Computer Controlled Cutting
Assignment
To characterize our laser cutter, making test part(s) that vary cutting settings and dimensions.
Goals
To make templates of different materials with which we can document and visualize the varying
parameters for laser cutting and etching.
At the end of this group work, we will have a chart of materials and their respective optimized
setting for cutting/etching on our laser cutter.
Laser Cutter Specs
SIL-1290
Specs
- Brand: SIL
- Model No: SIL-1290
- Laser Type: Co2 DC glass laser tube
- Laser power: 100 watt
- Wavelength: 10.6 um
- Supply voltage: AC 220 V + 10%
- Re-positioning accuracy: 0.1 mm
- Cutting speed: 0~30000 mm / min
- Engraving speed: 0~64000 mm / min
- Cooling method: Water cooled
- Work environment: Temp: 0 c ~ 45 c. humidity: 5% ~ 95%
- Acceleration speed: 1 G
- Working area: 1200×900 mm
- Graphics file support: .PLT, .CDR, .AI, .DWG, .DXF, .DST, .BMP, .JPEG, .TIFF, .GIF, .PCX, etc.
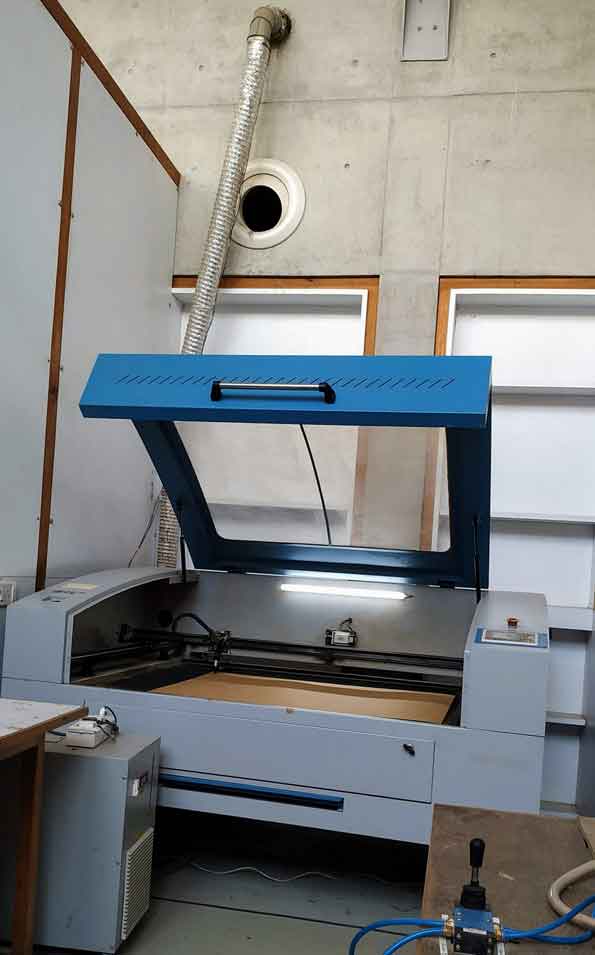
Epilog Mini
Specs
- Brand: Epilog
- Model No: Epilog Mini 24
- Laser Type: State-of-the-art, digitally controlled, air-cooled CO2 laser tubes are fully modular, permanently aligned and field replaceable.
- Laser power: 40 watt
- Motion Control System: High-speed, continuous-loop, DC servo motors using linear and rotary encoder technology for precise positioning.
- Resolution: User controlled from 75 to 1200 dpi.
- Supply voltage: AC 220 V + 10%
- Cooling method: Air Cooled
- Working area: 610 x 305 mm
- Operating Modes: Optimized raster, vector or combined modes.
- Normal Sound Level: 59 db
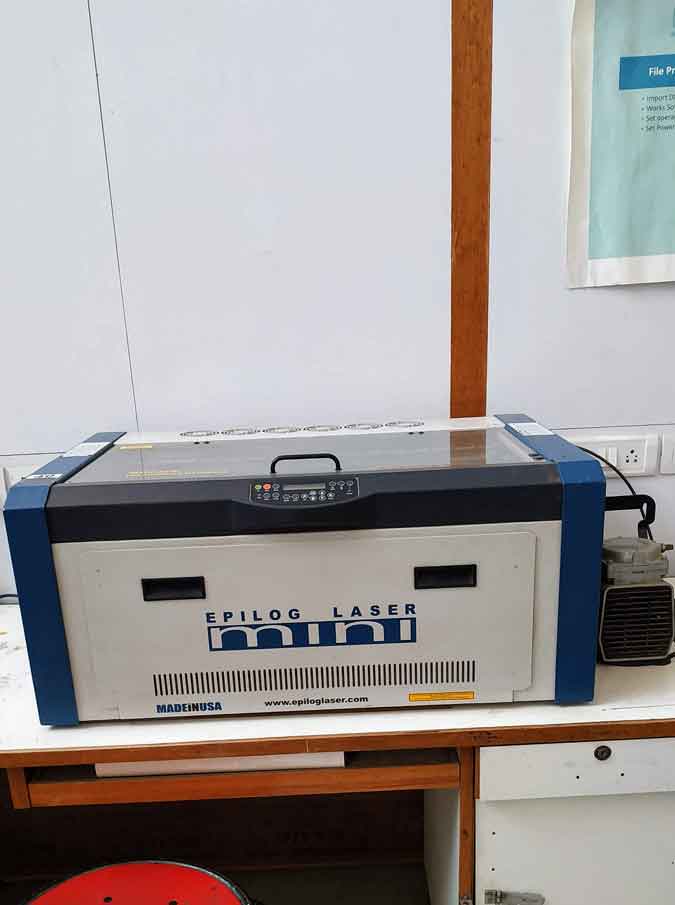
Designing a Test Template
We took inspiration from Nolox's Laser Cutting Material Design Template from thingieverse and started to design our own template in AutoCAD 2007 with all the parameters we wanted to test.

