Molding and Casting
So this is 10th week.- review the safety data sheets for each of your molding and casting materials, then make and compare test casts with each of them
- Design a 3D mould around the stock and tooling that you'll be using, machine it, and use it to cast parts.
Though 3d printing and cnc machining is good in creating complicated 3d geometries .It is very inefficient is replicating similar designs .Though there are faster and more precise machines are developing like SLS(selective laser sintering) and CLIP(Continuous Liquid Interface Production ) still it is consuming more time . So if we are looking for a rapid replication of an already existing slightly big object the best way so far is molding and casting .Once we created the mold it is just the curing time is needed to recreate the original one .Another advantage of molding and casting is that we get exact replica of the original one .We all are done some sort of moulding and casting in our life .Sometimes while helping our mom in kitchen or while playing in the beach etc . So the basic knowledge about molding and casting ain't strange to me .But i was really curious about the modern days molding and casting materials ,silicone ,liquid ,plastics aloys etc.So there are lot more for me to learn .
Some basics
If you are looking for a simple and good introduction to molding and casting i think this instructables page will help you a lot
Male and Female Mold(Positive and Negative Casting):-
A positive mold is an exact replica of the desired object . It directly applicable if we are
working on composits ,vaccum forming , sheet metals etc.For casting it could used to create
negativce moid or could be used in 2 part casting.
A negative mold is usually used for casting liquids like liquid plastic, molten metal,
gypsum, cement etc
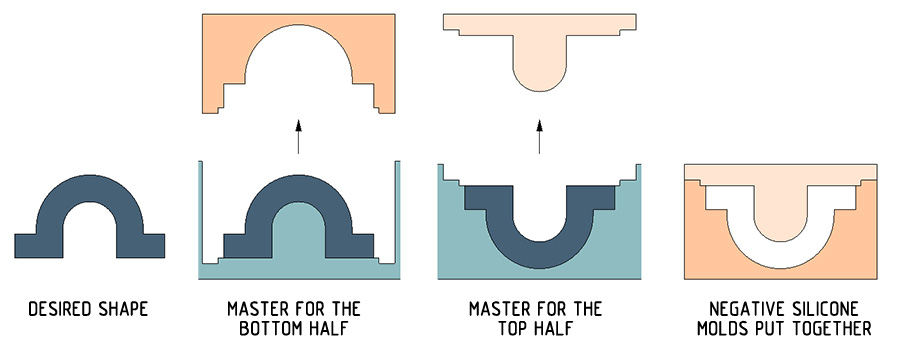
Designig Model With Autodesk Inventor
I decided to create a simple baring holder for my 3D-printer. This will hold a small bairing in T-Slot. usualy i give this work to outsource but this time i tray to make my own mold..I think this will help me to understat more about the strengts and weeknees of molding and casting methode .
