Week 12:: Composites
Assignments:
design and make a 3D mold (~ft2), and produce a fiber composite part in it
To perform the tasks in this this week I decided to use the following software:
- Photoshop CS5: For the layout and retouching of images for the web.
- Rhinoceros: To design the model and generate .stl files
- Aspire: To generate .crv3d files for CnC Machine
- Notepad++: For edit/create this web
Design and prepare
This week I decided to create an element for composites for my final project is a circular lamp to illuminate a cot with a dim light shaped moon and stars. For 3D design I used Rhinoceros, I have placed on a circular platform 19mm x 30mm a small moon and four stars.
Rhinoceros: Design
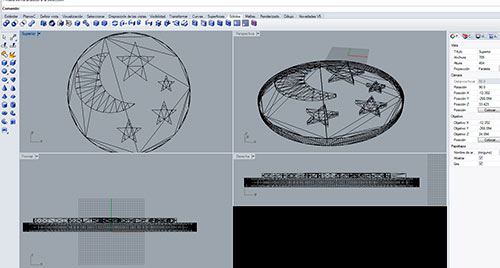
Rhinoceros: Render

After finishing the design I exported the result to .stl format to import from Aspire and create strategies for 3D cutting CNC machine (CAM 500). I created two routes, one for roughing and finishing another. The thickness of the foam core is 29mm, the lamp base is 19mm and 10mm reliefs. The drill used is 6mm, especially for milling foams. Export the two strategies .tap format and send them to the CNC machine as work order separately.
I milled with a 6mm tool special for foam (FCL16L 1L 6MM ). And for this kind of foam the speed could be the highest 24.000 rpm.
Aspire
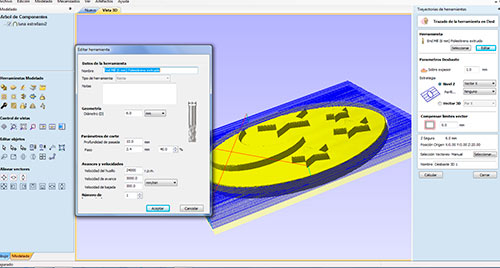
CNC 1
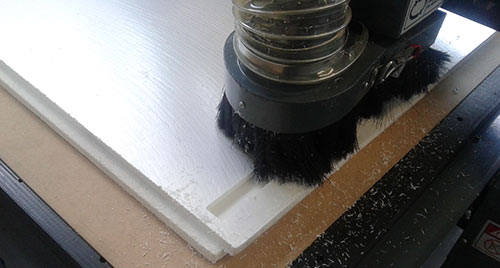
The mold is ready, now is the turn of the materials that will be used by a resin part, I opted for acrylic resin, specifically:
PLASTICRETE
P-CAST A02/P-FILLER ART (www.compositesshop.com)
50:100 by weight
As mesh material I will use burlap, I managed two colors for this item, black and yellow. It is a rigid and little flexible fabric.
PLASTICRETE
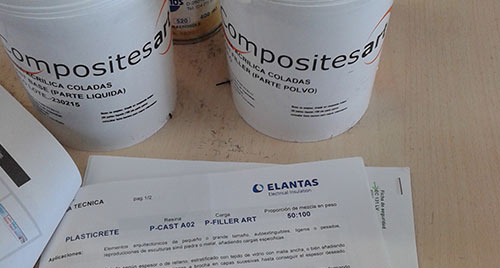
Burlap
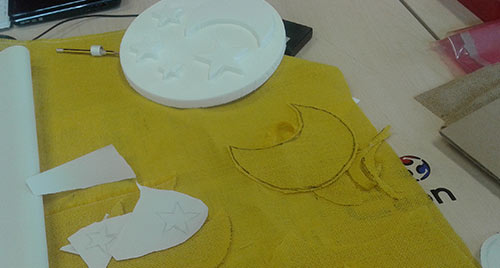
I tried to cut into the fabric forms for mold, but the burlap is difficult to handle, so I decided to do a test: cut shapes using laser cutting. (Thanks to Szilard for help with Rhinoceros). I used the following parameters:
- speed: 65%
- power: 75%
- frequency: 5000.
Laser Cut: Burlap from Carlos Cano on Vimeo.
fabric pieces:
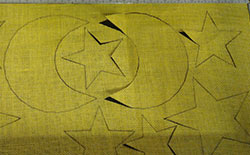
mixing components:
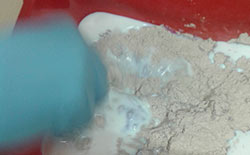
applying demolding:
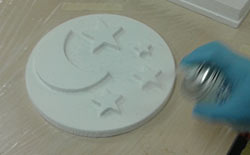
applying resin:
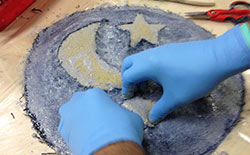
When I have all the material ready conducted the mixture of acrylic components to complete the work, so far so good, but when I try to apply the burlap soaked in the mixture over the mold does not fit, it is very difficult to work with this type of material not suited to the shape of the mold, it is too thick and stiff, I applied two layers of burlap. I can only hope that in the vacuum bag fits better ways. After waiting 15 hours unfortunately the result is not at all expected. I think it's a horrible final work. I made several mistakes in the final phase of work, I think that a single layer of burlap is enough, I have not applied enough acrylic resin, a type of thin and pliable fabric may be necessary. I think burlap is a good material for smooth surfaces, in my case, the stars and the moon have very irregular measures.
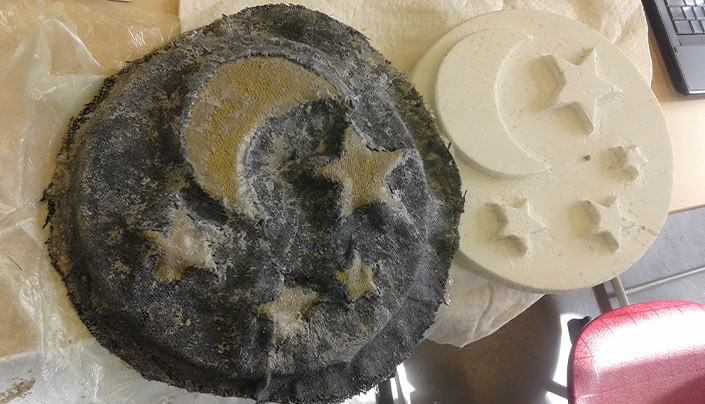
Files: