Assignments:
- group assignment:
characterize the design rules for your PCB production process
- individual assignment:
make an in-circuit programmer by milling and stuffing the PCB,
test it, then optionally try other PCB processes
Making Fab ISP 44:
Fabmodules.org (computer)
- I started out by finding .png for the circuit and outlines and started by inserting the images into Fabmodules.org
- In fabmodules I clicked the "output format" and made the image into "Roland mill(.rml)". I selected "process" and selected "PCB traces (1/64)" wich means that the tool that is used is 1/64". For the circuit I used 1/64" and for the outlines I used 1/32".
- After that selected the settings for the milling. The settings that I changed:
- Machine: MDX-20
- x0(mm): 0
- x0(mm): 0
- Cut depth: 0.2
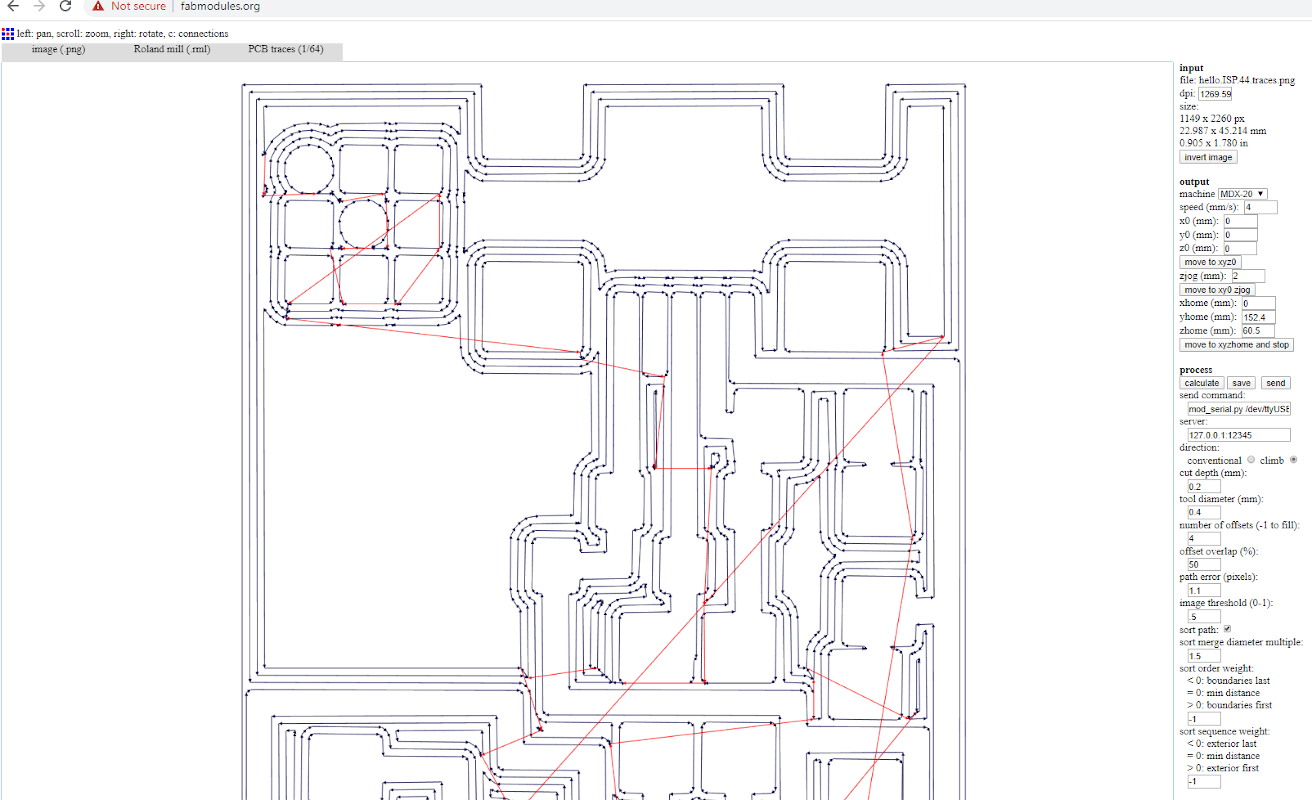
- After chancing the setting I clicked "calculate" and then Fabmodules calculated the tool path.