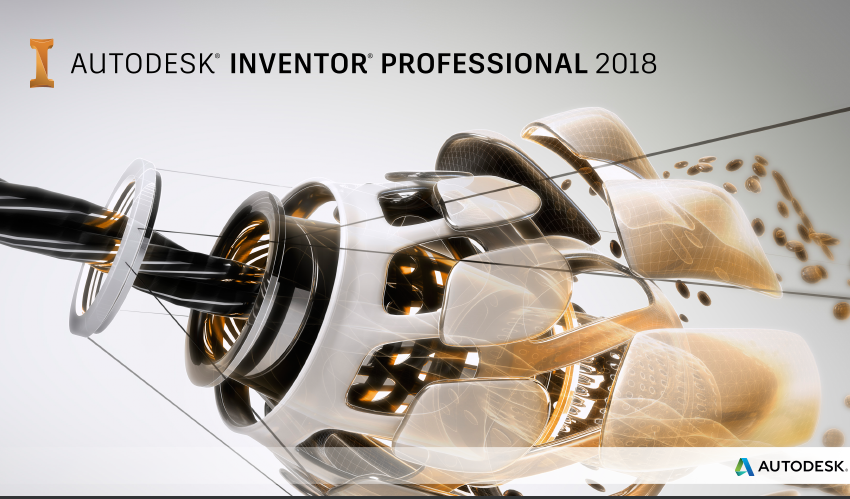
I have some working experience in inventor, but i dont have any previous molding experience, i usually prefere 3D-printing. so this is a nice experience for me. This helps veyrmuch in my compony project 3D-printer.
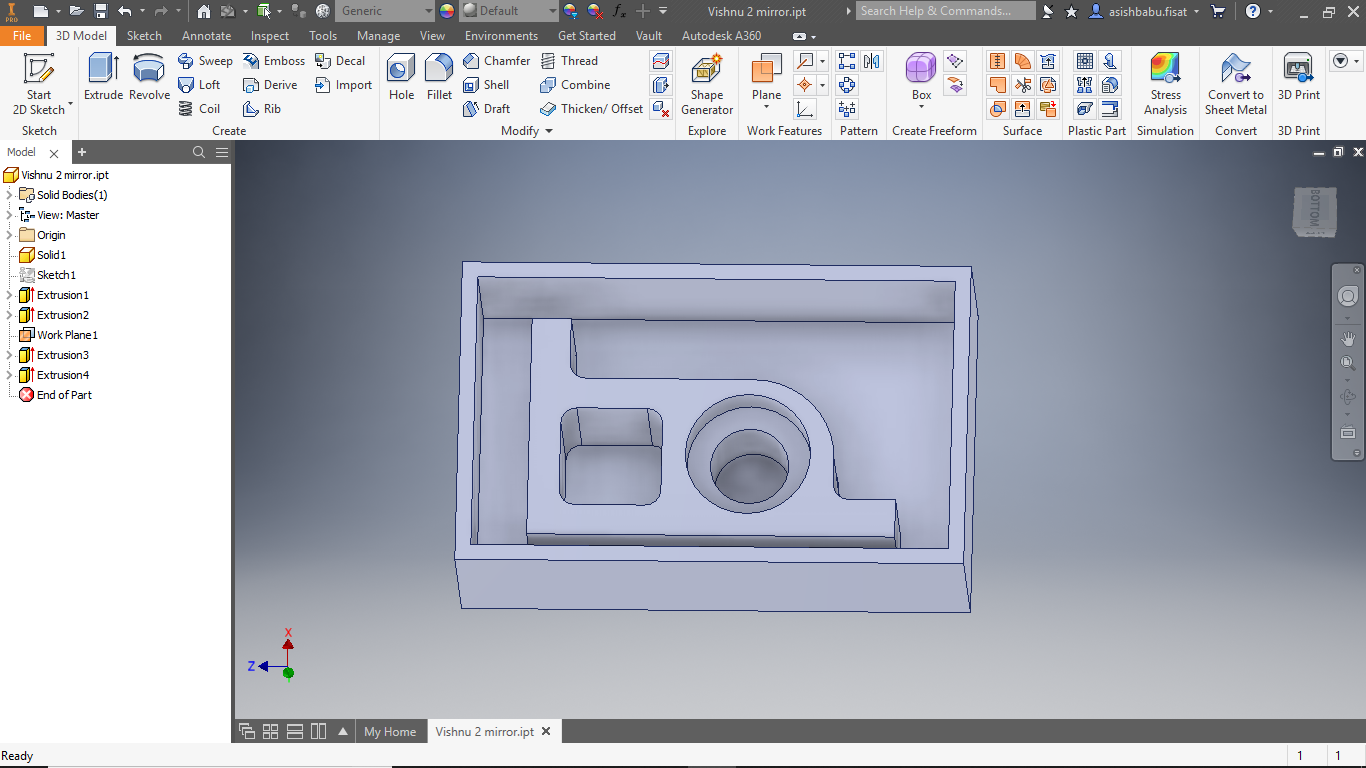
Download baring holder design Download mold design
Setting Up in Modella:-
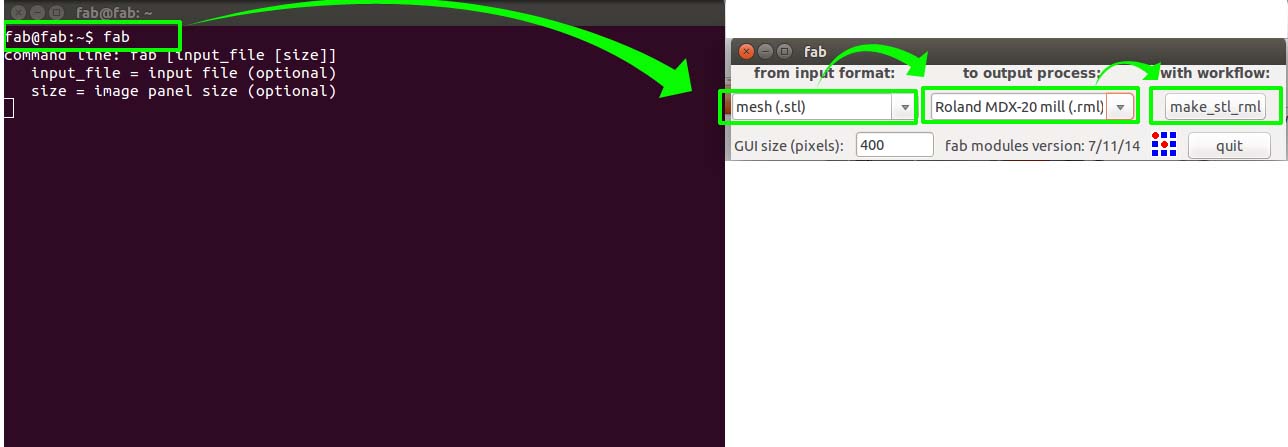
- Open fab module From terminal
- Selet input format -> mesh(.stl)
- Select to output process -> Roland MDX-20 mill(.rml)
- Proceed with "make_stl_rml"
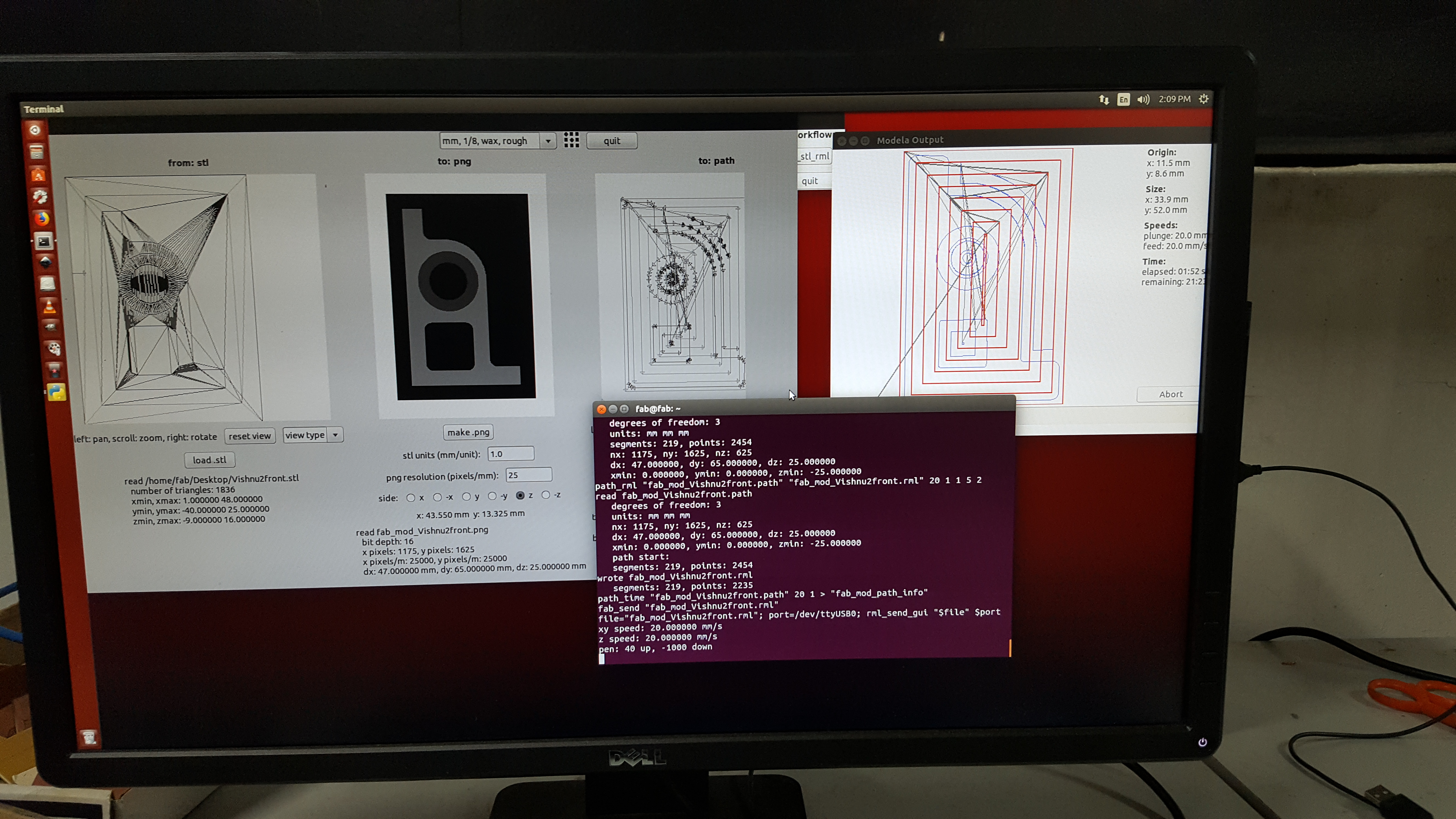
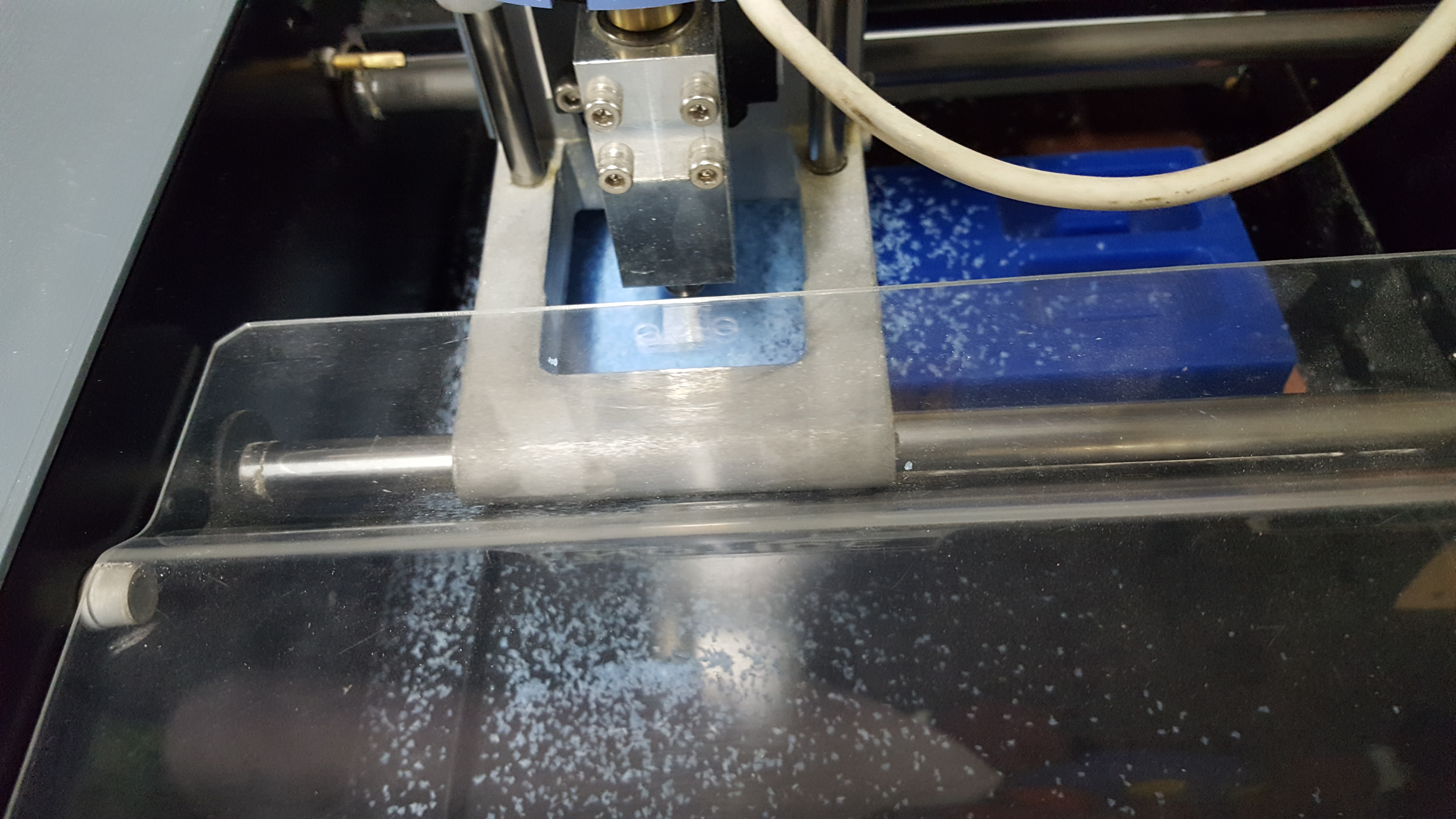
For setting origin see my week 5 page
Prepare -ve mold
Now we have to create a negetive mold. For that we take a smooth cast
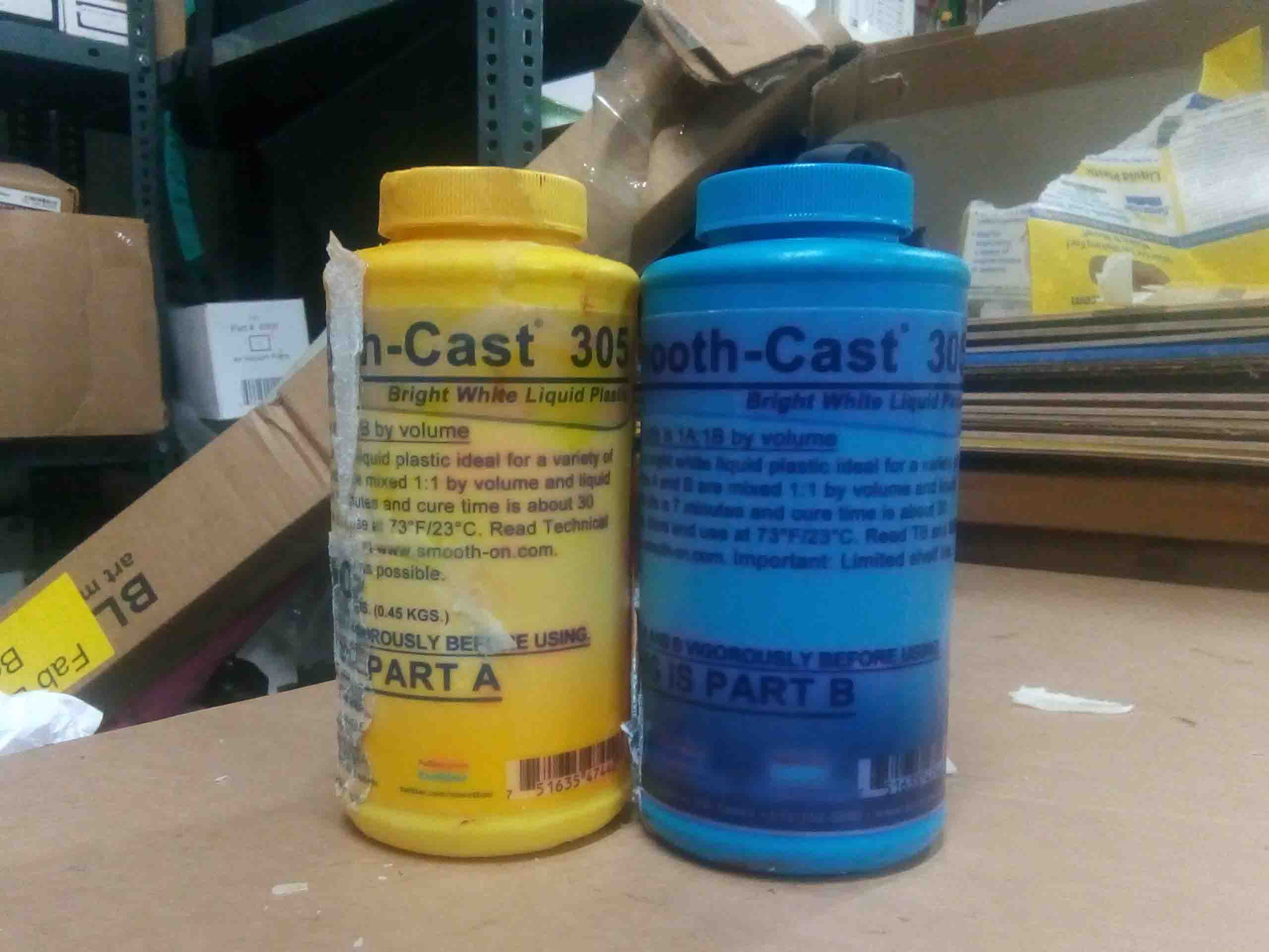
