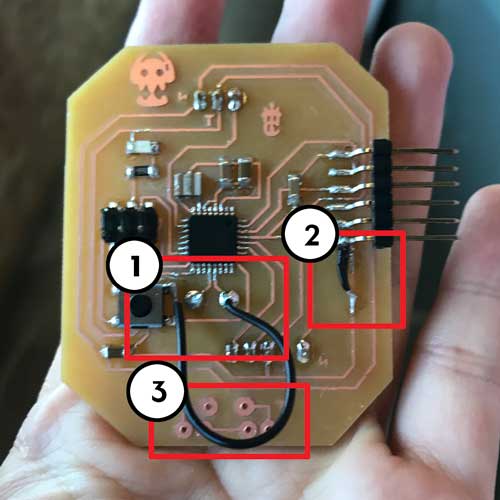
- The ground was not connected everywhere
- FTDI pins are my worst enemy
- I was going to put the jumper cable under the pcb but now the accelerometer is there.
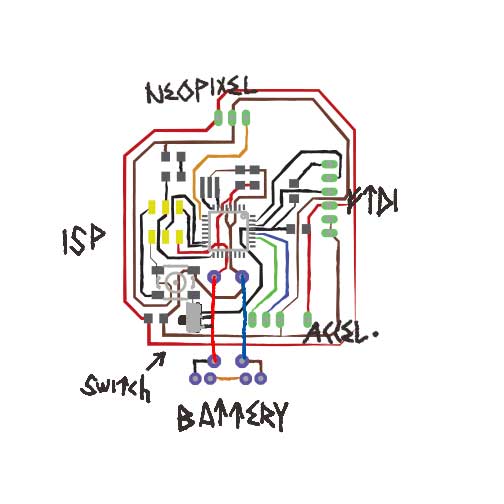
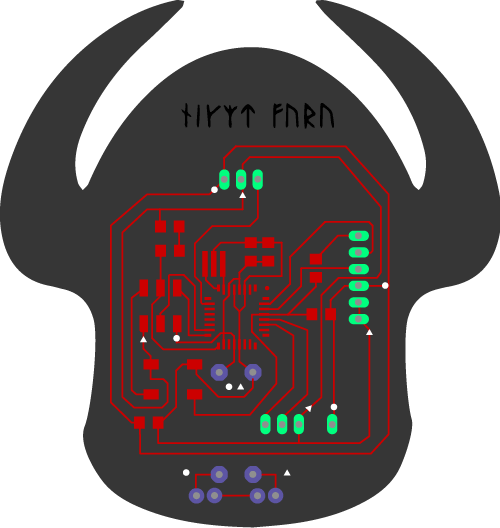
I had burned my accelerometer board, and we did not have another one.
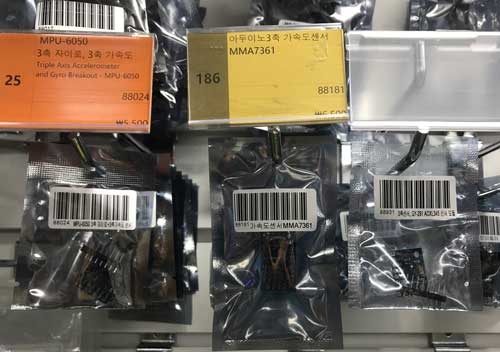
which means I had to order it online...
With Spike 5
It was the day for the first presentations!
Since I couldn't work on my PCB until the accelerometer gets to the lab,I went back to working with my hands.