- After Fabmodules had calculated the tool path I clicked "save"
- After saving the circuit I reapeated the process with the outlines but changed the tool to 1/32" and the cut dept to 1.7mm to cut through the bord.
On the milling machine (Roland MDX 20)
- I got myself a copper board and placed a double sided tape on the back side and plced the board on the milling machine. I placed the board so it's straight to minimise the waste of material.
- Turned on the milling machine
- The next thing that I did was to find myself a 1/64" drill bit and inserted it into the milling machine. I placed it high because later when I zero the z I will lower it. It is also important to not tighten the screew too hard because it's fragile.
Roland MDX 20 conrtol panel
- I opened Roland MDX 20 conrtol panel and the software asked me "Witch COM port is Roland MDX20 connected to? (a,b...): a=COM1, b=COM3, c=COM5" and I selectef "c" and clicked "ok".
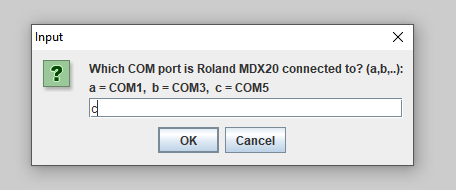
- In the software there are buttons above and big yellow space below that when you click somewhere in yhe yellow space and the milling machine moves to that spot. I started by clicking around until I had placed the drill bit over the bottom left corner of the brass plate to waste as little materila as possible.
- After finding the place where I wanted to have my X and Y axis I clicked "Set XY" and that makes the place that the drill bit is placed over the 0 axis.
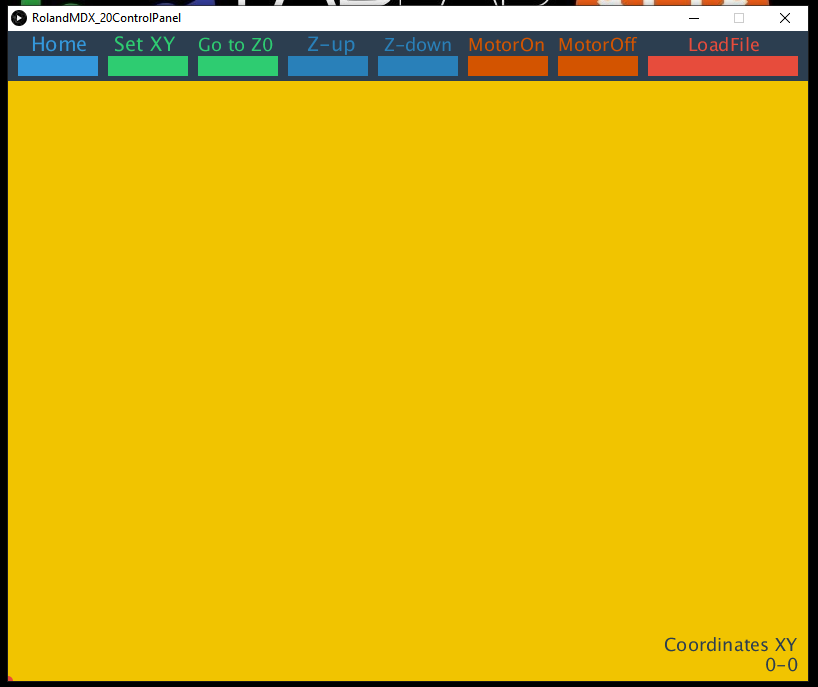
- To zero the Z axis I moved the drill bit as low as possible but left about one cm left so that the milling machine would be able to drill. When I had lower the drill I losen up the drill bit but made sure to not drop the drill bit (if it drops it brakes) and lowered it carefully down to the plate and then thighten the screw again. Note: if you 0 your Z axis somewhere else than on your XY the machine will not lift the drill when it's moves to the XY and it will scrape the board and possibly destroy the drill. So that does not happen you need to lift the drill bit useing the commands on the computer by clicking "Z-up"untill your are happy with the hight. If you move the Z up by using the buttons on the machine you will lose the Z axis and then need to make another Z axis.
