Seonghee Kim | |
6. 3D Scanning And Printing | |
HOME | ABOUT | ASSIGNMENTS | FINAL PROJECT| CONTACT | |
Week6
AssignmentS
-group assignment
test the design rules for your 3D printer(s)-individual assignment
design and 3D print an object (small, few cm) that could not be made subtractively
3D scan an object (and optionally print it)
Hardware and Softwares used
-Fusion 360
-Cura Creatable
-Creatable D2
-Kinect scanner
-Maker Bot
Outcome
I have tried 3D printing and 3D scanner before. This time We tried various types of printing value togeter such as length of T branches, slopes, bridges, joints. After some expriment, I got to know which value is good for 3D printing.
3D Printing
I tested the length of T branches and circle joints. For 3D printing, I have to do 3 steps; to design on Fusion 360, import to cura to make G-code, print on a creatable D2. Seoul Fab Lab use PLA 1.75mm
Tolerance Test: 3Ts on Creatable D2
To see how long T branch could be printed caccurate without support. T needs support even only 10mm.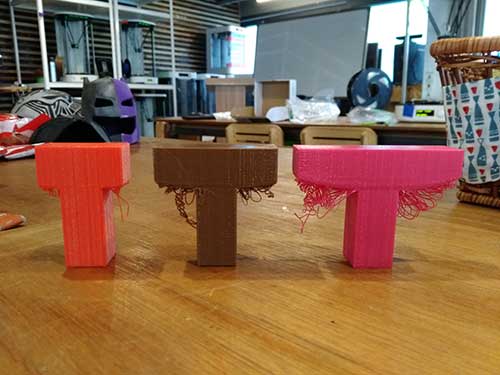
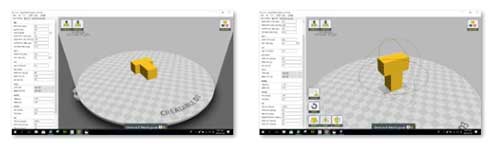
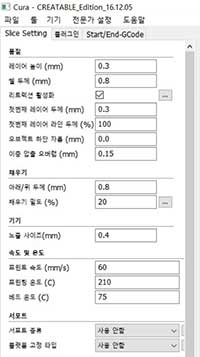
Test 3 Circle Joints
I want to make the firm circle joint, not loose one. So I tested 3 diffrent gap values. The hole of joint is smaller than the circle joint, it can not make substractively.
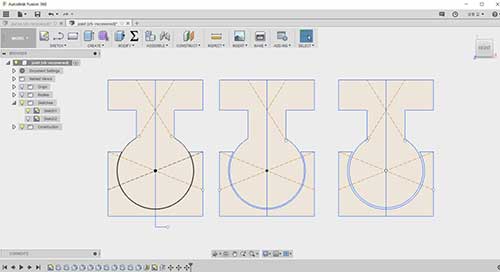
-From left 0.3mm gap, 0.6mm gap, 0.9mm gap
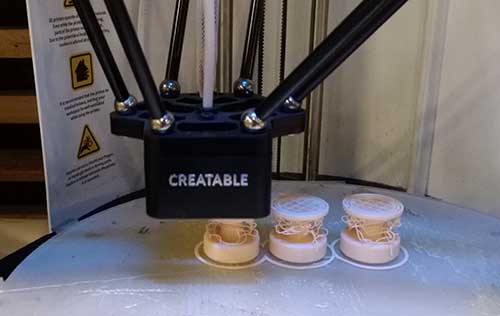
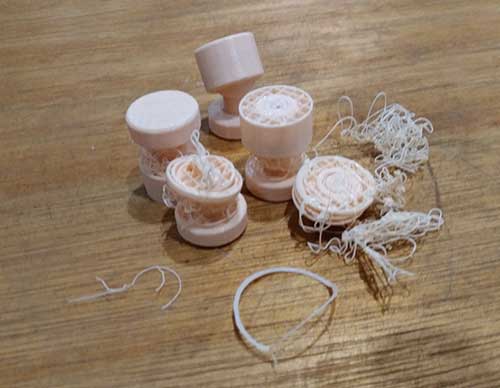
-Too many run downs I can see, I need a support.