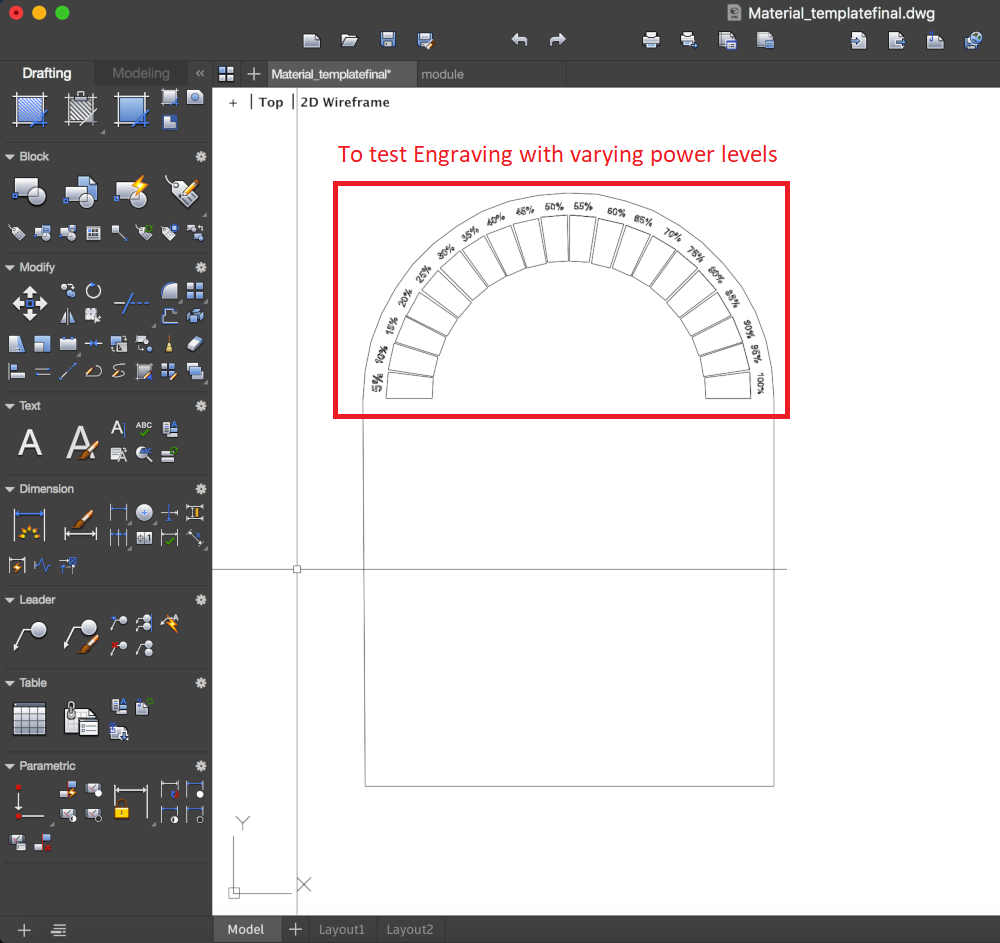
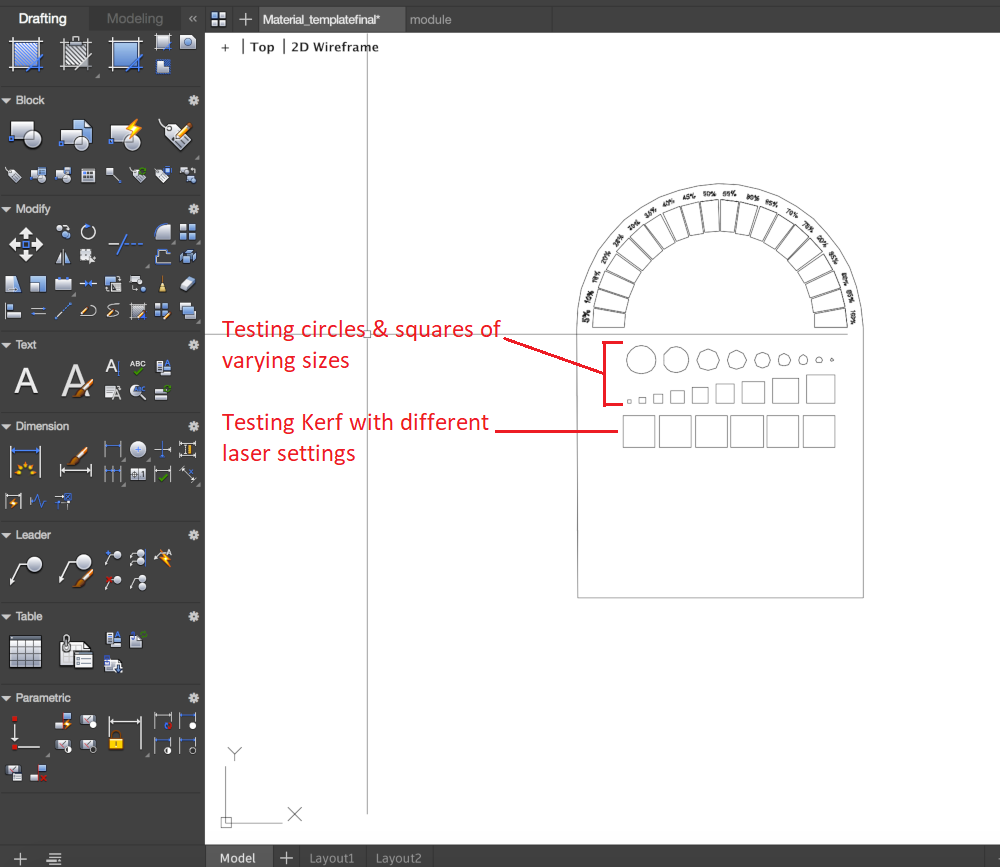
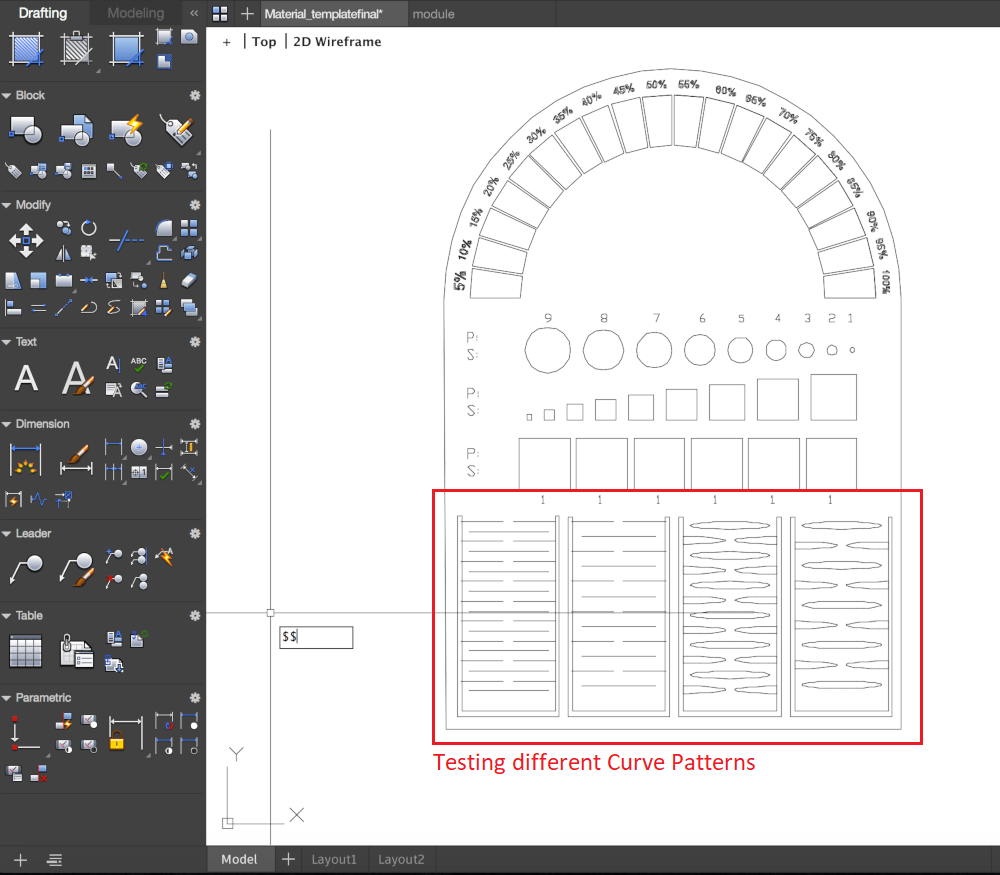
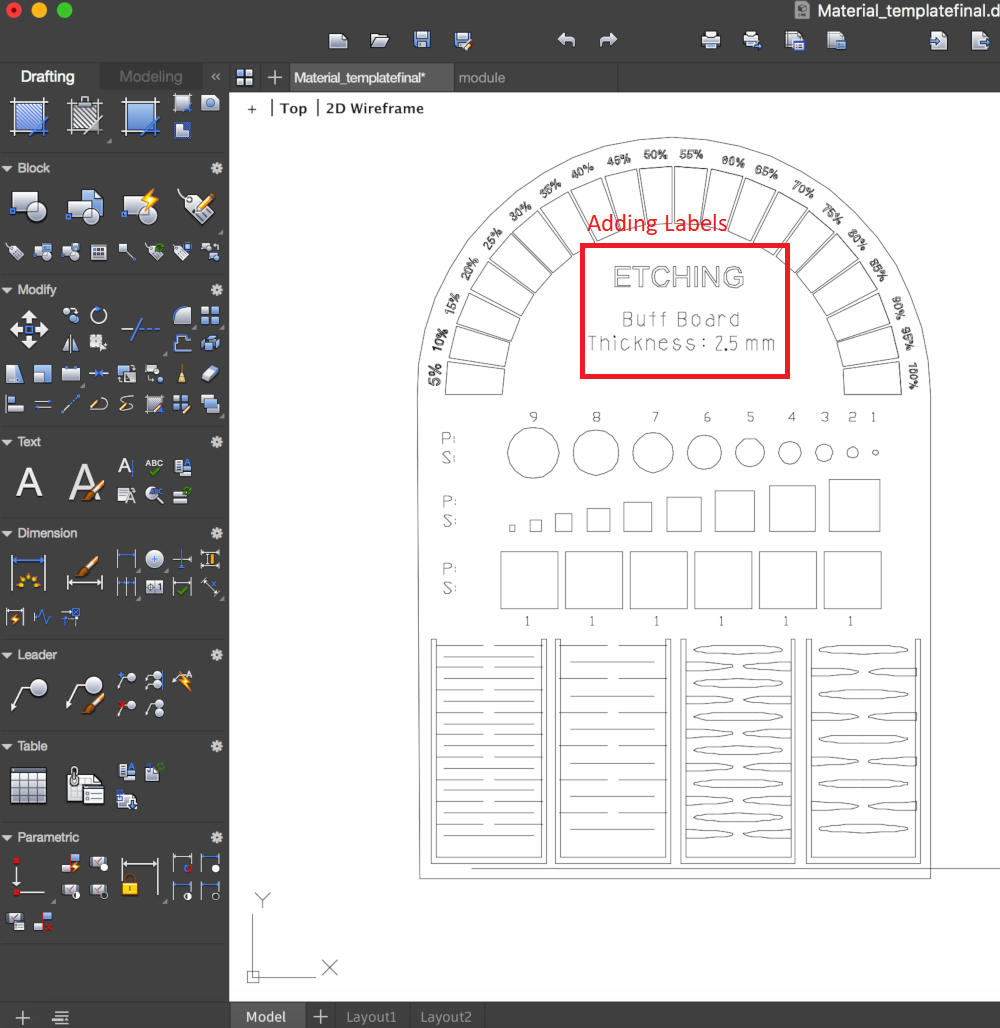
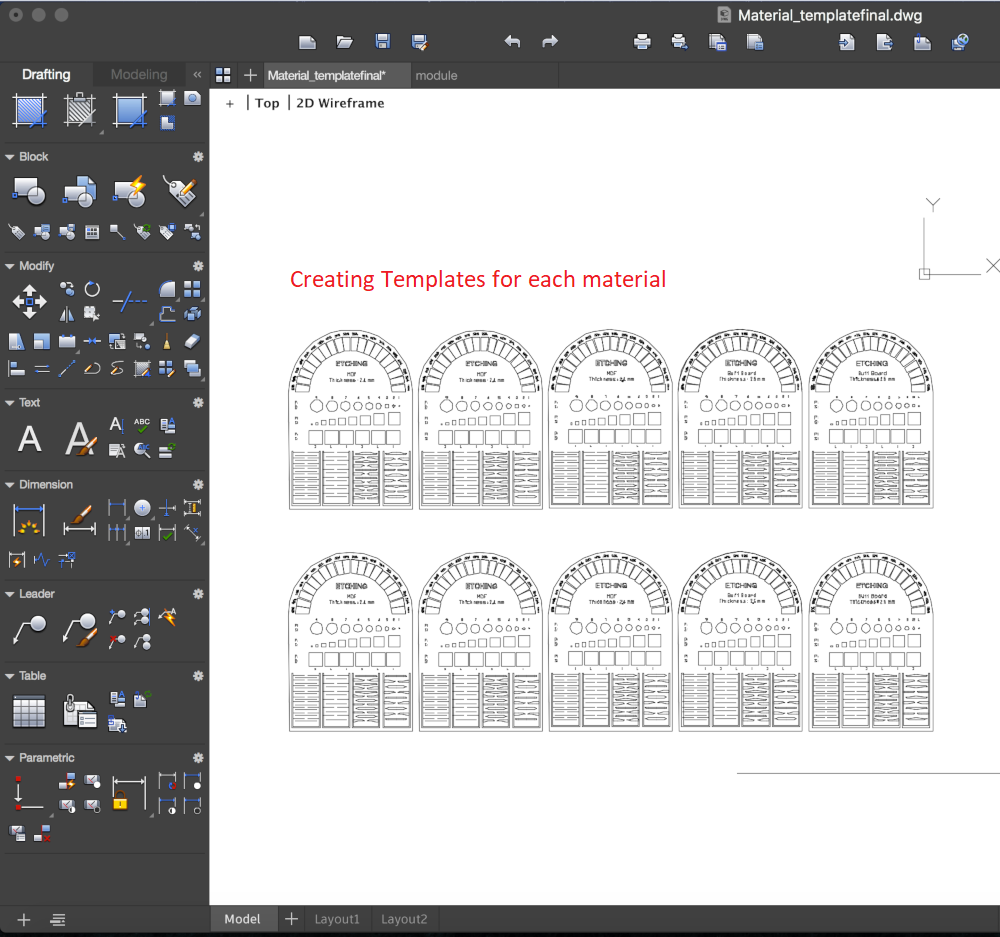
Laser CAM Software: RD-works
Since our template required so many different settings, we had to use multiple colored layers to stack all the power settings. RDworks has a limited number of layers and so it became very time consuming to cut even one template.