- The next thing to do is to load the file so I clicked "load file" and selected the circuit file because you want to start by making the circuit, if you start by cutting the outlines the plate has only the tape to hold it and will most likely move around and then the cuts will not be accurate. After you load your file the machine starts to cut automatically. This cut will take about 15 minutes.
- After the milling machine had finished cutting the circuit the next thing to do is to cut the outlines. To do that you repeat the same process all you need to change is the drill bit, to cut the outlines you use 1/32" instead the 1/64". You need to change the drill bit in both the machine and on Fab modules (where you generate the file). Also what you need to change is the cut dept and you also do that on Fab modules and you change that to 1.7mm. On the outlines you want to cut throug the board.
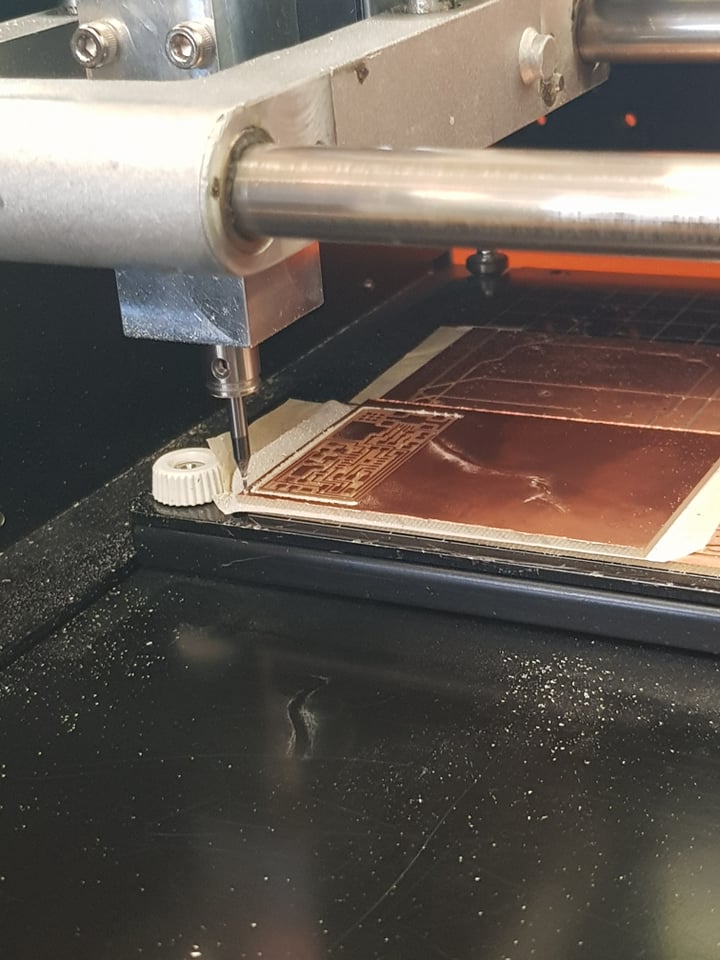
Manual
- After removing the boards form the milling machine it's important to wash the boards with soap and water. It's enough to wash it with soap and water. This is important because this process cleans the board and removes a lot of roughness that may be when the board is fresh out of the milling machine.
- Next step is soldering and I like to start by going through the blueprints of what I'm making and in this case it's Fab ISP44. In this pice there are 14 compoanents you need to solder to your board.
