Group Assignment
Review the safety data sheets for each of your molding and casting materials, then make and compare test casts with each of them.
Individual Assignment
Design a mold around the stock and tooling that you'll be using, mill it (rough cut + (at least) three-axis finish cut), and use it to cast parts.
Individual Assignment
Designing the mold
To design the mold I will be using two softwares. The mold will be apart of Beirut's topography extracted using SketchUp and imported into Fusion 360 to continue designing the mold and creating the Gcodes for milling.
SketchUp
Fusion 360
First I inserted the mesh which is the terrain.
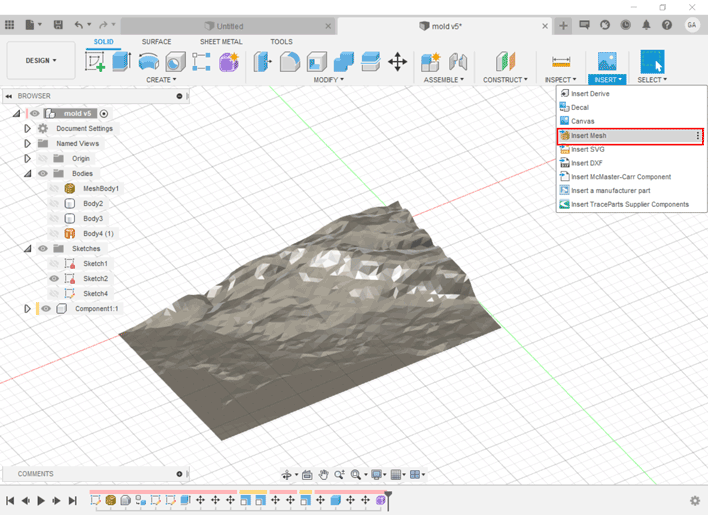
Second I will draw the box which represents the silicone mold.
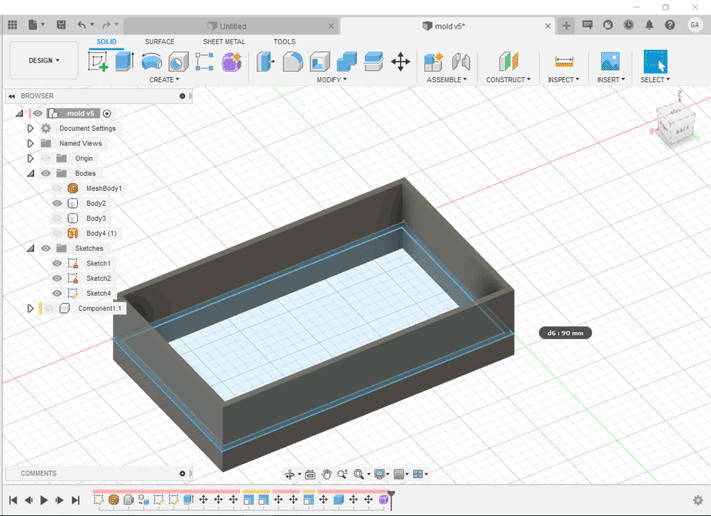
The silicone mold will have the dimensions of the modeling wax stock 150x90x36 mm
At the end of the terrain I created a rectangle with filleted edges.
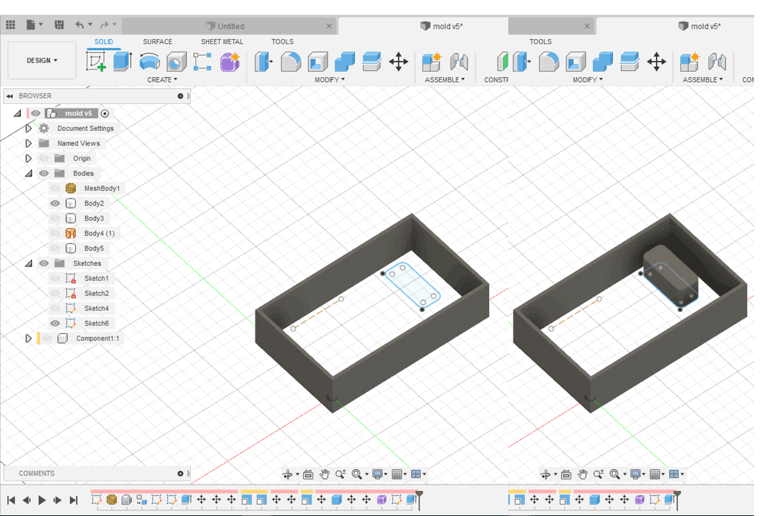
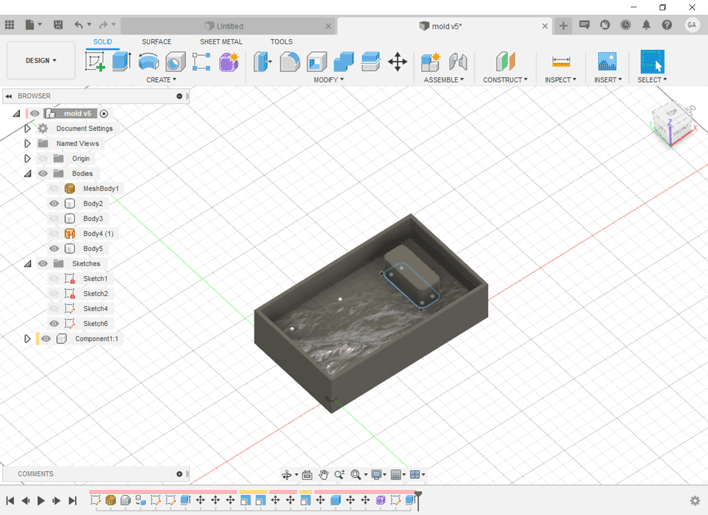
Preparing the Gcodes
In Fusion 360 we will change the workspace from Design into Manufacture in order to start creating the Gcodes for milling.