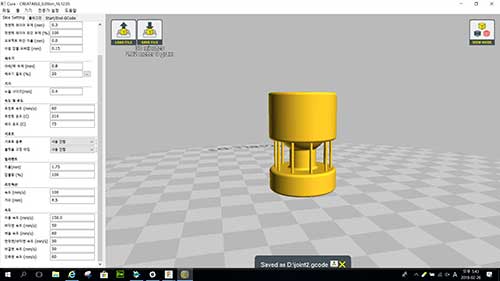
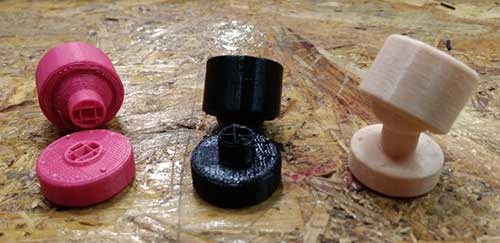
-Gap 0.3mm, 0.6mm joints are to tight so that it broken when I tried to turn it. Gap 0.9mm joint is nice to turn, but was not firm enough to stay.
Modeling and print object suitable for additive design.
I design the flexible fabric-like 3d print. I printed 2 types of design and tried to make a small purse. Those are consited with elements linked together with rings before it manufautred. so it is strong and flexible.
Fabric type 1.
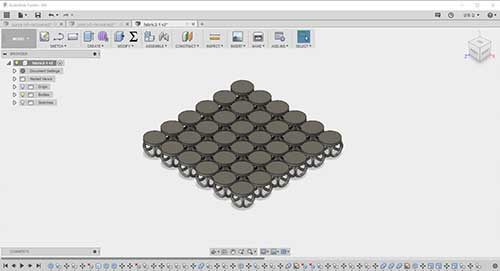
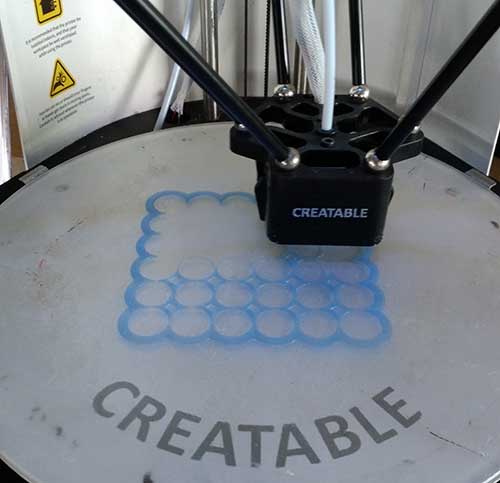
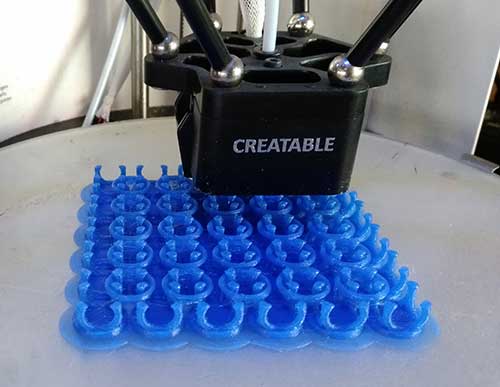
-Printig rings for flexbilty.
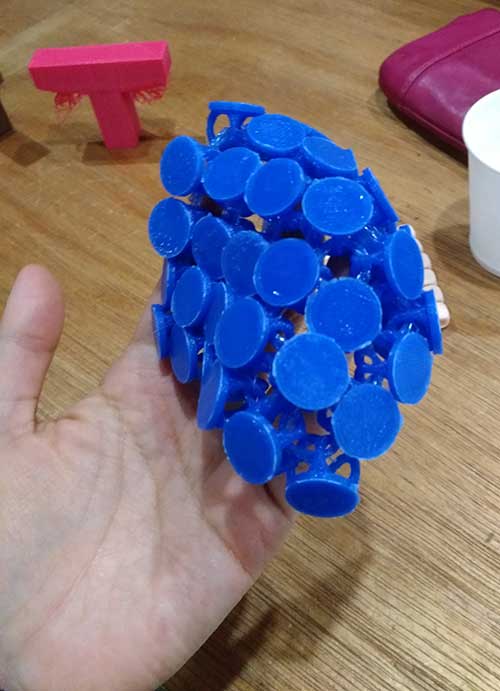
-After taking off the brims.