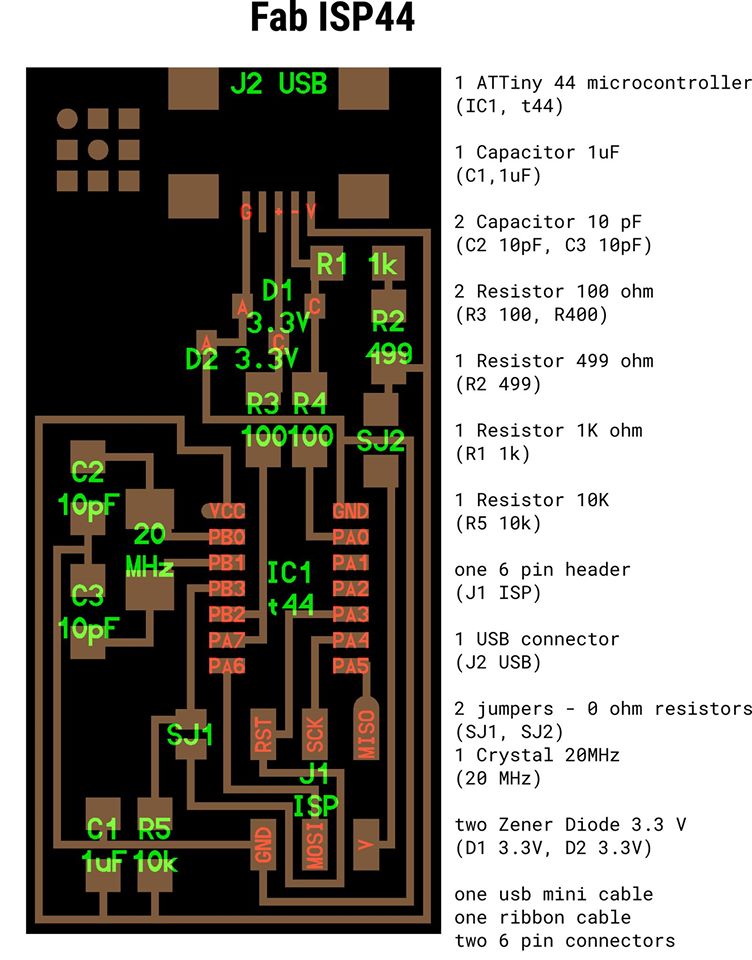
- How to solder:
- Mount the component
Begin by inserting the leads of the LED into the holes of the circuit board. Flip the board over and bend the leads outward at a 45′ angle. This will help the component make a better connection with the copper pad and prevent it from falling out while soldering.
- Heat The JointTurn your soldering iron on and if it has an adjustable heat control, set it to 400’C. At this point, touch the tip of the iron to the copper pad and the resistor lead at the same time. You need to hold the soldering iron in place for 3-4 seconds in order to heat the pad and the lead.
- Apply Solder To JointContinue holding the soldering iron on the copper pad and the lead and touch your solder to the joint. IMPORTANT – Don’t touch the solder directly to the tip of the iron. You want the joint to be hot enough to melt the solder when it’s touched. If the joint is too cold, it will form a bad connection.
- Snip The Leads Remove the soldering iron and let the solder cool down naturally. Don’t blow on the solder as this will cause a bad joint. Once cool, you can snip the extra wire from leads.
A proper solder joint is smooth, shiny and looks like a volcano or cone shape. You want just enough solder to cover the entire joint but not too much so it becomes a ball or spills to a nearby lead or joint.
- How to desolder:
- Step 1 – Place a piece of the desoldering braid on top of the joint/solder you want removed.
- Step 2 – Heat your soldering iron and touch the tip to the top of the braid. This will heat the solder below which will then be absorbed into the desoldering braid. You can now remove the braid to see the solder has been extracted and removed. Be careful touching the braid when you are heating it because it will get hot.
- Optional – If you have a lot of solder you want removed, you may want to use a device called a solder sucker. This is a handheld mechanical vacuum that sucks up hot solder with a press of a button.