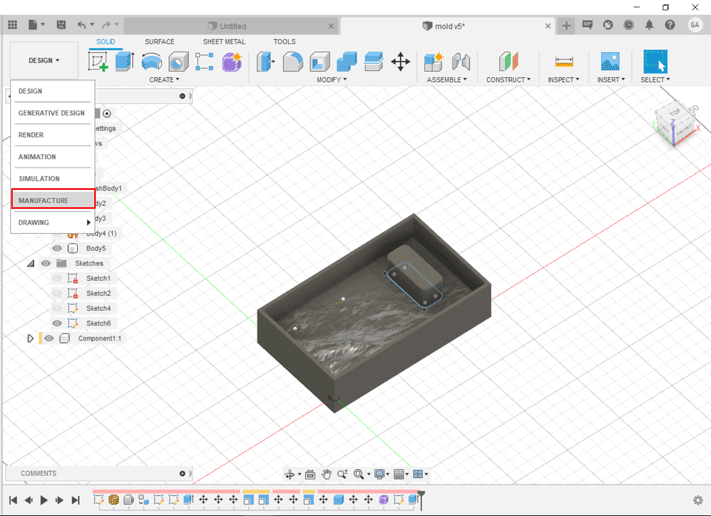
First in the setup section we have to create a new setup.
Right click to edit it we will change the work coordinates system and the stock dimensions.
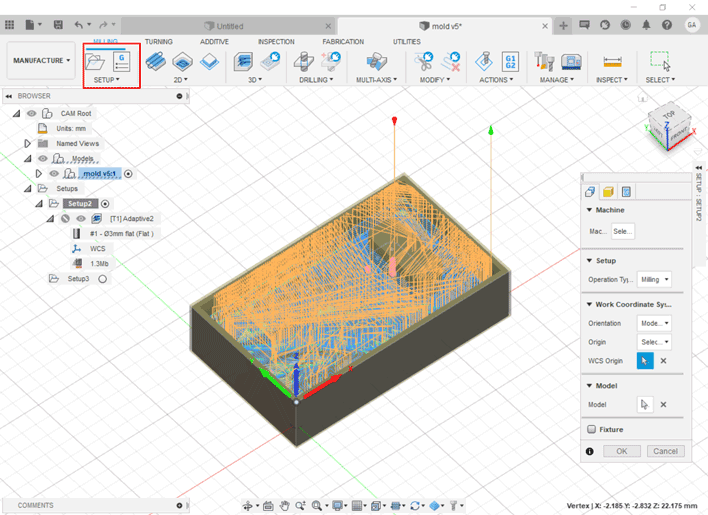
Then after checking these settings we will move into choosing the operation. In 3D we will choose Adaptive Clearing.
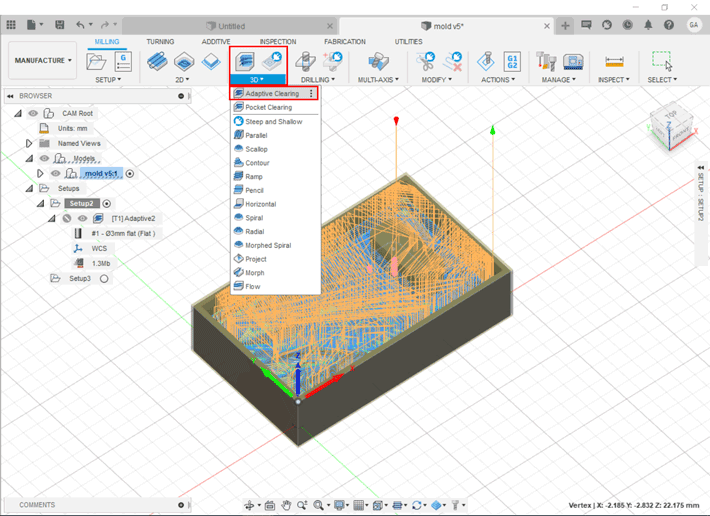
Right click on on Adaptive Clearing panel on the left side and edit. A new panel will open with settings to choose for milling the part.
Tool is endmill 4 mm
Spindle Speed 9000 rpm
Feedrate 1000 mm/min
Stepdown 2 mm per path
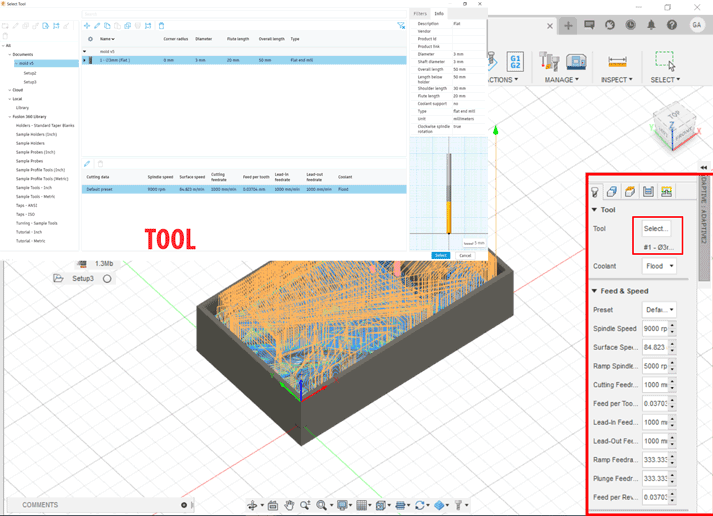
After selecting the needed settings we will click ok.
To visualize the toolpath in Actions we click Generate then in Actions also Simulate to run a simulation of the machining process and how it will appear as a final result.
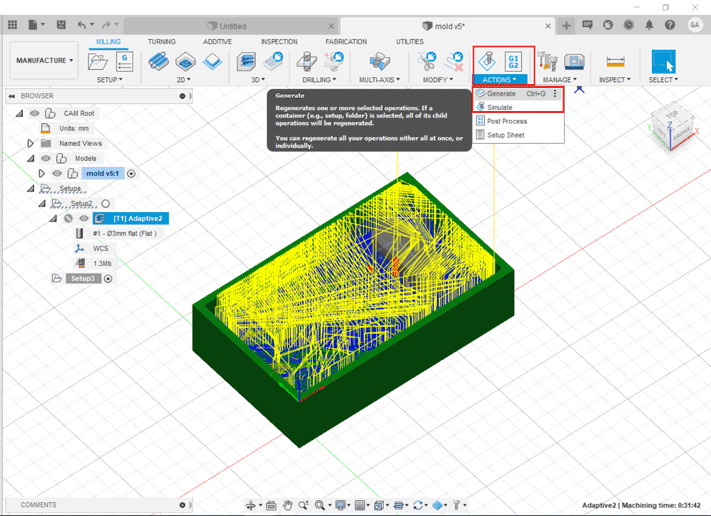
Simulation
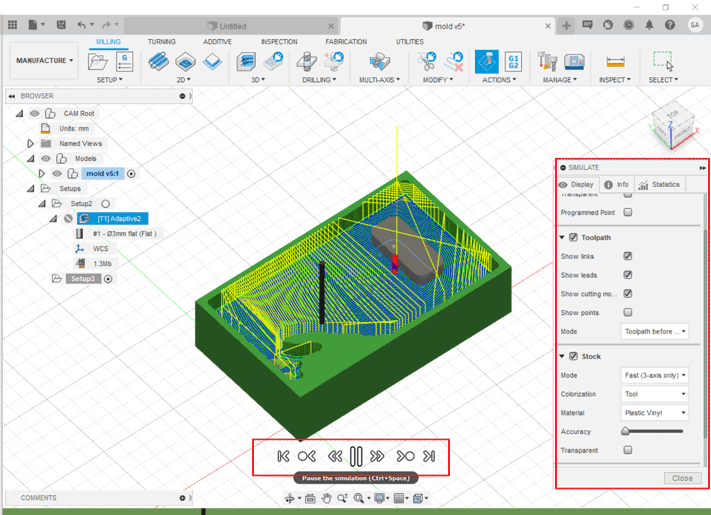
To generate the first code we will go back to Actions and Post Process.