there are two parts of resin. Part A and Part B. The proportion to mix both of them is "1:1". But first we need to measure the amount of resin needed for the negetive mold making. For that pour some water into the mold and pour it back to the glass and mark the level.
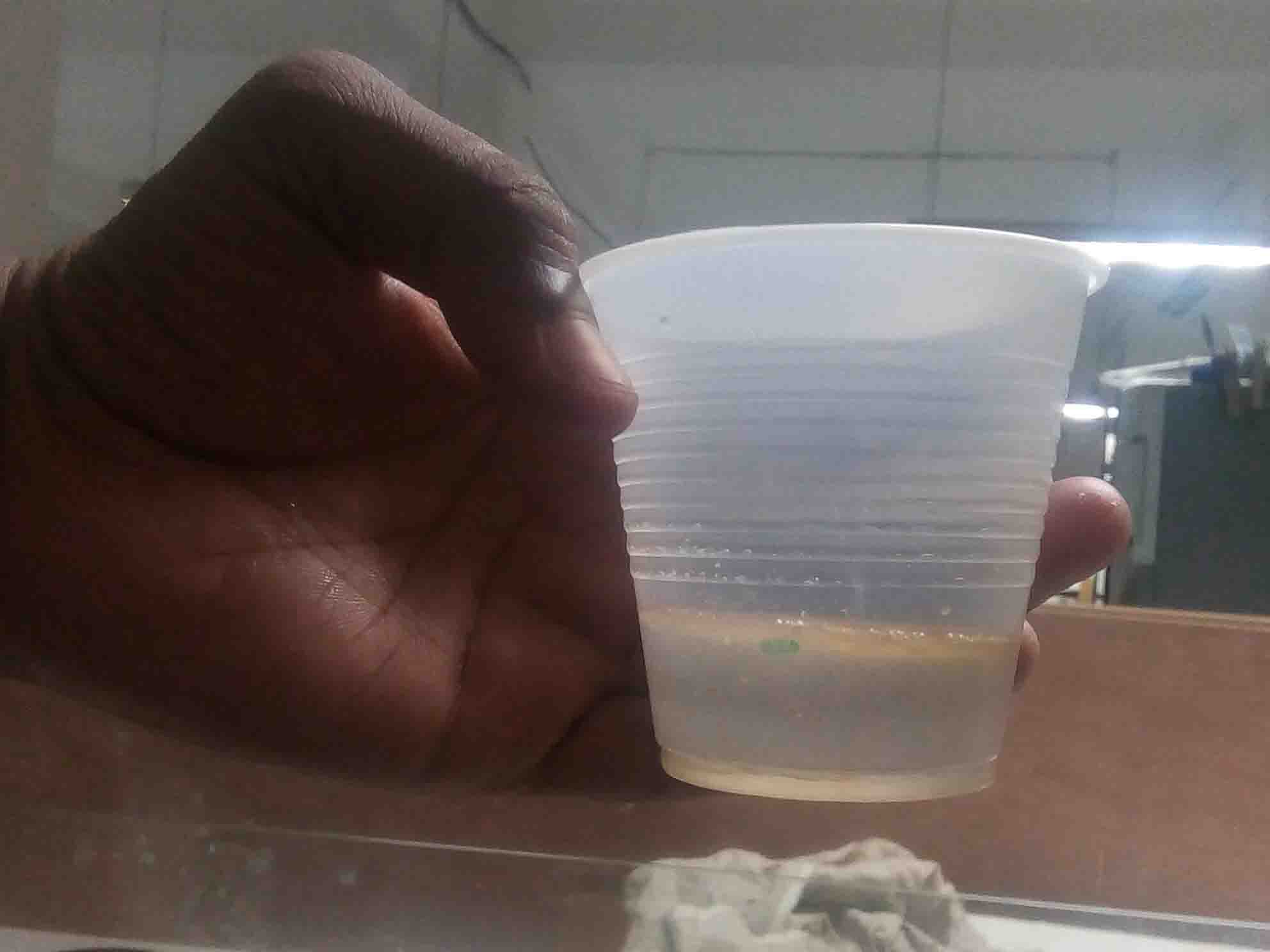
Now pour equal amount of Part A and Part B of the resin into the cup
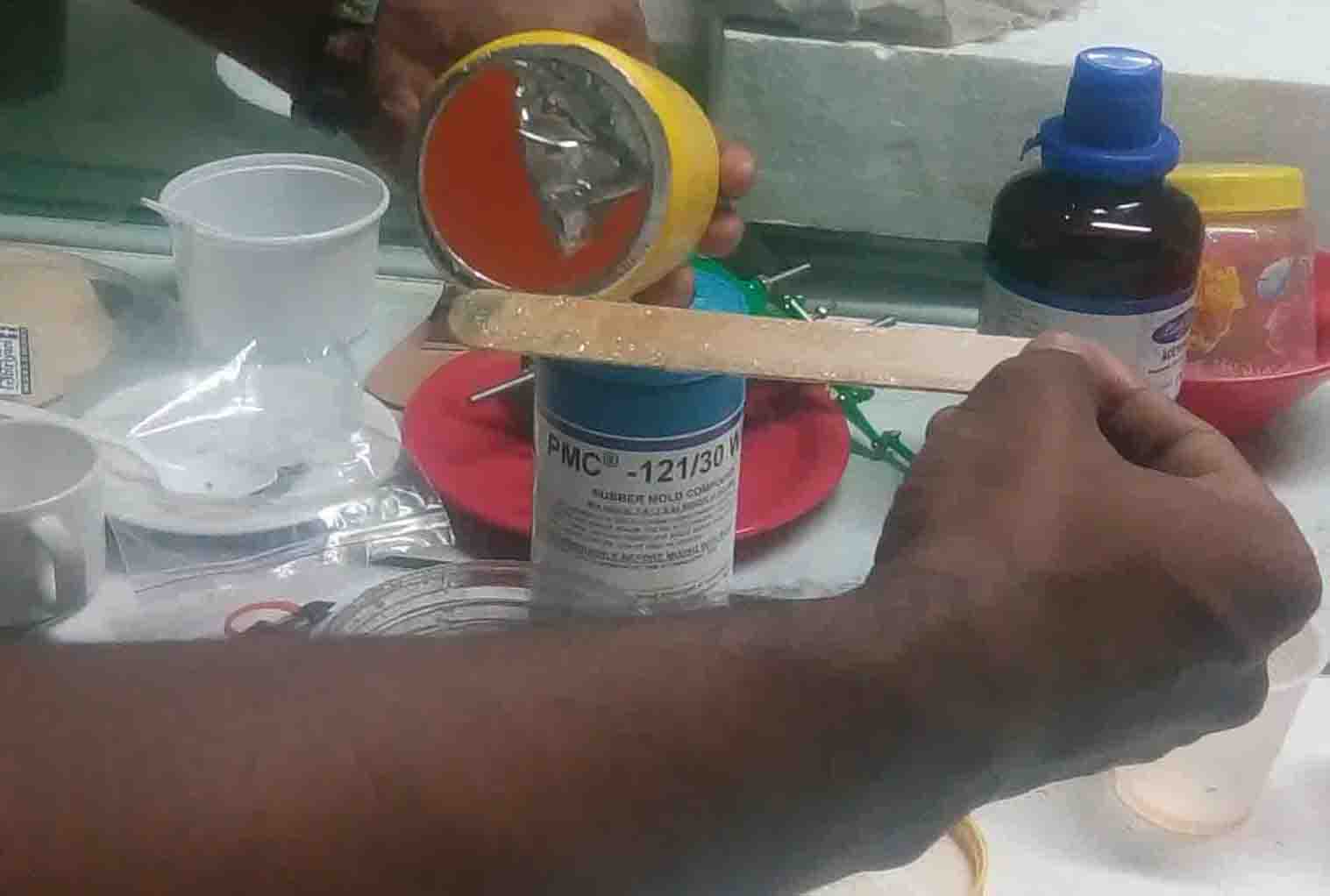
Now mix the well and pour into the mold. I used a hand dril attached with a acrylic rod to stir up the mixture. Because it was difficult to do with hands
Pour the resin into the mold. Tap it to the ground so that the air bubbles come up. Wait for 6 hour in order to set the resins. Please care full while you design you design. Because it can be very trick when it comes to mold. So after waiting for about 6 hours the mold is ready to use. Remove the negetive mold from the wax mold.
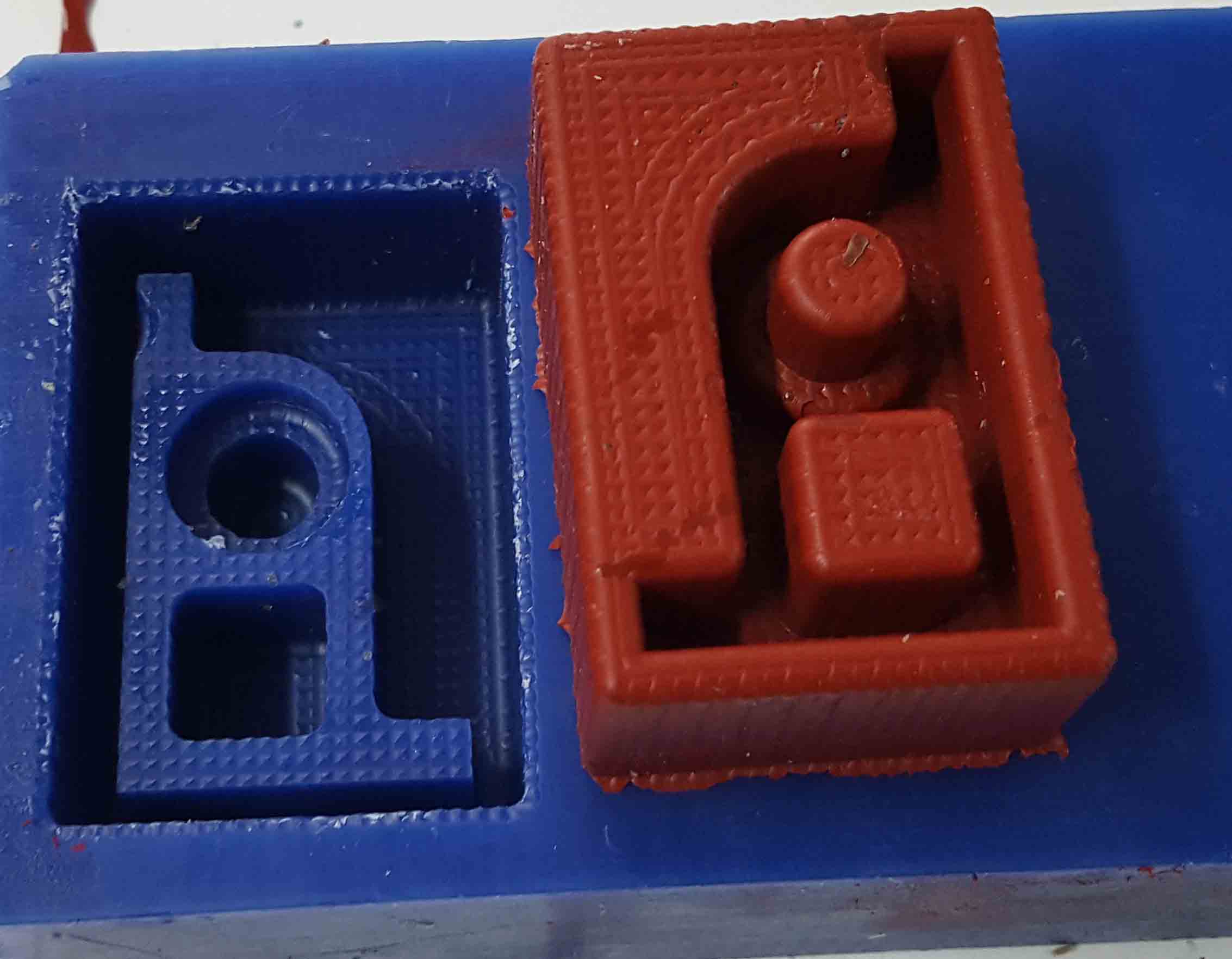
Casting
I use resin to cast this,It also have a mixing ratio in which we have to mix the resins. It specifically said that the ratio is 2:1 accoring to grams.