To use, press the plunger down at the end of the solder sucker. Heat the joint with your soldering iron and place the tip of the solder sucker over the hot solder. Press the release button to suck up the liquid solder. In order to empty the solder sucker, press down on the plunger.
- When you have finished soldering all the components to your board it's time for programming.
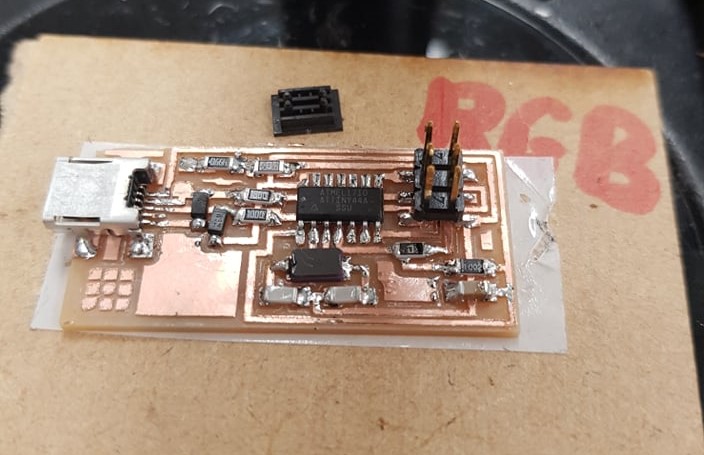
Problems:
There was a couple of proplems with Roland MDX 20 conrtol panel and Fab modules.
- When I had 0 the Z axis and did not have the drill on the 0 for the XY and started to mill the machine would move to the XY 0 without raising the Z so the drill scraped the board, scraching the board and possibly destroying the drill bit. To make that problem go away I tried raising the Z up by using the buttons on the machine but then I had lost the Z axis and neded to make another 0 for the Z. I finally realize that I neded to press "Z up" on the program so would not loose the Z.
- I also had a problem with the quality of my cuts and that problem was fixed by chainging the drill bit for a neew one.
- The problem with Fab modules was that it was not doing it's job correctly and made an error when making the code. I had tried a couple of times and was constantly making new codes and somehow it newer finished cuttint the last line in the outline and one time it just went straight to the middle and destroyed the circuit. I fixed that problem by using an old file form the first cut when the cut wasn't good quality.
Programming Fab ISP 44
- I started out by finding an computer with Linux and started it up.
- I connected the Fab ISP44 to the laptop by an mini-USB.
- Then I connected it to hello board with a ribbon cable to program with making sure the ribbon cable is correctly connected to the board (GND to GND) and connected that board to another computer with micro-USB
- To program the board I downloaded the c, makefile and py files
- opened a terminal, went into the folder where I had saved the files (using the cd command) and wrote:
sudo make -f Makefile flash
- After I had flashed the firmware I programed the fuses by writing:
sudo make fuse
sudo make program
- To make the board able to program other board I needed to take off the jumpers (0 ohm resistors)
- To program other boards I followed the same steps as I followed when I programmed the Fab ISP44.
Problems:
The problems I had with programming the Gab ISP44 to begin with was that I forgot to solder an 1k resistor and when I connected the Fab ISP44 to the computer and tried to fuse it the computer did not find the board and all I got was error. I fixed that problem by soldering the resistor on.
Another problem I had was that to program the Fab ISP44 I had to have 2 jumpers(0 ohm resistors) to be able to program it but so I could program other board with the Fab ISP44 I had to remove the jumpers.
Line test (group assingment)
The group assignment for this week was to make a line test. Line test is a test that tests how narrow your lines can be by running your milling machine or laser throug a test sheet that test the machine to make it's lines as narrow as possible until it can't go any narrower. The test here is to see how the fine of a lines the milling machine can make the board and it depends on how accurate the machine is and how fine of a tooth you are using and in my case I'm using 1/64 tooth witch is pretty precise and if you would be using 1/32 the drill would be to big and it would not be able to mill between the lines and therefor make it un precise.