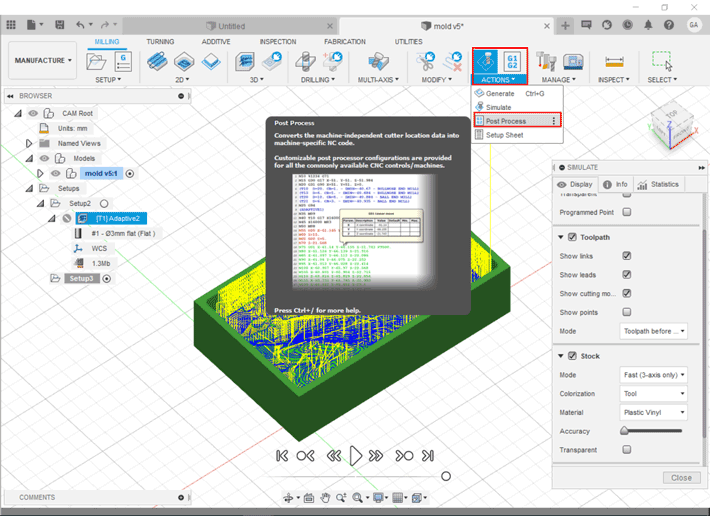
After finishing the first milling the rough milling we have to do some finishing so the part will become smooth.
Again we will click on setup and parallel.
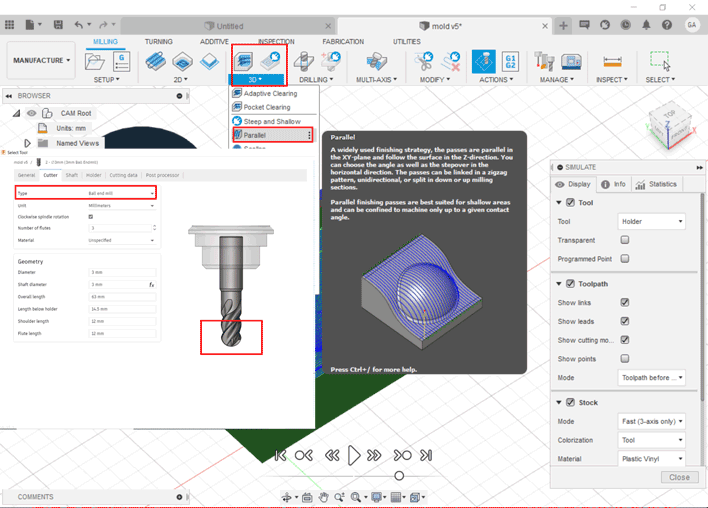
We will use as tool ball endmill 3 mm
Spindle Speed 9000 rpm
Feedrate 1000 mm/min
Stepover distance 1 mm
.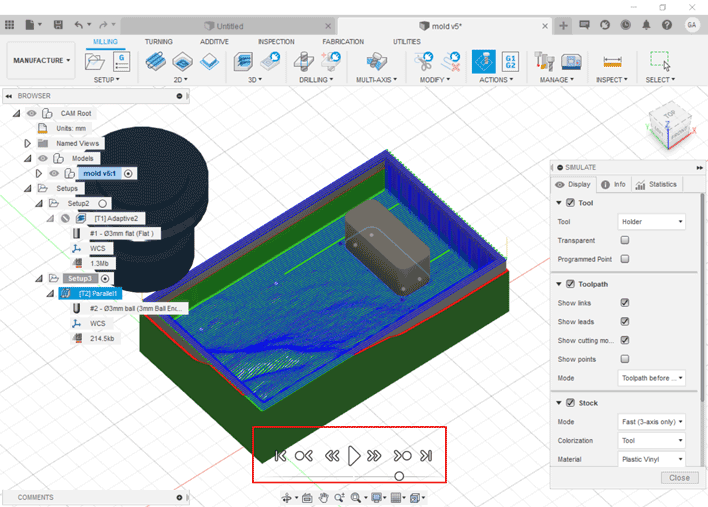
Then simulate to check the everything and generate the second code from Actions and Post Process.
Milling the Mold
I used to mill the modeling wax monoFab SRM-20.
The modeling wax is Ferris Fila-A-Wax.
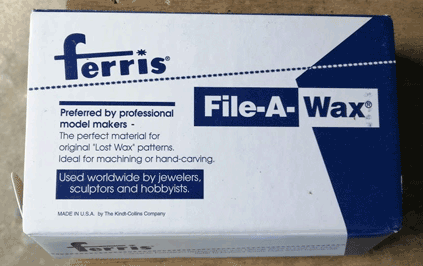
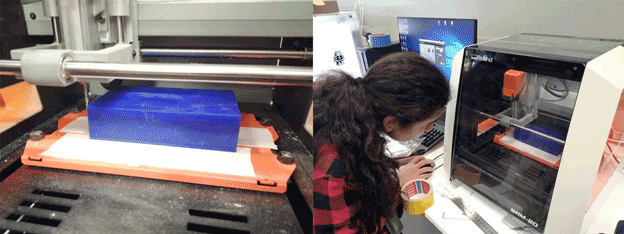
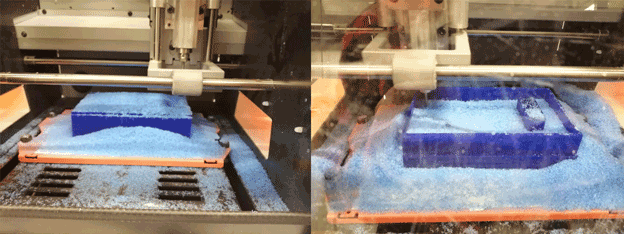
Silicone Mold
I used for the silicone mold GT Silicone Rubber Type: GTSIL-T30.