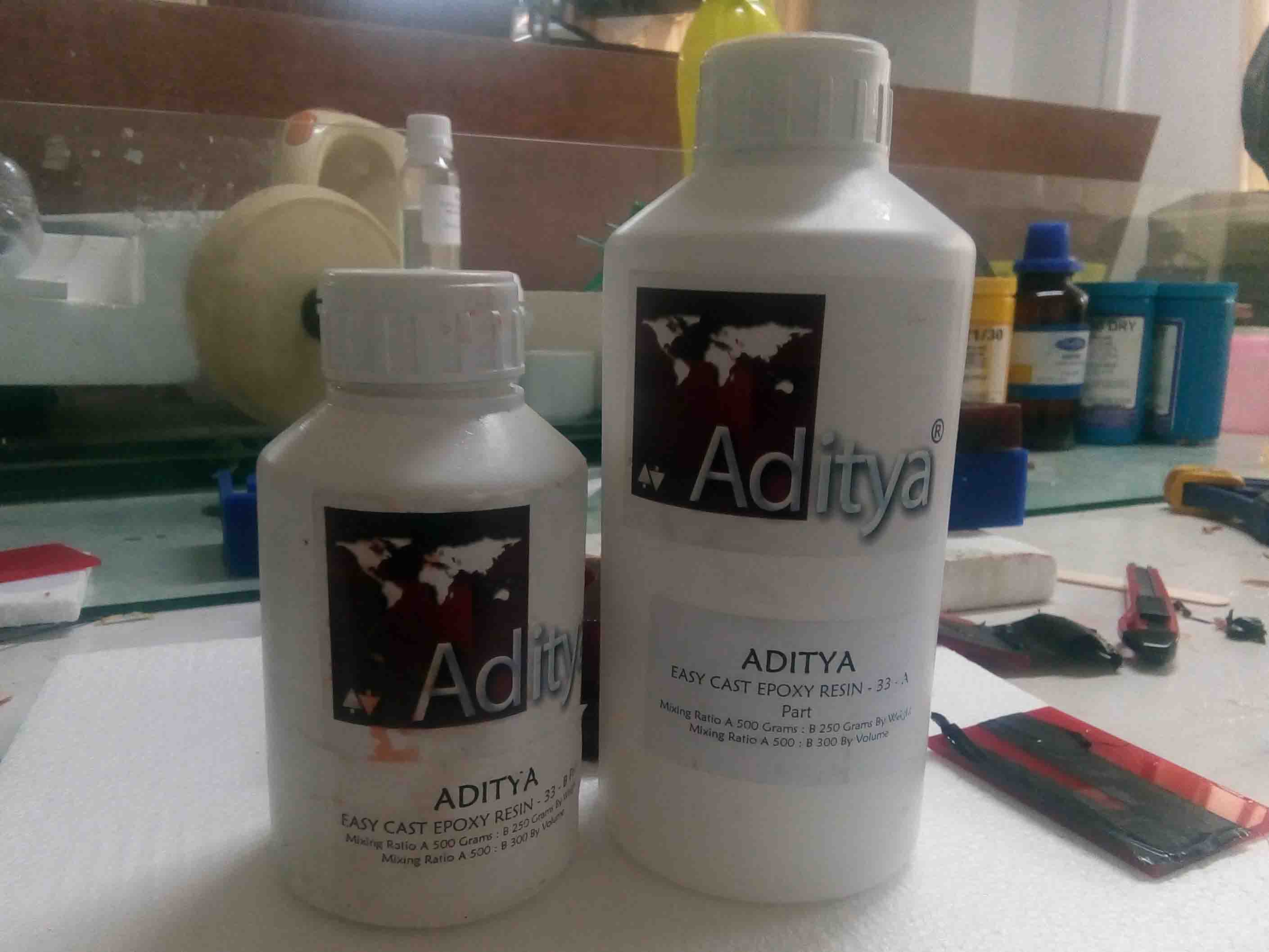
accuratly measure the required resin. I took some more than actual weight...
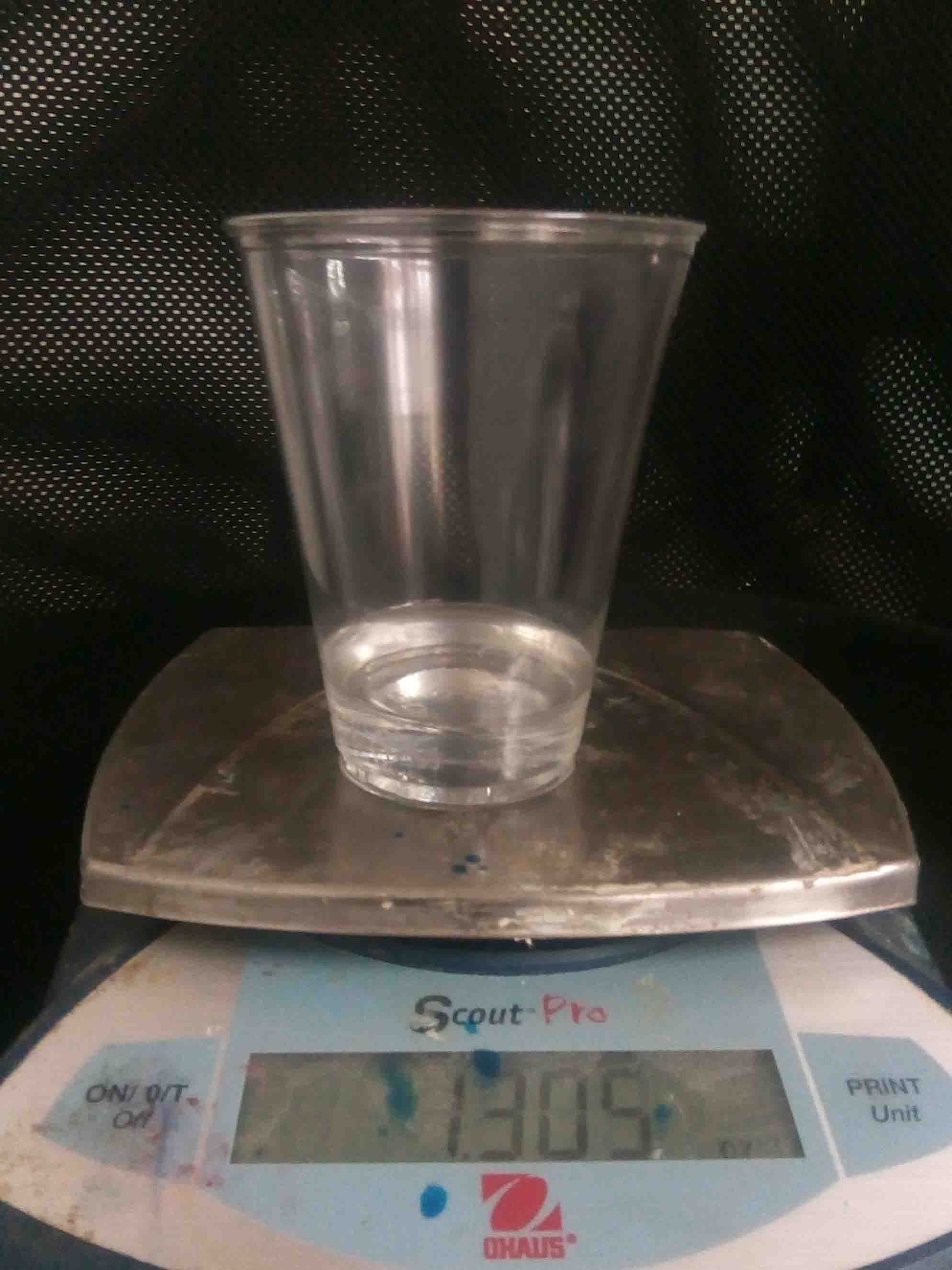
I mix both parts and stir it using a stick
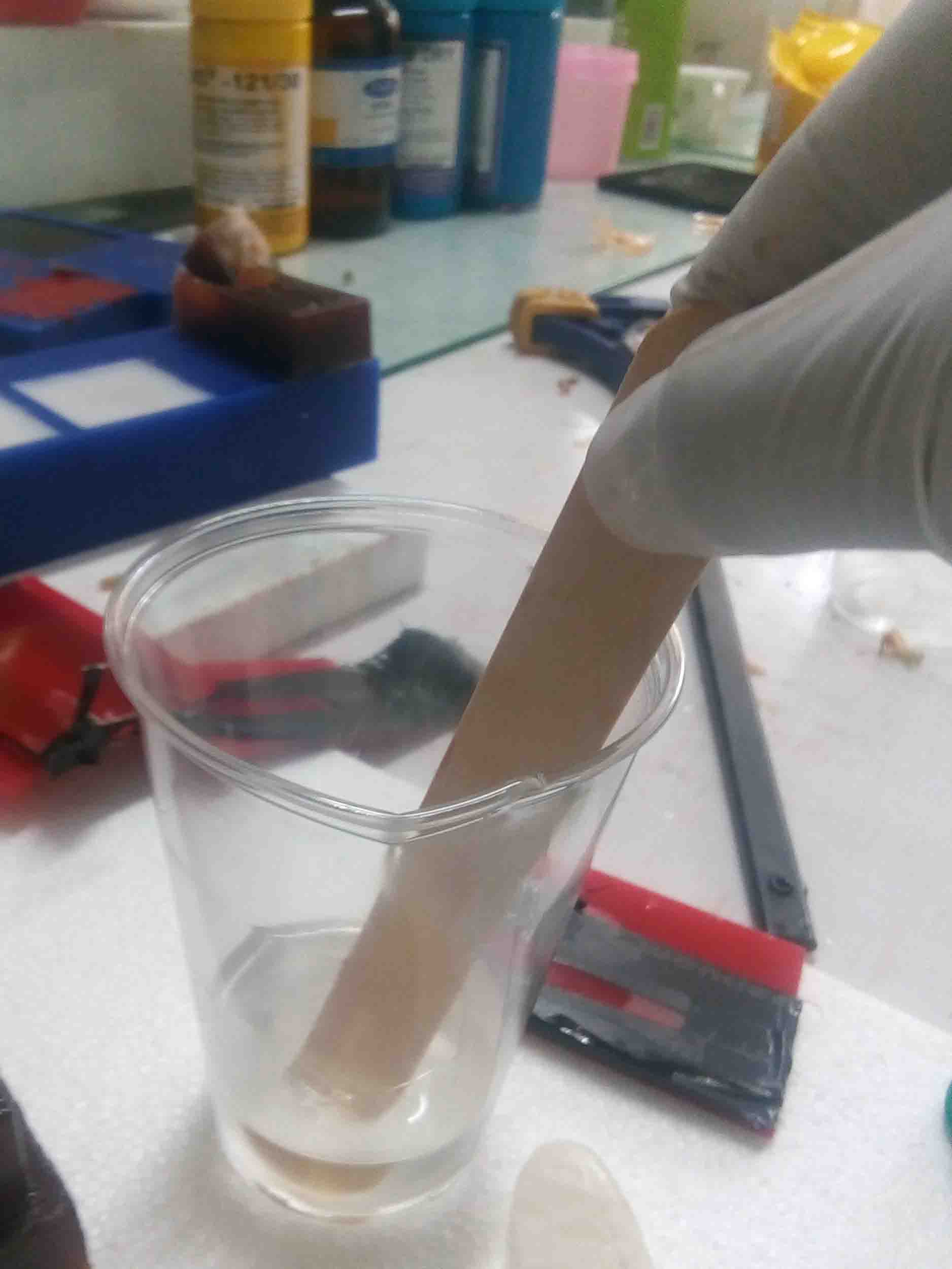
After curing time, i remove it from the -ve mold
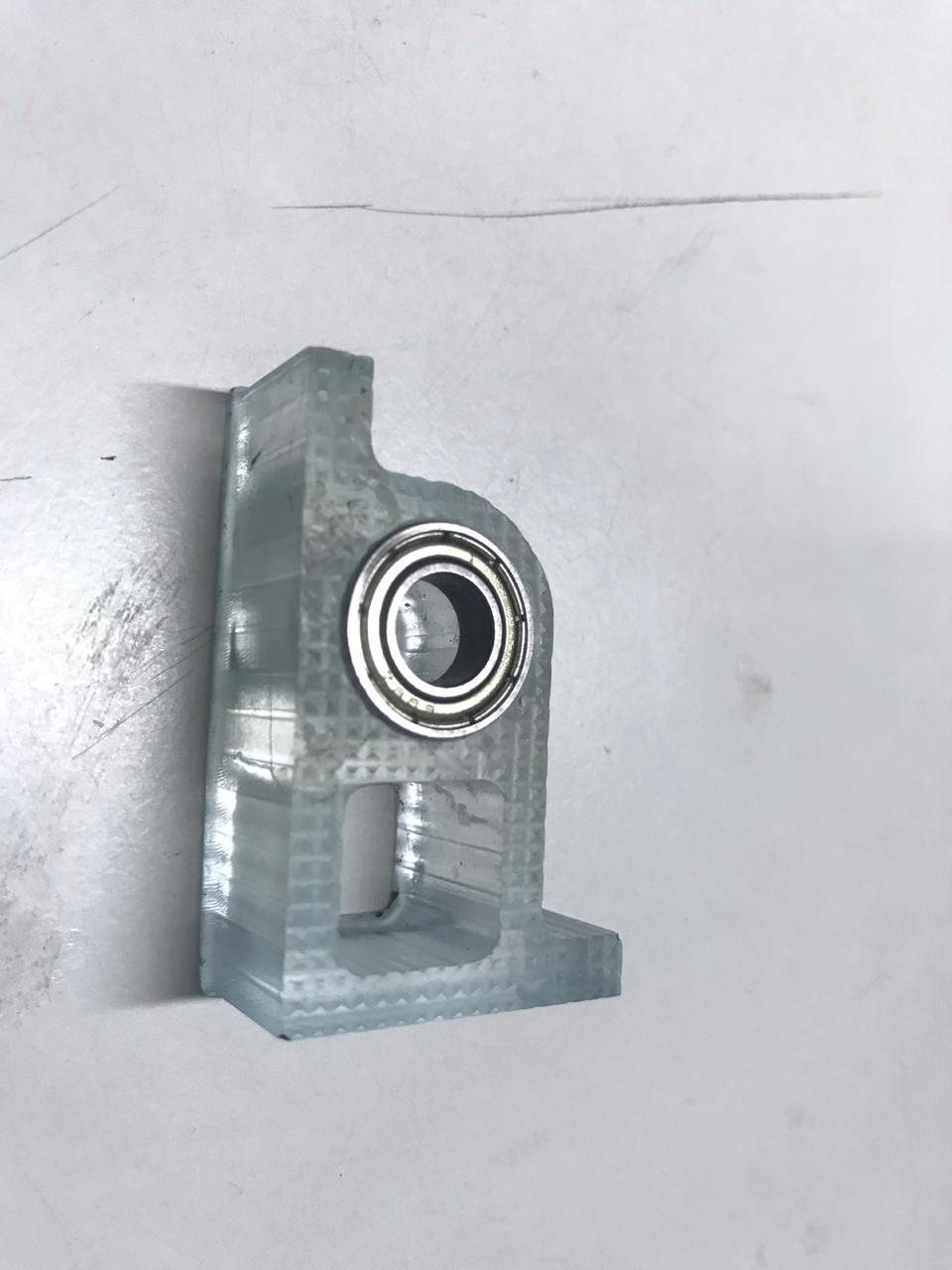
HERO SHOT
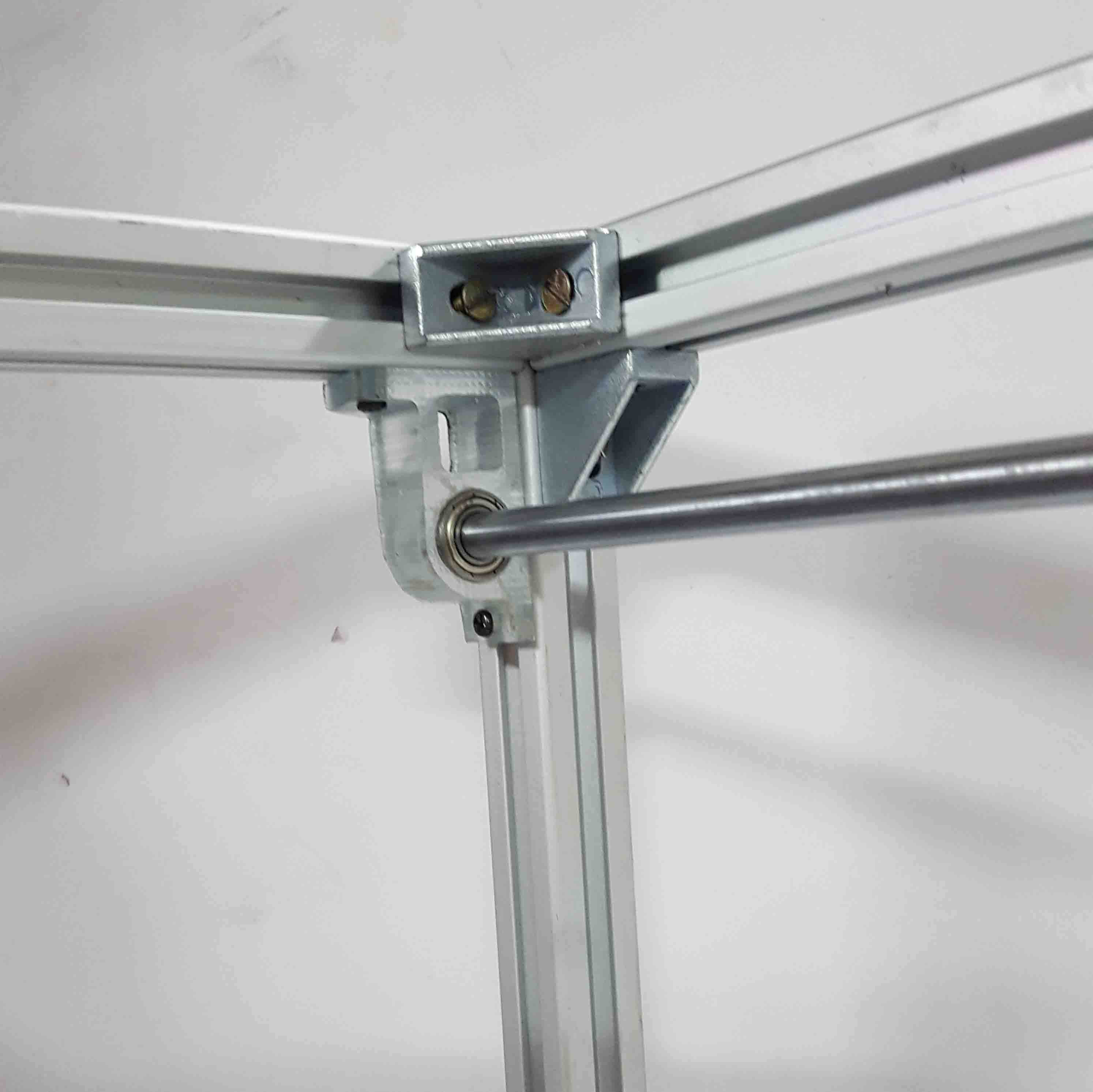
Group Assignment
Review the safety data sheets for each of your molding and casting materials, then make and compare test casts with each of them
Smooth Cast
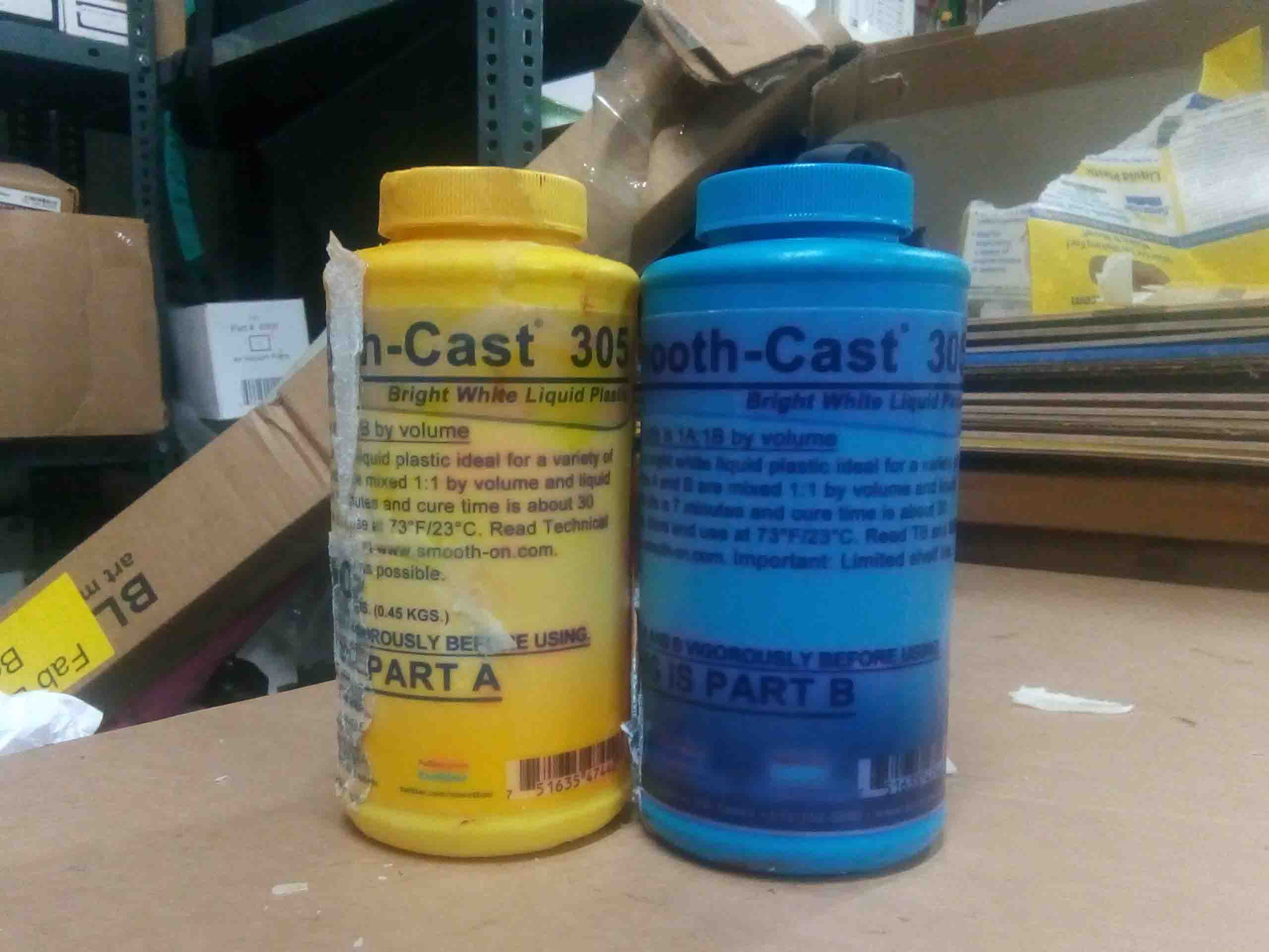