- I started out by running going to Fab Academy page for this week(Electronics Production) and found links to pages that contained the linetest and the outlines and saved those images on my computer.
- After saving the images I imported them to Fabmodules.org and basically repeated the process that I did earlyer with the Fab ISP44.
- In fabmodules I clicked the "output format" and made the image into "Roland mill(.rml)". I selected "process" and selected "PCB traces (1/64)" wich means that the tool that is used is 1/64". For the circuit I used 1/64" and for the outlines I used 1/32".
- After that selected the settings for the milling. The settings that I changed:
- Machine: MDX-20
- x0(mm): 0
- x0(mm): 0
- Cut depth: 0.2
- After chancing the setting I clicked "calculate" and then Fabmodules calculated the tool path.
- After Fabmodules had calculated the tool path I clicked "save"
- After saving the circuit I reapeated the process with the outlines but changed the tool to 1/32" and the cut dept to 1.7mm to cut through the bord.
On the milling machine (Roland MDX 20)
- I got myself a copper board and placed a double sided tape on the back side and plced the board on the milling machine. I placed the board so it's straight to minimise the waste of material.
- Turned on the milling machine
- The next thing that I did was to find myself a 1/64" drill bit and inserted it into the milling machine. I placed it high because later when I zero the z I will lower it. It is also important to not tighten the screew too hard because it's fragile.
Roland MDX 20 conrtol panel
- I opened Roland MDX 20 conrtol panel and the software asked me "Witch COM port is Roland MDX20 connected to? (a,b...): a=COM1, b=COM3, c=COM5" and I selectef "c" and clicked "ok".
- In the software there are buttons above and big yellow space below that when you click somewhere in yhe yellow space and the milling machine moves to that spot. I started by clicking around until I had placed the drill bit over the bottom left corner of the brass plate to waste as little materila as possible.
- After finding the place where I wanted to have my X and Y axis I clicked "Set XY" and that makes the place that the drill bit is placed over the 0 axis.
- To zero the Z axis I moved the drill bit as low as possible but left about one cm left so that the milling machine would be able to drill. When I had lower the drill I losen up the drill bit but made sure to not drop the drill bit (if it drops it brakes) and lowered it carefully down to the plate and then thighten the screw again. Note: if you 0 your Z axis somewhere else than on your XY the machine will not lift the drill when it's moves to the XY and it will scrape the board and possibly destroy the drill. So that does not happen you need to lift the drill bit useing the commands on the computer by clicking "Z-up"untill your are happy with the hight. If you move the Z up by using the buttons on the machine you will lose the Z axis and then need to make another Z axis.
- The next thing to do is to load the file so I clicked "load file" and selected the circuit file because you want to start by making the circuit, if you start by cutting the outlines the plate has only the tape to hold it and will most likely move around and then the cuts will not be accurate. After you load your file the machine starts to cut automatically. This cut will take about 15 minutes.
- After the milling machine had finished cutting the circuit the next thing to do is to cut the outlines. To do that you repeat the same process all you need to change is the drill bit, to cut the outlines you use 1/32" instead the 1/64". You need to change the drill bit in both the machine and on Fab modules (where you generate the file). Also what you need to change is the cut dept and you also do that on Fab modules and you change that to 1.7mm. On the outlines you want to cut throug the board.
Manual
- After removing the boards form the milling machine it's important to wash the boards with soap and water. It's enough to wash it with soap and water. This is important because this process cleans the board and removes a lot of roughness that may be when the board is fresh out of the milling machine.
We had problems with connecting to the milling machine and was it because the printer that was also connected to the computer was stealing the port that was supposed to be for the milling machine. We fixed that problem by disconnecting the printer from the computer and the milling machine worked after that.
Tutorials I used:
Files:
Software I used:
Machines I used: