Assignment Ten: Molding and casting
This week's task is to make a part using silicone molding and urethane casting. An important requirement
is that the mold should be cut on the CNC using machinable wax. I had never done this before and I am
looking forward to it very much. Also, this week it is my responsibility to document the group project,
I have done so
here.
The assignment in steps:
Design a part and the mold positive
Cut the mold from machinable wax
Make the silicone mold and cast urethane
Here again, I used Onshape to design the part. I wanted to make a small
sippy cup but with no handles. So,
I designed a very basic one and placed in the centre of what would be the representation of a machinable wax block.
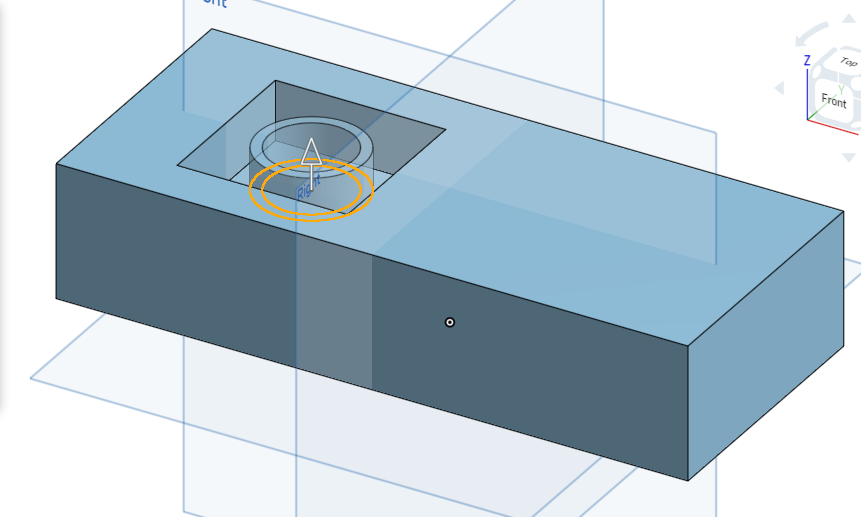
With that done, I opened the same design in Fusion 360 to make the Gcode for the cut. Initially, I made serious
mistakes by not doing a 3D clearing cut. After this, I was able to do a new toolpath that worked quite well.
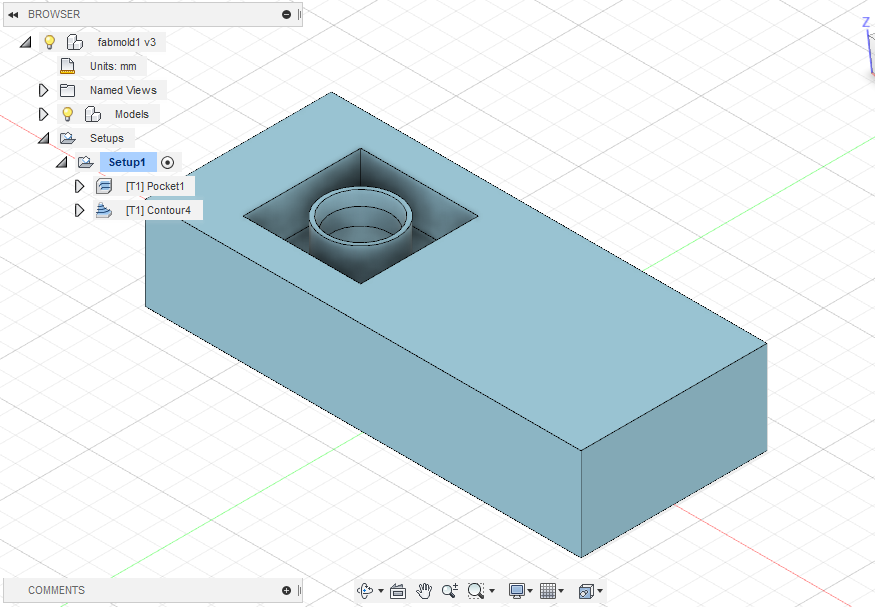
In the figure above, one can see that there are two cuts under the
Setup
tab: one is the 3D cut while the last is a 2D-type finishing pass. The finishing pass is quite important as it can
smooth the layers.
Reflection: I learnt a lot from my mistakes here, as I had initially
done a 2D cut (like during the make something big week) and realized that it did not clear the path and left
material on the pocket surface. This week helped me understand the usefulness of CNC milling and how it is
important to get the operations correct right from inside Fusion 360.
After saving the Gcode (the file is available
here), I ran it on the CNC mill quite easily.
First, mixing the two parts of the mixture is so important. To be really accurate, one can mix using
weights and measure this with a spring balance, in my case I simply mixed by volume. Sometimes the ratios
are different.
Silicone molding and urethane casting is a very chemical process and it all depends on the nature of
the chemicals used, so it is quite important to read the datasheet. After mixing, I poured the mixture into
the wax positive mold and waited for a day for it to cure. It gave some very good results, in fact the same
grooves from the finishing contour pass can be seen on the silicone mold.
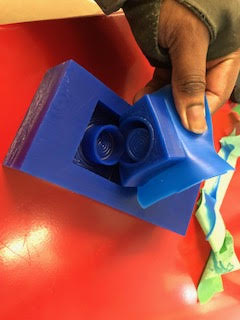
Once I got the negative silicone mold, the next step was to mix urethane and pour it into the mold.
Reflection: Mixing is so important! And one has to be very careful
when pouring the chemicals in to make sure that they are no bubbles in the mix. For more creative molds,
making a sprue with vents will be the best idea so that the bubbles are forced out of the place.