The Smooth-Cast™ 300 Series of liquid plastics are ultra-low viscosity casting resins that yield castings that are bright white and virtually bubble free. Vacuum degassing is not necessary. They offer the convenience of a 1A:1B by volume or 100A:90B by weight mix ratio. The differences between them are pot life and demold time
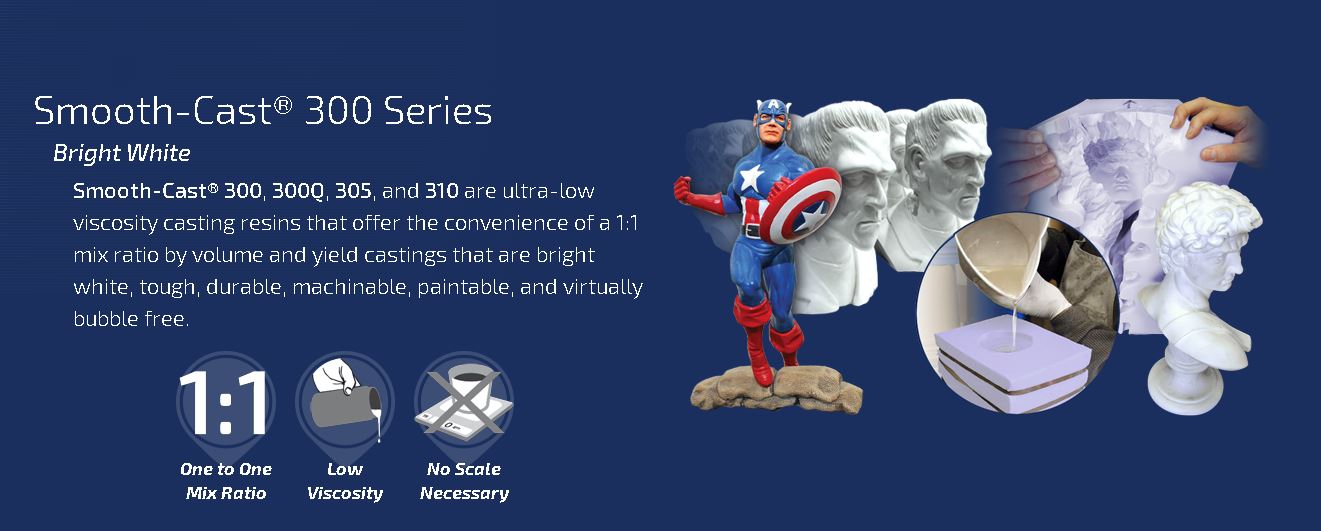
Instructions
- Applying A Release Agent- A release agent is necessary to facilitate demolding when casting into or over most surfaces. Use a release agent made specifically for mold making (Universal® Mold Release or Mann’s Ease Release® 200 available from Smooth-On or your Smooth-On distributor). A liberal coat of release agent should be applied onto all surfaces that will contact the plastic.
- IMPORTANT:To ensure thorough coverage, apply release and brush with a soft brush over all surfaces. Follow with a light mist coating and let the release agent dry for 30 minutes. Smooth-On silicone rubber molds usually do not require a release agent unless casting silicone into the mold. Applying a release agent will prolong the life of the mold.