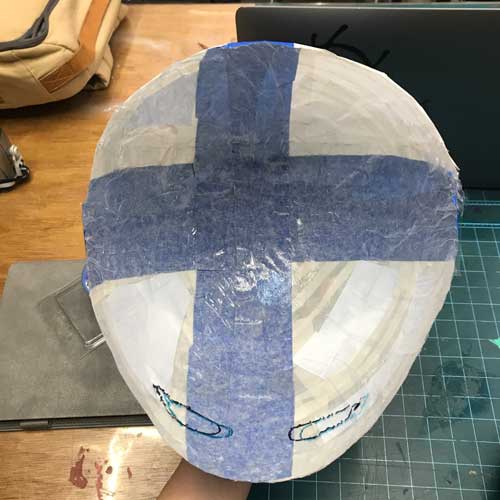
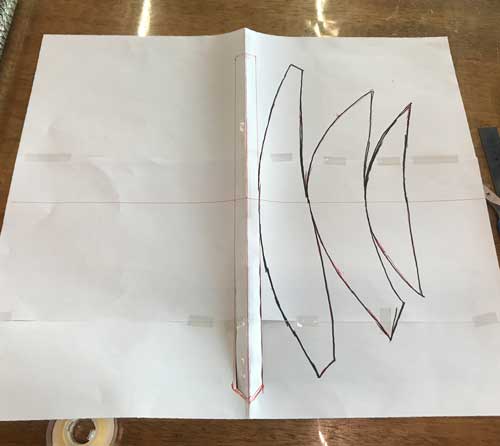
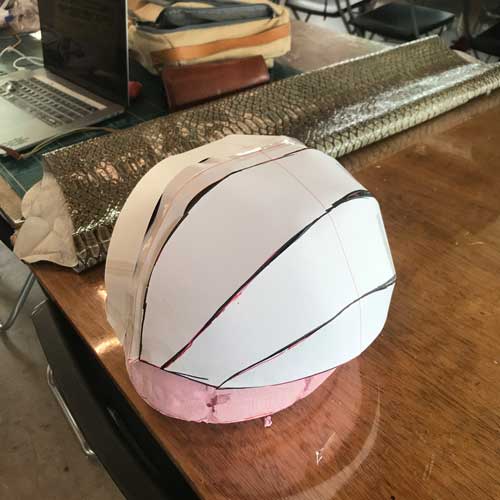
and tried it on for size. It fit perfectly!!!
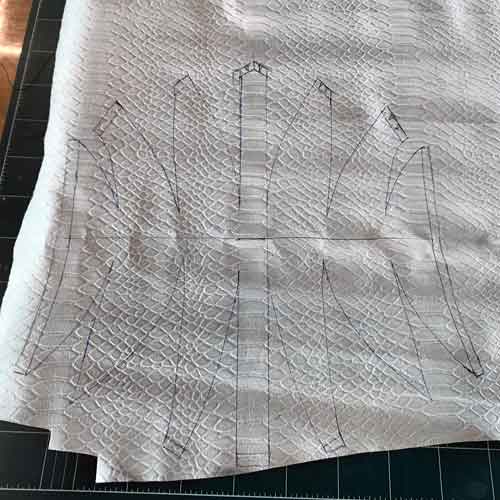
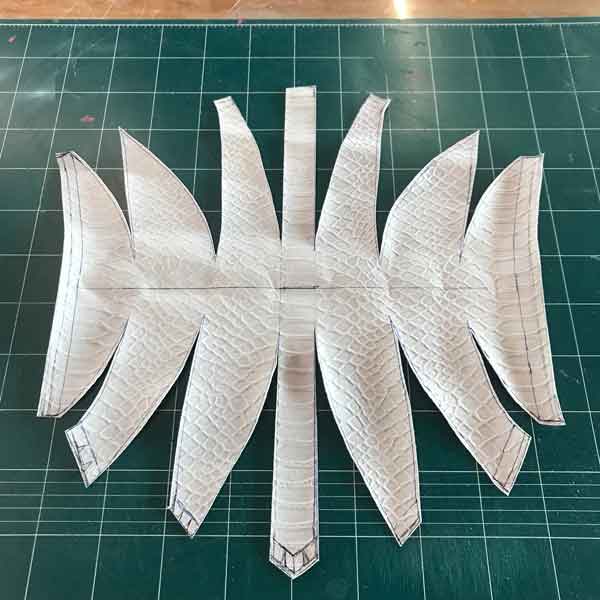
The sides were lengthened to make sure that I had enough leather to cover the bottom.
I used my leather tools to makes holes for sewing.
and attached one side for the clip button.
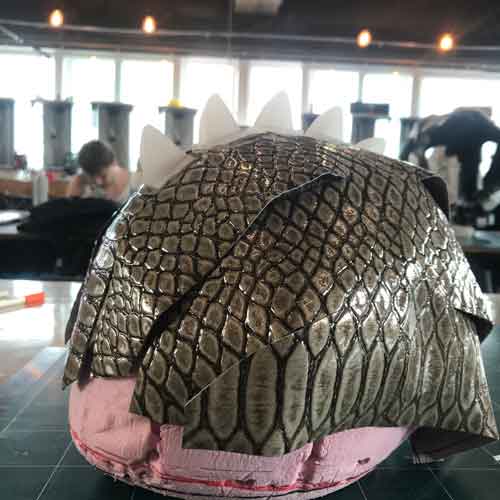
With Spike 6
It was time for the first presentations to start!