After reading the technical specification and safety datasheet I poured the silicone into the mold.
Features of this silicone:
- Good tension for easy de-molding.
- High performance in replication.
- Low shrinkage.
Specifications:
- Hardness Shore A range meaning that it will stay flexible when it dries.
- Mixing Ratio is 3% of the hardener added to amount of silicone used.
- Shrinkage 0.30%
- Unmolding time between 2-3 hours.
Safety:
- Always wear mask and gloves may cause drowsiness or dizziness.
- Store in a well-ventilated place. Keep container tightly closed.
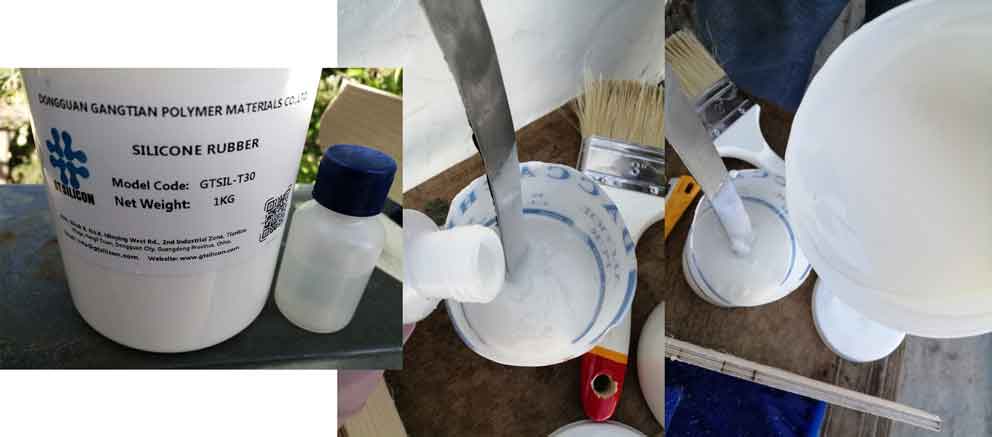
Pouring the Silicone:
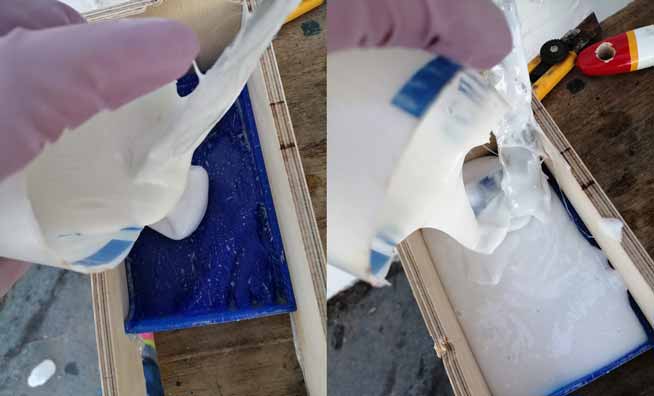
While pouring the silicone I shaked the mold a little bit so that all the areas of the mold have equal amount of silicone without having air bubbles while drying.
Removing the Mold
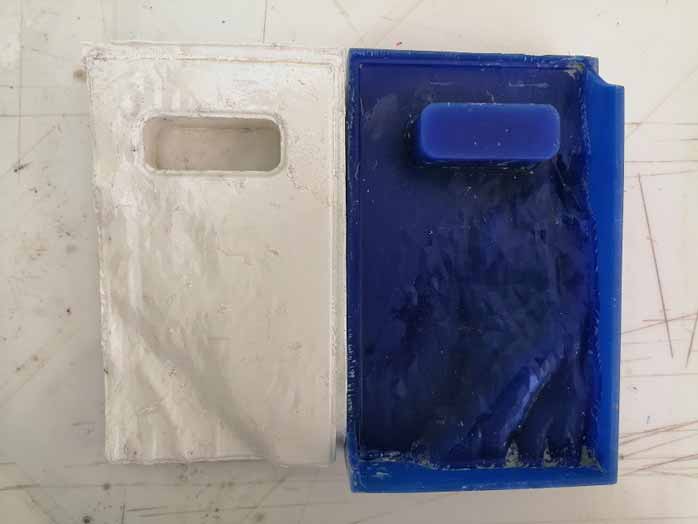
Casting Grey Cement and Resine:
Grey Cement
After the silicone mold dried I tried adding cement to it with moss to create the idea of Breathing or Biological Concrete .
While doing some research I found that breathing concrete is a new idea for buidings to absorb CO2, regulates heat and reduces pollution.
I was interested in trying it.
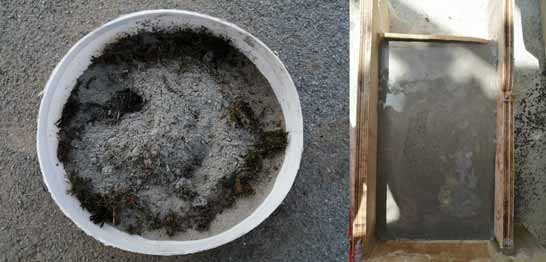
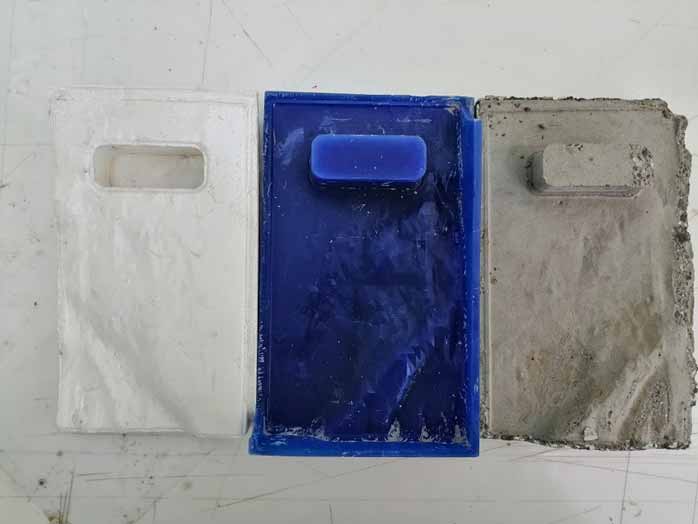
As we can notice that I removed the concrete before drying so on the sides some defects happened.
