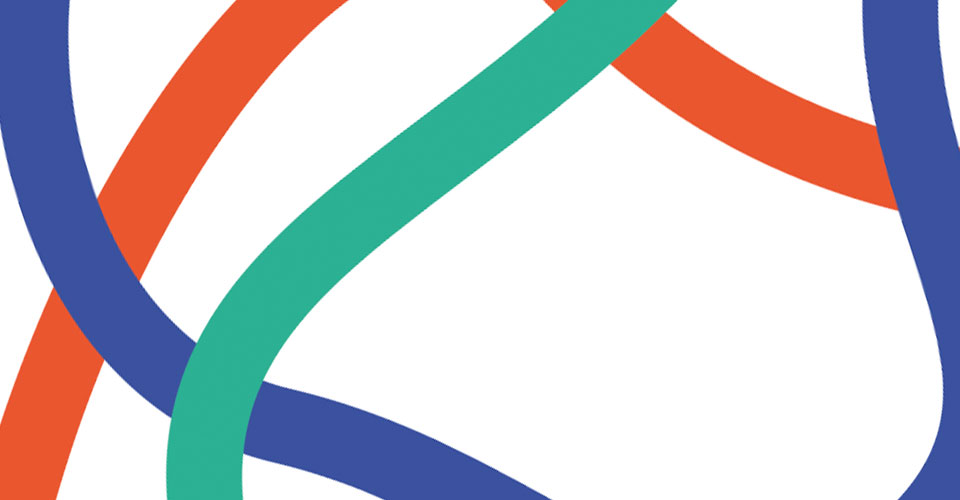
Final Project
FINAL PROJECT
3D ENCODE DNA | BRINGING GENETIC CODE TO THE PHYSICAL WORLD
WHAT IS IT?
Interactive kinetic piece that uses A,T,C,G as input and translates into a 4 states bit/pixel phygital tridimensional display.
WHAT FOR?
To better understand the genetic code as modular, mutable & complex tridimensional system.
WHY
To give agency to a broad audience to play with something that usually happens within labs.
SLIDE
"Presentation Slide"
VIDEO
FINAL HERO SHOTS
After the presentation, I kept working on adding additional nodes until I got to the 50. In the end, there were 48 functional nodes. One secondary PCB seemed not to work correctly as well as one motor.
"Acrylic structure."
"Acrylic structure lighting up."
"Acrylic structure randomizer."
"Detail side of the structure."
"Detail inner part of the structure."
"Detail inner part of the structure."
"Detail inner part of the structure."
"Mobile pixel including Gear Box."
"3D Encode DNA interface"
"Controller wiring"
"Hero shot milled boards."
"Super DNA and DNA boards."
"Hero shot I2C manufactured node."
AFTER PRESENTATION VIDEO
I created this video after assembling additional nodes. Very happy of how it turned out.
FILES
STRUCTURE
CAD FILES
Download Structure Fusion 360 Files
LASER CUTTER FILES
Download Acrylic Structure Files
Download Tolerances Test Files
3D PRINTING FILES BASE
INTERFACE
LASER CUTTER FILES
Download Interface Laser Cutter Files
VINYL CUTTER
Download Interface Vinyl Cutter Files
MOBILE PIXELS (X50)
GEAR BOX (X1)
Download GearBox Fusion 360 Files
SERVO GEAR (X1)
Download Servo Gear Fusion 360 File
GEAR SHAFT (X1)
Download Gear Shaft Fusion 360 file
ROD TOPPER (X1)
Download Rod Topper Fusion 360 file
BASE (X1)
Download GearBox Fusion 360 Files
SERVO SUPPORT (X1)
Download GearBox Fusion 360 Files
SPACERS (X3)
PCBS
MAIN BOARD DESIGN TO BE MILLED
- Note that this design is larger and has different pinout for the pinout of the interface controller
MAIN BOARD DESIGN TO BE MANUFACTURED
CODE MAIN BOARD
SECONDARY BOARDS DESIGN TO BE MILLED
- Note that this design is larger and won’t fit under the base for the servo motor.