My leather was ready, but I had lost my needles!!!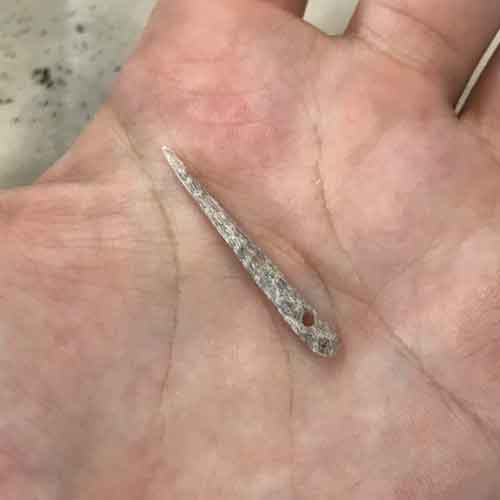
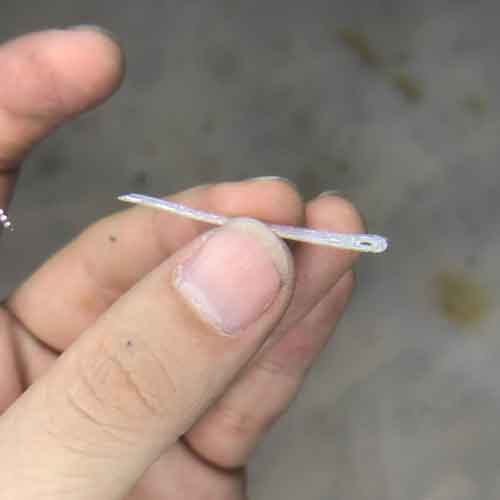
the leather was soft enough for me to not have much problems with them.
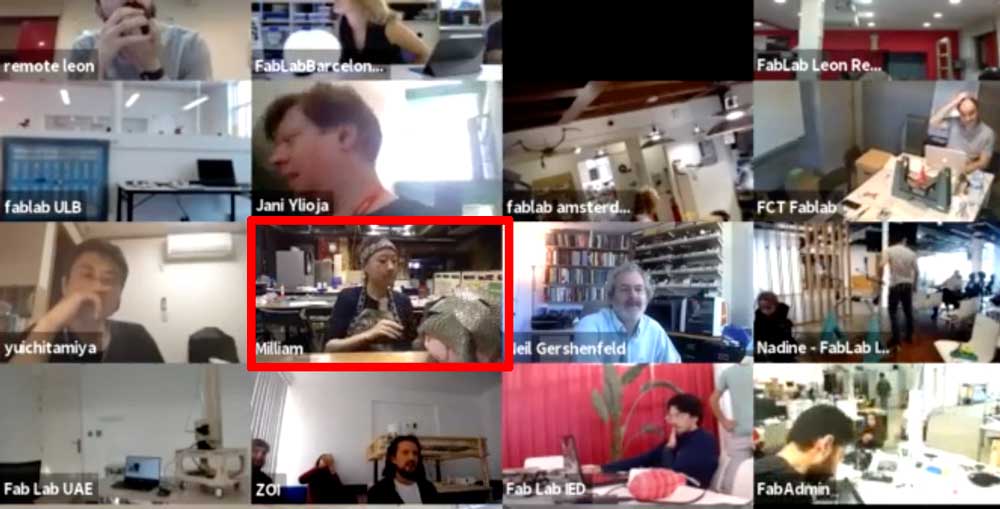