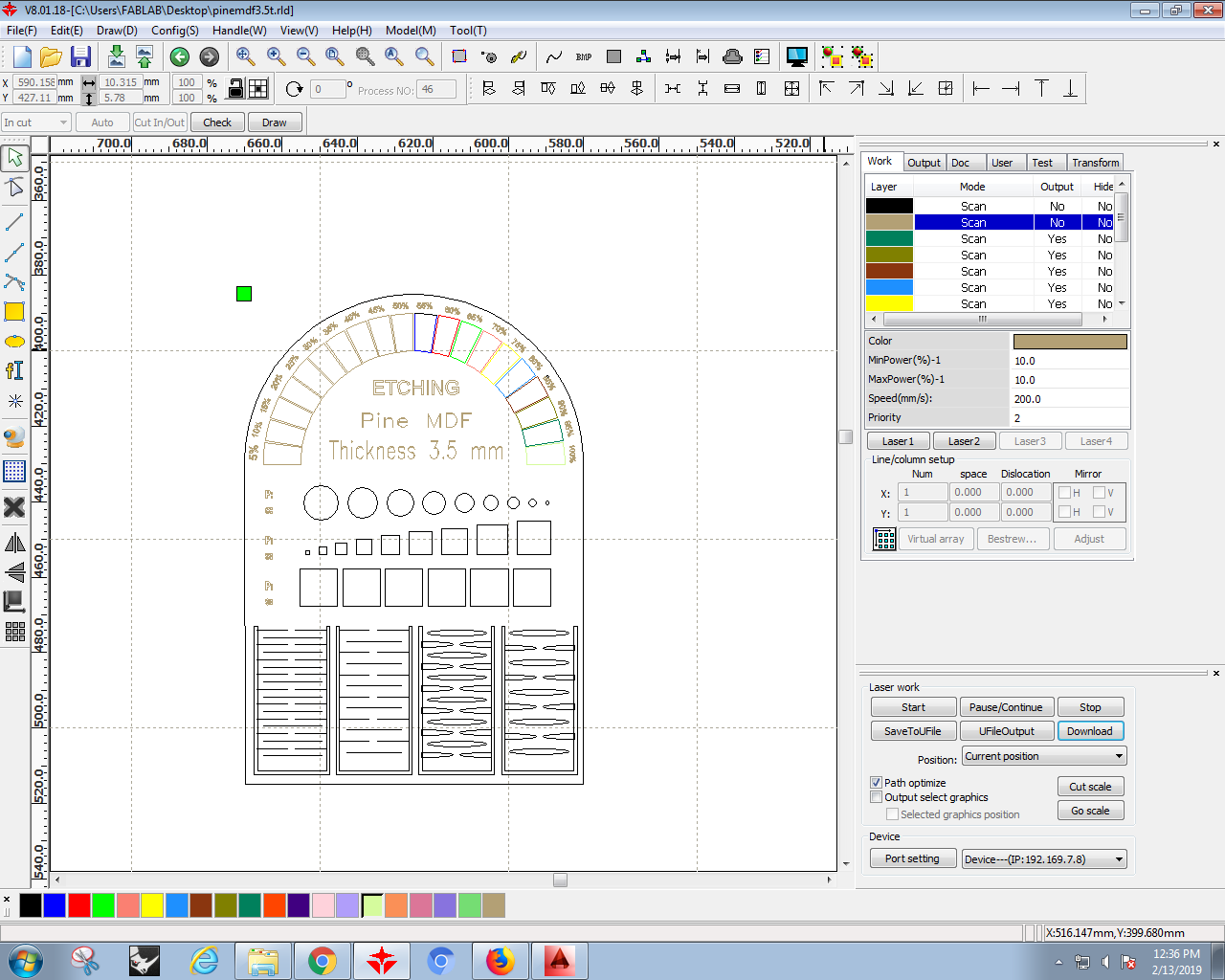
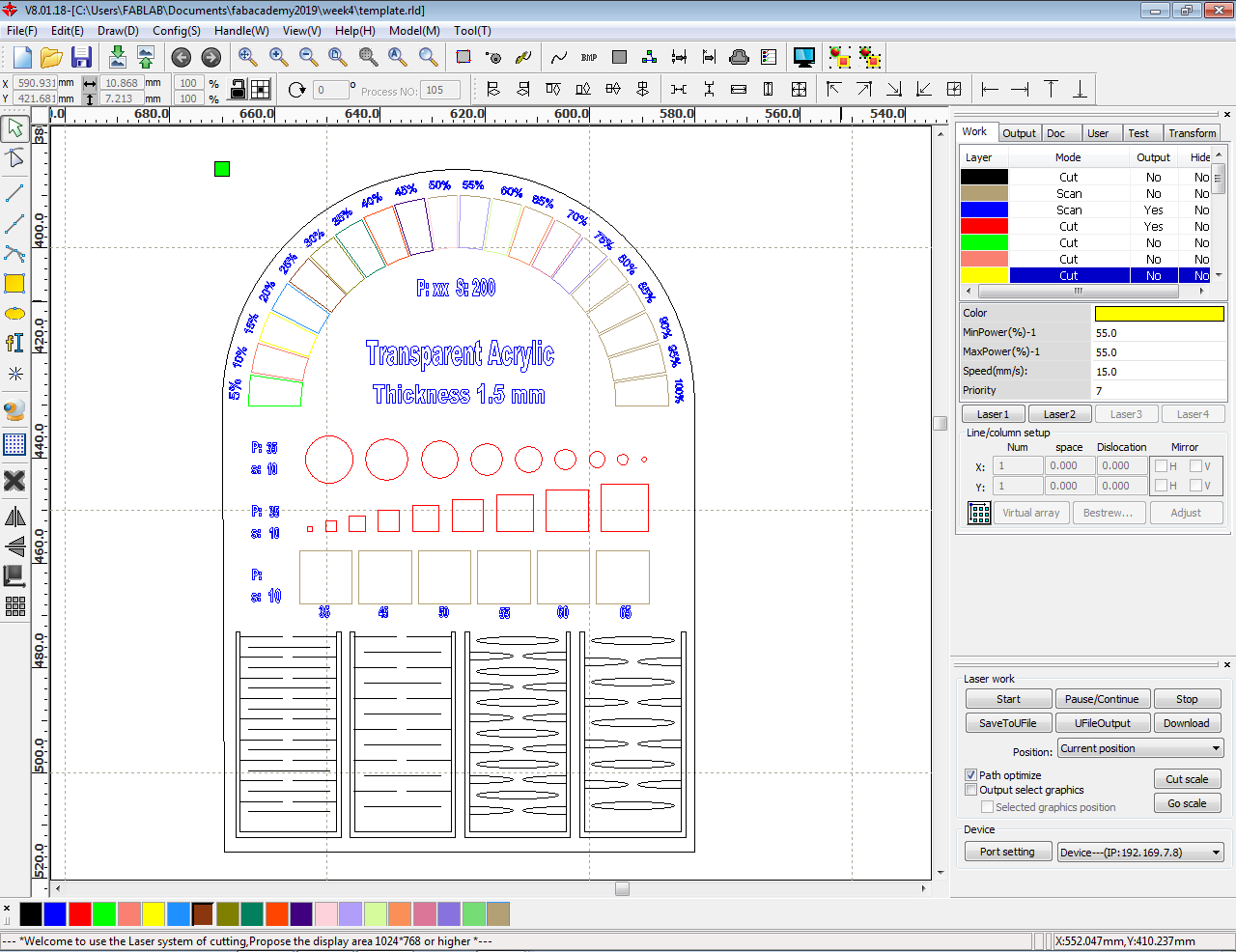
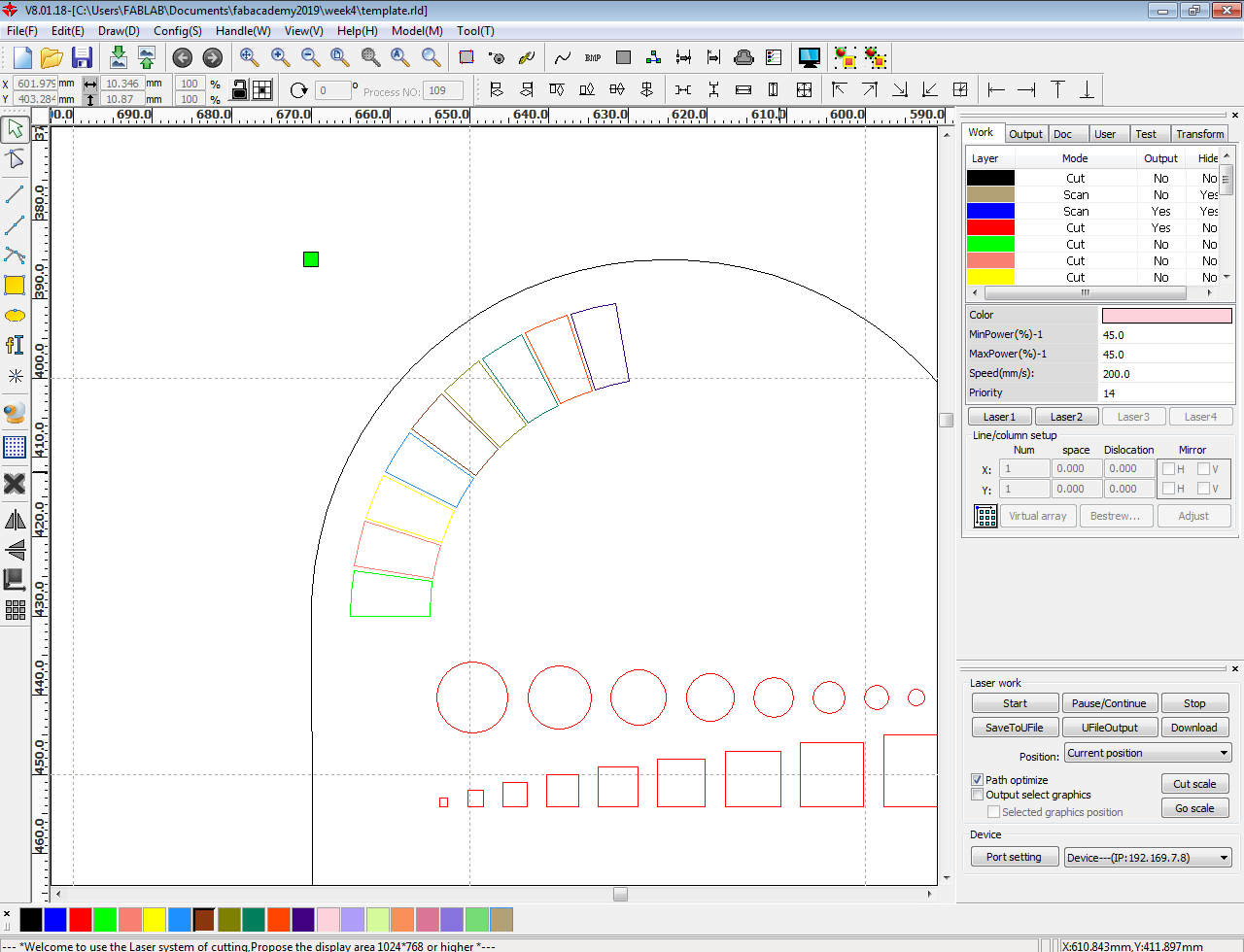
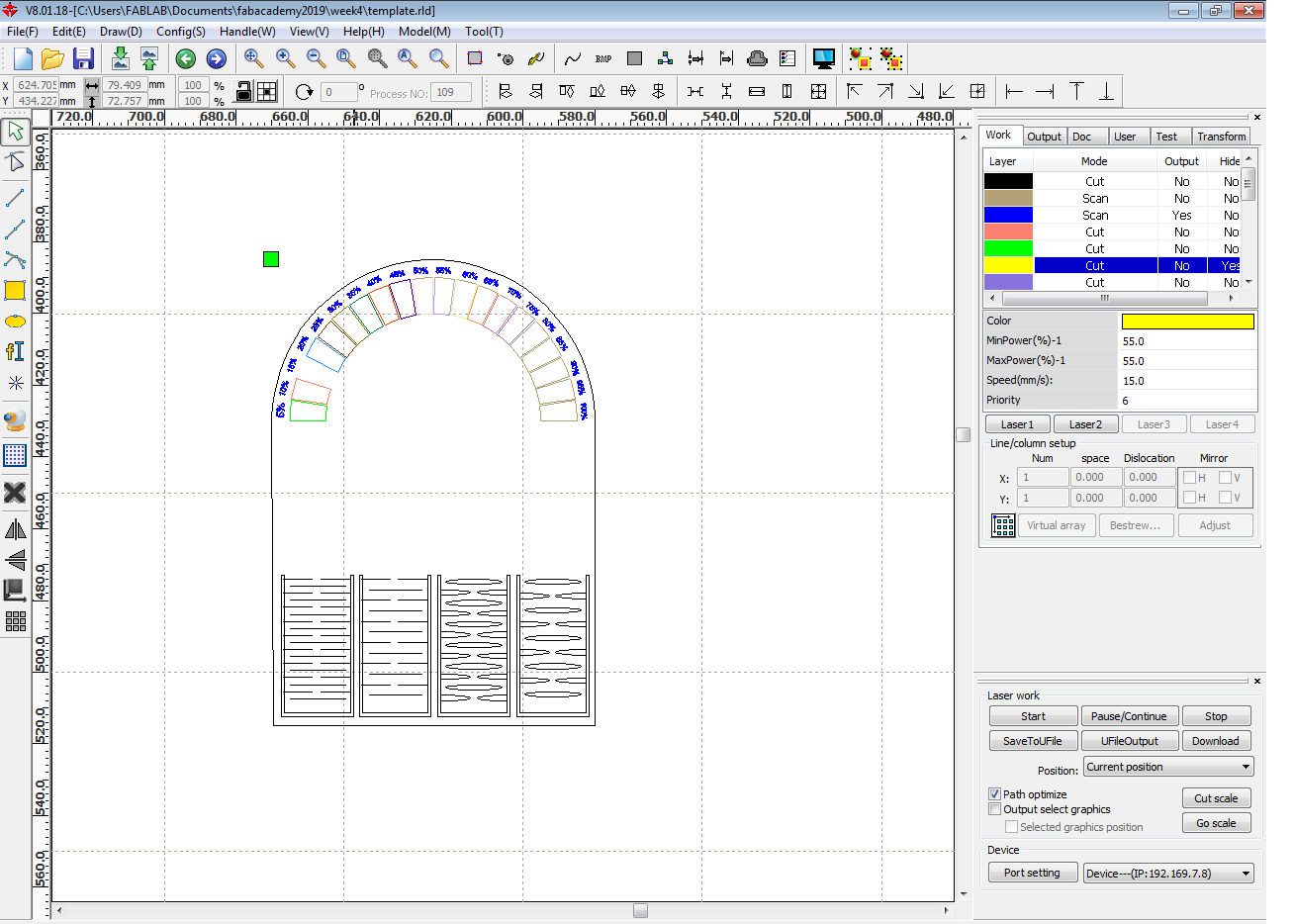
Collected Materials
Acryllic (transparent) | 1.5 mm |
Buff Board | 2.5 mm |
MDF | 3.5 mm |
Concrete Board | 2 mm |
Mill Board | 2 mm |
Laser cutting test on Acrylic:
We Started with 1.5mm clear white acryllic. We were extra careful while cutting plastic as it released harmful fumes.