Mixing Ratio is 10% water added to the grey cement.
- Unmolding time around 12 hours.
Safety:
- Always wear mask and gloves may cause allergy if inhaled or touches the skin.
- Store in a well-ventilated place. Keep container tightly closed from humidity.
Crystal Resine
After the concrete dried I tried another casting material the crystal resin.
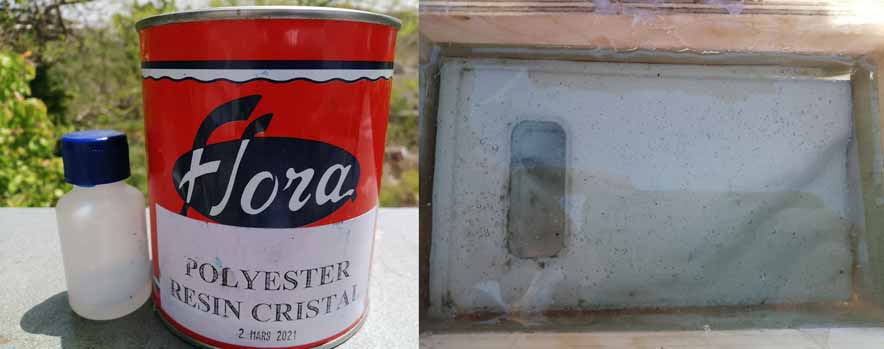
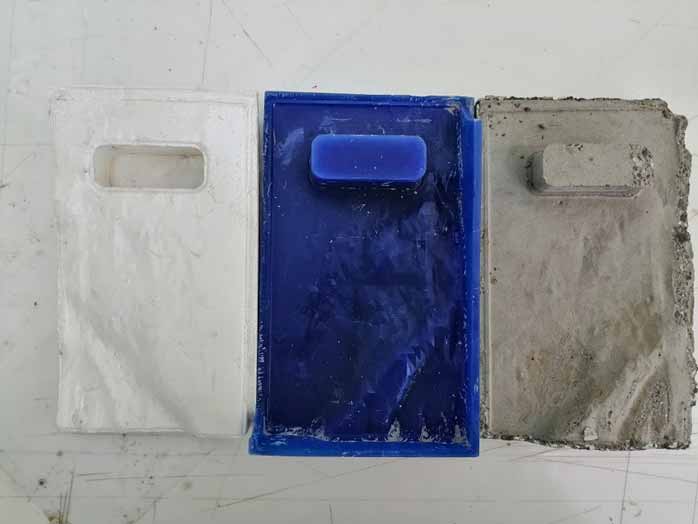
Mixing Ratio 1 part of Crystal Hardener followed by 2 parts of Crystal Resin according to the volume.
- Unmolding time around 12-24 hours varies with the room temperature.
Safety:
- Always wear mask and gloves may cause drowsiness or dizziness if inhaled or allergy if touches the skin.
- Store in a well-ventilated place. Protect from freezing.
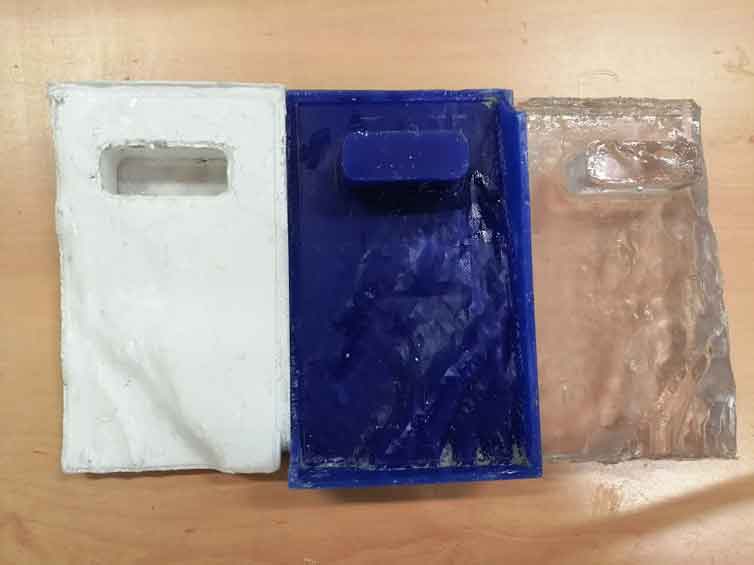
As the results did not end up as I expected and I had several errors when designing the mold I decided to design a new mold.
In the second design I decided to try creating a sample of a wall pattern that later on I can mill on a bigger material and can be used to design a 3D wall.
In the second design I used rhinoceros software to create the 3D surface then I took the dimension of the material I wan to mill on and created the outer box.
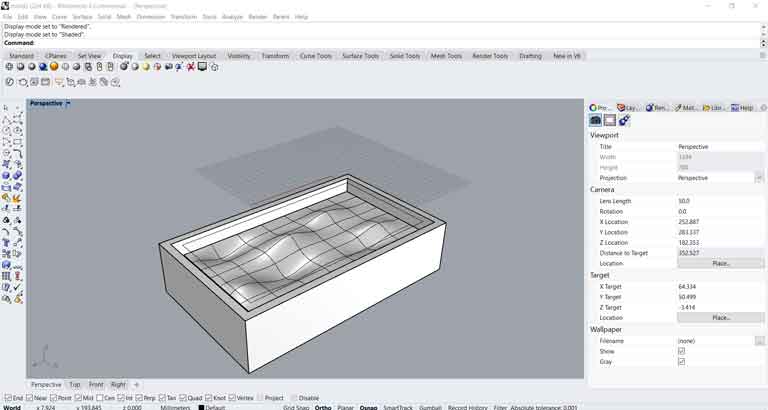
For the mold I decided this time not to use wax block instead I used PU600 High Density Polyurethane Model Board.