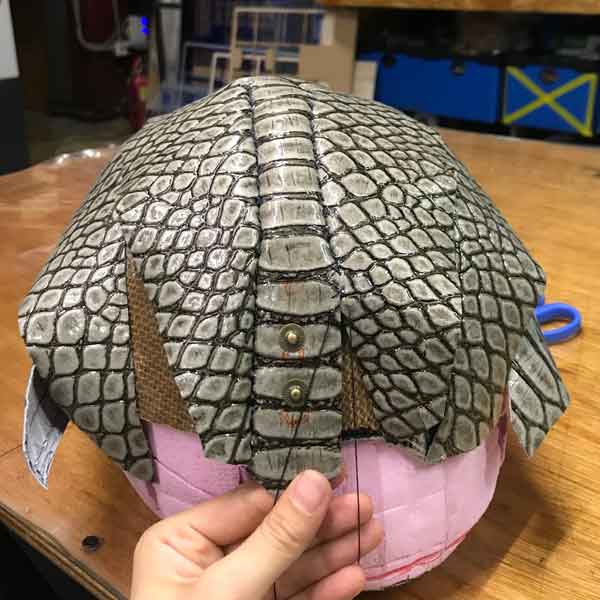
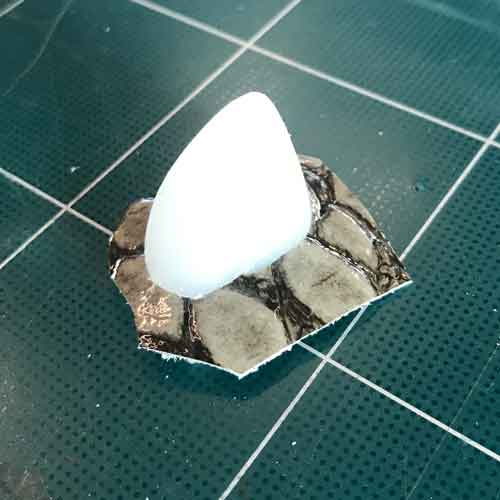
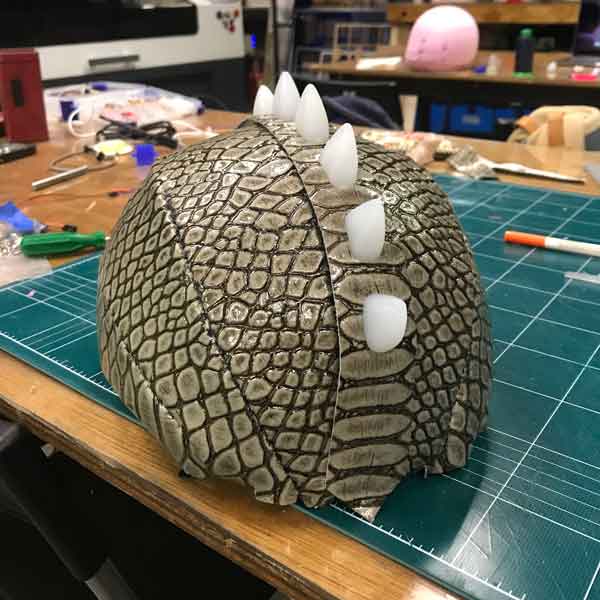
With Spike 7
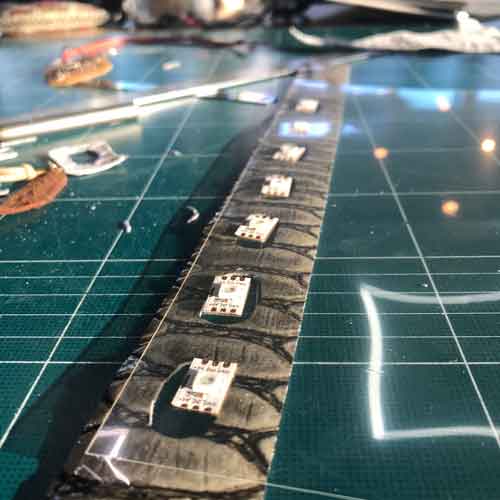
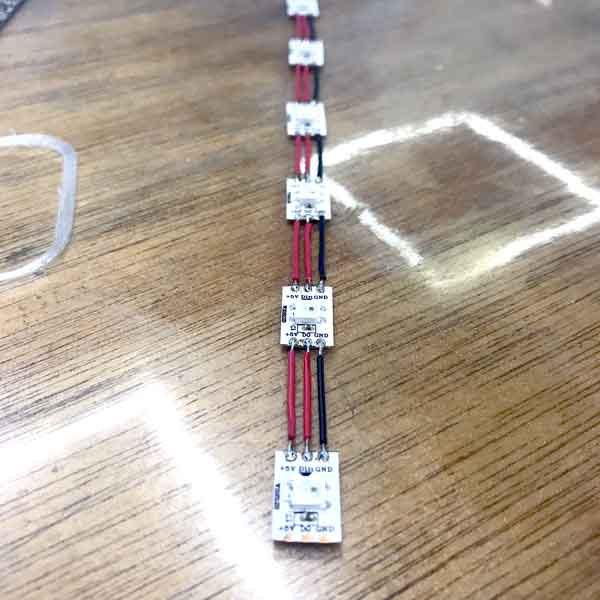