Fabric type 2.
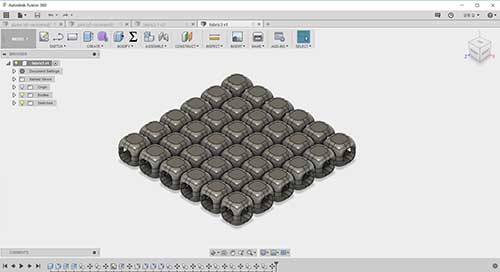
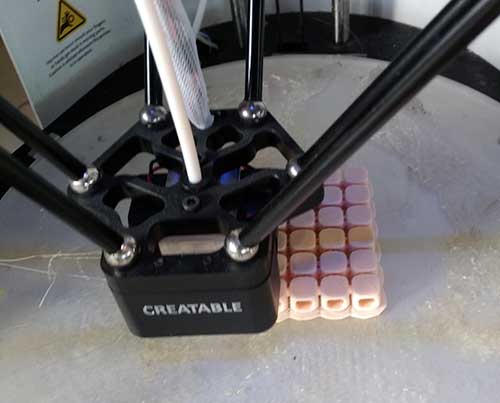
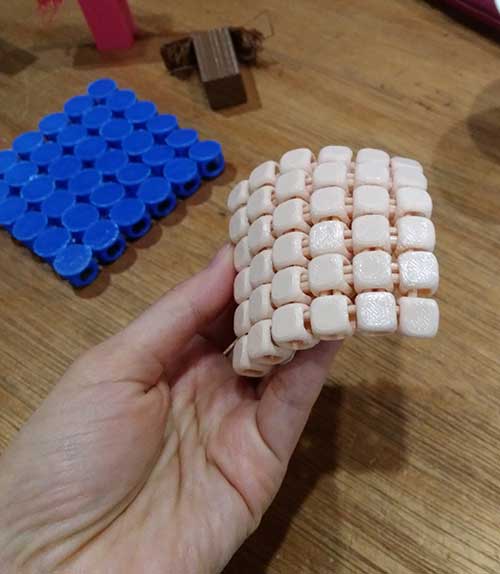
Print small purse
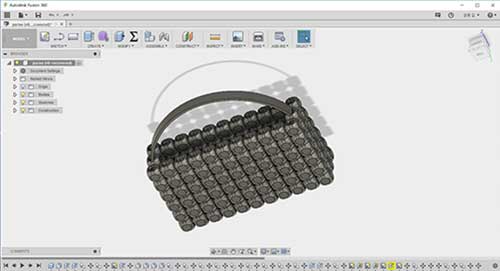
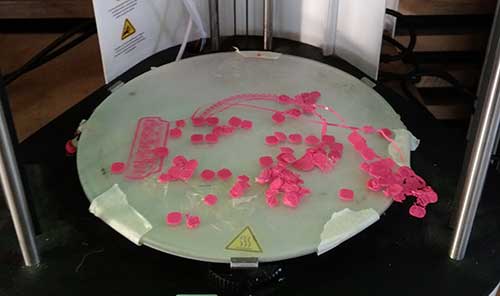
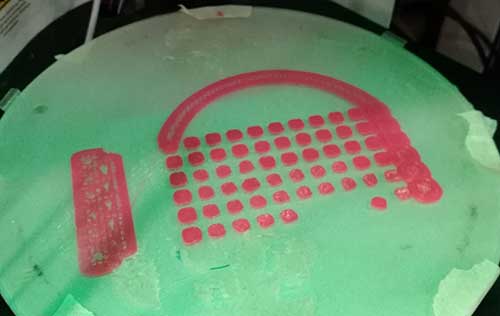
-With brim, without raft was also failed.