Observations:
Thickness of material | 1.5 mm |
Optimum Power for cut | Power max: 40 % Power min: 35 % |
Speed for cut | 10 mm/s |
Optimum Power for Texts and etching | Power max: 7 % Power min: 40 % |
Speed for text | 200 mm/s |
Etching test Results | only up to 70 % power |
Minimum diameter that can be cut | 1 mm |
Kerfing | 0.07 mm |
Minimum text can be cut | Font Size 4 |
Living hinges | Living hinges work, but not the best material for it because it breaks easily. |
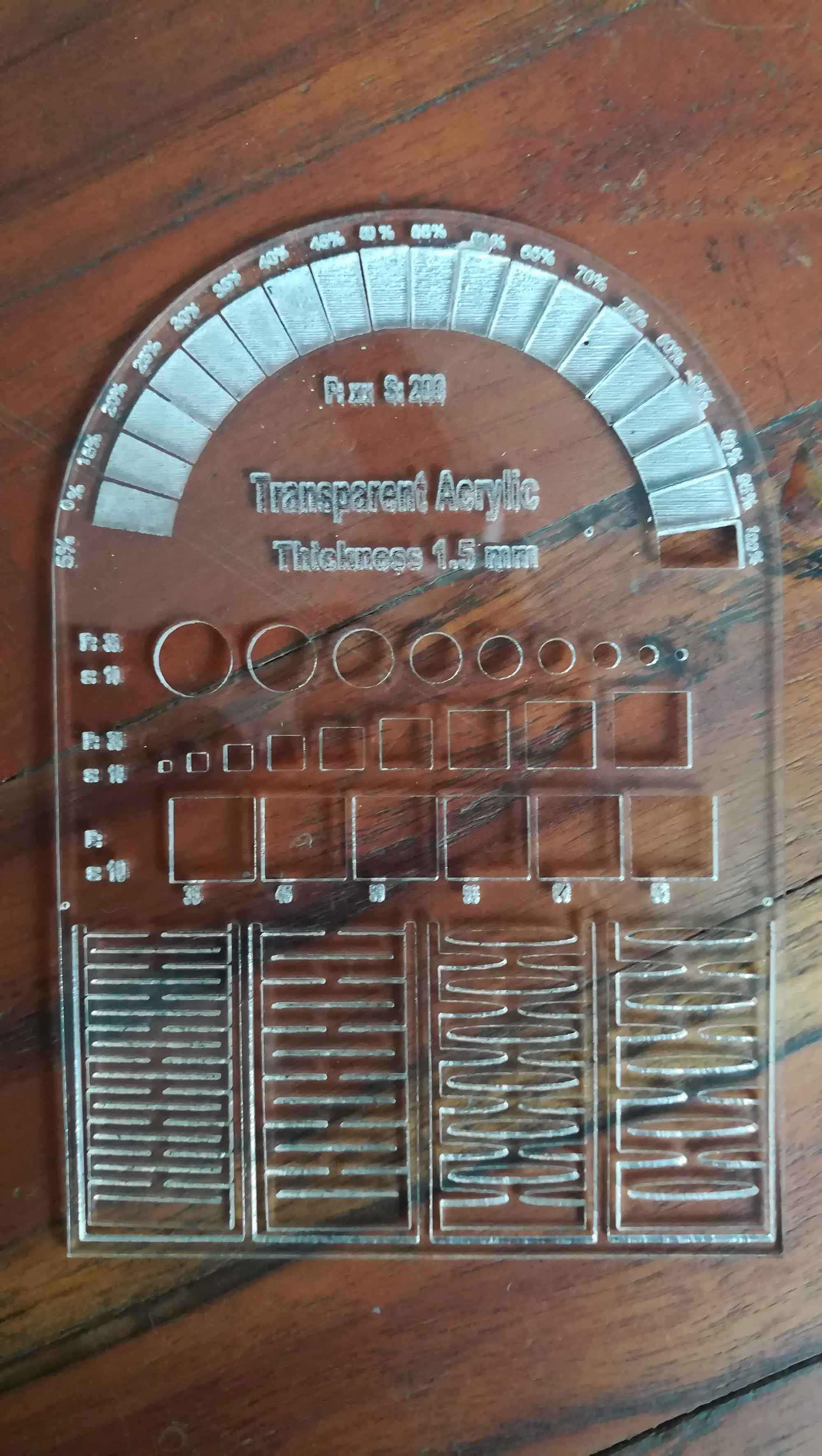
Laser Cutting test on Buff board :
Next we tried buff board. It is paper based and has a very thick consistency.