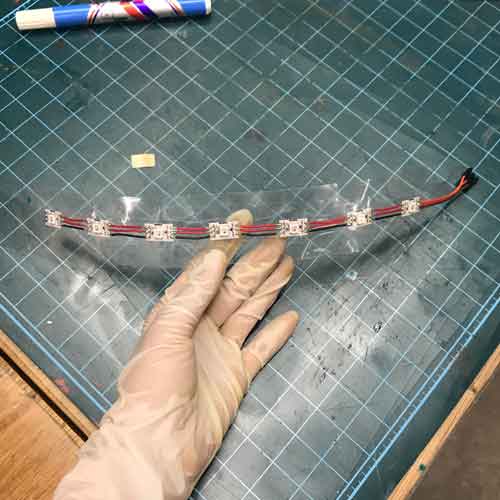
Gloves were worn becaus I have sweaty hands, and I wanted clean lamination
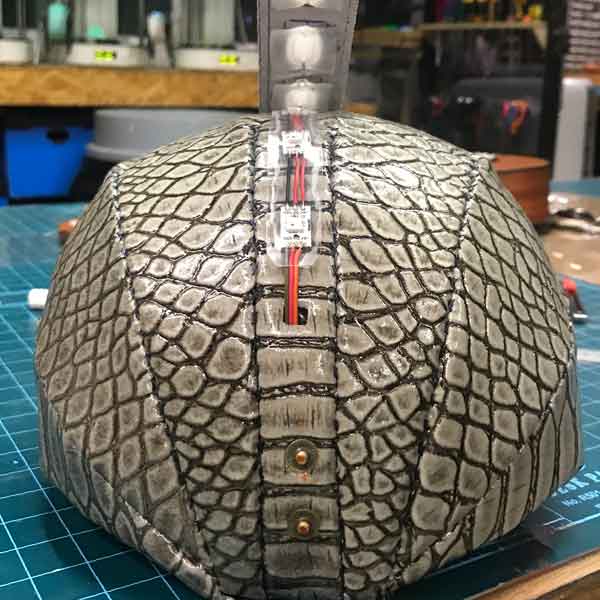
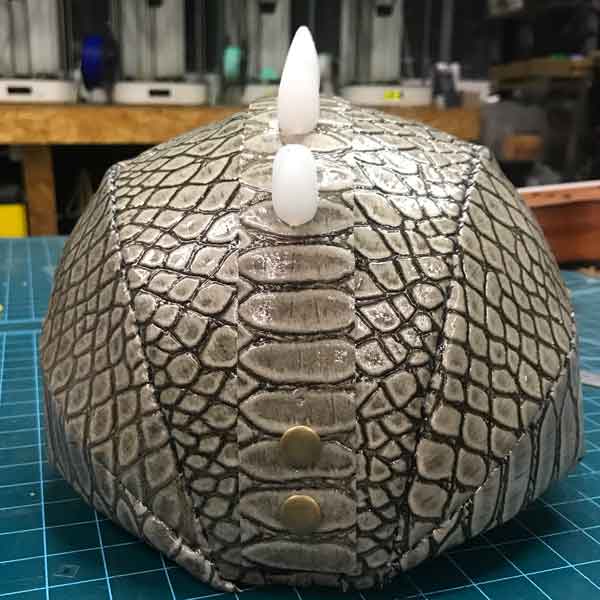
The Accelerometer came!!!