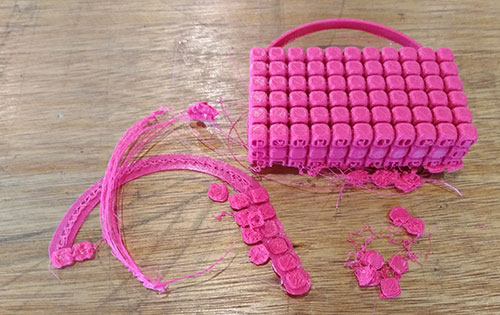
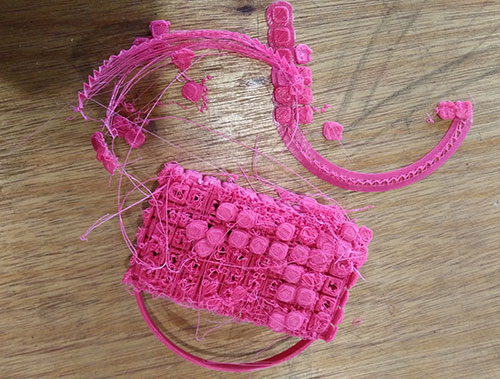
-Fail agian and also becuse of the support everywhere, it is not flexible.
3D Scanning: Kinect
check this video before start.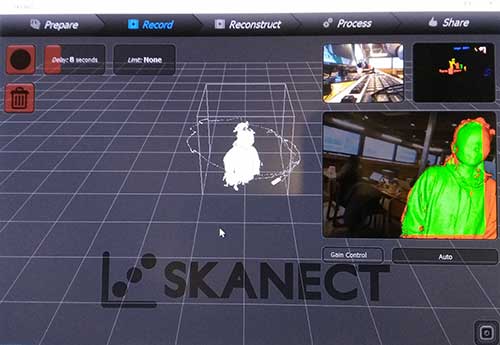
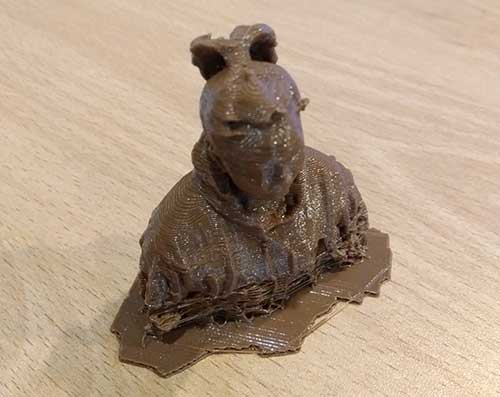
-Scan Euny with Kinect scanner. It's interface was easy to understand, but scanning was not easy at all. I tried 3 types of posture, but only 1 sucessed.
3D Scanning: Maker Bot
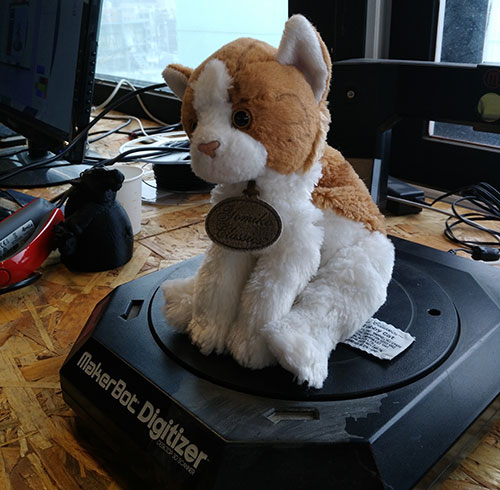
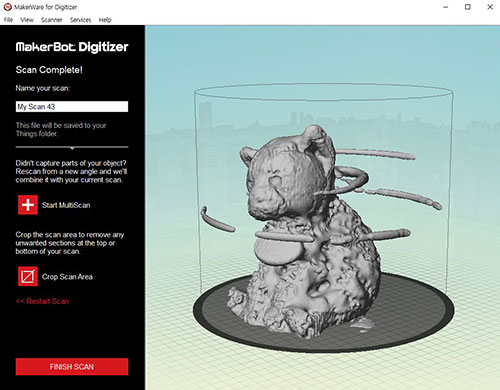
-I want to see how the fur comes out with the scanning. The result looks messy and creepy.
downloads
-click here to download fabric file.-click here to download the 3d scanning.
Date: 2018-02-27 Author: Seong Hee Kim @ Fablab Seoul