- MEASURING & MIXINGLiquid urethanes are moisture sensitive and will absorb atmospheric moisture. Mixing tools and containers should be clean and made of metal, glass or plastic. Materials should be stored and used in a warm environment (73°F/23°C). Stir or shake both Part A & Part B thoroughly before dispensing. After dispensing equal amounts of Parts A and B into mixing container (100A:90B by weight) and mix thoroughly. Stir deliberately making sure that you scrape the sides and bottom of the mixing container several times. Be careful not to splash low viscosity material out of the container.
- POURING, CURING & PERFORMANCEPour your mixture in a single spot at the lowest point of the containment field and let the mixture seek its level. This will help minimize air entrapment.Best results are obtained using a pressure casting technique. After pouring the mixed compound, the entire casting assembly (mold, dam structure, etc.) is placed in a pressure chamber and subjected to 60 PSI (4.2 kg/cm2) air pressure for the full cure time of the material.Use this product with at least room size ventilation or in proximity to a forced outlet air vent and do not inhale/breath fumes. Fumes, which may be visible with a significant mass concentration, will quickly dissipate with adequate ventilation. Castings with significant mass may be hot to the touch and irritate skin immediately following cure. Let casting cool to room temperature before handling.
- SafetyMaterials should be stored and used in a warm environment (73° F / 23° C). These products have a limited shelf life and should be used as soon as possible. All liquid urethanes are moisture sensitive and will absorb atmospheric moisture. Mixing tools and containers should be clean and made of metal, glass or plastic. Mixing should be done in a well-ventilated area. Wear safety glasses, long sleeves and rubber gloves to minimize contamination risk. Because no two applications are quite the same, a small test application to determine suitability for your project is recommended if performance of this material is in question.
- InhalationRemove source(s) of contamination and move victim to fresh air. If breathing has stopped, give artificial respiration, then oxygen if needed. Contact physician immediately.
- Eye ContactFlush eyes with plenty of water. If irritation persists, seek medical attention. Skin Contact: In case of skin contact, wash thoroughly with soap and water.
- IngestionDo not induce vomiting unless instructed by a physician. Never give anything by mouth to an unconscious person.
(Source:https://www.smooth-on.com/products/smooth-cast-300/)
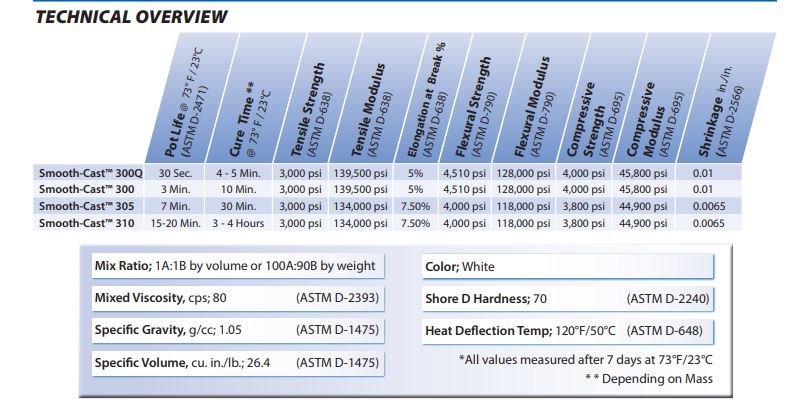
Casting Resin
For casting we are using Aditya Easy Cast Transparent Epoxy Resin - 33-750gm. It is very easy to use.
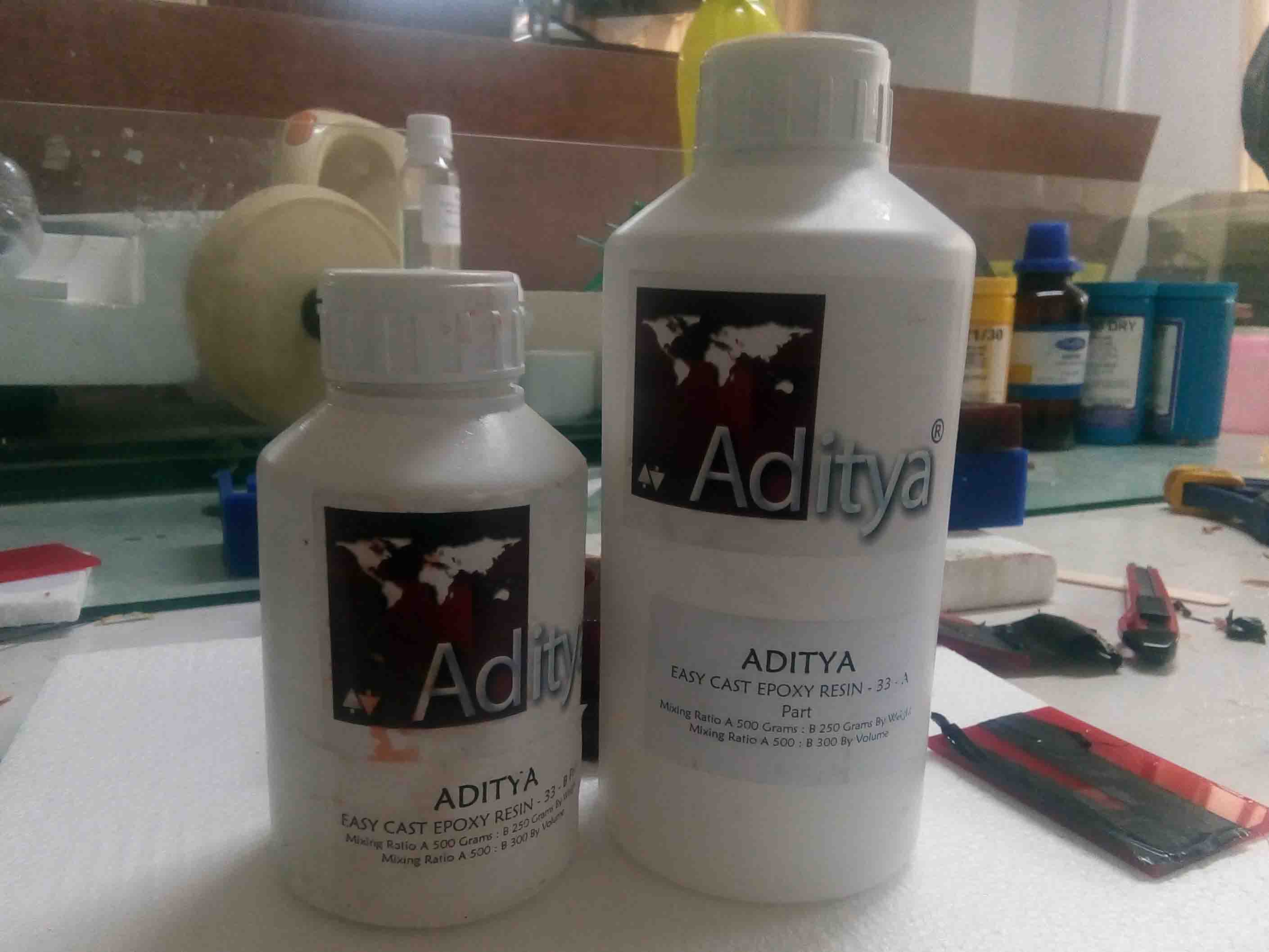
Description
Aditya Transparent Epoxy Resin is specially created for embedding and making small statue's casting. Ratio in Grams not ml....A Part 100 grams : B Part 50 Grams
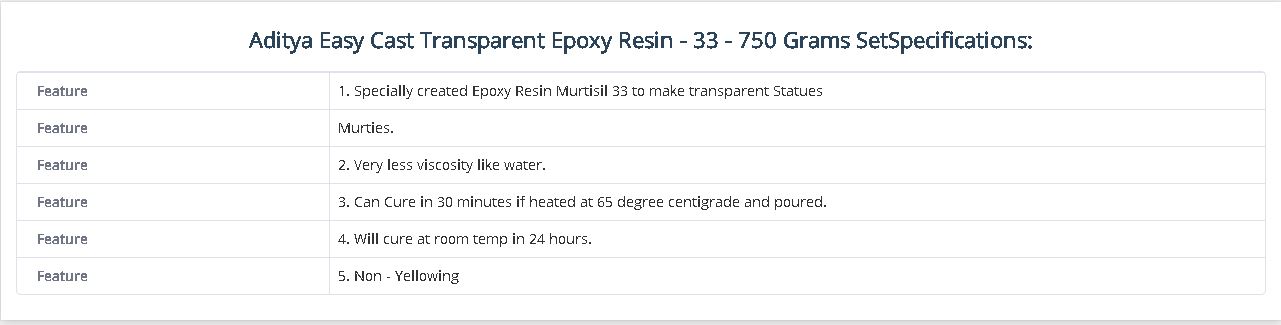