To create the Gcode I exported the file as STL format and imported it in the software Modela Player 4 which is connected to the machine monoFab SRM-20.
As a material I chose Sanmodur SS from the list. Sanmodur is a type of chemical wood or modelling boards. It is lightweight and easy to cut.
Below are the setting I used first for the roughing phase then for the finishing phase.
Roughing Phase:
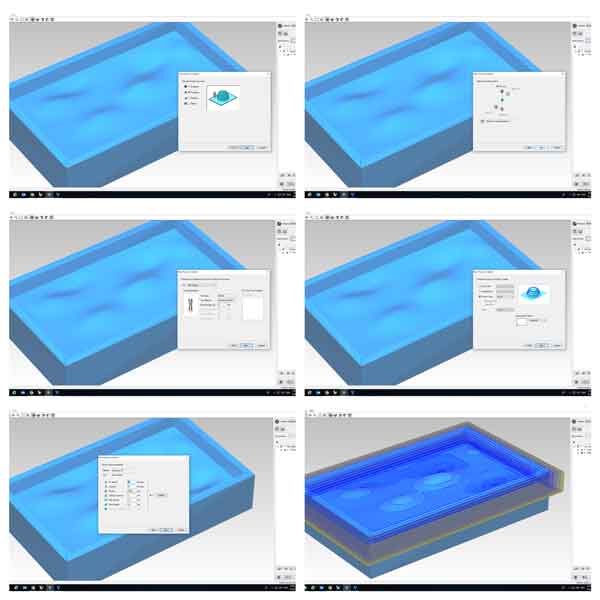
Finishing Phase:
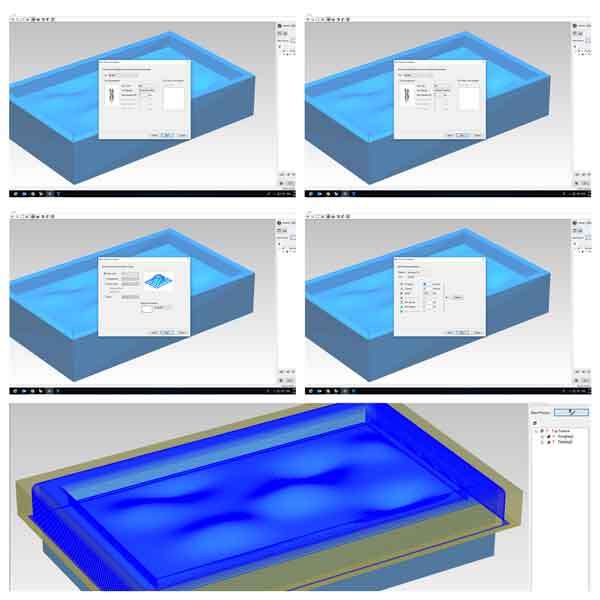
Pouring the Silicone:
As I mentiond previously I used for the silicone mold GT Silicone Rubber Type: GTSIL-T30.
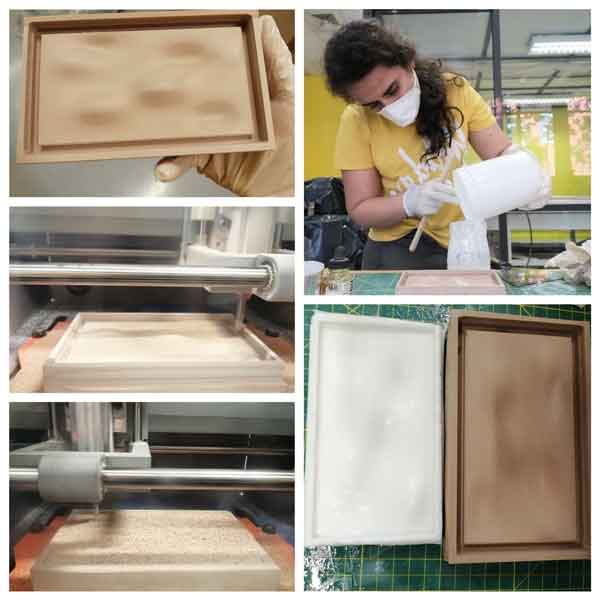
Crystal Resine:

Group Assignment
Here you can find our group assignment LINK
Molding and Casting
So the objective of this week is to get introduced to the Molding and Casting procedure used mainly to produce a certain shape multiple times using various material.
Molding and Casting is usually used in the Plastics industry and automotive industry, where the same object is mass produced. In the plastic manufacturing industry, injection molding is usually used to produce the plastic products. The procedure is also used when we want to produce shapes using other material such as wax, foam, rubber, silicone and resin. Molding and Casting is also used to produce sand casted metalic parts such as aluminum, steel, lead and much more.
In this section, we will learn on how to prepare a Mold and use it to Cast a certain object.
What is Molding and Casting?
Molding or moulding is the process of manufacturing by shaping liquid or pliable raw material using a rigid frame called a mold or matrix.This itself may have been made using a pattern or model of the final object. Casting is a manufacturing process in which a liquid material is usually poured into a mold, which contains a hollow cavity of the desired shape, and then allowed to solidify. The solidified part is also known as a casting, which is ejected or broken out of the mold to complete the process.
Machines Used
The main machine used in this week's assignment is the Desktop CNC Machine.
The Roland MDX-40 and SRM-20 was used for cnc milling the wax block that what then used for pouring silicone in it.
Testing Molding and Casting Material
The assignment this week was to review the safety data sheets for each of your molding and casting materials, then make and compare test casts with each of them.
The following are the material we used in this week's assignment.
Molding Material
Molding Material 1 - Alumilite - Amazing Mold Rubber
Molding Material 2 - Alumilite - High Strength 2
Casting Material
Casting Material 1 - Alumilite - Amazing Casting Resin - White
Casting Material 2 - Alumilite - Amazing Clear Cast
Casting Material 3 - Aristocrat - Liquid Glass
Casting Material 4 - PolyPol - 1003
Coloring Material - Alumilite Coloring Dyes, Various Colors
Test 1 - Testing Various Molding Material
In order to perform this week's assignment, we tried two differnt Molding Material and we compared the technical specification and the results.
The following material were available in the lab and were used during this week's assignment:
Molding Material 1 - Alumilite - Amazing Mold Rubber
Molding Material 2 - Alumilite - High Strength 2
Safety
Concerning Safety, both material had the same safety warnings:
Always use safety products when working with silicone and resin. Always wear gloves, apron, coveralls, boots, chemical goggles.