Observations:
Thickness of material | 2.5 mm |
Optimum Power for cut | Power max: 40 % Power min: 35 % |
Speed for cut | 50 mm/s |
Optimum Power for Texts and etching | Power max: 12 % Power min: 8 % |
Speed for text | 200 mm/s |
Etching test Results | only up to 35 % power, it starts charring and burning after that and completely burns throuh at 60% power. |
Minimum diameter can be cut | 1 mm |
Kerfing | 0.14 mm |
Minimum text can be cut | Font size 4 |
Living hinges | Much better material for hinges, but very soft. It is not as brittle as acryllic. |
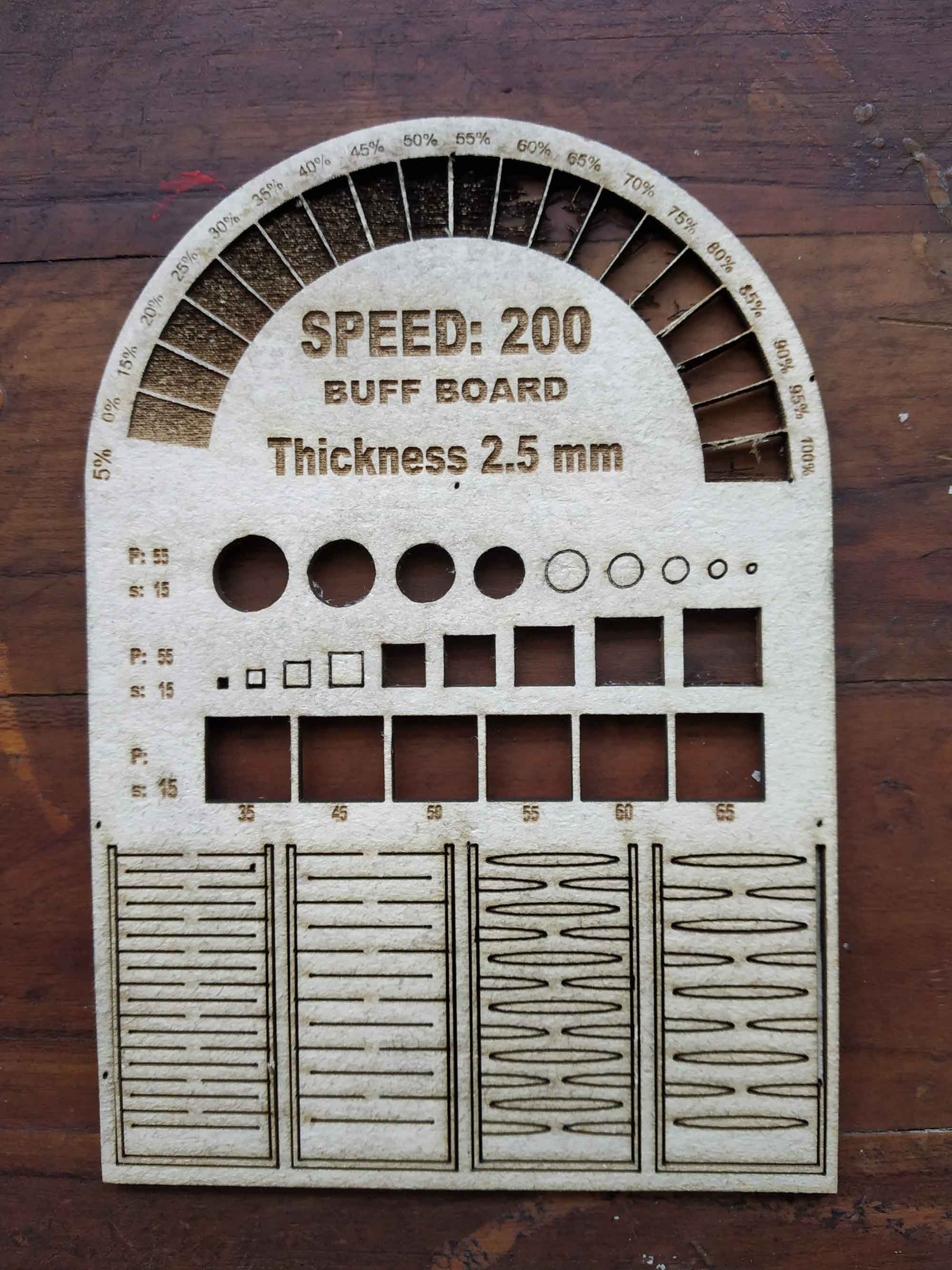
Laser cutting test on MDF:
Observations:
Thickness of material | 3.5 mm |
Optimum Power for cut | Power max: 55 % Power min: 50 % |
Speed for cut | 10 mm/s |
Optimum Power for Texts and etching | Power max: 15 % Power min: 5 % |
Speed for text | 60 mm/s |
Etching test Results | Works upto 100% power but heavy charring begins from 65% power. |
Minimum diameter can be cut | greater than 0.5 mm |
Kerfing | around 0.09 mm |
Minimum text can be cut | Font size 4 |
Living hinges | good material for living hinges but heavy charring occurs in single pass cut. |
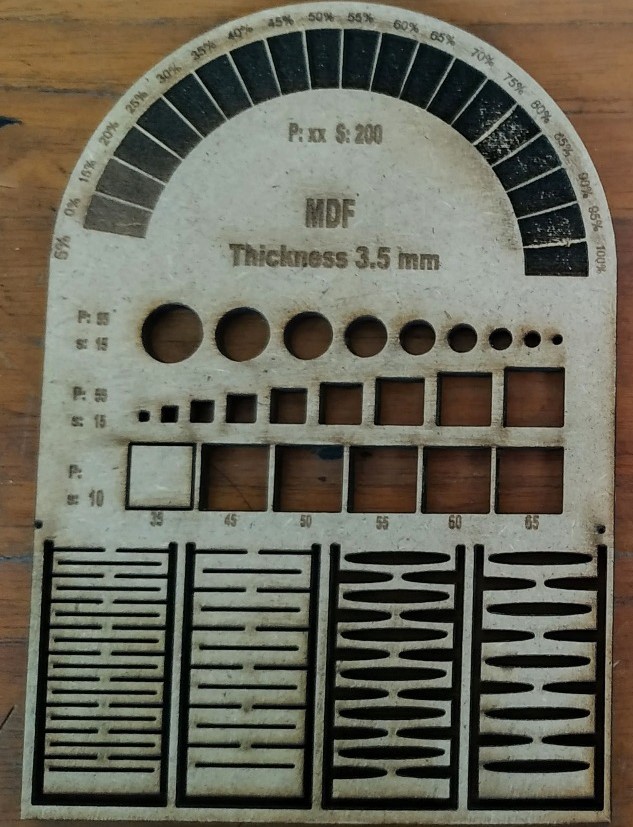
Laser cutting test on Concrete board:
Observations:
Thickness of material | 2 mm |
Optimum Power for cut | Power max: 35 % Power min: 35 % |
Speed for cut | 22 mm/s |
Optimum Power for Texts and etching | Power max: 10 % Power min: 7 % |
Speed for text | 200 mm/s |
Etching test Results | Up to 70 % power, it starts burning through after that. Minimum charring was observed. |
Minimum diameter can be cut | circles are hard to cut in 22 mm/s speed |
Kerfing | around 0.11 mm |
Minimum text can be cut | 1.5 mm |
Living hinges | Very flexible with minimum charring. Very good material for hinges. |
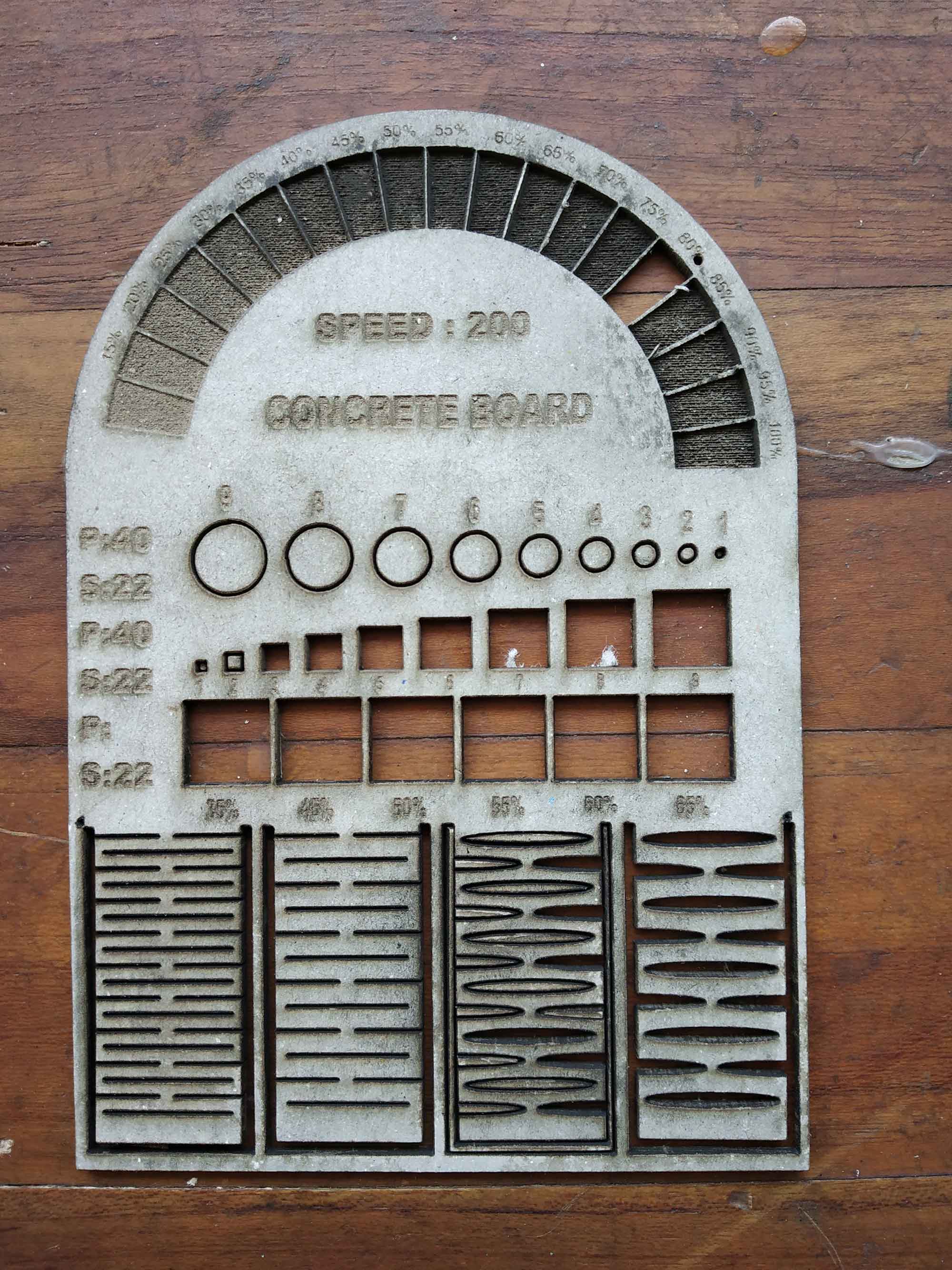
Laser cutting test on Mill Board:
Observations:
Thickness of material | 1.8 mm |
Optimum Power for cut | Power max: 45 % Power min: 15 % |
Speed for cut | 15 mm/s |
Optimum Power for Texts and etching | Power max: 10 % Power min: 7 % |
Speed for text | 200 mm/s |
Etching test Results | Upto 60% laser power. Heavy charring occurs after that and starts cutting through at 75%. |
Minimum diameter can be cut | Upto 1 mm diameter cut properly |
Kerfing | around 0.09 mm |
Minimum text can be cut | 1.5 mm |
Living hinges | Living hinges are Flexible and workable. |
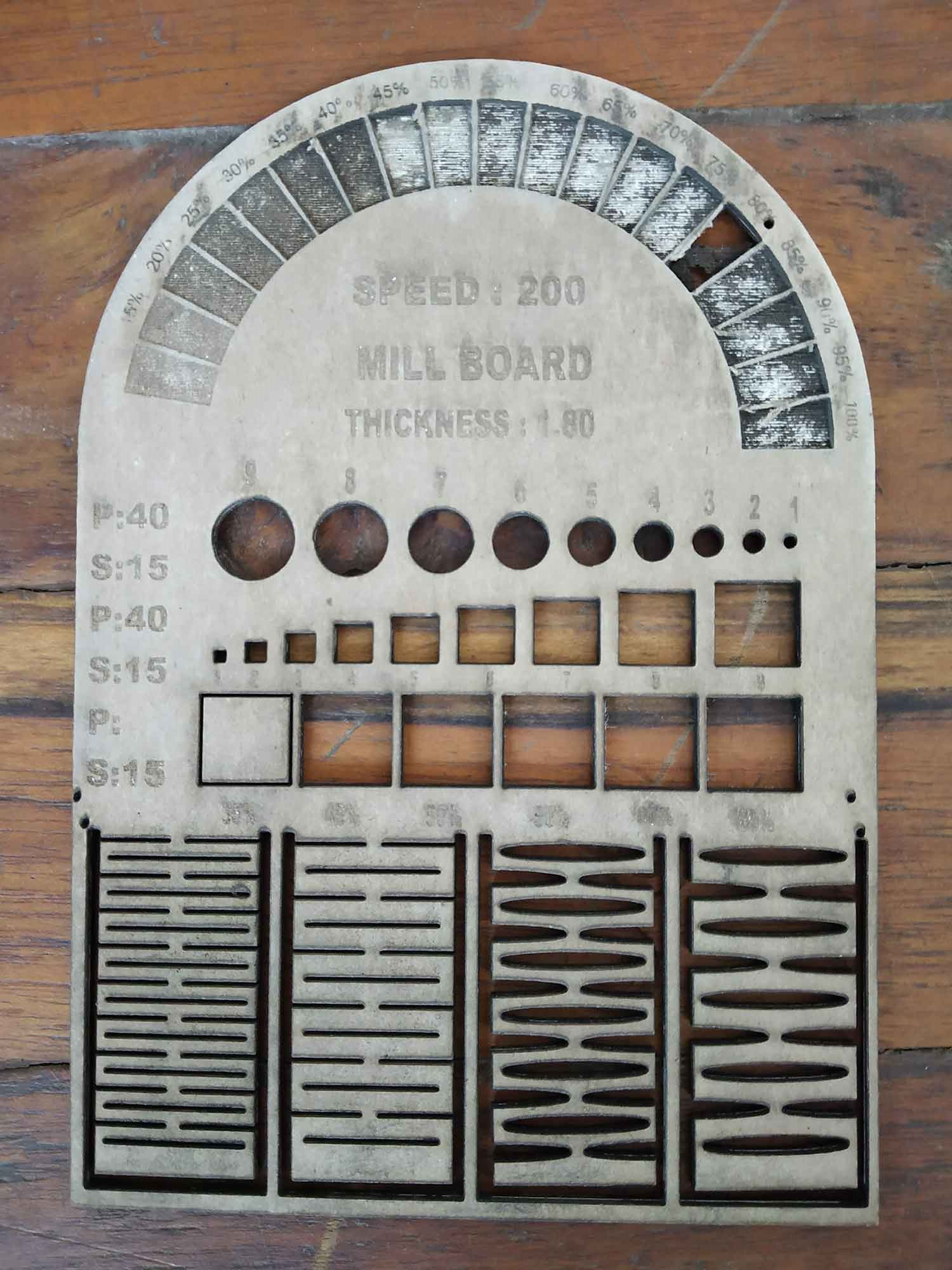