SECONDARY BOARD DESIGN TO BE MANUFACTURED
CODE SECONDARY BOARD
LICENSE
3D Encode DNA by Carla Molins Pitarch is licensed under CC BY-NC-ND 4.0
FINAL QUESTIONS FOR MY FINAL PROJECT
Document a final project masterpiece that integrates the range of units covered, answering:
WHAT DOES IT DO?
My final project is a phygital display that allows users to encode physical pixels using the genetic code: A,T,C,G creating a volumetric interactive experience that conveys some of the complexities that the DNA entitles.
"Visual explanation of the rationale behind my final project."
The main idea is to take advantatge of some logics of Computation & Digital Fabrication in order to convey the different states that the genetic code can have and how those changes relate to the whole of such a large system.
To sum up a bit, the object is meant to have a significant size and be positioned from the waist to eye-line height.
The kinetic piece will have 3 main components: The body, the interface and the display.
" First sketch of the Final Project Object."
As explained above, the input and interface will be the for letters of the genetic code A, T, C, G. The user will have the agency to “Type” the genetic code and to have a phygital display that will encode the genetic code in a pattern that it will be both intelligible but expressive and furthermore, alive. There’re additional controls to move along the letters and change the value as if you were on a text processor typing.
Each one of the elements of the display will have 4 positions according to each one of the 4 letters. The form and its functioning will be further developed in the next stage of the project.
WHO’S DONE THAT BEFOREHAND?
I haven’t found any physical project using the genetic code as programming language. However there are many wonderful projects that serve as a reference to develop this project. See References section.
As for Fabacademy projects that I could find that I could somehow relate, find a list here.
See physical Display fab project
See Soft Interface fab project
See Mechanism Design fab project
See Multiple mechanical outputs fab project
WHAT DID YOU DESIGN
Acrylic structure
"Acrylic structure."
Mobile Physical Pixels & Gear Box
"Mobile pixel including Gear Box."
Main board & Secondary Board
"LEFT: One floor with 10 I2C nodes. RIGHT: Main board connected to I2C bus."
Interface
"3D Encode DNA interface"
WHAT MATERIALS AND COMPONENTS DID YOU USE? WHERE DID THEY COME FROM? AND HOW MUCH DID THEY COST?
This is the complete bill of materials to build this project. It includes the source and the cost.
"BOM for 3D ENCODE DNA."
WHAT PARTS & SYSTEMS WERE MADE?
- Structure: Laser cut.
- Base joints: 3d printer
- Interface: Laser Cut + Vinyl Cutter
- Gear Box (including: base, Motor support, Geared shaft, * Servo Gear, Spacers and rod topper): 3d printer
- Pixel: Laser Cut, 3d printing.
-
Pcbs: prototype milling machine Final serial fabrication.
WHAT PROCESSES WERE USED?
- CAD, 3D PRINTING, LASER CUT, VINYL CUTTING, ELECTRONICS DESIGN, ELECTRONICS PRODUCTION.
WHAT QUESTIONS WERE ANSWERED?
When I started designing this project I wasn’t sure if a system that included so many nodes was feasible. Even though originally I wanted to have 96 I2C nodes, I settled on having 50 and they work which is great.
I also wondered how stable the system was going to be given that the I2C bus was so long. I’d say it’s functional but sometimes it gets stuck. I’ll keep working on reducing the nouse.
WHAT WORKED? AND WHAT DIDN’T?
In the end I ended up having 49 out of 50 functional nodes. The system is fully functional even though the interface is a bit flickery, some buttons don’t always work. I plan on replacing the interace in the future.
HOW WAS IT EVALUATED?
My main goal was to be able to control 50 nodes independently, and that was achieved.
The user experience was essential, and it needs another iteration to allow independent interaction. As for now, it needs some supervision as some wires might get tangled.
WHAT ARE THE IMPLICATIONS?
This project brings agency to users to explore complex genetics playfully and entertainingly. This accessibility towards a theme that would be restricted to scientific audiences democratizes knowledge and allows people to talk and wonder about these topics.
This project had a great scale in many aspects. Find here the link to all the weeks that I’ve worked developing and iterating some components for my final project.
Outputs week Networking week Interfacing week Wildcard week Application&Implications Invention&Intellectual Property
Finally, find the whole long process here:
ACKNOWLEDGMENTS
I want to thank my partner Daniel for all the support, both in the making and logistics. :)
"Building the structure :)."