Mixed High Strength rubber will absorb into porous materials and may stain! Avoid clothing, carpet, upholstery, and any other porous materials which will stain and will not come out. Mold making and casting is best done in a designated area such as a basement, garage, or hobby room with adequate air movement or ventilation. Cover any surfaces including floors with plastic sheeting, or plywood to prevent damage from spilled resin. To clean up unmixed or still liquid material, use rubbing alcohol on a rag or paper towel to quickly clean and remove. In some instances, such as spills on non-porous surfaces, it's easier to clean up silicone after it's allowed to cure. Then simply peel away and discard.
The following are the safety warning for both material:
- Keep out of reach of children
- Avoid eye and skin contact
- In case of skin contact, wash with soap and water
- Use with ventilation. In case of ill effects, remove to fresh air
- Keep container closed
- Do not take internally
- Do not use for food
A detailed discription of the technical data sheet for both materials is described below.
You can download the data sheet for the material from the following links:
Material 1 - Amazing Mold Rubber
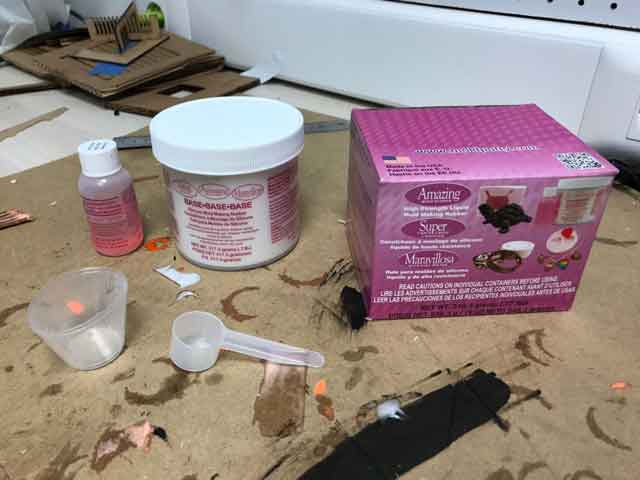
The following is a summary of the data sheet of the Amazing Mold Rubber:
- Color: Pink
- Mix Ratio: 10:1 by WEIGHT
- Open Time: 20-30 mins
- Demold Time: 2-4 hours
- Mixed Viscosity (cps.): 15,000
- Specific Gravity: 1.15
- Shore A Hardness 25
- Linear Shrink 3%
- Tensile Strength 550 psi
- Elongation 500%
- Temperature Range (F) -67 to 395
- Vacuum Required No
Material 2 - High Strength 2
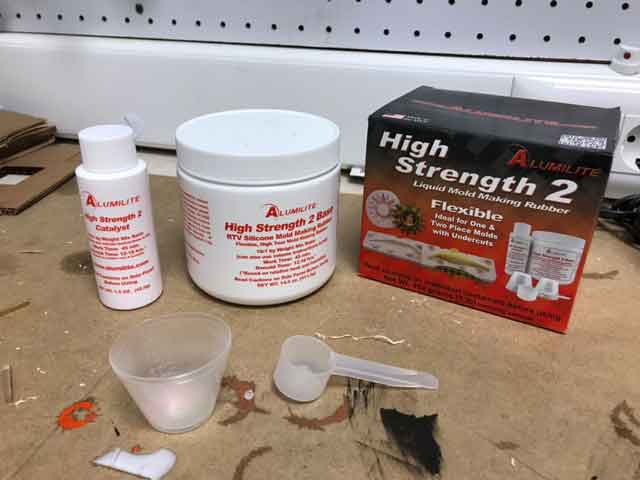
The following is a summary of the data sheet of the High Strength 2.
- Color: Pink
- Mix Ratio: 10:1 by WEIGHT
- Open Time: 45 mins
- Demold Time: 12-18 hours
- Mixed Viscosity (cps.): 18,000
- Specific Gravity: 1.15
- Shore A Hardness 25
- Linear Shrink 3%
- Tensile Strength 550 psi
- Elongation 500%
- Temperature Range (F) -67 to 395
- Vacuum Required No
We can notice that this material takes more time to cure than material 1. However both have almost the same final result which is a high tear strength rubber material.
Test 2 - Testing Various Casting Material
In order to perform this week's assignment, we tried many types of casting material and we compared the technical specification and the results.
The following material were available in the lab and were used during this week's assignment:
Casting Material 1 - Alumilite - Amazing Casting Resin - White
Casting Material 2 - Alumilite - Amazing Clear Cast
Casting Material 3 - Aristocrat - Liquid Glass
Casting Material 4 - PolyPol - 1003
Coloring Material - Alumilite Coloring Dyes, Various Colors
Concerning Safety, all material had the same safety warnings:
Always use safety products when working with resin. Always wear gloves, apron, coveralls, boots, chemical goggles.
Hardener contains a polyamine curing agent. Polymer should be used only by adults or under close supervision by an adult. KEEP OUT OF REACH OF CHILDREN.
The following are the safety warning for all material:
- Fatal or harmful if swallowed
- Keep out of reach of children
- Avoid eye and skin contact.in case of eye contact, flush with water for ten minutes and seek prompt medical attention
- In case of skin contact, wash with soap and water. Resin and hardener are skin irritants and may cause allergic reaction
- AVOID INHALATION – Use in well ventilated areas.. In case of ill effects, remove to fresh air
- Keep container closed
- Do not take internally
- Do not use for food
A detailed discription of the technical data sheet for both materials is described below
You can download the data sheet for the material from the following links:
Casting Material 1 - Alumilite - Amazing Casting Resin - White
Casting Material 2 - Alumilite - Amazing Clear Cast
Casting Material 3 - Aristocrat - Liquid Glass
Casting Material 4 - PolyPol - 1003
Coloring Material - Alumilite Coloring Dyes, Various Colors
Material 1 - Alumilite - Amazing Casting Resin - White
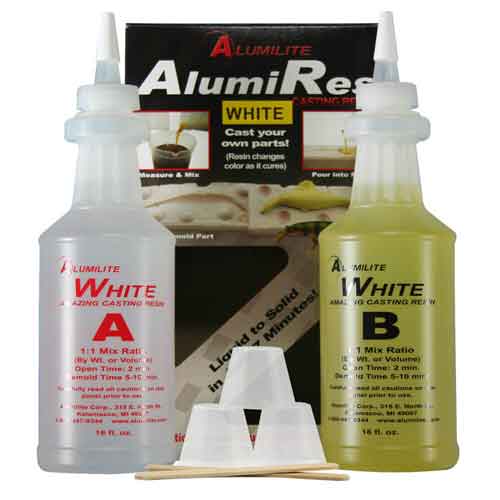
The following is a summary of the data sheet of the Amazing Casting Resin - White.