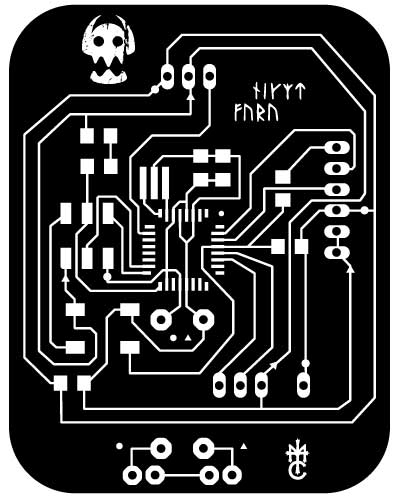
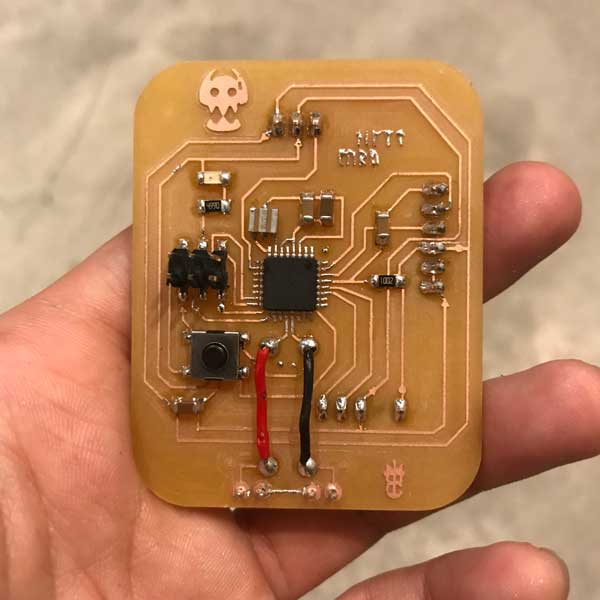
I forgot to factor in an [ON] switch.
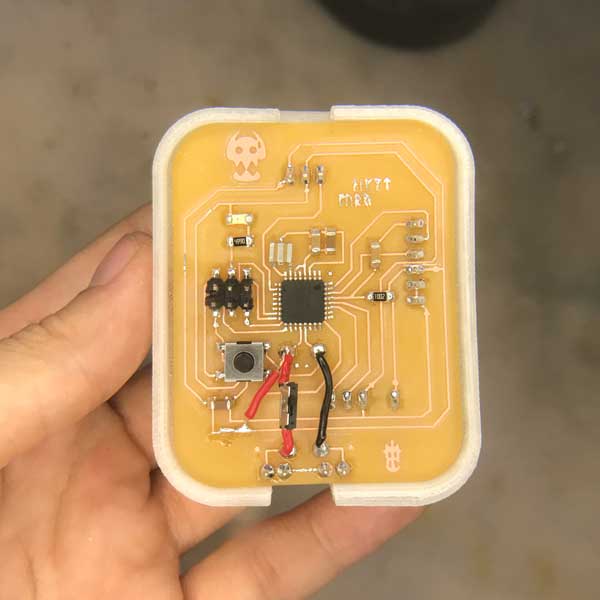
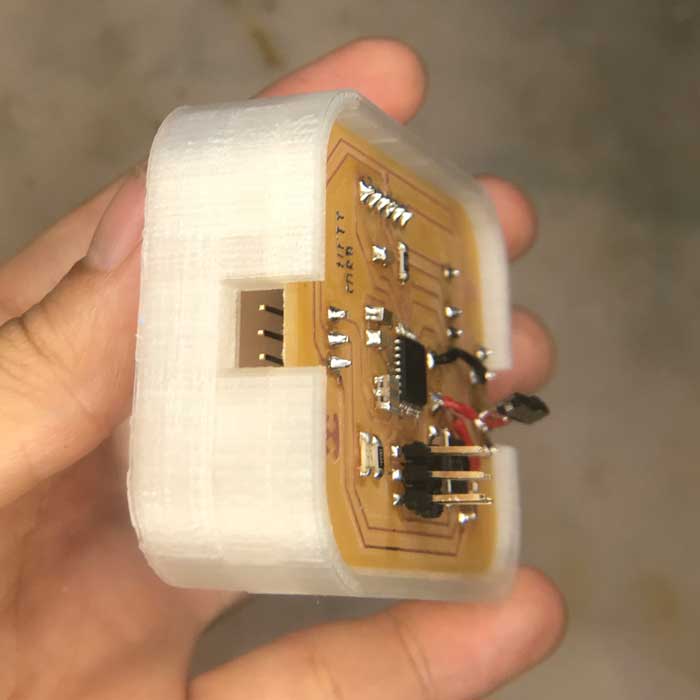
programming
that the neopixel actually works by showing when it turns on.