- Color: White
- Mixed Viscosity (cps.): 90
- Hardness Shore D: 72
- Specific Gravity: 1.05
- Shrinkage (in/in): 0.006
- Tensile Strength (psi): 4500
- Elongation: 10%
- Heat Deflection (Degrees F) 185
- Izod Impact (lb/in): 0.40
The following are General Properties for the material
- Color "A": Clear
- Color "B": Translucent yellow
- Mix Ratio: 1:1 by WEIGHT or Volume
- Open Time: 2.5-3 mins
- Demold Time: 5-15 mins
- Full Cure Schedule: 72 Hours
Material 2 - Alumilite - Amazing Clear Cast
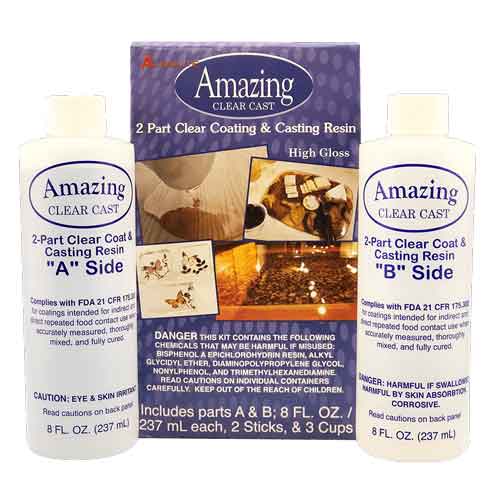
The following is a summary of the data sheet of the Amazing Clear Cast.
- Color: Clear
- Mixed Viscosity (cps.): 2,600
- Hardness Shore D: 80
- Specific Gravity: 1.08
- Shrinkage (in/in): 0.003
- Tensile Strength (psi): 8,000
- Elongation: 1-3%
- Heat Deflection (Degrees F) N/A
- Izod Impact (lb/in): 2.26
- Compression (psi): 27,000
The following are General Properties for the material.
- Color "A": Translucent Blue
- Color "B": Clear
- Mix Ratio: 1:1 by WEIGHT or Volume
- Open Time: 45-60 mins
- Demold Time: 18-24 mins
- Full Cure Schedule: 72 Hours
We can notice that this material takes more time to cure than material 1.
Material 3 - Aristocrat - Liquid Glass
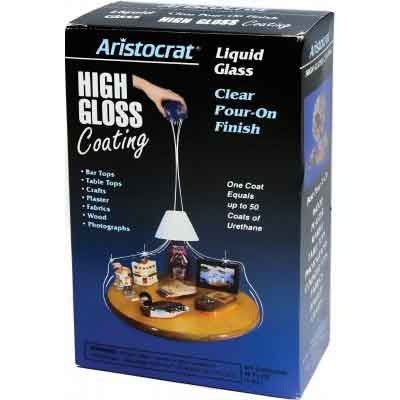
The following is a summary of the data sheet of the Aristocrat - Liquid Glass.
- Color: Clear(Yellowish)
- Hardness Shore D: 81-83
- Shrinkage (in/in): 0.003
- Tensile Strength (psi): 5,800
- Elongation: 7%
- Izod Impact (lb/in): 0.95
- Compression (psi): 3,500
The following are General Properties for the material.
- Color "A": Translucent Blue
- Color "B": Clear
- Mix Ratio: 1:1 by WEIGHT or Volume
- Open Time: 10-15 mins
- Demold Time: 18-24 mins
- Full Cure Schedule: 72 Hours
Material 4 - PolyPol - 1003
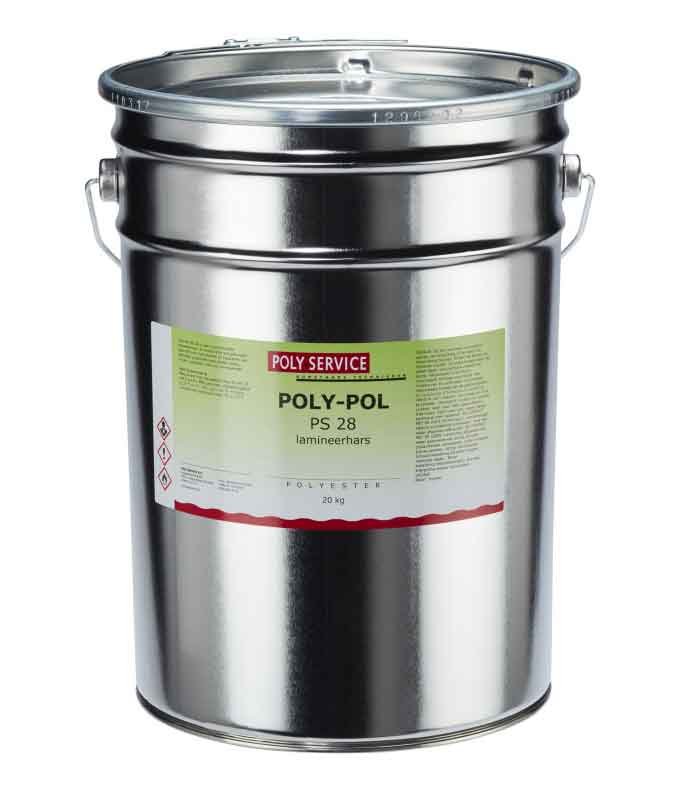
The following is a summary of the data sheet of the PolyPol - 1003.
- Color: Bluish Cloudy Viscous Liquid
- Mixed Viscosity (cps.): 600-800
- Specific Gravity: 1.1-1.2
- Tensile Strength (MPa): 60
The following are General Properties for the material.
- Color "A": Translucent Blue
- Color "B": Clear
- Mix Ratio: 3% by Volume
- Open Time: 15-25 mins
- Demold Time: 25-35 mins
- Full Cure Schedule: 72 Hours
This work is licensed under a Creative Commons Attribution-NonCommercial-ShareAlike 4.0 International License